鋼鐵企業廠區煤氣管道數量較多,涉及BFG(高爐煤氣)、COG(焦爐煤氣)、LDG(轉爐煤氣)和CRG(歐冶爐煤氣)幾種煤氣介質,且煤氣管道動輒超過數十公里,煤氣管網的安全至關重要。其中,管道腐蝕作為煤氣管道的主要破壞形式,對于鋼鐵生產流程的穩定和安全產生重要影響。煤氣管道有哪些種類?煤氣管道的腐蝕機理是什么?煤氣管道如何修復?如何監測?小編帶你詳細了解。
01 概述
鋼廠煤氣管道數量較多,涉及BFG(高爐煤氣)、COG(焦爐煤氣)、LDG(轉爐煤氣)和CRG(歐冶爐煤氣)幾種煤氣介質。其中較大部分煤氣管道,介質的壓力遠低于0.1MPa。金屬的腐蝕主要是由于化學或電化學作用引起的破壞。煤氣管道中的煤氣成分復雜,主要有CO(一氧化碳)、H2(氫氣)、CO2(二氧化碳)、CH4(甲烷)、O2(氧氣)、N2(氮氣)、H2S(硫化氫)、NH3(氨氣)、HCN(氰化氫)、NO(一氧化氮),還有水、氯化銨、萘、焦油等,其中CO2、H2S 等與煤氣冷凝水結合形成酸性腐蝕環境。煤氣管道通常采用普通碳鋼材料,在這種工作環境條件下,尤其是BFG 介質,極易造成管道內壁“點狀”“蜂窩狀”的局部腐蝕。從管道現場腐蝕的情況看,腐蝕基本都發生在管道的下半部分。這種腐蝕是管道最具有破壞性和隱藏性的腐蝕形態之一,它常常使得管道在整體失重還很小的情況下,就穿孔產生泄漏。近年來,隨著管道使用年限的增加,管壁腐蝕引起的穿孔泄漏事故時有發生,腐蝕泄漏不僅會發生在管道本體上,也會發生在與管道相連的喇叭口、排水密封罐上,還會發生在波紋管等管道附件上,對生產和人員造成一定的安全隱患。
國內鋼鐵企業武鋼、南鋼、日照鋼鐵以及邯鄲鋼鐵等在采用干法除塵后管道及附屬設備也出現腐蝕問題,腐蝕部位主要集中在煤氣管道、排水器、補償器和TRT葉片等。
02 腐蝕機理及原因
2.1 城市煤氣管網腐蝕
城市煤氣管網中,管道內壁形成腐蝕損傷主要由化學腐蝕和電化學腐蝕共同作用而形成,從而在管道內壁形成腐蝕溝槽、深坑或大面積腐蝕減薄等,根據現場管道腐蝕缺陷檢測與特征分析,某市人工煤氣管網以體積型缺陷為主,包括管壁的均勻腐蝕缺陷、局部腐蝕缺陷等。在某些區域人工煤氣管道存在明顯的沉降現象,沉降將導致管道發生位移變形,同時在該地區存在不同程度的積液和內腐蝕,積液將導致荷載的增加,內腐蝕的發生將使得管道出現局部應力集中和增大,直接影響到管道的安全運行能力。
2.2 高爐煤氣管道腐蝕
煉鐵系統中,干法除塵后的高爐煤氣經TRT 余壓發電機做功溫度有較大幅度降低,在低于露點時煤氣中的飽和水會隨著溫度降低不斷轉變為冷凝水。高爐原燃料中含有大量氯鹽,在冶煉過程中與水發生化學反應生成氯化氫氣體而進入高爐煤氣中,由氯化氫極易溶解在水中,所以當有冷凝水析出時會伴隨氯化氫溶解。此冷凝水檢測其PH 值長期在1~2 之間為強酸,對金屬管道腐蝕性較大。當煤氣管道被腐蝕后,出現穿孔泄露問題,膨脹節、排水器、流量計的一次部件以及高爐熱風爐的換熱器也均被腐蝕。
依據不同PH 值的酸性溶液檢測其對碳鋼、不銹鋼腐蝕速率,檢測結果碳鋼:PH=1 時,腐蝕率達到34.1384(mm/a),PH=2~5 時,腐蝕率1.9682~3.757(mm/a);不銹鋼:PH=1~5 時,腐蝕率0.0083~0.0106(mm/a)試驗證明,PH 值越低的鹽酸,對碳鋼的腐蝕速率越大,PH 值等于1 時,腐蝕速率可以達到34.1384mm/a, 即一年里管道腐蝕可以達到3.4 個厘米。鹽酸的析氫腐蝕是造成管道腐蝕的主要原因。不銹鋼情況相對較好,因為耐酸本是不銹鋼的優勢之一。冷凝水中含有大量的氯離子,因為氯離子屬于活潑離子,穿透能力強,能夠被金屬表面較強吸附。Cl- 濃度越高,水溶液的導電性就越強,Cl- 就越容易到達金屬表面,加快腐蝕的進程。奧氏體不銹鋼比普通碳鋼更容易受到氯離子的侵蝕。同時因管道、波紋管中的焊縫因焊接組織復雜、受力復雜、加上可能存在焊接缺陷,更容易被氯離子侵蝕。現場檢查發現,管網上不銹鋼膨脹節和不銹鋼設施腐蝕嚴重,尤其焊縫泄漏點多。
2.3 轉爐煤氣管道腐蝕
轉爐煤氣系統中,轉爐煤氣中主要含CO、CO2、O2和N2,其中O2和CO2對于煤氣管道及設施均有不同程度、不同種類的腐蝕;CO2是轉爐煤氣中含量最多的雜質,可以造成酸腐蝕和應力腐蝕等多重腐蝕,因此推斷其可能是造成轉爐煤氣輸送設施腐蝕最嚴重的影響因子;煤氣中O2的含量較少,但其對轉爐煤氣輸送設施的腐蝕也有著重要的影響,因為煤氣中含有水,而只要有O2,就可以造成環境中的干濕交替循環,加劇腐蝕。電除塵前的煤氣由于含塵量和含水量高,柜前管道、氣柜及電除塵器腐蝕嚴重。煤氣溫度偏高也是其管道及設施腐蝕的一個關鍵性因素。煤氣冷凝水呈弱酸性,pH值分別是5.7、4.46,總酸度分別是2.5,3.0,對管道產生腐蝕。
2.4 架空煤氣管道外腐蝕
管外局部腐蝕主要是大氣腐蝕,多發生在防護層破損且潮濕、易積存灰層的部位。大氣腐蝕是在金屬表面存在水膜時發生的電化學腐蝕,主要是氧還原陰極的過程。影響管道在大氣中腐蝕的主要因素有相對濕度、溫度、大氣成分等。
在一定的溫度下,干燥的空氣對鋼鐵的腐蝕速度是很低的,只有在空氣的相對濕度增加到一定范圍時,腐蝕速度才突然升高,這一大氣相對濕度范圍稱為臨界濕度,經測定臨界濕度約為50 % ~ 70 %。
當管道表面處在比自身溫度高的空氣中,金屬表面可能產生結露現象。在臨界濕度附近能否結露和溫度變化有關,平均溫度高的地區大氣腐蝕速度較大。
工業大氣中含有SO2、H2S、CO2、灰層等污染物質。其中SO2 是危害性最大的一種污染物,其腐蝕機理可由“酸的再生循環”作用來解釋: SO2 首先被吸附在管道表面上與氧一起生成FeSO4,然后FeSO4水解生成游離的硫酸,硫酸又加速腐蝕鋼鐵,新生成的FeSO4 再水解生成游離酸,如此反復循環,加速鋼鐵的腐蝕。固體塵粒落在管道表面成為吸附水分子的凝聚中心。
2.5 埋入地下煤氣管道腐蝕
煤氣管道經常鋪設在地質惡劣的條件下,受煤氣雜質的制約,在局部管道內壁處受腐蝕嚴重,埋藏突發性露氣的安全隱患。由于煤氣管道局部腐蝕具有不可預測性,是引發煤氣管道事故的主要原因,一般情況下造成煤氣管道局部腐蝕的原因包括地質環境和管道的材質及制造工藝。
天然氣管道在埋地環境下,主要受細菌、土壤以及雜散電流等的腐蝕。管道附近產生的二次感應交流電流疊加在管道產生的具有破壞作用的電流形成了雜散電流腐蝕,腐蝕量小,但集中腐蝕性強。另外,土壤中的硫酸鹽還原菌將可溶硫酸鹽還原成硫化氫與鐵,形成細菌腐蝕。管道鋼材的材質與制造因素是管道腐蝕的內因,特別是管道鋼材的化學組分與微晶比較多,造成了嚴重的腐蝕問題。
2.6 焦爐煤氣管道腐蝕
由于焦爐煤氣中含有H2S、CO2 等腐蝕性介質,因此焦爐煤氣對管道、管道配件、設備的腐蝕是比較嚴重的,如不采取處理措施,將影響到焦爐煤氣的正常供應。由于煤氣在管道內流速緩慢,使荼等有機物沉積成一層海棉狀的沉積物,水分積存在其中,煤氣中的硫化氫在這種條件下對煤氣管道產生嚴重腐蝕。
如攀鋼一期焦化出現管道腐蝕,經化驗,焦爐煤氣H2S 含量平均高達750 mg/m3,最高達1380 mg/m3,因此,焦爐煤氣中H2S 含量偏高是焦爐煤氣管道腐蝕的根本原因。
03 應對措施
3.1 高爐煤氣管道腐蝕應對措施
(一)采用先進的工藝技術,提升設備設施抗氯離子腐蝕的能力
(1)新建煤氣管道或大修煤氣管道內防腐采用玻璃鋼鱗片防腐工藝,能夠延長管道壽命。
首鋼遷鋼2#高爐,爐容2500m?,高爐煤氣管道內壁防腐蝕主材料采用VEGF材料(VEGF涂料);首鋼京唐鋼鐵廠特大高爐,爐容5500m?,高爐煤氣管道內壁防腐蝕主材料采用VEGF材料。
(2)波紋膨脹節采用高分子復合補償器,能夠解決氯離子對不銹鋼腐蝕和波紋膨脹節與管道的焊縫腐蝕。
(二)除塵系統增設除鹽裝置,減少氯離子進入凈煤氣管網中,預防煤氣管網腐蝕。
(1)在利用完高爐煤氣余壓發電后、煤氣進入管網前增加煤氣洗凈塔,對煤氣進行洗滌凈化的塔式結構,又稱脫鹽塔、洗氯塔。
(2)管道噴堿降溫控制煤氣溫度,確保煤氣溫度低于露點溫度。通過在TRT 出口增加噴堿降溫裝置,將煤氣降溫至露點以下,盡最大量將煤氣中飽和水全部析出,加入的堿液可中和溶解的酸性物質,從而降低管道腐蝕,對析出冷凝水段進行防腐蝕控制,避免后續管道大面積腐蝕。
3.2 焦爐煤氣管道腐蝕應對措施
針對焦爐煤氣管道腐蝕,可以進行如下的措施:
(1)焦爐煤氣中H2S 含量控制在200 mg/m3 以內,只有這樣才能從根本上解決焦爐煤氣管道腐蝕嚴重的問題。
(2)管道內、外壁應進行防腐處理
根據寶鋼的經驗,要對焦爐煤氣管道內壁涂刷兩遍防腐漆,先涂環氧瀝青鋁粉耐油底漆,再涂環氧瀝青耐油面漆。并且為了保證施工質量,除管道外壁的最后一道涂層外,涂漆施工都在加工廠內進行,收到了較好的效果。焦爐煤氣管道的面漆顏色改為鉑色或銀灰色。
(3)適當提高煤氣流速,建議在保證用戶使用的情況下,適當提高煤氣流速,以減緩焦爐煤氣管道的腐蝕。不同管徑的煤氣流速控制如下表。
表不同管徑的煤氣流速控制標準
(4)增設冷凝水排水器,在焦爐煤氣管道沿線適當多增設排水器,同時要加強管道的維護,使排水器能正常工作。
(5)增設隔熱板,在有鐵水罐車、運渣罐車通行的位置,在管道底部增設隔熱板進行保護。
04 修復方法
煤氣管道常規的修復方法有,焊接修復、帶壓堵漏、鋼板局部托補、環氧樹脂包覆、整體更換、碳纖維復合材料包覆,這些方法都有各自的特點,如焊接修復方法通常在停輸狀態下進行,對于焊縫泄漏及薄壁管體缺陷修復,在線焊接修復存在巨大的安全隱患;帶壓堵漏,是一種臨時性的補救方法,且安全風險高;鋼板局部托補修復,施工難度高、安全風險大,會增加管道自重,影響管道應力分布及支架沉降,如管道有泄漏,原管道與托補板間的夾層會積水,從而可能加速管道腐蝕;環氧樹脂包覆,老化速度快,可導致管道短期內再次發生泄漏;整體更換,成本高,需要停機,影響連續生產。碳纖維復合材料包覆修復具有不需動火焊接、工藝簡單、施工迅速、操作安全、使用壽命長、可實現不停輸修復,并且成本相對較低。
表煤氣管道的不停輸修復方法
05 總結
作為鋼鐵企業內部最為常見和分布最為廣泛的煤氣管道,直接影響整個鋼鐵生產流程的穩定和安全。煤氣管道的腐蝕原因主要包括化學腐蝕、電腐蝕、應力腐蝕等形式,通過噴涂防腐涂層、優化管道設計、改進生產工藝,降低管道腐蝕發生的頻率,并通過日常完善的監測方法,實現對管道連續的監測。
參考文獻:
(1)煤氣管網典型腐蝕及安全承載能力分析,陸彬等
(2)轉爐煤氣回收系統的腐蝕與防腐問題探討,宋玲等
(3)包鋼架空煤氣管道外腐蝕原因分析及應對措施,石磊等
(4)煤氣管道的防腐問題處理,陳恒立等
(5)焦爐煤氣中腐蝕性介質的生成與影響,熊仁愷
(6)高爐煤氣干法除塵腐蝕機理及解決辦法探討,劉廷飛
(7)關于高爐煤氣管道防腐蝕材料的選擇,曾邵等
(8)攀鋼焦爐煤氣管道腐蝕的原因及處理措施,馬作舫等
(9)冶金煤氣大口徑管道腐蝕檢測及修復方法,李杰等
免責聲明:本網站所轉載的文字、圖片與視頻資料版權歸原創作者所有,如果涉及侵權,請第一時間聯系本網刪除。
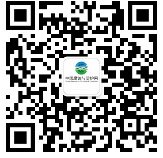
官方微信
《中國腐蝕與防護網電子期刊》征訂啟事
- 投稿聯系:編輯部
- 電話:010-62316606-806
- 郵箱:fsfhzy666@163.com
- 中國腐蝕與防護網官方QQ群:140808414