加氫裂化裝置存在的主要腐蝕類型主要有:氫損傷(包括高溫氫腐蝕、氫脆、氫致剝離)、高溫H2+H2S腐蝕、連多硫酸腐蝕、 Cr-Mo鋼的回火脆性、高溫S腐蝕、低溫部位的H2S+H2O腐蝕、H2S+NH3 +H2O腐蝕。
1.氫損傷
【定義】由于氫原子擴散進入金屬本體或與金屬反應引起金屬材料性能的破壞稱為氫損傷。
【部位】氫損傷發生的主要部位在:高溫、高壓氫氣環境下的反應系統設備和管線。
【分類】氫損傷主要可以分為:氫脆、高溫氫腐蝕和氫致剝離。
(1)氫脆
【定義】鋼在臨氫條件下使用,氫以原子狀態擴散浸入晶格內、又以分子狀態聚集于晶界或非金屬夾渣物周圍。
【特征】物理過程,可逆的,稱為一次脆化現象。材料的抗拉強度或硬度沒有特別大的變化,但是在常溫條件下材料的缺口強度或韌性降低,有時還產生裂紋。受到氫脆的材料經過脫氫處理后,如果沒有產生裂紋,其延性和韌性都能得到恢復。
(2)高溫氫腐蝕
【定義】氫在高溫(T>220℃)高壓下與合金中的夾雜物(碳合物F3C或固溶碳C)或合金添加物(如Si)發生化學反應,生成高壓氣體。
從而導致鋼材產生脫碳和結晶界裂紋。受到高溫氫腐蝕的材料的抗拉強度和延性、韌性顯著降低。
【特征】高溫氫腐蝕與氫脆性質完全不同,它是化學反應過程,具有不可逆性,稱為永久脆化現象。高溫氫腐蝕主要有2種形式:一是表面脫碳;一是內部脫碳。
鋼材與氫接觸后可產生表面脫碳。表面脫碳不會產生裂紋,但材料的強度和硬度稍有下降,而延伸率增加。發生的主要反應有:Fe3C+2H2→CH4+3Fe。
這一反應一般從鋼的表面開始,逐漸向內部推進,生成的甲烷氣體不易逸出,他們聚集在晶界或雜質周圍,形成的局部壓力可高達幾千大氣壓以上,因此,不僅鋼的表面和里層脫碳脆化,而且還發展為嚴重的鼓泡開裂。
鋼中的固溶的碳也會與鋼中溶解的氫反應:C+4H→CH4;Si+4H→SiH4。
高溫氫腐蝕的特點是要經過一個潛伏期,根據材料和環境條件的不同,潛伏期短可幾個小時,長則數年。
鋼材受到高溫氫腐蝕后,表面的尺寸變化很小,主要是降低材料屈服強度和沖擊韌性,從而引起材料開裂。鋼材發生氫腐蝕的溫度和壓力有一個組合條件,及潛伏值,超過這個極限值,就會發生氫腐蝕。
【影響高溫氫腐蝕的主要因素】
■溫度、壓力和暴露時間的影響。溫度越高或者壓力越大高溫腐蝕的起始時間就越早。
■合金元素和雜質元素的影響。
■熱處理的影響。鋼的抗氫腐蝕的性能與鋼的顯微組織也有密切關系。
■應力的影響。應力值越大,腐蝕越強。
(3)氫致剝離
【定義】氫在高溫高壓下擴散進入鋼中,當設備檢修或冷卻過程中,溫度降低至150℃以下時,由于氫氣來不及向外釋放,鋼中吸藏了部分氫氣,在一定條件下就會產生堆焊層與母材的開裂現象。
(4)氫損傷的防護措施
■嚴格控制降溫、降壓速率,不能過大。降溫速率:20~25℃/h,降壓速率:1.0~1.5MPa/h。(可以很好的防治氫脆、氫致開裂)。
■控制材料的雜質元素的含量,焊后熱處理。
■根據最新版本的納爾遜曲線選擇抗氫腐蝕材料。嚴禁設備超溫、超壓。
2.高溫H2+H2S腐蝕
【定義】高溫H2+H2S腐蝕是指金屬在高溫(204℃,也有說300~420℃)、H2和H2S環境下發生的腐蝕破壞現象。
【腐蝕部位】高溫H2+H2S腐蝕部位主要發生在混氫以后的反應系統設備上如:加氫反應器、反應流出物高壓換熱器、反應爐爐管、熱高分及相應的工藝管線。腐蝕形態為H2S對鋼的化學腐蝕,表現為均勻腐蝕、氫脆和氫腐蝕。
【腐蝕因素】在加氫過程中,氫也是造成設備腐蝕的一個因素。它不僅能直接腐蝕金屬,還對高溫H2S起一種促進作用。影響因素有:
■濃度:H2S濃度在1%(體積)以下時,隨著濃度的增加而增加,腐蝕速率急劇增加,當濃度超過1%(體積)時腐蝕速率基本不變。
■溫度:在315-480℃時,隨著溫度增加,腐蝕率相應增加,而且,溫度每增加50℃,腐蝕速率大約增加2倍。
■時間:腐蝕率隨著時間的增長而下降,一般裝置開工5000h內,腐蝕速率最高。在以后時間內腐蝕速率減小2-10倍。
■壓力:在高溫H2S+H2腐蝕中,壓力高低對腐蝕速率沒有影響,而在單純高溫氫氣中,壓力對腐蝕有很大影響。
【防護措施】高溫H2S+H2引起的是均勻腐蝕。要嚴格按照Couper曲線估算材料的腐蝕速率,合理設計選材。
一般在250℃以下時,可以選用碳鋼;溫度超過250℃使用鉻鉬鋼(僅有H2存在)及或奧氏體不銹鋼(抗H2+H2S腐蝕)。
3、連多硫酸腐蝕
【腐蝕部位】奧氏體不銹鋼設備(如反應器堆焊層、爐管、奧氏體不銹鋼空冷、換熱器等)。
【防護措施】選用超低碳或穩定型的奧氏體不銹鋼;制造上要盡量消除或減輕由于冷加工和焊接引起的殘余應力,并注意加工成不形成應力集中或應力集中盡可能小的結構;氮氣保護,保持設備溫度在150℃左右,中和清洗。
4、Cr-Mo鋼的回火脆性
【定義】在325~575℃溫度范圍內長時間保持或從此溫度范圍緩慢地冷卻時,其材料的破壞韌性就引起劣化的現象。
這是由于鋼中的微量雜質元素和合金元素向原奧氏體晶界偏析,使晶界凝集力下降所至。材料一旦發生回火脆化,其轉變溫度就向高溫側遷移。
【腐蝕部位】使用Cr-Mo鋼的部位,主要發生在2.25Cr-1Mo和3Cr-1Mo材質設備上(如反應器、高壓換熱器、熱高分等)。
【主要防護措施】
■嚴格控制回火脆性系數(J-系數和(X)系數)的大小(J=(Si+Mn)×(P+Sn)×104;(X)=(10P+5Sb+4Sn+As)×10-2)。
■通過階梯冷卻試驗控制材料的回火脆化度vTr54 +3△vTr54 ≤ 0℃。
■采用熱態型的開停工方案(先升溫后升壓,先降壓后降溫)。
5、高溫硫腐蝕
【定義】在加氫裂化裝置中高溫S腐蝕是由原料中所含的硫化物(主要是H2S和單質S)在240~260℃以上時與金屬發生反應而使金屬性能產生破壞的現象。
【腐蝕部位】所引起的是均勻腐蝕,主要出現在混氫前的原料油系統和分餾系統的高溫部位(塔底、重沸爐的進出口管線的彎頭、三通、大小頭處)。設計中可按照McConomy曲線估算材料的腐蝕速率。
【腐蝕機理】
H2S+Fe→FeS(<340℃);
H2S→S+H2(<340℃);
Fe+S→FeS。
由以上反應方程式可知,腐蝕本應生成致密的FeS保護膜,可以防止腐蝕反應進行,但當介質流速大時,腐蝕產物FeS難以附著在金屬表面,從而達不到應用的保護效果,金屬始終處在裸露狀態下,結果腐蝕會不斷向縱深發展。
【防腐蝕對策】
■為了減緩脫丁烷塔和第一分餾塔系統腐蝕,采用脫戊烷塔流程或增大脫丁烷塔的設計負荷。
■上循環氫脫硫塔系統。
■相應材質采用Cr-Mo鋼。
6、低溫部位的H2S+H2O腐蝕
【定義】H2S+H2O腐蝕環境,亦即通常所說的濕硫化氫腐蝕,一般系指液相水和硫化氫共存(或含水物流在露點以下)時硫化氫所引起的腐蝕。濕硫化氫腐蝕形態主要表現為設備均勻減薄和應力腐蝕。
【腐蝕部位】低溫濕硫化氫腐蝕主要存在于循環氫脫硫塔、高分界位后路、主汽提塔、脫丁烷塔、液態烴回流罐、冷卻器等部位及相應管線。
【腐蝕機理】在低溫下,H2S腐蝕僅發生在有水和強酸或和氧同時存在的環境。H2S為弱酸,在水中發生電離:
H2S=H++HS-
HS-=H++S-
因此,電化學腐蝕的陽極反應為:
Fe=Fe2++2e
Fe2++S-=FeS或Fe2++HS-=FeS+H++e
而陰極反應為:H++2e=2H=H2
【影響濕硫化氫應力腐蝕開裂的因素】
■硫化氫濃度。H2S濃度大于50PPm考慮濕硫化氫應力腐蝕。
■鋼材的強度等級。強度越高,越容易發生濕硫化氫應力腐蝕開裂。
■鋼材的化學成分。S、P元素在鋼材生成和焊接過程中容易產生偏析,導致馬氏體和貝氏體組織增加,鋼材的顯微組織硬度增高,對降低濕硫化氫應力開裂產生不利影響。
■硬度值。焊縫和熱影響區的硬度值越高,對硫化氫應力腐蝕越敏感。
【防腐對策】
■綜合經濟和防腐等方面考慮,選用工藝防腐措施較好。如向低溫部位注緩飾劑(如主汽體塔頂、脫丁烷塔頂)。
■焊后熱處理,焊縫和熱影響區的硬度HB<200。
■降低材料中的S、P含量。如使用Q345R(R-HIC鋼)。
7、H2S+NH3 +H2O腐蝕
【定義】H2S+NH3 +H2O腐蝕是指在H2S、NH3、H2O共同作用下,造成的腐蝕現象。腐蝕主要表現為垢下腐蝕,NH4HS的垢下腐蝕。主要發生在高壓空冷器及下游脫水線。
【腐蝕機理】在H2S環境下,H2S與金屬反應,形成FeS保護膜。但工藝介質流速過高,則會因沖刷造成保護膜損壞。
反應式為:Fe+H2S→FeS+H2。在H2S和NH3濃度高,即含高濃度NH4HS的濕環境下,按照如下反應式進行反應,FeS與NH4HS生成絡合物,造成保護膜損壞,并且腐蝕加劇。
反應式為:FeS+6NH4HS→[Fe(NH3)6]2+。通過這些反應,在局部高流速部位和湍流部位產生嚴重的壁厚減薄。
產生局部流速過大的原因:由污染物和堵塞引發的偏流和湍流;由設計不當引起的偏流。在流速極低的部位和滯留部位也可能產生腐蝕。
其原因是當流速小的時候,在低流速部位和滯留部位產生堆積物,在這些堆積物下面產生高濃度NH4HS,引發局部腐蝕。
另外,在硫化鐵堆積時,同鐵產生原電池,硫化鐵變成陰極,有促進腐蝕的可能性。
根據美國防腐蝕工程師聯合會(NACE)標準,防腐措施依照空冷器管子物流腐蝕系數Kp值。
Kp= (H2S)mol%×(NH3)mol%
其中:H2S——物流中H2S的濃度 mol%;
NH3——物流中NH3的濃度 mol%;
當Kp<0.07時,材料可以選用碳鋼。
當Kp=0.1%~0.5%材料為碳鋼,流速適應范圍為4.6~6.09m/s。
當Kp>0.5%當流速當流速低于1.5~3.05m/s或流速高于7.62m/s時,選用3RE60 Monel或Incoloy800高合金材料。反應流出物空冷器要求襯316L保護套管。
【防腐對策】
■嚴格控制Kp值。
■管子入口襯316L不銹鋼保護套管。
■在高壓空冷前注水,注入水溶性緩蝕劑,防止胺鹽結晶。
■采用對稱平衡型結構,以利于流體分配均勻。
■操作上避免偏流。
選材要點
1、高硫低酸值原油在高溫下主要是高溫硫腐蝕,選用設備材料以含適量的Cr為主;高硫高酸值原油在高溫下主要是環烷酸的腐蝕,選用設備材料以含Mo=2%~3%(wt)的TP316不銹鋼最為有效。
2、設計腐蝕裕量最大不應超過6mm,否則應更換材料。
3、高溫臨氫環境下操作的設備根據操作的氫分壓和操作溫度參照納爾遜曲線選材。
4、高溫H2+H2S腐蝕根據Couper曲線選材。
5、高溫硫腐蝕根據McConomy曲線選材。
6、根據預選材料的腐蝕速率,按下列原則確定主材材料:
(1)所選材料的腐蝕速率不超過0.25mm/a;
(2)當選用鉻鉬鋼時,應考慮其可能發生的回火脆性問題;
(3)當選用奧氏體不銹鋼時,應選用穩定型奧氏體不銹鋼。
7、濕酸性腐蝕環境下的選材
(1)對于以濕硫化氫為主要腐蝕介質的環境,主材選用應符合下列要求:
①對于有少量凝結水出現的氣相介質環境,當氣相硫化氫分壓小于0.00035MPa時,主材應選用碳鋼;當氣相硫化氫分壓大于或等于0.00035MPa時,主材宜選用碳鋼,并滿足抗硫化物應力腐蝕開裂(SSCC)要求。
②對于液相或氣液混相的介質環境,主材的選用應符合下列要求:
a)當介質中的硫化氫含量小于50μg/g時, 主材可選用碳鋼;
b)當介質中的硫化氫含量為50~10000μg/g時,如果液相的pH值為5.5~7.5,主材可選用碳鋼;如果液相的pH值小于5.5或大于7.5,無縫鋼管宜選用碳鋼,并滿足抗SSCC要求,而鋼板焊制鋼管宜選用“抗氫誘導開裂(HIC)碳鋼”;
c)當介質中的硫化氫含量大于10000μg/g時,無論介質的液相呈中性、酸性或堿性,鋼板焊制鋼管均宜選用“HIC碳鋼”,而無縫鋼管可選用碳鋼,并滿足抗SSCC要求;
d)當所選材料的均勻腐蝕速率大于0.25mm/a時,應考慮提高材料,或采取其它措施。
③當介質中同時有氨或胺存在時,應考慮氨或胺對材料均勻腐蝕速率的影響以及胺的應力腐蝕裂紋的影響。
(2)當濕硫化氫腐蝕環境中同時含有乙醇胺并以其作為脫硫劑時,主材選用應符合下列要求:
①對于有少量凝結水出現的氣相介質環境,主材宜選用碳鋼,并滿足抗SSCC要求;
②對于液相介質環境,主材的選用視下列情況分別處理:
a)當介質溫度小于等于110℃時,主材宜選用碳鋼,并滿足抗SSCC和抗堿應力腐蝕開裂(ASCC)要求;
b)當介質溫度大于110℃時,主材宜選用超低碳奧氏體不銹鋼。
8、高溫硫、高溫硫化物腐蝕環境下的選材
(1)對于介質溫度大于或等于240℃且含活性硫化物腐蝕介質的管道,均應考慮高溫硫化物腐蝕對材料選用的影響。一般情況下,應以介質中的總硫含量和介質操作溫度為參數,按McConomy估算預選材料的腐蝕速率,然后按下列原則確定主材材料:
①結合溫度分布情況,適當將整個裝置的高溫油品管道劃分為幾個溫度段,在每個溫度段內選擇合適的材料;
②應優先選用碳鋼、1Cr5Mo,必要時可選用1Cr9Mo材料;
③對大口徑管道,宜選用碳鋼+不銹鋼復合板卷制鋼管。
(2)當介質的流速大于或等于30m/s時,應考慮采用耐沖刷腐蝕的材料。
9、溫氫氣和硫化氫共同存在腐蝕環境下的選材
(1)質溫度大于或等于200℃的含有氫氣與硫化氫的管道,均應考慮高溫氫損傷對材料選用的影響,一般情況下,應以介質溫度加一定裕量和氫分壓為參數,按納爾遜曲線進行預選材。
(2)在上面的基礎上,對于介質溫度大于或等于200℃的氫氣與硫化氫共存介質管道,還應考慮高溫硫化氫和氫氣共同腐蝕對材料選用的影響,一般情況下,應以介質中硫化氫的含量和介質溫度為參數,并結合烴類物料的輕重類別,查Couper曲線估算預選材料的腐蝕速率。
免責聲明:本網站所轉載的文字、圖片與視頻資料版權歸原創作者所有,如果涉及侵權,請第一時間聯系本網刪除。
相關文章
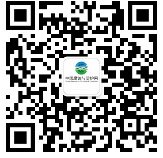
官方微信
《中國腐蝕與防護網電子期刊》征訂啟事
- 投稿聯系:編輯部
- 電話:010-62316606-806
- 郵箱:fsfhzy666@163.com
- 中國腐蝕與防護網官方QQ群:140808414
點擊排行
PPT新聞
“海洋金屬”——鈦合金在艦船的
點擊數:7844
腐蝕與“海上絲綢之路”
點擊數:6261