NH4H2PO4作為一種高效的復(fù)合肥料和工業(yè)原料,市場(chǎng)前景廣闊。目前,NH4H2PO4主要是以熱法磷酸或濕法磷酸與氨反應(yīng)制得,其生產(chǎn)過(guò)程中會(huì)產(chǎn)生大量的低溫余熱[1,2]。低溫余熱資源回收利用的途徑主要為用作一般加熱熱源,被熱泵回收利用,低溫余熱發(fā)電[3]。隨著我國(guó)對(duì)低溫余熱發(fā)電的大力支持,再加上其自身具有顯著的經(jīng)濟(jì)效益和社會(huì)效益,低溫余熱發(fā)電受到諸多青睞[4]。
低溫余熱發(fā)電技術(shù)的核心原理為有機(jī)朗肯循環(huán) (ORC),低溫余熱發(fā)電裝置主要由循環(huán)泵、蒸發(fā)器、汽輪機(jī)、冷凝器四部分組成[3]。蒸汽在汽輪機(jī)中做完功后,其壓力和溫度不斷降低,并在汽輪機(jī)轉(zhuǎn)動(dòng)部件 (如轉(zhuǎn)子) 表面形成較薄的液膜,由于低溫余熱發(fā)電裝置中無(wú)除氧、除鹽等設(shè)施,蒸汽中氧氣、腐蝕性雜質(zhì)鹽等又會(huì)溶于薄液膜中而形成強(qiáng)電解質(zhì)溶液,誘發(fā)轉(zhuǎn)子材料發(fā)生腐蝕破壞,給低溫余熱發(fā)電裝置的運(yùn)行帶來(lái)安全隱患[4]。
目前,關(guān)于轉(zhuǎn)子材料的腐蝕研究,更多集中于核電或火力發(fā)電汽輪機(jī)低壓轉(zhuǎn)子材料的腐蝕行為研究[5-12]。Luo等[5-7]利用U型試樣研究了核電汽輪機(jī)焊接轉(zhuǎn)子25Cr2Ni2MoV焊接接頭在180 ℃、3.5% NaCl溶液中的腐蝕行為,研究表明,焊縫區(qū)優(yōu)先產(chǎn)生大量夾雜物誘發(fā)的點(diǎn)蝕坑,此外,焊接接頭的母材、焊縫、熱影響區(qū)存在電勢(shì)差,并誘發(fā)電偶腐蝕。歐陽(yáng)玉清等[8]研究了溫度對(duì)核電汽輪機(jī)焊接轉(zhuǎn)子25Cr2Ni2MoV焊接接頭電偶腐蝕的影響,研究表明,隨著溫度升高,材料電偶腐蝕效應(yīng)增強(qiáng)。Maeng等[9]通過(guò)恒速率拉伸實(shí)驗(yàn)研究了高溫水中醋酸對(duì)火力發(fā)電汽輪機(jī)低壓轉(zhuǎn)子材料3.5NiCrMoV應(yīng)力腐蝕行為的影響,研究表明,隨著醋酸濃度增大,材料的應(yīng)力腐蝕敏感性增大,此外,高濃度的醋酸也會(huì)造成裂紋尖端鈍化。與核電或火力發(fā)電汽輪機(jī)所用的蒸汽不同,利用NH4H2PO4生產(chǎn)行業(yè)產(chǎn)生的低溫余熱資源發(fā)電的裝置所用蒸汽溫度較低、壓力較小,造成轉(zhuǎn)子表面更容易形成一層薄液膜。正常情況下,核電或火力發(fā)電汽輪機(jī)中蒸汽的含氧量限制在5 10-3 mg/L以下,而啟停機(jī)時(shí),從冷凝器進(jìn)入的氧含量增大,最高氧含量可達(dá)20 mg/L,而低溫余熱發(fā)電裝置中無(wú)除氧設(shè)施,造成了其蒸汽中的氧含量遠(yuǎn)高于核電或火力發(fā)電汽輪機(jī)所用的蒸汽[13]。低溫余熱發(fā)電裝置中也無(wú)除鹽設(shè)施,致使其蒸汽中還含有部分殘留的NH4H2PO4,NH4H2PO4易溶于水,形成酸性水溶液。然而,汽輪機(jī)轉(zhuǎn)子常見材料在含NH4H2PO4酸性溶液條件下NH4H2PO4溶液濃度等變化對(duì)材料腐蝕行為的影響規(guī)律及其機(jī)理鮮有報(bào)道,即NH4H2PO4溶液濃度、溶解氧、溫度等腐蝕因素影響的基礎(chǔ)研究尚未系統(tǒng)開展。
本文以2Cr-1Ni-1.2Mo-0.2V鋼作為研究對(duì)象,研究結(jié)果可為利用NH4H2PO4生產(chǎn)行業(yè)產(chǎn)生的低溫余熱資源發(fā)電的裝置開發(fā)及其防護(hù)提供理論依據(jù)和數(shù)據(jù)支持。
1 實(shí)驗(yàn)方法
實(shí)驗(yàn)用材為2Cr-1Ni-1.2Mo-0.2V鋼 (1R鋼),主要化學(xué)成分 (質(zhì)量分?jǐn)?shù),%) 為:C 0.32,Si 0.02,Mn 0.6,S 0.0059,P 0.0015,Cr 2.23,Mo 1.17,Ni 0.95,V 0.22,Al 0.0058,Cu 0.048,As 0.006,Fe余量。1R鋼的組織以回火索氏體為主,同時(shí)還有少量塊狀的鐵素體組織。
實(shí)驗(yàn)用溶液為不同濃度的NH4H2PO4溶液,即純度為99%的NH4H2PO4藥劑與去離子水混合而成的0 (純?nèi)ルx子水)、1、30、60、90、120 mmol/L NH4H2PO4溶液。
利用線切割的方式將實(shí)驗(yàn)用材1R鋼加工成所需的試樣,失重實(shí)驗(yàn)試樣規(guī)格為50 mm×20 mm×4 mm,XPS試樣規(guī)格為5 mm×5 mm×2 mm,電化學(xué)實(shí)驗(yàn)試樣規(guī)格為10 mm×10 mm×10 mm。試樣加工后,認(rèn)真清洗試樣表面的油污和鐵銹,電化學(xué)實(shí)驗(yàn)試樣采用環(huán)氧樹脂對(duì)其進(jìn)行真空冷鑲。隨后試樣表面逐級(jí)打磨至2000#水磨砂紙并最終拋光,拋光后,試樣在無(wú)水乙醇中超聲處理5 min,以去除試樣表面殘留的SiC顆粒,然后用去離子水清洗試樣表面,無(wú)水乙醇脫除殘留水分、冷風(fēng)吹干,最后放入干燥器中待用,其中失重實(shí)驗(yàn)試樣在干燥器中靜置24 h后稱重 (精確至0.1 mg)。去除失重實(shí)驗(yàn)試樣腐蝕產(chǎn)物的酸洗液由500 mL鹽酸 (HCl, =1.19 g/mL)+5 g 1,3-二丁基-2-硫脲+500 mL去離子水配置而成。酸洗液去除腐蝕產(chǎn)物后,用去離子水、無(wú)水乙醇清洗試樣,冷風(fēng)快速吹干,在干燥皿中靜置24 h后稱重 (精確至0.1 mg),并用 公式 (1) 計(jì)算材料腐蝕速率[14]。
(1)
其中,R均為腐蝕速率,g·m-2·h-1;M和Mt是實(shí)驗(yàn)前和酸洗后的質(zhì)量,g;S是試樣表面積,m2;T是實(shí)驗(yàn)時(shí)間,h。
電化學(xué)實(shí)驗(yàn)在PARSTAT4000型電化學(xué)工作站上進(jìn)行,三電極體系,1R鋼為工作電極,鉑片為輔助電極,飽和甘汞電極 (SCE) 為參比電極,測(cè)試溫度為(25±2) ℃。開始測(cè)試前,試樣需在0 (純?nèi)ルx子水)、1、30、60、90、120 mmol/L NH4H2PO4溶液中浸泡20 h,待試樣表面穩(wěn)定后再進(jìn)行測(cè)試[15]。先測(cè)900 s開路電位,開路電位穩(wěn)定后再進(jìn)行相應(yīng)的電化學(xué)測(cè)試,其中極化掃描在開路電位±0.25 V的范圍內(nèi)進(jìn)行,掃速為0.1666 mV/s;電化學(xué)阻抗譜 (EIS) 測(cè)試是在穩(wěn)定的開路處對(duì)工作電極施加一個(gè)±5 mV的交流電壓擾動(dòng)下進(jìn)行的,測(cè)試頻率范圍為105~10-2 Hz,并使用ZSimDemo軟件對(duì)其數(shù)據(jù)進(jìn)行擬合分析。
通過(guò)失重法測(cè)量1R鋼在不同濃度NH4H2PO4溶液中的腐蝕速率,利用LEXT-OLS5000激光共聚焦顯微鏡 (CLSM) 分析材料表面腐蝕形貌;選取在120 mmol/L NH4H2PO4溶液中浸泡20 h后的試樣,通過(guò)場(chǎng)發(fā)射掃描電鏡 (FE-SEM,Thermo Fisher APREO) 及其附帶的Quantax400能譜儀 (EDS) 分析內(nèi)外層腐蝕產(chǎn)物形貌及其合金元素分布;在120 mmol/L NH4H2PO4溶液中浸泡20 h后的試樣表面刮取腐蝕產(chǎn)物粉末,使用X射線衍射儀 (XRD,Bruker D8 Advance) 對(duì)其進(jìn)行物相分析,XRD測(cè)試采用Co靶,Kα波長(zhǎng)0.15406 nm,管電壓40 kV,管電流為40 mA,掃描速度為20°/min,衍射角掃描范圍為10°~80°,使用MDI Jade6軟件處理數(shù)據(jù);選取在30、60、90、120 mmol/L NH4H2PO4溶液中浸泡20 h后的試樣,用去離子水去除表面疏松的腐蝕產(chǎn)物,通過(guò)X射線光電子能譜儀 (XPS,AXIS ULTRADLD) 分析與1R鋼基體結(jié)合緊固的腐蝕產(chǎn)物組成,XPS測(cè)試所用光源為單色Al (=1486.6 eV),測(cè)試深度約5 nm,收集Fe 2p、Cr 2p、Mo 3d等能譜圖,通過(guò)C 1s (284.6 eV) 荷電校正后,采用XPS PEAK41軟件處理數(shù)據(jù)。
2 結(jié)果與討論
2.1 腐蝕速率
圖1為1R鋼在0 (去離子水)、1、30、60、90、120 mmol/L NH4H2PO4溶液中浸泡20 h的平均腐蝕速率。可見,1R鋼在去離子水中的腐蝕速率最小,約為0.017 g·m-2·h-1,在1 mmol/L NH4H2PO4溶液的腐蝕速率約為0.152 g·m-2·h-1,其值比1R鋼在去離子水中的腐蝕速率大7.973倍。繼續(xù)增大NH4H2PO4溶液的濃度,發(fā)現(xiàn)1R鋼的腐蝕速率也隨之增大。1~30、30~60、60~90、90~120 mmol/L NH4H2PO4溶液對(duì)應(yīng)的1R鋼的腐蝕速率相對(duì)于NH4H2PO4溶液濃度的導(dǎo)數(shù)分別約為0.001、0.002、0.003、0.001 L·m-2·h-1 mmol-1,即隨著NH4H2PO4溶液濃度的增大,1R鋼的腐蝕速率先快速增大后緩慢增大。
圖1 1R鋼在不同濃度NH4H2PO4溶液中浸泡20 h的平均腐蝕速率
2.2 腐蝕形貌及成分分析
圖2為1R鋼在0 (去離子水)、1、30、60、90、120 mmol/L NH4H2PO4溶液中浸泡20 h后的腐蝕形貌,圖2中所選區(qū)域的三維形貌見圖3。可見,1R鋼在去離子水和1 mmol/L NH4H2PO4溶液中浸泡20 h后,鋼基體表面均出現(xiàn)點(diǎn)蝕坑 (圖2a2和b2),從在這兩種溶液中浸泡后的試樣表面隨機(jī)選取2個(gè)點(diǎn)蝕坑,用激光共聚焦顯微鏡獲取其三維形貌 (見圖4a和b),可見1R鋼在去離子水中浸泡后而生成的點(diǎn)蝕坑孔徑和孔深分別為72.9和11.1 μm,而1R鋼在1 mmol/L NH4H2PO4溶液中浸泡后生成的點(diǎn)蝕坑孔徑和孔深分別73.5和3.1 μm,可見加入少量的NH4H2PO4,可明顯抑制點(diǎn)蝕坑向縱向發(fā)展。
圖2 1R鋼在不同濃度NH4H2PO4溶液中浸泡20 h的表面腐蝕形貌
圖3 圖2中所選區(qū)域的三維形貌
圖4 在120 mmol/L NH4H2PO4溶液中浸泡20 h后的1R鋼試樣表面微觀形貌
將1R鋼放入1 mmol/L NH4H2PO4溶液中浸泡20 h,發(fā)現(xiàn)材料表面被部分黃色腐蝕產(chǎn)物覆蓋,覆蓋度約15% (圖2b1)。當(dāng)NH4H2PO4溶液濃度大于或等于30 mmol/L時(shí),1R鋼表面均被黃色的腐蝕產(chǎn)物完全覆蓋 (圖2c1~f1)。利用激光共聚焦顯微鏡獲取1R鋼在30、60、90、120 mmol/L NH4H2PO4溶液中浸泡20 h后的表面三維形貌 (圖3c~f),可見材料表面的最大高度差分別為26.9、20.1、17.2和15.8 μm,說(shuō)明隨著NH4H2PO4溶液濃度的增大,材料表面起伏程度逐漸減小。表1為1R鋼在30、60、90、120 mmol/L NH4H2PO4溶液中浸泡20 h后的表面粗糙度參數(shù),可見表面粗糙度參數(shù)隨NH4H2PO4溶液濃度的增大而減小,這與上述表面起伏程度分析結(jié)果一致。隨著表面粗糙度的減小,表面積比參數(shù)也在減小,表明材料與腐蝕介質(zhì)接觸的有效面積減小,此結(jié)果會(huì)抑制材料腐蝕速率增大[16]。
表1 1R鋼在30、60、90和120 mmol/L NH4H2PO4溶液中浸泡20 h后的表面粗糙度參數(shù)
1R鋼在30~120 mmol/L NH4H2PO4溶液中浸泡20 h后其表面覆蓋的黃色的腐蝕產(chǎn)物較為疏松,用鑷子輕輕剝落這些黃色的腐蝕產(chǎn)物,便可看到內(nèi)部黑色的腐蝕產(chǎn)物。利用激光共聚焦顯微鏡測(cè)得剝落區(qū)相較于未剝落區(qū)的高度,本文將其高度近似等價(jià)于材料表面覆蓋的腐蝕產(chǎn)物膜厚度,表明1R鋼在30、60、90、120 mmol/L NH4H2PO4溶液中浸泡20 h后其表面覆蓋的厚度分別為8.7、10.6、14.8和18.6 μm,即隨著NH4H2PO4溶液濃度的增大,1R鋼表面覆蓋的腐蝕產(chǎn)物逐漸增厚。去除腐蝕產(chǎn)物膜后,在30、60、90、120 mmol/L NH4H2PO4溶液中浸泡20 h后的1R鋼基體均光滑平整,均未出現(xiàn)局部腐蝕,材料腐蝕特征為均勻腐蝕 (圖2c2~f2)。
為驗(yàn)證1R鋼在30~120 mmol/L NH4H2PO4溶液中浸泡20 h后其表面形成的腐蝕產(chǎn)物膜為雙層結(jié)構(gòu),本文選取在120 mmol/L NH4H2PO4溶液中浸泡20 h后的1R鋼試樣,其表面微觀形貌見圖4。可見1R鋼試樣表面腐蝕產(chǎn)物膜為雙層結(jié)構(gòu),外層膜較為疏松 (圖4a),利用膠布將外層腐蝕產(chǎn)物膜輕輕粘除,可觀察到內(nèi)層腐蝕產(chǎn)物膜 (圖4b),內(nèi)層腐蝕產(chǎn)物膜較薄,可看到膜層下方鋼基體晶界,但內(nèi)層膜致密度高于外層膜[17]。
為了進(jìn)一步分析在120 mmol/L NH4H2PO4溶液中浸泡20 h后的1R鋼試樣表面內(nèi)外層腐蝕產(chǎn)物膜的差異性,分別對(duì)內(nèi)外層腐蝕產(chǎn)物膜進(jìn)行EDS分析。由表2中EDS結(jié)果可知,外層腐蝕產(chǎn)物膜主要由O、P和Fe構(gòu)成,Fe/P/O原子比為1.03∶1∶5.85,Fe含量為31.37% (質(zhì)量分?jǐn)?shù)),可推測(cè)外層腐蝕產(chǎn)物膜主要為鋼基體溶解生成的Fe2+及Fe3+ (溶液中的O將鋼基體溶解生成的Fe2+氧化為Fe3+) 與溶液中的陰離子 (如PO43-) 結(jié)合而形成的疏松膜層,再結(jié)合外層腐蝕產(chǎn)物膜中Fe/P/O原子比為1.03∶1∶5.85,說(shuō)明該腐蝕產(chǎn)物膜層可能為一個(gè)FePO4和Fe3(PO4)2混合的膜層[18]。內(nèi)層腐蝕產(chǎn)物主要由Fe、Cr、Mo、O和P構(gòu)成,Fe/Cr/Mo原子比為101.95∶3.24∶1,Fe含量為88.70%,內(nèi)層腐蝕產(chǎn)物中Fe含量約為外層腐蝕產(chǎn)物膜中Fe含量的2.83倍;P/O原子比為1∶10.37,可推測(cè)內(nèi)層腐蝕產(chǎn)物膜主要為鋼基體與溶液中的O反應(yīng)而生成的氧化物膜層[17]。
表2 在120 mmol/L NH4H2PO4溶液中浸泡20 h后的1R鋼試樣表面腐蝕產(chǎn)物EDS分析
為證實(shí)上述猜想,本文對(duì)在120 mmol/L NH4H2PO4溶液中浸泡20 h后的1R鋼表面生成的腐蝕產(chǎn)物進(jìn)行XRD分析 (圖5)。由圖可知,有明顯的Fe3(PO4)2·8H2O衍射峰,該結(jié)果表明,腐蝕產(chǎn)物的主要成分有Fe3(PO4)2,反應(yīng)過(guò)程中,鋼基體溶解生成的Fe2+與NH4H2PO4分解而成的PO43-結(jié)合并沉積在鋼基體上[18]。腐蝕產(chǎn)物的XRD圖譜也顯現(xiàn)出FePO4、Fe3O4衍射峰,結(jié)果表明,鋼基體溶解生成的Fe2+被溶液中的溶解氧氧化為Fe3+,該Fe3+與NH4H2PO4分解而成的PO43-結(jié)合并沉積在鋼基體上,另外,鋼基體與溶液中的O反應(yīng)而生成FePO4。結(jié)合圖4,5和表2可知,1R鋼在120 mmol/L NH4H2PO4溶液中浸泡20 h后形成的腐蝕產(chǎn)物膜為雙層結(jié)構(gòu),外層腐蝕產(chǎn)物膜主要由Fe3(PO4)2、FePO4構(gòu)成,內(nèi)層腐蝕產(chǎn)物膜主要由Fe3O4構(gòu)成,這與龍晉明等[19]的研究結(jié)果相似。
圖5 在120 mmol/L NH4H2PO4溶液中浸泡20 h后的1R鋼試樣表面腐蝕產(chǎn)物的XRD譜
2.3 XPS測(cè)試
通過(guò)上述分析,表明1R鋼在30~120 mmol/L溶液中浸泡20 h后形成的腐蝕產(chǎn)物膜為雙層結(jié)構(gòu),外層產(chǎn)物膜較疏松,且易脫落,而內(nèi)層腐蝕產(chǎn)物膜附著力較強(qiáng),因此本文用去離子水去除表面外層疏松的腐蝕產(chǎn)物,保留與基體結(jié)合緊固的內(nèi)層腐蝕產(chǎn)物,并研究其相組成及其相對(duì)含量。
1R鋼在30~120 mmol/L NH4H2PO4溶液中浸泡20 h后形成的內(nèi)層腐蝕產(chǎn)物膜中Fe 2p3/2、Cr 2p3/2、Mo 3d的XPS圖譜如圖6所示。通過(guò)NIST的原子譜數(shù)據(jù)庫(kù)和相關(guān)文獻(xiàn)對(duì)圖譜進(jìn)行分峰擬合,主要組成物質(zhì)的結(jié)合能分別為:Fe 2p3/2 Fe3O4/711.4 eV;Fe(OH)3/713.9 eV;Fe3(PO4)2/710.1 eV;FePO4/712.8 eV,Cr2p3/2 CrO3/578.3 eV;Cr(OH)3/577.1 eV,Mo 3d5/2 Mo6+/232.5 eV及Mo 3d3/2 Mo6+/235.8 eV。表3為XPS圖譜擬合出的峰面積及各峰的面積比[18-22]。可見內(nèi)層腐蝕產(chǎn)物膜主要由Fe的氧化物、磷化物、氫氧化物,Cr的氧化物和氫氧化物及Mo6+的相應(yīng)化合物組成。將NH4H2PO4溶液濃度由30 mmol/L提高到120 mmol/L,雖然溶液濃度增大了3倍,但是Fe3(PO4)2的峰面積比僅由16.8%增至25.7%,FePO4的峰面積比由20.9%減至16.3%,Fe(OH)3的峰面積比由15.6%減至10.1%,Fe3O4的峰面積比基本沒(méi)變,變化的原因是隨著NH4H2PO4溶液濃度的增大,溶液pH變小,從而抑制Fe2+氧化[23]。實(shí)驗(yàn)表明30~120 mmol/L NH4H2PO4溶液中pH在4.1至4.9之間,接近FePO4沉淀產(chǎn)生的最佳pH (3~5),隨著Fe3+減少,FePO4的含量便會(huì)出現(xiàn)減少的趨勢(shì),水解而得的Fe(OH)3也會(huì)出現(xiàn)減少的趨勢(shì)[24,25]。將溶液濃度由30 mmol/L提高到120 mmol/L,腐蝕產(chǎn)物膜中CrO3的峰面積比由31.2%增至61.4%,這或許是因?yàn)閜H增大會(huì)促進(jìn)穩(wěn)定的Cr的氧化物生成[26]。
圖6 1R鋼在不同濃度NH4H2PO4溶液中形成的內(nèi)層腐蝕產(chǎn)物膜中Fe 2p3/2,Cr2p3/2和Mo 3d XPS圖譜
表3 內(nèi)層腐蝕產(chǎn)物膜中Fe 2p3/2、Cr 2p3/2、Mo 3d的XPS圖譜擬合出的峰面積及其所占的比重
為了進(jìn)一步分析1R鋼在30~120 mmol/L NH4H2PO4溶液中浸泡20 h后表面形成的內(nèi)層腐蝕產(chǎn)物膜的差異性,本文利用 公式 (2) 計(jì)算不同濃度NH4H2PO4溶液對(duì)應(yīng)的內(nèi)層腐蝕產(chǎn)物膜中Fe、Cr、Mo之間原子分?jǐn)?shù) (Cx )[28]。其計(jì)算結(jié)果見表4。
表4 內(nèi)層腐蝕產(chǎn)物膜中主要元素含量
(2)
其中,Ix 是各元素的峰強(qiáng)度,可用其對(duì)應(yīng)的峰面積表示,Sx 為各元素的靈敏度因子,Fe 2p、Cr 2p、Mo 3d對(duì)應(yīng)的靈敏度因子分別為2.957、2.427、3.321。從表5中可以看出,Fe對(duì)應(yīng)的化合物為內(nèi)層腐蝕產(chǎn)物膜中最主要的物質(zhì),隨著NH4H2PO4溶液濃度的增大,內(nèi)層腐蝕產(chǎn)物膜中Fe含量呈下降趨勢(shì),而Cr、Mo含量卻呈遞增趨勢(shì)。這是因?yàn)殡S著NH4H2PO4溶液濃度的增大,溶液pH變小,電導(dǎo)率增大,內(nèi)層腐蝕產(chǎn)物膜中Fe、Cr、Mo對(duì)應(yīng)的化合物發(fā)生選擇性溶解,穩(wěn)定性較差的Fe的氧化物、氫氧化物、磷化物溶解速度較快,而Cr的氧化物和氫氧化物及高價(jià)態(tài)Mo6+相應(yīng)的化合物由于耐蝕性較好,溶解緩慢而出現(xiàn)一定的富集,從而造成內(nèi)層腐蝕產(chǎn)物膜中Fe含量減少,而Cr、Mo含量增多的結(jié)果[27-30]。
表5 1R鋼在不同濃度NH4H2PO4溶液中的電化學(xué)阻抗譜參數(shù)
2.4 開路電位
1R鋼在不同濃度NH4H2PO4溶液中浸泡20 h后測(cè)得的穩(wěn)定開路電位,pH值和電導(dǎo)率如圖7所示。由圖7a可知,1R鋼的開路電位隨NH4H2PO4溶液濃度的增大先負(fù)移后基本不變,值得注意的是,1R鋼在30~120 mmol/L NH4H2PO4溶液中浸泡20 h后測(cè)得的開路電位極為相近 (圖7a)。實(shí)驗(yàn)發(fā)現(xiàn)當(dāng)溶液由去離子水變成30 mmol/L NH4H2PO4溶液時(shí),溶液pH由6降到4.9,溶液電導(dǎo)率由0.6 μS/cm增到2695 μS/cm,電導(dǎo)率增大了約4491倍 (圖7b),隨著溶液pH快速下降,電導(dǎo)率快速上升,而此時(shí)1R鋼表面尚未形成致密的腐蝕產(chǎn)物膜,所以在此濃度范圍內(nèi),1R鋼的腐蝕傾向性隨NH4H2PO4溶液濃度的增大而增大,開路電位負(fù)移[32];將NH4H2PO4溶液濃度由30 mmol/L增大到120 mmol/L,溶液pH由4.9降到4.1,溶液電導(dǎo)率由2695 μS/cm增到8995 μS/cm電導(dǎo)率僅增大了約2.3倍;隨著NH4H2PO4溶液濃度的增大,試樣表面腐蝕產(chǎn)物形成也會(huì)加快,試樣表面覆蓋腐蝕產(chǎn)物逐漸增厚;內(nèi)層腐蝕產(chǎn)物膜中Cr、Mo出現(xiàn)一定程度的富集 (表5),一定程度抑制1R鋼腐蝕,促進(jìn)腐蝕因素與抑制腐蝕因素共同作用,最終造成了1R鋼的腐蝕傾向性基本不變的結(jié)果,故開路電位極為相近[30-33]。
圖7 1R鋼在不同濃度NH4H2PO4溶液中的開路電位及不同濃度NH4H2PO4溶液的pH和電導(dǎo)率
2.5 極化曲線
圖8為1R鋼在不同濃度NH4H2PO4溶液中浸泡20 h后從陰極向陽(yáng)極方向進(jìn)行掃描測(cè)試的Tafel曲線及其相應(yīng)的自腐蝕電位和自腐蝕電流密度。由圖可見,自腐蝕電位隨NH4H2PO4溶液濃度的增大先負(fù)移后基本不變,其變化規(guī)律與上文開路電位分析結(jié)果一致。自腐蝕電位只是反映材料腐蝕的傾向,并不能說(shuō)明材料腐蝕速率的大小,自腐蝕電流密度卻與材料腐蝕速率大小相關(guān),一般材料自腐蝕電流密度越大,材料腐蝕越快[34,35]。從圖8b中可獲知1R鋼的自腐蝕電流密度隨NH4H2PO4溶液濃度的增大而增大,所以1R鋼的腐蝕速率隨NH4H2PO4溶液濃度的增大而增大。
圖8 不同濃度NH4H2PO4溶液下1R鋼的極化曲線、自腐蝕電位和自腐蝕電流密度
2.6 電化學(xué)阻抗譜
圖9為1R鋼在不同濃度NH4H2PO4溶液中浸泡20 h后測(cè)得的電化學(xué)阻抗譜。從Nyquist圖可知,當(dāng)NH4H2PO4溶液濃度為0~1 mmol/L時(shí),電化學(xué)阻抗譜均有兩個(gè)容抗弧,相應(yīng)的,在Bode圖 (圖9a4) 上有兩個(gè)時(shí)間常數(shù),而高頻部分的容抗弧只有在低電導(dǎo)率溶液中才會(huì)出現(xiàn),一旦溶液電導(dǎo)率增大到一定程度,高頻部分的容抗弧便消失不見 (圖9a2),由高頻部分的容抗弧擬合出來(lái)的電阻的倒數(shù)與溶液電導(dǎo)率呈線性關(guān)系[38]。隨著NH4H2PO4溶液濃度的增大,1R鋼試樣表面腐蝕產(chǎn)物增多,電化學(xué)阻抗譜表現(xiàn)為高頻區(qū)和低頻區(qū)各出現(xiàn)一個(gè)容抗弧 (圖9a2),其中高頻容抗弧與腐蝕產(chǎn)物膜的膜層電容及膜層電阻有關(guān),而低頻容抗弧與雙電層電容及電荷轉(zhuǎn)移電阻有關(guān),此外,低頻區(qū)也出現(xiàn)了感抗弧,相應(yīng)的,在Bode圖 (圖9a4) 上還有一個(gè)低頻區(qū)的時(shí)間常數(shù)[17]。
圖9 不同濃度NH4H2PO4溶液下1R鋼的電化學(xué)阻抗譜
結(jié)合圖2和4,給出了圖10所示的等效電路[37,39],擬合結(jié)果如表5所示。圖10a為1R鋼在0~1 mmol/L NH4H2PO4溶液中腐蝕的等效模型,此時(shí)1R鋼表面的腐蝕產(chǎn)物較少,其中,Rs為溶液電阻,Qdl為雙電層電容,Rct為電荷轉(zhuǎn)移電阻;圖10b為腐蝕產(chǎn)物完全覆蓋在1R鋼表面時(shí)的等效電路模型,其中,Rs為溶液電阻,Qf為腐蝕產(chǎn)物膜的膜層電容,Rf為膜層電阻,RL和L為感抗元件,感抗一般出現(xiàn)在腐蝕前期和后期,即尚未生成完整的保護(hù)膜層及后期部分膜層脫落時(shí),通常,在局部電極表面出現(xiàn)腐蝕中間產(chǎn)物,Qdl為雙電層電容,Rct為電荷轉(zhuǎn)移電阻。其中,常相位角元件 的阻抗值可用 公式 (3) 計(jì)算[26]。
圖10 不同濃度NH4H2PO4溶液下1R鋼的等效電路
(3)
其中,ZQ為常相位角Q的阻抗值,Y0為導(dǎo)納模量,w為角頻率,j為虛數(shù)單位,n為彌散指數(shù)。
從表5中可知,去離子水的溶液電阻最大,其值為7.58 104 Ω·cm2,而上文中測(cè)得的去離子水的電導(dǎo)率為0.6 μS/cm,轉(zhuǎn)換為電阻率約為1.67 106 Ω·cm,造成電化學(xué)工作站測(cè)出來(lái)的溶液電阻偏小的原因是鹽橋中的KCl,鋼基體溶解生成的Fe2+等進(jìn)入去離子水中,從而提高了溶液的導(dǎo)電性。將1、30、60、90、120 mmol/L NH4H2PO4溶液的導(dǎo)電率轉(zhuǎn)換為電阻率,其值分別為8961.9、371.1、199.5、139.4、111.2 Ω·cm,與電化學(xué)工作站測(cè)出來(lái)的溶液電阻值相近。此外,膜層電阻Rf、電荷轉(zhuǎn)移電阻Rct、感抗電阻RL均隨NH4H2PO4溶液濃度的增大而減小,而且電荷轉(zhuǎn)移電阻Rct隨NH4H2PO4溶液濃度的變化趨勢(shì)與上文腐蝕速率分析結(jié)果一致。
1R鋼試樣的電極反應(yīng)為:
其中,陽(yáng)極反應(yīng)為金屬基體中鐵的溶解,而陰極反應(yīng)為氧的去極化反應(yīng),部分Fe2+也會(huì)被溶液中的溶解氧氧化為Fe3+,隨著腐蝕過(guò)程的進(jìn)行,H+、Fe2+、Fe3+、NH4+等向陰極區(qū)方向移動(dòng),而OH-、H2PO4-、HPO42-、PO43-等向陽(yáng)極區(qū)方向移動(dòng),并在活化陽(yáng)極區(qū)附近形成較為穩(wěn)定的Fe(OH)3、FePO4、Fe3(PO4)2腐蝕產(chǎn)物[17,18]。
隨著NH4H2PO4溶液濃度的增大,1R鋼試樣表面形成的腐蝕產(chǎn)物膜覆蓋程度及致密程度均有所提高,內(nèi)層腐蝕產(chǎn)物膜中Cr、Mo出現(xiàn)一定程度的富集,抑制了1R鋼腐蝕,但在所研究的濃度范圍內(nèi),溶液pH下降、電導(dǎo)率增大、材料表面形成的銹層疏松等促進(jìn)材料腐蝕的因素處于主導(dǎo)地位,所以1R鋼的腐蝕速率隨NH4H2PO4溶液濃度的增大而增大,不過(guò)隨著NH4H2PO4溶液濃度的增大,抑制材料腐蝕的因素逐漸增強(qiáng),從而造成1R鋼的腐蝕速率隨NH4H2PO4溶液濃度的增大先快速增大后緩慢增大的結(jié)果。這與上文腐蝕速率分析、形貌觀察結(jié)果一致。
3 結(jié)論
(1) 2Cr-1Ni-1.2Mo-0.2V鋼在去離子水中浸泡20 h后的平均腐蝕速率約為0.017 g·m-2·h-1,在1 mmol/L NH4H2PO4溶液中的腐蝕速率便增大7.973倍。1~30、30~60、60~90、90~120 mmol/L NH4H2PO4溶液對(duì)應(yīng)的2Cr-1Ni-1.2Mo-0.2V鋼的腐蝕速率相對(duì)于NH4H2PO4溶液濃度的導(dǎo)數(shù)分別約為0.001、0.002、0.003、0.001 L·g·m-2·h-1 mmol-1,即隨著NH4H2PO4溶液濃度的增大,2Cr-1Ni-1.2Mo-0.2V鋼的腐蝕速率先快速增大后緩慢增大
(2) 2Cr-1Ni-1.2Mo-0.2V鋼僅在低濃度NH4H2PO4溶液中萌發(fā)點(diǎn)蝕,溶液濃度大于或等于30 mmol/L后,材料腐蝕形態(tài)表現(xiàn)為均勻腐蝕。2Cr-1Ni-1.2Mo-0.2V鋼表面腐蝕產(chǎn)物膜為雙層結(jié)構(gòu),外層腐蝕產(chǎn)物膜疏松,且易脫落,主要由Fe3(PO4)2、FePO4組成,而內(nèi)層腐蝕產(chǎn)物膜附著力較強(qiáng),主要由Fe3O4構(gòu)成。隨著NH4H2PO4溶液濃度的增大,外層腐蝕產(chǎn)物膜覆蓋程度及致密程度均有所提高,內(nèi)層腐蝕產(chǎn)物膜中Cr、Mo出現(xiàn)一定程度的富集,抑制了2Cr-1Ni-1.2Mo-0.2V鋼的腐蝕。
(3) 在0~120 mmol/L NH4H2PO4溶液中,隨著NH4H2PO4溶液濃度的增大,2Cr-1Ni-1.2Mo-0.2V鋼的穩(wěn)定開路電位和自腐蝕電位均先負(fù)移后基本不變,而自腐蝕電流密度逐漸增大、電荷轉(zhuǎn)移傳遞電阻逐漸減小,即2Cr-1Ni-1.2Mo-0.2V鋼的腐蝕速率隨NH4H2PO4溶液濃度的增大而增大。
參考文獻(xiàn):
略
免責(zé)聲明:本網(wǎng)站所轉(zhuǎn)載的文字、圖片與視頻資料版權(quán)歸原創(chuàng)作者所有,如果涉及侵權(quán),請(qǐng)第一時(shí)間聯(lián)系本網(wǎng)刪除。
-
標(biāo)簽: CrNiMoV鋼, NH4H2PO4, 腐蝕產(chǎn)物膜, 電化學(xué)腐蝕
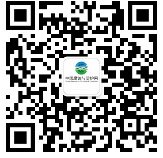
官方微信
《腐蝕與防護(hù)網(wǎng)電子期刊》征訂啟事
- 投稿聯(lián)系:編輯部
- 電話:010-62316606-806
- 郵箱:fsfhzy666@163.com
- 腐蝕與防護(hù)網(wǎng)官方QQ群:140808414