7xxx系鋁合金(Al-Zn-Mg-Cu系)因其比強度高、成形性好等優點,作為結構材料廣泛應用于航空航天及車輛工程領域[1,2]。但是,該系合金容易發生應力腐蝕開裂(SCC),不僅降低了其服役壽命,也限制了其應用。為了降低該系合金的SCC敏感性,人們進行了大量的研究,發現元素含量和比例[3,4]、再結晶程度[5,6]、熱處理制度[7,8]等都對SCC敏感性有重要影響。7xxx系鋁合金是可熱處理強化合金,淬火是決定其最終性能的一個關鍵工序。淬火速率對該系合金SCC敏感性影響很大。
Yuan等[9]通過評價裂紋擴展速率發現7xxx系鋁合金的SCC敏感性在淬火速率8~150℃/s區間內隨著淬火速率的減小而降低。Xie等[7]采用分級淬火的方法發現淬火速率越小,7097鋁合金的SCC敏感性越低,認為隨著淬火速率減小,晶界附近的無沉淀析出帶(PFZ)增寬,晶界析出相(GBP)中Cu含量的增加,均會降低裂紋擴展速率。Jiang等[10]對比了7046鋁合金在空氣淬火(1.4℃/s)與水淬火(80℃/s)條件下的SCC敏感因子,發現隨淬火速率減小SCC敏感性增高,認為這是隨淬火速率減小晶界PFZ增寬后更容易被溶解造成的。Chen等[11]通過對比伸長率的損失發現7085鋁合金的SCC敏感性在淬火速率1~150℃/s區間內隨淬火速率減小先降低再升高,認為淬火速率大于50℃/s時,GBP的尺寸和間距增大降低了SCC敏感性;而淬火速率小于50℃/s后,GBP中Cu含量的降低提高了SCC敏感性。Xiao等[12]通過評價強度的損失發現過時效態7xxx鋁合金的SCC敏感性在淬火速率5~130℃/s區間內隨淬火速率減小先降低再升高,而峰時效態合金的SCC敏感性隨淬火速率的減小而降低,認為GBP的面積分數起了決定性作用,GBP面積分數小于22.3%時SCC敏感性隨淬火速率減小而降低,高于22.3%后則隨淬火速率減小而升高。
SCC對材料強度、伸長率、服役壽命等都有影響,通過單一的性能損失難以反映SCC對材料整體性能的影響。上述研究均采用不同介質進行淬火,只能獲得離散變化的淬火速率。而實際工業生產的淬火過程中,厚截面材料表層到心部的淬火速率是連續減小的。淬火速率不僅改變GBP的化學成分、尺寸、相間距、數量,還會改變PFZ的寬度[9,13],進而對SCC敏感性造成有利或不利的影響。通過微觀組織的單一特征變化不能全面地解釋淬火速率對SCC敏感性的影響機理。
本工作以7136鋁合金為對象,通過浸入式末端淬火的方法獲得大范圍連續變化的淬火速率,結合慢應變速率拉伸(SSRT)實驗中獲得的強度、伸長率和斷裂時間等數據綜合研究淬火速率對該合金SCC敏感性的影響規律,并探討微觀組織特征對SCC的影響機理。這可以深化人們對7xxx系鋁合金SCC敏感性的理解,為調控材料性能提供參考。
1 實驗方法
實驗材料為16 mm厚的7136鋁合金擠壓板材,實測化學成分(質量分數,%)為Al-9.10Zn-2.18Mg-2.07Cu-0.13Zr,Fe < 0.08,Si < 0.05。為準確表述實驗過程及試樣位置,建立三維坐標系,定義板材的擠壓方向(ED)為x軸,橫向(TD)為y軸,法向(ND)為z軸。從板材上沿ED切取長度和寬度分別為360和170 mm的試樣置于SX-4-10型箱式電阻爐中進行雙級固溶,制度為450℃、1 h + 470℃、0.5 h。固溶后在2 s內將試樣轉移至室溫(約25℃)水槽中進行浸入式末端淬火,TD垂直于水面,試樣浸入水中深度為25 mm,其余部分位于空氣中。圖1為浸入式末端淬火示意圖,圖中藍色表示水中的部分,灰色表示空氣中的部分。在試樣TD-ND面z = 8 mm處沿y軸的不同位置鉆出8個直徑為1.5 mm、深度為10 mm的小孔預埋熱電偶。使用QT-6-K高精度測溫儀采集末端淬火過程中的時間-溫度曲線,數據采集頻率為20 Hz。待試樣完全冷卻至室溫后,立即在SX2-9-12TP箱式電阻爐中進行120℃、24 h的人工時效。
圖1 末端淬火示意圖及慢應變速率拉伸試樣尺寸
按照HB 7235-95標準在YYF-100型慢應變速率應力腐蝕試驗機上執行SSRT實驗。在板材ND-ED面沿y軸連續切取厚度為3 mm的試樣,具體尺寸見圖1。取試樣中心位置所對應的y軸淬火速率作為名義淬火速率。每組平行樣為3個,應變速率為1 × 10-6 s-1,腐蝕介質為3.5%NaCl (質量分數)溶液,惰性介質為硅油。通過試驗機自帶的加熱裝置將介質溫度控制在(50 ± 2)℃。實驗結束后,分析不同試樣的應力-應變曲線、斷裂時間等數據。
使用EVO MA10掃描電子顯微鏡(SEM,加速電壓20 kV)觀察試樣的斷口形貌,再在斷口處取樣,觀察和分析斷裂位置附近(ED-TD面)的腐蝕裂紋特征,并統計腐蝕裂紋數量,測量最大腐蝕深度。在板材不同位置切取試樣觀察第二相特征,并使用X-MaxN能譜分析儀(EDS)對第二相粒子進行成分分析。電子背散射衍射(EBSD)分析在配有EBSD探頭的EVO MA10 SEM上進行。試樣經過機械拋光后進行電解拋光,電解電壓為15 V,時間約為10 s,拋光液為10%HClO4 + 90%C2H5OH (體積分數)的混合溶液。使用HKL Channel 5軟件處理EBSD數據。使用Titan G2 60-300掃描透射電子顯微鏡(STEM)在高角環形暗場像(HAADF)模式下觀察微觀組織特征,重點觀察晶界(GB)和亞晶界(SGB)上析出相等特征,使用Super-X型EDS檢測GBP的化學成分,束斑尺寸為2 nm,加速電壓300 kV。STEM樣品預磨至80 μm厚后,使用沖孔器沖成直徑為3 mm的圓片后進行雙噴減薄,雙噴液為20%HNO3 + 80%CH3OH (體積分數),使用液氮將溫度控制在-20℃以下。
2 實驗結果
2.1 時間-溫度曲線與淬火速率
圖2a為7136鋁合金試樣不同位置的時間-溫度曲線。可見,溫度下降率隨y值增大而減小,y = 10 mm處溫度下降率最大,y = 100、120和150 mm處的冷卻曲線形狀基本相同。研究[14]發現,7xxx系鋁合金的淬火敏感區間約為210~420℃。依據試樣的時間-溫度曲線計算不同位置在該溫度區間的平均淬火速率,如圖2b所示。在y = 0~60 mm范圍內,淬火速率隨y值增大迅速減小,從y = 10 mm時的384.0℃/s減小到y = 60 mm的5.3℃/s。y > 60 mm后淬火速率緩慢減小,并穩定在約1.8℃/s。
圖2 7136鋁合金試樣不同位置的時間-溫度曲線與平均淬火速率
2.2 SSRT實驗結果
實驗結果表明,7136鋁合金試樣的強度隨著淬火速率的減小而降低,伸長率則升高。作為代表給出淬火速率為263.0、5.3和1.8℃/s時7136鋁合金試樣的應力-應變曲線,如圖3所示。淬火速率為263.0℃/s試樣的強度最高,硅油和NaCl溶液中的強度分別約為537.0和523.1 MPa,而伸長率最低,分別約為15.1%和13.4%。淬火速率為5.3℃/s試樣的強度和伸長率居中,硅油和NaCl溶液中強度分別為478.2和458.3 MPa,伸長率分別為15.7%和14.2%。淬火速率為1.8℃/s試樣的強度最低,而伸長率最高,硅油和NaCl溶液中的強度分別為395.0和391.5 MPa,伸長率分別為24.5%和22.3%。
圖3 淬火速率為263.0、5.3和1.8℃/s時7136鋁合金試樣的應力-應變曲線
由此可知,試樣在硅油中的拉伸性能均高于NaCl溶液中,為評價各性能的損失情況,引入性能下降率KN,計算公式如下:
式中,NOil為試樣在硅油中的性能,NNaCl為試樣在NaCl溶液中的性能。分別用KR、KA和Kt表示強度(Rm)、伸長率(A)和斷裂時間(t)的下降率,結果如圖4,圖中還給出了不同淬火速率下7136鋁合金試樣的強度、伸長率和斷裂時間。由圖4a可見,淬火速率大于5.3℃/s時,隨淬火速率減小強度緩慢降低,淬火速率小于5.3℃/s后強度迅速降低。KR在淬火速率大于20℃/s時隨淬火速率減小緩慢升高,淬火速率小于20℃/s之后迅速地升高,在淬火速率約為5.3℃/s時有最高值4.3%,然后迅速降低,淬火速率約為1.8℃/s后基本穩定在1.0%左右。
圖4 不同淬火速率下7136鋁合金試樣的強度、伸長率及斷裂時間及相應的下降率(KR、KA、Kt)
由圖4b可知,硅油中的試樣伸長率在淬火速率大于5.3℃/s時基本不變,淬火速率小于5.3℃/s后迅速增高。NaCl溶液中試樣的伸長率在淬火速率大于5.3℃/s時隨淬火速率的減小先出現明顯降低再逐漸升高,淬火速率小于5.3℃/s后迅速升高。KA隨淬火速率減小呈“M”狀變化。
由圖4c可知,淬火速率大于100℃/s時,硅油中試樣的斷裂時間變化不大,之后隨淬火速率減小逐漸升高,最終穩定在68 h左右;NaCl溶液中試樣的斷裂時間在淬火速率大于100℃/s時隨淬火速率減小緩慢降低,淬火速率在20~100℃/s時斷裂時間幾乎不變,之后迅速升高并穩定在63 h左右。Kt隨淬火速率的減小迅速增加到16.6%,之后緩慢增大,在淬火速率為5.3℃/s時達到峰值(19.5%)后迅速降低。
可見,KR、KA和Kt表現出的規律并不一致,說明采用單一的性能損失很難準確地評價材料的SCC敏感性。為綜合評估材料SCC的敏感性,引入SCC敏感指數(ISSRT),計算公式如下[4]:
式中,RmNaCl為NaCl溶液中的斷裂強度(MPa),RmOil為硅油中的斷裂強度(MPa),ANaCl為NaCl溶液中的伸長率(%),AOil為硅油中的伸長率(%)。ISSRT越大表示SCC敏感性越高。
圖5給出不同淬火速率下7136鋁合金試樣的ISSRT。隨著淬火速率的減小,ISSRT呈先升高再降低的趨勢,淬火速率為5.3℃/s時的 最高(0.049),淬火速率為263.0和1.8℃/s時的ISSRT分別為0.027和0.024。根據以上實驗結果,可以確定試樣的SCC敏感性隨淬火速率減小先升高后降低,且淬火速率為5.3℃/s時最高。
圖5 不同淬火速率下7136鋁合金試樣的應力腐蝕敏感指數(ISSRT)
2.3 斷口SEM像
圖6為NaCl溶液中不同淬火速率7136鋁合金試樣斷口形貌的SEM像。淬火速率為263.0℃/s試樣的斷口表層有較窄的腐蝕裂紋,存在少量的腐蝕產物,斷口以穿晶斷裂為主,如圖6a和a1所示。淬火速率為5.3℃/s試樣的斷口出現較寬的腐蝕裂紋,裂紋已擴展到試樣內部較深的區域,如圖6b所示。觀察圖6b1發現,斷口表面存在大量的泥漿狀腐蝕產物,以沿晶斷裂為主。淬火速率為1.8℃/s的試樣表面存在大量腐蝕裂紋,裂紋內塞積有顆粒狀腐蝕產物,如圖6c所示。觀察圖6c1發現有較細的裂紋從腐蝕產物附近延伸到試樣內部,斷口以沿晶斷裂為主。
圖6 在NaCl溶液中的不同淬火速率下7136鋁合金試樣斷口形貌的SEM像
為更好地分析試樣的斷裂行為,圖7給出NaCl溶液中不同淬火速率下7136鋁合金試樣斷口附近(ED-TD面)的SEM像。淬火速率為263.0℃/s試樣的表層存在一些腐蝕裂紋,密度約為12 mm-1;裂紋比較尖銳,最大深度約為71.0 μm,如圖7a1所示。將試樣用Graff Sargent試劑(1 mL HF + 16 mL HNO3 + 3 g CrO3 + 83 mL H2O)腐蝕后,可以觀察到裂紋主要是穿過晶粒向試樣內部擴展,如圖7a2所示;晶粒內存在一些白色初生相,EDS分析顯示其成分(原子分數,下同)為:(76.15~85.68)%Al、(2.87~7.90)%Fe、(5.31~13.26)%Cu和少量Zn元素,應該為Al7Cu2Fe相[15,16]。
圖7 在NaCl溶液中不同淬火速率下7136鋁合金試樣斷口附近的SEM像
淬火速率為5.3℃/s試樣腐蝕裂紋數量明顯增加,約為19 mm-1,最大深度約為78.9 μm,如圖7b1所示。從圖7b2可以觀察到該裂紋很寬,其前部沿晶界擴展到試樣內部;晶界和晶內均分布有白色淬火相,EDS分析顯示其成分為:(65.90~92.35)%Al、(2.43~6.52)%Mg、(5.31~8.58)%Zn和(1.25~2.71)%Cu,應該為η (Mg(ZnCu)2)相[15]。
淬火速率為1.8℃/s試樣表面的腐蝕裂紋數量達到29 mm-1,但是最大深度明顯減小,約為43.9 μm,如圖7c1所示。仔細觀察圖7c2發現裂紋主要沿晶界和亞晶界擴展,路徑很曲折。晶內和晶界上的淬火相尺寸明顯比圖7b2更大,數量也更多。
綜合以上結果可知,隨淬火速率減小,腐蝕裂紋的最大深度先增大后減小,腐蝕裂紋的數量逐漸增多。
2.4 微觀組織
2.4.1 EBSD像
實驗結果表明淬火速率對晶粒組織基本無影響,作為代表,圖8給出淬火速率為263.0和1.8℃/s試樣的EBSD像。黑色線代表角度大于15°的晶界,通常稱為晶界,白色線代表角度為2°~15°的晶界,一般稱為亞晶界[17]。2種試樣晶粒組織差異很小,主要為被拉長的未再結晶晶粒,其中有許多亞晶,還有少量細小的再結晶晶粒。淬火速率為263.0℃/s試樣的再結晶分數約為(38.3 ± 3.9)%。淬火速率為1.8℃/s試樣的再結晶分數約為(37.1 ± 4.5)%,2者非常接近。
圖8 不同淬火速率7136鋁合金試樣縱截面晶粒取向分布圖
2.4.2 SEM像
圖9a給出淬火速率為263℃/s 7136鋁合金試樣的SEM像。可以觀察到大量尺寸為1.6~9.1 μm的白色第二相沿ED方向呈鏈狀分布,EDS分析其成分為(75.22~86.32)%Al、(3.11~7.70)%Fe、(5.61~15.81)%Cu和少量Zn元素,應該為Al7Cu2Fe相。這些相形成于熔鑄過程,在擠壓等變形過程中會破碎。固溶時,它們容易引起其周圍晶粒發生再結晶[18]。在腐蝕環境中,它們通常充當陰極引起電偶腐蝕[16,19]。淬火速率為1.8℃/s試樣的SEM像如圖9b所示。除Al7Cu2Fe相以外,晶界和晶內均出現大量η淬火相。晶界上的η相襯托出晶粒形貌。在晶界附近可以觀察到明顯的PFZ。
圖9 不同淬火速率7136鋁合金試樣的SEM像
2.4.3 STEM-HAADF像
圖10為不同淬火速率7136鋁合金試樣的STEM-HAADF像。淬火速率為263.0℃/s試樣晶粒內未發現淬火相,如圖10a所示。晶界上分布有η相,長度為(64.0 ± 22.9) nm,相間距為(60.0 ± 8.5) nm。晶界附近可見寬度比較均勻的PFZ,寬度為(55.7 ± 11.2) nm。亞晶界上的析出相(SGBP)分布更連續,尺寸更小,長度為(34.0 ± 12.9) nm,其附近的PFZ也更窄,寬度僅為(45.1 ± 8.0) nm。
圖10 不同淬火速率7136鋁合金試樣的STEM-HAADF像
淬火速率減小至5.3℃/s時,試樣的晶內和晶界上都出現了大量的淬火相,如圖10b所示。一些淬火相在雙噴時脫落,形成黑色的孔洞。淬火速率減小,試樣在高溫下的時間更長,有利于溶質原子擴散,因而在晶界、亞晶界及Al3Zr粒子等界面能高的地方形成粗大的η相[20]。因此GBP的尺寸差異很大,尺寸大的長度為(453.8 ± 130.3) nm,尺寸小的為(57.4 ± 22.0) nm,與淬火速率為263℃/s試樣中的相當。晶界附近的PFZ寬度差別也更大,寬的達(223.0 ± 49.2) nm,窄的僅為(125.9 ± 10.7) nm,平均約174.5 nm。SGBP尺寸增加至(101.5 ± 34.7) nm,分布較連續,亞晶界附近的PFZ寬度為(70.6 ± 12.7) nm。
淬火速率繼續減小至1.8℃/s時,晶界和亞晶界上的淬火相進一步長大,附近的PFZ明顯更寬,如圖10c所示。尺寸大的GBP可達1000 nm,尺寸小的GBP長度增加至80.0 nm左右,晶界附近的PFZ寬度為(303.0 ± 35.0) nm。SGBP的長度為(101.5 ± 34.7) nm,其附近的PFZ寬度為(139.0 ± 7.7) nm,一部分已經超過淬火速率為5.3℃/s試樣中部分晶界PFZ的寬度。
綜合圖7b2和c2、圖9以及圖10的觀察,發現淬火相的尺寸和數量隨著淬火速率的減小而增加。這些淬火相幾乎沒有強化作用,且消耗了大量的溶質原子,減少了時效后η'強化相的數量,降低了試樣的強度(圖4a)。由于PFZ內沒有強化相,因此寬度增加后,也降低了試樣的強度[12]。因此,如圖4a所示,拉伸強度隨淬火速率減小而降低。統計晶界及亞晶界析出相形貌特征參數如圖11所示。可見,GBP尺寸、相間距及PFZ寬度均隨淬火速率減小而增加,在其他7xxx合金中發現了相似的規律。這是因為淬火速率減小后,更多的溶質原子擴散到晶界和亞晶界上,時效后形成尺寸和相間距更大的GBP,同時導致了PFZ寬度的增加[7,21]。
圖11 不同淬火速率7136鋁合金試樣晶界和亞晶界上析出相的特征參數
此外,還通過STEM-EDS分析了不同淬火速率7136鋁合金試樣GBP中的化學成分,作為代表給出淬火速率為263.0℃/s試樣的STEM-HAADF像和EDS面掃描圖,如圖12所示。從圖12a可見,晶界上有3個明亮的η相,晶界附近有明顯的PFZ。由圖12b~e可知,η相中Zn、Mg、Cu元素含量高,而PFZ中Zn、Mg和Cu元素含量低。
圖12 淬火速率為263.0℃/s時7136鋁合金試樣晶界處的STEM-HAADF像和EDS面掃描圖
在不同淬火速率7136鋁合金試樣中統計了大量GBP中Zn、Mg、Cu元素含量,如圖13所示。隨著淬火速率的減小,GBP中Zn、Mg、Cu元素的含量均呈增加的趨勢,但是3種元素的增加率不同。淬火速率從263.0℃/s減小至5.3℃/s時,Zn、Mg和Cu元素含量的增加率分別為44.9%、47.8%和28.9%;當淬火速率從5.3℃/s減小至1.8℃/s時,它們的增加率分別為11.0%、9.8%和88.4%。淬火速率大于5.3℃/s時,Zn、Mg元素的增加率明顯高于Cu元素,而淬火速率小于5.3℃/s后Cu元素的增加率比Zn、Mg元素的更高。
圖13 不同淬火速率7136鋁合金試樣晶界析出相中Zn、Mg、Cu元素的含量
慢速淬火時,Zn、Mg和Cu原子傾向擴散至晶界,在一些位置上形成了η相,而且使得晶界處這些元素濃度高于基體;淬火速率越小,晶界附近這些元素的濃度越高。Zn、Mg原子的擴散速率比Cu原子更快[22],淬火速率大于5.3℃/s時,GBP中Zn、Mg元素的增加率高于Cu元素。隨著淬火速率繼續減小,GBP中Zn、Mg原子接近飽和,它們的增加率隨之降低。而擴散速率較慢的Cu原子在慢速淬火過程以及后續的時效過程中可以不斷進入到GBP里[3]。另外,在淬火或者時效過程中Cu原子可以置換GBP中部分Zn原子[23],從而引起Cu元素含量繼續增加。
3 分析討論
根據SSRT結果可以確定7136鋁合金的SCC敏感性隨淬火速率減小先升高再降低,這不同于以往的一些研究結果[10~12]。淬火速率對晶界及亞晶界析出相的化學成分和晶界形貌特征的影響很復雜,需要綜合考慮其對SCC敏感性的影響。基于實驗結果繪制了不同淬火速率時7136鋁合金SCC裂紋擴展示意圖,如圖14所示。
圖14 不同淬火速率下7136鋁合金應力腐蝕開裂裂紋擴展示意圖
淬火速率為263.0℃/s時,試樣晶內、晶界和亞晶界沒有淬火相出現,晶界和亞晶界附近的PFZ很窄。NaCl溶液中試樣的斷口處未觀察到晶界和亞晶界被明顯腐蝕的特征,說明此時沒有沿晶界和亞晶界發生陽極溶解。試樣表面的Al7Cu2Fe相等引起其周圍基體發生腐蝕并形成腐蝕坑[10,16],在外加應力的作用下,腐蝕坑底部形成應力集中,進而引發SCC裂紋的萌生[24~26]。腐蝕過程中產生的H會擴散到基體中,并沿著位錯運動到裂紋尖端,降低了晶格結合力,導致SCC裂紋不斷擴展[24]。擴展過程中,因為晶界和亞晶界附近狹窄的PFZ抑制了陽極溶解通道的形成[13,27],裂紋選擇在晶內不斷擴展,如圖14a所示。此時SCC以氫脆為主,裂紋主要穿晶擴展,強度、伸長率和斷裂時間的損失不大,試樣的SCC敏感性并不高。
淬火速率減小至約5.3℃/s時,淬火相的數量明顯增多,尺寸增大,GBP的相間距有所增大,晶界附近的PFZ寬度比淬火速率為263.0℃/s時明顯增加,亞晶界附近的PFZ寬度增加很小(圖11)。淬火相是H不可逆的陷阱,可以捕獲試樣中的H并使之以氣體的形式排放出去,因而減緩了氫脆[28,29]。然而,淬火相的腐蝕電位比基體和Al7Cu2Fe相更負,因而試樣表面的淬火相在腐蝕溶液中會充當陽極優先被溶解[27],形成腐蝕裂紋源。GBP中Zn、Mg元素含量比淬火速率為263.0℃/s時大幅增加,引起GBP與基體和Al7Cu2Fe相的電勢差增大[15,30],這促進了腐蝕裂紋擴展。晶界附近的PFZ寬度增加有利于裂紋的形成和擴展[10],因而晶界成為快速腐蝕通道,但多數亞晶界對微裂紋的產生和擴展還有較強的抑制作用。此時腐蝕裂紋在氫脆和陽極溶解共同作用下沿晶界迅速擴展到試樣內部更深的地方,導致更大的腐蝕深度,如圖14b所示。因而試樣強度和斷裂時間等的損失更大,試樣的SCC敏感性很高。
淬火速率減小至約1.8℃/s時,淬火相的數量和尺寸、晶界和亞晶界附近的PFZ寬度都很大,如圖11所示。淬火相增多可以捕獲更多的H,因而氫脆進一步被削弱。試樣表面更多的淬火相被溶解并在外力作用下形成裂紋源,裂紋數量比淬火速率為263.0和5.3℃/s時分別增加了141.7%和52.6%,這大幅緩解了應力集中。GBP中Cu元素大量的增加也可有效抑制SCC裂紋擴展[7,8,24,31,32]。圖15是淬火速率為5.3和1.8℃/s時板材的晶界和亞晶界PFZ寬度分布情況。可見,淬火速率為5.3℃/s時,約80%的晶界PFZ寬度在100~200 nm,而淬火速率為1.8℃/s時有約75%的亞晶界PFZ在這個寬度范圍內,即淬火速率為1.8℃/s時許多亞晶界PFZ寬度已經超過了淬火速率為5.3℃/s試樣中晶界PFZ的寬度。更寬的PFZ導致陽極溶解通道更容易形成,這就增加了沿晶界和亞晶界裂紋的數量(圖14c),因而主裂紋被鈍化。微裂紋的產生既釋放了應力又延緩了裂紋擴展的速率。Tanguy等[25]也發現腐蝕裂紋增多可以降低SCC的擴展速率。因此,淬火速率為1.8℃/s時試樣各項性能的損失都很小,試樣的SCC敏感性反而降低。
圖15 淬火速率為5.3和1.8℃/s時7136鋁合金試樣中不同無沉淀析出帶寬度的晶界和亞晶界的比例
4 結論
(1) 7136鋁合金應力腐蝕開裂敏感性隨著淬火速率的減小先升高再降低,淬火速率約為5.3℃/s時的應力腐蝕開裂敏感性最高。
(2) 隨著淬火速率的減小,晶界析出相增大,相間距增大,PFZ增寬。晶界析出相中Zn、Mg和Cu元素含量隨淬火速率減小而增加。淬火速率大于5.3℃/s時,晶界析出相中Zn、Mg元素的含量迅速增加,Cu元素含量緩慢增加;淬火速率小于5.3℃/s后,Zn、Mg元素含量增速降低,而Cu元素含量迅速增加。
(3) 淬火速率減小,晶界和亞晶界附近的PFZ寬化,能夠充當腐蝕裂紋擴展路徑,應力腐蝕裂紋擴展方式從以穿晶擴展為主轉變為沿晶界和亞晶界擴展。
參考文獻
1 Deng Y L, Zhang X M. Development of aluminium and aluminium alloy [J]. Chin. J. Nonferrous Met., 2019, 29: 2115
1 鄧運來, 張新明. 鋁及鋁合金材料進展 [J]. 中國有色金屬學報, 2019, 29: 2115
2 Rometsch P A, Zhang Y, Knight S. Heat treatment of 7xxx series aluminium alloys—Some recent developments [J]. Trans. Nonferrous Met. Soc. China, 2014, 24: 2003
doi: 10.1016/S1003-6326(14)63306-9
3 Knight S P, Pohl K, Holroyd N J H, et al. Some effects of alloy composition on stress corrosion cracking in Al-Zn-Mg-Cu alloys [J]. Corros. Sci., 2015, 98: 50
doi: 10.1016/j.corsci.2015.05.016
4 Chen S Y, Li J Y, Hu G Y, et al. Effect of Zn/Mg ratios on SCC, electrochemical corrosion properties and microstructure of Al-Zn-Mg alloy [J]. J. Alloys Compd., 2018, 757: 259
doi: 10.1016/j.jallcom.2018.05.063
5 Liu L, Jia Y Y, Jiang J T, et al. The effect of Cu and Sc on the localized corrosion resistance of Al-Zn-Mg-X alloys [J]. J. Alloys Compd., 2019, 799: 1
doi: 10.1016/j.jallcom.2019.05.189
6 Yu M Y, Zhang Y A, Li X W, et al. Effect of recrystallization on plasticity, fracture toughness and stress corrosion cracking of a high-alloying Al-Zn-Mg-Cu alloy [J]. Mater. Lett., 2020, 275: 128074
doi: 10.1016/j.matlet.2020.128074
7 Xie P, Chen S Y, Chen K H, et al. Enhancing the stress corrosion cracking resistance of a low-Cu containing Al-Zn-Mg-Cu aluminum alloy by step-quench and aging heat treatment [J]. Corros. Sci., 2019, 161: 108184
doi: 10.1016/j.corsci.2019.108184
8 Chen J F, Zhang X F, Zou L C, et al. Effect of precipitate state on the stress corrosion behavior of 7050 aluminum alloy [J]. Mater. Charact., 2016, 114: 1
doi: 10.1016/j.matchar.2016.01.022
9 Yuan D L, Chen K H, Chen S Y, et al. Enhancing stress corrosion cracking resistance of low Cu-containing Al-Zn-Mg-Cu alloys by slow quench rate [J]. Mater. Des., 2019, 164: 107558
doi: 10.1016/j.matdes.2018.107558
10 Jiang F Q, Huang J W, Jiang Y G, et al. Effects of quenching rate and over-aging on microstructures, mechanical properties and corrosion resistance of an Al-Zn-Mg (7046A) alloy [J]. J. Alloys Compd., 2021, 854: 157272
doi: 10.1016/j.jallcom.2020.157272
11 Chen S Y, Chen K H, Peng G S, et al. Effect of quenching rate on microstructure and stress corrosion cracking of 7085 aluminum alloy [J]. Trans. Nonferrous Met. Soc. China, 2012, 22: 47
doi: 10.1016/S1003-6326(11)61138-2
12 Xiao Q F, Xu Y M, Huang J W, et al. Effects of quenching agents, two-step aging and microalloying on tensile properties and stress corrosion cracking of Al-Zn-Mg-Cu alloys [J]. J. Mater. Res. Technol., 2020, 9: 10198
doi: 10.1016/j.jmrt.2020.07.014
13 Liu S D, Chen B, Li C B, et al. Mechanism of low exfoliation corrosion resistance due to slow quenching in high strength aluminium alloy [J]. Corros. Sci., 2015, 91: 203
doi: 10.1016/j.corsci.2014.11.024
14 Liu S D, Zhong Q M, Zhang Y, et al. Investigation of quench sensitivity of high strength Al-Zn-Mg-Cu alloys by time-temperature-properties diagrams [J]. Mater. Des., 2010, 31: 3116
doi: 10.1016/j.matdes.2009.12.038
15 Ma Z M, Liu J, Yang Z S, et al. Effect of cooling rate and grain structure on the exfoliation corrosion susceptibility of AA 7136 alloy [J]. Mater. Charact., 2020, 168: 110533
doi: 10.1016/j.matchar.2020.110533
16 Sun Y W, Pan Q L, Sun Y Q, et al. Localized corrosion behavior associated with Al7Cu2Fe intermetallic in Al-Zn-Mg-Cu-Zr alloy [J]. J. Alloys Compd., 2019, 783: 329
doi: 10.1016/j.jallcom.2018.12.151
17 Fang H C, Chao H, Chen K H. Effect of recrystallization on intergranular fracture and corrosion of Al-Zn-Mg-Cu-Zr alloy [J]. J. Alloys Compd., 2015, 622: 166
doi: 10.1016/j.jallcom.2014.10.044
18 Liao Y G, Han X Q, Zeng M X, et al. Influence of Cu on microstructure and tensile properties of 7xxx series aluminum alloy [J]. Mater. Des., 2015, 66: 581
doi: 10.1016/j.matdes.2014.05.003
19 Chemin A, Marques D, Bisanha L, et al. Influence of Al7Cu2Fe intermetallic particles on the localized corrosion of high strength aluminum alloys [J]. Mater. Des., 2014, 53: 118
doi: 10.1016/j.matdes.2013.07.003
20 Godard D, Archambault P, Aeby-Gautier E, et al. Precipitation sequences during quenching of the AA 7010 alloy [J]. Acta Mater., 2002, 50: 2319
doi: 10.1016/S1359-6454(02)00063-0
21 Chen J S, Li X W, Xiong B Q, et al. Quench sensitivity of novel Al-Zn-Mg-Cu alloys containing different Cu contents [J]. Rare Met., 2020, 39: 1395
doi: 10.1007/s12598-017-0981-y
22 Du Y, Chang Y A, Huang B Y, et al. Diffusion coefficients of some solutes in fcc and liquid Al: Critical evaluation and correlation [J]. Mater. Sci. Eng., 2003, A363: 140
23 Garner A, Euesden R, Yao Y C, et al. Multiscale analysis of grain boundary microstructure in high strength 7xxx Al alloys [J]. Acta Mater., 2021, 202: 190
doi: 10.1016/j.actamat.2020.10.021
24 Song R G, Dietzel W, Zhang B J, et al. Stress corrosion cracking and hydrogen embrittlement of an Al-Zn-Mg-Cu alloy [J]. Acta Mater., 2004, 52: 4727
doi: 10.1016/j.actamat.2004.06.023
25 Tanguy D, Bayle B, Dif R, et al. Hydrogen effects during IGSCC of pure Al-5Mg alloy in NaCl media [J]. Corros. Sci., 2002, 44: 1163
doi: 10.1016/S0010-938X(01)00140-8
26 Magnin T, Chambreuil A, Bayle B. The corrosion-enhanced plasticity model for stress corrosion cracking in ductile fcc alloys [J]. Acta Mater., 1996, 44: 1457
doi: 10.1016/1359-6454(95)00301-0
27 Song F X, Zhang X M, Liu S D, et al. The effect of quench rate and overageing temper on the corrosion behaviour of AA7050 [J]. Corros. Sci., 2014, 78: 276
doi: 10.1016/j.corsci.2013.10.010
28 Christodoulou L, Flower H M. Hydrogen embrittlement and trapping in Al-6%-Zn-3%-Mg [J]. Acta Metall., 1980, 28: 481
doi: 10.1016/0001-6160(80)90138-8
29 Tsai T C, Chuang T H. Role of grain size on the stress corrosion cracking of 7475 aluminum alloys [J]. Mater. Sci. Eng., 1997, A225: 135
30 Wang L, Dong C F, Zhang D W, et al. Effect of alloying elements on initial corrosion behavior of aluminum alloy in Bangkok, Thailand [J]. Acta Metall. Sin., 2020, 56: 119
30 王 力, 董超芳, 張達威 等. 合金元素對鋁合金在泰國曼谷地區初期腐蝕行為的影響 [J]. 金屬學報, 2020, 56: 119
31 Sarkar B, Marek M, Starke E A. The effect of copper content and heat treatment on the stress corrosion characteristics of Al-6Zn-2Mg-XCu alloys [J]. Metall. Trans., 1981, 12A: 1939
32 Rao A C U, Vasu V, Govindaraju M, et al. Stress corrosion cracking behaviour of 7xxx aluminum alloys: A literature review [J]. Trans. Nonferrous Met. Soc. China, 2016, 26: 1447
doi: 10.1016/S1003-6326(16)64220-6
免責聲明:本網站所轉載的文字、圖片與視頻資料版權歸原創作者所有,如果涉及侵權,請第一時間聯系本網刪除。
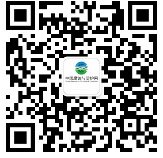
官方微信
《腐蝕與防護網電子期刊》征訂啟事
- 投稿聯系:編輯部
- 電話:010-62316606-806
- 郵箱:fsfhzy666@163.com
- 腐蝕與防護網官方QQ群:140808414