鎂(Mg)合金作為最輕的工程金屬材料,被譽(yù)為“21世紀(jì)的綠色工程材料”,在汽車、軌道交通、航空航天、國(guó)防和軍事裝備等方面有著廣闊的應(yīng)用前景。開發(fā)高強(qiáng)度、高延展性鎂合金是承載部件應(yīng)用的熱點(diǎn),也是一個(gè)永恒的研究熱點(diǎn)。目前,90%以上的鎂合金產(chǎn)品是采用古鑄造法制備的,鎂合金由于其固有的六方密排(HCP)晶體結(jié)構(gòu),通常表現(xiàn)出較差的變形能力。然而,采用鑄造方法制造大型部件時(shí),不可避免地存在以下問題:(1)由于熔體體積大,冷卻速度慢,導(dǎo)致晶粒粗大,力學(xué)性能差;(ii)不均勻的溶質(zhì)場(chǎng)和流場(chǎng)導(dǎo)致宏觀偏析、縮孔等鑄件缺陷頻發(fā),因此通常采用后續(xù)的塑性變形來改善鑄件缺陷,提高力學(xué)性能;(三)由于特殊大型模具的要求,研發(fā)周期長(zhǎng)。此外,鑄造工藝存在設(shè)計(jì)自由度有限、產(chǎn)品合格率低、材料利用率低、能耗高、污染重等缺點(diǎn)。因此,迫切需要開發(fā)新的鎂合金制造方法來克服上述問題。
鑄造工藝屬于成型制造,機(jī)械加工屬于減法制造,是滿足產(chǎn)品尺寸和表面精度的必要條件。相比之下,增材制造(AM)工藝是一種年輕而蓬勃發(fā)展的先進(jìn)制造技術(shù),它通過逐點(diǎn)、逐軌道、逐層添加材料來制備部件。因此,增材制造工藝具有以下優(yōu)點(diǎn):(1)由于極端的微區(qū)冶金凝固條件,冷卻速度快,導(dǎo)致微觀組織精細(xì),強(qiáng)度高;(ii)通常幾百微米大小的小熔池導(dǎo)致成分分布均勻,沒有宏觀偏析;(三)研發(fā)周期短。此外,增材制造工藝由于具有層狀切片的特點(diǎn),理論上可以加工任何大型復(fù)雜形狀,材料利用率高,制造精度高。采用增材制造技術(shù)制造金屬部件,具有零件集成化、重量減輕、縮短周期、提高使用性能、近凈成形和材料損耗低等明顯優(yōu)勢(shì)。因此,采用增材制造技術(shù)制備鎂合金部件具有很好的工程應(yīng)用前景。
主流的金屬增材制造技術(shù)主要包括三種工藝:采用粉末床的激光粉末床熔合(LPBF)、采用粉末給料的激光定向能沉積(LDED)和采用送絲的絲弧增材制造(WAAM),其中LPBF具有最高的冷卻速度(~ 106 K/s)和制造精度(±0.1 mm)。盡管鎂合金粉末具有易燃易爆的特點(diǎn),但近年來鎂合金的LPBF研究受到了廣泛的關(guān)注。然而,目前對(duì)鎂合金LPBF的研究主要集中在傳統(tǒng)的商業(yè)鑄造鎂合金系列(如純Mg、AZ91D、AZ61、ZK60、WE43)上,面臨著易形成粗柱狀晶粒、易開裂、氣孔缺陷多、強(qiáng)度和延展性有待進(jìn)一步提高等挑戰(zhàn)。與上述工業(yè)鎂合金相比,Mg- gd基稀土鎂合金具有兩大明顯優(yōu)勢(shì):高室溫抗拉強(qiáng)度(500 MPa比300 MPa)和優(yōu)異的耐熱性(使用溫度從150℃提高到300℃)。在前人的工作中,已成功研制出高強(qiáng)度、耐熱的變形Mg-Gd-Y-Zn-Mn合金。例如,mg - 12.6 - gd - 1.3 - 0.5 - 0.9 -鋅- y - mn (wt. %,整個(gè)文本在重量百分比)合金顯示超高屈服強(qiáng)度543 MPa (y),極限抗拉強(qiáng)度(ut) 564 MPa的但低伸長(zhǎng)(EL)只有1.2%的熱擠壓后,冷軋10%,2%冷拉伸和老化過程,mg - 12 - gd - 2 - y - 1 -鋅- 0.5 - mn (GWZ1221M)合金展覽y 427 MPa, UTS 509 MPa,相對(duì)較高的EL擠壓和peak-aging治療后的5.1%。
眾所周知,由于Zr元素具有較高的凝固生長(zhǎng)限制因子(GRF,又稱Q值),是鑄造Mg-RE合金中常用的晶粒細(xì)化元素。Zr元素對(duì)LPBF制備的Mg-Gd基合金也有明顯的細(xì)化作用。Mn元素對(duì)鑄態(tài)Mg-RE合金晶粒細(xì)化作用不明顯,但固溶熱處理過程中α-Mn顆粒析出,使擠壓態(tài)Mg-RE合金晶粒細(xì)化。另一方面,Mn元素可以增強(qiáng)耐蝕性,其成本明顯低于Zr元素。更重要的是,與Zr一樣,Mn也可以與Mg發(fā)生包晶反應(yīng),所以Mn的加入也可能產(chǎn)生一定的晶粒細(xì)化效果。然而,在Mg-Al-Zn基合金中添加Mn則表現(xiàn)出相反的晶粒細(xì)化效果:鑄態(tài)Mg-8.89Al-0.45Zn-0.19Mn (AZ91D)合金呈現(xiàn)出極其細(xì)小均勻的等軸晶粒,平均晶粒尺寸僅為1.2μm,而鑄態(tài)Mg-10.6Al-0.6Zn-0.3Mn (AZ111)合金呈現(xiàn)出與BD平行的粗柱狀晶粒,平均晶粒尺寸為28μm。LPBF工藝的冷卻速度明顯高于常規(guī)鑄造工藝,但Mn元素是否能細(xì)化鑄態(tài)鎂合金的晶粒尚不清楚。目前還沒有關(guān)于含錳Mg-Gd基合金LPBF的報(bào)道。因此,選擇具有良好強(qiáng)度和延展性的GWZ1221M合金制作定制預(yù)合金粉末,然后使用LPBF-AM工藝打印樣品,以表征成型合金的獨(dú)特組織和力學(xué)性能。析出強(qiáng)化對(duì)Mg-Gd基合金的抗拉強(qiáng)度貢獻(xiàn)最大,因此后續(xù)的固溶和時(shí)效熱處理可以改善組織,提高力學(xué)性能。
在此,上海交通大學(xué)材料科學(xué)與工程學(xué)院鄧慶琛教授團(tuán)隊(duì)進(jìn)行了研究,相關(guān)研究成果以題為“Developing a novel high-strength Mg-Gd-Y-Zn-Mn alloy for laser powder bed fusion additive manufacturing process”發(fā)表在期刊Journal of Magnesium and Alloys上。
鏈接:https://www.sciencedirect.com/science/article/pii/S2213956723002293
200-300目預(yù)合金粉末形貌如圖1所示。大多數(shù)粉末呈球形,但仍有一些衛(wèi)星狀粉末和不規(guī)則形狀粉末存在(圖1a)。平均粒徑約為64μm。由于離心霧化過程的高冷卻速率,粉末呈現(xiàn)出精細(xì)的等軸晶粒形貌(圖1b)。共晶相主要沿晶界分布,粉末晶粒尺寸約為2 ~ 4μm。此外,粉末表面還會(huì)出現(xiàn)一些細(xì)小的球形氧化物,這些氧化物是在惰性化過程中形成的,以保證儲(chǔ)存、運(yùn)輸和人類搬運(yùn)過程中的安全。
GWZ1221M合金粉末態(tài)、成品態(tài)和LPBF-T4態(tài)下的XRD圖譜如圖2所示。GWZ1221M粉末由α-Mg基體、β-(Mg,Zn)3(Gd,Y)次級(jí)相和少量Y2O3氧化物組成。與含Mg、Gd或Zn的氧化物形成相比,Y2O3氧化物的形成焓最低,有利于Y2O3氧化物的形成。由于Y2O3氧化物的熔點(diǎn)高達(dá)2410℃,因此在LPBF及后續(xù)熱處理過程中始終存在Y2O3氧化物。LPBF工藝與離心霧化工藝一樣,只是將預(yù)合金粉末重新熔化形成熔池,并進(jìn)行快速凝固,因此鑄態(tài)合金的相組成與粉末相組成相同。經(jīng)過適當(dāng)?shù)墓倘軣崽幚砗螅?beta;-(Mg,Zn)3(Gd,Y)二次相溶入α-Mg基體或轉(zhuǎn)變?yōu)殚L(zhǎng)周期有序堆積(LPSO)結(jié)構(gòu)。Mg-RE-Zn基合金中普遍存在LPSO結(jié)構(gòu),可以提高合金的綜合力學(xué)性能。結(jié)果表明,LPBF-T4合金由α-Mg基體、LPSO組織和Y2O3氧化物組成。時(shí)效熱處理在LPBF-T6合金中產(chǎn)生了大量棱柱狀時(shí)效析出物,但納米級(jí)的析出物難以通過XRD檢測(cè)到,需要通過TEM識(shí)別。
圖1所示。200-300目預(yù)合金粉末的形貌。
圖2所示。GWZ1221M合金粉末態(tài)、鑄態(tài)和LPBF-T4態(tài)下的XRD譜圖。
圖3為構(gòu)建高度分別為6 mm和10 mm的GWZ1221M立方體樣品的宏觀OM圖像。低建高為6 mm的建方樣品內(nèi)部無裂縫,高建高為10 mm的建方樣品內(nèi)部有明顯裂縫。建筑高度越高,熱應(yīng)力積累越大,導(dǎo)致開裂敏感性越高。僅通過調(diào)整激光能量密度是無法避免開裂的,需要通過改進(jìn)3D打印機(jī)或改變合金成分來避免。特殊的鎂合金3D打印機(jī)應(yīng)該有更高的預(yù)熱溫度,如400℃的構(gòu)建平臺(tái),或有兩個(gè)激光與另一個(gè)激光加熱,以原位熱應(yīng)力消除。此外,應(yīng)選用G10K合金等本征延展性較高的合金,以避免產(chǎn)生不良裂紋。鑄態(tài)GWZ1221M合金由于鎖孔不穩(wěn)定而不可避免地存在一些小的孔洞缺陷,并被凝固前沿捕獲。值得注意的是,構(gòu)建樣品邊緣的孔缺陷直徑明顯大于內(nèi)部的孔缺陷,這主要是由于雙向掃描降低了樣品邊緣的掃描速度,導(dǎo)致激光能量密度增加。通過激光離焦和優(yōu)化工藝參數(shù),制備的GWZ1221M合金的相對(duì)密度高達(dá)99.85%。對(duì)于低沸點(diǎn)、高飽和蒸汽壓的鎂合金,由于Mg元素不可避免的汽化,在構(gòu)建樣品中不可避免地存在少量孔隙缺陷,但優(yōu)化激光能量密度可以消除大部分孔隙缺陷。優(yōu)化造腔風(fēng)場(chǎng),及時(shí)去除汽化產(chǎn)物,或提高粉床和造平臺(tái)的預(yù)熱溫度,都有利于減少氣孔缺陷。值得注意的是,由于過多的激光能量輸入而產(chǎn)生的少量孔隙缺陷(< 1%)不會(huì)大大降低拉伸性能,但可能對(duì)疲勞性能有害。
GWZ1221M合金的SEM圖像如圖4所示,可以看到合金的晶粒和二次相的形貌。熔池邊界用黃色虛線表示。熔池的深度一般大于寬度(圖4a),為鎖孔熔化模式。由于冷卻速率最高,熔池邊界呈現(xiàn)出最細(xì)的等軸晶粒(圖4b)。除了凝固過程沿晶界形成網(wǎng)狀的β-(Mg,Zn)3(Gd,Y)次相外,固相轉(zhuǎn)變形成的一些細(xì)小點(diǎn)狀的β-(Mg,Zn)3(Gd,Y)次相也分布在晶粒內(nèi)部(圖4b-d)。在熔池邊界附近的晶粒內(nèi)部出現(xiàn)了一些平行的片層(圖4c, d),這是由于枝晶臂在給定方向上優(yōu)先生長(zhǎng)造成的。此外,少量大小為幾微米的不規(guī)則片狀相(如圖4c中白色箭頭所示)均勻分布在合金內(nèi)部,這被確定為不需要的Y2O3氧化物。Y2O3氧化物會(huì)降低材料的力學(xué)性能,減弱時(shí)效析出電位,在今后的工作中應(yīng)加以避免。
通過EBSD觀察進(jìn)一步揭示了鑄態(tài)GWZ1221M合金內(nèi)部晶粒的形貌和取向,如圖5所示。合金由隨機(jī)取向的細(xì)小等軸晶粒組成,平均晶粒尺寸為4.3±2.2 μm(圖5a)。在鑄態(tài)GWZ1221M合金中未觀察到大柱狀晶粒,而在鑄態(tài)WE43合金中卻經(jīng)常觀察到大柱狀晶粒。由{0001}極圖可知,構(gòu)建后的合金幾乎不存在織構(gòu),最大織構(gòu)強(qiáng)度僅為2.95泥(多重均勻分布,圖5b)。
根據(jù)參考文獻(xiàn),將鑄態(tài)GWZ1221M合金在515℃固溶12 h,即可得到鑄態(tài)t4合金。鑄態(tài)t4合金的枝晶晶粒仍然粗大,平均晶粒尺寸略有增大,達(dá)到182.4±57.2μm。β-(Mg,Zn)3(Gd,Y)相消失,出現(xiàn)大量的X相(又稱塊狀LPSO)和片層狀LPSO結(jié)構(gòu)以及少量立方相。X相從晶界開始形核,向晶粒內(nèi)部生長(zhǎng),而晶粒內(nèi)部的片層狀LPSO結(jié)構(gòu)的生長(zhǎng)方向與晶粒基面平行。固溶處理的Mg-RE基合金中經(jīng)常發(fā)現(xiàn)立方相,確定為REH2而不是MgH2。熱力學(xué)上,RE的電負(fù)性比Mg低,因此對(duì)h的結(jié)合傾向更高。盡管立方相對(duì)力學(xué)性能不利,但該相的數(shù)量相對(duì)較少,難以完全消除。
鑄態(tài)GWZ1221M合金與鑄態(tài)GWZ1221M合金的顯微組織存在顯著差異,因此鑄態(tài)GWZ1221M合金的最佳固溶熱處理?xiàng)l件應(yīng)與鑄態(tài)GWZ1221M合金不同。通過對(duì)鑄態(tài)Mg-Gd基合金固溶熱處理?xiàng)l件的優(yōu)化,鑄態(tài)Mg-Gd基合金固溶熱處理溫度低于鑄態(tài)Mg-Gd基合金,因?yàn)殍T態(tài)Mg-Gd基合金晶粒更小,二次相更少。因此,構(gòu)建的GWZ1221M合金的最佳固溶熱處理?xiàng)l件為450℃×12 h (LPBF-T4態(tài)),與構(gòu)建的GWZ1031K合金相同。
為了得到LPBF-T4 GWZ1221M合金的峰時(shí)效條件,測(cè)量了175℃和200℃下的時(shí)效硬化曲線,如圖8所示。175℃和200℃時(shí)效硬化曲線特征參數(shù)如表2所示。鑄態(tài)GWZ1221M合金的硬度為112.9±0.9 HV,硬度下降至96.7±0.4 HV,主要是由于硬脆相β-(Mg,Zn)3(Gd,Y)析出和殘余應(yīng)力釋放所致。隨著時(shí)效時(shí)間的延長(zhǎng),硬度持續(xù)穩(wěn)定上升,達(dá)到峰值后逐漸降低。與200℃相比,175℃時(shí)效可以產(chǎn)生更強(qiáng)的析出電位和較大的硬度增量(34.0 HV vs . 30.2 HV),但原子擴(kuò)散速度變慢,達(dá)到硬度峰值的時(shí)間變長(zhǎng)(256 h vs . 32 h),硬度增量與擠壓態(tài)GWZ1221M合金的硬度增量(33.3 HV)相當(dāng),表明Mg-Gd基合金具有優(yōu)異的時(shí)效硬化能力。為了追求優(yōu)異的力學(xué)性能,LPBF-T4合金的時(shí)效條件選擇為175℃×256 h (LPBF-T6態(tài))。在未來的實(shí)際工程應(yīng)用中,200℃×32 h作為時(shí)效熱處理?xiàng)l件較為合適,可以節(jié)約成本和能耗。
不同熱處理狀態(tài)下LPBF和鑄造工藝制備的GWZ1221M合金室溫拉伸性能對(duì)比如圖10所示。顯然,在不同熱處理狀態(tài)下,LPBF工藝制備的GWZ1221M合金的抗拉強(qiáng)度(YS和UTS)均明顯高于鑄造工藝制備的合金。以GWZ1221M合金為例,鑄態(tài)合金的YS、UTS和EL分別為315±8 MPa、340±7 MPa和2.7±0.5%,而鑄態(tài)合金的YS、UTS和EL分別為155±2 MPa、222±6 MPa和3.4±0.5%。固溶熱處理能顯著提高鑄態(tài)和鑄態(tài)合金的拉伸延展性。在LPBF-T4狀態(tài)下,EL從構(gòu)建狀態(tài)的2.7±0.5%增加到6.9±0.6%。固溶熱處理降低了鑄態(tài)合金的YS和UTS,但降低了鑄態(tài)合金的YS,提高了鑄態(tài)合金的UTS。正如預(yù)期的那樣,時(shí)效熱處理可以顯著提高YS,同時(shí)大大降低EL。將鑄造t4合金在200℃下人工時(shí)效128 h,得到鑄造t6合金。LPBF-T6合金的YS為320±3 MPa, UTS為395±4 MPa, EL為2.1±0.4%,與鑄態(tài)t6合金相比,其抗拉強(qiáng)度和延展性都有了意想不到的提高。LPBF-T5合金為225℃直接時(shí)效32 h的鑄態(tài)合金,鑄態(tài)合金中含有大量消耗大量RE原子的β-(Mg,Zn)3(Gd,Y)相,因此從鑄態(tài)到LPBF-T5狀態(tài)的YS增量?jī)H為27 MPa,明顯低于LPBF-T4到LPBF-T6狀態(tài)的YS增量(73 MPa)。
圖4所示。GWZ1221M合金的SEM圖像。
圖5所示。GWZ1221M合金的EBSD晶粒取向圖(a)和{0001}極形圖(b)。
圖6所示。LPBF-T4 GWZ1221M合金175℃和200℃時(shí)效硬化曲線。
圖7所示。不同熱處理狀態(tài)下LPBF和鑄造法制備GWZ1221M合金的室溫拉伸性能:(a)典型拉伸曲線和(b) YS、UTS和EL的平均值。
總之,鑄態(tài)GWZ1221M合金在LPBF過程中表現(xiàn)出細(xì)小的等軸晶(4.3±2.2μm)和薄的β-(Mg,Zn)3(Gd,Y)相,而鑄態(tài)合金則表現(xiàn)出典型的粗枝晶(178.2±73.6 μm)和粗的片層共晶化合物,表明在Mg-Gd基合金的LPBF過程中,相對(duì)便宜的Mn可以取代昂貴的Zr作為晶粒細(xì)化劑。固溶熱處理使硬脆的β-(Mg,Zn)3(Gd,Y)相轉(zhuǎn)變?yōu)榛鵛相和具有較好塑性變形能力的片層狀LPSO,然后峰時(shí)效處理引入大量棱柱狀β′析出。鑄態(tài)合金的YS、UTS和EL分別為315±8 MPa、340±7 MPa和2.7±0.5%,而LPBF-T6合金的YS、UTS和EL分別為320±3 MPa、395±4 MPa和2.1±0.4%。鑄態(tài)和LPBF-T6 GWZ1221M合金的抗拉強(qiáng)度(YS和UTS)均明顯高于鑄態(tài)和成品鎂合金。
免責(zé)聲明:本網(wǎng)站所轉(zhuǎn)載的文字、圖片與視頻資料版權(quán)歸原創(chuàng)作者所有,如果涉及侵權(quán),請(qǐng)第一時(shí)間聯(lián)系本網(wǎng)刪除。
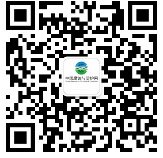
官方微信
《腐蝕與防護(hù)網(wǎng)電子期刊》征訂啟事
- 投稿聯(lián)系:編輯部
- 電話:010-62316606
- 郵箱:fsfhzy666@163.com
- 腐蝕與防護(hù)網(wǎng)官方QQ群:140808414