冷換設(shè)備是煉化企業(yè)使用量最大的一類設(shè)備,其腐蝕泄漏問題是困擾煉油裝置長周期安全運行的一個主要隱患。基于某煉化企業(yè)冷換設(shè)備在1個運行周期及大檢修期間的腐蝕案例,分別從腐蝕類型、腐蝕部位、腐蝕成因等方面對其腐蝕情況進行統(tǒng)計分析,深入研究了冷換設(shè)備的腐蝕成因及主要影響因素,提出了從選材、制造、運行控制、循環(huán)水管理等方面對冷換設(shè)備的防腐進行優(yōu)化的措施,為煉化企業(yè)冷換設(shè)備的腐蝕防護工作提供了有益的借鑒。
近年來,隨著原油的劣質(zhì)化日益加重,原油中所含的硫、酸、氯等腐蝕性雜質(zhì)含量不斷提高,使設(shè)備腐蝕問題成為困擾煉油裝置長周期安全運行的一個主要隱患。冷換設(shè)備是煉油裝置中應(yīng)用最廣泛的設(shè)備,投資占總體工藝設(shè)備投資的1/3以上,同時也是服役環(huán)境最惡劣的設(shè)備之一,經(jīng)常因腐蝕、制造等因素發(fā)生泄漏,尤其是腐蝕泄漏問題,一直困擾著設(shè)備的管理工作,嚴(yán)重影響產(chǎn)品質(zhì)量,甚至導(dǎo)致裝置非計劃停工及重大安全事故。
1 典型冷換設(shè)備的腐蝕統(tǒng)計分析
國內(nèi)沿海某煉化企業(yè)1200萬t/a原油加工能力,涉及常減壓、催化裂化、加氫裂化、加氫精制、延遲焦化、硫磺回收等11套煉油裝置,共有冷換設(shè)備457臺。2014年裝置停工大檢修期間,針對401臺冷換設(shè)備進行開蓋檢查,發(fā)現(xiàn)存在腐蝕問題的冷換設(shè)備共計73臺,約占18.2%。通過對腐蝕失效的73臺冷換設(shè)備進行統(tǒng)計分析發(fā)現(xiàn),其腐蝕失效涉及的因素不僅與服役環(huán)境有關(guān),還與設(shè)備材質(zhì)、制造缺陷等密切相關(guān)。按照冷換設(shè)備失效類型進行統(tǒng)計分類(見圖1),可分為均勻減薄、局部腐蝕、開裂、焊接缺陷和機械變形5種。其中與腐蝕相關(guān)的減薄、局部/坑蝕和開裂問題最多,約占失效案例的92%,與制造相關(guān)的約占8%。
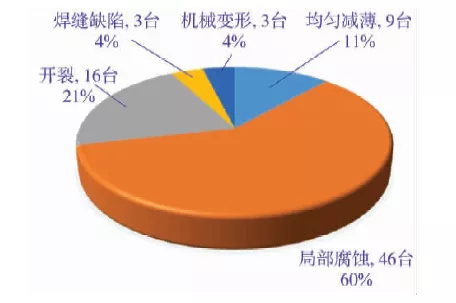
圖1 冷換設(shè)備失效類型統(tǒng)計
注:同1臺換熱器可能同時發(fā)生1種或幾種腐蝕類型,下同。
按照冷換設(shè)備出現(xiàn)腐蝕的部位進行統(tǒng)計分析,結(jié)果如圖2所示。冷換設(shè)備的腐蝕主要發(fā)生在管束、管箱、管板、換熱管管口、入口接管和殼體等部位,分別占腐蝕案例的25%、23%、31%、12%、5%和4%。其中發(fā)生在管束、管箱、管板上的最為突出,合計約占腐蝕案例的79%;易導(dǎo)致冷換設(shè)備腐蝕泄漏的部位出現(xiàn)在管束和換熱管管口的案例,合計約占腐蝕案例的1/3。
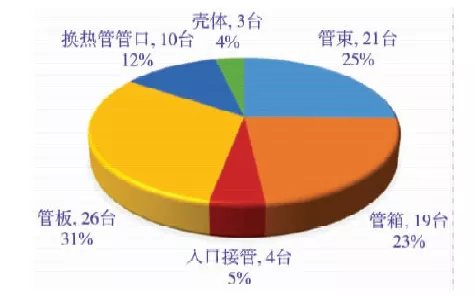
圖2 腐蝕部位統(tǒng)計
根據(jù)冷換設(shè)備發(fā)生腐蝕失效的成因進行初步歸納分析,主要分為工藝介質(zhì)腐蝕、循環(huán)水腐蝕、焊接及施工質(zhì)量問題和選材等級低等4大類,如圖3所示。其中由工藝介質(zhì)導(dǎo)致的腐蝕失效問題最多,約占總腐蝕案例的45%;其次是因循環(huán)水腐蝕導(dǎo)致的失效,約占40%;焊接及施工質(zhì)量問題約占10%;選材等級低問題約占5%。
2 冷換設(shè)備的腐蝕成因分析
工藝介質(zhì)腐蝕
工藝介質(zhì),主要是指油品、油氣等工藝物流。由于油品發(fā)生高溫分解、加氫、裂解等反應(yīng),因此工藝介質(zhì)中除了含有石油產(chǎn)品外,還含有硫、硫化氫、氯化氫、氨氮等腐蝕性物質(zhì)。這些腐蝕性物質(zhì)會對冷換設(shè)備產(chǎn)生HCl-H2S-H2O腐蝕、高溫硫腐蝕、高溫環(huán)烷酸腐蝕、氯化銨結(jié)垢及垢下腐蝕等。腐蝕形態(tài)主要表現(xiàn)為均勻腐蝕、點蝕、應(yīng)力腐蝕、沖刷腐蝕、開裂等,詳見圖1的統(tǒng)計。原油-常頂油氣換熱器(E101/E201/E301/E401)為并列的4臺換熱器,2009年4月投用。該換熱器管程介質(zhì)為常頂油氣,操作溫度(進出口溫度)118~93℃,管束材質(zhì)為TA1,管板材質(zhì)為16MnⅣ+TA1;殼程介質(zhì)為原油,操作溫度(進出口溫度)40~60℃,筒體和封頭材質(zhì)為16MnR(自GB713—2008標(biāo)準(zhǔn)起牌號更新為Q345R,下同)。
檢修期間發(fā)現(xiàn),管箱內(nèi)壁污垢、銹蝕較重,隔板及基體布滿蝕坑,隔板中部存在明顯的沖刷腐蝕減薄現(xiàn)象。從測厚情況看,E201管箱隔板沖蝕部位區(qū)域測厚值為10.14~10.37mm,其余部位為15.45~15.51mm;E301管箱隔板沖蝕部位區(qū)
域測厚值為9.51~10.02mm,其余部位為15.32~15.57mm;E401管箱隔板沖蝕部位區(qū)域測厚值為6.92~7.12mm,其余部位為13.95~15.51mm。管/箱出入口接管(光譜材質(zhì)檢測為317L)表面存在裂紋(見圖4)。
為分析腐蝕原因,與現(xiàn)場工作人員進行交流發(fā)現(xiàn),因油品性質(zhì)變輕,2011年對常減壓裝置進行了擴容原油適應(yīng)性改造。改造后,常壓塔頂(簡稱常頂)負(fù)荷高于設(shè)計值,具體為:設(shè)計流量102t/h,實際流量126t/h;設(shè)計流速22m/s,計算最大塔頂流速達到27m/s。高流速的常頂油氣加上腐蝕介質(zhì)會對管箱造成嚴(yán)重的沖刷腐蝕,且高流速、高剪切力會破壞已經(jīng)形成的緩釋劑保護膜,使金屬裸露,加速腐蝕。另外,此部位的常頂注水點設(shè)置在E101/E201/E301/E401管箱入口法蘭上部管線,而緩蝕劑與中和劑注入點在常頂,注水后時間太短,中和劑不能充分與生成的鹽酸反應(yīng);而且通過模擬,最優(yōu)操作時,注水后液態(tài)水也只有5%,量明顯不足。這就導(dǎo)致了HCl-H2S-H2O腐蝕環(huán)境的形成,進而造成奧氏體不銹鋼的應(yīng)力腐蝕開裂。
循環(huán)水介質(zhì)腐蝕
隨著節(jié)能環(huán)保要求的提高,循環(huán)水濃縮倍數(shù)不斷提高,回用污水后水質(zhì)狀況日益變差,導(dǎo)致裝置循環(huán)水側(cè)的腐蝕和結(jié)垢問題日益突出。循環(huán)水的水質(zhì)狀況對水冷器的腐蝕影響較大,主要因為循環(huán)水中雜質(zhì)含量較多,同時存在大量粘泥,容易在金屬表面結(jié)垢,產(chǎn)生垢下腐蝕,造成管子出現(xiàn)蝕坑、穿孔。另外,如果循環(huán)水中存在一定量的氯離子,則會造成不銹鋼管束點蝕,甚至引起奧氏體不銹鋼管束開裂。根據(jù)圖3的腐蝕成因統(tǒng)計分析可見,循環(huán)水造成的冷換設(shè)備腐蝕占總體的40%。
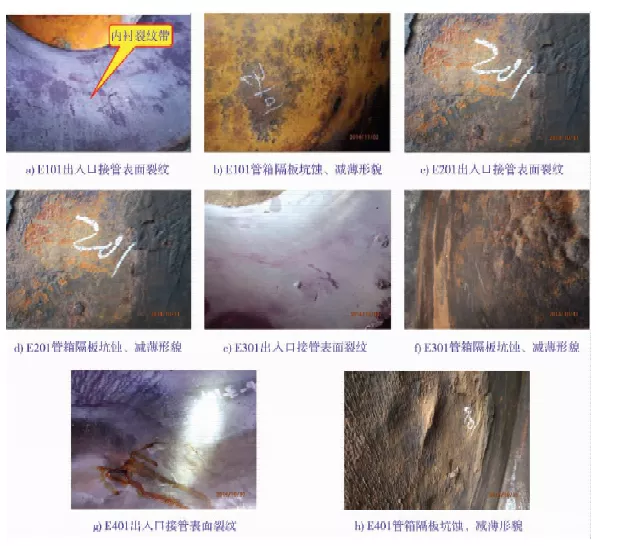
圖4 換熱器E101/E201/E301/E401腐蝕宏觀形貌
催化分餾塔頂油氣冷凝器E203ABCD管程為循環(huán)水。因循環(huán)水中微生物控制不力,導(dǎo)致細(xì)菌大量繁殖,形成粘泥,吸附水中灰分,附著在設(shè)備壁上,產(chǎn)生粘泥下腐蝕和結(jié)垢腐蝕,同時,又因換熱器結(jié)構(gòu)不合理,在管子與管板的連接處產(chǎn)生了較大的附加應(yīng)力,從而造成4臺換熱器的管板腐蝕嚴(yán)重且存在開裂現(xiàn)象(見圖5和圖6)。
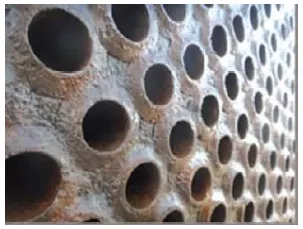
圖5?。?03D管板腐蝕開裂形貌
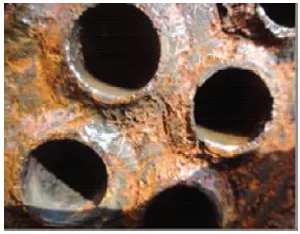
圖6?。牛玻埃常凉馨蹇游g及焊縫開裂形貌
脫硫聯(lián)合裝置循環(huán)堿液冷卻器E505A,管程為循環(huán)水,管束多處出現(xiàn)腐蝕穿孔,穿孔處位于殼程進料口一側(cè)、導(dǎo)流筒和管板之間。對管束進行測厚,結(jié)果顯示,穿孔處附近厚度為1.5mm,未穿孔處為2.3mm。內(nèi)窺鏡觀察發(fā)現(xiàn),其管束內(nèi)壁有片層狀垢物(見圖7)。
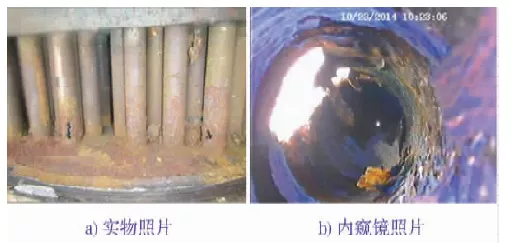
圖7 循環(huán)堿液冷卻器E505A管束穿孔
加氫低分氣冷卻器E102,管程為循環(huán)水,管箱和管板表面結(jié)硬質(zhì)黃褐色垢物,垢下為紅棕色鐵銹,環(huán)焊縫點蝕坑深度達0.5mm(見圖8)。
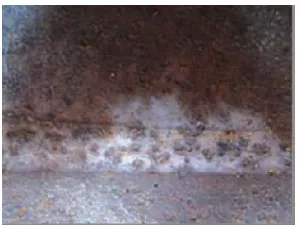
圖8 加氫低分氣冷卻器E-102管板點蝕形貌
脫硫聯(lián)合裝置再生塔頂冷凝器E302AB,操作介質(zhì)為循環(huán)水/貧液,管束材質(zhì)為00Cr17Ni14Mo2,筒體和封頭材質(zhì)為16MnR+316L。檢修發(fā)現(xiàn),管箱內(nèi)結(jié)黃褐色硬質(zhì)垢,垢下點蝕坑深度達0.2~0.4mm(見圖9)

圖9?。牛常埃玻粒鹿芟涓g形貌
制造/設(shè)計缺陷
根據(jù)圖3的統(tǒng)計,因焊接、施工質(zhì)量、設(shè)計缺陷(包括選材等級低)造成的換熱器腐蝕大概占15%。換熱器在制造、安裝或運輸過程中,因制造和施工質(zhì)量的低劣或不穩(wěn)定,以及運輸過程中的不文明操作,造成焊接質(zhì)量不合格,涂層存在針孔、漏涂、磨損,設(shè)備出現(xiàn)凹坑、局部擦傷、擠壓等,這些缺陷可導(dǎo)致腐蝕的加劇,容易導(dǎo)致泄漏發(fā)生。在此次檢維修的過程中,發(fā)現(xiàn)發(fā)生在焊縫處的腐蝕較多,比如多處出現(xiàn)換熱管管口、管板焊縫開裂,同時還發(fā)現(xiàn)管箱密封面處焊縫缺陷(見圖10~圖13)。
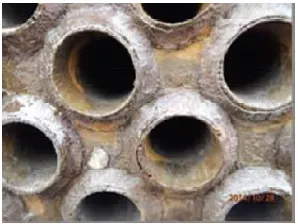
圖10 原油-減一中油換熱器E204A管頭焊縫腐蝕
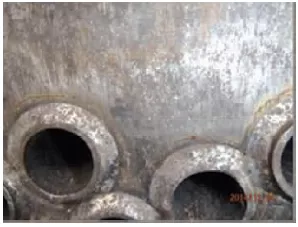
圖11 原油-常頂循換熱器E302管板熱影響區(qū)裂紋
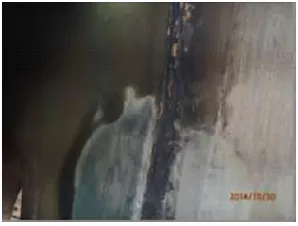
圖12 脫鹽油-減二中E406A換熱器管箱密封面處焊縫缺陷
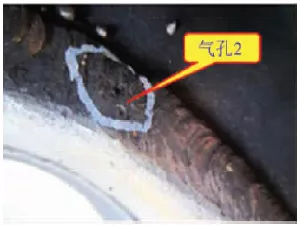
圖13 頂循環(huán)油-熱水換熱器E204D管箱焊縫缺陷
另外,換熱器的壽命與選材相關(guān)性很大。換熱器的選材原則上既要滿足工藝過程的要求,又要滿足強度要求和制造工藝要求,所以要根據(jù)不同介質(zhì)和工藝,選擇合適的金屬材料。此次檢修過程中,發(fā)現(xiàn)4臺換熱器因選材等級偏低造成了嚴(yán)重腐蝕。
3 冷換設(shè)備的防護措施
材料/制造
設(shè)備的制造和選材是設(shè)備設(shè)計的關(guān)鍵和基礎(chǔ),將直接影響設(shè)備的使用壽命、安全性以及成本。所以一定要嚴(yán)把冷換設(shè)備的制造質(zhì)量,并保證焊接、施工質(zhì)量。施工過程中,應(yīng)文明操作,避免擠壓、擦傷等。采用耐蝕涂層時,確保涂層質(zhì)量沒有缺陷,并注意開、停工過程的蒸汽吹掃,防止涂料失效。
針對高溫部位,要防止高溫硫、高溫環(huán)烷酸、高溫氫/硫化氫等的腐蝕。碳鋼及合金鋼在高溫硫、高溫環(huán)烷酸及高溫氫/硫化氫等環(huán)境中的腐蝕速率可參考API RP581—2016《基于風(fēng)險的檢驗技術(shù)》,API RP939-C-2009《避免煉油廠硫腐蝕失效導(dǎo)則》中的Modified McConomy Curves 、Couper-Gorman H2/H2S Curves??;針對低溫部位,要避免碳鋼在濕硫化氫環(huán)境中的損傷。關(guān)于冷換設(shè)備的選材可參照SH/T3219-2012《高酸原油加工裝置設(shè)備和管道設(shè)計選材導(dǎo)則》、SH/T3096—2012《高硫原油加工裝置設(shè)備和管道設(shè)計選材導(dǎo)則》的有關(guān)規(guī)定,以煉油裝置正常操作條件下原油的硫含量和酸值為依據(jù),充分考慮最苛刻條件下可能出現(xiàn)的最大硫含量與最高酸值來確定最適用的材料,力求做到所選用的材料經(jīng)濟、可靠和耐用。
運行控制
根據(jù)國內(nèi)外煉油企業(yè)的生產(chǎn)經(jīng)驗,對于低溫服役環(huán)境,工藝防腐是關(guān)鍵,尤其是常減壓裝置,如果工藝防腐做得不好,即使材質(zhì)等級很高(如上述案例中常頂換熱器使用鈦材),也避免不了腐蝕。所以針對煉油裝置冷換設(shè)備低溫處,要參照執(zhí)行中國石化《煉油工藝防腐蝕管理規(guī)定》實施細(xì)則的相關(guān)要求加強工藝防腐措施。例如,對常減壓蒸餾裝置,控制處理量和原油質(zhì)量在設(shè)計范圍內(nèi)。加強常減壓裝置的“一脫三注”系統(tǒng)操作管理,控制脫后含鹽≤3mg/L、脫后含水≤0.3%、污水含油≤200mg/L??刂扑斃淠穑?值為5.5~7.5(注有機胺時)、7.0-9.0(注氨水時)、6.5~8.0(有機胺+氨水);鐵離子含量≤3mg/L??刂扑攦?nèi)部操作溫度高于水露點溫度14℃以上、塔頂回流返塔溫度高于90℃等。針對高溫部位,以設(shè)備材質(zhì)為基礎(chǔ),對新建或在役煉油裝置制定有針對性的最低設(shè)防值,并按要求嚴(yán)格執(zhí)行。運行期間要加強工藝介質(zhì)化驗分析,禁止超出設(shè)計/設(shè)防值,同時應(yīng)對腐蝕嚴(yán)重部位強化監(jiān)檢測措施并提出材質(zhì)升級方案。
水冷器防護措施
循環(huán)水管理:根據(jù)中國石化《煉油工藝防腐蝕管理規(guī)定》實施細(xì)則管理規(guī)定:
1)循環(huán)冷卻水管程流速不宜小于1。0m/s,當(dāng)循環(huán)冷卻水殼程流速小于0。3m/s時,應(yīng)采取防腐涂層、反向沖洗等措施。循環(huán)冷卻水水冷器出口溫度推薦不超過50℃。采用超聲波流量計對水冷器水側(cè)進行流速抽查,防止偏流或流速過低。對于結(jié)垢傾向嚴(yán)重的水冷器,可以加設(shè)反沖洗設(shè)施或采用超聲波除垢等技術(shù)。
2)循環(huán)冷卻水水質(zhì)應(yīng)符合GB50050-2017循環(huán)冷卻水水質(zhì)的控制指標(biāo)要求。使用再生水作為補充水應(yīng)符合Q/SH0628.2-2014《水務(wù)管理技術(shù)要求第2 部分:循環(huán)水》的要求。
3)緩蝕阻垢劑應(yīng)針對水質(zhì)和工況選擇高效、低毒、化學(xué)穩(wěn)定性和復(fù)配性能好的環(huán)境友好型藥劑。當(dāng)采用含鋅鹽藥劑配方時,循環(huán)冷卻水中鋅鹽含量應(yīng)小于2mg/L(以鋅離子計);循環(huán)冷卻水系統(tǒng)中有銅合金換熱設(shè)備時,水處理藥劑配方應(yīng)有銅緩蝕劑。
4)循環(huán)冷卻水微生物控制宜以氧化型殺菌劑為主,非氧化型殺菌劑為輔。當(dāng)氧化型殺菌劑連續(xù)投加時,應(yīng)控制余氯量為0.1~0.5mg/L;沖擊投加時,宜每天投加2~3次,每次投加時間宜控制水中余氯0.5~1mg/L,保持2~3h。非氧化型殺菌劑宜選擇多種交替使用。
5)循環(huán)冷卻水濃縮倍數(shù)應(yīng)按照有關(guān)要求進行控制,當(dāng)出現(xiàn)超標(biāo)時,可采取增大排污量的方式來調(diào)整;循環(huán)冷卻水出換熱器的溫度控制推薦不超過50℃;各裝置應(yīng)根據(jù)實際情況建立腐蝕監(jiān)檢測系統(tǒng)和腐蝕管理系統(tǒng),保證生產(chǎn)的安全運行。
水冷器管束防腐
1)升級材質(zhì)
嚴(yán)格控制水冷器管束材料的加工、熱處理工藝,使用更合適的材料,可以有效緩解循環(huán)水結(jié)垢、垢下腐蝕等。目前,大多數(shù)煉廠水冷器管束材質(zhì)以碳鋼為主,對腐蝕嚴(yán)重部位可升級材質(zhì)以提高水冷器的使用壽命。煉化裝置中應(yīng)用較多的高等級水冷器管束材質(zhì)有08Cr2A1Mo、092A1MoRe、022Cr19Ni10、022Cr17Ni12Mo,雙相鋼、鈦材等。奧氏體不銹鋼具有良好的耐蝕性,并且結(jié)垢不易附著管壁表面,使用效果較好,但在使用過程中要嚴(yán)格控制循環(huán)水以及工藝介質(zhì)氯離子的含量。進行材質(zhì)升級時,應(yīng)從介質(zhì)控制、防腐涂料、陰極保護、經(jīng)濟效益等方面綜合考慮。
2)防腐涂料
水冷器管束涂料防腐已廣泛應(yīng)用于煉油裝置的冷換設(shè)備。采用耐腐蝕涂料解決碳鋼換熱器管束的腐蝕與結(jié)垢問題,可取得較好的效果。通過使用性價比較高的防腐涂料,可有效延長水冷器的使用壽命,節(jié)約鋼材,增加經(jīng)濟效益。
3)犧牲陽極用犧牲陽極法對管板和管束進行保護,是防止水冷器在循環(huán)水中腐蝕的重要手段之一。該措施不但可延長碳鋼材料水冷器使用壽命,而且可達到提高防腐效果與降低成本的雙重效果。一般常用的犧牲陽極材料有鋁、鎂、鋅3種,分別適用于不同的腐蝕介質(zhì)。煉廠水冷器的保護宜選擇使用鎂合金犧牲陽極。在使用鎂陽極塊的時候,要做好犧牲陽極規(guī)格的選取、保護面積的計算及安裝位置的確定工作
免責(zé)聲明:本網(wǎng)站所轉(zhuǎn)載的文字、圖片與視頻資料版權(quán)歸原創(chuàng)作者所有,如果涉及侵權(quán),請第一時間聯(lián)系本網(wǎng)刪除。
相關(guān)文章
無相關(guān)信息
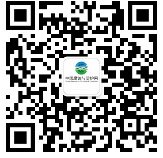
官方微信
《中國腐蝕與防護網(wǎng)電子期刊》征訂啟事
- 投稿聯(lián)系:編輯部
- 電話:010-62316606-806
- 郵箱:fsfhzy666@163.com
- 中國腐蝕與防護網(wǎng)官方QQ群:140808414
文章推薦
點擊排行
PPT新聞
“海洋金屬”——鈦合金在艦船的
點擊數(shù):7130
腐蝕與“海上絲綢之路”
點擊數(shù):5741