0·前言
目前摩托車行業油箱涂裝前處理仍采用標準的三元鋅系磷化工藝,該工藝是被多行業長期驗證的傳統工藝,具備工藝成熟穩定、適用面廣等優點。但存在著影響人體健康的重金屬物質及致癌的亞硝酸鹽,生產用能源消耗較高,且不可避免地產生沉渣對系統管路及噴咀造成堵塞,設備維護成本高,同時排放大量含磷、鎳廢水其處理費用不低,另處理鋁合金件需特殊工藝條件。為適應日趨嚴格的環保政策,日趨嚴格的職業健康法規,不斷降低企業制造成本的同時,發揮企業的社會責任。因此尋求“低毒性、低污染、低能耗、低成本、高效率”的新型金屬涂裝前處理工藝加以應用或作技術儲備成為行業的必然趨勢。作者在多家硅烷生產商提供材料作工藝實驗的基礎上選擇了XB-108G1作生產投入,其應用情況總結于此供同行交流指正。
1·硅烷處理成膜機理
第一步:硅烷偶聯劑分子一端硅酸酯水解形成硅醇
X-Si(OR)n+nH2O→X-Si(OH)n+nROH
第二步:硅醇與金屬基體表面的MeOH反應生成Si-O-Me共價鍵
-SiOH+Me一OH→Me-O-Si+H2O
第三步:硅醇在與金屬表面偶聯交叉結合的同時(當然分子另一端要與涂料形成穩定的共價鍵)縮聚形成具有Si-O-Si三維網狀結構的硅烷膜。
-SiOH+HO-Si→-Si-O-Si-+H2O
2·試驗
2.1試驗材料
試板:150mm×70mm×0.8mm的冷扎鋼板、熱扎板。
油箱:125ml排量摩托車外置油箱。
磷化處理設備:現懸掛輸送式油箱噴淋磷化處理生產線。
硅烷處理設備:人工浸漬式塑料槽(800mm×600mm×600mm)。
涂料:現正常生產加工油箱用涂料(環氧酯灰色底漆+丙烯酸鋁粉中涂漆+丙烯酸透明紅面漆+雙組份聚氨酯清漆)。
2.2磷化處理液配制
調整現油箱噴淋磷化生產線槽液在正常工藝范圍內(總酸:20-30點,游離酸1.5-2.5點,促進劑1-2ml)。
2.3硅烷處理液配制
測定處理槽需配刻度容積,加一定量的純水(可自來水),按需配容積3%左右用量加入XB-108G1硅烷處理液,加水到規定刻度,攪拌均勻,檢測槽液指標(PH值:4-5,電導率:小于1800μs/cm)即可。
2.4涂裝工藝流程
噴淋磷化處理:熱水洗--預脫脂(60±5℃)--脫脂(60±5℃)--水洗--水洗--表調--磷化(40±5℃)--水洗--水洗--純水洗--純水直噴。
浸漬硅烷處理:脫脂(60±5℃)--水洗--純水洗--硅烷(常溫)--水洗--純水洗。
噴涂工藝:前處理--脫水烘干(120℃×20min)--擦凈除塵--自動靜電底中面涂及補正--面漆烘干(130℃×30min)--轉移--擦凈除塵--自動靜電清漆及補正--烘干(120℃×30min)。
2.5性能對比檢測
3·結果與討論
3.1涂膜附著力
1)硅烷或磷化前處理的油箱或試板噴涂底漆后單一涂層附著力合格(0~1級),且經過2個月的測試未出現失效的情況。
2)硅烷前處理的油箱或試板噴涂底漆+(中涂)+面涂+清漆后復合涂層附著力曾出現層間不合格(≤2級、但磷化≤1級),理論上硅烷處理的好處在于提升附著力,它把底層抓得太牢而出現底與中涂間附著力差,實際也證明了這一點。
3)針對第2)項經與涂料、前處理材料商共同探討后認為問題出在底漆上,必須改善底漆的柔韌性。經兩次調整底漆,同時用其它廠家底漆驗證后測試附著力合格(0~1級之間)。因此硅烷前處理的投入可在涂料配套過程中作適當調整解決復合涂層的附著力問題。
3.2涂膜耐蝕性
1)硅烷或磷化前處理的冷扎板噴漆后(底漆+面漆+清漆)涂膜性能測試耐水性、耐汽油性(93#、E20)、耐酸堿、耐濕熱、耐蝕性(中性鹽霧)按企業標準要求合格,但針對鹽霧時間192h的基礎上再延長(240h、288h)后磷化前處理的試板顯得差一些。實際上這也更證明了硅烷膜較磷化膜與底漆的附著力提升相關。
2)硅烷或磷化前處理的油箱噴漆后(底漆+中涂+面涂+清漆)涂膜性能測試中性鹽霧試驗(192h、240h、288h)合格。與試板情況比較說明中性鹽霧與涂層厚度有關。
3)硅烷或磷化前處理的熱扎板噴漆后(底漆+面漆+清漆)涂膜中性鹽霧按標準192h合格。從檢測結果看240h基本合格,但288h硅烷顯得差一些,這與熱扎板材質較冷扎板而言脫脂工序對后處理的影響有關、同時相對油箱則與漆膜厚度也有關而未表現出來。
3.3有害物分析
1)從表5可以看出硅烷處理工藝材料本身總磷、總鎳、總砷三項指標均遠遠低于現磷化處理。氨氮指標略高于現磷化,但仍低于《綜合污水排放標準》一級標準值。
2)采用硅烷工藝生產,其處理槽液要排放廢水,從表5看均低于《綜合污水排放標準》一級標準值,其對公司整個廢水處理系統無任何影響。
3.4制造成本分析
1)硅烷工藝常溫處理,相對磷化不使用熱交換泵、蒸汽、磷化除渣機等,從而節約能耗。經近10個月的生產驗證統計每平米節能0.64元/m2(磷化用蒸汽331kg/h、電15.2Kwh,硅烷不用蒸汽、電10.8Kwh)。
2)硅烷取代磷化工藝后直接材料成本經近10個月的生產驗證統計每平米0.434元/m2(磷化用脫脂劑0.327元/m2、表調劑0.134元/m2、磷化液1.172元/m2,而硅烷用脫脂劑0.318元/m2、硅烷液0.881元/m2)。
4·結語
在現有油箱噴淋磷化處理線工藝基礎上對工藝槽及管路清潔后切換為硅烷處理工藝可行。
實際生產驗證油箱底漆適當調整后復合涂層附著力提升,其它理化性能滿足企業標準要求。
因硅烷相對磷化采用了無磷、無鎳,生產過程基本無沉渣、常溫處理、無須使用致癌物亞硝酸鹽促進劑的處理工藝。不僅降低了能源消耗,生產成本下降,而且減少了有害物質排放,社會環境效益遠遠大于經濟效益。
生產管理簡單,操作方便。但應注意對硅烷槽液的過濾處理維護作關注。
總之,硅烷工藝通過油箱涂裝線的投入切換正常生產品質符合要求,系統設備維護及生產管理控制簡單,廢水排放更加環保且能源及材料費用降低。
免責聲明:本網站所轉載的文字、圖片與視頻資料版權歸原創作者所有,如果涉及侵權,請第一時間聯系本網刪除。
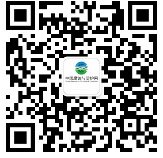
官方微信
《腐蝕與防護網電子期刊》征訂啟事
- 投稿聯系:編輯部
- 電話:010-62316606-806
- 郵箱:fsfhzy666@163.com
- 腐蝕與防護網官方QQ群:140808414