海洋資源的開發(fā)利用需要大量海上設(shè)施設(shè)備,如用于海洋石油開采的鉆井平臺,海洋風(fēng)力發(fā)電設(shè)備及跨海大橋等。目前,作為海上設(shè)備平臺使用的工程結(jié)構(gòu)材料多為金屬材料,在惡劣的高腐蝕海洋環(huán)境中極易發(fā)生腐蝕。目前,在全浸泡環(huán)境中金屬材料的防腐蝕措施通常采用重防腐涂料聯(lián)合陰極保護(hù)作為主要的腐蝕防護(hù)手段。
然而,陰極保護(hù)會產(chǎn)生過剩的OH-使得涂層與金屬界面發(fā)生堿化,從而導(dǎo)致涂層陰極剝離。關(guān)于陰極剝離已有許多學(xué)者進(jìn)行了研究。Bi等研究了低碳鋼表面涂層下陰極氧還原與陰極剝離的關(guān)系,認(rèn)為氧的還原反應(yīng)產(chǎn)生的界面堿化導(dǎo)致了涂層的剝離。Shi等使用局部掃描振動電極技術(shù) (SVET) 研究了低碳鋼上缺陷環(huán)氧涂層防護(hù)作用,結(jié)果表明:施加陰極保護(hù),涂層缺陷處形成的鈣質(zhì)膜層有利于陰極保護(hù)過程。Eltai等認(rèn)為陰極保護(hù)導(dǎo)致完好環(huán)氧清漆涂層的阻抗下降,涂層的吸水量由于陰極保護(hù)電位的提高而增加。李玉楠研究了陰極保護(hù)對破損有機(jī)涂層防護(hù)作用的影響,結(jié)果表明:完好涂層的-850 mV (vs Cu/CuSO4) 保護(hù)準(zhǔn)則對破損涂層是不適用的,為了陰極保護(hù)能夠發(fā)揮正常的作用,應(yīng)該將保護(hù)電位負(fù)移。張麗研究了外加電流陰極極化下環(huán)氧清漆及環(huán)氧富鋅涂層的失效行為,結(jié)果表明:對環(huán)氧清漆涂層施加-900 mV (vs SCE) 陰極保護(hù)后,增強(qiáng)了基材/涂層界面處的堿性環(huán)境,加速了涂層中交聯(lián)結(jié)構(gòu)破壞,減弱了基材/涂層界面處的附著力,降低了涂層壽命。
本文主要研究不同陰極保護(hù)電位對破損環(huán)氧涂層下海洋平臺研制鋼的陰極保護(hù)效果及對破損的高附著化學(xué)鍵合防腐涂料防腐性能的影響及陰極剝離機(jī)理。
1 實(shí)驗(yàn)方法
實(shí)驗(yàn)中所用的金屬基體材料為海洋平臺研制鋼,其化學(xué)成分 (質(zhì)量分?jǐn)?shù),%) 為:C 2.76,Mo 0.58,Si 0.24,Ni 2.61,Cr 0.79,F(xiàn)e 92.48。鋼片的尺寸為50 mm×50 mm×3 mm,參照GB 13288-1991《涂裝前鋼材表面粗糙度等級的評定》中關(guān)于涂裝前鋼材的表面粗糙度等級相關(guān)規(guī)定,將試樣進(jìn)行噴砂處理,再經(jīng)丙酮超聲除油,無水乙醇除水,吹干,置于干燥器中備用。
本實(shí)驗(yàn)所用的涂料是由哈爾濱工程大學(xué)研制的HGL-2化學(xué)鍵合防腐涂料底漆,使用前按A、B組分質(zhì)量比3∶1混合攪勻,抽真空除去涂料中氣泡,靜置1 h后,均勻涂覆到備用鋼片上。25 ℃固化24 h后,60 ℃固化48 h。
采用Ф=3 mm的鉆孔器人為制造涂層缺陷,缺陷面積約占測試面積的0.6%。
采用PosiTector6000測厚儀測定涂層厚度,選取固化后涂層厚度為 (100±5) μm的試樣進(jìn)行電化學(xué)阻抗譜 (EIS) 測試。
本實(shí)驗(yàn)施加陰極保護(hù)的恒電位儀為IviumStat電化學(xué)工作站,參比電極為飽和甘汞電極,輔助陽極為自制的高純度石墨電極,有效實(shí)驗(yàn)面積為11.34 cm2,破損面積約占測試面積的0.6%。實(shí)驗(yàn)在室溫靜態(tài)模擬海水中進(jìn)行,實(shí)驗(yàn)裝置示意圖如圖1所示。本實(shí)驗(yàn)采用人工海水溶液,溶液配方參照國標(biāo)GB/T 7790-2008,NaCl:23 g/L,MgCl2·10H2O:9.8 g/L,Na2SO4·10H2O:8.9 g/L,CaCl2:1.2 g/L。
對于海洋工程而言,金屬材料所要求的陰極保護(hù)電位比穩(wěn)態(tài)下自腐蝕電位至少低200 mV;對于涂覆有機(jī)涂層的保護(hù)體系,目前最常使用的電位規(guī)范是-850 mV (vs Cu/CuSO4),即-780 mV (vs SCE)。潘大偉等研究了-750~-950 mV (vs Ag/AgCl) 電位對于海洋高強(qiáng)鋼 裸鋼)的保護(hù)效果,結(jié)果表明最佳的陰極保護(hù)電位區(qū)間為-0.76~-0.94 V。眾所周知有機(jī)涂層本身具有防護(hù)效果,可以降低陰極保護(hù)電位;而-780 mV (vs SCE) 是完整涂層常用的保護(hù)電位,不是其最低的保護(hù)電位。本實(shí)驗(yàn)所用的試樣是0.6%破損的有機(jī)涂層金屬體系,所以為了方便電位節(jié)點(diǎn)的設(shè)置 (本實(shí)驗(yàn)以100 mV為梯度來設(shè)置保護(hù)電位) 以及參考海洋工程中有機(jī)涂層選擇的陰極保護(hù)電位,故而本文選擇了-750,-850,-950和-1050 mV (vs SCE) 對海洋平臺研制鋼在模擬海水中進(jìn)行HGL-2化學(xué)鍵合防腐涂料與陰極保護(hù)聯(lián)合保護(hù)效果的研究。
施加了不同陰極保護(hù)電位的涂層耐腐蝕性能測試采用PGSTAT302電化學(xué)工作站進(jìn)行EIS測試。測試選用三電極體系:施加陰極保護(hù)電位的試樣為工作電極,Pt片為輔助電極,飽和甘汞電極為參比電極 (SCE)。阻抗測試頻率范圍為105~10-2 Hz,擾動信號為10 mV,試樣測試面積為11.34 cm2,破損面積約占測試面積的0.6%。測試溶液為人工海水溶液。為了防止外界電磁信號的干擾,EIS測試在Faraday屏蔽籠里進(jìn)行。測試得到的EIS數(shù)據(jù)均采用ZSimpWin軟件進(jìn)行擬合。
采用JSM-6480型掃描電子顯微鏡 (SEM) 對涂層下的金屬基體進(jìn)行表面微觀形貌觀察,采用SAM型X射線能譜儀 (EDS) 對金屬基體元素進(jìn)行分析,并采用X'PertPro型X射線衍射儀 (XRD) 對金屬表面附著產(chǎn)物進(jìn)行物相分析。根據(jù)國標(biāo)GBT 16545-2015 金屬和合金的腐蝕 -腐蝕試樣上腐蝕產(chǎn)物的清除,采用浸泡法去除金屬表面的附著物。
2 結(jié)果與討論
2.1 宏觀腐蝕形貌
破損涂層施加不同陰極保護(hù)電位1056 h后,試樣的宏觀表面形貌如圖2所示。在開路電位 (未施加陰極保護(hù)) 下的試樣 (圖2a) 破損處發(fā)生了嚴(yán)重的腐蝕,涂層表面附著了大量的腐蝕產(chǎn)物,破損涂層周圍未見明顯鼓泡現(xiàn)象。施加陰極保護(hù)電位的試樣(圖2b~e),破損處的金屬腐蝕程度降低,表面無明顯銹蝕產(chǎn)生;但隨著陰極保護(hù)電位的增加,破損處白色沉積物增多,破損周圍的涂層發(fā)生鼓泡的程度增大。施加不同陰極保護(hù)電位1056 h后涂層鼓泡情況見表1。每個(gè)電位下均觀察4個(gè)平行試樣,鼓泡數(shù)目及鼓泡處距離破損邊緣的距離均為4個(gè)平行試樣的平均值。可見,施加不同陰極保護(hù)電位1056 h后,隨著電位的負(fù)移,涂層鼓泡數(shù)量增多,鼓泡處距離破損邊緣的距離變大。
圖3為施加不同陰極保護(hù)電位后涂層陰極剝離形貌。每個(gè)電位下均觀察4個(gè)平行試樣,陰極剝離距離及剝離面積均為4個(gè)平行試樣的平均值。施加不同保護(hù)電位1056 h后涂層的剝離距離及剝離面積見表2。圖4為圖3c腐蝕處的局部放大圖,A處于未腐蝕區(qū)域,B處于圖中黑色腐蝕區(qū)域,A和B處的EDS分析結(jié)果見表3。
由圖3及表2可知,開路電位下的涂層陰極剝離面積最小,僅54 mm2,但破損處有明顯腐蝕發(fā)生。在-750 mV保護(hù)電位下,剝離面積增大 (增至117 mm2),破損處仍有腐蝕發(fā)生,說明此時(shí)處于欠保護(hù)狀態(tài)。-850 mV保護(hù)電位下,剝離面積進(jìn)一步增大 (增至169 mm2),破損處未發(fā)生腐蝕,說明對破損處金屬基體保護(hù)效果較好。但在涂層鼓泡處,基體顏色較深,EDS結(jié)果 (圖4及表3) 顯示鼓泡區(qū)域O含量 (原子分?jǐn)?shù)) 要略高于未鼓泡區(qū)域的,而Fe含量要略少于未鼓泡區(qū)域的,說明鼓泡處仍有一定腐蝕,但腐蝕非常弱。這是由于涂層的電流屏蔽作用,尤其是在涂層鼓泡失效后,涂層下的金屬可能未達(dá)到完全停止腐蝕所需的保護(hù)電流。對于-950 mV保護(hù)電位而言,陰極剝離程度與-850 mV保護(hù)電位下的相比略有增加 (增至183 mm2),但破損處與剝離處均未發(fā)生腐蝕,保護(hù)效果良好。-1050 mV保護(hù)電位下,破損處發(fā)生了嚴(yán)重的析氫現(xiàn)象,基體雖未發(fā)生腐蝕,但涂層剝離面積劇增 (增至243 mm2)。
2.2 EIS測試
EIS技術(shù)常被用于腐蝕過程的研究。本實(shí)驗(yàn)對不同保護(hù)電位下的試樣進(jìn)行EIS測試,其測試結(jié)果采用圖5中的等效電路圖進(jìn)行擬合。由于破損區(qū)域較大,電化學(xué)阻抗主要反映破損處及涂層剝離區(qū)域的信息。其中,Rs是電解質(zhì)溶液電阻;Qc是常相位角元件,代表沉淀膜電容;Rf是沉淀膜層電阻;Qdl代表雙電層電容;Rt代表電荷轉(zhuǎn)移電阻。
圖6a為開路電位下試樣的EIS測試結(jié)果。結(jié)果顯示,隨著浸泡時(shí)間的延長,容抗弧半徑減小,測試體系的低頻阻抗模值不斷地下降,說明隨著浸泡時(shí)間的延長,試樣腐蝕程度不斷加劇。在浸泡開始階段 (100 h),由于涂層破損處無保護(hù)作用,采用一個(gè)時(shí)間常數(shù)進(jìn)行擬合 (圖5a) ;隨著浸泡時(shí)間的延長,腐蝕產(chǎn)物不斷堆積,在破損處的表面形成了腐蝕產(chǎn)物膜,浸泡后期采用兩個(gè)時(shí)間常數(shù)進(jìn)行擬合 (圖5b)。
圖6b是在-750 mV保護(hù)電位下的EIS測試結(jié)果。在浸泡97 h內(nèi),涂層容抗弧稍有增大,這可能是破損處產(chǎn)生了稀疏的沉積層導(dǎo)致阻抗略增大;之后,破損處發(fā)生了腐蝕,阻抗下降,說明在模擬海水中,-750 mV保護(hù)電位不能完全為基體提供保護(hù)。在實(shí)驗(yàn)初期 (100 h),采用一個(gè)時(shí)間常數(shù) (圖5a) 進(jìn)行擬合,隨著時(shí)間的延長,破損處表面生成稀疏的沉積層,采用兩個(gè)時(shí)間常數(shù) (圖5b) 進(jìn)行擬合。
圖6c是-850 mV保護(hù)電位下的EIS圖。隨著時(shí)間的延長,涂層的容抗弧增大,阻抗值呈現(xiàn)上升趨勢,腐蝕傾向較小,說明破損處金屬處于保護(hù)狀態(tài)。在實(shí)驗(yàn)過程中,破損處逐漸形成了一層白色沉積層,導(dǎo)致體系中阻抗上升。說明這層沉積層對破損處的金屬有一定的保護(hù)作用,采用兩個(gè)時(shí)間常數(shù) (圖5b) 進(jìn)行擬合 (100 h之后)。
圖6d是在-950 mV保護(hù)電位下的EIS圖,與圖6c相似,隨著時(shí)間的延長,涂層的阻抗值呈現(xiàn)上升趨勢,說明破損處金屬處于保護(hù)狀態(tài),腐蝕傾向較小。破損處形成了沉淀層,采用兩個(gè)時(shí)間常數(shù)的等效電路圖 (圖5b) 進(jìn)行擬合 (100 h之后)。
圖6e是在-1050 mV保護(hù)電位下的EIS圖。在施加1056 h陰極保護(hù)期間,體系的阻抗值先升高后稍有降低,50 h后譜圖體現(xiàn)出兩個(gè)時(shí)間常數(shù)的信息,采用圖5b進(jìn)行擬合,并且在實(shí)驗(yàn)過程中破損處可觀察到十分嚴(yán)重的析氫現(xiàn)象。
2.3 不同保護(hù)電位對鈣質(zhì)沉積層保護(hù)性能的影響分析
Rt表征金屬腐蝕發(fā)生的難易程度,Rt越高,金屬越不容易發(fā)生腐蝕。圖7為不同保護(hù)電位下的EIS數(shù)據(jù)擬合的Rt隨時(shí)間的變化曲線。由等效電路圖可知,在實(shí)驗(yàn)過程中,EIS主要反映破損處金屬基體的信息。在開路電位下,Rt從開始的103 Ω·cm2下降到400 Ω·cm2,之后穩(wěn)定在約200 Ω·cm2,表明金屬基體隨著浸泡時(shí)間的延長,更容易發(fā)生腐蝕。-750 mV保護(hù)電位下,實(shí)驗(yàn)初期Rt稍有上升,100 h后略有下降,之后穩(wěn)定在約3×103 Ω·cm2;-850 mV保護(hù)電位下,Rt逐漸上升,100 h后穩(wěn)定在約4×103 Ω·cm2。-950 mV保護(hù)電位下,Rt逐漸上升,180 h后達(dá)到約2×104 Ω·cm2,之后穩(wěn)定在1.2×104 Ω·cm2,具有最好的耐蝕性能。-1050 mV保護(hù)電位下,Rt逐漸上升,84 h后達(dá)到最高值約1.2×104 Ω·cm2;之后稍有降低,耐蝕性能略有下降。
Rf一定程度上反映了鈣質(zhì)沉積層保護(hù)性能的好壞,Rf值越高,鈣質(zhì)沉積層保護(hù)性能越好。圖8為施加保護(hù)電位1056 h期間不同保護(hù)電位下的Rf隨時(shí)間的變化曲線。由圖可知,在開路電位及-750 mV保護(hù)電位下,Rf均很小,在10~100 Ω·cm2之間變化,沉積層幾乎無保護(hù)作用。-850 mV保護(hù)電位下,破損處Rf較開路電位和-750 mV保護(hù)電位下的略大,約在100 Ω·cm2變化。-950 mV保護(hù)電位下的Rf值一直呈現(xiàn)增大趨勢,在350 h后穩(wěn)定在約2000 Ω·cm2。施加-1050 mV保護(hù)電位前期 (150 h),Rf值上升,之后略有下降,穩(wěn)定在約800 Ω·cm2。結(jié)果顯示,-950 mV保護(hù)電位下,鈣質(zhì)沉積層的保護(hù)性能最佳。
圖9為施加不同保護(hù)電位破損處沉積層物相分析結(jié)果。可見,在開路電位下破損處的腐蝕產(chǎn)物膜層成分為Fe2O3;-750 mV保護(hù)電位下,沉淀膜成分為CaCO3和Fe2O3,無Mg(OH)2;-850,-950和-1050 mV保護(hù)電位下沉積層的成分均為CaCO3和Mg(OH)2的混合物,無Fe2O3。李成杰等[17]研究了在靜態(tài)及動態(tài)條件下鈣質(zhì)沉積層中Ca/Mg比值的變化,結(jié)果表明在-800~-1000 mV (vs SCE) 電位下均能形成不同Ca/Mg比值的鈣質(zhì)沉積層。
圖10為施加不同保護(hù)電位下浸泡1056 h后破損處的表面微觀形貌圖,圖11為相應(yīng)地去除沉積層后的微觀形貌圖。開路電位下破損處的金屬基體經(jīng)1056 h浸泡,表面生成大量的腐蝕產(chǎn)物 (圖10a),去除腐蝕產(chǎn)物后可見明顯的腐蝕坑 (圖11a)。在此過程中,涂層阻抗值不斷下降,電荷轉(zhuǎn)移電阻最低,但涂層的剝離程度較小。當(dāng)不施加保護(hù)電位時(shí),隨著水溶液沿著涂層破損處滲透到涂層/金屬界面區(qū),溶解氧也隨水溶液一起擴(kuò)散到界面區(qū),導(dǎo)致作為陽極的金屬基材發(fā)生腐蝕溶解反應(yīng),陰極發(fā)生溶解氧的還原,發(fā)生如下反應(yīng):
Fe的溶解量與OH-的生產(chǎn)量成正相關(guān),受到腐蝕的金屬少,產(chǎn)生的OH-少,引起界面的堿化程度低,故而涂層未鼓泡,剝離面積小。
從圖10b可看出,-750 mV保護(hù)電位下,破損處有腐蝕產(chǎn)物,同時(shí)有稀疏的CaCO3沉積產(chǎn)生,無Mg(OH)2,沉淀層不完整,這是由于在靜態(tài)條件下CaCO3容易成核,而Mg(OH)2的形成需要在pH值達(dá)到9.3以上才能成核[17,18]。而在-750 mV電位下的界面堿性較弱,不能形成Mg(OH)2沉淀。去除表面的沉積層及腐蝕產(chǎn)物后,金屬沒有形成腐蝕坑。施加陰極保護(hù)電位時(shí),仍主要發(fā)生式 (2) 的陰極反應(yīng)。由外加陰極極化提供電子。當(dāng)外電流提供的電子不能完全滿足氧的去極化反應(yīng)時(shí),金屬則會發(fā)生腐蝕以提供電子,即發(fā)生反應(yīng)式 (1)。結(jié)合圖3b可看出,施加-750 mV保護(hù)電位時(shí)保護(hù)不足,此時(shí)的腐蝕速率小于自然浸泡下的金屬腐蝕速率,但陰極保護(hù)造成的界面堿化程度較高,造成涂層的剝離面積遠(yuǎn)遠(yuǎn)大于不施加陰極電位涂層的剝離面積。
從圖10c可看出,-850 mV保護(hù)電位下鈣質(zhì)沉積層較-750 mV的多,沉積層分布不均勻,與基體表面相接觸的沉積層成分主要為Mg(OH)2,比較疏松,呈絮狀物沉積在表面,有的區(qū)域表面沉積層相對較厚,顆粒較大,其主要成分為CaCO3。這可能是因?yàn)樵陉帢O極化條件下,帶正電的Mg(OH)2會被吸附到帶負(fù)電的金屬表面,而呈現(xiàn)顆粒狀的CaCO3的生長是在Mg(OH)2生長之后[17,19]。整個(gè)區(qū)域的沉淀層生長不均勻,膜層不完整,因此沉淀膜電阻較低。去除鈣質(zhì)沉積層之后,金屬基體表面未見明顯腐蝕坑。
從圖10d可看出,-950 mV保護(hù)電位下整個(gè)鈣質(zhì)沉積層則較為均勻完整,無明顯孔洞,鈣質(zhì)沉積層較為致密,膜層質(zhì)量較好,鈣質(zhì)沉積層成分主要為CaCO3和Mg(OH)2。結(jié)合圖8可知,此時(shí)有較高的膜層電阻,約在103 Ω·cm2波動。去除沉淀膜層之后,金屬基體未見腐蝕坑。說明-950 mV保護(hù)電位對破損處金屬體系具有較好的保護(hù)效果。
在外加-850或-950 mV保護(hù)電位時(shí),涂層剝離面積增大,仍主要發(fā)生式 (2) 的陰極反應(yīng)。由于陰極極化增大,離子及氧的遷移加快,氧被還原成OH-的速度加快,局部pH值上升,堿性環(huán)境增強(qiáng),使得涂層剝離加大。
從圖10e可看出,-1050 mV保護(hù)電位條件下的鈣質(zhì)沉積層較厚,為CaCO3和Mg(OH)2的混合鈣質(zhì)層,鈣質(zhì)沉積層表面隨機(jī)分布著絮狀的Mg(OH)2及顆粒狀的CaCO3,沉積層存在明顯孔洞。去除沉淀膜層后,破損處的金屬基體未見明顯腐蝕痕跡。-1050 mV保護(hù)電位時(shí),陰極除了發(fā)生式 (2) 的反應(yīng)外還發(fā)生式 (3) 的反應(yīng):
H2的產(chǎn)生破壞了沉積層的完整性,表現(xiàn)為多孔的膜層和相對較低的膜層電阻,雖然金屬基體未發(fā)生腐蝕,但嚴(yán)重的析氫導(dǎo)致OH-的增多,生成大量的OH-加劇了涂層的陰極剝離 (圖3)。
綜上結(jié)果,-850,-950和-1050 mV保護(hù)電位對金屬基體的保護(hù)效果較好,開路電位及-750 mV保護(hù)電位下的保護(hù)性較弱。-1050 mV保護(hù)電位下,陰極主要發(fā)生式 (2) 和 (3) 兩個(gè)界面反應(yīng),界面堿性較強(qiáng),嚴(yán)重破壞了涂層與金屬界面的附著力;從圖3及表4可以看出,涂層剝離面積大 (243 mm2)。而在-850和-950 mV電位下,主要發(fā)生式 (2) 的反應(yīng),界面堿化程度相對較低,陰極剝離程度相對較小,涂層剝離面積分別為169和183 mm2,在此保護(hù)電位范圍內(nèi),破損處的基體均未發(fā)生腐蝕。但對于涂層鼓泡處,由于涂層的電流屏蔽作用,-850 mV (vs SCE) 不能完全抑制涂層鼓泡處的金屬發(fā)生腐蝕,但腐蝕非常微弱。-950 mV保護(hù)電位下的沉淀膜層較為完整致密,阻抗及沉淀膜層電阻均較高。故而綜合考慮陰極保護(hù)電位的保護(hù)效果、界面堿化程度、陰極剝離程度等結(jié)果,認(rèn)為在本實(shí)驗(yàn)所研究的電位范圍內(nèi)涂層防護(hù)與陰極保護(hù)協(xié)同作用最佳的保護(hù)電位是-950 mV。
3 結(jié)論
(1) 在本實(shí)驗(yàn)選擇的保護(hù)電位中,隨著電位的負(fù)移,涂層剝離面積逐漸增大。
(2) 不同保護(hù)電位下破損處都生成了CaCO3或者CaCO3和Mg(OH)2的混合鈣質(zhì)沉積層。其中,-950 mV (vs SCE) 保護(hù)電位下生成的沉積層完整致密。
(3) 保護(hù)電位-750 mV不能完全為金屬基體提供保護(hù);在此保護(hù)電位下,破損處金屬仍會發(fā)生腐蝕。-850和-950 mV保護(hù)電位均能對破損處金屬提供良好的保護(hù),使金屬基體不發(fā)生腐蝕。但由于涂層的電流屏蔽作用,-850 mV不能完全抑制涂層鼓泡處的金屬腐蝕,但腐蝕程度很輕;-1050 mV保護(hù)電位下金屬基體未發(fā)生腐蝕,但破損處發(fā)生了嚴(yán)重的析氫現(xiàn)象,界面堿化程度較大,涂層剝離程度最大。
免責(zé)聲明:本網(wǎng)站所轉(zhuǎn)載的文字、圖片與視頻資料版權(quán)歸原創(chuàng)作者所有,如果涉及侵權(quán),請第一時(shí)間聯(lián)系本網(wǎng)刪除。
-
標(biāo)簽: 環(huán)氧涂層 ; 陰極保護(hù)電位 ; 破損 ; 陰極剝離
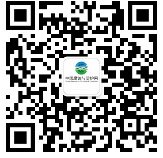
官方微信
《中國腐蝕與防護(hù)網(wǎng)電子期刊》征訂啟事
- 投稿聯(lián)系:編輯部
- 電話:010-62316606-806
- 郵箱:fsfhzy666@163.com
- 中國腐蝕與防護(hù)網(wǎng)官方QQ群:140808414