B2-NiAl金屬間化合物由于其高熔點和低密度,以及優良的抗氧化性能和導熱性能,在航空渦輪機葉片、大型高溫不銹鋼鍋爐防護等高溫或極端溫度環境中應用廣泛[1],尤其在受到超高溫載荷作用下的航空發動機關鍵零部件中,NiAl金屬間化合物作為熱障涂層(TBCs)的一種新型粘接層,具有很好的抗氧化性能和抗脫落性,從而可以提高航空發動機的服役壽命[2-3]。
近年來,對NiAl涂層的研究集中于熱障涂層的抗氧化性能和抗腐蝕性能。YANG等[4]通過真空離子濺射方法獲得了柱狀晶體的 β-NiAl涂層,研究了1000 ℃下涂層的氧化行為,發現柱狀微晶對涂層的初始氧化有較大的影響,但對最終的氧化層厚度沒有明顯影響。ZHANG等[5]采用電泳沉積法和熱壓成形方法在 γ-TiAl基體上制備了 B2-NiAl涂層,發現在900 ℃下,NiAl涂層表面會形成少量的α-Al2O3氧化膜,從而達到抗氧化的目的。SAEEDI等[6]通過機械研磨和高速燃料系統制備了Ni-5%Al涂層,研究了該涂層與常規 NiAl涂層的顯微硬度和氧化速率,發現新涂層的氧化速率常數低于常規涂層,但該涂層具有較高的硬度。王楠[7]對采用超音速電弧噴涂技術制備的NiAl涂層進行了耐NaCl溶液腐蝕性能研究,發現該涂層具有Ni的耐腐蝕性能以及Al的鈍化性能,涂層的自封閉性是涂層抗腐蝕能力增強的主要原因。BAI等[8]采用高速氧燃料熱噴涂技術在不銹鋼生物燃料鍋爐上制備了防止氯腐蝕的 β-NiAl涂層,研究了HCl合成氣體對涂層的腐蝕過程及腐蝕機理,并發現在 700 ℃下,樣品邊緣處的涂層與基體由于氧化,形成了氧化鋁薄膜。雖然以上對 NiAl涂層的抗氧化性能和抗腐蝕性能進行了較為系統的研究,并且從工藝或者制備的角度去分析了涂層的抗氧化性能,但并未對涂層在高溫下的抗氧化機理進行分析,也沒有提出提升涂層性能的新方法。
NiAl涂層雖然具有良好的抗氧化性能,但為了獲得性能更良好的涂層,通常采用元素摻雜的方法來改善其性能。李鐵藩等[9]采用復合電沉積和擴散滲鋁技術得到了含有少量Y2O3的β-NiAl新型涂層,發現在1100 ℃下涂層的氧化速率會降低,對氧化膜的抗剝落能力有較大的提升,且 Y2O3能夠在氧化過程中有效地抑制涂層的退化。李惠[10]利用等離子噴涂技術制備了 Cr3C2-NiCr/NiAl復合涂層材料,通過摩擦磨損試驗機在不同溫度下對復合涂層進行摩擦磨損試驗。發現在室溫下磨損機制以磨粒磨損為主,磨損比較小;在高溫下,磨損以氧化磨損和粘著磨損為主。TAWANCY[11]研究了 Hf、Ti和 α-Cr摻雜 β-NiAl涂層的抗氧化性能以及涂層對基體粘附性的影響,發現Hf對Al2O3的形成有一定的抑制作用;Ti和α-Cr對涂層表面影響較大,從而降低了涂層的抗氧化性能。以上文獻對 NiAl涂層的抗氧化性能和抗腐蝕性能進行了較為系統的研究,并且從元素摻雜的角度對NiAl涂層的抗氧化性能進行改善和優化,但由于長度尺度和試驗條件的限制,難以從機理上去解釋NiAl涂層的失效機理及其他性能,不能達到對NiAl涂層改進的目的。因此,需要尋找一種方法或者途徑對 NiAl涂層在高溫下的失效過程及失效機理進行研究。
對于NiAl涂層材料來說,一般的涂層厚度為微米或者納米級別,且涂層通常在高溫、強沖擊作用下使用,僅僅采用實驗方法來研究涂層的失效過程和微觀變形機理有一定難度,分子動力學方法則可以彌補該不足[12]。沙憲偉等[13-14]采用分子動力學方法研究了不同溫度下B2-NiAl的表面能,及其形核和生長的微觀機理,發現加熱是誘發馬氏體相變的主要原因,B2-NiAl在高溫下會轉化為Fct結構L10相的馬氏體。GUO等[15]采用分子動力學方法模擬了 B2-NiAl裂紋尖端的低溫變形機制,當存在足夠高的應力集中時,在[100]晶向的裂紋尖端附近形成馬氏體層狀結構,但是在[110]裂紋方向的裂紋尖端沒有發生馬氏體相變,發生相變的原因是應力使原子層的相對位移發生了變化。EVTEEV等[16]采用分子動力學方法模擬了NiAl 合金的熔化過程,發現初始 NiAl合金結構為B2-NiAl,體系的形成熱為-0.08 eV/atom,隨著溫度的升高,在溫度為1500 K時熔化,結構轉化為非晶態,對應的形成熱為-0.34 eV/atom。BARAS等[17]利用分子動力學模擬了不同晶向NiAl納米晶體的生長過程和機理,發現在[101]取向,NiAl以晶粒傾斜的形式結晶,NiAl在生長過程中會伴隨著位錯形核現象。CUI等[18]構建了 Pt摻雜 B2-NiAl涂層的原子間勢函數,并采用分子動力學方法研究了Pt在B2-NiAl的占位以及Pt濃度對NiAl涂層性能的影響,發現Pt在B2-NiAl中更容易占據Ni的位置,當Pt原子數分數達到20%時,形成了B2-NiAl和α-Al2Pt雙相結構,這種結構對B2-NiAl有一定的促進作用。
以上這些研究主要集中于采用分子動力學方法模擬B2-NiAl涂層的形成和相變過程,對B2-NiAl涂層的形成和相變機理進行了探索,但 NiAl作為高溫涂層材料,服役環境溫度通常在 600 ℃以上,并且B2-NiAl涂層在高溫下因應力集中而萌發微裂紋和微孔洞[19-20],微裂紋的形成會對涂層的力學性能造成極大的影響,甚至會造成涂層的斷裂失效。因此,本文采用分子動力學方法研究 B2-NiAl涂層在溫度為600 ℃下的拉伸失效過程及其微觀機理,通過預設裂紋和孔洞研究微缺陷對涂層力學性能及其失效過程和失效機理的影響,以期為NiAl涂層的制備和防護提供一定的理論參考。
1 分子動力學模型及方法
1.1 分子動力學模型
為了研究微缺陷對單晶B2-NiAl涂層在高溫和高速拉伸載荷下的變形過程及其塑性變形機理的影響,完美B2-NiAl涂層(Sample 1)、含中心對稱微裂紋涂層(Sample 2)、含有中心微裂紋與單微孔洞涂層(Sample 3)和含有中心微裂紋與雙微孔洞涂層(Sample 4)的分子動力學模型如圖1所示。B2-NiAl涂層的單胞結構為類體心立方結構(BCC)[21],晶格參數為a=b=c=0.288 nm,α、β和γ為90°。圖1a為不含缺陷的單晶B2-NiAl模型,x-y平面為表面平面,其長度為34.56 nm×23.04 nm,板厚度為1.73 nm,超過勢函數截斷半徑的兩倍,x、y、z分別為 B2-NiAl涂層的[100]、[010]和[001]晶向。B2-NiAl涂層通常在高溫下使用,由于基體受到高溫作用使涂層出現微裂紋[22],為了研究微裂紋對涂層變形及機理的影響,采用關閉原子間勢函數的方法,在模型中心預設了一條長度為 3.456 nm的裂紋,裂紋長度為總寬度的1/10[23],如圖1b所示。當存在微裂紋時,利用在裂紋邊界預制孔洞的方法可以抑制裂紋的擴展[24-25],由于原子之間的相互作用,孔洞直徑應大于分子模擬勢函數的截斷半徑,故在裂紋邊緣設置半徑為0.432 nm的孔洞[24],其單孔洞和雙孔洞如圖1c和圖1d所示。所有模型在z向邊界設置3倍晶格常數厚度的邊界層以用于加載,邊界層原子設置為剛性原子。
圖1 含有微缺陷單晶B2-NiAl涂層的分子動力學模型
Fig.1 MD models of single crystal B2-NiAl coating with micro defects, x, y and z are respectively [100],[010]and [001]crystallographic orientation: (a) perfect model of B2-NiAl coating; (b) model with center crack;(c) model with center crack and void; (d) model with center crack and double voids
1.2 分子動力學方法
為了描述單晶B2-NiAl涂層在高溫高沖擊下體系內原子間的相互作用,采用PUN等[26]發展的嵌入原子勢(EAM),其基本形式為:
式中:U為體系總能量,主要分為嵌入能(式(1)中 Fi(ρi))和對勢項兩部分;ρi為除第 i個原子以外的所有其他原子的核外電子在第i個原子處產生的電子云密度之和;rij為第i個原子與第j個原子之間的距離;ρi(rij)為擬合的電子密度的分布函數。該勢函數已經成功地應用在高溫下B2-NiAl涂層力學性能和抗氧化性能的計算模擬中,取得了比較準確的計算結果[27]。考慮到原子之間的力為相互作用力,原子的平均應力通過 Virial理論[28]對所有原子勢能的體積平均得到,其表達式為:
式中:i和j為體系內的原子;N為原子數目;V為體系的體積;mi與vi分別為第i個原子的質量和速度;σ12為體系的平均應力,1和2分別表示應力張量的方向,該應力主要由兩部分構成,分別是速度項和位移項,速度項表示動能對原子的貢獻項,位移項表示力對原子的貢獻項,它表示除了原子i以外的原子對原子i產生的作用力。
描述原子坐標軌跡的牛頓運動方程采用 Verletvelocity方法[29]進行求解,整個模擬分為兩部分進行,首先在NVE系綜下對模型充分弛豫,使結構達到能量最小構型。在弛豫完成后,整個模擬過程在 NVT系綜下進行,采用Nose/Hoover熱浴[30]使體系內溫度保持在900 K高溫下,將上下邊界設定為加載邊界,每100 步輸出原子坐標、溫度、勢能和動能等信息。通過鍵對分析技術(CAN)和中心對稱參數法(CSP)表征原子內部結構的變化[31],通過計算加載過程中的徑向分布函數(RDF)[32]來表征B2-NiAl涂層的成分變化。模擬通過LAMMPS開源軟件編程進行計算,采用OVITO后處理軟件進行可視化分析[33]。
2 結果與分析
2.1 微缺陷對單晶B2-NiAl涂層力學性能的影響
高溫條件下B2-NiAl涂層的力學性能與拉伸過程中的應力-應變曲線相關,為了研究微缺陷對B2-NiAl涂層力學性能的影響,算得不同樣本(Sample 1—4)的應力-應變曲線、屈服應力、應變以及彈性模量等力學參數,如圖2所示。從應力-應變曲線(圖2a)可以看出,在初始時刻,B2-NiAl涂層模型的初始應力不為零。這是由于NiAl涂層在溫度為900 K的高溫下,原子具有熱振動性,使加載前的涂層內部具有能量,從而出現應力不為零的現象。這與郭宇等[34]研究FCC銅金屬在高溫下的力學性能的結果相符合。隨著加載的進行,B2-NiAl涂層的失效過程可以分為彈性階段和塑性階段(屈服階段和斷裂失效階段)。在彈性階段,四種樣本模型的應力應變曲線都呈現出振蕩性,這也是由于高溫導致B2-NiAl涂層中原子發生振動,從而表現出應力的不穩定性。在塑性階段,材料隨著加載的進行,發生屈服,材料屈服后應力大幅下降至最低點,最終在0附近波動,屈服后,所有模型都出現了“應變強化”現象。模型1和2屈服持續時間較短,應力達到屈服點后便直接快速下降;引入孔洞后,模型3和4的屈服過程時間增加,從而提升了材料的塑性能力。
圖2 不同樣本模型下的力學性能
Fig.2 Mechanical properties of different models:(a) stress-strain curve; (b) parameters of yield stress and strain, and elasticity modulus
為了進一步分析微缺陷對B2-NiAl涂層在高溫高速拉伸載荷作用下力學參數的影響,4種模型的屈服應力、應變及彈性模量等力學參數如圖2b所示。隨著缺陷的增加,材料的屈服應力明顯下降,彈性模量也有所降低,從而使材料的強度降低,但屈服應變逐漸減小。在外加載荷的作用下,含有裂紋和雙孔洞的樣本由于局部應力集中,會更快達到屈服點,完美樣本由于不存在應力集中,發生屈服的時間會向后推遲。
2.2 微缺陷對單晶B2-NiAl涂層變形過程及塑性變形機理的影響
為了研究B2-NiAl涂層在高溫高速拉伸載荷作用下的變形失效過程和塑性變形機理,采用CNA分析技術對涂層在拉伸過程中的原子構型進行著色表征。無缺陷B2-NiAl涂層模型在拉伸載荷作用下對應不同應變(ε=0.044、0.087、0.103、0.109、0.123、0.125)時的微觀原子構型如圖3所示。對材料進行加載,當應變ε=0.044時,在模型邊界處發生頸縮現象,模型內部出現大量的點缺陷,如圖3a所示。這是由于應力隨著加載的進行而增加,導致涂層出現“頸縮”和大量的點缺陷,但此時涂層內部還未出現位錯發射,對應的應力-應變曲線處于彈性階段。繼續加載,應力繼續隨著應變的增加而增大,當應變ε=0.087時,模型表面的點缺陷數量快速增加,并開始產生位錯形核和發射現象,在邊界和體系內部出現少量的面心立方結構,這些結構分布比較均勻,如圖3b所示。這是由于在高溫和高速載荷作用下會使體系內位錯形核和發射,從而使原子重新堆垛成面心立方結構。隨著外加載荷的繼續增加,當應變ε=0.103時,在邊界局部區域出現位錯塞積,導致應力集中,從而使邊界處形成沿[100]方向的裂口和孔洞,如圖3c所示。繼續加載,當應變ε=0.109時,邊界處的初始裂紋繼續擴展,孔洞也繼續長大,裂紋和孔洞貫穿,形成更長的裂紋。隨著加載的繼續進行,在裂紋前端不斷地有新的孔洞形成,孔洞和裂紋繼續長大并貫穿,但此時裂紋沿著[111]方向不斷擴展延伸,當模型出現斷裂時,會釋放大量的應力,從而導致斷口以上的結構恢復成BCC結構,如圖3e和圖3f所示。
圖3 模型1(無缺陷B2-NiAl)在單軸拉伸載荷作用下變形及失效過程的微觀原子構型圖
Fig.3 Micro atomic configurations of deformation and failure process of model 1 (perfect B2-NiAl coating) under uniaxial tensile load
需要注意的是,裂尖附近的位錯塞積比較密集,從而使裂紋尖端出現應力集中并出現大面積的 FCC相變區,使得模型體系的內能量得以釋放。同時,在模型的另一邊界處,由于應力集中,也開始出現裂紋,最終與從右邊擴展的裂紋相遇而貫通,從而導致材料的斷裂失效。因此,模型1的失效過程和機理可以歸結為:涂層由于載荷作用,體系內發生大量的位錯,但由于邊界處為固定約束,在邊界處因位錯塞積而導致應力集中,從而形成微裂紋,但裂紋并不會一直沿著微裂紋方向擴展,而是在裂紋尖端附近形成應力集中,從而形成微孔洞。微孔洞和微裂紋隨著應力的增加而長大和擴展,最后貫通形成新裂紋,但此時裂紋的擴展方向主要沿著[111]滑移方向,當應變達到0.123時,主裂紋附近區域發生大面積的相變現象,從而使主裂紋附近的應力下降。而左側邊界附近由于位錯塞積導致應力集中,形成新的微裂紋,微裂紋繼續擴展并與主裂紋貫穿,導致材料發生斷裂失效。對于完美結構的B2-NiAl涂層,在拉伸載荷作用下,主要受到位錯和相變等因素的影響。
為了研究微裂紋對B2-NiAl涂層在高溫高速拉伸載荷作用下變形失效過程和塑性變形機理的影響,獲得中心微裂紋缺陷的B2-NiAl涂層模型在不同應變下(ε=0.008、0.044、0.052、0.061、0.078、0.085)的裂紋擴展過程,如圖4所示。初始拉伸后,當應變ε=0.008時,由于應變較小,使得裂紋沒有擴展,但裂紋尖端附近出現無序原子,在完美晶體結構部分出現點缺陷,如圖4a所示。這是由于高溫導致原子運動加劇,裂紋尖端鍵合力較小,有序原子在此情況下更易轉變為無序原子。隨著應變的增加,中心裂紋在此時由于應力較小并未發生擴展,但是在拉伸方向([010])的加載使裂紋尖端發生鈍化,且在裂紋尖端處出現少量綠色的FCC結構原子,發生BCC轉變為FCC的相變現象,如圖4b所示。相比完美模型,模型2由于裂紋尖端處的應力集中,導致在裂紋尖端處提前出現相變現象,從而影響了應力-應變曲線。隨著拉伸過程的進行,如圖4c所示,裂紋尖端處發生位錯塞積,在裂紋尖端附近應力集中,此時裂紋長度未明顯改變,裂紋的鈍化現象更加明顯,但并未立即擴展。繼續加載,當裂尖處應力值達到裂紋擴展所需的應力值時,裂紋開始沿著<100>方向擴展,此時在裂尖附近可以看到明顯的位錯發射和塞積,位錯沿著<111>方向發射,材料展現出塑性,如圖4d所示。這是由于在樣本B2-NiAl的滑移面上,裂紋前端剪切帶內的相變區域變長變寬,從而導致裂尖附近產生大量塑性變形。繼續加載,裂紋沿著<100>方向快速擴展,斷裂后體系內的應力值也快速下降,如圖4e所示,但此時模型在左側并沒有完全斷裂,未斷裂的結構由于應力集中出現了孔洞。繼續加載到應變ε=0.087時,孔洞逐漸演化長大,最終與主裂紋貫通,導致材料斷裂失效,如圖4f所示。對比完美無缺陷B2-NiAl,引入中心對稱微裂紋后,涂層在ε=0.085時已經發生斷裂,斷裂時的應變減小,這是由于微裂紋缺陷的存在使得涂層在裂紋尖端附近應力集中,從而造成了涂層的快速失效。
在裂紋擴展的整個過程中,應力值始終集中在裂尖位置。在應力值達到裂紋擴展所需的臨界應力值時,裂紋快速擴展,直至材料斷裂。裂紋面平整光滑,這說明裂紋以脆性解理的方式擴展。相比完美構型的NiAl涂層,含有裂紋后的擴展主要以預制裂紋為主導作用,而位錯和相變的因素起次要作用。整個裂紋擴展機理主要是:由于裂紋尖端附近出現位錯塞積,導致應力集中,進而在裂紋附近出現微孔洞,微孔洞長大并與主裂紋的擴展相遇而貫通,從而形成新的主裂紋,最終重復這個過程而導致材料失效。值得注意的是,當材料屈服后,裂紋尖端附近出現了大面積的塑性區。這是由于材料為BCC結構,所以進入塑性階段后,在<111>方向有大面積的位錯發射和塞積。這與HEALY等[35]研究BCC單晶鐵在高速拉伸下的相變機理相符合。
為了研究孔洞和裂紋雙缺陷對B2-NiAl涂層在高溫高速拉伸載荷作用下變形失效過程和塑性變形機理的影響,獲得含有單孔洞和中心微裂紋缺陷B2-NiAl涂層模型的缺陷演化過程,如圖5所示。在弛豫結束后,B2-NiAl中產生了大量的無序結構,形成了許多點缺陷。這是因為原子在較低溫度下具有較小的振蕩,這導致晶體材料具有更穩定的晶體結構,而在高溫下,原子的運動在其平衡位置附近相對較快,更易形成無序原子。在ε=0.049之前,裂紋并沒有擴展,而是沿著拉伸方向變寬,在裂紋尖端發生鈍化,孔洞也逐漸長大,如圖5a所示。這是由于此時加載時間較短,薄膜內應力未達到裂紋起裂的應力值。隨著應變增大,當應變ε=0.062時,應力達到初始屈服所需要的大小,材料發生屈服,孔洞邊緣產生了應力集中現象,所以在孔洞邊緣產生了裂尖,裂紋沿著[100]方向起裂,如圖5b所示。但是由于孔洞的存在使材料具有了一定的塑性,所以材料經歷了一段塑性變形階段。當應變ε增加到0.069時,應力-應變曲線出現了二次屈服現象。這是因為隨著應變的增加,裂尖前端有一小部分區域由于發射和塞積,產生了應力集中現象,應力集中使材料原子鍵斷裂而形成了一個微孔洞,最后裂紋與微孔洞貫穿形成一個新裂紋。
圖4 模型2(含有中心裂紋缺陷B2-NiAl涂層)在單軸拉伸載荷作用下變形及失效過程的微觀原子構型圖
Fig.4 Micro atomic configurations of deformation and failure process of model 2(B2-NiAl coating with a center crack) under uniaxial tensile load
當應變達到0.073時,主裂紋右端裂尖附近出現了大面積的位錯塞積和相變,此時應力還未達到微裂紋和微孔洞形成的條件,但在主裂紋左端的裂尖開始擴展,并且在主裂紋前端出現了一個應力集中區域,應力集中使得位錯塞積區出現了微孔洞,微孔洞和主裂紋在載荷作用下繼續長大和擴展,并貫穿,如圖5d所示。繼續加載,當ε=0.079時,在裂尖附近產生大量的FCC結構,這是因為B2-NiAl在應力誘導下,裂尖發生了相變,生成了FCC結構的L01相NiAl,這與曹莉霞等[36]研究應力誘發NiAl相變的結果相符合。隨著應變的繼續增加,裂紋逐漸擴展,最后B2-NiAl沿著[100]方向斷裂,但裂紋的擴展過程一直遵循著一個規律,即在裂尖前端產生應力集中區域,并在該區域中形成微孔洞,最后微孔洞生長與原裂紋擴展,長大的孔洞和裂紋貫穿形成新裂紋,最終導致裂紋不斷沿著[100]方向擴展,直至失效。然而,雖然模型3和模型2的失效過程和機理差不多,但引入孔洞之后,材料在屈服時,由于孔洞的存在使得應力集中現象減弱,涂層的斷裂應變顯著增加(模型 2在ε=0.078時已經快完全斷裂,模型3在 0.079時裂紋并未完全擴展到端部),孔洞的引入有效地提高了含有微裂紋涂層的塑性,這可能是由于孔洞減弱了裂紋尖端的應力集中。
圖5 模型3(含有單孔洞和中心裂紋缺陷B2-NiAl涂層)在單軸拉伸載荷作用下變形及失效過程的微觀原子構型圖
Fig.5 Micro atomic configurations of deformation and failure process of model 3(B2-NiAl coating with an void and a center crack) under uniaxial tensile load
圖6是含有雙孔洞和中心微裂紋缺陷的B2-NiAl涂層模型缺陷演化過程中對應的原子構型圖。當應變達到0.042時,體系內由于拉伸載荷作用而具有內應力并出現密集的點缺陷,特別是在微裂紋和微孔洞附近聚集;由于應力還未達到使裂紋起裂的臨界值,裂紋并沒有沿著[100]方向擴展,只是沿著加載方向逐漸擴展,但由于預制了雙孔洞,在加載方向的擴展距離比較均勻,裂紋尖端不再有明顯的鈍化現象,如圖6a所示。隨著應變增加到0.046時,裂紋并沒有從右端開始起裂,而是在裂紋左端的孔洞邊緣產生應力集中,并在[100]方向形成了裂尖,裂紋沿著加載方向擴展,如圖6b所示。由于孔洞的存在使材料具有了一定的塑性,當材料發生二次屈服時,又出現了一次應力集中現象,這次應力集中出現在裂紋右端孔洞的邊緣,使得裂紋右段也產生了裂尖,如圖6c所示。當應變達到0.062時,材料出現二次屈服現象,這次屈服是因為右端孔洞前方出現了一片應力集中區域,并且在這個區域中形成了一個微孔洞,微孔洞隨應變增加而長大,最后與裂紋貫穿形成新裂紋,如圖6d所示。當應變達到0.069時,裂紋沿著[100]方向開始向兩側擴展,裂紋尖端附近出現了大量的位錯塞積,位錯塞積區內的應力比較集中,從而導致在其內部出現了原子重新堆垛,形成了新的FCC結構,如圖6e所示。當應變加載到0.087時,裂紋右側部分已經擴展到邊界,但左側部分仍然還有少量區域未發生斷裂,如圖6f所示。
圖6 模型4(含有雙孔洞和中心裂紋缺陷B2-NiAl涂層)在單軸拉伸載荷作用下變形及失效過程的微觀原子構型圖
Fig.6 Micro atomic configurations of deformation and failure process of model 4(B2-NiAl coating with two voids and a center crack) under uniaxial tensile load
2.3 微缺陷對單晶B2-NiAl涂層結構的影響
納米涂層在高溫高速載荷下的失效過程和失效機理與涂層內部的結構變化有較大的關系[37],因此,需要采用徑向分布函數分析微缺陷對涂層內部結構變化的影響。單軸拉伸載荷作用下,B2-NiAl在不同應變下的徑向分布曲線如圖7所示。從圖7a可以看出,完美結構的晶體主要有6個明顯的特征峰:第1、2、3、6峰比較尖銳,說明具有短程有序和長程有序性,此代表著完美BCC結構的原子;第4、5峰出現分叉,說明第 4、5峰具有無序性,此代表著排列為無序的原子。隨著應變的增加,第1峰的高度增加,變銳,這說明隨著應變的增加,原子的配位數也隨即增大,短程有序性增強;但其他峰的高度降低,變平緩,配位數減小,長程無序性增加,這是由于體系內部位錯塞積和應力集中所造成的。當模型引入微裂紋后,RDF中出現了第7峰,該峰隨著應變的增加而變銳、變高,短程有序性增加,并且第1—6峰都隨著應變的增加而變銳、變高,晶體結構的有序性增加,如圖7b是在拉伸過程中,由于裂紋的存在使得應力集中只存在于裂紋尖端附近,相比完美模型,并沒有在體系內部形成大面積的位錯塞積。模型在引入孔洞后,對第 1—6峰的影響與引入裂紋的結果相似,但對第7峰的影響更劇烈,隨著應變的增加,第7峰峰值變高、變銳,說明孔洞引入后對短程有序性影響比較明顯。
圖7 在單軸拉伸載荷作用下B2-NiAl在不同應變下的徑向分布曲線
Fig.7 RDF of B2-NiAl coating under uniaxial tensile load in different strain: (a) sample 1; (b) sample 2; (c) sample 3; (d) sample 4
在拉伸載荷作用下,位錯的運動和塞積會形成新結構。圖8是在單軸拉伸載荷作用下含有裂紋的B2-NiAl在 ε=0.078時的原子構型圖。當模型應變 ε達到0.078時,裂紋尖端附近的原子重新堆垛形成了面心立方結構的L01相NiAl,晶體結構發生相變,從而對裂紋擴展和材料的斷裂產生影響。為了進一步分析相變的形成原因和機理,獲得單軸拉伸載荷作用下含有裂紋B2-NiAl在相變前后的原子應力云圖,如圖9所示。對比相變前后的應力云圖和相變圖可以發現,裂紋尖端處應力集中是裂紋尖端發生 BCC結構到FCC結構相變的根本原因,應力集中導致BCC結構高度畸變,原子重新排列成 FCC結構,并造成應力下降,這與文獻[31]的結論符合良好。
圖8 單軸拉伸載荷作用下含有裂紋的B2-NiAl在ε=0.078時的原子構型圖
Fig.8 Atomic configurations of deformation and failure process of B2-NiAl coating with cracks under uniaxial tensile load at ε=0.078
圖9 單軸拉伸載荷作用下含有裂紋B2-NiAl在相變前后的原子應力云圖
Fig.9 Atomic stress nephogram of phase tranmision of B2-NiAl coating with cracks under uniaxial tensile load: (a) before transition; (b) after transition
3 結論
1)B2-NiAl高溫涂層在拉伸載荷下以脆性解理方式失效,其應力-應變曲線具有高強度、低塑性的特性。模型引入裂紋后,材料的強度會明顯降低,但對材料的塑性沒有明顯的影響,材料仍然以脆性解理的方式擴展失效。增加孔洞后,材料的塑性會有明顯的提高,但強度會降低,涂層在拉伸過程中出現了明顯的“二次屈服”現象。
2)B2-NiAl高溫涂層在拉伸載荷下的失效形式主要受到位錯和相變因素的影響,裂紋在邊界處沿著[111]方向擴展。模型引入裂紋后,涂層的失效形式主要受到裂紋的影響,裂紋主要沿著[100]方向擴展,位錯和相變起次要作用。孔洞的引入有助于提高含有裂紋的B2-NiAl涂層的塑性,但并不會改變最終的失效形式。
3)位錯塞積是造成應力集中的主要原因,而應力集中則會導致微裂紋和微孔洞的形成。位錯塞積使涂層材料的晶體結構發生相變,相變后會使涂層的應力下降。涂層材料出現微裂紋時,可以引入孔洞來減小裂紋尖端處的應力集中,從而提升材料塑性,該方法可以為涂層的制備和防護提供一定的理論參考。
參考文獻:
[1]MAI Q X, DANIELS R D, HARPALANI H B. Structural changes induced by heating in electroless nickel-phosphorus alloys[J]. Thin solid films, 1988, l66(1-2): 235-247.
[2]吳錦楊。 自愈合熱障涂層的制備和研究[D]. 武漢: 華中科技大學, 2012.WU Jin-yang. Preparation and study of self-healing thermal barrier coatings[D]. Wuhan: Huazhong University of Science and Technology, 2012.
[3]吳波。 NiAl薄膜沉積及其退火熱處理的分子動力學模擬[M]. 南京: 南京工業大學, 2016.WU Bo. Molecular dynamics simulation of NiAl film deposition and annealing heat treatment[M]. Nanjing:Nanjing Tech University, 2016.
[4]YANG S L, WANG F H, SUN Z M, et al. Influence of columnar microstructure of a sputtered NiAl coating on its oxidation behavior at 1000 ℃[J]. Intermetallics, 2002,10: 467-471.
[5]ZHANG H, PENG X, WANG F. Fabrication of an oxidation-resistant β-NiAl coating on γ-TiAl[J]. Surface &coatings technology, 2012, 206: 2454-2458.
[6]SAEEDI B, SABOUR R A A, GHOLAMI G H. A study on nanostructured in-situ oxide dispersed NiAl coating and its high temperature oxidation behavior[J]. Surface &coatings technology, 2015, 276: 704-713.
[7]王楠, 周勇。 超音速電弧噴涂 NiAl復合涂層的電化學行為研究[J]. 表面技術, 2017, 46(2): 184-188.WANG Nan, ZHOU Yong. Electrochemical behavior of NiAl composite coating by supersonic arc spraying[J].Surface technology, 2017, 46(2): 184-188.
[8]BAI M, REDDY L, HUSSAIN T. Experimental and thermodynamic investigations on the chlorine-induced corrosion of HVOF thermal sprayed NiAl coatings and 304 stainless steels at 700 ℃[J]. Corrosion science, 2018,135: 147-157.
[9]李鐵藩, 馬信清。 Y2O3質點對 β-NiAl涂層抗氧化性能的影響[J]. 中國稀土學報, 1991, 9(3): 229-233.LI Tie-fan, MA Xin-qing. Influnce of Y2O3 doping on β-NiAl coating in inoxidizability[J]. Journal of rare earths, 1991, 9(3): 229-233.
[10]李惠, 焦雷, 陸鵬程, 等。 CuCo2Be 合金表面等離子噴涂 Cr3C2-NiCr/NiAl 復合涂層不同溫度下的摩擦磨損特性[J]. 稀有金屬材料與工程, 2018, 47(2): 588-593.LI Hui, JIAO Lei, LU Peng-cheng, et al. Friction and wear properties of plasma sprayed Cr3C2-NiCr/NiAl composite coating on CuCo2Be alloy at different temperatures[J]. Rare metal materials and engineering, 2018,47(2): 588-593.
[11]TAWANCY H M. Infuence of superalloy substrate composition on the oxidation resistance of β-NiAl diffusion coating[J]. Metallography, microstructure, and analysis,2018, 7(1): 65-76.
[12]朱志雄, 張鴻, 劉超峰, 等。 Ni-Al 合金凝固過程的分子動力學模擬[J]. 中國有色金屬學報, 2009, 19(8):1409-1416.ZHU Zhi-xiong, ZHANG Hong, LIU Chao-feng, et al.Molecular dynamics simulation for solidification process of Ni-Al alloys[J]. The Chinese journal of nonferrous metals, 2009, 19(8): 1409-1416.
[13]沙憲偉, 張修睦, 陳魁英, 等。 NiAl表面能的分子動力學計算[J]. 金屬學報, 1996, 32(11): 1184-1188.SHA Xian-wei, ZHANG Xiu-mu, CHEN Kui-ying, et al.Surface energy of NiAl alloy calculated by molecular dynamics simulation[J]. Acta metallurgica sinica, 1996,32(11): 1184-1188.
[14]沙憲偉, 張修睦, 陳魁英, 等。 NiAl熱誘發馬氏體相變的分子動力學模擬[J]. 金屬學報, 1996, 32(7): 685-694.SHA Xian-wei, ZHANG Xiu-mu, CHEN Kui-ying, et al.Molecular dynamics simulation of thermally induced martensitic transformations in NiAl[J]. Acta metallurgica sinica, 1996, 32(7): 685-694.
[15]GUO Ya-fang, WANG Yue-sheng, WU Wen-ping, et al.Atomistic simulation of martensitic phase transformation at the crack tip in B2NiAl[J]. Acta materialia, 2007, 55:3891-3897.
[16]EVTEEV A V, LEVCHENKO E V, RILEY D P, et al.Reaction of a Ni-coated Al-nanoparticle to form B2NiAl:A molecular dynamics study[J]. Philosophical magazine letters, 2009, 89(12): 815-830.
[17]BARAS F, POLITANO O. Epitaxial growth of the intermetallic compound NiAl on low-index Ni surfaces in Ni/Al reactive multilayer nanofoils[J]. Acta materialia,2018, 148: 133-146.
[18]CUI Yuan-yuan, CHEN Hong-fei, YANG Guang, et al.Molecular dynamics simulations of lattice site preference and phase separation in B2NiAl with Pt addition[J]. Journal of alloys and compounds, 2018, 740: 863-869.
[19]MAUREL V, R?MY L, HARVEY M, et al. The respective roles of thermally grown oxide roughness and NiAl coating anisotropy in oxide spallation[J]. Surface & coatings technology, 2013, 215: 52-61.
[20]DING J, LI F X, KANG K J. Effects of material creep on displacement instability in a surface groove under thermo-mechanical cycling[J]. Surface & coatings technology, 2009, 204(1-2): 157-164.
[21]MISHIN Y, MEHL M J, PAPACONSTANTOPOULOS D A. Embedded-atom potential for B2NiAl[J]. Physical review B, 2002, 65: 224114 .
[22]張而耕, 陳強, 黃彪, 等。 熱障涂層材料制備及失效機理的研究進展[J]. 陶瓷學報, 2016, 37(1): 5-10.ZHANG Er-geng, CHEN Qiang, HUANG Biao, et al.Research progress and performance of thermal barrier coatings[J]. Journal of ceramics, 2016, 37(1): 5-10.
[23]WU W P, YAO Z Z. Molecular dynamics simulation of stress distribution and microstructure evolution ahead of a growing crack in single crystal nickel [J]. Theoretical &applied fracture mechanics, 2012, 62(1): 67-75.
[24]羅德春, 芮執元, 曹卉, 等。 單晶 γ-TiAl中孔洞位置對裂紋擴展影響的分子動力學模擬[J]. 功能材料, 2016,47(6): 136-141.LUO De-chun, RUI Zhi-yuan, CAO Hui, et al. Effect of holes position on single crystal γ-TiAl alloy crack propagation based on molecular dynamics simulation[J]. Functional materials, 2016, 47(6): 136-141.
[25]吉伯海, 袁周致遠, 劉天笳, 等。 鋼箱梁疲勞裂紋鉆孔止裂修復的影響因素[J]. 江蘇大學學報(自然科學版),2016, 37(1): 97-102.JI Bo-hai, YUAN Zhou-zhi-yuan, LIU Tian-jia, et al. Influencing factors of stop-hole method for fatigue crack of steel box girder[J]. Journal of Jiangsu University (natural science edition), 2016, 37(1): 97-102.
[26]PUN G P P, MISHIN Y. Development of an interatomic potential for the Ni-Al system[J]. Philosophical magazine,2009, 89(34-36): 3245-3267.
[27]SUNDARAM D S, PURI P, YANG V. Thermochemical behavior of nickel-coated nanoaluminum particles[J].Journal of physical chemistry C, 2013, 117: 7858-7869.
[28]趙亞溥。 納米與介觀力學 [M]. 北京: 科學出版社,2014.ZHAO Ya-pu. Nano and mesoscopic mechanics [M]. Beijing: Science Press, 2014.
[29]SWOPE W C, ANDERSEN H C, BERENS P H, et al. A computer simulation method for the calculation of equilibrium constants for the formation of physical clusters of molecules: Application to small water clusters[J]. The journal of chemical physics, 1982, 76(1): 637-649.
[30]NOSE S. A unified formulation of the constant temperature molecular dynamics methods[J]. The journal of chemical physics, 1984, 81(1): 511.
[31]DING Jun, WANG Lu-sheng, SONG Kun, et al. Molecular dynamics simulation of crack propagation in singlecrystal aluminum plate with central cracks[J]. Journal of nanomaterials, 2017, 2017: 1-12.
[32]丁軍, 劉泊, 王路生, 等。 微觀尺度下單晶銅熔點多因素影響的分子動力學模擬研究[J]. 材料導報, 2017,31(6): 147-152.DING Jun, LIU Bo, WANG Lu-sheng, et al. Microscale molecular dynamics simulation of different factors influence on melting point of single crystal copper[J]. Materials review, 2017, 31(6): 147-152.
[33]STUKOWSKI A. Visualization and analysis of atomistic simulation data with ovito: The open visualization tool[J].Modelling and simulation in materials science and engineering, 2010, 18(6): 2154-2162.
[34]郭宇, 莊茁, 李曉雁。 FCC金屬塑性屈服的尺度效應和應變率響應[J]. 力學學報, 2006, 38(3): 398-406.GUO Yu, ZUANG Zhuo, LI Xiao-yan. Effects of specimen size and applied strain rate on the plastic flow of FCC metals[J]. Chinese journal of theoretical and applied mechanics, 2006, 38(3): 398-406.
[35]HEALY C J, ACKLAND G J. Molecular dynamics simulations of compression-tension asymmetry in plasticity of Fe nanopillars[J]. Acta materialia, 2014, 70(5): 105-112.
[36]曹莉霞, 尚家香, 張躍。 應力誘發 NiAl單晶馬氏體相變的分子動力學模擬[J]. 物理學報, 2009, 58(10): 7307-7312.CAO Li-xia, SHANG Jia-xiang, ZHANG Yue. Molecular dynamics simulation of stress-induced martensitic phase transformation in NiAl[J]. Acta physica sinica, 2009,58(10): 7307-7312.
[37]賴莉珊, 吳永全, 沈通, 等。 納米 Al2O3顆粒對純 Fe液誘導凝固過程的分子動力學模擬[J]. 物理化學學報,2012, 28(6): 1347-1354.LAI Li-shan, WU Yong-quan, SHEN Tong, et al. Molecular dynamics simulation of induced solidification process of pure liquid Fe by Al2O3 nanoparticles[J]. Acta physico-chimica sinica, 2012, 28(6): 1347-1354.
免責聲明:本網站所轉載的文字、圖片與視頻資料版權歸原創作者所有,如果涉及侵權,請第一時間聯系本網刪除。
相關文章
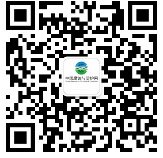
官方微信
《中國腐蝕與防護網電子期刊》征訂啟事
- 投稿聯系:編輯部
- 電話:010-62316606-806
- 郵箱:fsfhzy666@163.com
- 中國腐蝕與防護網官方QQ群:140808414
點擊排行
PPT新聞
“海洋金屬”——鈦合金在艦船的
點擊數:8107
腐蝕與“海上絲綢之路”
點擊數:6456