1.引言
工業管道作為化學工業的“血管”,在化工生產中扮演重要的角色。大多數工業管道都是在施工現場進行焊接和安裝,由于施工現場條件比較復雜,施工的質量容易受到影響;另外,在定期檢驗過程中,經常會遇到現場工業管道與設計圖紙不符的情況。以上的種種原因都可能導致壓力管道在運行過程中出現事故,導致人員和財產損失。如何能夠保證工業管道運行安全,一直以來都是廣大學者研究的重點方向。
隨著科學技術的進步,越來越多的學者使用有限元分析軟件對工業管道進行應力分析和強度評定,有限元分析方法也得到了學界的認可。淡勇等采用有限元方法對超高壓管道進行應力分析和強度評定,并對計算結果進行分解和應力分類。白芳等利用模擬與實驗相結合的方法對X80鋼多層焊道的殘余應力進行研究。柏慧等研究了熱輻射對加氫反應器熱箱部位溫度及應力分布的影響,考慮熱輻射會使熱箱部位的溫度場分布更均勻,應力顯著減小。許金沙等研究了搪玻璃層熱膨脹系數、溫差、厚度三個因素對搪玻璃層耐溫差急變性能的影響,并通過試驗研究對數值模擬結果進行了驗證。吳新麗等采用Sysweld建立焊接模型,對經歷不同熱處理工藝的管板與環形支承板對接焊縫的焊接殘余應力進行模擬分析,同時將模擬計算應力值與盲孔法測試應力值進行比較,并通過模擬試驗驗證其力學性能。霍玉峰等建立了鋼渣罐三維瞬態熱彈塑性仿真模型,對緩冷過程鋼渣罐的溫度場進行了分析,對罐體和縱橫加勁肋等典型部位的應力和塑性應變也進行了分析。蘇文獻等利用有限元分析軟件對復雜載荷作用下帶夾套縮聚釜泄漏進行失效分析與改進設計。黃云等采用有限元方法研究單、雙重裂紋的尺寸和位置變化對油氣管道應力的影響,并擬合得出相應公式。張國威等基于熱-結構耦合的干氣壓縮機出口輸氣管道進行應力分析,當管道溫差過大時,外壁所受應力較大。伍穎等對管道上典型的平滑凹痕缺陷,根據管道的實際運行狀況,建立了有限元模型,并得出應力隨各參數的變化規律,采用非線性回歸分析方法對計算結果進行了擬合。帥健等分析占壓載荷作用下管道的應力與變形,管道在上覆土體和夯實地基的不均勻作用下發生局部彎曲和橢圓化變形。
從上文的文獻中可以得出,國內外學者對于管道應力分析方面進行了大量的研究,但是大部分研究都是忽略溫度下的單一和復雜載荷作用下的壓力管道應力和強度分析,局限性比較大。本文研究了某化工企業中一條高溫高壓管道,建立了管道管件和焊縫的三維物理模型,利用有限元分析方法,研究了管道和焊縫在設計工況和使用工況下應力場和溫度場隨時間變化的情況,并基于分析設計標準進行應力評定,確定安全使用范圍。
2. 有限元模型
2.1 物理模型和材料屬性
該管道為某化工企業在用工業管道,在管道管件彎頭與三通焊縫連接處發現焊縫未焊滿情況,如圖1(a)中紅色框所示。從現場測量后得出,焊縫高度與管道表面相差10mm左右。管道整體設計壓力為44.8Mpa,設計溫度為260℃;工作壓力為38Mpa,工作溫度為110℃。三通管外徑為241.3mm,內徑為125.1mm;彎管外徑為241.3mm,內徑為140.9mm。管道焊縫焊接系數0.85。由于本文主要研究三通和彎管連接處焊縫的應力分布情況,因此只選取了管道的三通和彎管這一部分進行有限元分析。三通、彎管和焊縫的物理模型完全按照設計圖紙的尺寸來建立,如圖1(b)中所示。
三通和彎管材質為ASME標準的SA-182F11 CL2,焊縫材質保持與管件材質一致。管件材料的熱膨脹系數、彈性模量、導熱系數、泊松比和密度等特性參數參照ASME-SECTION Ⅱ PART-D中的材料特性進行選取。
圖1 管道實物和三維物理模型
2.2單元選擇和網格劃分
在管道結構分析中有限元模型選擇了8 節點六面體結構分析單元Solid185單元。Solid185 單元用于構造三維實體結構模型,該單元具有塑性、超彈性、應力剛化、蠕變、大變形和大應變等功能。對于管道溫度場分析的有限元模型,選擇8 節點的等參單元Solid 70單元。Solid 70單元可用于三維的穩態或瞬態熱分析問題,并可以補償由于恒定速度場質量輸運帶來的熱流損失。管道物理模型的網格單元數為387 040,網格節點總數為413 987。對三通管和彎管連接的焊縫處進行網格加密處理,以確保滿足計算精度要求。管道整體網格細節如圖2所示。
圖2 管道網格模型
2.3邊界約束條件
管道應力分析模型邊界條件如圖3所示,彎管端面A施加全位移約束、管道內表面B施加垂直表面方向的內壓力、三通管兩個端面C和D分別施加垂直端面向外的拉力。三通端面上施加的壓強可由Lame方程進行確定,Lame方程計算公式如下:
(1)
式中:P為設計壓力或工作壓力,Mpa;K為端面處管外徑與管內徑之比;P2為三通管端面處受到的壓力,Mpa。
圖3 邊界條件
在設計工況和使用工況下管道應力分析模型邊界條件具體設置如表1所示。
表2 溫度分析邊界條件管道溫度場分析模型的內表面的溫度在設計工況下設置為設計溫度,在使用工況下設置為工作溫度,由于管道外表面沒有保溫,根據環境條件設置自然對流換熱系數。為了得到管道和焊縫應力場和溫度場隨時間變化的關系,則在非穩態條件下設置計算總時間為1000s,時間步長為50s。在設計工況和使用工況下管道溫度模型邊界條件具體設置如表2中所示。
表2 溫度分析邊界條件
3 .結果分析
3.1溫度分布
圖4中給出了使用工況下50s和1000s時刻管道溫度分布情況。從圖4(a)中可以看出管道內壁最高溫度為110℃,管道外壁最低溫度為34.2℃,管道內外溫差75.8℃。最低溫度出現在彎管內側。從圖4(b)中可得到在1000s時刻管道外壁最低溫度為104.9℃,管道內外溫差15.1℃。在1000s時刻管道整體溫度分布較50s時刻更為均勻,管道內外壁溫差降低60.7℃,最低溫度由彎管內側移至三通接口處。
圖4 使用工況溫度分布
圖5中同樣給出了設計工況下50s和1000s時刻管道溫度分布情況。從圖5(a)中可以看出管道內壁最高溫度為260℃,在50s時刻管道外壁最低溫度為50.5℃,管道內外溫差209.5℃。最低溫度同樣出現在彎管內側。從圖5(b)中可得到在1000s時刻管道外壁最低溫度為245.8℃,管道內外溫差14.2℃。在1000s時刻管道整體溫度分布較50s時刻更為均勻,管道內外壁溫差降低195.3℃,最低溫度由彎管內側移至三通接口處,與使用工況下相似。
圖5 設計工況溫度分布
圖6中給出了兩種工況下管道各個時刻的最低溫度隨時間變化關系。從圖中可以看出,隨著時間的增加,管道溫度不斷升高。在使用工況下,300s之前升溫速度較快,300s之后溫度逐步平穩,700s之后溫度基本不再變化,在1000s時刻溫度達到104.9℃,此時管道溫度已經達到平衡狀態。在設計工況下,400s之前升溫速度較快,400s至800s之間升溫速度較慢,800s之后溫度也基本不再變化,在1000s時刻溫度達到245.8℃。
圖6 兩種工況下管道溫度隨時間的變化
3.2應力分布
圖7中是管道在使用工況下50s和1000s時刻應力分布情況。從圖7(a)中可以看出,在50s時刻,管道最大應力為430.1Mpa,最大應力點出現在彎管外側表面處;焊縫處應力水平較焊縫兩側有明顯的升高,焊縫處最大應力為305Mpa,最大應力點出現在焊縫外表面處。從圖7(b)中可以得到,在1000s時刻,管道最大應力為380.8Mpa,最大應力點出現在彎管內側表面處;焊縫處最大應力為210.8Mpa,最大應力點出現在焊縫外表面處。對比圖7(a)和(b)發現,隨著時間增加管道最大應力降低了49.3Mpa,焊縫處最大應力降低了94.2Mpa,管道最大應力點由彎管處外表面轉移到內表面,焊縫最大應力點基本沒有變化。
圖7 使用工況應力分布
圖8中是管道在設計工況下50s和1000s時刻應力分布情況。從圖8(a)中可以看出,在50s時刻,管道最大應力為684.3Mpa,最大應力點出現在彎管內側表面處;焊縫處應力水平較焊縫兩側有明顯的升高,焊縫處最大應力為529.8Mpa,最大應力點出現在焊縫外表面處。從圖8(b)中可以得到,在1000s時刻,管道最大應力為454.2Mpa,最大應力點出現在彎管外側表面處;焊縫處最大應力為259.2Mpa,最大應力點出現在焊縫外表面處。對比圖8(a)和(b)發現,隨著時間增加管道最大應力降低了230.1Mpa,焊縫處最大應力降低了270.6Mpa,管道最大應力點由彎管處內表面轉移到外表面,焊縫最大應力點基本沒有變化。
圖8 設計工況應力分布
圖9中給出了使用工況和設計工況下管道和焊縫最大應力隨時間變化情況。圖9(a)中是管道整體最大應力隨時間變化情況,在兩種工況下,管道最大應力都是隨著時間增加而降低;在設計工況下,400s之前管道應力下降速率較大,400s之后管道應力下降速率較小,400s之后管道最大應力基本不發生變化;在使用工況下,300s之前管道應力下降速率較大,300s之后管道應力基本不再變化。圖9(b)中是焊縫最大應力隨時間變化情況,焊縫最大應力隨著時間增加而降低;在設計工況下,500s之前焊縫應力下降速率較大,500s之后下降速率降低,500s之后焊縫最大應力基本不再變化;在使用工況下,300s之前焊縫應力下降速率較大,300s之后焊縫最大應力基本不發生變化。對照圖6和圖9發現,管道和焊縫的應力速率變化與管道溫度速率變化有相互對應關系,溫度變化速率大則應力變化速率也大,溫度變化速率小則應力變化速率也小。
圖9 兩種工況下管道和焊縫最大應力隨時間的變化情況
3.3強度評定
對兩種工況下管道和焊縫應力集中處分別進行強度評定,評定依據為JB4732-1995(2005年確認)《鋼制壓力容器—分析設計標準》中關于彈性應力分析法的評估策略,利用線性化原理對應力集中處進行應力的分類評定。首先,通過最大應力節點,并沿著壁厚最短距離設置線性化路徑;其次,三通和彎管連接處焊縫由于幾何不連續,因此沿相交處所取截面結果所得的薄膜應力為一次局部薄膜應力PL,對應一次局部薄膜應力強度SⅡ;管道總體結構不連續區的彎曲應力應該歸為二次應力的范疇,為了滿足JB4732-1995(2005年確認)《鋼制壓力容器—分析設計標準》中對各應力強度依次逐級評定的要求,對薄膜應力加彎曲應力加二次應力按照SⅣ處理。應力評定強度結果如表3所示。
從表3中應力評定結果可以得出,在使用工況下管道管件和焊縫處均滿足應力強度要求;在設計工況下管道管件滿足應力強度要求,焊縫處在50s時刻應力評定為不合格,說明在設計工況下管道焊縫處初始升溫過程中可能會出現開裂等失效情況,容易造成人員和財產損失。
4. 分析和討論
通過對高壓管道和焊縫進行溫度分析、應力分析和強度評定,在得到分析結果后發現該管道在設計和使用中存在以問題:在管道設計工況下,對管道和焊縫進行應力分析得到應力分布情況,由于管道焊縫處有未焊滿,導致在焊縫處存在應力集中現象;在對管道焊縫升溫過程中進行線性化強度評定,發現在升溫初始50s時焊縫處強度評定不合格,不滿足強度要求。出現這種情況的原因為,在管道初始升溫階段管道內外溫差較大,管道內二次應力水平較高,再加上高強度的機械載荷和局部應力集中現象,從而導致在焊縫等結構不連續處出現強度評定不合格。為了保證管道在設計工況下能夠安全運行,應當在焊縫處進行補焊作業,使焊縫表面與管道表面平齊。當焊縫填滿后,一方面焊縫強度得到提升,另一方面可以消除管道焊縫處結構不連續,降低應力集中影響。
5. 結論
以某化工企業一條高溫高壓管道和焊縫為研究對象,基于彈性分析策略評價了管道和焊縫處高應力區的應力強度,并分析了該管道和焊縫的溫度分布和應力分布情況,得到以下結論:
在使用工況下,隨著時間增加管道溫度不斷升高,1000s時管道溫度為104.9℃,內外溫差15.1℃;在設計工況下,隨著時間增加管道溫度不斷升高,1000s時管道溫度為245.8℃,內外溫差14.2℃;管道內外溫差隨著時間增加而降低。
該管道在彎管和焊縫處存在應力集中現象,在使用工況下,彎管最大應力為430.1Mpa,焊縫最大應力為305Mpa;在設計工況下,彎管最大應力為684.3Mpa,焊縫最大應力為529.8Mpa;管道和焊縫最大應力隨著時間增加逐漸減小。
對管道和焊縫升溫過程中進行線性化強度評定,在使用工況下管道管件和焊縫處均滿足應力強度要求;在設計工況下管道管件滿足應力強度要求,管道焊縫處在50s時刻應力評定為不合格,不滿足強度要求。
為了保證管道在設計工況下能夠安全運行,應當在焊縫處進行補焊作業,使焊縫表面與管道表面平齊。
免責聲明:本網站所轉載的文字、圖片與視頻資料版權歸原創作者所有,如果涉及侵權,請第一時間聯系本網刪除。
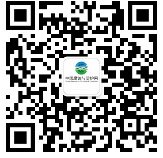
官方微信
《中國腐蝕與防護網電子期刊》征訂啟事
- 投稿聯系:編輯部
- 電話:010-62316606-806
- 郵箱:fsfhzy666@163.com
- 中國腐蝕與防護網官方QQ群:140808414