摘要:
采用電化學阻抗譜、開路電位測試和陰極極化曲線,結合掃描電鏡成像分析,研究了模擬大氣環境不同液膜厚度和交流電場對A6082-T6鋁合金腐蝕行為的影響。結果表明:降低液膜厚度加速了鋁合金A6082-T6的腐蝕,交流電場顯著改變了鋁合金局部腐蝕形態,從大量點蝕轉變成出現嚴重的剝蝕。
關鍵詞 : 交流電場, 液膜厚度, 鋁合金, 腐蝕行為, 電化學阻抗譜, 微觀形貌
鋁合金廣泛應用于常規工業、航天航空、機械零件等領域,其中A6082-T6鋁合金屬于Al-Mg-Si系熱處理可強化金屬合金,具有良好的可成型性,強度高,易于加工,耐蝕性和抗氧化性好等特點[1,2,3]。進入21世紀,我國經濟高速發展,電網建設越來越多,金屬的用量也大幅增加,其中鋁合金在輸電網中也有應用。這些大型構件服役于大氣環境中,經過風吹日曬、雨水浸蝕、應力和電磁場等作用,加速了其性能退化,容易導致輸電網的安全隱患。目前,對鋁合金在大氣環境下失效行為的研究主要是溫度、濕度和大氣污染物等因素的影響[4,5,6,7],而輸電構件一直服役于電場環境下,一般在500 kV交流電網輸電桿塔周圍分布的電場強度為10~100 kV/m,電場因素愈加凸顯,因此鋁合金在交變電場下的腐蝕研究刻不容緩。
在大氣環境下,鋁合金的環境失效行為以局部腐蝕為主,如孔蝕、晶間腐蝕、剝蝕和縫隙腐蝕等,其中剝蝕是對鋁合金有較大危害的一種腐蝕形態[8,9]。許多學者研究了鋁合金在NaCl溶液和薄液膜下的腐蝕行為[10,11,12],表明在含有Cl-溶液中,Cl-容易進入鋁合金的氧化膜進而誘發鋁合金發生晶間腐蝕、剝蝕等局部腐蝕。隨著工業的發展,大氣中的SO2越來越多。含硫污染物沉積在鋁合金表面,會誘發局部腐蝕,其主要腐蝕產物為Al3(SO4)2(OH)5·9H2O,Al2O3以及Al(OH)3。這些腐蝕產物會對鋁合金起到一定的保護作用,但是隨著SO2的增多,由于其溶解產生H+,導致電解液的pH值下降,腐蝕產物慢慢會溶解,對鋁合金的保護能力下降。這些研究表明,鋁合金局部腐蝕形態和腐蝕產物對鋁合金腐蝕行為,繼而對其服役性能具有重要影響。
目前,已經有學者針對外加電場對金屬腐蝕行為的影響進行了相關研究[13,14,15,16,17]。Dai等[17]研究了直流電場作用下碳鋼在模擬海洋大氣環境中的腐蝕行為,結果表明,直流電場加快了碳鋼在模擬海洋大氣中的腐蝕速率。Huang等[18]研究表明,直流電場對薄液膜下Cu的腐蝕速率有減緩作用。已有報道主要關注直流電場對鋼材等腐蝕行為的影響,而鮮有針對鋁合金在交流電場作用下的大氣腐蝕行為開展研究。針對以上現狀,本文設計一套電場加載下大氣腐蝕行為實驗裝置,研究了交流電場對A6082-T6鋁合金模擬大氣腐蝕行為的影響;結合電化學阻抗譜、陰極極化曲線和形貌分析,探討了液膜厚度和交流電場強度對A6082-T6鋁合金在3.5% (質量分數) NaCl溶液中腐蝕行為的影響機制。
1 實驗方法
本實驗所用材料為A6082-T6鋁合金,化學成分 (質量分數,%) 為:Si 0.7~1.3,Fe 0.50,Cu 0.10,Mn 0.6~1.2,Cr 0.25,Zn 0.20,Ti 0.10,Al余量。
實驗前將每個作為工作電極的鋁合金樣品依次用400~2000#的砂紙進行逐級打磨,接著用1.0 μm金剛石粉末在拋光機上拋光至鏡面。因薄液膜厚度的測定以及液膜在工作電極上均勻性和穩定性的要求很高,故打磨電極時要求受力均勻,保持電極表面水平。最后,去離子水清洗,并浸泡在無水乙醇中超聲10 min除油后用冷風吹干待用。測試溶液為3.5% (質量分數) NaCl水溶液。在本實驗中,采用課題組前期搭建的模擬大氣環境中薄液膜裝置,控制并測量鋁合金表面液膜厚度[19,20]。待工作電極表面形成穩定的預設薄液膜厚度后,測量不同薄液膜厚度下腐蝕不同時間的鋁合金電化學阻抗譜。為了實現不同液膜下鋁合金大氣腐蝕的連續監控,只采用電化學阻抗譜技術研究鋁合金在不同液膜厚度下的腐蝕行為。
研究外加交流電場強度對鋁合金A6082-T6在不同薄液膜厚度下的腐蝕行為所用裝置如圖1所示。在課題組原有薄液膜裝置的基礎上,上下加載兩個距離為5 cm的不銹鋼板,通過高壓電源裝置引入不同的交流電壓 (1,3和5 kV),從而在工作電極和不銹鋼板之間形成不同強度 (20,60和100 kV/m) 的電場。另外,需要特別注意的是底部電極與不銹鋼極板需要接地,模擬電網中大型構件接地的環境。由于交變電場的存在 (不管是正在加載,還是停止加載) 會嚴重干擾電化學阻抗譜的測量,因此外加電場下的鋁合金腐蝕電化學測試只針對極化曲線和開路電位,未測試電化學阻抗譜。還需要指出的是,由于外加電場下薄液膜很容易破裂,繼而影響電化學測試,因此在外加電場下薄液膜厚度最大只能到150 μm。
圖1 外加交流電場的薄液膜裝置示意圖
電化學阻抗譜采用VMP2多通道恒電位儀進行測定。測試過程中,外加正弦波的擾動振幅為5 mV,掃描頻率范圍是105~10-2 Hz。陰極極化曲線和開路電位曲線采用CHI630C電化學工作站進行測定,不同條件下的陰極極化曲線的掃描速率是1 mV/s。由于陽極極化會引起電極的溶解而改變薄液膜厚度以及電流分布,因此研究薄液膜下的腐蝕過程主要采用陰極極化曲線。電化學測試采用三電極系統,其中鋁合金A6082-T6為工作電極,大面積Pt絲網為輔助電極,Ag/AgCl (KCl濃度為3 mol/L) 為參比電極。若無特別說明,本文所有電位均相對于該參比電極。腐蝕產物形貌采用SU-8010場發射掃描電鏡 (SEM) 觀察,通過SEM附帶能譜儀 (EDS) 分析元素組成。實驗溫度25 ℃。
2 結果與討論
2.1 未加電場下的鋁合金腐蝕行為
A6082-T6鋁合金在本體溶液和典型液膜厚度下的電化學阻抗譜以及對應擬合結果如圖2所示。對照各Nyquist和Bode圖可看出,A6082-T6鋁合金在本體溶液中,高頻區和中頻區分別出現一個容抗弧,在低頻區出現擴散;液膜厚度較厚 (圖中為256 μm,346和160 μm的薄液膜規律類似,圖略去) 時,出現兩個容抗弧。結合課題組之前的研究結果,認為這兩個容抗弧分別對應表面膜和電荷轉移電化學過程。液膜厚度減薄至70 μm時,隨時間的演化,在腐蝕后期低頻區出現感抗。許多合金腐蝕時電化學阻抗譜中都出現了低頻區的感抗行為[21,22,23,24],主要原因有兩個方面,一是與腐蝕過程中電極表面被吸附物質的弛豫行為有關,二是與局部腐蝕有關。結合電化學阻抗譜數據擬合和表面腐蝕形貌觀察結果,認為感抗弧的出現與局部腐蝕的形成有關。圖3為鋁合金A6082-T6在NaCl本體和薄液膜溶液中電化學阻抗譜擬合所用等效電路[9,21],圖3a用于擬合低頻無感抗的電化學阻抗譜,圖3b用于擬合出現低頻感抗的電化學阻抗譜。其中,Rs表示溶液電阻,Rf表示電極表面腐蝕產物膜電阻,Rct表示電荷轉移電阻,R表示電感電阻,Zo為有限層擴散阻抗,L表示感抗,CPEsurf和CPEdl分別表示表面腐蝕產物膜電容和雙電層電容 (用恒相位角元件CPE表示)。根據等效電路進行擬合得到的Rct和Rct+Rf數據如圖4所示。A6082-T6鋁合金的初期腐蝕速率是在薄液膜下的較大,在較厚液膜和本體溶液中的較小。這是由于在NaCl溶液中,液膜越薄,O2越容易進入電極/液膜界面,溶解氧越容易供給。但是另一方面,整體數據分布零散,表明腐蝕速率波動嚴重。隨浸泡時間延長,不同液膜厚度下的腐蝕速率差異明顯,但是仍然表明在70和90 μm下,A6082-T6鋁合金的腐蝕速率最大,而在較厚液膜下的腐蝕速率較小。在本體溶液中的腐蝕速率介于薄液膜與厚液膜下的之間。
圖2 A6082-T6鋁合金在本體溶液以及典型薄液膜厚度溶液中浸泡72 h的Nyquist和Bode圖
圖3 鋁合金A6082-T6在3.5%NaCl溶液中電化學阻抗譜擬合用等效電路圖
圖4 A6082-T6鋁合金在含3.5%NaCl不同厚度薄液膜下電化學阻抗譜擬合的Rct及Rf+Rct的變化曲線
2.2 外加電場下的鋁合金腐蝕行為
由于外加電場的存在,電化學阻抗譜測試的穩定性與因果性條件很難滿足,應用開路電位方法和極化曲線技術測試A6082-T6鋁合金在外加電場的薄液膜下的腐蝕行為。外加電場和液膜厚度協同作用下的鋁合金A6082-T6開路電位和陰極極化曲線分別如圖5和6所示。鋁合金在3.5%NaCl本體溶液及不同厚度液膜下浸泡20 min,達到相對穩定電位后測得陰極極化曲線。圖5結果表明,薄液膜的厚度對陰極極化曲線的開路電位影響不大,穩定的開路電位約在-0.73~-0.74 V。施加交流電場后,開路電位有一定程度的負移,約在5~10 mV范圍,但是與交流電場的強度沒有顯著關聯性。在外加交流電場的作用下,鋁合金電極的開路電位發生一定幅度的負移,這是因為在外加電場作用下,液膜中的正電荷會向鋁合金/液膜界面遷移,這樣電極和溶液界面的雙電層電容的電荷密度會增加,促進了陰極的還原反應。結果也表明,交流電場影響電極腐蝕的陰、陽極耦合反應進而影響開路電位的作用機制較為復雜,沒有簡單的對應關系。圖6所示的不同厚度液膜和電場強度下陰極極化曲線均可以分成兩個區域:區域I是弱極化區;區域II是在陰極電位下氧的擴散控制區。陰極極化曲線結果也表明,液膜厚度和電場強度對陰極極限電流密度影響較大。A6082-T6鋁合金在薄液膜下的電流密度都比在本體溶液中的高,在任何一個電場強度下,隨著薄液膜厚度變薄,陰極極限擴散電流密度增加;而在同一個液膜厚度下,電場強度的增加并沒有顯著改變極限擴散電流密度,表明液膜減薄提高了陰極極限電流密度,從而加速了腐蝕,但電場的存在并沒有顯著改變腐蝕速率。
圖5 在本體3.5%NaCl溶液及不同厚度薄液膜體系中浸泡20 min后施加不同交流電場對A6082-T6鋁合金開路電位的影響
圖6 不同交流電場下鋁合金在3.5%NaCl本體溶液和不同厚度薄液膜下的陰極極化曲線和-1.0 V極限擴散電流
2.3 微觀形貌和組成分析
浸泡72 h后,未加交流電場試樣的表面形貌和EDS結果如圖7所示。結果表明,A6082-T6鋁合金在浸泡72 h后,發生明顯的局部腐蝕,在薄液膜厚度為160 μm時,出現了大量的蝕孔和少量剝蝕,點蝕密集且多,蝕孔里布滿白色顆粒狀的腐蝕產物,EDS測得主要元素包括Si,O和Al,而孔外不包括Si,這也表明鋁合金在薄液膜厚度為160 μm時腐蝕速率較快。當薄液膜厚度為90和70 μm時,發生嚴重的剝蝕和開裂,形成大量片狀的腐蝕產物,這可能是電化學阻抗譜低頻出現感抗的原因;而腐蝕產物的大量存在表明極薄液膜下腐蝕速率加快,與電化學阻抗譜的測試結果一致。
圖7 A6082-T6鋁合金在3.5%NaCl本體溶液及不同厚度薄液膜下浸泡72 h后的SEM像和薄液膜厚度為160 μm下的EDS結果
A6082-T6鋁合金在外加20 kV/m交流電場的3.5%NaCl本體溶液及不同厚度薄液膜下浸泡12 h后的SEM形貌和液膜厚度為250 μm時樣品的EDS結果如圖8所示。A6082-T6鋁合金在外加20 kV/m的交流電場下浸泡12 h后,隨著薄液膜厚度變薄,電極表面腐蝕變得更嚴重;在薄液膜厚度為250 μm時,出現大量的點蝕,蝕孔里布滿白色的腐蝕產物,通過EDS測得含有Si的腐蝕產物;在薄液膜厚度為150 μm時,發生輕微的剝蝕,有片狀的腐蝕產物。圖8所示的形貌與EDS數據與未加電場條件下的圖7結果沒有顯著區別。
圖8 A6082-T6鋁合金在外加20 kV/m的交流電場下3.5%NaCl本體溶液及不同厚度薄液膜下浸泡12 h后的SEM像和液膜厚度為250 μm時樣品的EDS結果
從圖9中可以看出,A6082-T6鋁合金在外加60 kV/m的交流電場下浸泡12 h后,電極表面發生明顯的局部腐蝕。在本體溶液中時,出現少量蝕孔和大量的白色腐蝕產物。隨薄液膜厚度變薄,電極表面腐蝕變得越嚴重,點蝕越多且越大;在薄液膜厚度為150 μm時,在大量點蝕蝕孔附近出現輕微的剝蝕,且表面凸起處產物呈瘤狀,EDS分析結果表明腐蝕產物含氧量較之前兩種電場強度下的腐蝕產物要高。
圖9 A6082-T6鋁合金在外加60 kV/m交流電場的3.5%NaCl本體溶液及不同厚度薄液膜下浸泡12 h后的SEM像和液膜厚度為150 μm時樣品的EDS結果
如圖10所示,A6082-T6鋁合金在外加100 kV/m的交流電場下在本體溶液中浸泡12 h后出現大量點蝕,蝕孔中布滿大量的白色腐蝕產物;隨薄液膜厚度變薄,電極表面腐蝕變得越嚴重,出現嚴重的剝蝕,剝蝕附近伴隨點蝕。剝蝕是對鋁合金有較大危害的一種腐蝕,在薄液膜厚度為250和150 μm時,表面局部區域有嚴重的剝落。結合圖8,9,10可見,外加交流電場顯著改變了腐蝕形態以及腐蝕產物分布,但液膜厚度仍是影響腐蝕速率的主要因素。有研究[25]表明,在外加交流電下,金屬材料的電極電位會有瞬間的波動,從而引起一種復雜的電流波動,這種波動會破壞金屬的鈍化,增加孔蝕。在交流電場存在的環境中,溶解氧在薄液膜中的傳質加強,加快溶解氧到達鋁合金表面的速度,加快了鋁合金的腐蝕反應,這是液膜厚度影響腐蝕速率的核心原因。溶解氧的還原反應生成的OH-雖然會受外加電場的影響而發生遷移,并有可能影響腐蝕產物的吸附狀態等,但是在本實驗中交流電場的作用下,無論是電化學實驗結果還是形貌觀察結果,均無法表明交流電場顯著改變了鋁合金A6082-T6的腐蝕速率。
圖10 A6082-T6鋁合金在外加100 kV/m的交流電場下3.5%NaCl本體溶液及不同厚度薄液膜下浸泡12 h后的SEM像和在本體溶液中浸泡樣品的EDS結果
3 結論
(1) 薄液膜厚度是影響A6082-T6鋁合金腐蝕速率的主要因素,液膜越薄,腐蝕速率越高;交流電場對在模擬大氣環境下的鋁合金腐蝕速率有影響,但不顯著。
(2) 有交流電場存在時,鋁合金的腐蝕形態從出現點蝕到發展成嚴重剝蝕。因此,工業設計時應充分考慮環境中交流電場對鋁合金腐蝕的影響。
參考文獻
[1] Trdan U, Grum J. Evaluation of corrosion resistance of AA6082-T651 aluminium alloy after laser shock peening by means of cyclic polarisation and ElS methods [J]. Corros. Sci., 2012, 59: 324
doi: 10.1016/j.corsci.2012.03.019
[2] Panagopoulos C N, Georgiou E P, Gavras A G. Corrosion and wear of 6082 aluminum alloy [J]. Tribol. Int., 2009, 42: 886
doi: 10.1016/j.triboint.2008.12.002
[3] Shang B D, Shi Z M, Wang G, et al. Investigation of quench sensitivity and transformation kinetics during isothermal treatment in 6082 aluminum alloy [J]. Mater. Des., 2011, 32: 3818
doi: 10.1016/j.matdes.2011.03.016
[4] Ralston K D, Fabijanic D, Birbilis N. Effect of grain size on corrosion of high purity aluminium [J]. Electrochim. Acta, 2011, 56: 1729
doi: 10.1016/j.electacta.2010.09.023
[5] Chen S Y, Chen K H, Peng G S, et al. Effect of heat treatment on strength, exfoliation corrosion and electrochemical behavior of 7085 aluminum alloy [J]. Mater. Des., 2012, 35: 93
doi: 10.1016/j.matdes.2011.09.033
[6] Zaid B, Saidi D, Benzaid A, et al. Effects of pH and chloride concentration on pitting corrosion of AA6061 aluminum alloy [J]. Corros. Sci., 2008, 50: 1841
doi: 10.1016/j.corsci.2008.03.006
[7] Szklarska-Smialowska Z. Pitting corrosion of aluminum [J]. Corros. Sci., 1999, 41: 1743
doi: 10.1016/S0010-938X(99)00012-8
[8] Deepa P, Padmalatha R. Corrosion behaviour of 6063 aluminium alloy in acidic and in alkaline media [J]. Arab. J. Chem., 2017, 10 (Suppl.2): S2234
doi: 10.1016/j.arabjc.2013.07.059
[9] Tian W M, Li S M, Wang B, et alPitting corrosion of naturally aged AA 7075 aluminum alloys with bimodal grain size [J]. Corros. Sci., 2016, 113: 1
[10] Cao M, Liu L, Yu Z F, et al. Electrochemical corrosion behavior of 2A02 Al alloy under an accelerated simulation marine atmospheric environment [J]. J. Mater. Sci. Technol., 2019, 35: 651
doi: 10.1016/j.jmst.2018.09.060
[11] Qu Q, Yan C W, Wan W, et al. Effects of NaCl and SO2 on the initial atmospheric corrosion of zinc [J]. Corros. Sci., 2002, 44: 2789
doi: 10.1016/S0010-938X(02)00076-8
[12] ?ekularac G, Milo?ev I. Corrosion of aluminium alloy AlSi7Mg0.3 in artificial sea water with added sodium sulphide [J]. Corros. Sci., 2018, 144: 54
doi: 10.1016/j.corsci.2018.08.038
[13] Tan T, Chen T, Zhang J X, et al. Corrosion behavior of galvanized steel in different simulated service environments [J]. Corros. Prot., 2014, 35: 307
[13] (談天, 陳彤, 張俊喜等. 鍍鋅鋼在模擬不同服役環境中的腐蝕行為 [J]. 腐蝕與防護, 2014, 35: 307)
[14] Huang H L, Tian J, Zhang G A. Atmospheric corrosion behavior of tin under an alternating current electric field [J]. J. Electr. Mater., 2017, 46: 4359
doi: 10.1007/s11664-017-5395-y
[15] Luo X, Li X Q, Dong C L. Effect of corrosion products on corrosion process of 6061 aluminium alloy in marine atmosphere [J]. Corros. Prot., 2018, 39: 587
[15] (羅雪, 李小強, 董重里. 腐蝕產物對6061鋁合金海洋大氣腐蝕過程的影響 [J]. 腐蝕與防護, 2018, 39: 587)
[16] Zhang X, Dai N W, Yang Y, et al. Effect of direct current electric field on corrosion mechanism of Zn exposed to simulated industrial environment [J]. J. Chin. Soc. Corros. Prot., 2017, 37: 451
[16] (張鑫, 戴念維, 楊燕等. 模擬工業環境下直流電場對金屬Zn腐蝕機理的影響 [J]. 中國腐蝕與防護學報, 2017, 37: 451)
doi: 10.11902/1005.4537.2017.159
[17] Dai N W, Zhang J X, Chen Q M, et al. Effect of the direct current electric field on the initial corrosion of steel in simulated industrial atmospheric environment [J]. Corros. Sci., 2015, 99: 295
doi: 10.1016/j.corsci.2015.07.029
[18] Huang H L, Guo X P, Zhang G A, et al. Effect of direct current electric field on atmospheric corrosion behavior of copper under thin electrolyte layer [J]. Corros. Sci., 2011, 53: 3446
doi: 10.1016/j.corsci.2011.04.017
[19] Cheng Y L, Zhang Z, Cao F H, et al. A study of the corrosion of aluminum alloy 2024-T3 under thin electrolyte layers [J]. Corros. Sci., 2004, 46: 1649
doi: 10.1016/j.corsci.2003.10.005
[20] Liu W J, Cao F H, Chen A N, et al. Corrosion behaviour of AM60 magnesium alloys containing Ce or La under thin electrolyte layers. Part 1: Microstructural characterization and electrochemical behaviour [J]. Corros. Sci., 2010, 52: 627
doi: 10.1016/j.corsci.2009.10.031
[21] Arenas M A, De Damborenea J. Interference by cerium cations during the multi-step zinc dissolution process in a chloride-containing electrolyte [J]. Corros. Sci., 2006, 48: 3196
doi: 10.1016/j.corsci.2005.10.015
[22] Nguyen T H, Foley R T. The chemical nature of aluminum corrosion: II. The initial dissolution step [J]. J. Electrochem. Soc., 1982, 129: 27
doi: 10.1149/1.2123768
[23] Hu G Y, Chen S Y, Jiang H L, et al. Effect of RE Ce on microstructure and properties of 7A52 aluminum alloy [J]. Chin. J. Nonferrous Met., 2016, 26: 1372
[23] (胡桂云, 陳送義, 姜慧麗等. 稀土Ce對7A52鋁合金組織與性能的影響 [J]. 中國有色金屬學報, 2016, 26: 1372)
[24] Li J F, Zhang Z, Cao F H, et al. Exfoliation corrosion and electrochemical impedance behavior of LC4 alloy [J]. Chin. J. Nonferrous Met., 2002, 12: 1189
[24] (李勁風, 張昭, 曹發和等. LC4鋁合金剝蝕及其電化學阻抗行為 [J]. 中國有色金屬學報, 2002, 12: 1189)
[25] Cao C N. Principle of Electrochemistry of Corrosion [M]. Beijing: Chemical Industry Press, 2008: 158
[25] (曹楚南. 腐蝕電化學原理 [M]. 北京: 化學工業出版社, 2008: 158)
免責聲明:本網站所轉載的文字、圖片與視頻資料版權歸原創作者所有,如果涉及侵權,請第一時間聯系本網刪除。
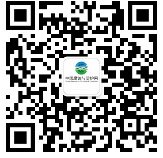
官方微信
《中國腐蝕與防護網電子期刊》征訂啟事
- 投稿聯系:編輯部
- 電話:010-62316606-806
- 郵箱:fsfhzy666@163.com
- 中國腐蝕與防護網官方QQ群:140808414