宇航用某型號激光器在電裝前的存儲階段發生嚴重腐蝕,殼體鍍金層表面及其與陶瓷絕緣子的焊接位置表面大片區域發生變色,并呈放射狀向周圍擴散。該型號激光器殼體材料為FeCo、Ni、Au,焊接區為AgCu焊料,陶瓷絕緣子為Al2O3;而同批次同型號相同工藝材料的殼體及焊接區表面完好。該器件的存儲環境溫度為22℃,濕度為50%。為查明腐蝕原因,避免類似事故再次發生,本文通過腐蝕形貌觀察、腐蝕產物能譜分析、制樣鏡檢、金相及SEM等理化檢驗方法對失效原因進行了分析。
一、理化檢驗與結果
1、宏觀檢查
對失效件進行宏觀檢查,發現圖1標識區域為變色最嚴重區域,其表面腐蝕變色形貌如圖1b所示。從圖中可見:LD激光器鍍金層表面大片區域發生腐蝕變色,并呈放射狀向四周擴散。另外,部分引腳焊盤的周邊也存在腐蝕變色現象。
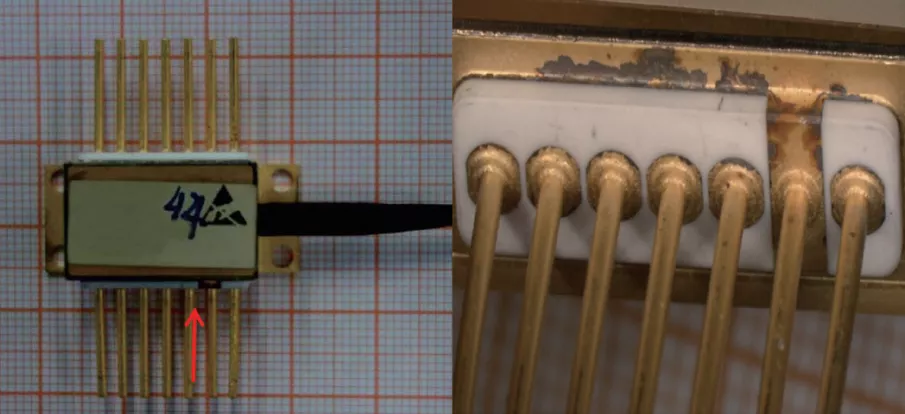
a)整體形貌 b)局部腐蝕變色形貌
圖1 LD激光器的宏觀形貌
2、微觀分析
采用掃描電子顯微鏡對激光器表面形貌進行檢查,結果如圖2所示,變色區Ⅰ表面的腐蝕形貌,鍍金層表面附著有大量疏松腐蝕產物;未變色區Ⅱ表面的局部放大形貌,鍍層表面潔凈、結構未見異常。
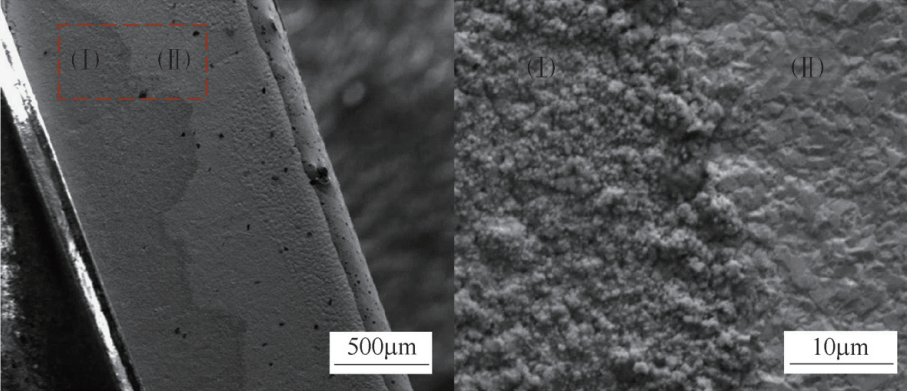
a)變色與未變色形貌 b)Ⅰ與Ⅱ處放大
圖2 LD激光器殼體表面腐蝕變色的SEM形貌
表1 激光器表面不同區域EDS分析結果(質量分數) (%)

在圖2所示位置對激光器表面的腐蝕產物及未變色區域進行能譜(EDS)的對比分析,結果如表1所示。能譜分析結果表明:腐蝕產物主要含C、O、S、Ag、Cu、Au等元素,而未變色區域主要成分為Au,且不含S、Ag、Cu,據此推測鍍金層表面變色區域附著的腐蝕產物的物相可能為Ag、Cu的硫化物。
3、金相檢測
將上述激光器灌封后沿引腳軸向進行磨拋,對激光器表面變色區的鍍層完整性進行金相檢查。圖3a為殼體與陶瓷絕緣體焊接位置附近低倍金相形貌,其鍍層變色區域與焊接區域的高倍金相形貌如圖3b、3c所示。由圖3b可知,殼體表面變色位置的鍍金層與鍍鎳層完整致密,未見鍍層破損脫落或腐蝕通道;但在殼體變色位置與陶瓷絕緣子的焊接界面處發現開裂現象,開裂位置及金相形貌如圖3c所示。另外,從圖3d中開裂位置高倍金相形貌可以看出,在焊接位置頂端,陶瓷絕緣子與焊料表面鍍層結合處較為疏松。
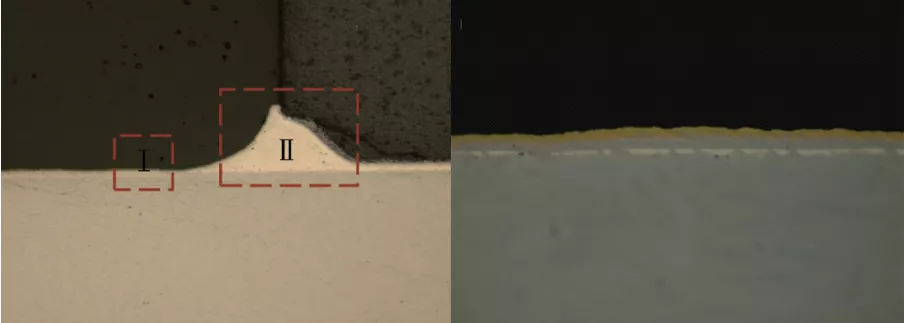
a)低倍金相形貌 b)Ⅰ處高倍金相形貌
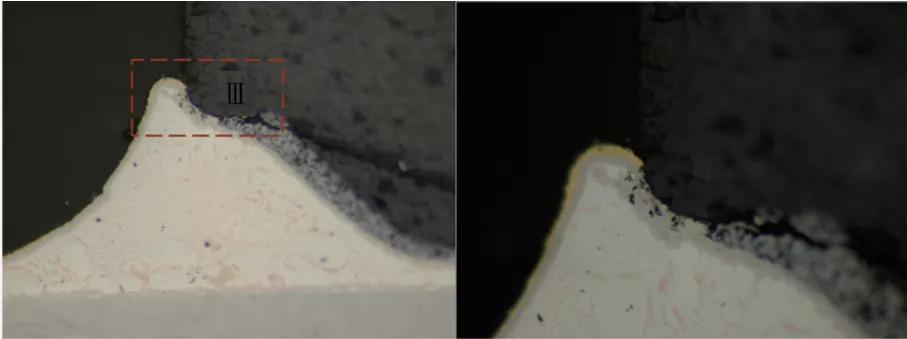
c)Ⅱ處高倍金相形貌 d)Ⅲ處高倍金相形貌
圖3 焊接區剖面金相形貌
4、掃描電鏡物相分析
使用掃描電子顯微鏡與能譜分析儀,對殼體鍍層表面的腐蝕產物與陶瓷絕緣子-焊料焊接界面的形貌與成分進行檢測。陶瓷絕緣子與殼體焊接位置的形貌如圖4所示,裂紋從陶瓷絕緣子內部穿過陶瓷絕緣子表面的mo-mo層擴展到焊料。
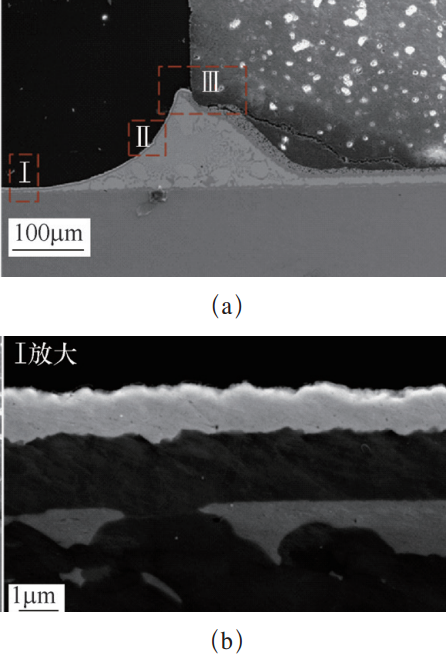
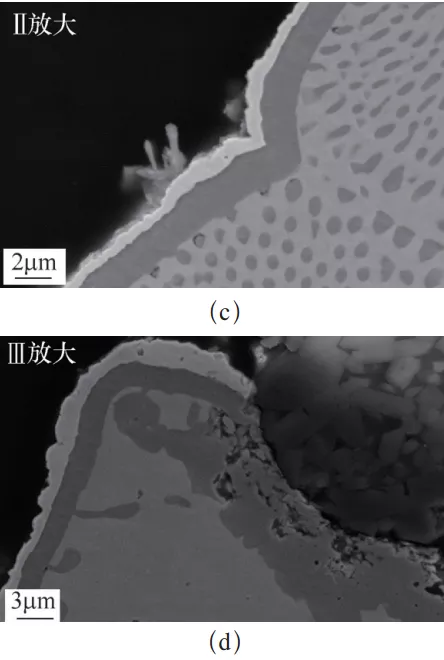
圖4 焊接區剖面SEM形貌
從圖4中Ⅰ放大和Ⅱ放大可以看出,變色區殼體鍍層表面及焊接區鍍層表面鍍鎳層與鍍金層完整致密,在鍍金層表面均存在腐蝕產物,對圖中標識區域進行EDX能譜測試,EDX測試結果顯示,圖中標識位置均存在主要元素為Ag、S、Cu的產物,從而確認變色區域表面為Ag、Cu的硫化物。
如圖5所示,對圖4中Ⅲ區域進行面掃描分析,從面掃描結果可以看出:AgCu焊料中的富Cu相在焊接界面與Ni發生互溶,并生成金屬間化合物,焊接界面附近焊料內以富銀相為主。另外,在焊接界面及焊料鍍層部分位置均有S元素分布。
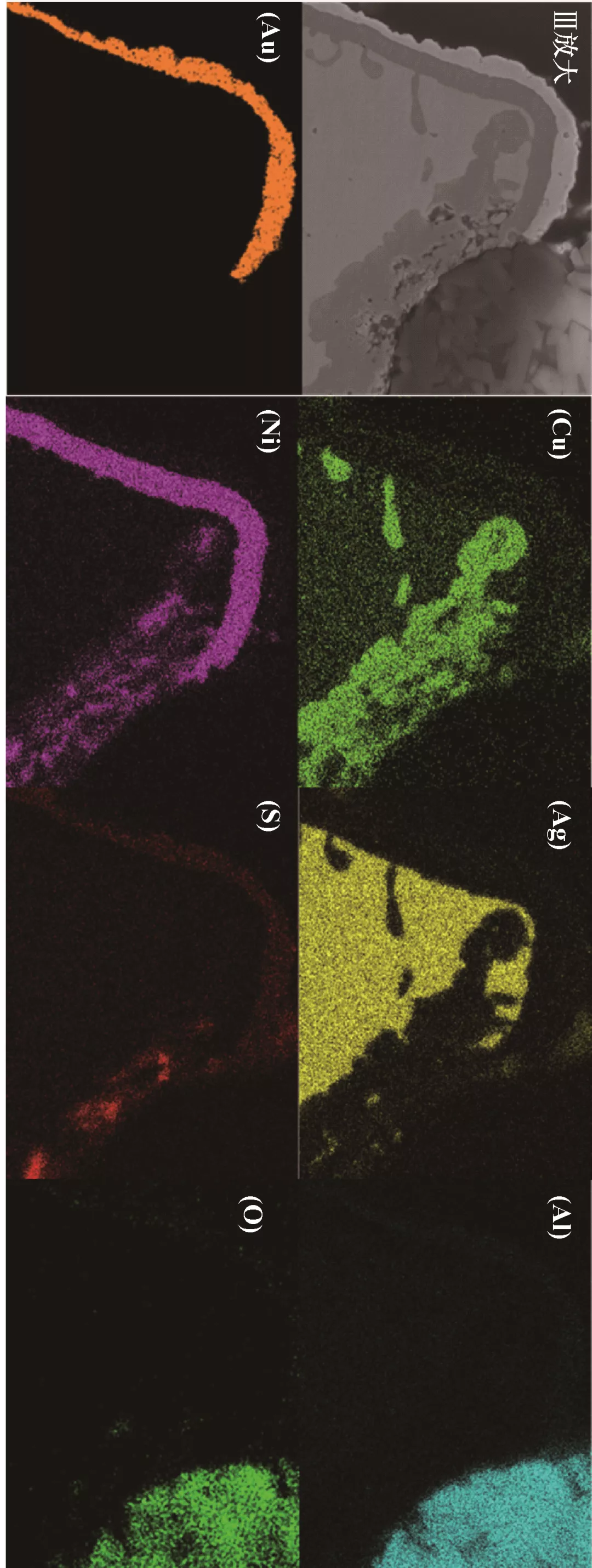
圖5 焊接區剖面SEM形貌Ⅲ處局部面掃描分布
為進一步確認焊接界面的腐蝕程度,在圖6所示位置對焊接頂端及裂紋周邊位置進行能譜(EDS)分析,結果如表2所示。能譜分析結果表明:在陶瓷絕緣子與焊料界面頂端,結合較為疏松位置,S含量較高。沿裂紋向陶瓷絕緣子內部延伸方向,S含量降低。在譜圖5位置處,已經不含S。另外,在S元素分布區域,均有Ag、Cu分布。
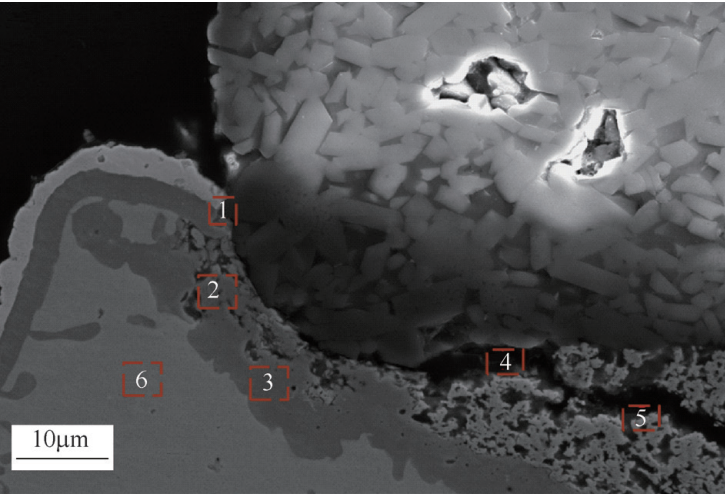
圖6 焊接區局部SEM形貌
表2 焊接位置不同區域EDS分析結果(質量分數) (%)
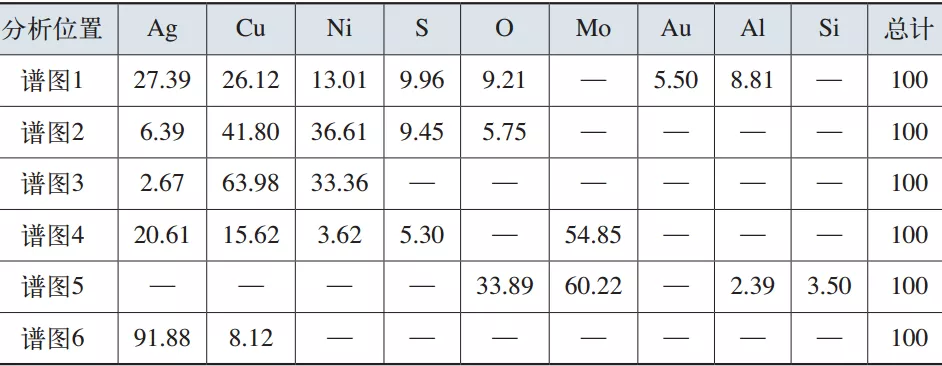
二、失效原因分析
將上述激光器沿引腳軸向繼續磨拋,對激光器表面其他變色位置進行剖面檢查,圖7a為陶瓷絕緣子與殼體焊接位置形貌,裂紋從陶瓷絕緣子內部穿過陶瓷絕緣子表面的mo-mo層擴展到焊料,與圖4所示剖面焊接位置處裂紋路徑一致。
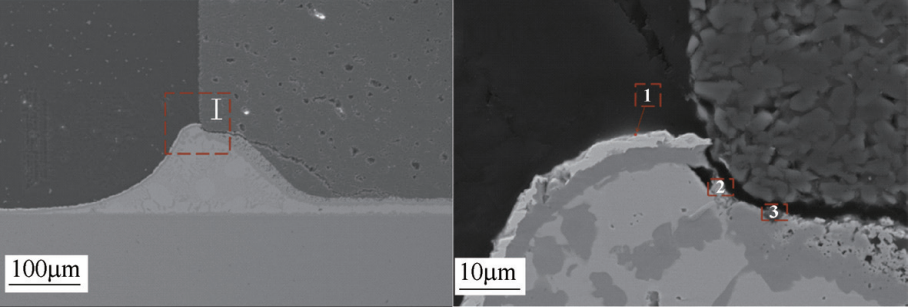
a)焊接區整體形貌 b)局部放大形貌
圖7 陶瓷絕緣子與殼體焊接位置的SEM形貌
對圖7b中標示區域進行能譜(EDX)分析,從能譜結果可以看出,焊料區鍍層表面物質的主要成分為Ag、S、Cu、Au,說明變色區表面的腐蝕產物均為Ag、Cu的硫化物,如表3所示。另外,在焊接區與陶瓷絕緣子的焊接界面處,均有S、Ag、Cu元素分布,且S含量沿裂紋向陶瓷絕緣子內部延伸方向逐漸降低,與圖6所示位置的元素分布情況類似。
表3 焊接位置不同區域EDS分析結果(質量分數) (%)
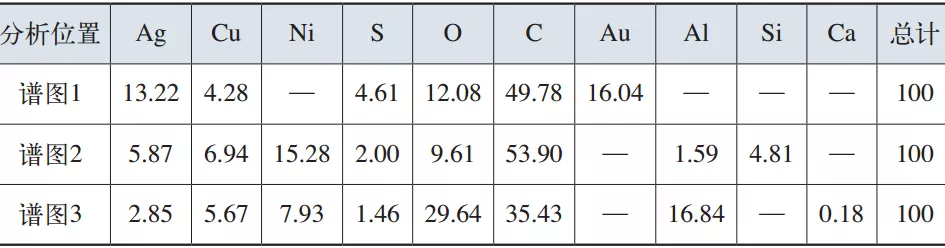
將同批次同型號相同工藝材料未發生腐蝕的激光器進行灌封并沿引腳進行軸向磨拋,對陶瓷絕緣子與殼體焊接位置的形貌進行SEM檢查。從圖8a可以看出,裂紋僅在陶瓷絕緣子內部,并沒有穿過陶瓷絕緣子表面繼續往外擴展。圖8b為頂端焊料區與陶瓷絕緣子的焊接形貌,在焊接位置頂端,陶瓷絕緣子與焊料表面鍍層結合良好,且焊料區鍍層表面無Ag、Cu的硫化物。
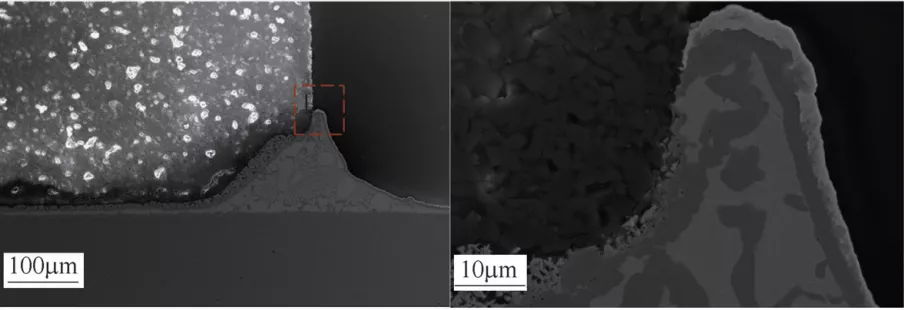
a)焊接區整體形貌 b)局部放大形貌
圖8 陶瓷絕緣子與殼體焊接位置的SEM形貌
基于上述電鏡觀察及物相分析的結果,再結合兩處變色剖面及同批次同型號未變色剖面的差異。通過對比,發現激光器表面變色主要是由于陶瓷絕緣子與焊接區之間存在貫穿裂紋,為腐蝕介質進入界面及AgCu焊料的遷移提供了通道。另外,在焊接位置頂端,陶瓷絕緣子與焊料表面鍍層結合處較為疏松,更加有利于腐蝕介質的進入及AgCu焊料的遷出。
焊接區的AgCu焊料沿裂紋遷移至殼體表面后發生了爬行腐蝕,即在含硫物質的作用下生成大量Ag、Cu的硫化物,并在Ag、Cu的暴露面上及其周圍擴散、堆集,從而導致激光器表面大片區域發生變色。且空氣中的含硫物質可引起Ag、Cu的爬行腐蝕,而界面位置開裂就會加快氣體介質的進入,使Ag、Cu的爬行腐蝕速度加快。
失效激光器的陶瓷/可伐封接工藝為:陶瓷絕緣子表面燒結Mo層后鍍Ni,后與AgCu焊料進行焊接。但Ni的富集會導致鉬的海綿強度下降,造成AgCu焊料焊接陶瓷時強度較低,且鉬層本身強度較低,因而容易出現開裂現象。
三、結論與建議
綜合兩處變色剖面與未變色剖面的差異以及分析結果表明:陶瓷與焊接界面位置開裂,導致AgCu焊料發生爬行腐蝕,致使激光器表面大片區域發生變色。
而未發生失效現象的同批次同型號激光器在陶瓷絕緣子內部也發現開裂現象,但裂紋沒有擴展至焊接界面,后續仍存在裂紋擴展至界面的風險。宇航用元器件發射過程中存在外力沖擊,太空服役環境下存在溫度循環,都可能使裂紋進一步擴展并導致封裝結構失效。鑒于上述現象和應用背景,提出以下建議:
(1)對于類似結構的陶瓷/可伐封接器件,用Ag焊料或Cu焊料焊接,可保證焊接強度較高,降低開裂風險。
(2)建議陶瓷絕緣子表面燒結金屬Wu,代替本身強度較低的金屬鉬。
免責聲明:本網站所轉載的文字、圖片與視頻資料版權歸原創作者所有,如果涉及侵權,請第一時間聯系本網刪除。
相關文章
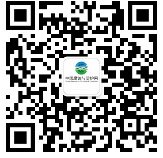
官方微信
《腐蝕與防護網電子期刊》征訂啟事
- 投稿聯系:編輯部
- 電話:010-62316606-806
- 郵箱:fsfhzy666@163.com
- 腐蝕與防護網官方QQ群:140808414
點擊排行
PPT新聞
“海洋金屬”——鈦合金在艦船的
點擊數:8148
腐蝕與“海上絲綢之路”
點擊數:6486