單晶高溫合金的高溫強度、蠕變性能和抗疲勞性能優異,是制造先進航空發動機渦輪葉片的首選材料[1, 2]。隨著航空發動機推重比的增大,渦輪入口溫度的不斷提高,單晶葉片的工作環境愈趨惡劣。在服役過程中產生的熱疲勞和熱腐蝕等因素使表面出現裂紋或蝕坑等損傷,導致性能下降甚至發生斷裂[3]。內腔結構復雜的單晶葉片鑄造成本昂貴[4],且廢品率極高。如果將損傷的葉片直接報廢,會造成巨大的材料浪費和經濟損失。因此,修復受損葉片,延長其使用壽命,可降低發動機的運行和維護成本,對國際建設具有重大意義。
單晶高溫合金表面的缺陷是一種局部損傷,常用焊接方法修復,涉及的方法有熔焊(包括鎢極惰性氣體保護電弧焊、真空電子束焊和激光焊等)、釬焊和瞬時液相擴散焊(TLP)等。使修復區形成與母材單晶高溫合金基體一致的無缺陷單晶組織,具有與母材單晶高溫合金相同或相近的性能,一直是單晶高溫合金修復的目標,也是單晶高溫合金領域的重要研究課題。本文針對單晶高溫合金表面缺陷的修復問題,結合近年來國內外相關研究成果,全面闡述了用各類焊接方法修復后修復區的顯微組織和力學性能,分析了各種修復方法(工藝)存在的問題及局限性,并展望了單晶高溫合金表面缺陷修復的發展方向。
1 單晶高溫合金典型的表面缺陷
單晶高溫合金渦輪葉片的工作環境十分復雜,在高溫下不僅受到包括機械離心力以及共振等多種應力的作用,還受到含硫燃氣的熱腐蝕作用,使其表面出現裂紋或蝕坑等缺陷。
單晶高溫合金典型的表面缺陷是裂紋。單晶葉片表面通常有大量氣膜孔用來加速葉片冷卻從而提高其耐溫性能,但是在這些氣膜孔的邊緣存在較大的應力集中[5]。在單晶葉片服役過程中,表面應力集中區域會萌生大量細小的微裂紋。在高溫高應力工作環境下微裂紋沿著特定方向持續擴展,逐漸聚集成較大的裂紋[6]。對裂紋擴展行為的深入研究發現,單晶高溫合金中的熱疲勞裂紋的擴展方向與枝晶的生長方向呈45°角,而且在熱循環下限溫度不變的情況下隨著上限溫度的提高,熱疲勞裂紋的萌生壽命縮短而擴展速率提高[7];在熱機械疲勞試驗中,裂紋通常沿局部區域滑移帶在{111}面內向合金內部延伸擴展[8]。單晶葉片中裂紋的寬度一般小于100 μm,如圖1所示[9],若不及時修復將造成葉片斷裂失效[10~12]。
圖1 CMSX-4單晶高溫合金中裂紋擴展形貌[9]
單晶高溫合金表面的另一種典型缺陷是蝕坑。作為熱端部件,單晶葉片在高溫含硫燃氣的作用下表面會發生熱腐蝕。根據相關相圖,S與Ni生成Ni3S2和NiS等硫化物,在高溫有氧條件下還會生成Ni2SO4等硫酸鹽產物。這些硫化物和硫酸鹽沉積在葉片表面,使原始單晶結構遭到破壞[13];而且未燃盡的燃料質點與單晶高溫合金中合金元素結合生成碳化物,使表面的耐蝕性能降低。研究發現,進行100 h的熱腐蝕實驗后,在DD6表面生成兩層腐蝕產物,外層為NiO、Al2O3、CrO等氧化物,內層為NiS和Ni2SO4等硫化物與硫酸鹽。同時,近腐蝕層基體中Al的消耗和γ′相立方化程度的降低使力學性能下降[14]。在服役過程中生成的腐蝕產物極易剝落成為蝕坑,在通常情況下腐蝕層較淺的蝕坑其形貌一般寬而淺,其寬度一般大于200 μm,深度約為100 μm。但是,在蝕坑部位往往產生許多深入基體的裂紋,如圖2所示[15]。
圖2 典型蝕坑形貌及延伸裂紋[15]
2 熔焊修復
2.1 熔焊修復的工藝
熔焊是目前研究最多的修復工藝,包括鎢極惰性氣體保護電弧焊、電子束焊和激光焊等。
2.1.1 鎢極惰性氣體保護電弧焊
作為一種傳統的高溫合金焊接技術,鎢極惰性氣體保護電弧焊(TIG,Tungsten Inert Gas)操作簡便、成本低,最早用于單晶高溫合金表面缺陷的修復。
對單晶高溫合金TIG焊修復的研究,主要集中在熱輸入條件對修復區凝固組織的影響。研究表明,降低熱輸入有利于修復區形成單晶組織和降低裂紋敏感性。減小焊接電流是降低熱輸入的有效方法。焊接電流減小可提高熔池凝固界面前沿的溫度梯度[16],使雜晶不易形核且可避免產生裂紋。Y. Fujita用TIG焊對CMSX-4單晶表面進行重熔,在焊接電流為50 mA、焊接速度為10 mm/s的條件下得到了無裂紋且雜晶較少的凝固組織[17]。此外,提高焊接速度以降低單位時間內修復區的熱輸入,也有相同的效果[18, 19]。美國橡樹嶺國家實驗室的S. S. Babu研究了TIG焊修復區內雜晶的生成和裂紋的形成與熔池冷卻速度的關系(圖3)。結果表明,快速冷卻條件下的熱輸入量低,雜晶和裂紋較少[20]。值得注意的是,由于TIG焊操作簡便可進行自動焊接,Liburdi公司已經實現了TIG焊補長修復JT9D發動機單晶葉片的工程應用[21]。
圖3 不同冷卻速度條件下TMS-75單晶高溫合金TIG焊修復后形貌[20]
但是,用TIG焊修復單晶高溫合金表面缺陷也有較多的不足之處。TIG電弧的能量密度低、熱作用范圍大,修復區的凝固組織難以生成單晶,雜晶和裂紋等缺陷使修復后的力學性能降低。雖然通過改變工藝參數和降低熱輸入可避免裂紋的產生,但是到目前雜晶的問題仍然沒有解決。因此,TIG焊只能用于修復低應力損傷區,如葉片尖端的補長修復[22, 23],難以修復高溫高應力工作區表面的裂紋或燒蝕坑。
2.1.2 真空電子束焊
真空電子束焊屬于高能束熔化焊,有比TIG焊高的溫度梯度,有利于抑制修復區中雜晶等缺陷的生成[24]。同時,在高真空條件下,合金元素燒損少,工件不易氧化[25]。近年來,在單晶高溫合金表面缺陷修復領域真空電子束焊受到了普遍關注。
與TIG焊類似,真空電子束焊對修復區組織結構影響最大的工藝參數是電子束流和焊接速度。在一般情況下,電子束流增大將增加修復區熱輸入,產生較多的雜晶和裂紋[18, 26]。焊接速度對雜晶形成的影響則較為復雜。焊速增大雖然加快固液界面的移動,促進雜晶的形成[27],但是又使熱輸入量減少和溫度梯度增大,降低雜晶的形成傾向[18, 22];對比結果表明,溫度梯度對雜晶的影響比固液界面移動速率更大,因此在實際修復過程中焊速的提高通常能降低修復區內的雜晶含量和減少裂紋數量。
事實上,電子束焊修復容易產生裂紋的冶金原因,正在于修復區內無法避免雜晶。合金元素容易在晶界處偏析,在高溫和復雜應力環境下晶界成為裂紋擴展的通道,最終使單晶高溫合金工件斷裂失效[27](圖4)。雖然可用散焦電子束[22]或對基體預熱[27]降低熱應力以抑制修復區內部裂紋的生成,但同時會降低修復區內部的溫度梯度而使雜晶增多。另外,真空電子束焊對修復表面的粗糙度要求較高,而且設備昂貴,對使用環境高真空要求苛刻,極大地制約了其在單晶高溫合金領域的應用。
圖4 PWA1480單晶高溫合金電子束焊修復組織[27]
2.1.3 激光焊
近年來,激光焊在單晶高溫合金修復領域得到了大量研究和應用。激光束與電子束都屬于高能束,修復區熔池溫度梯度高,有利于抑制修復區內雜晶的生成,而且不需要真空等條件,可操作性更強。激光熔凝和激光熔覆是激光焊修復中常用的兩種方法,雖然二者在物理本質上都屬于熔池的快速凝固過程,但是其工藝有較大的不同。
激光熔凝是用激光束掃過單晶高溫合金表面的待修復區,使其快速重熔,凝固后即可修復表面微裂紋等缺陷[28, 29]。激光熔凝工藝的原理,如圖5所示[30]。迄今為止,針對單晶高溫合金的激光熔凝修復工藝參數(激光功率和掃描速率)進行了深入研究。降低激光功率或提高掃描速度可增大修復區的溫度梯度并降低固液界面的移動速率,從而抑制雜晶的生成和減少裂紋敏感性,甚至能得到無雜晶無裂紋的單晶組織[31~35]。
圖5 (a)激光熔凝工藝示意圖和(b)激光熔凝熔池剖面[30]
在激光熔凝時同步添加熔覆材料或在待修復區預置熔覆材料,使待修復區表面和熔覆材料一起快速熔凝,便是激光熔覆,其工藝原理如圖6所示[36]。熔覆材料的成分與基體相同或相近(如表1所示),以利于恢復基體單晶組織并得到相同或相近的性能。激光熔覆工藝不僅可通過單層熔覆修復表面微裂紋等小尺寸缺陷,還能通過多層熔覆修復蝕坑等大尺寸缺陷,適用范圍更廣[37]。
圖6 單層激光熔覆工藝示意圖[36]
表1 幾種單晶高溫合金基體與熔覆材料的主要化學成分(質量分數, %)
采用激光熔覆修復單晶高溫合金表面缺陷時,激光功率和掃描速率對修復區單晶組織生長的影響規律與激光熔凝相同。需要注意的是,在激光熔覆過程中除激光功率和掃描速率外,適當的送粉速率和熔覆層搭接率對于修復區內單晶組織的生長也十分重要。送粉速率過高會使熔覆層的內雜晶增多,因為送粉過快使粉末形成屏蔽面導致透光率下降和基體的重熔量不足[38]。Hao Chen等提高激光功率和掃描速度,有效降低了熔覆層內雜晶的含量[36]。在熔覆層搭接率適當的情況下在各熔覆層內都能得到與基體晶體取向一致的單晶組織,除頂部出現微量雜晶外在層間沒有雜晶和裂紋,如圖7所示[39]。
圖7 激光熔覆單層(a)EBSD圖像, (b)宏觀截面, (c)微觀組織; 三層(d)EBSD圖像, (e)宏觀截面, (f)微觀組織[39]
目前對單晶高溫合金激光修復后力學性能的研究較少,因為單晶高溫合金的高溫力學性能在很大程度上取決于強化相γ′相的形狀和尺寸。激光修復過程屬于快速凝固過程,修復后雖然能生成與基體晶體取向一致的單晶組織,但是γ′相的沉淀析出不充分使其力學性能不高[45]。雖然對修復后的單晶高溫合金進行固溶和時效處理可使γ′相充分析出,但是在激光修復過程中產生的較大內應力使熱處理后的修復區將出現了大量再結晶區域[43]。這也限制了激光修復技術在單晶高溫合金領域的應用。激光焊更適用于單晶葉片表面的淺層微裂紋和葉片尖端等低應力區域的修復。
2.2 基體晶體取向對修復區組織的影響
在理論上,熔焊修復時的熱流方向應該與單晶基體的擇優生長方向[001]一致,以確保在該方向上產生較大的溫度梯度,使修復區內的單晶組織沿著[001]定向生長。但是在實際的修復過程中,基體待修復表面的法向并非沿著[001]方向,使溫度梯度方向與[001]方向有一定的偏差,導致修復區內的組織結構尤其是雜晶的含量和分布發生較大的變化[46]。研究基體晶體取向對修復區組織結構的影響,可揭示雜晶的含量和分布隨著基體晶體取向變化的規律,在此基礎上選擇工藝參數實現高質量修復,為完成修復提供理論指導。
在單晶高溫合金的修復過程中,溫度梯度與[001]方向之間的偏差方向可表示為[100]、[010]和[001]方向的矢量和。因此,研究基體晶體取向對修復區組織結構影響時,可看作基體表面分別繞[100](x軸)、[010](y軸)和[001](z軸)旋轉不同角度,如圖8所示[29]。
圖8 單晶基體繞[100]、[010]和[001]軸旋轉示意圖[29]
當基體表面繞[100](x軸)旋轉時,隨著旋轉角度的增大修復區內溫度梯度沿[001]的分量減小,雜晶生成的趨勢增加,裂紋敏感性提高[47]。S. MOKADEM發現,當繞[100]軸旋轉角度達到45°時在修復區的底部出現大量的雜晶,嚴重影響修復后的性能[30]。當基體表面繞[010](y軸)方向旋轉時,修復區的雜晶隨著旋轉角度的增加而減少。L. Wang發現,雜晶往往分布在不同晶區的交點和交線處,隨著繞[010]軸旋轉角度的增加,晶區交點和交線明顯減少,使雜晶的含量降低;當旋轉角度達到45°時,可得到無雜晶的修復區[28, 29]。當基體表面繞[001](z軸)方向旋轉時修復區內雜晶的總含量不變,但是原本散亂分布的雜晶出現了聚集,這也是晶區交點和交線分布的變化所致。基體繞[001]和[010]軸旋轉不同角度得到的激光熔凝修復組織,如圖9所示[29]。
圖9 單晶激光熔凝區橫截面[29]
2.3 修復區熔池的數值模擬
在熔焊修復過程中,熔池內液體的流動行為和溫度場的分布比較復雜,而且熔池有一定的移動速度,只進行實驗難以得到高質量修復區的工藝參數窗口。隨著計算材料學的發展,數值模擬技術在單晶高溫合金熔焊修復領域得到了廣泛的應用。
國內外學者采用數值模擬技術并結合熔池的幾何模型(圖10)[35]從理論上研究了工藝參數對修復區單晶組織生長行為的影響和相互作用,預測了雜晶等缺陷的分布[31, 47],從而在減少實驗的情況下得到高質量修復的工藝窗口。T. D. ANDERSON利用數值模擬技術研究了CMSX-4電子束焊修復區內雜晶的分布規律,發現修復區內不同枝晶生長方向交匯處的雜晶較多[18]。其原因是,在這些位置枝晶的生長軸與最大熱流方向不平行,即形成了離軸熱流[30]。與枝晶生長方向平行于最大熱流方向的情況相比,離軸熱流會降低該處的溫度梯度并提高固液界面的移動速率,導致大量雜晶的生成[48]。為了驗證數值模擬計算結果的正確性,J. N. DuPont模擬了[100](掃描方向)-240 W(激光功率)-1 mm/s(掃描速率)條件下熔池內枝晶的生長方向,即熔池晶區分布,并與相同參數下得到的CMSX-4單晶激光熔凝組織比較。結果表明,二者的晶區分布高度一致,如圖11所示[48]。L. Wang結合熱場模擬得到了基體晶體取向不同的修復區雜晶含量的分布規律,如圖12所示[28],與在相同實驗條件下得到的熔凝組織中雜晶的分布相近[29]。M. G?umann采用數值模擬技術得到了雜晶的形成規律,通過擬合得到了修復區組織結構與激光功率P、掃描速率Vb和預熱溫度T0等工藝參數的函數關系(圖13),確定了修復區單晶生長的工藝窗口,為工程應用提供了理論基礎[49]。
圖10 單晶修復區熔池幾何模型[35]
圖11 參數為[100]-240W-1 mm/s條件下實際與模擬的激光熔凝組織對照[48]
圖12 基體表面旋轉不同角度時,激光熔凝組織中雜晶含量的模擬分布情況[28]
圖13 修復區組織結構與激光功率P、掃描速率Vb和預熱溫度T0的函數關系[49]
2.4 熔焊修復的不足之處
熔焊修復操作簡便,電子束與激光束等高能束可產生較大的溫度梯度,有利于修復區內單晶組織生長,在單晶高溫合金修復領域以及得到了實際應用。但是,采用熔焊技術進行單晶高溫合金表面缺陷修復,雜晶的生成和裂紋的產生是兩個亟待解決的問題。
1) 雜晶破壞了單晶結構,使修復后單晶高溫合金的力學性能降低,是目前熔焊修復的主要難題。熔焊修復利用了定向凝固中的柱狀晶向等軸晶轉變(Columnar to Equiaxed Transition,CET)理論[50]
式中為溫度梯度,為凝固速率,為與材料有關的系數,K為臨界值。
與滿足式(1)時熔池內的凝固組織呈柱狀晶生長而得到單晶組織;不滿足此條件時熔池內的凝固組織發生柱狀晶向等軸晶生長的轉變,如圖14所示[51]。分析已有的研究結果發現,雜晶通常出現在修復區表層和修復區內不同枝晶生長方向的交匯處,因為這些位置的溫度梯度低且凝固快,即與不滿足式(1)的條件。根據CET理論,此時凝固組織極易發生柱狀晶向等軸晶生長的轉變,從而在修復區表層和修復區內不同枝晶生長方向的交匯處生成大量與基體晶體取向不同的雜晶。調整工藝參數或基體取向能控制熔池內的溫度梯度和凝固速率,可減少修復區內的雜晶甚至在某些特定參數下使基本沒有雜晶、在修復區內生成單晶高溫合金晶向一致的單晶組織。但是,修復區內較大的殘余應力使后續熱處理時在修復區出現再結晶,使修復后的單晶高溫合金不能在高溫高應力條件下應用。
圖14 不同溫度梯度與凝固速率下的凝固組織[51]
2) 裂紋的生成是鎳基單晶高溫合金熔焊修復過程中面臨的另一個難題。單晶高溫合金的Al、Ti含量較高,使其對裂紋有極高的敏感性。在熔焊修復過程中Al、Ti等元素在晶界偏析或偏聚生成低熔共晶。在凝固階段,在拉應力的作用下在雜晶晶界或生長方向偏離角度較大的相鄰枝晶間極易生成凝固裂紋(圖15)和液化裂紋[39],使修復失敗。
圖15 激光熔覆過程中凝固裂紋形成機理示意圖[39]
3 釬焊修復
釬焊修復單晶高溫合金使用的釬料是低熔點合金,修復時釬料熔化而基體不熔化,液態釬料潤濕填充修復區內的間隙,經降溫凝固過程,實現釬焊修復[52]。
釬焊修復是在較低的溫度下對基體均勻加熱,對基體的組織結構影響不大,而且殘余熱應力較小,工件變形量小,可避免熔焊時基體中高含量的Al、Ti使修復區出現凝固裂紋和液化裂紋[53]。目前國內外有關單晶高溫合金釬焊連接的研究報道較多,但是關于單晶高溫合金釬焊修復的研究報道較少。現有的研究,主要是研發單晶高溫合金修復用新型釬料。
單晶高溫合金用的釬料,通常使用B[54, 55]、Si[56]作為降熔元素。但是B、Si元素在Ni基體中的固溶度很小,加之單晶母材中的快速擴散通道少,釬焊后接頭內殘留的大量低熔點脆性化合物使單晶高溫合金釬焊修復后的性能降低。B. LAUX從相圖發現,Mn元素與鎳基高溫合金具有良好的相容性,并據此研發出新型Ni-Mn體系釬料。使用該體系釬料修復Rene N5單晶,與使用含硼釬料D-15(Ni-15Cr-10Co-3.4Ta-3.5Al-2.3B)相比,修復區中沒有出現脆性硼化物(圖16),重熔溫度提高[57];分析用Ni-Mn系釬料修復單晶高溫合金過程中組織的演變時發現,與使用D-15釬料相同,隨著保溫時間的延長修復區組織由枝晶生長逐漸變為平面生長;雖然液相也沒有完全消耗,但是因為Mn在Ni中完全固溶且Mn的擴散很慢,液態釬料在冷卻凝固過程中不會析出低熔共晶組織,釬焊修復后不會產生凝固裂紋,使修復后的單晶高溫合金具有一定的力學性能[58, 59]。
圖16 不同釬料釬焊修復Rene N5單晶后微觀組織[57]
綜合以上的分析,用釬焊修復單晶高溫合金,利用的是液態釬料對孔隙的潤濕填充。雖然在修復過程中釬料與基體在一定程度上互擴散,但是在修復區內并不能生成與基體相同的單晶組織。脆性化合物和晶界使修復后的高溫合金難以恢復到單晶母材優異高溫力學性能。
4 瞬時液相擴散焊修復(TLP)
采用瞬時液相擴散(Transient Liquid Phase,TLP)連接技術修復單晶高溫合金表面缺陷時,先將低熔點的中間層材料預置于待修復區,中間層材料熔化形成的液相填充修復區,在長時間保溫期間液相與母材間的固-液互擴散實現了等溫凝固。TLP技術與釬焊的區別在于,前者為等溫凝固,后者為降溫凝固。同時,TLP成分和組織結構的均勻化使修復區最終生成與基體一致的單晶組織,實現了高性能的修復。典型的TLP過程,如圖17所示[60]。
圖17 典型TLP過程示意圖[60]
TLP連接技術曾被希望用于單晶渦輪葉片的連接制造,相關的研究報道較多,但是針對單晶高溫合金缺陷TLP修復的研究報道較少。已有的研究,主要是關于TLP過程中修復區內組織結構的演變,以及新型中間層修復材料的研發。
TLP中間層材料常用的降熔元素,是原子半徑較小且降熔效果好的B元素[61, 62]。在TLP過程中B向基體擴散,修復區內的基體表面逐漸外延凝固,由初始階段的胞狀生長逐漸變為平面生長。隨著保溫時間的延長等溫凝固區的寬度增加,修復區中心的殘余液相區寬度減小,如圖18所示[63]。
圖18 隨保溫時間延長,固液界面示意圖[63]
B在Ni基體中的固溶度很低,在等溫凝固過程中在近基體表面析出大量的硼化物[64, 65]。這些硼化物在等溫凝固后經過長時間的擴散均勻化才能消除。因此,有研究者針對單晶高溫合金的TLP修復開發了新型中間層材料的。例如,Dinkel等用Ni-(20~23)%Ge(質量分數)合金對PWA1483和Rene N5進行TLP修復,在1160~1200℃保溫48~55 h后在修復區生成了與基體晶體取向一致的單晶組織。修復后其980℃抗拉強度達到基體的92%以上,基本上恢復了單晶高溫合金的性能[66, 67]。
綜上所述,用TLP可使修復區單晶化,甚至使其性能達到母材的90%以上,是一種理想的單晶高溫合金修復技術,但是,擴散均勻化所需的保溫時間過長。因為單晶高溫合金中沒有晶界作為原子的快速通道,即使B之類的小半徑原子的擴散也十分緩慢,修復尺寸為30~40 μm的缺陷需要保溫至少24 h以上;如果修復寬度繼續增加不僅保溫時間大幅度增加,甚至在修復區組織中出現晶界,導致修復失敗,如圖19所示[63]。TLP過程的動力學緩慢,嚴重局限了其在單晶高溫合金修復尤其是大尺寸缺陷修復中的應用。
圖19 不同保溫時間下,修復區(原始尺寸為300 μm)的微觀組織[63]
5 結論和展望
單晶高溫合金優異的力學性能源于其獨特的單晶組織,因此恢復與基體相同的單晶組織是單晶高溫合金修復的目標。
熔焊修復方法操作簡便,而且電子束和激光束等高能束可產生較大的溫度梯度,有利于修復區內單晶組織生長。但是,熔焊修復無法避免產生雜晶與出現裂紋,因此只適用于單晶高溫合金表面淺層微裂紋修復或單晶葉片尖端等低應力區的補長修復。
釬焊修復的殘余熱應力小,可避免出現裂紋。但是,修復區內殘留的大量低熔點脆性化合物使修復后的性能不足原單晶性能的50%。
瞬時液相擴散焊(TLP)既能實現修復區的單晶化又能避免裂紋等問題,且修復后高溫力學性能良好。但是,TLP實現修復區成分均勻化和結構單晶化需要數十小時甚至數天,過程的動力學緩慢、工藝性差。如何在TLP原理的基礎上從材料和工藝入手加速修復過程動力學,是TLP修復迫切需要解決的問題和發展方向。
參考文獻
1 Xia W S, Zhao X B, Yue L, et al. Microstructural evolution and creep mechanisms in Ni-based single crystal superalloys: A review [J]. J. Alloy. Compd., 2020, 819: 152954
2 Zhang J, Wang L, Wang D, et al. Recent progress in research and development of nickel-based single crystal superalloys [J]. Acta Metall. Sin., 2019, 55(9): 1077
2 張健, 王莉, 王棟等. 鎳基單晶高溫合金的研發進展 [J]. 金屬學報, 2019, 55(9): 1077
3 Gallardo J M, Rodríguez J A, Herrera E J. Failure of gas turbine blades [J]. Wear, 2002, 252(3-4): 264
4 Viswanathan I, Gandy D, Findlan S. Power industry experiences surge in welding research [J]. Weld. J., 2003, 82(9): 40
5 Jiang K H, Chen J W, Jing F L, et al. Thermomechanical fatigue on the nickel based single crystal superalloy DD6 with film cooling hole [J]. Journal of Aerospace Power, 2019, 34(5): 980
5 蔣康河, 陳競煒, 荊甫雷等. 鎳基單晶高溫合金DD6氣膜孔熱機械疲勞試驗 [J]. 航空動力學報, 2019, 34(5): 980
6 Cervellon A, Hémery S, Kürnsteiner P, et al. Crack initiation mechanisms during very high cycle fatigue of Ni-based single crystal superalloys at high temperature [J]. Acta Mater., 2020, 188: 131
7 Liu Y, Yu J J, Xu Y, et al. Thermal fatigue behavior of single-crystal superalloy [J]. Rare Metal Mat. Eng., 2009, 38(1): 59
7 劉源, 于金江, 徐巖等. 單晶高溫合金的冷熱疲勞裂紋生長行為研究 [J]. 稀有金屬材料與工程, 2009, 38(1): 59
8 Zhang J, Zhao Y S, Jia Y L, et al. Thermo-mechanical fatigue behaviors of a nickel-base single crystal superalloy [J]. Materials for Mechanical Engineering, 2013, 37(8): 41
8 張劍, 趙云松, 賈玉亮等. 一種鎳基單晶高溫合金的熱機械疲勞行為 [J]. 機械工程材料, 2013, 37(8): 41
9 Hong H U, Kang J G, Choi B G, et al. A comparative study on thermomechanical and low cycle fatigue failures of a single crystal nickel-based superalloy [J]. Int. J. Fatigue, 2011, 33(12): 1592
10 Zhang Y L, Wang X G, Li J G, et al. The low-cycle fatigue deformation mechanisms of two single crystal superalloys at room temperature and 600℃ [J]. Scr. Mater., 2019, 171: 122
11 Pei H Q, Wen Z X, Wang Z H, et al. Transient thermal fatigue crack propagation behavior of a nickel-based single-crystal superalloy [J]. Int. J. Fatigue, 2020, 131: 105303
12 Chen X S, Sakaguchi M. Transition behavior from Mode I cracking to crystallographic cracking in a Ni-base single crystal superalloy [J]. Int. J. Fatigue, 2020, 132: 105400
13 Montero X, Ishida A, Meissner T M, et al. Effect of surface treatment and crystal orientation on hot corrosion of a Ni-based single-crystal superalloy [J]. Corrosion Sci., 2020, 166: 108472
14 Shi Z X, Liu S Z, Wang X G, et al. Corrosion behavior of the second generation single crystal superalloy DD6 in hot gas [J] J. Iron Steel Res., 2015, 27(5): 61
14 史振學, 劉世忠, 王效光等. 第2代單晶高溫合金DD6的燃氣熱腐蝕行為 [J]. 鋼鐵研究學報, 2015, 27(5): 61
15 Eliaz N, Shemesh G, Latanision R M. Hot corrosion in gas turbine components [J]. Eng. Fail. Anal., 2002, 9(1): 31
16 Ma C Y, Tian Z L, Du Z Y, et al. Effect of heat input on structure and mechanical properties of welded joint in a 800 MPa grade RPC steel [J]. Transactions of The China Welding Institution, 2004, 25(2): 23
16 馬成勇, 田志凌, 杜則裕等. 熱輸入對800 MPa級鋼接頭組織及性能的影響 [J]. 焊接學報, 2004, 25(2): 23
17 Fujita Y, Saida K, Nishimoto K. Study of microstructure in surface-melted region of Ni-base single crystal superalloy CMSX-4 [J]. Materials Science Forum, 2006, 512: 313
18 Anderson T D, Dupont J N, Debroy T, et al. Stray grain formation in welds of single-crystal Ni-base superalloy CMSX-4 [J]. Metall. Mater. Trans. A-Phys. Metall. Mater. Sci., 2010, 41A(1): 181
19 Anderson T D, Dupont J N. Stray grain formation and solidification cracking susceptibility of single crystal Ni-base superalloy CMSX-4 [J]. Weld. J., 2011, 90(2): 27s
20 Babu S S, David S A, Park J W, et al. Joining of nickel base superalloy single crystals [J]. Sci. Technol. Weld. Join., 2013, 9(1): 1
21 Liburdi J, Lowden P, Pilcher C. Automated welding of turbine blades [A]. ASME 1989 International Gas Turbine and Aeroengine Congress and Exposition [C]. Toronto, 1989
22 Churchman C, Bonifaz E A, Richards N L. Comparison of single crystal Ni based superalloy repair by gas tungsten arc and electron beam processes [J]. Mater. Sci. Technol., 2011, 27(4): 811
23 Sidhu R K, Ojo O A, Richards N L, et al. Metallographic and OIM study of weld cracking in GTA weld build-up of polycrystalline, directionally solidified and single crystal Ni based superalloys [J]. Sci. Technol. Weld. Join., 2009, 14(2): 125
24 Chauvet E, Tassin C, Blandin J, et al. Producing Ni-base superalloys single crystal by selective electron beam melting [J]. Scr. Mater., 2018, 152: 15
25 Guercio D G, Galati M, Saboori A, et al. Microstructure and mechanical performance of Ti-6Al-4V lattice structures manufactured via electron beam melting (EBM): a review [J]. Acta Metall. Sin.Engl. Lett., 2020, 33(2): 183
26 Huang Y D, Zeng Z Q, Cai Z P, et al. Influence of electron beam thermal effect on cracks formation in fused region of single crystal superalloys DD407 [J]. Rare Metal Mat. Eng., 2017, 46(7): 1920
26 黃永德, 曾志強, 蔡祖鵬等. 電子束熱作用對DD407單晶熔凝區裂紋形成的影響 [J]. 稀有金屬材料與工程, 2017, 46(7): 1920
27 David S A, Vitek J M, Babu S S, et al. Welding of nickel base superalloy single crystals [J]. Sci. Technol. Weld. Join., 1997, 2(2): 79
28 Wang L, Wang N, Yao W J, et al. Effect of substrate orientation on the columnar-to-equiaxed transition in laser surface remelted single crystal superalloys [J]. Acta Mater., 2015, 88: 283
29 Wang L, Wang N. Effect of substrate orientation on the formation of equiaxed stray grains in laser surface remelted single crystal superalloys: experimental investigation [J]. Acta Mater., 2016, 104: 250
30 Mokadem S, Bezen?on C, Hauert A, et al. Laser repair of superalloy single crystals with varying substrate orientations [J]. Metall. Mater. Trans. A-Phys. Metall. Mater. Sci., 2007, 38(7): 1500
31 Liu W P, Dupont J N. Effects of melt-pool geometry on crystal growth and microstructure development in laser surface-melted superalloy single crystals: mathematical modeling of single-crystal growth in a melt pool (part I) [J]. Acta Mater., 2004, 52(16): 4833
32 Park J W, Vitek J M, Babu S S, et al. Stray grain formation, thermomechanical stress and solidification cracking in single crystal nickel base superalloy welds [J]. Sci. Technol. Weld. Join., 2004, 9(6): 472
33 Vitek J M, David S A, Boatner L A. Microstructural development in single crystal nickel base superalloy welds [J]. Sci. Technol. Weld. Join., 1997, 2(3): 109
34 Park J W, Babu S S, Vitek J M, et al. Stray grain formation in single crystal Ni-base superalloy welds [J]. J. Appl. Phys., 2003, 94(6): 4203
35 Vitek J M. The effect of welding conditions on stray grain formation in single crystal welds-theoretical analysis [J]. Acta Mater., 2005, 53(1): 53
36 Chen H, Lu Y Y, Luo D, et al. Epitaxial laser deposition of single crystal Ni-based superalloys: repair of complex geometry [J]. J. Mater. Process. Technol., 2020, 285: 116782
37 Chen H, Huang G S, Lu Y Y, et al. Epitaxial laser deposition of single crystal Ni-based superalloy: variation of stray grains [J]. Mater. Charact., 2019, 158: 109982
38 Zhang Q M, Wang Z D, Liu X M, et al. Influence of processing parameters on geometrical features of powder feeding laser cladding [J]. Transactions of The China Welding Institution, 2000, 21(2): 43
38 張慶茂, 王忠東, 劉喜明等. 工藝參數對送粉激光熔覆層幾何形貌的影響 [J]. 焊接學報. 2000, 21(2): 43
39 Zhou Z P, Huang L, Shang Y J, et al. Causes analysis on cracks in nickel-based single crystal superalloy fabricated by laser powder deposition additive manufacturing [J]. Mater. Des., 2018, 160: 1238
40 Ci S W, Liang J J, Li J G, et al. Microstructure and tensile properties of DD32 single crystal Ni-base superalloy repaired by laser metal forming [J]. J. Mater. Sci. Technol., 2020, 45: 23
41 Felberbaum L, Voisey K, G?umann M, et al. Thermal fatigue of single-crystalline superalloy CMSX-4?: a comparison of epitaxial laser-deposited material with the base single crystal [J]. Mater. Sci. Eng. A-Struct. Mater. Prop. Microstruct. Process., 2001, 299(1-2): 152
42 Kaierle S, Overmeyer L, Alfred I, et al. Single-crystal turbine blade tip repair by laser cladding and remelting [J]. CIRP Journal of Manufacturing Science and Technology, 2017, 19: 196
43 G?umann M, Henry S, Cléton F, et al. Epitaxial laser metal forming: analysis of microstructure formation [J]. Mater. Sci. Eng. A-Struct. Mater. Prop. Microstruct. Process., 1999, 271(1-2): 232
44 Luo D, Lu Y Y, Guo X X, et al. Laser repairing process of V-groove in single-crystal superalloy [J]. Chin. J. Las., 2016, 43(5): 37
44 羅登, 路媛媛, 郭溪溪等. 單晶高溫合金V槽的激光修復工藝研究 [J]. 中國激光, 2016, 43(5): 37
45 Vilar R, Almeida A. Repair and manufacturing of single crystal Ni-based superalloys components by laser powder deposition—A review [J]. J. Laser Appl., 2015, 27(spec. issue): S17004.
46 Wang N, Mokadem S, Rappaz M, et al. Solidification cracking of superalloy single- and bi-crystals [J]. Acta Mater., 2004, 52(11): 3173
47 Liu W, Dupont J N. Effects of substrate crystallographic orientations on crystal growth and microstructure development in laser surface-melted superalloy single crystals: mathematical modeling of single-crystal growth in a melt pool (Part II) [J]. Acta Mater., 2005, 53(5): 1545
48 Anderson T D, Dupont J N, Debroy T. Origin of stray grain formation in single-crystal superalloy weld pools from heat transfer and fluid flow modeling [J]. Acta Mater., 2010, 58(4): 1441
49 G?umann M, Bezen?on C, Canalis P, et al. Single-crystal laser deposition of superalloys: processing-microstructure maps [J]. Acta Mater., 2001, 49(6): 1051
50 Kurz W, Bezen?on C, G?umann M. Columnar to equiaxed transition in solidification processing [J]. Sci. Technol. Adv. Mater., 2001, 2(1): 185
51 Boris R; Christian N; Stefan K, et al. Crack repair of single crystal turbine blades using laser cladding technology [A]. Proceedings of the 3rd International Conference In Through-Life Engineering Services [C]. Cranfield, 2014
52 Liu D, Song Y Y, Shi B, et al. Vacuum brazing of GH99 superalloy using graphene reinforced BNi-2 composite filler [J]. J. Mater. Sci. Technol., 2018, 34(10): 1843
53 Dong K W, Kong J, Yang Y, et al. Vacuum brazing of TiAl-based alloy and GH536 superalloy with a low-melting point amorphous Ti35Zr25Be30Co10 filler [J]. J. Manuf. Process., 2019, 47: 410
54 Sun Y, Liu J D, Li B, et al. Microstructure evolution of single crystal superalloy DD5 joints brazed using AWS BNi-2 filler alloy [J]. Mater. Res. Innov., 2014, 18(): 341
55 Sun Y, Liu J D, Liu Z M, et al. Microstructure evolution and mechanical properties of DD5 single crystal superalloy joint brazed by Co-based filler alloy [J]. Acta Metall. Sin., 2013, 49(12): 1581
55 孫元, 劉紀德, 劉忠明等. 鈷基釬料釬焊DD5單晶高溫合金的接頭微觀組織演變與力學性能研究 [J]. 金屬學報, 2013, 49(12): 1581
56 Chai L, Hou J B. Effect of Si content in filler metal on microstructure and creep rupture properties of N5 crystal brazed joints [J]. Heat Treatment of Metals, 2017, 42(3): 143
56 柴祿, 侯金保. 釬料Si含量對N5單晶釬焊接頭組織和持久性能的影響 [J]. 金屬熱處理, 2017, 42(3): 143
57 Laux B, Piegert S, R?sler J. et al. Braze alloy development for fast epitaxial high-temperature brazing of single-crystalline nickel-based superalloys [J]. Metall. Mater. Trans. A, 2009, 40A(1): 138
58 Laux B, Piegert S, R?sler J. Fast epitaxial high temperature brazing of single crystalline nickel based superalloys [J]. J. Eng. Gas Turbines Power, 2009, 131(3): 032102
59 Laux B, Piegert S, R?sler J. Advanced braze alloys for fast epitaxial high-temperature brazing of single-crystalline nickel-base superalloys [J]. J. Eng. Gas Turbines. Power, 2008, 132(3): 32101.
60 Gale W F, Butts D A. Transient liquid phase bonding [J]. Sci. Technol. Weld. Join., 2004, 9(4): 283
61 Chai L, Huang J H, Hou J B, et al. Effect of holding time on microstructure and properties of transient liquid-phase-bonded joints of a single crystal alloy [J]. J. Mater. Eng. Perform., 2015, 24(6): 2287
62 Sheng N C, Hu X B, Liu J D, et al. M3B2 and M5B3 formation in diffusion-affected zone during transient liquid phase bonding single-crystal superalloys [J]. Metall. Mater. Trans. A-Phys. Metall. Mater. Sci., 2015, 46(4): 1670
63 Sheng N C, Liu J D, Jin T, et al. Wide gap TLP bonding a single-crystal superalloy: evolution of the L/S interface morphology and formation of the isolated grain boundaries [J]. Metall. Mater. Trans. A-Phys. Metall. Mater. Sci., 2013, 44(4): 1793
64 Hu X B, Sheng N C, Zhu Y M, et al. Atomic-scale investigation of the borides precipitated in a transient liquid phase-bonded Ni-based superalloy [J]. Metall. Mater. Trans. A-Phys. Metall. Mater. Sci., 2020, 51(4): 1689
65 Sheng N, Liu J D, Jin T, et al. Precipitation behaviors in the diffusion affected zone of TLP bonded single crystal superalloy joint [J]. J. Mater. Sci. Technol., 2015, 31(2): 129
66 Heinz P, Volek A, Singer R F, et al. Diffusion brazing of single crystalline nickel base superalloys using boron free nickel base braze alloys [A]. Diffusion in Solids and Liquids III [C]. ?Algarve, 2008
67 Neumeier S, Dinkel M, Pyczak F, et al. Nanoindentation and XRD investigations of single crystalline Ni-Ge brazed nickel-base superalloys PWA 1483 and René N5 [J]. Mater. Sci. Eng. A-Struct. Mater. Prop. Microstruct. Process., 2011, 528(3): 815
免責聲明:本網站所轉載的文字、圖片與視頻資料版權歸原創作者所有,如果涉及侵權,請第一時間聯系本網刪除。
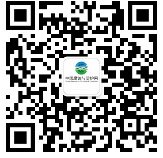
官方微信
《中國腐蝕與防護網電子期刊》征訂啟事
- 投稿聯系:編輯部
- 電話:010-62316606-806
- 郵箱:fsfhzy666@163.com
- 中國腐蝕與防護網官方QQ群:140808414