摘要
碳氮共滲工藝應用廣泛,但對碳氮共滲后零部件的滾動接觸疲勞失效機理研究較少。采用氣體碳氮共滲對馬氏體軸承鋼進行表面改性處理,對碳氮共滲試樣進行滾動接觸疲勞試驗,研究碳氮共滲對軸承鋼滾動接觸疲勞性能的影響及其失效機理。研究結果表明:碳氮共滲試樣表面硬度、殘余應力和殘余奧氏體含量顯著提高,使得其接觸疲勞壽命明顯高于常規試樣。 疲勞裂紋萌生于表面和亞表面,其中大量表面平行裂紋主要由表面白色蝕刻層硬度梯度變化而導致,表面材料受到嚴重微觀塑性變形產生晶粒細化;亞表面裂紋萌生位置受最大應力的分布和滲層厚度的影響。表面和亞表面疲勞裂紋的擴展和連接最終導致碳氮共滲試樣出現淺層剝落和分層剝落的失效形貌。
關鍵詞: 碳氮共滲 ; 馬氏體軸承鋼 ; 滾動接觸疲勞 ; 失效機理 ; 裂紋萌生
0 前言
滾動接觸疲勞(RCF)是軸承最常見的失效模式,尤其是在高速、重載等復雜工況下,RCF會導致軸承過早失效而嚴重影響設備的可靠性及使用壽命[1-3]。在接觸疲勞載荷作用下,裂紋會萌生于接觸表面或亞表面[4-5],疲勞裂紋的演化最終會導致材料表面形成點蝕、剝落坑和分層而失效。材料表面抗接觸疲勞性能對軸承壽命有很大的影響[6-9],因此,獲得具有優良耐磨、耐腐蝕和抗氧化性能的改性硬化表面層以提高材料的疲勞性能是很有必要的。
碳氮共滲是提高軸承壽命的主要方式。相比于單獨滲氮和滲碳處理,碳氮共滲改性處理能綜合滲氮和滲碳的優勢,提高表面硬度、耐磨性及耐蝕性,同時表層與基體形成硬度梯度下降緩慢,可提高軸承鋼等工程材料的力學性能,特別是摩擦學性能。近幾年,已有較多研究人員對表面碳氮改性試樣的疲勞失效機理進行研究[10-15]。KARAMIS等[16]研究證明碳氮處理后低碳鋼AISI 1020表面硬度提高2倍,基體材料仍保持良好的韌性,試樣的摩擦學性能得到顯著改善。谷臣清等[17]發現高溫碳氮共滲后M50NiL鋼疲勞裂紋沿滲層的擴展行為與滲層的塑性和韌性等有關,滲層高溫硬度的提高是馬氏體回火相析出發生改變的結果。KANCHANOMAI等[18]研究了殘余應力對碳氮化AISI 1015鋼疲勞性能的影響,發現碳氮改性層內存在較大的殘余壓應力,其疲勞壽命約為未處理試樣的5倍。過渡區內殘余應力的變化是誘發疲勞裂紋的主要原因。在現有文獻中,對于表面改性材料的疲勞性能研究主要集中于疲勞壽命和滲層宏觀摩擦磨損性能,而對滾動接觸疲勞載荷下的微觀失效特征及其機理以及疲勞過程中微觀組織的動態變化對于疲勞性能影響的研究工作很少見。
本文以GCr15馬氏體軸承鋼為試驗對象,應用氣體碳氮共滲在試樣表面制備硬化改性層。使用MJP-30型滾動接觸疲勞試驗機進行滾動接觸疲勞試驗。研究表面碳氮共滲試樣滾動接觸疲勞行為及失效機理,為碳氮共滲后的零部件在接觸疲勞等方面的應用提供理論依據。
1 試驗方法
1.1 試驗材料及熱處理工藝
試驗原材料為退火態GCr15鋼,其化學成分(質量分數/%)為:0.89~0.92C;0.28~0.32Mn;1.77~1.82Cr;0.28~0.31Si;0.01~0.02S;其余為Fe。表面改性工藝選取為氣體碳氮共滲,設備選用多用爐,采用氨氣+甲醇+氮氣+丙烷的氣氛在溫度860℃±5℃下保溫3h進行共滲處理,淬火冷卻至室溫,隨后在170℃±5℃下回火保溫2h。由于碳氮共滲工藝只對試樣表面一定深度范圍內的基體起到改性強化作用,而內部基體則相當于進行同溫條件下的常規熱處理,因此將疲勞試樣的對照組選為與碳氮共滲工藝相同溫度的常規熱處理試樣。
1.2 接觸疲勞試驗
根據YB-T5345—2006將試樣設計加工為圓環狀,外徑和內徑分別為60mm和30mm,厚度為20mm。為了增加接觸應力,主試樣的外圓接觸面被加工成寬度為5mm、高度為3mm的凸平臺,試樣示意圖如圖1所示。試驗在MJP-30型滾動接觸疲勞試驗機上進行。主、陪試樣分別由獨立軸驅動,試驗機配備振動信號傳感器,用于監控測試過程,試樣在試驗過程中會因表面發生點蝕而產生較大震動,當震動信號頻率高于300dB時,試驗機自動停止。
圖1 疲勞試樣尺寸示意圖
試驗全程采用油潤滑,在試驗過程中,最大赫茲接觸應力選取2.0GPa和2.6GPa。下軸轉速1 000r/min;上軸轉速選取900r/min和850r/min,從而獲得10%和15%的滑差比率,分別與上述不同載荷組成對照組,進而研究試樣在不同工況下的滾動接觸疲勞失效機理。由于滾動接觸疲勞壽命存在較大分散性,為了得到統計結果,在每種試驗條件下進行了3組滾動接觸疲勞試驗。
試驗結束后利用電火花線切割機切取基體的軸向及徑向截面,經過機械研磨拋光后利用4%的硝酸酒精溶液進行腐蝕。使用金相顯微鏡(OM)和掃描電子顯微鏡(SEM)觀察試驗前后試樣接觸表面及其亞表面顯微組織結構的變化。采用顯微維氏硬度計測定滲層亞表面沿深度方向的顯微硬度分布,每個壓痕點間距為25 μm。輝光放電發射光譜儀(GD-OES)用于表征試樣亞表面碳、氮元素含量隨深度的變化。試樣滲層及基體物相使用X射線衍射儀(XRD)進行分析,掃描速度為2(°)/min,掃描范圍為20°~100°,用Jade6軟件將所得數據與標準峰進行匹配確定物相成分。試驗前利用高速殘余應力分析儀分別對兩組試樣接觸表面的殘余應力進行表征,測試方法為雙探測器同傾法, X光管發出的X射線為Cr靶的 Kα輻射,測試電壓和電流分別為25kV和5mA,選擇的衍射晶面為(BCC,hkl-211)。透射電鏡薄片試樣由聚焦離子束(FIB)切取制備,利用30kV、50~120pA的電子光束將其進行減薄。待測薄片厚度最終控制在50~70nm,應用透射電鏡(TEM)對其微觀組織進行觀察。
2 試驗結果與討論
2.1 碳氮共滲層的微觀形貌和顯微硬度
碳氮共滲初始試樣腐蝕后的橫截面金相形貌如圖2a所示,可以看出碳氮擴散層與基體之間存在明顯的邊界。圖2b和2c分別為框選區域A和B內的放大形貌圖,滲層與內部基體的宏觀組織組成物相類似均以回火馬氏體為主。滲層中碳化物數量較多,主要呈球狀,平均尺寸為0.95 μm。一定含量的碳化物析出有利于試樣接觸表面耐磨性能的提升。隨深度增加,基體內部碳化物數量明顯減少。
圖2 碳氮共滲層與基體微觀組織形貌
利用輝光放電質譜儀對碳氮共滲試樣亞表面元素分布進行分析,含量變化曲線如圖3所示。碳、氮元素含量的分布曲線存在三個階段。在曲線最開始的Ⅰ 階段存在一個高峰,這表明在氣體碳氮共滲處理后近表面碳含量為1.92wt.%,相比基體碳含量提高約2倍。但近表面氮元素含量較少,氮元素含量僅為0.45wt.%。在Ⅱ階段兩元素含量均存在平緩區;最后在Ⅲ階段碳、氮元素含量隨深度增加逐漸減少,在距表面180 μm處的碳含量與基體碳含量基本持平。試樣亞表面顯微硬度隨深度變化的測量結果如圖4所示,碳氮共滲處理主要對試樣表面起到改性強化作用,滲層硬度提高至795HV0.05,在距離表面200 μm以下的材料硬度趨于基體硬度,為745HV0.05。顯微硬度變化趨勢和碳、氮元素含量隨深度的變化相符合,判斷該碳氮共滲工藝下有效硬化層厚度在180~200 μm范圍內。
圖3 碳、氮元素濃度含量隨深度變化曲線
圖4 碳氮共滲層和內部基體橫截面顯微硬度隨深度變化曲線
2.2 碳氮共滲層的物相
圖5 為碳氮共滲試樣試驗前后碳氮共滲層與內部基體的XRD圖譜。可以看出滲層處組織組成物與基體內部大致相同,主要由馬氏體、殘余奧氏體和滲碳體組成。由于共滲層中氮含量較低,在XRD圖譜中并沒有顯示出明顯的氮化物衍射峰。根據碳氮共滲原理,滲層的組織中應具有少量的氮化物。相比于基體內部,滲層處的奧氏體衍射峰峰強度更強,馬氏體的衍射峰強則相對較弱,這表明滲層處含有更多的殘余奧氏體。
圖5 碳氮共滲試樣滲層和基體的XRD圖譜
根據XRD圖譜分別選取(220)α、(200)γ、 (211)α、(220)γ 以及(311)γ 處的衍射峰,利用式 (1)計算殘余奧氏體體積分數[19]:
式中,vγ 為奧氏體相的體積分數(%);n 為衍射峰數目;R 為散射因子;I 為(hkl)晶面衍射峰的積分強度;θ 為衍射角;γ 為單胞體積;F 為結構因子;ρ 為多重性因子;exp(?2M)為溫度因子。
經計算,碳氮共滲在疲勞試驗前的滲層近表面及其基體內部殘余奧氏體含量分別為37.32%和7.07%。滲層處與內部基體中的殘余奧氏體含量差別較大,這是由于近表面碳、氮元素含量的提高降低了馬氏體轉變溫度(Ms),同時在一定程度上增加了奧氏體的穩定性,使得奧氏體轉化不完全,最終導致滲層處相比基體含有更多的殘余奧氏體。
2.3 滾動接觸疲勞性能分析
圖6 所示為碳氮共滲試樣和常規熱處理試樣在載荷和滑差率分別為2.0GPa-10%,2.0GPa-15%和2.6GPa-15%工況條件下滾動接觸疲勞壽命試驗結果。比較可見,碳氮共滲試樣疲勞性能明顯優于常規熱處理試樣,在三種工況環境下碳氮共滲處理試樣疲勞壽命分別提高5、8和3倍。隨著載荷和滑差率的增大,兩組試樣壽命均處于減少趨勢。疲勞壽命的改善一方面是由于碳氮共滲層的存在增加了接觸表面的硬度,使得試樣在接觸邊緣不容易形成應力集中區域而萌生疲勞裂紋。在一定的硬度范圍內,接觸疲勞抗性隨硬度的增大而升高。試樣亞表面硬度分布平緩,表面碳氮改性處理后的M50NiL、AISI 410鋼斷面滲層顯微硬度分布也出現這種趨勢[20-21],這能有效降低滲層與基體之間因硬度差異較大而導致組織組成物不兼容萌生裂紋的可能性,有利于試樣耐磨性和抗接觸疲勞性能的提高[12, 22]。再者,試樣經碳氮共滲處理后,碳、氮元素作為間隙元素擴散到鐵晶格中,造成嚴重晶格畸變,并起到彌散強化的作用,在提高滲層硬度的同時也使擴散層內部產生了較高的殘余壓應力[23-26]。經測得,在本次試驗中試驗前常規熱處理試樣以及碳氮共滲試樣接觸面殘余應力大小分別為?34.00MPa和?230.49MPa(沿試樣接觸表面周向等距離選取5個點,測試結果取平均值),均為殘余壓應力。 KANCHANOMAI等[18]在對碳氮共滲后的AISI 1015鋼研究中發現,共滲層中存在較大的殘余壓應力且隨著深度的增加而減少。較高的殘余壓應力可以誘使裂紋閉合并在一定程度上延緩其擴展演化,防止試樣表面較早出現剝落坑等失效形貌[27-29]。
圖6 不同工況下試樣的滾動接觸疲勞壽命
另一方面,殘余奧氏體含量的不同對于試樣的疲勞壽命也存在較大影響。已有較多研究表明,一定含量的殘余奧氏體能有效提高接觸疲勞性能[30-31]。在滾動接觸疲勞過程中,發生應變誘發馬氏體相變[32-34]。圖7為碳氮共滲試樣分別在2.0GPa-15%和2.6GPa-15%工況下經過2.8×106 和7.6×105 次循環疲勞失效后接觸面的XRD圖譜,對比原始物相衍射峰(圖5)可以看出馬氏體衍射峰強度變化較小,然而奧氏體衍射峰已消失。這表明在疲勞試驗后接觸表面的殘余奧氏體含量幾乎為0,近表面處的殘余奧氏體基本上已轉變為馬氏體。同樣的結果也出現在滾動接觸疲勞試驗后的AISI 52100軸承鋼表面中[35]。相變后的馬氏體體積發生膨脹,考慮到近表面材料硬度較大會對內部基體起到約束作用,這使得內部基體膨脹后的能量會以壓應力的形式保存于近表面的基體中。另外,一定量殘余奧氏體的存在可以確保樣品表面的載荷分布得更加均勻,利用其易變形特點,降低壓痕的邊緣效應,使起源于壓痕邊沿的表面疲勞源不易形成和擴展,從而提高試樣的接觸疲勞壽命。
圖7 不同工況碳氮共滲試樣失效后近表面XRD圖譜
2.4 失效形貌及其機理分析
通過觀察失效表面和橫截面來識別其損傷機理。接觸疲勞裂紋的萌生和擴展是切應力和材料切變強度相互作用的結果,常見的裂紋萌生類型有兩種:疲勞裂紋萌生于表面[36];疲勞裂紋萌生于亞表面[37]。在本次碳氮共滲失效試樣中,以上兩種裂紋類型均有出現且以亞表面裂紋為主。
2.4.1 表面裂紋萌生機理
圖8 為碳氮共滲試樣在2.6GPa-15%工況條件下循環1.7×105 次后的失效形貌。圖8a為接觸表面的宏觀形貌,經疲勞試驗后接觸表面呈現“層片狀” 結構,接觸表面裂紋垂直于滾動方向并向周圍擴展,局部區域出現淺層剝落的失效形貌。裂紋附近基體表面出現較多劃痕和犁溝,圖中圓圈標記位置。圖8b為該試樣橫截面形貌,切取位置由圖8a中的虛線A處標出。可以看出在接觸表面存在平均厚度為15~20 μm的白色蝕刻層 (WEL)。WEL表現出與基體不同的形貌特征,原始馬氏體結構已消失,取而代之的是致密組織形貌并與基體之間存在明顯的邊界。相比于滲層基體,WEL內球狀碳化物的數量大大減少,部分碳化物沿剪切方向被拉長。在WEL內部存在兩處裂紋:表面裂紋和層間裂紋。表面裂紋沿與滾動方向呈銳角演化一段距離隨即平行于接觸表面擴展;層間裂紋貫穿WEL與基體交界處,裂紋與接觸表面相平行。這與常規熱處理試樣中觀察到表面裂紋的演化形式存在較大區別[38]。
在疲勞循環載荷作用下,接觸表面呈現組織被剪切拉長特征是常見的現象[39-40],較高的摩擦力會導致表面材料發生嚴重的塑性變形進而影響內部微觀組織形貌,這一現象在WEL內尤為明顯。TEM明場形貌圖以及選區電子衍射花樣(SAED)顯示了距表面不同深度位置基體的微觀結構差異,結果如圖8c所示。“A”區域處于WEL內部,可以看出馬氏體組織沿剪切方向被大幅拉長,晶界處和晶粒內聚集的位錯團簇將其劃分為亞晶以及納米晶,平均晶粒尺寸為50~75nm,“1”處SAED花樣為清晰且較為連續的 α-Fe衍射環。“B”區域基體呈層片結構的拉長馬氏體晶粒,層片間距集中在150nm,拉長晶粒邊界清晰,晶粒長度在200~350nm。從 “2”處SAED可以看出 α-Fe衍射斑點發生了變形,表現為不連續的多晶衍射環。圖中兩處SAED存在明顯區別,這是因為相比于內部基體,WEL內晶粒細化嚴重,衍射區域中小尺寸晶粒數量增多使得取向更加隨機,呈現出更為完整的衍射環。 DAUTZENBERG等[41]通過計算彎曲馬氏體板條邊界的曲率得出有效剪應變沿深度方向的變化規律,即在一定深度范圍內距離表面越近剪切應變越大。根據在WEL與基體交界處的塑性流動線,其等效剪應變最大估計值約為13.8。由于WEL層內塑性流線幾乎和磨損表面相平行,無法進行剪應變的估算。然而,有研究表明近表面的有效剪應變可達到62.98[42]。這意味著近表面WEL內剪切應變遠大于其以下的基體,導致該位置晶粒細化最為嚴重,表面基體率先超過材料疲勞極限而萌生表面裂紋。
圖8 2.6GPA-15%工況條件下碳氮共滲試樣循環1.7×105次后表面以及橫截面失效形貌
圖8d為近表面顯微硬度變化曲線,壓痕點間隔10 μm,每個數據點是三個測試結果的平均值。根據結果可知,距表面10 μm處基體硬度為860HV0.05,顯微硬度隨距表面深度的加大逐漸降低,最后趨于原始滲層硬度值790HV0.05。值得注意的是,距表面20 μm及其附近的基體并未出現形變形貌,但硬度相比于原始滲層硬度仍有提高。近表面WEL處硬度最大,與先前材料經疲勞試驗后的表面變形研究結果一致,接觸面晶粒細化起到強化材料硬度的作用[32, 43-44]。ZHANG等[45]在研究中指出WEL為表面裂紋萌生的早期階段,WEL的高硬度可能導致脆性裂紋的形成和隨后的疲勞裂紋擴展。WEL與基體之間因硬度以及彈性模量的差異會導致材料的不兼容,在循環載荷作用下兩者之間的交界處易萌生層間平行裂紋。表面裂紋會導致接觸表面呈現“層片狀”結構,潤滑油進入裂紋內部形成高壓腔,增加了裂紋尖端的應力,加速裂紋向內部擴展[46],當與層間裂紋相連時則會導致表面淺層剝落的失效形貌。疲勞試樣表面出現上述WEL形貌而誘發表面裂紋的失效形貌只在2.6GPa-15%的工況條件下出現,其他工況均未觀察到該現象,說明高載荷和高滑差是產生WEL的主要原因。
2.4.2 亞表面萌生裂紋
如圖9a為碳氮共滲試樣在載荷2.0GPa-15%工況條件下,進行2.92×106 次循環后接觸面的典型剝落坑失效形貌。接觸表面存在較多點蝕坑微孔,這是由潤滑油中的顆粒雜質導致。剝落坑的底部較為平坦,與接觸表面形成約為30°的坡度。在循環載荷作用下,剝落坑邊緣處發生應力集中而誘發橫向裂紋。如圖9a框選區所示,裂紋處的基體由于塑性變形已出現較多微裂紋,當該部分基體超過屈服極限時發生剝落進而產生更大的失效形貌。根據虛線B處的橫截面可知剝落坑深度約為182 μm(圖9b),近似于滲層厚度。在剝落坑底端存在兩條沿相互垂直方向擴展的裂紋。
圖9 2.0GPa-15%工況條件下碳氮共滲試樣2.92×106 次循環后接觸表面以及橫截面失效形貌
剝落坑主要由亞表面裂紋導致。圖10a為試樣在載荷條件為2.0GPa表面裂紋形貌,裂紋萌生位置距表面約178 μm。主裂紋沿滾動方向呈銳角向接觸表面演化,分支裂紋表現出與主裂紋不同的演化方式。分支裂紋的擴展演化不僅受應力作用影響還與材料本身有關,如晶界、夾雜以及碳化物顆粒等。在循環載荷作用下,亞表面裂紋演化至接觸表面進而造成如圖9a的剝落坑失效形貌。值得注意的是,不同載荷下裂紋分布的位置存在較大區別,如圖10b為載荷2.6GPa亞表面裂紋分布位置,可以看出在距表面164 μm和256 μm處均有裂紋出現。
圖10 不同載荷條件下亞表面裂紋分布位置
由赫茲接觸理論,裂紋起源于距表面0.75b 的最大剪切應力處,其中 b 為接觸圓半徑。采用有限元軟件ABAQUS計算了Mises應力,為簡化模型便于計算,建模時將試驗裝置簡化為二維平面模型,云圖結果僅顯示截取的主滾動接觸試樣部分。模型的彈性參數與實際試樣相同,其中碳氮共滲層為239GPa,基體為208GPa;泊松比分別為0.28和0.3。模型采用四結點雙線性平面應變四邊形單元 (CPE4R)來劃分,并同時采用了減縮積分和沙漏控制。對試樣施加分別為2.0GPa和2.6GPa的載荷后,所得接觸區域的Mises應力云圖分布如圖11。當載荷為2.0GPa時,應力集中分布于滲層內部,此時最大應力位于距表面150 μm左右的范圍內,此深度與該載荷條件下亞表面裂紋出現的位置不相符。然而當載荷增大為2.6GPa時,最大應力下移至滲層與基體的交界位置,裂紋萌生位置在最大應力的范圍內。由此推測,出現上述裂紋分布情況主要還與碳氮改性硬化層的厚度有關。
圖11 不同載荷條件下試樣亞表面應力分布圖
當載荷較小時,最大應力分布于碳氮共滲層內。由于碳氮改性層內部硬度較高,相比之下過渡區處的基體材料會率先因塑性變形局域化而出現疲勞損傷。如圖12所示,亞表面微觀形貌隨距接觸表面的距離不同出現較大差異。滲層內部無典型失效特征,隨深度增加基體內部開始出現較多因塑性剪切而產生“滑移線”損傷形貌。圖12c為基體的放大形貌,可以看出這些“滑移線”平均長度為8 μm,普遍以垂直于接觸表面的方向分布。這類微觀失效形貌在所有工況條件下的失效樣中均能觀察到。在循環載荷作用下,“滑移線”會導致附近基體發生應力集中,當塑性變形超過材料的應變極限時易成為疲勞裂紋源。相應的當載荷增大至2.6GPa,最大應力分布位置距接觸表面226 μm,最大應力處的基體會因微觀缺陷如孔洞、夾雜而導致應力集中萌生微觀裂紋。由于此時碳氮共滲層與基體之間的過渡區仍處于最大剪切應力的分布范圍內,同樣會因“滑移線”而萌生裂紋。因此在大載荷工況條件下,將導致裂紋分布深度更為廣泛,在滲層過渡區和最大剪切應力分布范圍內均有裂紋出現。
圖12 碳氮共滲試樣疲勞后橫截面“滑移線”形貌圖
圖13 為碳氮共滲試樣的滾動接觸疲勞失效機理示意圖。首先,在循環載荷以及摩擦力作用下,試樣接觸表面材料晶粒細化出現白色蝕刻層。與此同時,滲層過渡區因塑性變形局域化而出現“滑移線”的損傷形貌。然后,隨著循環次數的增加,接觸表面超過疲勞極限而萌生表面裂紋,表面白色蝕刻層與基體交界處出現表面平行裂紋。當表面裂紋與層間裂紋相連時出現淺層剝落坑。淺層剝落坑使試樣在滾動接觸過程中震動加劇,促使“滑移線” 處基體演化為亞表面裂紋并向接觸表面擴展。最后,亞表面裂紋演化至接觸表面,導致試樣形成剝落坑而失效。
圖13 碳氮共滲試樣的滾動接觸疲勞失效機理示意圖
3 結論
(1)碳氮共滲工藝可提高滾動接觸疲勞性能。載荷和滑差率越大,疲勞壽命越短。碳氮共滲試樣疲勞性能的改善是表面高硬度、殘余壓應力以及殘余奧氏體的綜合作用。在滾動接觸疲勞過程中,表面材料發生由應變誘導的馬氏體相變。滲層內較高含量的殘余奧氏體在相變過程中能延緩裂紋擴展,改善表面接觸應力分布,這對于提高疲勞性能存在積極作用。
(2)碳氮共滲試樣接觸表面受高載高滑差作用易形成納米梯度結構,其中表面晶粒細化程度最為嚴重。該結構在提高表面硬度的同時也會因與基體組織的不兼容而誘發表面平行裂紋,裂紋演化至表面導致淺層剝落。
(3)亞表面裂紋是導致碳氮共滲試樣疲勞失效的主要原因,裂紋萌生位置受最大應力和滲層厚度的共同影響。亞表面裂紋擴展至表面或與表面裂紋連接,產生剝落坑失效形貌。
參考文獻: 略
免責聲明:本網站所轉載的文字、圖片與視頻資料版權歸原創作者所有,如果涉及侵權,請第一時間聯系本網刪除。
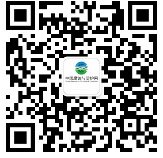
官方微信
《腐蝕與防護網電子期刊》征訂啟事
- 投稿聯系:編輯部
- 電話:010-62316606-806
- 郵箱:fsfhzy666@163.com
- 腐蝕與防護網官方QQ群:140808414