導(dǎo)讀
噴丸強(qiáng)化作為表面強(qiáng)化工藝之一,其工藝相對(duì)其他表面改性工藝而言比較簡(jiǎn)單,但是使用效果卻非常顯著,目前已應(yīng)用于航天航空、機(jī)車、汽車等各個(gè)領(lǐng)域。
噴丸強(qiáng)化原理是利用噴射出的彈丸強(qiáng)烈撞擊材料,在表面形成小凹坑,使材料表面發(fā)生塑性變形,從而在金屬表面產(chǎn)生殘余應(yīng)力。表層下壓縮的晶粒由于要恢復(fù)到原來的形狀,從而會(huì)產(chǎn)生一個(gè)均勻的殘余壓應(yīng)力層,使材料表面得到強(qiáng)化,經(jīng)過噴丸處理之后,材料表層的組織結(jié)構(gòu)發(fā)生變化,晶粒細(xì)化,位錯(cuò)密度增大,晶格畸變?cè)龃?,最終形成很高的殘余壓應(yīng)力。材料表層殘余應(yīng)力的存在將明顯地提高材料的抗疲勞性能和疲勞壽命,提高材料表面的強(qiáng)度和硬度、以及抗應(yīng)力腐蝕及耐高溫氧化等性能。
一、試驗(yàn)用材料
試驗(yàn)選用2A14鋁合金桶形零件,其材料強(qiáng)度較高,熱強(qiáng)性好,具有良好的可切削性,電焊和焊縫性能良好,其具體成分如表1所示。
表1 2A14鋁合金化學(xué)成分

將2A14鋁合金桶形零件分為4組(見圖1),第一組表面粗糙度值Ra=0.30~0.65μm,第二組表面粗糙度值Ra=2.20~4.71μm,第三組表面粗糙度值Ra=6.5~7.1μm,第四組表面粗糙度值Ra=1.40~1.75μm。
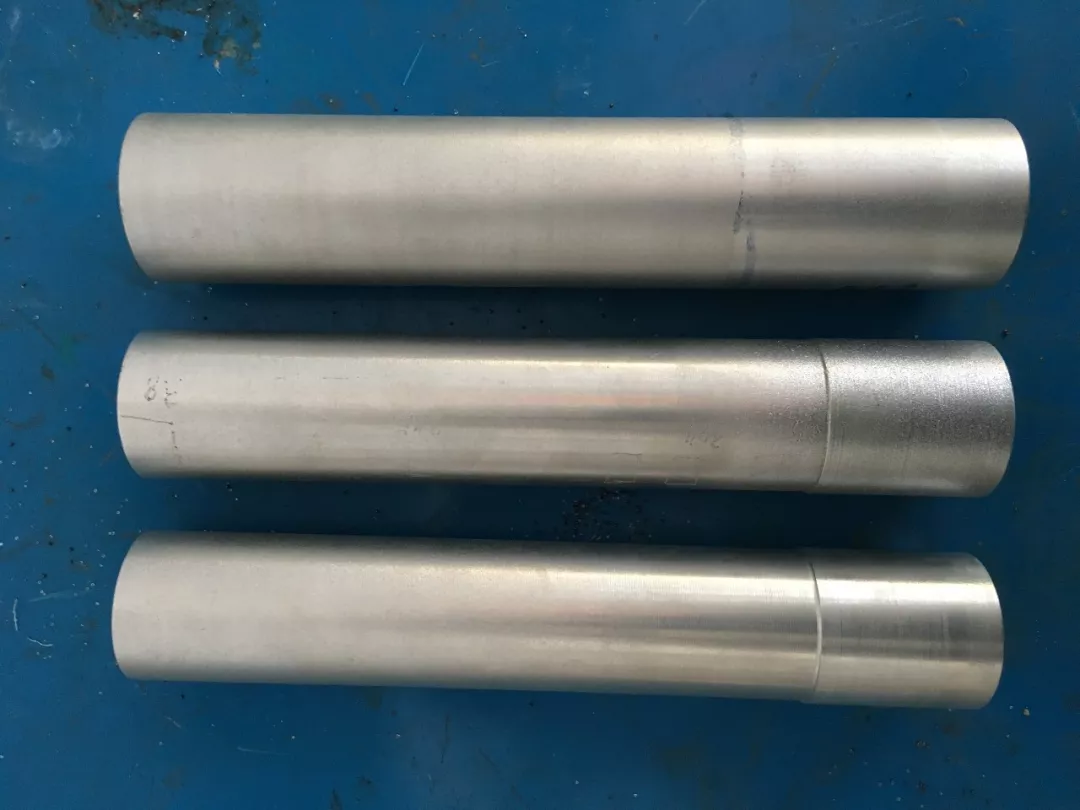
(a)第一組
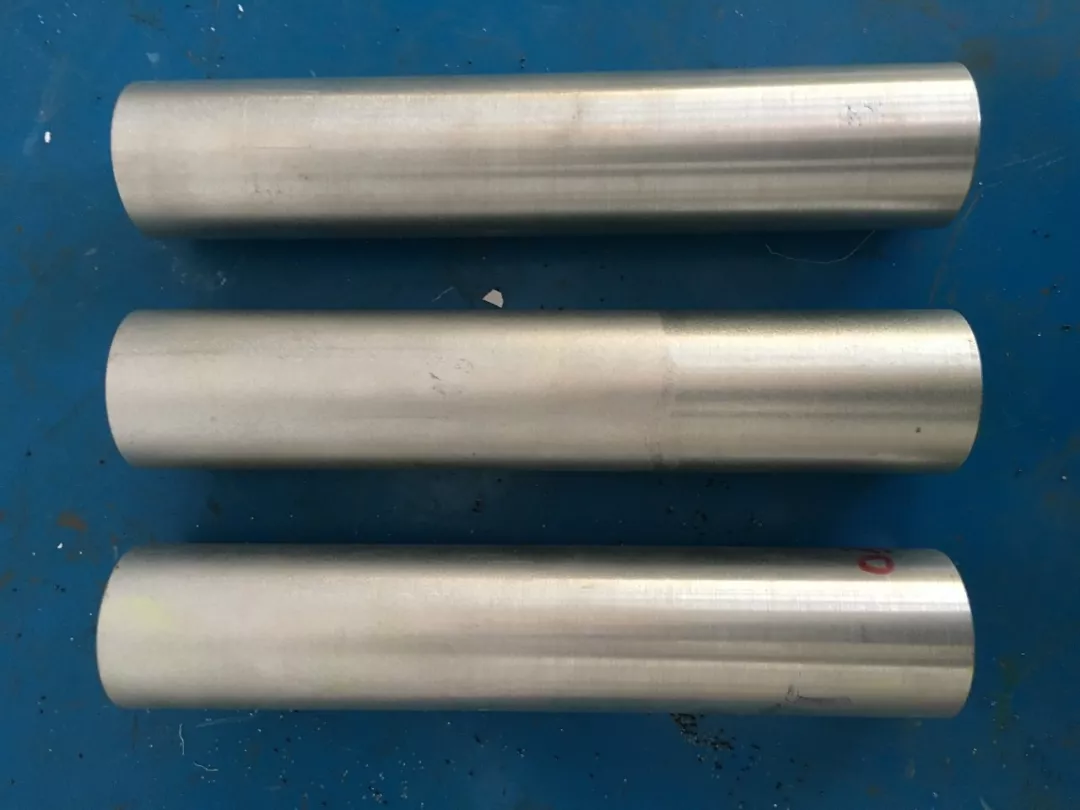
(b)第二組
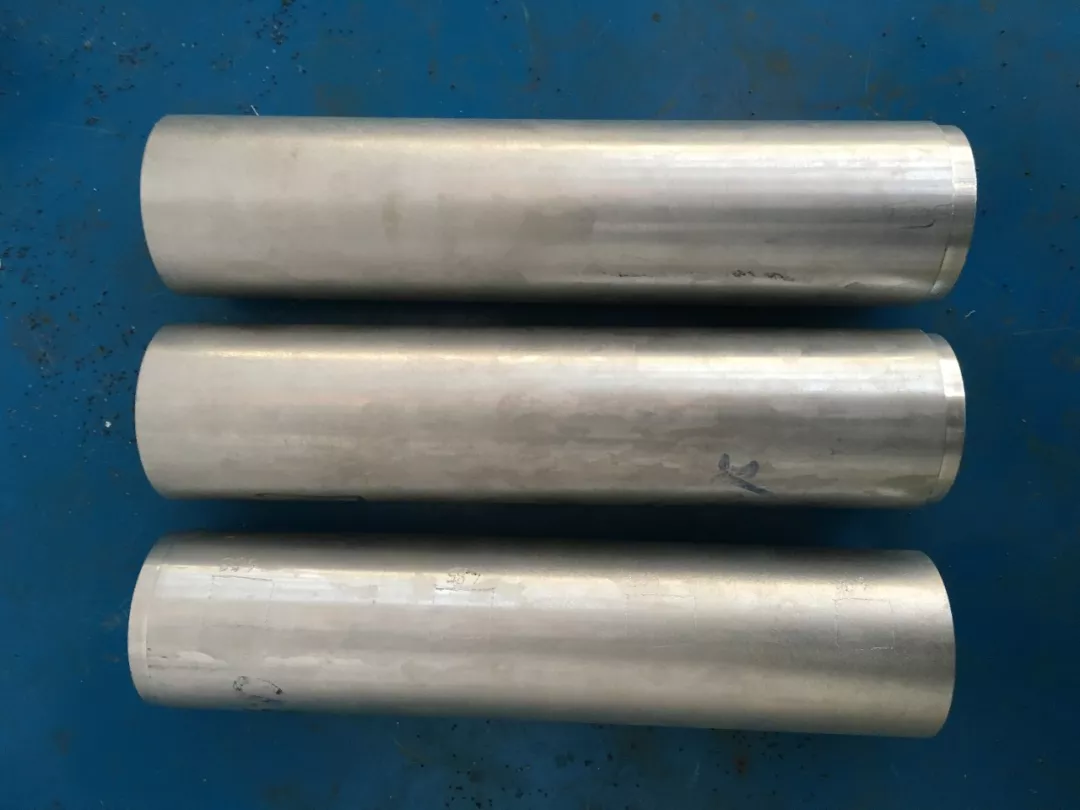
(c)第三組

(d)第四組
圖1 噴丸處理前的零件
采用型號(hào)為SP1200 G4的氣動(dòng)式噴丸機(jī),其工作原理如圖2所示,玻璃鋼丸在負(fù)壓的情況下被吸附到了高壓噴嘴前,彈丸在高壓的作用下噴射到零件的表面,使得在零件表面上產(chǎn)生塑性變形。噴丸丸粒采用規(guī)格為AGB70的玻璃彈丸,符合AMS 2431/6標(biāo)準(zhǔn),其形貌如圖3所示。
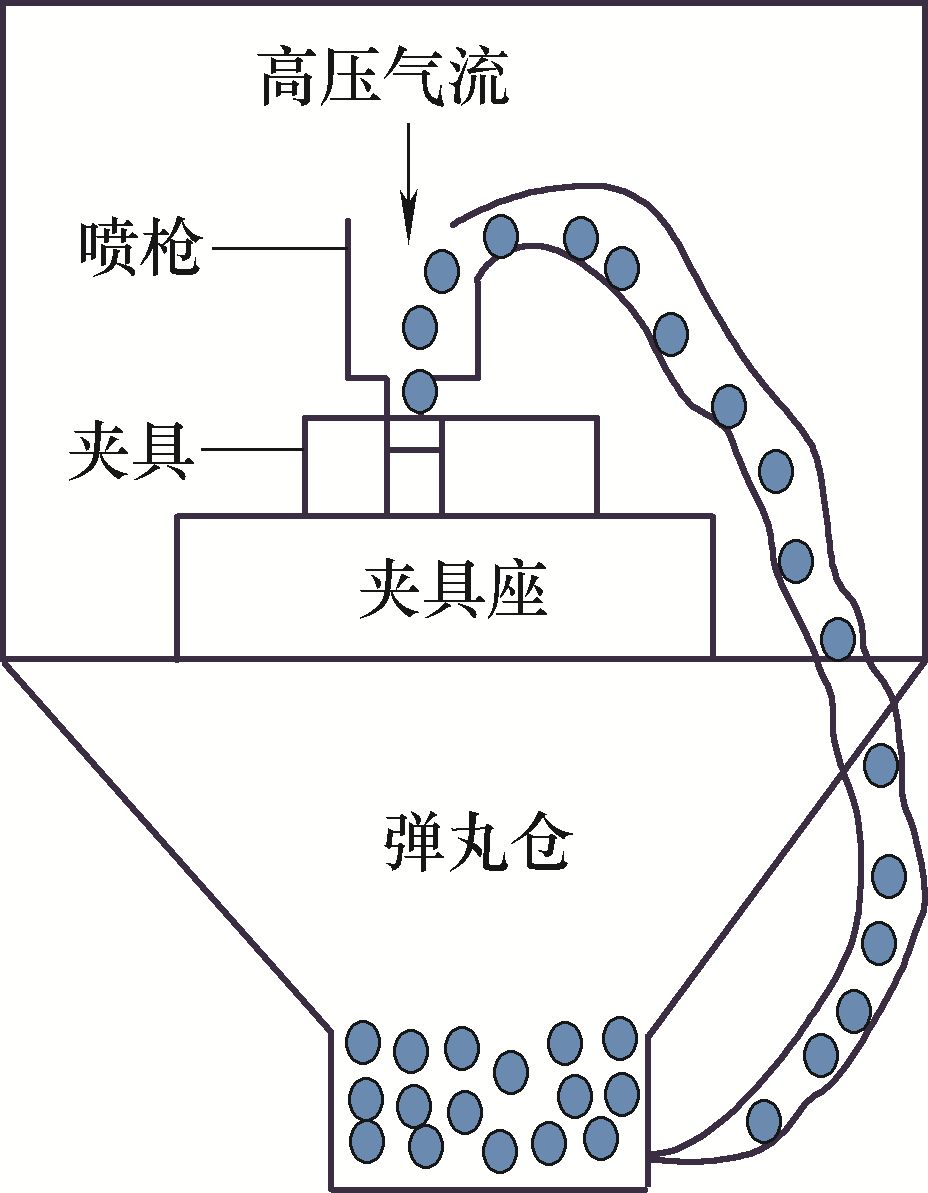
圖2 噴丸處理
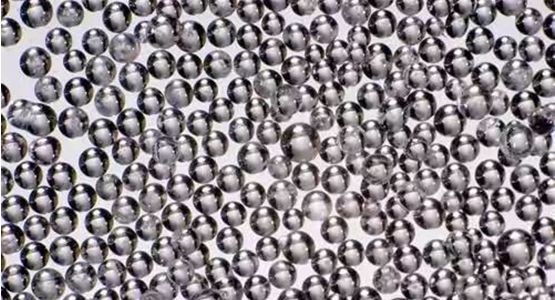
圖3 玻璃丸粒
噴丸強(qiáng)度的驗(yàn)證采用如圖4所示的自制工裝,將驗(yàn)證ALMEN試片的標(biāo)準(zhǔn)底座通過螺釘固定在自制工裝中,并將ALMEN標(biāo)準(zhǔn)試片固定于標(biāo)準(zhǔn)底座上。ALMEN標(biāo)準(zhǔn)試片滿足SAE J 442和AMS 2431/2文件要求。測(cè)試次數(shù)滿足最低要求的4次。
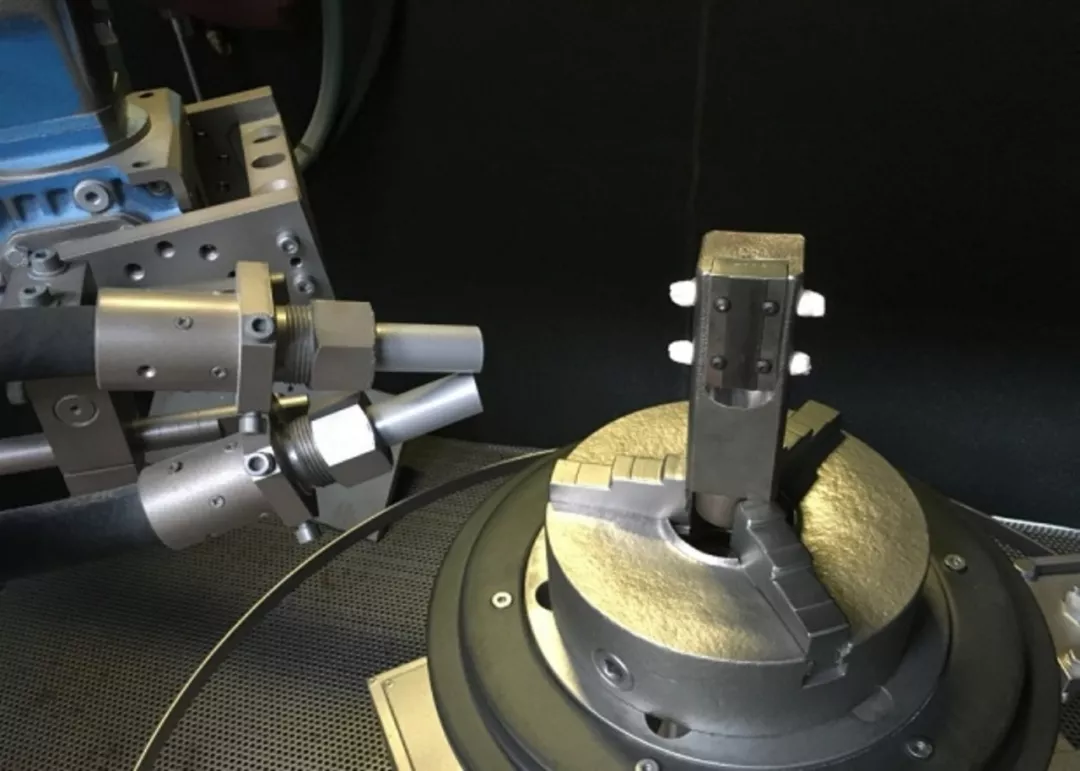
圖4 自制工裝
二、試驗(yàn)方法
1、噴丸壓力和丸流量的選擇
噴丸時(shí),在有一定壓力氣流的情況下,彈丸以一定的動(dòng)能形成一條有規(guī)律的彈丸流作用于材料表面。而彈丸噴出速度和沖擊力量是由氣流壓力的大小決定的,材料塑性變形的程度是由噴丸在材料表面的強(qiáng)度決定的。而通過ALMEN試片的驗(yàn)證,繪制出飽和曲線,確定出飽和點(diǎn),就能確定出相應(yīng)的噴丸強(qiáng)度。在確定氣流的壓力值時(shí),應(yīng)盡量考慮使用較低的氣流壓力,以減少對(duì)于材料表面的磨損。
彈丸流量是單位時(shí)間內(nèi)噴嘴噴射出彈丸的數(shù)量,流量和氣流壓力相關(guān),低的氣流壓力應(yīng)該對(duì)應(yīng)較低的流量,對(duì)于該零件選擇將氣流壓力定為0.5×105Pa,彈丸流量為3kg/min。彈丸流量和氣流壓力確定后,通過調(diào)整噴槍上下移動(dòng)的速度,可以得到不同的噴丸強(qiáng)度,通過調(diào)整噴槍上下移動(dòng)的速度為300mm/min、600mm/min和900mm/min時(shí),分別得到對(duì)該零件的噴丸強(qiáng)度為三個(gè)固定值:0.35mm(A)、0.31mm(A)和0.27mm(A)。
2、噴丸時(shí)間的確定和覆蓋率的檢測(cè)
噴丸時(shí)間由ALMEN試片的飽和時(shí)間決定,但可根據(jù)試片達(dá)到的飽和時(shí)間對(duì)零件表面達(dá)到100%覆蓋率的時(shí)間,進(jìn)行相應(yīng)的借鑒,阿夫拉米方程對(duì)于平均覆蓋率是基于隨機(jī)統(tǒng)計(jì)的顆粒到達(dá)速度一致的假設(shè),該方程為

式中,C為覆蓋率(%);n為阿夫拉米指數(shù);r為凹痕半徑;R為形成凹痕的平均速度;t為形成凹痕所需時(shí)間。
根據(jù)阿夫拉米方程,可以觀察到覆蓋率越來越接近百分之百,但理論上不可能達(dá)到百分之百。最后百分之十覆蓋率所需時(shí)間是開始百分之九十覆蓋率所需時(shí)間的1.5倍。達(dá)到100%覆蓋率的最后1%所用噴丸時(shí)間將大約占總時(shí)間的20%,達(dá)到最后2%覆蓋率所需噴丸時(shí)間將接近總時(shí)間的40%,在99%的覆蓋率情況下,有85%的位置被擊打過兩次或更多,有50%的位置被擊打過5次或更多。一般來說,覆蓋率達(dá)到98%,就可以說是等于100%覆蓋了。如果想要達(dá)到百分之百的覆蓋率,可能會(huì)導(dǎo)致過度噴丸情況。98%的覆蓋率控制將會(huì)顯著節(jié)省噴丸時(shí)間。通過以上公式推測(cè),凹坑半徑就為彈丸的半徑,形成凹坑的平均速度近似為噴射速度,得出達(dá)到100%覆蓋率的時(shí)間為20min。
表面覆蓋率采用熒光法進(jìn)行測(cè)定,在進(jìn)行噴丸前在零件表面涂抹上一層熒光劑,并在黑燈下進(jìn)行照射,確保零件表面完全覆蓋上一層熒光劑,再對(duì)零件進(jìn)行噴丸。噴丸后在黑燈下進(jìn)行照射,若無熒光,或基本沒有熒光,則可判斷其覆蓋率達(dá)到100%。具體過程如圖5所示。
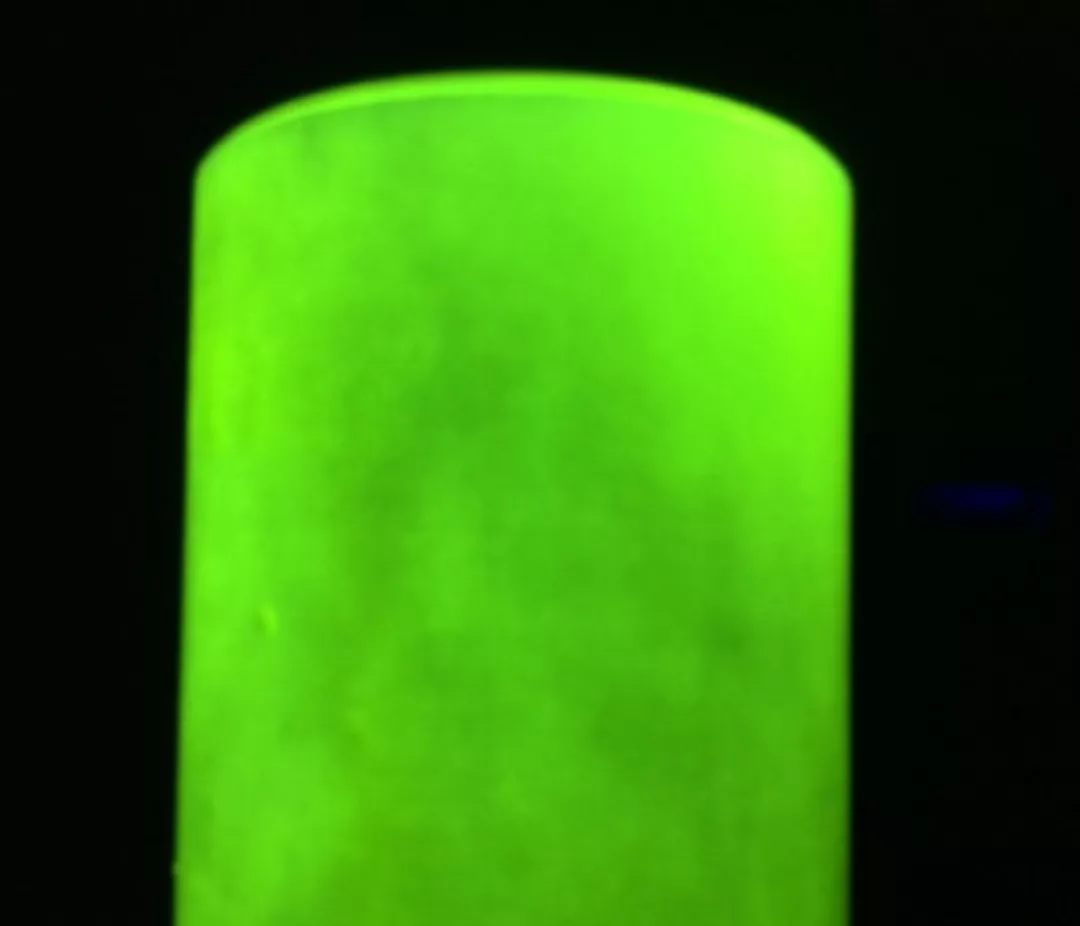
(a)零件表面涂熒光劑效果
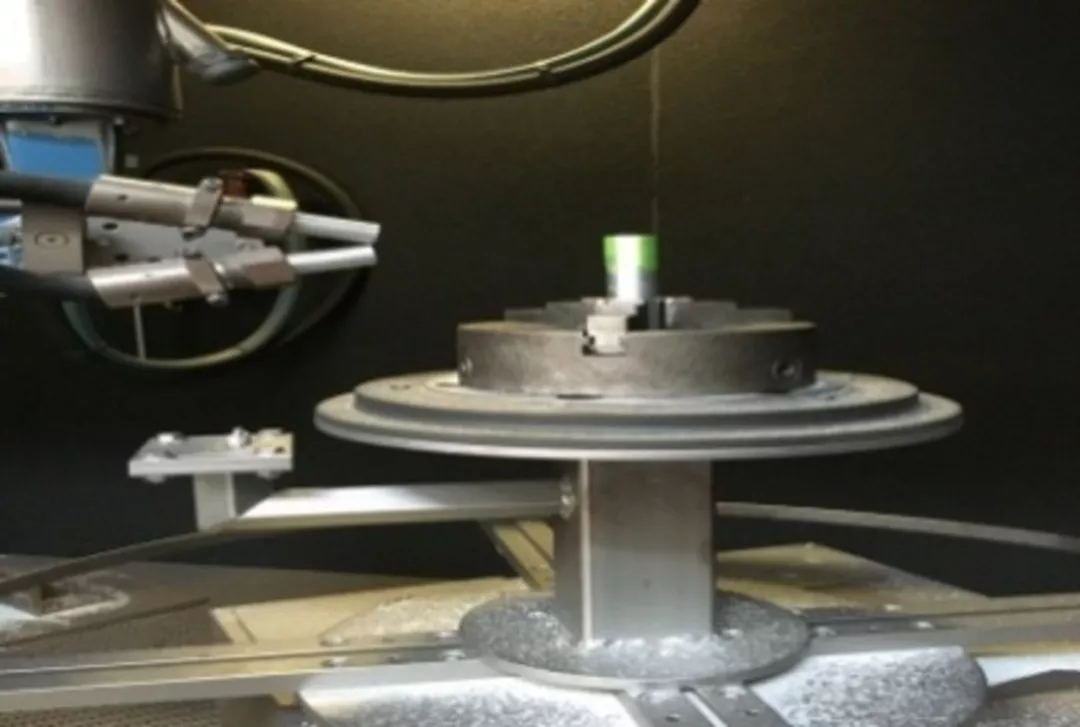
(b)零件進(jìn)行噴丸前
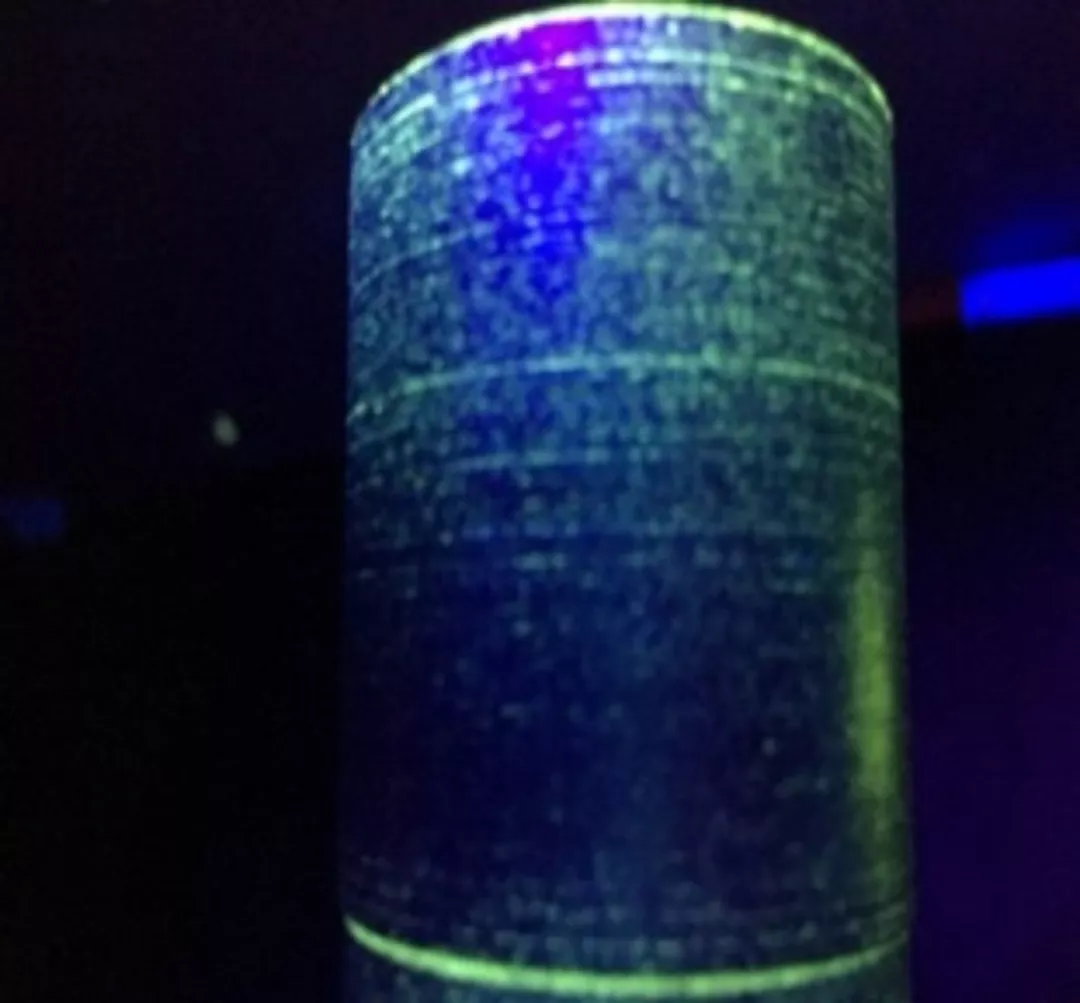
(c)零件噴丸后效果
圖5 熒光法進(jìn)行覆蓋率測(cè)試過程
選取一個(gè)零件,進(jìn)一步對(duì)其表面噴丸后的形貌進(jìn)行檢測(cè),如圖6所示,從圖6a、圖6b中可以看出,彈丸坑均勻分布在零件表面上,沒有出現(xiàn)噴射不到的面,和熒光覆蓋率檢測(cè)一致,說明表面覆蓋率良好。放大后如圖6c所示,表面無裂紋出現(xiàn),且形成了一層較為致密的強(qiáng)化層。
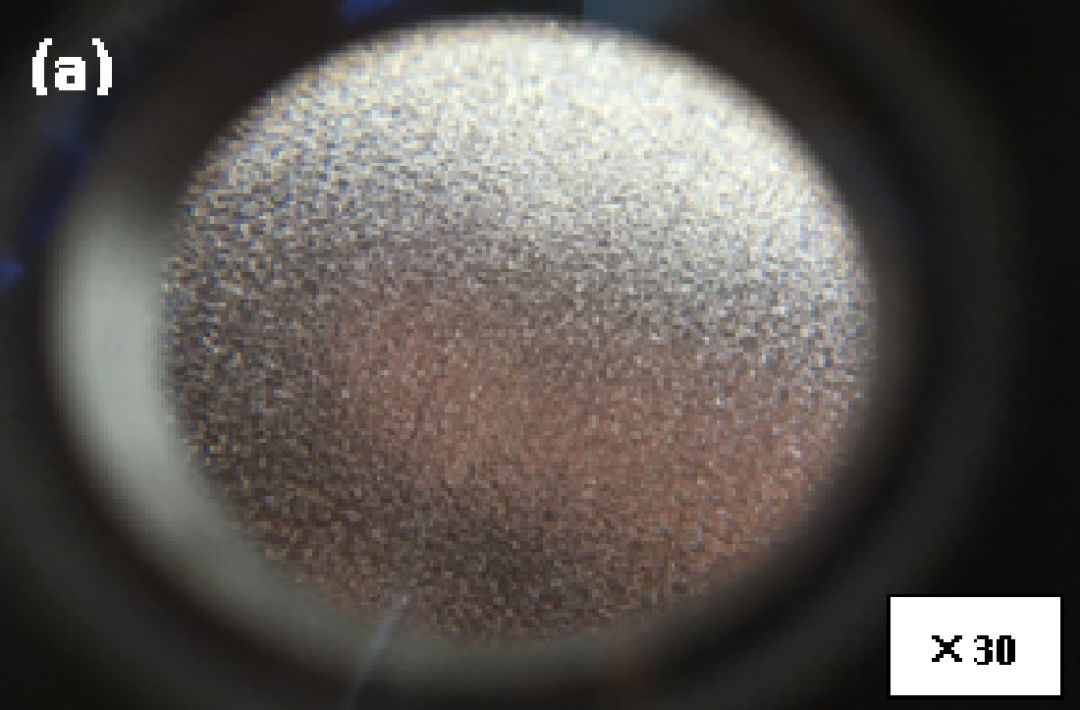
(a)
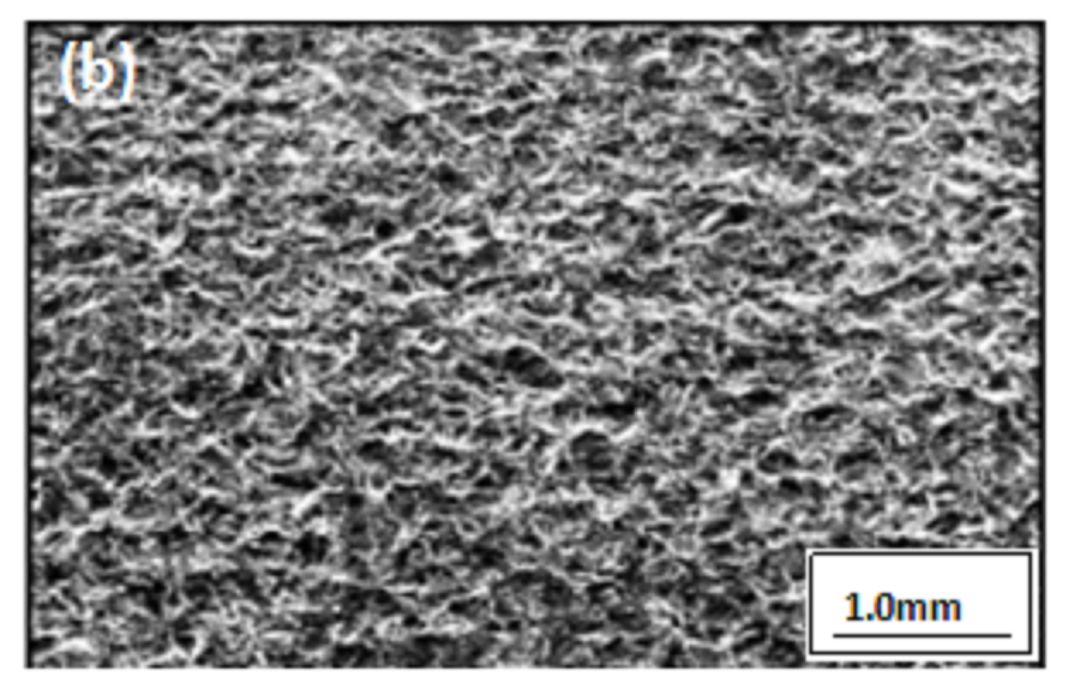
(b)
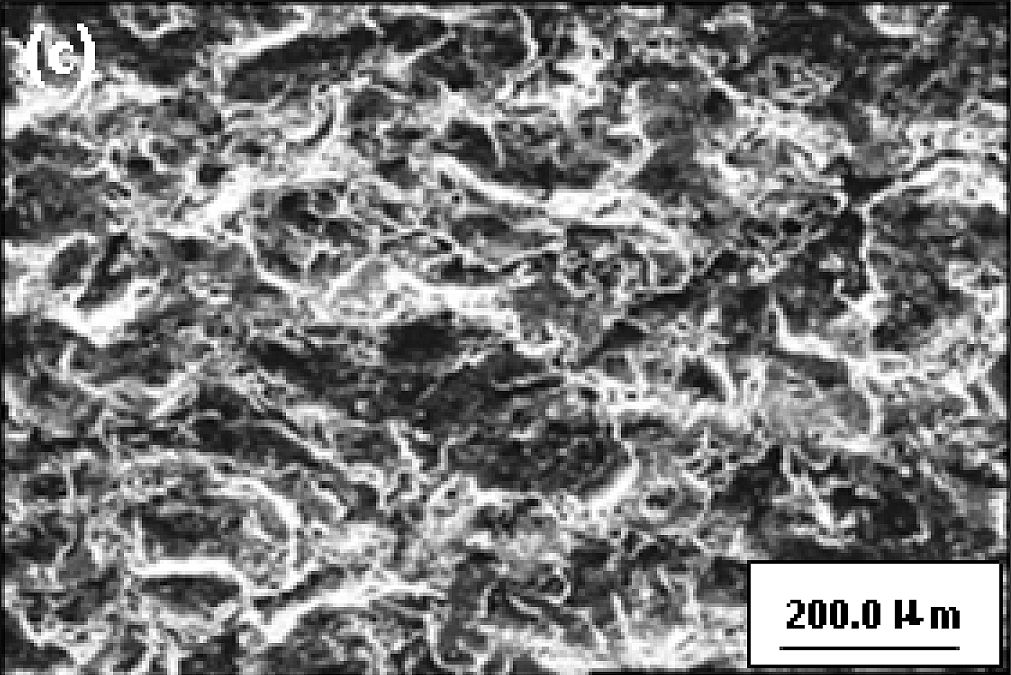
(c)
圖6 鋁合金桶形件噴丸后表面形貌
三、表面粗糙度分析
利用針尖曲率半徑為2μm左右的金剛石觸針沿被測(cè)表面緩慢滑行,金剛石觸針的上下位移量由電學(xué)長(zhǎng)度傳感器轉(zhuǎn)化成電信號(hào),經(jīng)放大、濾波、計(jì)算后顯示儀表指示出表面粗糙度值,并用Ra來評(píng)定輪廓表面的粗糙度。
利用粗糙度儀對(duì)2A14鋁合金表面進(jìn)行粗糙度測(cè)試,分別測(cè)量了噴丸前和噴丸后的表面粗糙度,如表2所示。當(dāng)未噴丸零件表面粗糙度值較小時(shí),噴丸以后表面粗糙度值開始增大,這是因?yàn)閲娡枨傲慵砻嬗捕炔皇翘撸慵砻孑^均整,且彈丸在零件表面產(chǎn)生的撞擊能量是不均勻的,導(dǎo)致在相對(duì)較平整的材料表面形成較大的凹坑,從而造成表面粗糙度值增大;但是當(dāng)被噴丸零件的表面粗糙度值較大時(shí),零件表面本身就是不均勻的,且是不平整的,當(dāng)彈丸以均勻的速度打擊在零件表面時(shí),造成表面的塑性變形,反而會(huì)使原本粗糙不平整的表面變得平整。
表2 噴丸工藝對(duì)鋁合金表面粗糙度的影響
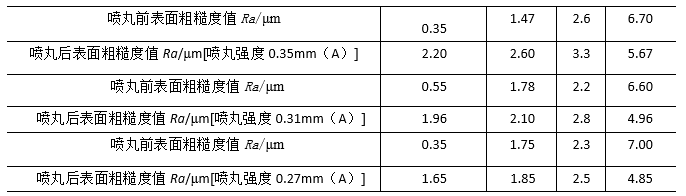
從表2可以看出,不同的噴丸強(qiáng)度下,表面產(chǎn)生的強(qiáng)度越高,其相對(duì)低強(qiáng)度對(duì)表面的影響也越大,但是對(duì)表面粗糙度的影響總的趨勢(shì)是一致的。零件表面噴丸的實(shí)際效果主要取決于彈丸噴射在零件表面上能量的傳遞,而能量主要取決于彈丸的質(zhì)量和速度,如圖7所示為彈丸粒子受力與加速方向示意圖。

圖7 彈丸粒子受力與加速方向
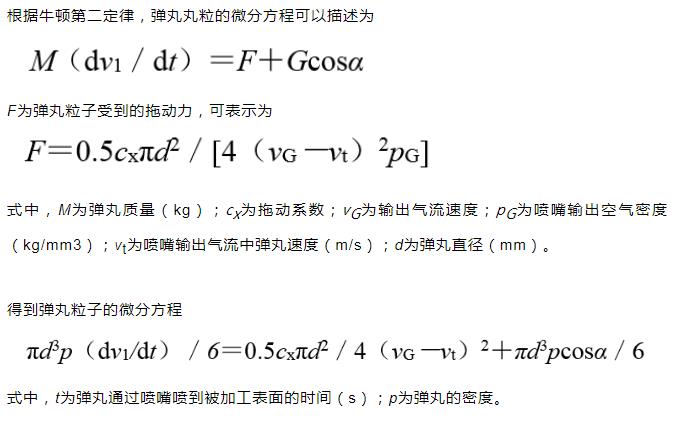
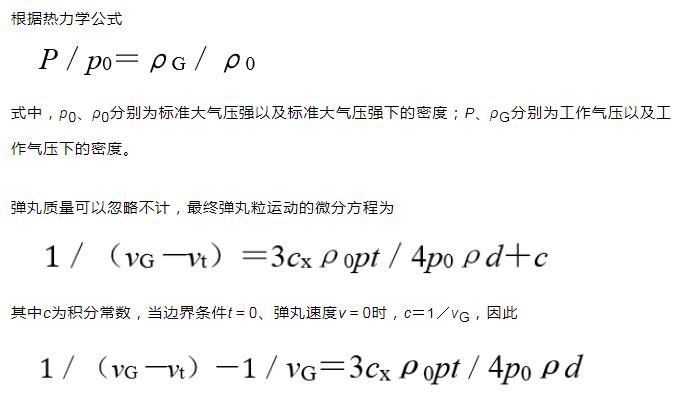
其中c為積分常數(shù),當(dāng)邊界條件t=0、彈丸速度v=0時(shí),c=1/vG,因此從以上推導(dǎo)公式可以看出,不同噴丸工藝參數(shù)對(duì)表層的性能影響可以歸結(jié)為:彈丸的動(dòng)能和噴嘴輸出氣流彈丸的速度、彈丸到達(dá)零件表面的時(shí)間、彈丸密度以及時(shí)間有關(guān)。
若需更大范圍地控制零件表面的粗糙度,即改變零件表面狀態(tài),還需調(diào)整彈丸的丸粒大小,其不僅能夠反映零件表面噴丸后的微觀集合形狀特征,也可以反映表面凹坑輪廓的最大高度,也可以控制不平整的表面。對(duì)零件表面粗糙度的影響,不僅和噴丸的強(qiáng)度有關(guān),同時(shí)也和噴丸粒子的尺寸以及表面覆蓋率都有相應(yīng)的關(guān)系。
四、結(jié)語
(1)有出現(xiàn)噴射不到的面,說明表面覆蓋率良好,表面無裂紋出現(xiàn),且形成了一層較為致密的強(qiáng)化層。
(2)同種彈丸不同的噴丸強(qiáng)度可以在一定范圍內(nèi)改變零件的表面粗糙度,當(dāng)零件表面粗糙度值Ra=0.30~0.65μm時(shí),可將 表面粗糙度值提高到Ra=2.2μ m左右。當(dāng)零件表面粗糙度值Ra=1.40~1.75μ m時(shí),噴丸后表面粗糙度將和零件表面粗糙度基本一 致,在Ra=1.6μ m左右。當(dāng)零件表面粗糙度值Ra=2.8~7.1μ m時(shí),可將表面粗糙度值降低到Ra=2.3~6.1μm。
(3)從彈丸粒子的微分方程推導(dǎo)出不同噴丸工藝參數(shù)對(duì)表層的性能影響,可以歸結(jié)為彈丸的動(dòng)能和噴嘴輸出氣流彈丸的速度、彈丸到達(dá)零件表面的時(shí)間、 彈丸密度以及時(shí)間有關(guān),其強(qiáng)度越高,相比于低強(qiáng)度對(duì)表面的影響也越大,但是對(duì)表面粗糙度的影響總的趨勢(shì)是一致的。
免責(zé)聲明:本網(wǎng)站所轉(zhuǎn)載的文字、圖片與視頻資料版權(quán)歸原創(chuàng)作者所有,如果涉及侵權(quán),請(qǐng)第一時(shí)間聯(lián)系本網(wǎng)刪除。
-
標(biāo)簽: 噴丸強(qiáng)化, 表面強(qiáng)化, 金屬加工
相關(guān)文章
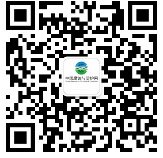
官方微信
《中國腐蝕與防護(hù)網(wǎng)電子期刊》征訂啟事
- 投稿聯(lián)系:編輯部
- 電話:010-62316606-806
- 郵箱:fsfhzy666@163.com
- 中國腐蝕與防護(hù)網(wǎng)官方QQ群:140808414
文章推薦
點(diǎn)擊排行
PPT新聞
“海洋金屬”——鈦合金在艦船的
點(diǎn)擊數(shù):7130
腐蝕與“海上絲綢之路”
點(diǎn)擊數(shù):5741