摘要
采用硫酸浸泡實驗,研究了Q345NS鋼焊接接頭耐硫酸腐蝕行為,并對焊接過程中合金元素擴散和耐硫酸腐蝕的行為與機理進行了分析。結果表明:焊接過程中,母材與焊材之間的元素濃度差促使母材中Cr、Cu、Sb等合金元素向焊縫內擴散富集,同時,焊接過程中的高溫會促進該進程,導致熱影響區靠近母材一側形成了合金元素貧瘠帶;焊縫處高溫導致Cu、Sb的二次分配,含量差異性進一步擴大;Cu、Sb在腐蝕層的大量富集,促進腐蝕層致密化,提升了材料耐硫酸腐蝕性能。
關鍵詞: 焊接接頭 ; 耐硫酸腐蝕 ; 元素擴散 ; 致密 ; Q345NS鋼
高爐煤氣管網長時間服役使得管道內腐蝕不斷加劇。隨著高爐煤氣干法除塵設施的推廣和應用,含塵量得到了有效控制,用水量大大降低,與此同時也帶來了更嚴重的腐蝕問題[1-3]。煤氣中氯化物、H2S、SO2等雜質在干法除塵中不能被去除[4],當上述雜質溶于凝結水中時,溶液呈酸性,腐蝕碳鋼材料的煤氣管道,嚴重時發生煤氣泄漏,危害很大[5]。
管道的腐蝕基本發生在管道的下半部分[6],主要表現為:管壁減薄、局部點蝕,因焊接工藝與現場施工各異,焊接接頭往往成為腐蝕誘發源頭。目前,國內外研究主要集中在管體母材的耐硫酸腐蝕行為,但對焊接接頭的耐硫酸腐蝕研究較少。因此,本文對工業焊管工藝下焊接接頭的耐硫酸腐蝕行為進行研究,為長壽管道的選材與焊接工藝優化提供數據支撐。
1 實驗方法
本實驗采用Q345NS耐硫酸露點腐蝕鋼板作為長壽管道母材,在某管廠進行埋弧螺旋制管。焊接工藝為自動埋弧焊,坡口為X型,焊絲為TH550-NQ-Ⅲ。以上材料化學成分如表1所示。焊接工藝參數見表2。
表1 試驗材料的化學成分
表2 焊接工藝參數
參照GB/T 7901對Q345NS鋼及其焊接接頭進行硫酸全浸實驗。實驗溶液為20%硫酸,溫度為20 ℃,浸泡時間為24 h。腐蝕試樣尺寸為50 mm×25 mm×5 mm,每種材料取3個平行樣。實驗前先用丙酮和無水乙醇進行超聲清洗,去除表面油污。試樣清洗完畢后置于干燥器中24 h,采用精度為0.1 mg電子天平稱量樣品的初始質量。
采用HH-6型數顯恒溫水浴鍋進行上述實驗,實驗后采用含有緩蝕劑 (六次甲基四胺) 的鹽酸溶液清洗表面腐蝕產物,酸洗后用清水沖凈,再依次用丙酮和無水乙醇浸泡,取出后立即用熱風吹干,放入真空干燥箱中保存24 h 后對試樣進行稱量。
腐蝕速率 (R) 按下式進行計算:
式中,R為腐蝕速率,mm/a;m和mt為實驗前后的試樣質量,g;s為試樣的總面積,cm2;t為實驗時間,h;ρ為材料的密度,kg/m3。
相對腐蝕率=RQ345NS/RQ235B×100%。
采用Sigma 500熱場發射掃描電鏡 (SEM) 對Q345NS焊接接頭腐蝕后各區域進行微觀形貌觀察,并利用其自帶的能譜儀 (EDS) 分析腐蝕產物的化學成分;除銹后,利用ATOS I 350XL三維光學測試儀對Q345NS焊接接頭進行3D形貌分析。
2 結果和分析
2.1 焊接接頭的微觀組織分析
Q345NS焊接接頭區域焊縫 (WM)、熱影響區 (HAZ) 與母材 (BM) 的顯微組織如圖l所示,由圖1可以看出,WM主要由鐵素體、貝氏體與少量珠光體組成。焊接過程中,WM區溫度較高,導致先共析鐵素體沿晶界析出,晶粒不規則長大 (圖1b) ;HAZ內為鐵素體、貝氏體與少量珠光體,組織較為均勻 (圖1c);BM為鐵素體與珠光體,晶粒細小且組織均勻 (圖1d)。
圖1 Q345NS鋼焊接接頭金相照片
2.2 焊接接頭與母材腐蝕速率分析
采用失重法測得各個試樣的腐蝕速率結果見圖2。從結果可看出,Q345NS鋼焊接接頭的腐蝕速率較母材上升了3.3%,這表明焊接對母材本身耐蝕性可能會產生不利影響。這是因為現場焊接水平各異,會導致咬邊、裂縫、氣孔以及焊縫表面不良等焊接缺陷的發生和較大的殘余應力,成為腐蝕敏感部位[7,8]。此外由于母材與焊材化學成分的不同,往往會引起電偶腐蝕[9]。因此焊接時,除選擇合適的焊接工藝外,還應選擇合金成分相似、耐蝕性大于或者與母材相近的焊材。
圖2 Q345NS鋼焊接接頭與母材腐蝕速率
2.3 焊接接頭腐蝕形貌分析
圖3為Q345NS焊接接頭與母材在20 ℃、20% H2SO4、24 h除銹前后表面腐蝕形貌圖片。由圖可以清晰看到鋼焊接接頭BM、HAZ與WM的對應區域,除銹前BM呈灰黑色,HAZ呈淡黃色,WM呈土黃色;除銹后,鋼焊接接頭與Q345NS母材相比,整體顏色偏淡;就鋼焊接接頭而言,BM與WM顏色較為相近,呈淡灰色,而HAZ呈灰色。焊接接頭各區域顏色的差異性表明其耐蝕性存在差異性。
圖3 Q345NS鋼焊接接頭與母材酸洗前后腐蝕形貌
BM、HAZ與WM腐蝕后的微觀形貌如圖4所示。由圖可知,BM腐蝕產物較為致密,表面形成大量孔洞,形成大量條帶多孔狀腐蝕結構;HAZ腐蝕產物結構與BM相似,但腐蝕產物進一步增大;WM與BM腐蝕形貌相似,但出現了局部條帶狀腐蝕坑,同時也最不均衡。
圖4 Q345NS鋼焊接接頭微觀腐蝕形貌
2.4 焊接接頭元素擴散行為分析
為了進一步分析鋼焊接接頭不同區域腐蝕差異性,對鋼焊接接頭腐蝕后的3D形貌進行了分析,結果如圖5所示。由圖可知,BM腐蝕深度跨度800~2400 μm,多集中于1600~2000 μm,平行焊縫方向腐蝕較為均勻,而垂直焊縫方向上,越靠近焊縫腐蝕深度越淺,腐蝕越輕;WM腐蝕差異性最大,不同位置腐蝕不均,腐蝕深度為400~1600 μm。HAZ腐蝕程度最輕,腐蝕深度為400~800 μm。BM與HAZ腐蝕差異性表明在焊接高溫作用下,WM、HAZ內合金元素發生了顯著的擴散作用。
圖5 Q345NS鋼焊接接頭3D腐蝕形貌
由于焊材與母材兩者的成分差異,在濃度梯度的作用下必然會發生母材中Cr、Cu、Sb向焊縫方向的擴散,此外焊接產生的高溫為擴散提供了充足的能量[10,11],而隨著溫度的逐漸降低,擴散行為減弱。這就導致兩個結果,一是BM內Cr、Cu、Sb向HAZ與WM擴散,導致HAZ與WM耐蝕合金元素含量升高,耐蝕性得到提升;二是WM在高溫與元素擴散作用下,產生耐蝕合金元素的二次分配,產生顯著的腐蝕差異性。
從母材至焊縫方向進行合金元素EDS點掃描,結果如圖6所示。由于焊材不含Sb,可見Sb在高溫與濃度差的雙重作用下,發生了顯著的擴散作用。Cu的擴散作用更為明顯,且含量波動較大,由于WM溫度可達1400 ℃,超過Cu熔點1083 ℃,較大的晶粒尺寸為Cu在晶界富集與擴散提供了有效通道,導致Cu發生顯著的二次分配。
圖6 Q345NS鋼焊接接頭不同區域元素含量變化圖
此外在熱影響區外靠近母材一側約600 μm的范圍出現了明顯的Cr、Cu、Sb元素貧瘠帶,成為元素擴散行為的又一佐證。
依據上述分析,建立了腐蝕不同階段焊接接頭元素擴散模型示意圖,如圖7所示。
圖7 Q345NS鋼焊接接頭元素擴散模型
2.5 焊接接頭腐蝕機理分析
焊接接頭在20%H2SO4溶液中腐蝕24 h后腐蝕產物形貌如圖8所示。可以看出,BM表面存在大量孔洞,腐蝕產物較為致密,形成多孔狀結構形貌。HAZ腐蝕產物結構與BM基本一致,但多孔結構尺寸更大。WM腐蝕程度介于BM與HAZ之間,腐蝕層結構呈破碎的形貌。
圖8 Q345NS鋼焊接接頭在20%H2SO4溶液中腐蝕24 h后腐蝕產物
表3為焊接接頭腐蝕產物的EDS分析,可以判斷腐蝕產物主要由Fe的硫酸鹽、Cu、Sb化合物及氧化物組成。HAZ中Cu是基體的81倍,Sb同樣高達64倍。Sb對含Cu化合物的生成起到了促進作用。
表3 Q345NS焊接接頭腐蝕產物的EDS分析
耐蝕鋼的耐酸腐蝕性能依賴于致密腐蝕層的形成,Sb是關鍵元素[12,13]。Sb加入不僅形成了Sb2O5[14]的保護性氧化層,還促進了Cu2S[15]膜的形成,進一步抑制了陽極氧化和陰極反應,使得鈍化膜的厚度增加,隔絕了硫酸溶液,腐蝕速度大大降低[16]。
3 結論
(1) 硫酸浸泡實驗表明,焊接對母材耐蝕性產生了不利影響,Q345NS鋼焊接接頭的腐蝕速率較母材上升了3.3%,因此焊接時,應選擇耐蝕性優于或者與母材相近的焊材。
(2) 焊接過程中,母材與焊材之間的元素濃度差導致了母材中Cr、Cu、Sb等合金元素向焊縫內擴散富集,同時,焊接過程中的高溫會促進該進程,導致熱影響區靠近母材一側形成了合金元素貧瘠帶;焊縫處高溫導致Cu、Sb的二次分配,腐蝕差異性進一步擴大。
(3) Cu、Sb在腐蝕層大量富集,促進腐蝕層致密化,提升了材料耐硫酸腐蝕性能。
參考文獻
1 Zhang Y, Sun W Q, Ye Y H. Overview on rapid corrosion of gas pipe with dry-type blast furnace gas dedusting technology [A]. Proceedings of the 7th National Conference on Energy and Thermal Engineering [C]. Chongqing, 2013: 321
1 張琰, 孫文強, 葉宇衡. 干法除塵高爐煤氣管道的腐蝕問題綜述 [A]. 第七屆全國能源與熱工學術年會論文集 [C]. 重慶, 2013: 321
2 Yang Z. Discussion on rapid corrosion of gas piping occurring in application of dry-type blast furnace gas dedusting technology [J]. World Iron Steel, 2010, 10(5): 43
2 楊鎮. 高爐煤氣干法除塵中煤氣管道快速腐蝕問題探討 [J]. 世界鋼鐵, 2010, 10(5): 43
3 Chen X D, Deng W L. Analysis of corrosion failure for gas piping conveying dry-dedusted gas and discussion about countermeasures [J]. Energy Metall. Ind., 2011, 30(6): 16
3 陳小東, 鄧萬里. 高爐干法除塵后煤氣管道腐蝕情況分析及對策 [J]. 冶金能源, 2011, 30(6): 16
4 Su F, Tang X G. Application of anti-acid corrosion technique in dry dusting system of blast furnace gas [J]. Metall. Power, 2010, (1): 20
4 蘇峰, 唐效國. 干法除塵高爐煤氣酸性腐蝕防控技術在萊鋼的應用及探索 [J]. 冶金動力, 2010, (1): 20
5 Guan X Y, Ma Z F, Xiong S L. Causes of corrosion of blast furnace gas pipe and anticorrosive measures [J]. Metall. Power, 2011, (6): 25
5 官習艷, 馬作仿, 熊樹林. 高爐煤氣管道的腐蝕及預防措施 [J]. 冶金動力, 2011, (6): 25
6 Chen C, Ding C J. Research on corrosion mechanism and anticorrosive measures of gas piping [J]. Ind. Heat., 2015, 44(1): 41
6 陳超, 丁翠嬌. 煤氣管道腐蝕機理與預防措施研究現狀 [J]. 工業加熱, 2015, 44(1): 41
7 Fan Z, Liu J Y, Li S L, et al. Microstructure and seawater corrosion to welding joint of X70 pipeline steel [J]. J. Southwest Petrol. Univ. (Sci. Technol. Ed.), 2009, 31(5): 171
7 范舟, 劉建儀, 李士倫等. X70管線鋼焊接接頭組織及其海水腐蝕規律 [J]. 西南石油大學學報 (自然科學版), 2009, 31(5): 171
8 Li Y D, Tang X, Li Y. Research progress of localized corrosion of welded joints [J]. Mater. Rev., 2017, 31(11): 158
8 李亞東, 唐曉, 李焰. 焊接接頭局部腐蝕的研究進展 [J]. 材料導報, 2017, 31(11): 158
9 Huang C, Huang F, Zhang Y, et al. Galvanic corrosion behavior for weld joint of high strength weathering steel [J]. J. Chin. Soc. Corros. Prot., 2019, 39: 527
9 黃宸, 黃峰, 張宇等. 高強耐候鋼焊接接頭電偶腐蝕行為研究 [J]. 中國腐蝕與防護學報, 2019, 39: 527
10 Wang C J, Hu X W, Peng H, et al. Effect of heating temperature on shear strength of TA2/Q235B compound plate [J]. Hot Work. Technol., 2020, 49(10): 67
10 王承劍, 胡學文, 彭歡等. 加熱溫度對TA2/Q235B復合板剪切強度的影響 [J]. 熱加工工藝, 2020, 49(10): 67
11 Ma T, Li H R, Gao J X, et al. Diffusion behavior of Cu in carbon steel and its influence on corrosion resistance of carbon steel [J]. Chin. J. Mater. Res., 2019, 33: 225
11 馬濤, 李慧蓉, 高建新等. 銅在碳鋼中擴散及其對碳鋼耐腐蝕性的影響 [J]. 材料研究學報, 2019, 33: 225
12 Qian Y H, Li Z G, Yang A N. Application and properties of low alloying sulfuric acid dew point corrosion—resistant steels [J]. Spec. Steel, 2005, 26(5): 30
12 錢余海, 李自剛, 楊阿娜. 低合金耐硫酸露點腐蝕鋼的性能和應用 [J]. 特殊鋼, 2005, 26(5): 30
13 Zhang W, Ma Y P, Liu Y G, et al. Sulfuric-acid dew point corrosion-resistant steel [J]. Anhui Metall., 2009, (3): 25
13 張武, 馬玉平, 劉永剛等. 耐硫酸露點腐蝕用鋼的研究與應用綜述 [J]. 安徽冶金, 2009, (3): 25
14 Le D P, Ji W S, Kim J G, et al. Effect of antimony on the corrosion behavior of low-alloy steel for flue gas desulfurization system [J]. Corros. Sci., 2008, 50: 1195
15 Ye X X, Zhou C, Zhang C. Corrosion performance of a new low alloy steel Cu-Sb-Mo for resisting dew-point corrosion induced by sulfuric acid and hydrochloric acid [J]. Corros. Sci. Prot. Technol., 2015, 27: 135
15 葉先祥, 周成, 張聰. 新型耐硫酸鹽酸露點腐蝕鋼的性能研究 [J]. 腐蝕科學與防護技術, 2015, 27: 135
16 Zhang C, Zhou C, Ye X X. The corrosion behavior of a new acid resistant steel in a concentrated sulphuric acid solution containing HCl [J]. Corros. Prot., 2015, 36: 599
16 張聰, 周成, 葉先祥. 新型耐酸鋼在硫酸鹽酸混合溶液中的腐蝕行為 [J]. 腐蝕與防護, 2015, 36: 599
免責聲明:本網站所轉載的文字、圖片與視頻資料版權歸原創作者所有,如果涉及侵權,請第一時間聯系本網刪除。
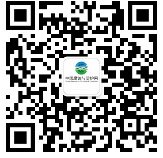
官方微信
《中國腐蝕與防護網電子期刊》征訂啟事
- 投稿聯系:編輯部
- 電話:010-62316606-806
- 郵箱:fsfhzy666@163.com
- 中國腐蝕與防護網官方QQ群:140808414