高端裝備的輕量化是一個永恒的發展主題,是提高服役性能、降低能耗的必要手段。提高零部件的輕量化水平有3種途徑。一種是將多種不同的結構和功能集成到一個新的輕量化結構中。第二,盡可能選擇力學性能高的新型輕質材料。第三,采用新技術提高零部件的服役性能,實現低成本制造。值得注意的是,形狀復雜的鎂合金構件不斷向大尺寸、多功能方向發展。此外,作為最輕的金屬結構材料,鎂合金是在高端設備中實現極端輕量化的最佳候選材料。
鎂合金優異的性能引起了人們的關注。研究人員對高性能材料的制備和鎂合金的形變強韌化機制進行了廣泛的研究,開發出了許多具有高力學性能的鎂合金。大型鎂合金結構件不僅要求具有較高的強度和韌性,還要求具有較高的抗沖擊載荷能力。
塑性成形是提高鎂合金結構件綜合性能的重要手段。研究人員通過設計和優化塑性成形過程中的工藝參數,實現了關鍵構件中金屬的有序流動、晶粒細化和纖維結構的合理分布。解決了鎂合金構件應用中的一些難題,在實現設備輕量化方面表現出突出的優勢。
在此,中北大學材料科學與工程學院于建民教授團隊研究了具有高力學性能的大型鎂合金構件成形的研究與發展現狀。本文通過對變形強韌化機制、大規格鑄錠坯制備和典型構件整體塑性成形工藝的分析,總結了目前高性能大型鎂合金的成形進展和成形技術特點。針對大尺寸鎂合金構件性能均勻性差、成形精度低、生產成本高等關鍵問題,提出了大尺寸高性能鎂合金構件塑性成形發展趨勢及重點研究方向。
相關研究成果以題“Recent research and development on forming for large magnesium alloy components with high mechanical properties”發表在金屬頂刊Journal of Magnesium and Alloys上。
鏈接:https://www.sciencedirect.com/science/article/pii/S2213956723002207
圖1 .
變形參數對鎂合金抗拉強度的影響。( a ) Az80和( b ) Az91D。鎂合金的力學性能對變形溫度高度敏感,一般認為較低的溫度會產生較好的強韌化效果。然而,過低的變形溫度導致鎂合金塑性較差,變形能力降低。另一方面,可以通過降低成形溫度來提高強化能力。因此,實現這些因素之間的最佳匹配是鎂合金塑性成形需要突破的關鍵技術之一。研究發現,提高變形溫度雖然可以通過促進動態再結晶( DRXed )晶粒的形核來改善晶粒細化,但也會導致再結晶晶粒的長大此外,一些合金在一定的變形溫度下會誘發異常織構的形成,這也會改變k值和后續的強韌化效果以及變形機制
圖2 .
( a ) UTS和TYS隨變形道次的變化,( b-e )不同晶粒隨變形道次的變化變形程度:提高變形程度可以有效細化組織,提高鎂合金的韌性。通常,構件力學性能的提高通常是通過改變擠壓比、軋制壓下量和變形道次來增強晶粒細化效果。例如,Dong等研究了Mg - 13Gd - 4Y - 2Zn - 0.5 Zr ( wt . % )合金在多向鍛造( MDF )過程中的微觀組織、織構演變和力學性能。結果表明,隨著MDF道次的增加,合金的平均晶粒尺寸逐漸減小。4道次后,合金平均晶粒尺寸細化至2.7 μ m,組織分布均勻。極限抗拉強度( UTS )和拉伸屈服強度( TYS )分別為385 MPa和360 MPa
圖3 .
( a )普通冷卻和( b )強制風冷的間接擠壓過程示意圖,( c-d )電子背散射衍射 ( EBSD )圖像極圖( IPF )和對應的( 0001 )極圖( PF ),( c )對應( a ),( d )對應( b )。變形后冷卻速度:快速冷卻可以提高強韌化效果。變形后不同的冷卻速度導致了組織分布的差異,從而改變了鎂合金的強韌化效果。例如,Xu等通過對擠壓后的Mg - Gd - Y - Zn - Zr合金施加強制空冷,實現了優異的強韌化協同效應,獲得了具有較小再結晶晶粒的雙峰組織(圖3 )。
圖4 .
不同MDF道次,( a , e , i) 3道次,( b , f , j) 5道次,( c , g , k) 7道次,( d、h、l) 9道次后樣品的( a-d )的IPF圖,( e-h )的極圖和( i-l )分布的基面( 0001 ) Schmid因子。變形道次:多道次變形可以增加累積變形程度,有利于鎂合金的強韌化。但變形前不同的加熱溫度和時間對后續的晶粒細化和強韌化效果有顯著影響。加熱次數過多或加熱溫度過高都會導致晶粒長大。例如,Li等采用MDF方法研究了變形道次對Mg - Gd - Y - Zn - Zr合金顯微組織和力學性能的影響。發現7道次后平均晶粒尺寸由初始的76μm細化至2.24μm。然而,平均晶粒尺寸在9道次后增加到7.12μm,這歸因于道次中部加熱過程中的動態回復(圖4 )
圖5 .
大型鎂合金構件示意圖。大型高性能鎂合金構件的典型結構如圖5所示。這些構件具有大尺寸、薄壁、截面變化劇烈、局部孔洞或突起以及縱向或橫向高筋等幾何特征。隨著構件的大型化和復雜化,其變形過程中的傳力路徑和變形狀態存在較強的不確定性。成形過程中力的傳遞路徑和變形狀態的強不確定性伴隨著構件的大型化和復雜化,其結構演化、性能和殘余應力也表現出隨機性。尺寸效應對大型構件有以下兩個方面的突出影響:( i )不同區域變形程度、溫度和冷卻速率的不均勻性導致構件各區域之間的性能存在顯著差異;( ii )大型構件的成形精度難以控制,尤其是局部特征的成形。
圖6 .
鍛后應變分布,( a )預鍛主軸頸,( b )終鍛主軸頸,( c )預鍛連桿頸,( d )終鍛連桿。頸加熱和冷卻速率以及成形溫度的不均勻分布。這導致大尺度構件不同區域的應變和性能差異顯著。大型構件具有復雜的截面結構,較高的高厚比導致坯料與模具之間的摩擦副性能存在顯著差異。這些導致強烈的不均勻變形,不同區域的金屬流動和溫度變化。甚至會導致湍流流動,造成構件流變行為的不穩定。這些現象會導致金屬塊、扭曲、起皺、屈曲和斷裂等擠壓缺陷的形成,嚴重影響構件的成形性能。此外,由于復雜構件的微觀組織形貌、尺寸和分布具有較高的應變速率/溫度敏感性,導致其性能參差不齊(圖6 )。
圖7 .
大型結構構件的變形過程。大尺寸構件截面變化劇烈,不同區域的升溫、降溫速率和變形程度存在顯著差異。因此,成形件性能的均勻性必然較差(圖7 )。此外,鎂合金成形性差,不易填充復雜模具型腔,導致大型鎂合金構件多采用頻繁加熱的多工步成形工藝。形狀復雜性和大尺寸的耦合往往導致嚴重的局部軟化和變形的不均勻性。
總之,高性能鎂合金主要依靠變形強化和韌化,而塑性成形是提高鎂合金結構件的力學性能的重要手段。目前,研究者們在強韌化機制以及變形參數如變形程度、變形溫度、冷卻速率和加熱次數對變形行為和強化效果的影響等方面取得了顯著的進展。鎂合金構件的形狀和性能的綜合調控是一個發展趨勢。對于大尺寸的塑性成形鎂合金結構件,如何在關鍵區域實現金屬的有序流動、組織細化和纖維結構的規則分布是難點。因此,通過合理設計、優化和調控塑性成形過程中的變形參數,提高鎂合金構件的綜合性能和承載能力,已成為該領域眾多學者研究的熱點問題。各種構件在塑性成形過程中具有一些共同的特點,如:各區域的結構特點不同,變形極不均勻;大型構件(凸臺、凹槽、環筋等。)成形困難或充不滿的局部特點;大型構件需要較高的成形力等。基于上述問題,提出了關鍵技術:
(1)針對大尺寸構件成形不均勻的問題,采用MDF或鐓擠復合等成形技術實現高性能坯料的均勻制備,并根據大尺寸構件的形狀特征和要素反向設計坯料形狀,減少各向異性,為大尺寸構件的均勻成形奠定了基礎。
(2)對于具有大投影面積和高成形力的大型構件,通過主動抵消摩擦阻力的結構設計、拉深輔助擠壓和局部加載技術可有效降低成形力,并通過合理設計局部加載順序和無縫集成各加載道次實現成形缺陷的消除。
(3)對于大型構件難以形成(凸板、凹槽、環筋等。)的局部特征,可基于分流分流成形原理,通過修改活動鑲塊、阻尼塊等模具結構,調控金屬流動的合理分布,使箱體內部的凸板、凹槽等特征充分成形。此外,內筋結構可以通過旋轉擠壓或強力旋壓整體成形。
(4)針對大型構件成形一致性差、質量不穩定的問題,可采用復合成形工藝來減少成形工序,如膨脹擠壓復合成形、等溫超塑性擠壓-模鍛成形、復合擠壓-脹形、模鍛-脹形-旋壓等。
免責聲明:本網站所轉載的文字、圖片與視頻資料版權歸原創作者所有,如果涉及侵權,請第一時間聯系本網刪除。
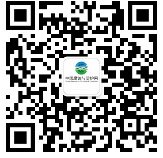
官方微信
《腐蝕與防護網電子期刊》征訂啟事
- 投稿聯系:編輯部
- 電話:010-62316606
- 郵箱:fsfhzy666@163.com
- 腐蝕與防護網官方QQ群:140808414