隨著我國汽車行業不斷地發展以及汽車保有量的增加,汽車在我國不同自然大氣環境條件下長時間服役均會產生不同程度的腐蝕,尤其在海洋氣候環境下腐蝕更為突出[1]。為了預測和評估汽車材料的服役壽命,科研工作者系統地研究了各種汽車常用金屬板材在不同大氣環境及加速條件下的腐蝕行為[2,3,4]。
目前國內外對于典型汽車金屬材料的耐蝕性研究,均主要采用室外和室內兩種腐蝕實驗方法,室外實驗主要采用大氣暴曬和路面實驗,室內加速實驗方法主要采用中性鹽霧實驗和循環鹽霧實驗[5,6]。姚望等[7]采用中性鹽霧實驗方法研究了超深沖鋼DC06的耐蝕性,結果表明隨實驗時間延長,試樣腐蝕速率總體上呈增加趨勢,表面腐蝕產物對鋼基體的保護作用不明顯。王振堯等[8]采用大氣暴露腐蝕與室內模擬加速實驗兩種方法研究了鋼在室內、外腐蝕行為的相關性,結果表明4種不同成分的鋼種在室內、外腐蝕相關性均較好,同時表明了加速倍率隨時間而發生變化。Zhang等[9]采用大氣暴曬方法對比研究了鋁合金2024-T4試樣表面和截面的腐蝕行為,結果表明隨著暴曬時間的延長,試樣表面發生嚴重的剝落腐蝕且表面和截面均存在點蝕和晶間腐蝕。王旭等[10]采用室內加速實驗模擬Q235碳鋼在污染海洋大氣環境下的腐蝕行為,結果表明采用周浸加速腐蝕方法與室外污染海洋大氣的實際情況具有良好的相關性,同時建立起合理的腐蝕壽命預測模型。
循環加速實驗采用的方法比較多,德系車企主要采用福特467標準,大眾汽車主要采用PV1210,日系汽車主要采用日產汽車M0158標準。由于我國汽車行業對國外循環腐蝕標準的研究較少,前期數據積累較少,循環腐蝕標準實驗時間與我國自然環境服役時間的對應關系尚不明確。本論文以汽車常用金屬材料DP600雙相鋼為研究對象,采用中性鹽霧實驗標準(GB/T 10125)與日產汽車循環腐蝕標準M0158(一),系統研究其腐蝕行為及其差異,同時建立腐蝕動力學規律,為汽車行業及相關企業選材和制定標準提供參考。
1 實驗材料及方法
實驗材料為DP600雙相鋼,其化學成分和金相組織分別見表1和圖1。采用精密線切割機床切割試樣,鹽霧實驗試樣規格為150 mm×75 mm×3 mm,電化學試樣規格為10 mm×10 mm×3 mm。實驗前,采用240#、400#、800#和1000#砂紙打磨試樣,用去離子水沖洗、無水乙醇脫水后并吹風機冷風吹干,靜置干燥器中24 h后對其進行稱重 (精確至0.1 mg)。
圖1 DP600雙相鋼軋向截面和橫向截面的金相組織
DP600鋼為鐵素體和馬氏體雙相鋼[11],其縱截面與橫截面金相組織比較類似,其中小島狀白色多邊形為鐵素體,呈等軸狀,沿軋向分布;灰黑色的為低碳馬氏體,馬氏體被鐵素體包圍,馬氏體呈島狀均勻分布。
中性鹽霧(NSS)實驗依據國標GB/T 10125-2012進行,實驗設備為鹽霧實驗箱(型號為SC/YWX-90);循環鹽霧腐蝕實驗(CCT)依據日產工程循環鹽霧腐蝕標準(M0158標準(一))進行,實驗設備為多功能循環鹽霧實驗箱(型號為Q-FOG LF-8165-TM CCT)。中性鹽霧實驗和循環鹽霧實驗周期均為120、240、480、720、960、1200 h,每組4塊平行樣,3塊用于失重分析,一塊用于形貌和腐蝕產物分析。實驗完成后,根據國標GB/T 16545-2015《金屬和合金的腐蝕 腐蝕試樣上腐蝕產物的清除》,選用除銹液成分為500 mL鹽酸+500 mL蒸餾水+3.5 g六次甲基四胺對試樣表面進行除銹處理,除銹完成后按照實驗前試樣處理步驟,記錄除銹后重量。
采用Nova Nano SEM400型場發射掃描電鏡(SEM)觀察試樣的微觀形貌。通過Bruker D8 Advance X射線衍射儀(XRD)分析試樣腐蝕產物相組成。采用三電極體系進行EIS測試,DP600鋼試樣為工作電極,對電極為鉑(Pt)電極,參比電極為飽和甘汞電極。電解液為3.5%(質量分數)NaCl溶液,掃描頻率為105~10-1 Hz,最后采用ZSimpwin軟件進行等效電路擬合。
2 結果與討論
2.1 腐蝕動力學
圖2為DP600雙相鋼在兩種加速實驗條件下的腐蝕失重及腐蝕速率曲線。在兩種加速實驗條件下,試樣的初期腐蝕失重相差不大,但隨著腐蝕時間的延長,腐蝕失重差距逐步擴大,且CCT試樣腐蝕失重均大于NSS腐蝕試樣,在1200 h時失重值相差最大為1009.98 g·m-2。在實驗前期(120 h),腐蝕速率相差不大;在120 ~ 480 h之間時,腐蝕速率不斷增加,且CCT試樣腐蝕速率變化遠大于NSS試樣的,說明其腐蝕程度更嚴重;到480 h時,它們的腐蝕速率均達到最大值分別為1.89 g·m-2·h-1(NSS實驗)和2.72 g·m-2·h-1(CCT);960 h后,由于銹層厚度的增加對Cl—的滲透起阻礙作用,導致腐蝕速率降低[12],但CCT試樣腐蝕速率下降明顯比NSS試樣的快;1200 h后,CCT試樣腐蝕速率變化較為平緩,而NSS試樣腐蝕速率下降較快,說明在NSS實驗下試樣表面銹層對腐蝕進程的阻礙作用進一步加強,此時兩種加速實驗的腐蝕速率差達到最大值0.84 g·m-2·h-1。
圖2 DP600雙相鋼在兩種加速實驗條件下的腐蝕失重及腐蝕速率變化曲線
通過圖2b可知,試樣在兩種加速實驗下的腐蝕速率呈先上升后下降的趨勢,因此對圖2a中腐蝕失重數據根據如下公式(1)進行冪指數分段擬合,相關擬合參數見表2。
ΔW=Atn(1)
其中,ΔW是失重量(g·m-2),t是實驗時間(h),A和n是與材料和環境有關的系數,R為回歸系數。
由R2值可以看出,腐蝕失重與時間的關系基本符合冪指數規則;由n值及整體曲線走勢可看出,在480 h前試樣腐蝕速率較大,之后腐蝕速率逐步降低,說明試樣腐蝕程度隨實驗進行先加劇后逐漸降低。
2.2 形貌分析
2.2.1 腐蝕產物微觀形貌
圖3為DP600雙相鋼在不同實驗周期后的腐蝕產物微觀形貌。試樣經NSS實驗240 h后,腐蝕產物呈細小且密集的針尖狀;720 h后,腐蝕產物疏松多孔,且形狀向團簇針尖狀轉變;1200 h后,試樣表面腐蝕產物轉變為團簇針尖狀和少量棉絮狀。試樣經CCT腐蝕240 h后,腐蝕產物為明顯的層片狀;720 h后轉變為團簇針尖狀;但1200 h后腐蝕產物基本為棉絮狀。總體上,隨著實驗周期的延長,兩種加速條件下試樣腐蝕產物形貌基本由針尖狀向團簇針尖狀和棉絮狀轉變,且NSS實驗條件下試樣腐蝕相對較輕。
圖3 DP600雙相鋼在兩種加速腐蝕實驗后的表面形貌
2.2.2 截面形貌
將NSS實驗條件下各周期腐蝕試樣進行斷面及線掃描分析,在實驗240 h后,試樣截面銹層較為致密,厚度為39.3 μm;720 h后,銹層厚度增加3倍左右,達到113 μm,厚度增加較大;1200 h后,銹層出現細小縱向裂紋(由于銹層本身較為疏松,縱向裂紋亦可能是在制樣過程中形成的),表面致密度變低,銹層厚度相比720 h的增加一倍左右,為220 μm,銹層厚度變化總體趨勢為先快后慢。
通過EDS對試樣銹層截面分別進行點和線掃描分析得出,銹層主要成分為Fe和O元素,隨著腐蝕時間的延長,主要成分不變。實驗240 h時,銹層中Fe元素分布較為均勻,而O元素則從外到內逐步降低,說明腐蝕程度從外到內逐步減弱;720 h后,銹層中間區域Fe和O含量高于兩邊區域;到1200 h后,Fe和O總體分布較為均勻,僅局部區域出現較大波動,這可能是由于該區域腐蝕嚴重,同時中間致密銹層阻礙氧和水分子的滲透所致。
將CCT條件下各周期腐蝕試樣進行銹層截面分析,通過點及線掃描得出,試樣腐蝕240 h后,銹層斷面較為疏松,中間有明顯的銹蝕坑和裂紋,銹層厚度為72.4 μm;720 h后,銹層有明顯裂紋,銹層厚度相比240 h的增加一倍左右,達到143 μm;1200 h后,銹層厚度相比720 h的也增加接近一倍左右,為275 μm,銹層厚度總體變化趨勢較平緩,但厚度值較大。對試樣截面進行線掃描分析得出,銹層主要成分為Fe和O且分布較均勻;但在720 h后,Fe和O元素強度均有所降低,說明試樣在該周期下腐蝕程度增加,隨著腐蝕的進行,銹層主要成分不變。
2.3 腐蝕產物相組成
圖6為DP600雙相鋼在加速實驗1200 h后腐蝕產物的 XRD分析結果。DP600雙相鋼在NSS實驗條件下腐蝕產物主要為Fe3O4、α-FeOOH和γ-FeOOH,而在CCT條件下試樣表面的腐蝕產物成分為Fe3O4、α-FeOOH、γ-FeOOH和β-FeOOH。腐蝕產物中,α-FeOOH電化學穩定性良好,具有較弱的還原性,其含量的增加會抑制鋼的電化學反應進程,容易形成致密的氧化膜從而降低鋼的腐蝕速率[13,14]。而β-FeOOH和γ-FeOOH是不穩定的產物,具有較強還原性,它們的存在會促進Cl—在銹層中的擴散,降低銹層的保護,從而加速鋼基體的腐蝕[15]。
圖6 DP600雙相鋼在加速實驗1200 h后腐蝕產物的XRD譜
為了明晰碳鋼在不同加速實驗條件下銹層結構及腐蝕產物的變化,對銹層截面進行拉曼光譜分析,在每個試樣銹層的內、中、外區域分別取1、2和3點進行分析(圖4和圖5)。根據相關文獻和拉曼光譜特征峰對照[16,17,18],對圖7中各個特征峰進行標記,得出腐蝕產物在XRD分析基礎上還檢測出α-Fe2O3和無定形鐵氧化合物δ-FeOOH。在NSS實驗下,初期銹層各區域特征峰值差異不大,其中內部銹層α-FeOOH的特征峰398 cm-1偏移為外銹層δ-FeOOH的特征峰407 cm-1,中部銹層的δ-FeOOH的特征峰1320 cm-1偏移外銹層為Fe3O4的特征峰1325 cm-1,同時含有較強的Fe3O4特征峰。到720 h后,內銹層在δ-FeOOH的特征峰222 cm-1偏移外銹層α-FeOOH的特征峰213 cm-1,而402 cm-1的特征峰則消失;α-Fe2O3的特征峰286 cm-1偏移為外銹層γ-FeOOH的特征峰273 cm-1,同時內銹層中γ-FeOOH的特征峰1307 cm-1到外銹層時則消失。實驗后期,銹層內、中、外部的特征峰差異不大。說明實驗初期,銹層表面腐蝕活性較大,且內銹層開始產生較為明顯的穩定性產物α-FeOOH,到中后期腐蝕加劇的同時,腐蝕產物中無定形鐵氧化合物(δ-FeOOH)以及非穩態物質(γ-FeOOH和δ-FeOOH)逐步向穩態物質(α-FeOOH)轉變,對銹層保護作用逐步加強。
圖4 DP600雙相鋼試樣在NSS實驗后的截面形貌與EDS分析
圖5 DP600雙相鋼試樣在CCT實驗后的截面形貌與EDS分析
圖7 DP600鋼在兩種加速實驗條件下腐蝕不同時間后表面銹層的拉曼光譜
試樣在CCT條件下,腐蝕初期的中部銹層α-FeOOH的特征峰較弱,內部和外部銹層特征峰值較強。特別說明,本文中無法明確特征峰1440 cm-1對應的腐蝕產物。720 h后,銹層內部和中部特征峰相差不大,銹層外部Fe3O4的特征峰較強,分別為288 cm-1和1322 cm-1,非穩態物質的特征峰均較弱。隨著腐蝕時間的延長,后期外部銹層主要腐蝕產物的特征峰情況變化不大,但相比上個周期,Fe3O4的特征峰1322 cm-1轉變為γ-FeOOH的特征峰1307 cm-1。總體上可以看出,試樣在腐蝕后期,銹層內部仍有較高含量的非穩態物質(γ-FeOOH和β-FeOOH等),說明試樣后期腐蝕趨勢仍大,銹層對基體保護作用無NSS實驗條件下的明顯。
2.4 電化學交流阻抗譜
將在兩種加速實驗條件下腐蝕不同周期的試樣進行電化學交流阻抗分析。NSS實驗條件下(圖8a),DP600雙相鋼的Nyquist圖總體上表現為高頻區的小容抗弧和低頻區的大容抗弧,隨著腐蝕實驗的增長,容抗弧半徑不斷增加。CCT條件下(圖8b),前期試樣阻抗曲線表現為高頻區的小容抗弧和低頻區的大容抗弧;中期試樣阻抗曲線變為一條傾斜45°的直線,這是Warburg阻抗的典型特征,說明該試樣受到擴散過程的控制;到后期,試樣阻抗曲線則表現為低中高頻區的大容抗弧。
圖8 DP600雙相鋼在兩種加速實驗條件下腐蝕不同時間后的電化學阻抗譜
根據實驗結果可知,加速實驗下試樣腐蝕產物層較薄時,認為其前期對試樣的腐蝕進程阻礙作用不大,因此可以采用圖9a的等效電路圖進行阻抗擬合;當銹層厚度增加并且對試樣腐蝕進程影響較大時,表面形成的雙電層電阻作用明顯,則采用圖9b的等效電路圖進行阻抗擬合。其中,等效元件Rs表示溶液電阻;Qdl代表電極表面與溶液之間的雙層電容;Qr代表雙電層電阻;n為常相位角指數,表示彌散效應程度;Rr代表腐蝕產物膜電阻;Rct代表電荷轉移電阻;W代表Warburg半無限擴散阻抗。等效電路擬合結果如表3和表4所示。
圖9 DP600雙相鋼阻抗等效電路圖
擬合數據結果表明,NSS實驗下溶液電阻Rs值初期為3.391 Ω·cm2,但到后期增加至32.71 Ω·cm2,其變化趨勢為逐步增加。腐蝕產物膜電阻Rr的值在480 h時為91.25 Ω·cm2,到后期增加至298.8 Ω·cm2,說明試樣銹層逐步增厚。電荷轉移電阻Rct值在480 h前從351.5 Ω·cm2降低至188.5 Ω·cm2,之后隨實驗時間的延長又逐步增加至409 Ω·cm2。根據銹層電阻Rr以及電荷轉移電阻Rct的變化情況可知,隨著實驗時間的延長,前期銹層厚度的增加對銹層的腐蝕進程阻礙作用不明顯;480 h后Rr和Rct的值均不斷增加,說明銹層厚度的增加對試樣的腐蝕進程影響逐步增加,從而導致試樣的腐蝕速率降低。
擬合數據結果表明,CCT下溶液電阻Rs值初期為1.743 Ω·cm2,但到后期增加至18.32 Ω·cm2,其變化趨勢為逐步增加。腐蝕產物膜電阻Rr的值在120 h時為10.81 Ω·cm2,到后期膜電阻值增加至48.36 Ω·cm2,說明隨著腐蝕的進行,銹層厚度不斷增加。電荷轉移電阻Rct值在480 h前從196.8 Ω·cm2降低至93.5 Ω·cm2,說明該時間段腐蝕速率逐步增加;之后隨著腐蝕的進行,電阻值增加至125.4 Ω·cm2,后期變化趨于平緩,說明隨銹層厚度增加腐蝕速率降低,但下降并不明顯,這與腐蝕動力學結果一致。總體上,NSS實驗條件下,膜電阻Rr和電荷轉移電阻Rct均明顯高于CCT實驗的結果,說明NSS試樣銹層保護能力更強,腐蝕速率更低。
2.5 腐蝕動力學規律
建立一個有實用性的腐蝕速率模型,能夠有效地反應材料在加速實驗條件下腐蝕速率與時間的變化規律,進而能夠一定程度上反應其在自然環境下的腐蝕率情況。根據表2擬合相關參數可知,試樣在不同加速實驗下的不同階段的腐蝕動力學方程分別為:
式(7)~(10)建立了DP600雙相鋼在NSS和CCT實驗條件下腐蝕速率隨時間t的變化規律。根據(7)~(10)式,算出試樣在兩種加速實驗下腐蝕速率隨時間的變化趨勢,并與原始腐蝕速率數據進行對比分析 (圖10)。可以發現,通過(7)~(10)式所計算出的數據與試樣原始腐蝕速率數據初期誤差值較大,到中后期兩條線基本接近。也就是說,腐蝕速率擬合規律比較適用于加速腐蝕時間較長的實驗條件。
圖10 兩種加速實驗條件下試樣腐蝕速率擬合規律與測試數據的對比
2.6 腐蝕機制
DP600雙相鋼為鐵素體和等軸細小的馬氏體雙相鋼,晶粒較多,晶界占比較大,腐蝕接觸面積大。同時,鐵素體和馬氏體均為體心立方結構,但它們之間的結構存在較大差異,腐蝕電位也不同,易形成大量的微電池,從而加速材料的腐蝕過程[19]。
DP600雙相鋼在NSS實驗為連續性噴霧過程,溫度保持在35℃,濕度保持在95%以上(圖11),隨著實驗的進行實驗環境保持不變,試樣在較高的溫度和濕度條件下很容易發生腐蝕,其腐蝕反應機制如下:
圖11 兩種鹽霧加速實驗工作流程圖
而α-FeOOH為穩定性產物,其含量的增加又會進一步導致銹層致密度增加。腐蝕產物中γ-FeOOH、β-FeOOH和δ-FeOOH的還原性較強,使銹層中的陰極反應活性點增加,銹層與基體之間發生氧化還原反應,加速電化學反應,因此在腐蝕實驗前期,電荷轉移電阻Rct值逐步下降。實驗后期,隨著銹層內部被還原的銹層再次被空氣中的O2氧化生成較多的FeOOH,同時部分γ-FeOOH和δ-FeOOH轉換成為α-FeOOH,使陰極反應活性點減少,銹層越來越顯著地抑制鋼的陽極溶解,從而導致Rct值逐漸上升[24],這也說明NSS實驗條件下試樣銹層厚度的增加對腐蝕起到明顯的阻礙作用。
試樣在CCT過程中,初期為4 h的鹽霧階段,溫度為35℃,濕度在95%以上,溶液為5%NaCl,其腐蝕過程與前述中性鹽霧一致。之后為過渡階段,溫度逐步上升至60℃,濕度降至30%及以下,隨著溫度的升高,水分不斷蒸發,Cl—濃度增高及擴散作用加強,試樣腐蝕加劇。干燥持續時間為2 h,由于試樣表面水分因蒸發而非常少,試樣陰極過程受到抑制導致其腐蝕很輕微,同時導致銹層出現疏松多孔的特征。之后又為過渡階段,濕度上升至95%以上,溫度小幅度降低至50℃,Cl—與水分子在疏松多孔的腐蝕產物層中更易擴散,腐蝕加劇。最后為潮濕階段,持續時間為2 h,此時經干燥階段后沉積的鹽離子濃度升高的作用下發生潮解并釋放出Cl—。在潮解區,氧濃度逐步降低,發生Fe的陽極溶解反應(式(11)),在鹽粒子沉積附近發生氧的陰極還原反應(式(12)),導致腐蝕進一步加劇[24]。
在240~720 h和720~1200 h兩個時間段,銹層厚度增加均在一倍左右,變化差距不大,說明實驗后期隨銹層厚度的增加,銹層對基體的保護能力較弱。主要是因為在干濕交替條件下試樣腐蝕產物變的疏松多孔,Cl—在銹層中的催化和擴散作用均較強,導致銹層內部仍有較高濃度的Cl—。研究表明β-FeOOH在形成過程中,Cl—起到較強的催化作用(式(21)和式(22)),同時β-FeOOH的存在也促進了Cl—在銹層中的擴散,因為其形成需要Cl—和F—等元素來穩定其晶體的隧道結構[25,26],因此試樣銹層中有較高含量的β-FeOOH。而該產物為不穩定的產物,還原性較強,增加了陰極反應的活性區域,導致鋼基體腐蝕加劇。
從以上分析可知,試樣在CCT條件下的試樣腐蝕動力學變化,腐蝕產物微觀形貌及其轉變特征與NSS實驗的類似,反應機制也基本相同。但在相同周期下,其腐蝕失重和腐蝕速率均大于NSS實驗條件下的,腐蝕產物尺寸和密度也較大,主要是因為CCT條件下試樣經歷鹽霧、干燥和潮濕三個過程,而其中從鹽霧階段過渡到干燥階段以及干燥階段過渡到潮濕階段均加速材料的腐蝕進程;而NSS實驗條件下試樣一直處于單一的加速環境下,因此CCT下試樣腐蝕程度比NSS實驗條件下的更嚴重。
3 結論
(1) DP600雙相鋼在兩種鹽霧加速實驗過程中,前期腐蝕失重和腐蝕速率差異不大,隨著腐蝕時間的延長,腐蝕失重逐步增加,腐蝕速率則呈先增大后降低的趨勢,這主要是由于銹層中穩定相(α-FeOOH)和不穩定相(γ-FeOOH和β-FeOOH)相對含量隨實驗時間發生變化所致。
(2) NSS實驗條件下試樣主要腐蝕產物為Fe3O4、α-FeOOH、γ-FeOOH、α-Fe2O3和δ-FeOOH;CCT條件下的腐蝕產物組成基本相同,只是同時存在較多的β-FeOOH。這是因為在干濕交替條件下腐蝕產物疏松多孔,Cl—的催化和擴散作用較強,導致銹層內部仍有較高濃度的Cl—,從而產生較高含量的β-FeOOH。而該產物穩定性差,它的存在會增加陰極反應的活性區域,降低銹層對基體的保護作用,加速材料的腐蝕進程。
(3) 電化學交流阻抗鋪擬合結果表明,不同加速實驗條件下試樣表面腐蝕產物膜電阻和溶液電阻均隨著實驗時間的延長而逐步增加,說明銹層厚度的增加對試樣基體的腐蝕有一定的阻礙作用;電荷轉移電阻值均呈現先下降后上升的變化過程,但NSS實驗條件下的數值普遍高于CCT條件下的,一定程度上說明CCT條件下試樣腐蝕比NSS條件下的更加嚴重。
(4) 通過擬合試樣失重曲線,得出不同時間段腐蝕速率規律,對于NSS和CCT實驗分別為:前期(≤480 h),ΔD1-1=0.7349t0.1522,ΔD2-1=0.3511 t0.3313;后期(>480 h),ΔD1-2=14.6239 t?0.3236,ΔD2-2=6.8542 t?0.157。
免責聲明:本網站所轉載的文字、圖片與視頻資料版權歸原創作者所有,如果涉及侵權,請第一時間聯系本網刪除。
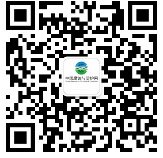
官方微信
《中國腐蝕與防護網電子期刊》征訂啟事
- 投稿聯系:編輯部
- 電話:010-62316606-806
- 郵箱:fsfhzy666@163.com
- 中國腐蝕與防護網官方QQ群:140808414