鋁鋰合金由于其低密度、良好的耐腐蝕性以及高強度和韌性的結合,在航空航天領域取得了成功的應用。常用的鋁鋰合金,包括2195、2050、2099和2199,主要通過鑄造和鍛造加工成薄片和試管。增材制造(AM)鋁鋰合金在制造仿生結構、晶格結構或其他復雜的功能/結構組件方面顯示出巨大的潛力。然而,激光粉末床熔合(LPBF)加工的鋁鋰合金仍然面臨挑戰。高能束激光加工會導致鋁鋰合金產生嚴重熱裂紋以及鋰元素的燒蝕。
近日,北京科技大學張百成副教授(通訊作者)等研究人員為了消除鋁鋰合金中的熱裂紋,降低鋰元素的燒損,開發了一種用于LPBF工藝的納米陶瓷顆粒改性的新型鋁鋰合金。相關工作以 “Effect of lithium anti-ablation and grain refinement introduced by TiC nanoparticles in LPBF Al-Li alloy” 為題發表在《Journal of Materials Research and Technology》上。北京科技大學博士研究生孫金娥為論文第一作者,本工作獲得北科大曲選輝教授指導。
熔體池中TiC納米顆粒有效地提高了鋁合金液體的粘度,減少了金屬汽化和液體飛濺,從而防止了LBPF過程中Li元素燒蝕。Li含量從打印鋁鋰合金中的0.87 wt.%,顯著提高到打印TiC改性鋁鋰合金中的1.34 wt. %。此外,在鋁鋰合金凝固過程中,TiC納米顆粒作為額外形核質點,促進了柱狀晶向等軸晶的轉化過程,極大的降低了材料熱裂性,實現了全致密鋁鋰合金制備。在LPBF過程中,在TiC納米顆粒表面發現了從TiC到Al3Ti的梯度轉變反應,原位形成的Al3Ti相顯著降低了與Al基體的晶格失配,從而使其具有優異的極限拉伸強度(343 MPa)和伸長率(9.3 %)。TiC納米顆粒誘導的鋰元素抗燒蝕作用為添加劑制造輕質合金提供了一條新的途徑。本研究通過調控不同激光功率(140-10-300W)和掃描速度(60 - 400 mm/s)制備了TiC改性的Al-Mg-Li合金,圖1 (a)顯示了該合金的OM顯微圖。在掃描速度為320~400 mm/s,激光功率為200~300W時,以及掃描速度為80~400 mm/s,激光功率為140~180W時合金中形成了不規則孔隙,這是由于較低的能量輸入導致了不良的熔合。此外,當掃描速度低于80 mm/s,激光功率在200-300W范圍內時,可以發現一些大的圓形孔隙,這些可見的冶金缺陷可以解釋為過高的能量輸入導致輕質元素如Al、Mg和Li的汽化。當激光功率在140~180W范圍內,掃描速度在60~240 mm/s范圍內時,打印TiC改性的Al-Mg-Li合金呈現幾乎全致密狀態,如圖1 (a)中紅色實線框所示。相反,打印的Al-Mg-Li合金在所有激光參數區域均形成了微小的熱裂紋,如圖1 (b)所示,這在LPBF打印的鋁-銅合金中也發現了類似的現象。此外,相應的相對密度結果表明,TiC改性的Al-Mg-Li合金的相對密度高于Al-Mg-Li合金。TiC改性Al-Mg-Li合金在60~240 mm/s掃描速度和140~180W激光功率下的高相對密度為99.6 %,而Al-Mg-Li合金應用工藝參數下的最高相對密度為96.1 %,這是由于嚴重的裂紋形成所致。因此,TiC改性Al-Mg-Li合金在寬工藝參數窗口下具有良好的LPBF打印性和有效的抗裂性。
圖1 不同激光功率和掃描速度下制備的(a)合金和(b)TiC納米顆粒改性Al-Mg-Li合金的光學顯微圖和相對密度
采用ICP-OES研究了相同激光加工參數(掃描速度為240 mm/s,激光功率為140 W)下不同狀態Al-Mg-Li合金中Li元素的含量,如圖2所示。結果表明,打印的TiC改性Al-Mg-Li合金的鋰含量與原料粉相似。而打印的Al-Mg-Li合金中的鋰含量顯著降低到0.87 wt.%。這是因為Li元素(342℃)的沸點比其他元素的沸點低很多,導致了高能激光束處理中Li的燒蝕。顯然,與Al-Mg-Li合金粉末和TiC改性Al-Mg-Li合金粉末中的鋰含量(1.4 wt.%)相比,TiC顯著降低了Al-Mg-Li合金中Li的損失率,降低了56.5 %,明顯低于任何LPBF加工鋁鋰合金的研究[13-15]。因此,納米陶瓷顆粒改性是防止LPBF過程中鋰元素損失的有效方法。
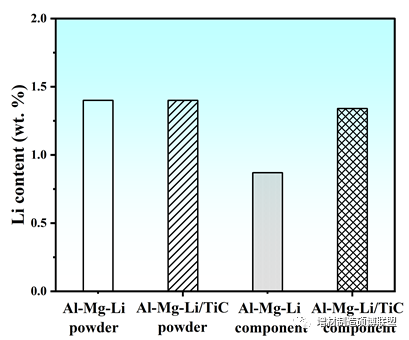
圖2 Al-Mg-Li合金粉末、TiC納米顆粒改性Al-Mg-Li合金粉末、LPBF打印Al-Mg-Li合金和TiC納米顆粒改性Al-Mg-Li合金中的Li含量選擇240mm/s的LPBF掃描速度和140W激光功率下制備的Al-Mg-Li合金和TiC改性Al-Mg-Li合金試樣進行掃描電鏡和EBSD表征,典型的掃描電鏡和EBSD微觀結構特征如圖3所示。如圖3 (a)所示,Al-Mg-Li合金呈現出LPBF打印鋁合金的典型熔體池(MP)形態,即沿建筑方向(BD)的“扇形”形態。注意到,由于LPBF過程中熱梯度與凝固速率的比值較高,MP內的微觀結構均由粗長的柱狀晶粒組成,如圖3 (b)所示。如圖3 (c)所示,LPBF打印的Al-Mg-Li合金由具有<001>優先生長取向的柱狀晶粒組成。此外,柱狀晶間處可見熱裂紋。相反,TiC改性Al-Mg-Li合金的微觀結構表現為隨機取向的全等軸晶粒,如圖3(d-f)所示。這表明TiC納米顆粒的加入有效地消除了熱裂紋,并對Al-Mg-Li合金的柱狀向等軸晶粒轉變起到了關鍵作用。
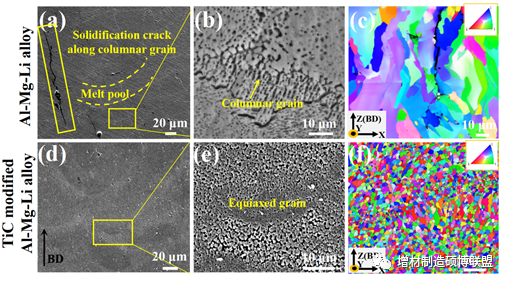
圖3 LPBF打印的(a-c)Al-Mg-Li合金和(d-f)TiC納米顆粒改性的Al-Mg-Li合金的掃描電鏡圖像和EBSD IPF圖像據統計,柱狀晶粒的平均粒徑為173 ±34µm(圖4 (a)),說明柱狀晶粒在多層上沿BD外延生長(層厚設為30µm)。等軸晶粒的平均粒徑約為1.5 ±0.9 μm,比打印的Al-Mg-Li合金細化了兩個數量級,如圖4 (b)所示。根據Liu等[22]和Qu等[24]的文獻,在TiC納米顆粒增強Al-Mg-Cu合金和6061合金中也發現了類似的晶粒細化現象,但這些合金的粒徑在2.22μm~10.6μm之間,大于本研究中獲得的1.5 μm的晶粒尺寸。這種期望的全等軸晶粒微觀結構與Sc或Zr改性LPBF Al合金[29]中發現的等軸/柱狀雙峰結構有顯著的區別,具有顯著的力學性能。
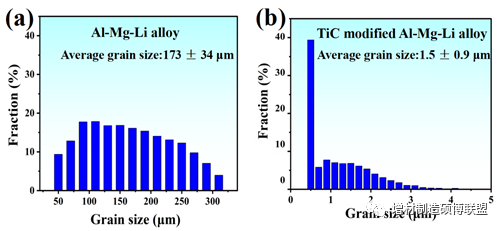
圖4 打印的(a)Al-Mg-Li合金和(b) TiC改性Al-Mg-Li合金的粒徑分布圖5顯示了描述材料內部微觀彈性應變的平均取向偏差(KAM)圖。在LPBF打印的Al-Mg-Li合金中,應變沿低角度取向偏差的柱狀晶界集中,如圖5 (a)和(c)所示。而打印的TiC改性Al-Mg-Li合金的KAM圖像應變分布均勻,平均局部取向偏差略有下降(圖5 (b)和(d))。結果表明,TiC納米顆粒的加入顯著降低了Al-Mg-Li合金的殘余應力。
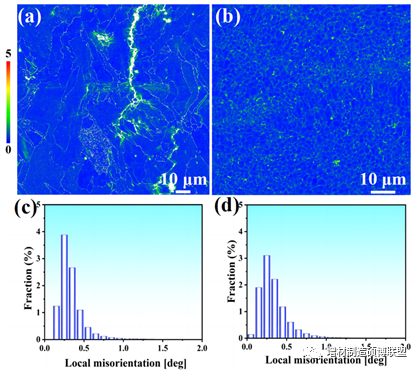
圖5(a、c)Al-Mg-Li合金和(b、d) TiC改性Al-Mg-Li合金的KAM圖和局部取向偏差分布通過透射電鏡分析研究了TiC改性的Al-Mg-Li合金的微觀結構和相演化,結果如圖6所示。如圖6 (a)所示,在TiC改性的Al-Mg-Li合金中,清晰可見尺寸為1-2 μm的精細等軸晶粒結構,與SEM和EBSD結果一致(圖4 (e)和(f))。觀察到一些明亮的立方沉淀物,尺寸為260 nm。根據圖6 (a)對應的STEM-EDX結果,立方沉淀物在Ti和Al中富集。圖6 (b)中的SAED圖樣分析證實,立方沉淀物為Al3Ti,具有L12超晶格結構。根據沉淀相統計,Al3Ti相分數為43.4%。Xia等人[17]研究報道,在LPBF(~106 K/s)的超高冷卻速率下,在LPBF過程中加入TiC納米顆粒會導致亞穩態L12-Al3Ti相的形成。L12-Al3Ti相分布在等軸晶粒內,其平均尺寸約為240 nm,這與我們的研究結果是一致的。此外,α-Al/Al3Ti界面的HRTEM圖像顯示,Al3Ti相的晶格失配為0.84%(失配定義為(dAl3Ti-dAl)/dAl3Ti),如圖6 (c)中黃色框區域對應的(d)所示。
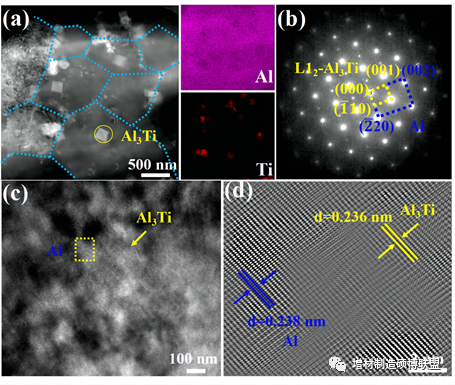
圖6 TiC改性的Al-Mg-Li合金的TEM圖:(a)高角環形暗場(HAADF)圖像和EDX元素映射;(b) Al3Ti的SAED圖;(c) Al3Ti的HRTEM圖像;(d) (c)中黃色區域對應的α-Al/Al3Ti界面的HRTEM圖像聚焦于晶界上板狀粒子的高倍透射電鏡圖像如圖7 (a)所示。圖7 (b)中相應的SAED圖顯示該粒子是由Al3Ti和TiC相組成的復合結構。根據EDX圖和圖7 (c)中的橫截面線掃描結果,元素在粒子中的分布表明,Al和Ti元素由內到外產生了明顯的擴散現象。另外,通過對圖7 (a)中A區域的高分辨率透射電鏡圖像分析,在α-Al基質(200)和TiC(111)之間有一個厚度為6 nm的Al3Ti(111)中間層,如圖7 (d)所示。Al3Ti中間層的存在表明在LPBF過程中,TiC納米顆粒表面發生了TiC與Al3Ti的反應。同時,在Al基體中,TiC與Al3Ti的晶格錯配(晶格錯配為6.9 %)可以顯著減少原TiC與Al基體的晶格錯配(18.8%)。此外,有趣的是,在粒子中心發現了明顯的堆積斷層(SFs),這可能是由于Al3Ti相在TiC納米顆粒上外延生長所致[31-33],如圖7 (a)中B區域對應的圖7 (e)所示。
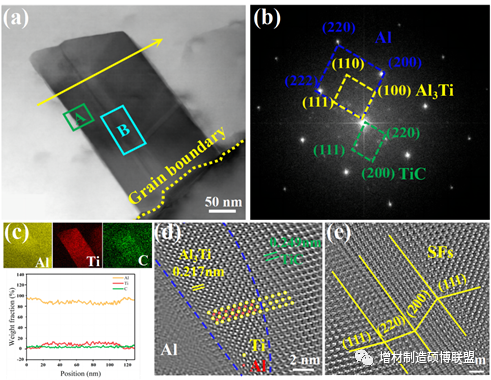
圖7 (a)TiC的高角環形暗場(HAADF)圖;(b)相應的SAED圖;(c)相應的EDX元素映射和TiC納米顆粒上的元素分布;(d) (a)中A區TiC-Al界面的高分辨率透射電鏡圖;(e) (a)中B區SFs的HRTEM圖LPBF加工過的Al-Mg-Li合金和TiC改性的Al-Mg-Li合金的力學性能如圖8所示。如圖8(a)所示,由于熱裂紋的存在,LPBF加工的Al-Mg-Li合金的極限抗拉強度(UTS)為63 ± 4 MPa,屈服強度(YS)為56 ± 3 MPa,延伸率為1.3 % ± 0.2 %。而TiC改性的Al-Mg-Li合金的UTS顯著高于343 ± 6 MPa,YS為340 ± 6 MPa,延伸率為9.3 ± 1.6 %。TiC改性Al-Mg-Li合金的強度和延伸率分別比Al-Mg-Li合金提高了約440 %和610 %。在TiC改性的Al-Mg-Li合金的加工硬化速率曲線中出現了連續的應變硬化轉變,這與均勻塑性區域的不穩定性相吻合,如圖8(b)中可見的鋸齒所示,這可以歸因于明顯的柱狀到等軸晶粒轉變引起的位錯和大晶界密度之間的高相互作用。在TiC納米顆粒上原位形成的Al3Ti層進一步改善了晶格結構,實現了良好的伸長率和SFs的形成誘導的加工硬化。值得注意的是,TiC改性的Al-Mg-Li合金的比強度優于之前報道的AM制造的Al-Li合金[15, 34-37],如圖8 (c)所示。TiC納米顆粒對Al-Mg-Li合金的改性為在LPBF過程中開發具有較高比強度、較高鋰含量的Al-Mg-Li合金提供了廣闊的機會空間。
圖8 LPBF加工的Al-Mg-Li合金和TiC改性Al-Mg-Li合金的(a)應力-應變曲線和(b)加工硬化率曲線;TiC改性Al-Mg-Li合金與之前報道的其他鋁鋰合金的比強度比較
如圖3中的ICP-OES結果所示,在Al-Mg-Li合金中加入TiC納米顆粒顯著降低了Li的損失率。由于Li元素(342℃)的沸點遠低于Al(2327℃),致使Li元素在Al-Mg-Li合金的高能激光加工過程中容易蒸發,最終造成Li元素的燒蝕。因此,Li元素的損失主要發生在金屬汽化過程中。在本研究中,加入TiC納米顆粒可以顯著提高鋁合金液體的粘度[24]。由于粘度的增加,所產生的粘性應力需要更少的液體表面變形來平衡反沖壓力。反沖壓力是由蒸汽射流推動熔體表面向下形成蒸汽凹陷而產生的。因此,鋁合金液體粘度的增加抑制了金屬的汽化。因此,Li含量在熔體池中得到了很好的固結。另一方面,蒸汽噴射流的高速向上的蒸汽流將液滴噴射出去,形成液體飛濺[38]。如圖9 (a)和(b)所示,TiC改性的Al-Mg-Li合金的液體濺射明顯降低。液體飛濺通常是指金屬蒸汽凹陷邊緣周圍熔體池的液體破裂。液體破裂是由流體動量引起的慣性壓力克服了表面張力引起的毛細管壓力引起的,類似于水的飛濺[39]。隨著金屬汽化量的降低,液體動量突然增加的驅動力也減小。因此,由液體破裂產生的液體飛濺顯著減少。此外,當激光熔化粉末時,液滴表面的納米顆粒也會產生毛細管壓力勢壘。這種毛細管壓力勢壘能夠在液滴碰撞時阻礙液滴的聚結。毛細管壓力勢壘可以用以下公式[40]來估計:
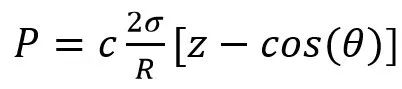
其中σ為液體鋁表面張力的(1100 mNm-1),R為顆粒半徑,θ為鋁在TiC上的接觸角,取51°[41],c為與飛濺表面納米顆粒覆蓋分數的相關常數(θ<90°,z為2.73),z為與兩個液體飛濺表面之間納米顆粒數相關的常數(θ<90°,z為0.633)。LPBF制備的TiC改性Al-Mg-Li合金的毛細管壓力勢壘為1.2 MPa,明顯比5.7×10-2MPa的慣性壓力高2個數量級,即從熔融溫度到526 K以上促進熔融直接液液接觸的動能,如圖9 (c)所示。結果表明,這種高壓屏障足以防止碰撞過程中液滴聚結,從而避免產生大的液濺。因此,可以得出結論,TiC的引入大大降低了金屬汽化,消除了金屬汽化產生的液體飛濺物,減少了鋁合金在LPBF加工過程中的鋰損失。
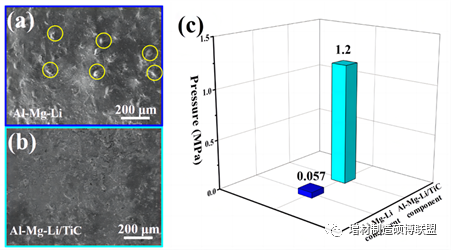
圖9 打印的(a)Al-Mg-Li合金和(b) TiC改性Al-Mg-Li合金的頂表面SEM圖;(c)慣性壓力,即促進打印Al-Mg-Li合金液滴聚結的直接液-液接觸的動能,以及TiC改性Al-Mg-Li合金的毛細管壓力勢壘熱裂紋是AM工藝中高強度鋁合金常見的問題,是導致材料打印性差的直接原因。一般來說,LPBF成形的熱裂紋是由冶金力和機械力的共同作用造成的[42]。LPBF加工的Al-Mg-Li合金的凝固行為和微觀結構演變的相關示意圖如圖10 (a)所示。當凝固過程中半固態溫度范圍較寬時,可引起冶金驅動力,導致長通道的樹突間區域,因此,由于液相不及時供給凝固收縮而造成裂紋的形成。另一方面,在LPBF成形過程中,較大的熱梯度和超高的冷卻速率通常會導致殘余應力的產生,即機械驅動力,這也導致了熱裂紋的形成。如圖3(b-c)所示,LPBF固有的溫度梯度與凝固速率的高比值導致Al-Mg-Li合金中出現粗柱狀晶粒,由于半固體態柱狀晶粒的適應應變能力低,因此粗柱狀晶粒之間形成熱裂紋[43]。相比之下,在LPBF成形的Al-Mg-Li合金中加入TiC納米顆粒,通過原位形成的Al3Ti誘導了大量的晶粒細化,有效地抑制了裂紋形成,如圖10 (b)所示,這是由于LPBF成形TiC改性Al-Mg-Li合金中細等軸晶粒的應變容納能力比LPBF成形Al-Mg-Li合金中的粗柱狀晶的應變容納能力更強(圖3 (c)和(f))。此外,在Al-Mg-Li合金中加入TiC,顯著降低了LPBF成形的殘余應力,如圖5 (b)和(d)所示。因此,我們可以合理地認為添加TiC可以通過減少細等軸晶粒之間的液相存在和減輕熱收縮引起的殘余應力來消除熱裂紋。
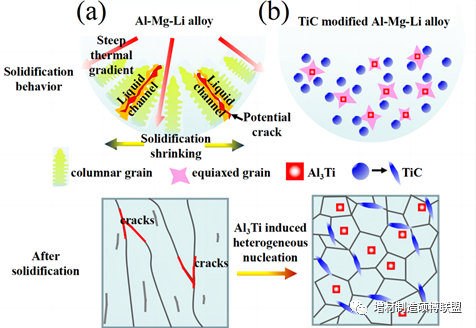
圖10 LPBF加工的(a)Al-Mg-Li合金和(b) TiC改性Al-Mg-Li合金的凝固行為和微觀組織演變示意圖此外,在LPBF加工的TiC改性Al-Mg-Li合金晶粒中發現了立方L12-Al3Ti沉淀相,如圖7所示。圖8 (c)中TiC納米顆粒上的Al和Ti元素分布和圖8 (d)中α-Al與TiC之間形成的Al3Ti相證明Al原位與TiC反應形成Al3Ti。因此,考慮到鋁合金LPBF過程中熔體池溫度超過2000℃時,該反應的標準吉布斯自由能差為顯著負值,具有較強的反應趨勢。根據熱力學計算結果(圖11),Al3Ti相在Al結晶前沉析,說明TiC的加入改變了Al相的凝固順序。在TiC上形成的Al3Ti作為隨后固化Al相的直接晶粒細化劑。因此,由于Al3Ti沉淀相與α-Al相同的晶格匹配,有效地促進了α-Al的非均勻成核。
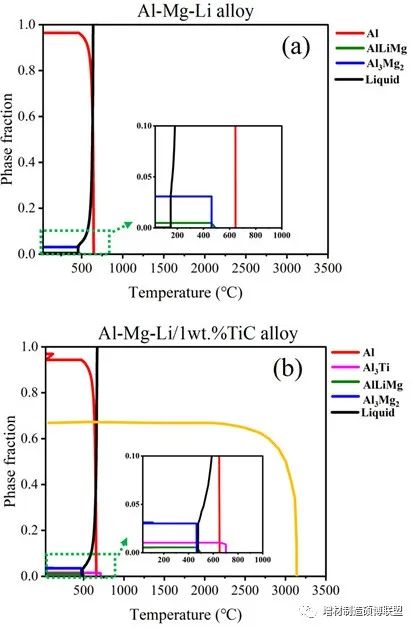
圖11 (a)Al-Mg-Li合金和(b) 1 wt.%TiC改性l-Mg-Li合金的相圖
如圖3 (d)和(f)所示,LPBF成形的TiC改性Al-Mg-Li合金呈現出完整的等軸晶粒結構,與打印的Al-Mg-Li合金的晶粒明顯不同。在力學性能方面,LPBF成形的TiC改性Al-Mg-Li合金的強度和伸長率分別為340 MPa和9.3 %,比強度為150 MPa,在所有LPBF打印Al-Mg-Li合金中具有優異的性能。LPBF成形的TiC改性Al-Mg-Li合金力學性能的提高主要是由于裂紋的消除和全等軸晶粒的形成。如圖4 (a)和(b)所示,LPBF成形的TiC改性Al-Mg-Li合金的平均粒徑比Al-Mg-Li合金的平均粒徑低兩個數量級。因此,引入了更多的單位面積晶界,通過有效抑制晶界對位錯運動的影響,大大提高了材料的晶界增強(σGB)。可以根據經典的Hall-Petch公式[45]給出,如下所示:
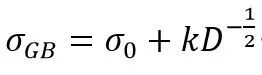
其中,σ0為晶格對位錯運動的固有阻力(約20 MPa),k為鋁合金的Hall-Petch常數(0.17 MN/m3/2)。D為晶粒尺寸。因此,計算得到的LPBF打印TiC改性Al-Mg-Li合金的晶界強度為158 MPa,如圖12所示,由于超細的等軸晶粒,其晶界強度高于其他LPBF打印鋁合金的晶界強度。這與文獻數據中的擬合線(黃色實線)[11, 13, 14, 24, 42]相一致。隨著晶粒尺寸的減小,TiC改性Al-Mg-Li合金的晶界強度在1.5µm時達到最大值,為158 MPa,Al-Mg-Li合金的晶界強度在173µm下降低到32 MPa。這些數據與σGB-1/√D外推的Hall-Petch線(藍色虛線)相一致。LPBF打印TiC改性Al-Mg-Li合金的明顯硬化與晶粒尺寸相當的LPBF打印鋁合金的硬化是一致的,這源于在較細粒徑下從位錯滑移到晶界強化過程的塑性變形機制。圖12 LPBF打印鋁合金的晶界強度隨粒徑尺寸的變化[11, 13, 14, 24, 42];黃色實線是文獻數據的擬合線;藍色虛線是σGB-1/√D外推的Hall Petch曲線圖;R2值代表模擬的測量指標此外,如圖6 (a)所示,Al3Ti相在LPBF成形TiC改性的Al-Mg-Li合金的晶粒內或晶界處均勻分布,在拉伸變形過程中釘扎位錯和晶界運動中起著關鍵作用。這有助于增強奧羅萬強化機制,提高了材料的力學性能。根據圖S1中的EDX-映射結果,Mg主要固溶于鋁基中,從而提供了固溶強化。因此,材料的整體屈服強度可以通過對個別加強機制的所有貢獻的總和來評估。LPBF成形的TiC改性Al-Mg-Li合金的強度增量是晶界強化、奧萬羅強化和固溶強化的代數和。此外,如圖7 (d)所示,新形成的Al3Ti相與α-Al的晶格失配低于TiC與α-Al的晶格失配,這不僅減少了原子排列失配,提高了成核效率,還提高了粘接強度,改善了延性。
特別地,發現在LPBF制備的TiC改性Al-Mg-Li合金中形成的堆疊斷層(SFs)很有趣(圖7 (e))。由于晶界的高能量和高原子活性,新的Al3Ti相很容易在晶界上的TiC納米顆粒上優先成核(圖7 (d))。而附著在TiC納米顆粒上的Al3Ti相的外延生長導致了TiC納米顆粒中產生SFs(圖7 (e)),這也在AlTi和Ag層之間觀察到了相似的現象。因此,形成的SFs扭曲了晶格,從而阻礙了位錯發射,導致了顯著的加工硬化。