摘要
利用U形彎試樣浸泡實驗和電化學(xué)測試技術(shù)研究了兩種油套管鋼在CO2注入井環(huán)空環(huán)境中的應(yīng)力腐蝕開裂行為。結(jié)果表明,TP110TS鋼和P110鋼在注入井環(huán)空環(huán)境 (大量CO2-微量H2S) 下存在一定的應(yīng)力腐蝕敏感性,其應(yīng)力腐蝕機制為陽極溶解和氫脆協(xié)同作用機制。在CO2-H2S環(huán)境下,咪唑啉類緩蝕劑的濃度對TP110TS和P110油套管鋼的應(yīng)力腐蝕產(chǎn)生不同的影響,添加足量的緩蝕劑對P110鋼的應(yīng)力腐蝕行為產(chǎn)生較好的抑制效果;但當(dāng)添加量不足時,緩蝕劑會增加P110鋼發(fā)生應(yīng)力腐蝕的傾向性。而TP110TS鋼的應(yīng)力腐蝕敏感性隨著緩蝕劑濃度的增加而減小,相對更適用于添加緩蝕劑的CO2-H2S環(huán)境。
關(guān)鍵詞: TP110TS鋼; P110鋼; 環(huán)空環(huán)境; 應(yīng)力腐蝕; CO2注入井
當(dāng)前油氣田生產(chǎn)中,越來越多的新型技術(shù)被用來提高生產(chǎn)效率,其中CO2驅(qū)注技術(shù)就因其具有更好的采收優(yōu)勢而被廣泛用于取代傳統(tǒng)水驅(qū)注[1,2]。然而,由于油管中所注入的CO2、污水 (含Cl-,SO42-等) 等易通過環(huán)空管泄漏,從而導(dǎo)致環(huán)空液的pH值降低,并且在這種密閉的環(huán)空環(huán)境下,硫酸鹽還原菌 (SRB) 的存在會導(dǎo)致管內(nèi)H2S含量升高。這種嚴苛的環(huán)境極易導(dǎo)致油套管的斷裂損壞,造成重大的經(jīng)濟損失和安全事故,嚴重影響石油開采的安全運行[3,4,5]。在這種H2S/CO2共存環(huán)境下,服役的油套管具有極高的應(yīng)力腐蝕開裂 (SCC) 危險性[6,7,8,9,10]。目前,雖然CO2或H2S環(huán)境中的腐蝕行為被廣泛研究[10,11,12,13],但實際生產(chǎn)過程中為了防止或減緩這種環(huán)境下的腐蝕問題,國內(nèi)外油氣田中多采用加注緩蝕劑的方法。而在各種緩蝕劑中,咪唑啉緩蝕劑以其低毒性、較好的防腐性和熱穩(wěn)定性成為國內(nèi)外油氣田中常用的緩蝕劑,其在H2S/CO2共存環(huán)境下表現(xiàn)出較好的耐蝕性能[14,15,16]。但對于含有緩蝕劑與H2S/CO2共存環(huán)境下油套管的腐蝕研究,大多數(shù)只關(guān)注油管內(nèi)的腐蝕問題,對于這種復(fù)雜油套管間CO2-H2S環(huán)空環(huán)境體系中的腐蝕問題有待進一步研究。
本文利用靜載荷應(yīng)力腐蝕實驗和電化學(xué)測試技術(shù),研究了咪唑啉緩蝕劑對TP110TS和P110油套管在CO2-H2S環(huán)空環(huán)境體系下的應(yīng)力腐蝕行為,為CO2注入井環(huán)空環(huán)境腐蝕防護方法的建立提供參考和依據(jù),更為復(fù)雜環(huán)境下服役材料的選擇提供一定的數(shù)據(jù)支撐。
1 實驗方法
實驗材料為P110和TP110TS油套管鋼,其化學(xué)成分如表1所示。參照測試標(biāo)準(zhǔn)GB/T13298-2015《金屬顯微組織檢驗方法》[17]對P110和TP110TS鋼進行金相組織觀察。實驗所用溶液為根據(jù)現(xiàn)場提取的某油田CO2驅(qū)注井環(huán)空保護液成分配置的模擬溶液。其母液成分 (g/L) 為:NaHCO3 2.71,NaCl 6.15,Na2SO4 0.33,使用0.5% (質(zhì)量分數(shù)) CH3COOH溶液調(diào)節(jié)溶液pH值至4,所用試劑均為化學(xué)純。配置溶液前,先通入高純N2除氧,以防止硫化物氧化。所用緩蝕劑為某商用咪唑啉類緩蝕劑。電化學(xué)實驗試樣尺寸為10 mm×10 mm×3 mm,并使用環(huán)氧樹脂密封,浸泡實驗試樣采用U形彎試樣。實驗前將試樣用砂紙逐級打磨至2000#,然后用丙酮清洗試樣表面并吹干備用。每組實驗取3個平行樣品進行實驗。實驗條件為:氣體總壓9 MPa,其中,H2S分壓為0.2 MPa,CO2分壓為4 MPa;溶液pH值為4,實驗溫度為室溫。
表1 TP110TS和P110油管鋼的化學(xué)組成
電化學(xué)測量采用三電極體系,Ag/AgCl電極為參比電極,Pt電極為輔助電極,試樣為工作電極。實驗前,用丙酮將試樣和Pt電極表面除油,裝入溶液介質(zhì),將電極組裝好后連接到高壓釜內(nèi)。密閉高壓釜,并通入N2除氧2 h,然后依次通入H2S,CO2和N2至所需分壓。加壓后靜置30 min,以保證開路電位穩(wěn)定。然后,在PARSTAT-2273電化學(xué)工作站上進行極化曲線和阻抗測量。極化曲線測試電位掃描由陰極向陽極進行,電位掃描范圍為-500~800 mV (vs OCP),掃描速率為0.5 mV/s;電化學(xué)阻抗測試頻率范圍為105~10-2 Hz,激勵電位為10 mV。
U形彎浸泡實驗與電化學(xué)實驗的測試條件相同。首先將U形彎平板試樣壓彎至張角為10°±1°自然回彈,然后用螺栓加載至張角為0° (U形)。對螺栓部位密封并將試樣表面進行除油后,將試樣置于高壓釜中進行浸泡,浸泡時間為720 h。浸泡結(jié)束后,先利用線切割機切下觀察部位并用丙酮進行除油。然后,將試樣置于除銹液 (500 mL HCl+500 mL H2O+3.5 g六次甲基四胺) 中超聲清洗去除腐蝕產(chǎn)物,再用丙酮清洗并吹干。利用FEI Quanta200型掃描電鏡 (SEM) 對浸泡后試樣的表面形貌進行觀察。
2 實驗結(jié)果
2.1 顯微組織
P110和TP110TS鋼的金相組織如圖1所示。可見,P110和TP110TS鋼的金相組織均為馬氏體+部分鐵素體,組織相對均勻,沒有明顯的軋制織構(gòu)特征。鋼中的夾雜物不明顯,其密度相對較低、尺寸較小,未發(fā)現(xiàn)扁平狀或點鏈狀夾雜物。比較P110和TP110TS鋼的金相組織,雖然都為馬氏體加部分鐵素體,但組織的大小和均勻程度還存在一定的差別。比較而言,TP110TS鋼的組織更加均勻,經(jīng)過回火處理之后馬氏體板條結(jié)構(gòu)退化、粒狀滲碳體析出增多。
圖1 P110和TP110TS油管鋼的金相組織
2.2 靜載荷應(yīng)力腐蝕實驗
2.2.1 宏觀形貌分析
圖2是U彎試樣在不同濃度緩蝕劑條件下浸泡720 h后的表面宏觀形貌圖。從圖2a和b中可以看出,當(dāng)不添加緩蝕劑時,TP110TS和P110鋼表面均發(fā)生了嚴重的腐蝕,并且試樣均發(fā)生了斷裂。這說明兩種材料在該環(huán)境下均易發(fā)生SCC,具有很高的應(yīng)力腐蝕敏感性。而當(dāng)添加濃度1 g/L咪唑啉緩蝕劑時,TP110TS和P110鋼表面腐蝕較為輕微,沒有明顯的腐蝕產(chǎn)物,表面依然有金屬光澤。緩蝕劑的添加對P110和TP110TS試樣SCC均產(chǎn)生了一定的抑制效果。
圖2 TP110TS和 P110鋼在添加不同濃度緩蝕劑條件下浸泡720 h后的宏觀形貌
進一步對不同實驗條件下的U彎試樣SCC情況進行統(tǒng)計,結(jié)果見表2。結(jié)果表明,在無緩蝕劑時,每組試樣均發(fā)生了斷裂,試樣表面發(fā)生嚴重的腐蝕。不同的是,P110鋼試樣表面具有明顯的均勻腐蝕和裂紋的形貌,而TP110TS鋼主要是以點蝕坑居多。這可能與兩種材料本身的耐蝕性能具有一定的相關(guān)性。隨緩蝕劑濃度的增加,P110和TP110TS鋼表面的點蝕情況均得到了改善;當(dāng)緩蝕劑濃度達1 g/L時,兩種材料的應(yīng)力腐蝕均得到了明顯抑制。
表2 不同緩蝕劑濃度條件下兩類油套管鋼U形彎腐蝕及開裂情況對比
2.2.2 U形彎應(yīng)力腐蝕微觀形貌
圖3是U彎試樣在不同濃度緩蝕劑條件下浸泡720 h,去除表面腐蝕產(chǎn)物后的表面微觀形貌。可以看出,在不添加緩蝕劑時,兩種材料的試樣表面都存在著嚴重的點蝕坑和裂紋。這說明在不添加緩蝕劑情況下,TP110TS和P110鋼在上述環(huán)境服役時均有發(fā)生嚴重SCC的傾向性。而當(dāng)添加一定濃度咪唑啉緩蝕劑時,對TP110TS鋼試樣腐蝕產(chǎn)生了一定的抑制效果,并且這種效果隨著緩蝕劑濃度的增加,試樣表面點蝕坑的深度和數(shù)量均呈現(xiàn)出明顯減少的趨勢。當(dāng)添加緩蝕劑濃度為0.4 g/L時,P110鋼表面幾乎不發(fā)生均勻腐蝕,但有大量的點蝕坑分布;而TP110TS鋼試樣表面的點蝕坑數(shù)量和深度呈現(xiàn)明顯減少的趨勢。當(dāng)緩蝕劑濃度達到1 g/L時,P110鋼表面的點蝕數(shù)量和深度銳減;而TP110TS鋼表面發(fā)生了輕微的點蝕,幾乎不腐蝕。當(dāng)緩蝕劑濃度大于0.4 g/L時,兩種材料的SCC和點腐蝕情況明顯減輕,試樣的腐蝕情況逐漸減弱,耐腐蝕能力逐漸加強。
圖3 P110和 TP110TS鋼在不同濃度緩蝕劑條件下浸泡720 h除銹后的微觀形貌
2.3 電化學(xué)測試結(jié)果
為了進一步分析不同濃度緩蝕劑對兩種材料SCC的影響機理,測試了P110鋼和TP110TS鋼在不同濃度緩蝕劑下的極化曲線和電化學(xué)阻抗譜。圖4是不同緩蝕劑濃度下TP110TS和P110鋼的極化曲線圖。表3為極化曲線擬合結(jié)果。可以看出,TP110TS鋼的自腐蝕電位 (Ecorr) 隨緩蝕劑濃度的增加不斷提高,并且腐蝕電流密度也呈現(xiàn)出減小的趨勢。這與U彎浸泡實驗結(jié)果相似,緩蝕劑的加入減緩了TP110TS鋼的腐蝕行為,進而對SCC產(chǎn)生了影響。對于P110鋼,當(dāng)緩蝕劑濃度大于0.4 g/L時,自腐蝕電流密度下降,而自腐蝕電位上升,這可能是由于P110鋼發(fā)生均勻腐蝕向點蝕轉(zhuǎn)變導(dǎo)致的。并且,通過極化曲線也可以看出,咪唑啉緩蝕劑對P110鋼的陰極過程有較明顯的抑制作用。
圖4 不同緩蝕劑濃度下TP110TS和P110鋼的極化曲線
表3 不同緩蝕劑濃度下TP110TS和P110鋼的極化曲線擬合結(jié)果
圖5為TP110TS和P110鋼在不同濃度緩蝕劑溶液中的EIS曲線,其擬合電路如圖6所示。其中,Rs 代表溶液電阻,Qf為腐蝕產(chǎn)物層電容的常相位角元件,Rf表示腐蝕產(chǎn)物電阻,Qdl為雙電層電容的常相位角元件,Rct表示電荷轉(zhuǎn)移電阻。表4為EIS擬合的電化學(xué)參數(shù)。從圖5中可以看出,緩蝕劑濃度的變化對TP110TS鋼和P110鋼的電化學(xué)過程均產(chǎn)生較大的影響,對于TP110TS鋼,隨緩蝕劑濃度的增大,電化學(xué)阻抗譜形狀未有變化,但容抗弧半徑增大。這說明對于TP110TS鋼,緩蝕劑濃度越大,耐腐蝕能力越強。緩蝕劑濃度增大,腐蝕電流呈減小的趨勢,說明緩蝕劑濃度越大,腐蝕速率越低。緩蝕劑的添加使得雙電層傳質(zhì)過程受到明顯的抑制,并抑制了硫化物吸附和H的析出過程,導(dǎo)致腐蝕性介質(zhì)通過緩蝕劑膜的阻力相應(yīng)增大。而對于P110鋼,當(dāng)緩蝕劑添加量大于0.4 g/L時,阻抗值明顯增大。這與極化曲線中的結(jié)果相一致。對比TP110TS和P110鋼的Nyquist圖可以看出,阻抗值的變化規(guī)律為:P110-1 g/L>TP110TS-1 g/L>TP110TS-0.4 g/L>P110-0.4 g/L,這與極化曲線中的自腐蝕電流密度結(jié)果相一致。這也表明,緩蝕劑的添加能有效增加雙電層的電阻,抑制腐蝕介質(zhì)與材料的反應(yīng),從而提高了材料的耐蝕性能。
圖5 不同緩蝕劑濃度下TP110TS和P110鋼的電化學(xué)阻抗譜
圖6 不同緩蝕劑濃度下TP110TS和P110鋼EIS的等效電路圖
表4 不同緩蝕劑濃度下TP110TS和P110鋼的電化學(xué)等效電路圖擬合結(jié)果
3 討論
當(dāng)前研究[18,19,20]表明,CO2驅(qū)駐井下油管鋼的腐蝕機理是一種典型的高H2S-CO2-Cl-環(huán)境的應(yīng)力腐蝕開裂。在實際的生產(chǎn)過程中,油管鋼會發(fā)生一些刺漏現(xiàn)象,這種現(xiàn)象會隨著服役時間的延長變得更為嚴重,由于漏點的存在會導(dǎo)致CO2等進入環(huán)空液,致使環(huán)空液pH值降低。又由于油管鋼的服役環(huán)境處于封閉狀態(tài),導(dǎo)致SRB的大量增加,從而促進了硫化物的轉(zhuǎn)變。因而在該環(huán)境下,油管鋼腐蝕過程主要是H+的還原反應(yīng)和鐵與硫化物、碳酸鹽等進行的反應(yīng)。具體如下[21,22]:
因此,在不添加緩蝕劑的條件下,在CO2,Cl-和H2S的作用下,油管鋼表面會產(chǎn)生大量的Hasd,導(dǎo)致油管鋼發(fā)生嚴重的SCC,如圖2和表2中所示,試樣易發(fā)生斷裂。其SCC機制具有一定的氫脆 (HE) 特征。
而當(dāng)在模擬環(huán)空溶液環(huán)境中添加咪唑啉類緩蝕劑后,緩蝕劑能夠在試樣表面形成一層具有較強結(jié)合力的吸附層,腐蝕產(chǎn)物與緩蝕劑相互結(jié)合,從而提升了表面腐蝕產(chǎn)物膜的致密性。另一方面,緩蝕劑還可以與鐵離子等形成絡(luò)合,進而增強了產(chǎn)物膜中分子間的結(jié)合力。通過上述兩種機制能夠有效地抑制雙電層的電化學(xué)反應(yīng),降低腐蝕速率。而在添加不同濃度緩蝕劑條件下,TP110TS和P110兩種油管鋼的腐蝕行為并不一致。當(dāng)緩蝕劑濃度較低時,P110鋼的表面不能完全被緩蝕劑所覆蓋,這會導(dǎo)致存在局部點暴露在溶液中,在一些活性離子 (Cl-) 作用下,產(chǎn)生局部腐蝕,從而導(dǎo)致局部陽極溶解的存在,因而在圖3中可以看到較多的點蝕坑的出現(xiàn)。這些局部點蝕坑的存在,進一步加速了P110鋼的SCC行為。而TP110TS鋼基體在模擬溶液中表現(xiàn)出較P110鋼更好的耐蝕性能,如圖3d所示。隨著緩蝕劑濃度的進一步增大,P110鋼表面的活性點被緩蝕劑進一步抑制,緩蝕劑與試樣表面形成更為緊密的吸附膜,進而抑制了表面點蝕坑的數(shù)量,并且這一結(jié)果也體現(xiàn)在圖4的結(jié)果中。當(dāng)緩蝕劑濃度在1 g/L時,P110鋼和TP110TS鋼的腐蝕電流密度都遠小于在0.4 g/L情況下的,通過電化學(xué)阻抗譜也可以看出其極化電阻呈現(xiàn)出明顯的增大現(xiàn)象 (圖5)。因此,在CO2注入井環(huán)空環(huán)境下,足量的咪唑啉緩蝕劑能有效抑制SCC,但當(dāng)用量不足時,緩蝕劑的添加會增大P110鋼發(fā)生應(yīng)力腐蝕的傾向性,其SCC機制為氫脆與局部陽極溶解的混合機制。而TP110TS鋼則不會出現(xiàn)該現(xiàn)象,其SCC敏感性隨著緩蝕劑濃度的增加而不斷減小。
4 結(jié)論
(1) TP110TS鋼和P110鋼在CO2注入井環(huán)空環(huán)境中均會發(fā)生應(yīng)力腐蝕,為陽極溶解和氫脆混合反應(yīng)機制。
(2) 咪唑啉類緩蝕劑濃度對TP110TS鋼和P110鋼的應(yīng)力腐蝕行為具有不同的影響作用。當(dāng)緩蝕劑濃度不足時,P110鋼的應(yīng)力腐蝕敏感性有增大的趨勢。而對于TP110TS鋼,隨著緩蝕劑含量增加,耐應(yīng)力腐蝕能力增強。TP110TS鋼較P110鋼更適合用于添加緩蝕劑的CO2-H2S環(huán)境。
免責(zé)聲明:本網(wǎng)站所轉(zhuǎn)載的文字、圖片與視頻資料版權(quán)歸原創(chuàng)作者所有,如果涉及侵權(quán),請第一時間聯(lián)系本網(wǎng)刪除。
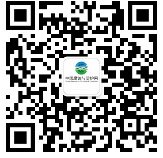
官方微信
《中國腐蝕與防護網(wǎng)電子期刊》征訂啟事
- 投稿聯(lián)系:編輯部
- 電話:010-62316606-806
- 郵箱:fsfhzy666@163.com
- 中國腐蝕與防護網(wǎng)官方QQ群:140808414