導讀:物理冶金學的傳統(tǒng)方法是在金屬中添加合金元素來增加它們的強度。還不太清楚固溶強化是否會發(fā)生在納米尺度的物體中,也完全不知道合金化會如何影響無缺陷面納米顆粒的強度。純金屬無缺陷納米顆粒顯示出接近理論極限的超高強度。在壓縮試驗中,它們彈性變形,直到第一次位錯成核,之后它們塌陷成扁平形狀。本文發(fā)現(xiàn)鎳納米粒子與鈷的合金化降低了它們的極限強度。這種反常的固溶軟化效應可以用溶質(zhì)誘導的分解剪應力的局部空間變化來解釋,從而導致過早的位錯成核。隨后的粒子變形需要更多加工,使其更加堅韌。強度和韌性之間的折衷使合金納米顆粒有了很好的應用前景。
晶體材料的理論強度的作用類似于物理學中光速的作用:它無法達到,但設定了可能達到的物理極限。達到金屬材料的理論強度是物理冶金的圣杯。金屬的理論強度通常在G/30–G/8的范圍內(nèi),其中G是金屬的彈性剪切模量。實際上,金屬和合金在低得多的應力下塑性屈服。它們的塑性變形由新的和現(xiàn)有的位錯運動以及新的內(nèi)部位錯源的激活所控制。已經(jīng)探索了幾種提高材料強度的策略,例如合金化、沉淀強化、晶粒尺寸減小、晶界工程和微觀結構調(diào)整。雖然這些策略確實有助于提高力量,但仍遠低于理論極限。
60年前,布倫納發(fā)現(xiàn)金屬晶須的強度隨著直徑的減小而增加,從幾微米到更小,最終達到GPa水平。強度的增加主要歸因于塑性變形機制的改變,從塊體材料中的位錯運動和增殖到亞微米尺寸的無缺陷樣品中的位錯成核。通過固態(tài)去濕獲得的金屬微粒和納米顆粒是強度接近理論極限的無缺陷金屬物體的例子。它們表現(xiàn)出比在拉伸中測試的無缺陷金屬晶須高得多的壓縮強度。在后一種情況下,大的表面積在比在壓縮中測試的納米顆粒所能支持的小得多的應力下催化位錯半環(huán)的異質(zhì)成核。
最近,據(jù)報道,由固態(tài)去濕產(chǎn)生的無缺陷面心立方鎳納米粒子的強度達到創(chuàng)紀錄的34 GPa。顆粒具有多面的形狀,具有相對圓形的角和邊緣,并且(111)頂面平行于基底排列。在壓縮過程中,顆粒表現(xiàn)出高達約0.2的彈性行為,隨后突然塌陷成圓餅形狀。圓形的邊緣和拐角降低了應力集中,并延遲了坍塌,直到應力接近理論極限。最近,通過兩階段固態(tài)去濕生產(chǎn)的體心立方鉬微粒達到了甚至更高的壓縮強度46 GPa(金屬材料有史以來報道的最高強度)。變形模式和尺寸指數(shù)與面心立方鎳納米顆粒相似,表明缺陷的存在和顆粒形狀對強度比晶體結構更重要。分子動力學模擬有助于理解無缺陷納米粒子強度的位錯機制。
以前對無缺陷納米粒子的研究集中在純金屬上。同時,大多數(shù)技術應用使用合金而不是純金屬。合金化是常規(guī)冶金中提高材料強度的標準方法。在塊狀合金中,溶質(zhì)原子充當釘扎中心,阻礙位錯運動并增加強度。然而,合金化對納米粒子成核控制變形的影響在很大程度上仍然未知。在變形的彈性階段積累的巨大彈性能可以推動新成核的位錯高速穿過粒子。尚不清楚傳統(tǒng)的固溶硬化機制能否在如此極端的條件下運行。此外,溶質(zhì)可以通過影響位錯成核過程來影響顆粒強度。然而,溶質(zhì)對無缺陷金屬納米顆粒強度的影響從未通過實驗或模擬進行過研究。
鈷在高溫下在催化裂化鎳中表現(xiàn)出無限的溶解度。這使我們能夠集中研究不受沉淀硬化和其他合金強化機制影響的固溶效應?;趯Υ髩K鎳鈷合金和鎳鈷合金線的了解,可以預期鈷的加入會增加納米顆粒的強度。事實上,鎳鈷合金在整體形式和線材形式上都完全遵循經(jīng)典的固溶硬化模式。直徑為1 mm的退火鋼絲的屈服應力從純鎳的47.7 MPa增加到Ni-0.3Co wt.%合金的68.3 MPa,流動應力從176 MPa增加到262 MPa。分子動力學模擬預測,Ni-Co納米線的強度在添加0.05至0.10摩爾分數(shù)的Co后增加到約10 GPa。
與這一預期相反,以色列理工學院的Eugen Rabkin和美國喬治·梅森大學的Yuri Mishin等人發(fā)現(xiàn)無缺陷鎳鈷納米粒子的強度實際上隨著鈷的加入而降低,產(chǎn)生違反直覺的溶質(zhì)軟化效應。分子動力學模擬表明,軟化是由顆粒近表面區(qū)域局部分解剪切應力的統(tǒng)計變化增加引起的,觸發(fā)了第一位錯的早期成核。同時,我們表明顆粒的韌性隨著鈷的加入而增加,產(chǎn)生了強度和韌性的組合,這對于技術應用是有吸引力的。相關研究成果以題“The impact of alloying on defect-free nanoparticles exhibiting softer but tougher behavior”發(fā)表在Nature communications上。
鏈接: https://www.nature.com/articles/s41467-021-22707-x
納米粒子是由單晶藍寶石襯底上的30納米厚的鎳鈷雙層膜通過固相去濕制備的(圖1a)。制備了兩種靶成分為Ni-0.3Co和Ni-0.5Co(摩爾分數(shù))的薄膜,以下分別稱為Ni-0.3Co和Ni-0.5Co。也沉積了相同厚度的純鎳膜作為參考。納米粒子是在1150 ℃的溫度下從襯底上去濕薄膜而形成的。
圖1 固態(tài)去濕法制備無缺陷鎳鈷納米粒子。(a)(0001)取向藍寶石襯底上初始鎳鈷雙層薄膜示意圖。(b)用于薄膜去濕的熱處理方案。
圖2 固態(tài)去濕法制備鎳和鎳鈷納米粒子的表征。通過固態(tài)去濕獲得的多面單晶(a)Ni,(b)Ni-0.3Co和(c)Ni-0.5Co納米粒子的掃描電鏡顯微照片。明場透射電鏡顯微照片、選區(qū)電子衍射(SAED)圖和透射電鏡能譜元素分布圖(藍色:鎳;黃色:鈷)為(d)Ni-0.3Co和(e)Ni-0.5Co納米粒子。沿著(d)和(e)中標記的線AA和BB穿過顆粒的濃度線輪廓。
圖3 鎳和鎳鈷納米粒子的力學測試。在這項工作中測量了(a)Ni,(b)Ni-0.3Co和(c)Ni-0.5Co顆粒的工程壓縮應力-應變曲線,Ni-0.3Co顆粒的掃描電鏡圖像(a)在壓縮試驗期間和(b)在塌陷成圓盤導致應變破裂后。
這里發(fā)現(xiàn)的合金化效應的一個有趣特征是顆粒強度對溶質(zhì)濃度的非單調(diào)依賴性。模擬顯示,在較高濃度下反彈之前,添加約(0.10-0.15)鈷原子后,顆粒強度相對于純鎳下降約33%(圖5c)。我們已經(jīng)驗證了這一假設,即這種效應是由材料的彈性軟化引起的,從應力-應變圖的初始部分的斜率可以明顯看出(圖5a)。然而,彈性最小值出現(xiàn)在大約(0.20–0.25)鈷,并且太淺(相對于純鎳大約12%)以至于不能解釋強度的深度最小值。一個更合理的解釋是,強度的最小值是由兩個相反因素之間的競爭引起的:溶質(zhì)誘導的第一次位錯成核勢壘的減少,以及一旦成核勢壘被克服,阻礙位錯運動的溶質(zhì)摩擦。如果第一種效應在較低的鈷濃度下更強(導致軟化),而第二種效應在較高的濃度下占主導地位(導致硬化),則可能出現(xiàn)最小值。
圖4 合金化對納米粒子機械強度的影響。(a)Ni,(b)Ni-0.3Co和(c)Ni-0.5Co的實驗抗壓強度與粒度的函數(shù)關系。直線顯示線性擬合。
圖5 納米粒子的機械特性。(a)40納米顆粒的典型工程應力-應變曲線。(b)強度是顆粒大小的函數(shù)。(c)強度是35納米顆?;瘜W成分的函數(shù)。誤差線代表一個標準偏差。
圖6 塑性變形早期的位錯過程。(a)Ni和(b)Ni-0.5Co的60納米粒子中的位錯成核和增殖。這些數(shù)字表示從模擬開始的時間(以皮秒為單位)。位錯通過DXA算法可視化,紅色原子代表堆垛層錯。非錯位原子是看不見的。(c)幾種化學成分的35納米納米顆粒中的位錯節(jié)數(shù)。
圖7 合金化增加了納米粒子的韌性。(a)35納米納米顆粒在350.5鈷的應變下變形的應力-應變曲線示例。(b)35納米顆粒的韌性是應變的函數(shù)。(c)鎳和(d)Ni-0.5Co 35納米顆粒的變形形狀。原子根據(jù)勢能被著色,較亮的顏色代表較大的能量。圖像下方顯示了張力。
圖8 壓縮下納米顆粒應力的表征。(a)在純Ni和Ni-0.3Co的35納米粒子中,按最小-最大公式(1)縮放的MRAS分布。插圖顯示了粒子橫截面中的最小-最大縮放的MRAS分布。(b)作為垂直于基底的z坐標的函數(shù)粒子中的MRAS(在粒子中心z=0)。為了清楚起見,只顯示了MRAS分布的高端。(c)粒子頂視圖中(b)所示點的位置。六邊形對應于頂部(111)面。請注意,最高MRAS值在Ni-0.3Co粒子中達到,并集中在刻面邊緣(紅色圓圈)。
本文報道的實驗和模擬表明,無缺陷的鎳納米粒子與鈷的合金化降低了它們的強度。這種反常的固溶軟化效應與以固溶硬化為主的大塊合金的既定行為相矛盾。同時,合金化使顆粒更堅韌,增加應變硬化,并穩(wěn)定塑性流動。應該強調(diào)的是,盡管相對軟化,納米粒子的強度仍然保持在幾十GPa的水平。這種超高強度和更高韌性的結合可以使合金納米粒子成為許多技術、生物和醫(yī)療應用的有前途的候選材料,包括納米電子、納米材料和催化。特別是,金屬納米粒子的催化活性可以通過應變工程來優(yōu)化。例如,催化活性可以通過核殼粒子的殼中產(chǎn)生的粘著應變來增強,但前提是材料能夠承受足夠高的應力。通過合金化實現(xiàn)的強度和韌性之間的協(xié)同作用可以為設計具有高級催化性能的金屬納米粒子打開新的機會。
免責聲明:本網(wǎng)站所轉載的文字、圖片與視頻資料版權歸原創(chuàng)作者所有,如果涉及侵權,請第一時間聯(lián)系本網(wǎng)刪除。
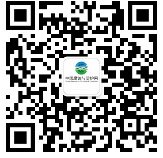
官方微信
《中國腐蝕與防護網(wǎng)電子期刊》征訂啟事
- 投稿聯(lián)系:編輯部
- 電話:010-62316606-806
- 郵箱:fsfhzy666@163.com
- 中國腐蝕與防護網(wǎng)官方QQ群:140808414