導(dǎo)讀:本文利用透射掃描電子顯微鏡對(duì)微電子工業(yè)中經(jīng)常遇到的WTi-Cu模型界面的機(jī)械變形進(jìn)行了現(xiàn)場研究。該方法闡明了塑性變形和斷裂過程之間的相互作用,同時(shí)加載垂直于(模式I)或平行于界面(模式II)。在模式I下,觀察到銅相的韌性破壞,表現(xiàn)為位錯(cuò)滑移促進(jìn)空隙成核和凝聚;模式II載荷顯示了界面裂紋的成核和擴(kuò)展,這些結(jié)果在經(jīng)典斷裂力學(xué)和位錯(cuò)塑性的框架下進(jìn)行了討論,為彈塑性界面在加載方向上的失效行為提供了基本的見解。
多層材料系統(tǒng)的異質(zhì)結(jié)構(gòu)允許各種可定制的特性,使其在不同的工程系統(tǒng)中得到廣泛的利用,但這些應(yīng)用中的大多數(shù)都表現(xiàn)為微米到亞微米的厚度,使得機(jī)械反應(yīng)的調(diào)查具有相當(dāng)?shù)奶魬?zhàn)性。隨著原位微觀和納米力學(xué)測試技術(shù)的興起,許多小組成功地研究了這些單獨(dú)階段以前無法實(shí)現(xiàn)的力學(xué)參數(shù)。但是量化異質(zhì)系統(tǒng)中的界面斷裂仍然是一個(gè)挑戰(zhàn),特別是在彈塑性系統(tǒng)中,塑性和斷裂過程之間的相互作用很難區(qū)分。
雖然微觀系統(tǒng)中的斷裂力學(xué)測試技術(shù)已經(jīng)在均質(zhì)材料中建立了線性彈性斷裂力學(xué)(LEFM),但解決彈塑性斷裂力學(xué)(EPFM)的類似技術(shù)卻很少受到關(guān)注。這是由多層幾何形狀的長度尺度和普遍的彈性和塑性變形場之間的復(fù)雜和不可分割的關(guān)系所決定的,這導(dǎo)致了在其均勻的對(duì)應(yīng)物中無法預(yù)測的破壞模式。
了解這些系統(tǒng)的局部界面斷裂特性與宏觀失效的角度高度相關(guān)。有一些方法可以確定至少有一個(gè)塑性變形的部件雙材料界面組合的界面特性,因?yàn)樗鼈兊慕缑娓街ψ銐蛉酰欢@種方法并不總是適用的,也不能解決塑性變形和界面斷裂之間的實(shí)際相互作用。鑒于這種失效特征,為了推進(jìn)對(duì)基本過程的理解,需要考慮其他方法。因此,研究本地空間封閉狀態(tài)下的特定界面的方法將是有益的。
在此,加州大學(xué)Markus Alfreider團(tuán)隊(duì)在掃描電子顯微鏡(SEM)內(nèi)利用透射掃描電子顯微鏡(TSEM)對(duì)電子透明的試樣進(jìn)行現(xiàn)場測試。TSEM的目的是在透射配置中使用專用的SEM,其顯著的好處是有一個(gè)大的實(shí)驗(yàn)室用于實(shí)驗(yàn)設(shè)置,并且由于較低的加速電壓(20-30千伏)而產(chǎn)生更好的對(duì)比度[42] 。同時(shí),這也有一個(gè)缺點(diǎn),即需要相當(dāng)薄的試樣來實(shí)現(xiàn)電子透明。試樣在垂直于界面的拉伸方向上被加載,并有預(yù)先定義的缺口,以獲得主要的模式I貢獻(xiàn)(開放模式),或在平行于界面的剪切方向上獲得主要的模式II貢獻(xiàn)(剪切模式)。實(shí)驗(yàn)過程中自動(dòng)和連續(xù)的圖像收集允許對(duì)斷裂事件的順序和伴隨的位錯(cuò)過程進(jìn)行關(guān)聯(lián),最終提供了對(duì)彈塑性雙材料界面的不同加載模式依賴性破壞機(jī)制的基本洞察力。
相關(guān)研究成果以題“Interface mediated deformation and fracture of an elastic-plastic bimaterial system resolved by in situ transmission scanning electron microscopy”發(fā)表在國際著名期刊Materials & Design上。
鏈接:https://doi.org/10.1016/j.matdes.2022.111136
圖1 (a)多層材料系統(tǒng)的STEM顯微照片,顯示了各層的情況。(b) 剪切和拉伸載荷的推拉裝置配置示意圖。(c,d) 安裝在推拉裝置上的剪切試樣的SEM圖像。
試樣被安裝在該裝置上,以促進(jìn)Cu和WTi之間界面的拉伸或剪切載荷,如圖1(b)所示。在將試樣操縱到鉑金沉積的標(biāo)高上,并用厚厚的鉑金層固定,以減少接觸順應(yīng)性,隨后在芯片上進(jìn)行塑形和減薄步驟,加速電壓和電流不斷降低,在5keV下最小為16 pA,導(dǎo)致電子透明箔,以后分別用于微結(jié)構(gòu)調(diào)查或微機(jī)械測試。機(jī)械測試前的剪切試樣的最終形狀顯示在圖1(c)和(d)。
圖2 (a)連續(xù)六個(gè)加載段的拉伸試樣載荷-位移數(shù)據(jù),直到最終失效。(b) 第4個(gè)加載步驟的ADF圖像(b)在預(yù)定的缺口處出現(xiàn)滑移痕跡之前和(c)之后。第5個(gè)加載步驟的ADF圖像(d)在未加載狀態(tài)下,(e)在左側(cè)缺口的裂紋尖端鈍化開始時(shí),以及(f)在突然的負(fù)載下降后,顯示出兩個(gè)缺口前面明顯的塑性(明亮區(qū)域)。虛線強(qiáng)調(diào)了WTi-Cu的界面。
圖3 (a, c, e, g, I, k)加載步驟6的ADF LR放大圖像,顯示了裂紋通過成核和凝聚而增長。以及(b,d,f,h,j,l)相應(yīng)的評(píng)估的裂紋擴(kuò)展區(qū)域和載荷,其中紅色區(qū)域描述兩個(gè)裂紋前沿,綠色區(qū)域是指尚未連接的空隙。微米條適用于所有圖像。
圖4 第6個(gè)加載步驟的載荷-位移數(shù)據(jù)(黑色方塊),以及內(nèi)部空洞的數(shù)量(開放的藍(lán)色方塊)。以及裂縫(紅色三角形)和空隙(綠色填充三角形)的相對(duì)面積,紫色的五角星描述了ADF LR圖像中的負(fù)載水平。詳見圖3。
圖5(a)連續(xù)八個(gè)加載步驟的剪切試樣的載荷-位移數(shù)據(jù),直到最終失效。(b)加載前試樣的BF圖像,羅馬數(shù)字(I-VI)描述了單個(gè)晶粒。(c-k) 實(shí)驗(yàn)期間后續(xù)步驟的HR BF圖像。紅色箭頭描述了文本中描述的個(gè)別特征,所有的微米條是500納米。
圖6 經(jīng)過傅里葉過濾的HR BF圖像和局部剪應(yīng)力作為單一位錯(cuò)弓出的曲率函數(shù),在載荷增加時(shí):(a, b)-104μN,(c, d)-87μN,(e, f)-44μN,(g, h)3μN和(i, j)49μN,其中(j)是相應(yīng)的未經(jīng)過濾的圖像,顯示機(jī)械振動(dòng)。(k)計(jì)算出的位錯(cuò)平行于圖像平面(藍(lán)色,向上指向的三角形)或傾斜的位錯(cuò)穿過116納米厚的箔片(橙色,向下指向的三角形)時(shí)的剪切應(yīng)力超過載荷。微米條適用于圖像(a-j),色條描述了剪應(yīng)力,單位為兆帕。
圖8 裂縫尖端開口位移δ相對(duì)于裂縫擴(kuò)展Δa。d-g的位置對(duì)應(yīng)于圖7中的HR ADF圖像,虛線代表ASTM 1820建議的1.4的斜率
圖9 (a, b)剪切試樣和(c, d)拉伸試樣的ADF LR圖像和來自有限元模擬的最大剪切應(yīng)力圖。模擬圖與各自的圖像比例為1:1,兩者的色條是相同的。
圖十 放大的LR BF圖像,聚焦于裂紋成核前第7個(gè)加載步驟的晶粒VI(F=271 μN),顯示了一個(gè)單一的位錯(cuò)弓出和局部剪切應(yīng)力的量化。
總的來說,這是第一次在推剪裝置上成功地實(shí)現(xiàn)了傳輸配置的剪切配置,從而開辟了在這種非常有限的范圍內(nèi)進(jìn)行現(xiàn)場混合模式斷裂研究的領(lǐng)域。雖然拉伸試樣純粹是由于銅相的局部塑性變形而失效,但剪切試樣在試樣內(nèi)部發(fā)生重大塑性變形后,出現(xiàn)了界面裂紋的成核和進(jìn)一步延伸。這可能與剪切構(gòu)型中裂紋尖端局部抑制位錯(cuò)活動(dòng)有關(guān),這既是由于局部應(yīng)力狀態(tài),也是由于裂紋尖端前的微觀結(jié)構(gòu)。此外,還確定了位錯(cuò)塑性激活的下限是Jdislocation≈15 J/m2,這與以前在同一材料系統(tǒng)上進(jìn)行的實(shí)驗(yàn)很一致。
免責(zé)聲明:本網(wǎng)站所轉(zhuǎn)載的文字、圖片與視頻資料版權(quán)歸原創(chuàng)作者所有,如果涉及侵權(quán),請(qǐng)第一時(shí)間聯(lián)系本網(wǎng)刪除。
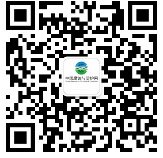
官方微信
《腐蝕與防護(hù)網(wǎng)電子期刊》征訂啟事
- 投稿聯(lián)系:編輯部
- 電話:010-62316606-806
- 郵箱:fsfhzy666@163.com
- 腐蝕與防護(hù)網(wǎng)官方QQ群:140808414