摘要
對提升鈦合金零件的疲勞強度,已有相關技術的試驗研究,但缺乏對技術的系統介紹,阻礙了該技術的產業化應用。 通過整理大量試驗數據及其結果,就激光沖擊強化對鈦合金零件的疲勞特性的影響展開分析。簡要介紹激光沖擊強化技術的發展狀況,分別從表面形貌、殘余應力、微觀組織、硬度、表面粗糙度等方面進行分析總結。結果發現,當激光脈沖能量為 7 J 時,材料塑性變形量最大;當激光功率密度為 3 GW / cm2 時,材料表面殘余壓應力值最高;當沖擊次數達到 5 次以上時, 材料表層的位錯密度不斷增大;當在工件表面覆蓋一層高強度的光滑金屬接觸膜時,材料表面粗糙度將降低。綜合數據可知激光功率密度及沖擊次數對鈦合金疲勞壽命的影響最大。整理了大量試驗數據,可為得到最佳的激光沖擊強化效果及提升疲勞壽命提供理論參考。
關鍵詞: 激光沖擊 ; 鈦合金 ; 疲勞強度 ; 表面形貌 ; 殘余應力 ; 力學性能
0 前言
鈦合金具有強度高、韌性好、抗腐蝕性好、耐高溫等特點,在航空和航天工業中的應用日益廣泛。目前,先進航空發動機中的壓氣機葉片、風扇葉片及零件設備由鈦合金制造而成,逐步實現了壓氣機鈦合金化[1]。然而,鈦合金具有耐磨性差、疲勞強度低、切削加工困難等缺陷,尤其是疲勞性能的影響大大限制了它的一系列應用。在實際工作過程中,航空發動機產生的熱應力、離心力和異物吸入等復合作用,使得鈦合金葉片發生疲勞斷裂。在過去的一些事故統計中,我國80%空軍現役飛行事故的發生與發動機葉片的疲勞斷裂有關。據報道,2014年,我國南航CZ3739航班由于壓氣機風扇的葉片斷裂導致飛機引擎在航班飛行中著火; 2015年,達美航空1288航班由于發動機葉片斷裂導致發生嚴重的事故;2018年,美國西南航空1380航班由于發動機葉片斷裂導致發動機爆炸。這三起重大事故是由葉片的疲勞斷裂引起的。為提高鈦合金構件的疲勞性能,提高其使用壽命,常采用的傳統表面強化技術有高速噴丸[2]、滾壓[3]、低塑性拋光[4]等。
高速噴丸采用高速彈丸流連續向材料表面噴射使其發生塑性變形,從而產生殘余壓應力層,能有效地改善工件的抗疲勞和抗應力腐蝕等性能[5]。然而,當零件長期處于室溫或高溫的條件下,易承受交變應力,其殘余應力會逐漸減小,組織晶粒逐漸變大,因此噴丸強化的零件在使用一段時間后,需再次進行噴丸強化后使用。滾壓強化是利用滾壓零件形成的壓力作用,使金屬表面產生加工硬化以提高零件性能、質量和使用壽命。然而,滾壓設備的問題主要在于加工時工件的尺寸穩定性不好,而且對機床的力較大,慢慢被其他設備取代。低塑性拋光是通過球形工具在工件表面自由的滾動,從而產生累積的塑性應變,從而降低工件表面粗糙度,并在工件表層產生殘余壓應力,能大幅度提高材料的疲勞強度[6]。然而,該技術工藝復雜,高強壓力會導致材料發生較大程度的扭曲變形。
激光沖擊強化技術(Laser shock processing/peening,LSP)[7],是一種將光能轉化為機械能的簡單有效的材料表面改性技術,能夠顯著改善材料表面形貌、微觀組織及殘余應力等性能,提高材料的耐磨性、耐腐蝕性和疲勞性能等[8-10]。相較于其他傳統的表面改性技術,激光沖擊強化技術因具有強化效率高、可控性良好、被處理工件表面完整性好等特點成為表面改性領域的研究熱點。激光沖擊強化技術基本原理如圖1所示,一束強短脈沖激光束作用于工件表面的吸收層,當吸收層充分吸收了激光能量時,將在短時間內汽化電離成等離子體向外噴射。由于在吸收層上會覆蓋一層約束層,約束層會限制等離子體的膨脹噴射,使得等離子體壓力迅速升高,產生超強沖擊波。沖擊波的壓力高達數GPa,遠高于工件材料的屈服強度,使材料的表層產生高幅值殘余壓應力,并使材料表面產生塑性變形,從而改善材料的疲勞性能等。
圖1 激光沖擊強化原理圖[11]
1 激光沖擊強化技術的發展
20世紀60年代,NEUMAN等[12]首次發現脈沖激光可以誘導形成沖擊波。1972年,美國Battelle Columbus實驗室成功研制出大功率激光沖擊試驗設備,并利用沖擊波沖擊鋁合金試樣,發現激光沖擊強化可以改變材料的微觀組織,提高力學性能,展現了激光沖擊強化技術的前景[13-14]。1978年, FORD等[15]與美國空軍實驗室共同進行研究,發現激光沖擊強化可以有效地控制材料裂紋擴展的速度,提高材料使用壽命。同年,法國FABBRO和PEYRE等[16-17]對激光沖擊強化技術進行比較全面的研究,并提出約束模式下激光沖擊波峰值壓力的估算式。1990年,GREVEY等[18]進行激光沖擊誘導合金鋼中馬氏體相變的研究。FORGET等[19]研究發現激光沖擊強化在鎳基合金內部誘導壓應力,能夠提高材料的抗磨損性能和疲勞壽命。
1960年,我國曾提出激光沖擊強化的概念,但受到國內技術落后和試驗設備缺乏的限制,并無實質性進展。2001年,江蘇大學的張永康和周建忠等[20-21]首次提出激光沖擊成形的新概念,并依照此理論進行大量試驗研究。2008年,在西安我國建立了第一條激光沖擊強化實際應用的生產線,并不斷在航空發動機等零部件上展開應用[22]。2010年,劉會霞等[23-24]結合激光沖擊成型技術提出基于激光沖擊波的高速沖裁方法,并結合試驗與有限元模擬分析激光沖擊的工藝。2010年,SEALY等[25]利用激光沖擊波技術,在Mg-Ca表面成功制備出微凹坑,以此獲得織構的表面。隨后,DAI等[26-27]在原有激光沖擊波技術的應用上進行改進,提出激光沖擊波微壓印等技術,并展開大量試驗研究。2011年,中國科學院沈陽自動化研究所[28-30]研制了我國首臺整體葉盤激光沖擊強化系統,進一步突破了激光沖擊強化的實際應用限制,可將航空發動機葉片的疲勞壽命提高達6倍以上。2014年,江蘇大學通過對激光沖擊強化的深入研究進行試驗,在鋁箔表面打出呈規則排列的凹坑,將激光沖擊強化成功引入到微機電系統器件領域的應用[31]。隨后,溫州大學的陳希章等[32-34]利用激光沖擊強化技術,在不同材料表面進行試驗,發現微觀組織和殘余應力是影響焊接效果的兩個關鍵因素,證明了激光沖擊加工是一種很有潛力的提高機械性能的方法。
2 激光沖擊強化對鈦合金疲勞性能的影響因素
機械零件在交變載荷的作用下,雖然應力水平低于材料的屈服極限,但經過長時間的應力反復循環作用后,也會發生突然脆性斷裂,這種現象叫做疲勞。疲勞裂紋和疲勞斷裂經常發生在零件的使用過程中,目前常用激光沖擊強化技術提高金屬零件的疲勞性能。激光沖擊強化會引起鈦合金表面形貌、殘余應力、微觀組織、硬度、表面粗糙度等變化,這些力學性能可以有效地抑制疲勞裂紋的萌生,提升疲勞極限進而提升激光沖擊強化的效果。
2.1 表面形貌
汪軍[35]深入研究激光沖擊強化過程中不同吸收層對TC4合金板料表面形貌的影響。試驗發現,激光沖擊強化處理后在吸收層為鋁箔和黑膠帶上存在激光燒蝕的痕跡,而在激光沖擊后除掉吸收層并用無水丙酮清洗后的試樣表面無痕跡,結果說明用鋁箔和黑膠帶作為吸收層具有良好的保護作用。在激光功率密度、光斑大小直徑、搭接率等因素均相同的情況下,試驗證明,黑膠帶相比鋁箔作為吸收層,材料表面經激光沖擊強化后會產生更大的塑性變形進而導致殘余應力變大,可更有效地提高試樣疲勞壽命。王學德等[36]將TC6鈦合金進行熱處理后隨爐冷卻,試樣經過雙面約束激光沖擊強化之后平直無彎曲,表面可以觀察到分布均勻且連續光滑的微凹坑,結果表明激光沖擊強化技術會使鈦合金試樣發生塑性變形,隨著塑性變形的增大,材料疲勞極限也增大。
孫汝劍等[37]通過改變脈沖能量的大小對TC17合金進行激光沖擊強化試驗。圖2所示為TC17鈦合金激光沖擊強化后的三維形貌,由圖可知,當脈沖能量為3J時,試樣塑性變形量最小,當脈沖能量為7J時,試樣塑性變形量最大。結果表明,不同的激光沖擊能量會使試樣的塑性變形發生明顯變化,且隨著激光脈沖能量的增加,試樣表面的塑性變形增大,但由于金屬材料在最初階段的塑性變形要比后續任何階段的塑性變形都容易,所以塑性變形的增加量會慢慢變少。
圖2 TC17鈦合金激光沖擊強化后的三維形貌[37]
由此看出,激光沖擊強化鈦合金后發生塑性變形,當激光沖擊強化時,吸收層材質的不同、激光脈沖能量的變化、材料熱處理工藝的不同等會導致鈦合金表面形貌產生較為明顯的變化。當激光脈沖能量達到7J時,試樣塑性變形量最大,可以達到一個較大的極限疲勞強度。
2.2 殘余應力
何衛鋒等[38]對鈦合金不同激光沖擊次數下的殘余應力分布進行試驗分析。圖3所示為不同次數沖擊下TC17鈦合金的殘余應力分布圖,結果表明,由一次沖擊到三次沖擊要比由三次沖擊到五次沖擊后產生的殘余應力值增加幅度要高,隨著沖擊次數的增加,材料發生塑性變形,其殘余壓應力的深度變化呈非線性增加。
圖3 不同次數沖擊下TC17鈦合金的殘余應力分布[38]
除不同沖擊次數會影響鈦合金的殘余應力外,激光功率密度的大小對鈦合金的殘余應力值也會產生影響。FABBRO等[16, 39]認為,在試驗中選取合適的激光功率密度,使誘導形成的高強沖擊波峰值壓力介于2~2.5倍雨貢紐彈性極限內,在此條件下能獲得較好的殘余壓應力值。張永康等[40]進行試驗結合有限元分析,對激光沖擊強化TC4鈦合金的殘余應力場分布進行分析,系統模擬不同功率密度下, 激光沖擊過程中材料殘余應力場的分布。結果表明,當沖擊波峰值壓力達到并大于材料雨貢紐彈性極限時,材料表層將產生殘余壓應力,并且殘余壓應力越大,材料的疲勞極限越高。楊豐槐[41]研究發現,激光脈沖寬度、光斑直徑和光斑形狀都會影響殘余應力的大小。從仿真結果來看,激光脈沖寬度越大,表面形成的殘余壓應力越大,但在實際生產加工過程中,考慮到脈沖寬度的不斷增大會導致零部件的表面過熱發生燒蝕,從而材料表面的殘余壓應力會減小,起到了相反的效果,因此需要選擇合理的激光沖擊強化工藝參數。
FABBRO等提出激光沖擊強化在材料表層誘導的殘余壓應力與激光的功率密度成正比關系,何衛鋒等[42]以TC6鈦合金為研究對象,分別采用2.5、 3、4、5GW/cm2 這4種功率密度對試樣進行激光沖擊強化試驗,圖4為不同功率密度下沖擊后沿深度方向的殘余應力分布,結果表明,當功率密度為3GW/cm2 時,表面殘余壓應力值最高,并且沖擊影響層的深度更深,表面壓應力值在深度為0.1mm時達到–690MPa。由殘余應力而引起的材料疲勞極限的變化
為:
(1)
圖4 不同功率密度下激光沖擊試樣沿深度方向的殘余應力分布[42]
由式(1)可知,激光沖擊后試樣表面形成的殘余壓應力會使材料的疲勞極限提高,統計發現,當功率密度為3GW/cm2 時表面殘余壓應力值最高,可以有效地提高鈦合金材料的疲勞壽命。
2.3 微觀組織
朱穎等[43]采用不同沖擊次數對TA15鈦合金進行激光沖擊強化試驗,研究不同沖擊次數對材料微觀組織的影響。對比未經激光沖擊和經過1次激光沖擊后的晶粒狀態的TEM像,如圖5所示,1次激光沖擊后的TA15合金晶粒明顯變細且分布均勻,較未經過激光沖擊前,試樣的位錯密度也有所提高,但也只是出現在少量的 β 相附近;2次激光沖擊后TA15合金在 α 相和 β 相的位錯都十分密集,且可以看出有位錯塞積、增殖、纏結等現象。昝垚旭等[44]采用掃描電鏡對激光沖擊Ti834合金顯微組織進行了研究。結果表明,當Ti834合金經過1次沖擊后,試樣表層位錯密度增加,組織相界處有位錯塞積,經過2次沖擊后,試樣的位錯密度較第一次有更明顯的增加,相界處出現大規模的位錯積塞,沖擊強化效果明顯。鈦合金經過激光沖擊強化后發生塑性變形,使其微觀組織結構也隨之發生變化,從而造成一定程度疲勞性能的改變。
王學德等[45]利用激光沖擊強化技術對TC11合金進行處理,分析了TC11合金激光沖擊前后微觀組織變化,圖6a中可以看出TC11合金原組織的相界非常清晰,圖6b、6c、6d分別是激光沖擊1、3、5次后的微觀組織。圖6b中發現存在大量的高密度位錯和亞晶結構;圖6c和6d中出現了納米層晶粒且納米晶隨著激光沖擊次數的增加變得更細小、均勻。結果表明,表面微觀組織在不同沖擊次數下呈現出位錯密度-位錯胞-納米晶的細化過程,這是因為晶粒細化后能夠使滑移形變抗力得到提升,循環滑移帶構建與擴散得到抑制,裂紋蔓延的晶界阻抗得到提高,而且會改變裂紋方向,提升疲勞強度;晶粒極細納米表層中的問題較少,不易發生裂紋; 納米層內嚴重的塑性形變部分及其高密度位錯,則使疲勞裂紋的生成與蔓延得到有效控制。顯微組織對材料疲勞性能的影響,除了與各材料組織自身的力學性能特征有關以外,還與材料組織晶粒度的分布特征有關,細化組織晶粒可提高材料的疲勞強度。位錯密度由 ρ 表示:
(2)
圖5 TA15合金TEM像[43]
圖6 不同沖擊次數下表面透射電鏡圖和衍射花樣[45]
由式(2)可知,位錯密度 ρ 隨著壓力√p 的變化而變化,激光功率密度增加,形成的激光沖擊波壓力越大,進而導致材料表層的位錯密度越大。對于鈦合金材料,位錯強化導致的強度增量與材料中位錯密度的平方根呈正比,位錯密度增大,微觀組織越細,材料的疲勞抗性提高越明顯。
2.4 顯微硬度
朱穎等[43]對兼有 α 型和 α+β 型的TA15合金進行激光沖擊強化,不同沖擊次數下TA15的表面顯微硬度變化趨勢如圖7所示,試驗結果表明,激光沖擊次數的增加影響試樣顯微硬度的增加,且2次沖擊后,顯微硬度有明顯提升,說明激光沖擊強化可以有效提高材料的表面顯微硬度,進而提升鈦合金的疲勞極限。周建忠等[46]研究了經激光沖擊強化后TC6鈦合金表面強度的變化。不同功率密度下激光沖擊強化的試樣深度方向顯微硬度分布如圖8所示,可以看出,試樣的顯微硬度隨著功率密度的增加而增大。高功率密度的激光束沖擊鈦合金,沖擊波從材料表面到內部的傳播過程中會發生衰減,到一定深度后硬度不再增強[47]。羅學昆等[48]對激光沖擊強化處理Ti-6Al-4V合金的試驗進行研究,主要探討激光功率密度的不同對Ti-6Al-4V合金顯微硬度的影響。圖9是激光沖擊強化前后Ti-6Al-4V合金距表面不同厚度層的顯微硬度分布。由圖可知,經激光沖擊強化后的試樣顯微硬度明顯高于未經激光沖擊強化的顯微硬度,這說明激光沖擊強化技術能夠提高Ti-6Al-4V合金的硬度。結果表明,激光功率密度越大,激光沖擊強化后試樣表面的硬度值越高,在107 循環周期下,原材料的疲勞極限較激光沖擊強后后提升了33.3%,可知激光沖擊強化技術可以有效地提高Ti-6Al-4V合金的疲勞極限。據研究表明,激光沖擊強化后,材料位錯密度不斷增加,使得被沖擊區域的硬度也隨之增大,這些高密度位錯會形成大量的位錯胞,可以抑制位錯運動的擴展,從而提高材料的硬度。由材料微觀組織分布可知,位錯密度越大,顯微硬度越大,材料的抗疲勞性能越好。
圖7 不同沖擊次數下TA15的表面顯微硬度變化趨勢[43]
圖8 顯微硬度分布圖[47]
圖9 激光沖擊處理前后Ti-6Al-4V合金距表面不同厚度層的顯微硬度分布[48]
2.5 表面粗糙度
表面粗糙度是材料表面完整性的一個重要指標,對材料的疲勞性能有著很大的影響,進而會影響零部件使用壽命。MAAWAD等的研究表明,隨著表面粗糙度的增加,激光沖擊強化后Ti-54M鈦合金的疲勞強度甚至從650MPa降低到了550MPa[49],SUN等的研究表明,對激光沖擊強化的試樣進行后處理拋光工藝后,其疲勞壽命相較未拋光前比基體提高約6.7倍[50],但多數是在常溫條件下進行激光沖擊強化試驗的。任旭東等[51]研究中高溫條件下激光沖擊強化對Ti-6Al-4V鈦合金表面完整性的影響,如圖10所示,隨著溫度的不斷升高,在兩種狀態下,材料表面粗糙度均逐漸增大,且相比于未激光沖擊強化的試樣,激光沖擊強化后試樣的表面變得更加粗糙。材料表面的粗糙度值變大,表面殘余壓應力值變小,從而縮短零部件的疲勞壽命[52]。楊豐槐等[41]應用有限元模擬分析計算激光沖擊TC4合金的表面粗糙度,發現激光沖擊次數、沖擊峰值壓力、光斑形狀這些參數會對鈦合金的表面粗糙度產生影響。模擬結果表明,當激光沖擊次數和峰值壓力增加時,材料的表面粗糙度逐漸增大;當其他參數均相同,光斑形狀不同時,圓形光斑沖擊后材料的表面粗糙度小于方形光斑沖擊后材料的表面粗糙度。吳俊峰等[53]試驗對比分析了不同強化工藝下 β 鍛TC17鈦合金的表面粗糙度變化規律,如表1所示,激光沖擊強化后試樣的表面粗糙度比噴丸強化和復合強化后的表面粗糙度低。
圖10 不同溫度下Ti-6Al-4V合金的表面粗糙度[51]
表1 不同強化工藝TC17合金表面粗糙度[53]
OCANA等[54]采用鋁箔作為吸收層,發現激光沖擊強化使Ti-6Al-4V合金的表面粗糙度從0.1 μm增大到0.82 μm;YELLA等[55]發現,激光沖擊強化采用黏性膠帶獲得的表面粗糙度遠小于采用黑漆獲得的表面粗糙度;SALIMIANRIZI等[56]發現,通過改變光斑的搭接方式和搭接率,可以有效降低材料表面粗糙度;江蘇大學戴峰澤等[57]嘗試在激光沖擊強化中工件表面覆蓋一層高強度的光滑金屬接觸膜,降低表面粗糙度。不同的表面粗糙程度會對材料產生不同的疲勞性能影響,材料疲勞強度隨其表面粗糙度的提升而降低,因此降低材料的表面粗糙度能有效提高其疲勞壽命。
表面粗糙度對疲勞強度的影響用表面加工系數 β 來表示:
(3)
式中,σ β 為某種表面狀態下標準光滑試樣的疲勞極限,σ β 0 為磨光標準光滑試樣的疲勞極限。可見,激光沖擊強化可以有效地提高疲勞強度。以此形式看來,鈦合金試樣表面粗糙度越大,對疲勞強度的降低影響就越大。
激光沖擊強化技術可以顯著改變鈦合金的表面形貌、微觀組織,有效提高材料的殘余應力和硬度,降低材料的表面粗糙度,這些力學性能的變化對鈦合金疲勞壽命起著重要的影響,其中殘余應力的大小起著關鍵的作用,殘余應力的增大導致材料硬度增大,其疲勞極限值也增大。
3 結論
激光沖擊強化相比傳統強化工藝效果更佳、可操控性強、適用性好,在航空航天行業中得到了越來越廣泛的應用與研究,對提升部件疲勞性能和延長材料使用壽命具有重要意義。首先介紹了激光沖擊強化技術的研究背景和發展概況,分別從激光沖擊強化鈦合金表面形貌、殘余應力、微觀組織、硬度、表面粗糙度等力學性能的變化對鈦合金疲勞性能的影響進行分析與總結,并對其發展前景進行了展望。
(1)激光工藝參數是影響激光沖擊強化效果的重要因素,選取合適的激光功率密度、不同沖擊次數、光斑形狀與大小等,可以有效地改善鈦合金的殘余應力分布,提高材料疲勞性能。然而目前對于鈦合金表面改性技術的研究不多,很多是基于單一工藝參數進行試驗對比,無法全面概括激光沖擊強化鈦合金的最優參數。未來研究,可以將不同激光工藝參數結合起來分析,有利于總結出更能顯著提高鈦合金強化效果的工藝參數。
(2)激光光斑的形狀、大小以及搭接率均會影響鈦合金表面性能,目前激光頭只能做到一種光斑沖擊,在試樣不變的情況下,激光頭光斑形狀與大小的切換可以有效地提高沖擊試驗的效率,得到最有效的強化效果。目前的激光器存在脈沖能量較低、光斑質量差、重復率低等問題,極大限制了激光沖擊強化技術的發展,未來新型激光器的開發,應著重于研究高質量激光束,抑制自發輻射光,提高散熱性能等。
(3)目前針對不同型號的鈦合金,主要以激光沖擊試驗為主,未來可以大幅度加入模擬仿真數據,不同型號的鈦合金制定不同密度的網格數,更加有利于驗證激光沖擊強化對鈦合金表面改性技術的研究。
參考文獻: 略
免責聲明:本網站所轉載的文字、圖片與視頻資料版權歸原創作者所有,如果涉及侵權,請第一時間聯系本網刪除。
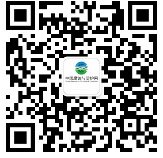
官方微信
《腐蝕與防護網電子期刊》征訂啟事
- 投稿聯系:編輯部
- 電話:010-62316606-806
- 郵箱:fsfhzy666@163.com
- 腐蝕與防護網官方QQ群:140808414