隨著中國深海和遠海戰略的實施,大批先進艦艇下水,國產航母和大量艦載機也投入服役。相比陸地航機,艦載機航空發動機和燃氣輪機熱端部件在服役過程中的環境條件異常苛刻,除發動機/燃氣輪機熱端零部件所承受的高溫、高壓、高轉速等載荷環境外,還承受海洋高鹽霧、高濕度等腐蝕環境的影響。渦輪轉子部件是艦載機航空發動機/燃氣輪機中服役環境最惡劣的部件,不僅要在高溫(600~1 300℃)條件下承受巨大的交變載荷,高溫燃氣和海洋大氣中的熱腐蝕也會加劇其損傷程度,渦輪轉子部件因此成為故障率最高的工作部件之一。如圖1所示,渦輪葉片因在燃氣-海洋大氣耦合環境中,在高溫、高轉速載荷下發生的熱腐蝕-疲勞失效[1,2,3,4,5,6]。相比于單一機械載荷作用下的疲勞失效,航空發動機和燃氣輪機熱端部件熱腐蝕-疲勞失效機理更為復雜,對熱腐蝕-疲勞壽命預測難度更大。目前,國內外對航空發動機和燃氣輪機熱端部件熱腐蝕-疲勞失效機理有了初步的認識,針對熱端部件材料開展了熱腐蝕機理研究、熱腐蝕-疲勞失效機理研究以及熱腐蝕-疲勞壽命預測,并取得了初步的成果。本文針對過去20年在航空發動機和燃機輪機熱端部件熱腐蝕-疲勞的研究進展進行梳理和總結歸納,以期促進燃氣-海洋環境耦合作用下航空發動機和燃氣輪機熱端部件結構完整性評定方法的發展,提高航空發動機和燃氣輪機的安全性和可靠性。Fig.1 Hot corrosion-fatigue failure of turbine blades鎳基高溫合金以其高溫下優異的疲勞性能、蠕變性能和持久性能[7,8,9],成為航空發動機與燃氣輪機渦輪葉片、渦輪盤等熱端部件的主要材料[10,11,12]。同時,為了降低渦輪葉片表面溫度和提高其抗氧化/腐蝕性能,在渦輪葉片表面通常噴涂有金屬涂層或熱障涂層(Thermal barrier coating,TBC)[13,14]。發動機在服役過程中,燃料中的雜質S在燃燒時會產生SO2、SO3等硫化物,與海洋大氣環境中NaCl反應后會在合金表面沉積一層Na2SO4熔鹽膜,形成的硫酸鹽等沉積物導致涂層、高溫合金發生熱腐蝕,最終導致發動機熱端部件過早失效[15,16]。高溫合金熱腐蝕是指沉積于合金表面的硫酸鹽等沉積物破壞表面氧化物而加速合金腐蝕的行為[17]。對于高溫合金來說,熱腐蝕造成的破壞要比單純高溫氧化嚴重得多,其嚴重性受多因素影響,包括溫度、沉積鹽的種類和含量、環境條件、氣體成分和合金成分等。根據環境溫度高低,熱腐蝕可分為低溫熱腐蝕和高溫熱腐蝕[18]。低溫熱腐蝕(560~815℃)一般在腐蝕鹽的熔點之下發生,限制條件是需要較高分壓的氣相SO3,與涂層或者基體中的合金元素反應形成新的硫酸鹽,這些硫酸鹽與Na2SO4形成低熔點(熔點為540℃)的共晶化合物,使合金發生局部點蝕。高溫熱腐蝕(815~980℃)通常在腐蝕鹽熔點以上溫度發生,熔融態堿金屬鹽在基體表面沉積,然后逐漸破壞氧化層并消耗基體金屬中的Cr,隨著Cr元素耗盡,氧化速度加快,涂層或基體內部開始形成細微的孔洞,為腐蝕介質浸入提供通道。此時熔融狀態的沉積鹽使合金發生均勻腐蝕,高溫熱腐蝕的氧化層與合金基體交界處相對平整,界面下方有明顯的硫化物形成。關于金屬材料,尤其是鐵基和鎳基高溫合金熱腐蝕機理,Rapp[19]和Singh等[20]在21世紀初對其進行了總結。因此,本文主要針對近20年渦輪盤、渦輪葉片高溫合金及涂層的熱腐蝕機理進行綜述。根據航空發動機和燃氣輪機具體的服役工況和渦輪前溫度,常用的涂層有滲鋁涂層[21](如在葉片表面和內腔滲鋁、滲鋁硅涂層)、MCrAlY涂層[22]和熱障涂層[23]等。高溫合金葉片的典型熱障涂層通常由金屬黏結層和隔熱陶瓷層組成,在高溫合金葉片基體與高溫燃氣間提供隔熱層和抗氧化層,從而保障葉片在較高的渦輪前溫度下安全工作。金屬黏結層可以提高基體合金與表面陶瓷層的結合強度,在高溫服役過程中還可以形成一層致密的熱生長氧化物(Thermally grown oxide,TGO)層,起到抗高溫氧化的作用。目前常用的TBCs材料有:Y2O3穩定的ZrO2(YSZ、Y2O3的質量分數一般為7%~8%)、莫來石、Al2O3、YSZ+CeO2、La2Zr2O7、硅酸鹽,其中YSZ是應用最廣泛的TBCs材料[21,24,25]。由于渦輪葉片表面涂層在服役過程中承受溫度高(>800℃),在燃氣和海洋環境耦合工況下,涂層通常發生高溫熱腐蝕。取決于涂層類型、成分和微觀結構,其熱腐蝕產物也有所區別。對于金屬涂層,其抗熱腐蝕性能與涂層表面形成連續致密的Al2O3保護性氧化層密切相關。李玉春[26]采用埋鹽法對K488合金及其表面滲鋁和滲鈷鋁涂層的K488合金的熱腐蝕行為進行研究,發現在900℃的25%NaC1+75%Na2SO4熔融鹽中滲鋁涂層表面生成了Al2O3和CoCr2O4的混合物,由于混合氧化物的存在使得耐腐蝕性提高,而滲鈷鋁涂層由于表面生成致密的Al2O3保護性氧化膜,表現出優異的抗熱腐蝕性能。李艷明等[27]針對燃機葉片常用材料DSM11鎳基高溫合金,在其表面制備了Al-Si、Al和Co-Al這3種涂層,并通過在涂層表面涂鹽(質量分數為5%NaC1+95%Na2SO4),研究了3種涂層在900℃的熱腐蝕性能,如圖2所示。研究結果表明,3種涂層的動力學曲線基本相似,均呈拋物線形,隨腐蝕時間的延長,質量先增加后減少。產生上述質量變化的原因在于:在腐蝕實驗前期(0~25 h),腐蝕產物與涂層結合緊密,腐蝕產物脫落較少;而在腐蝕的中、后期,表面腐蝕產物脫落,重新裸露出的內部涂層或基體進一步發生熱腐蝕,質量減少。在900℃熱腐蝕200 h后,Al-Si涂層和Co-Al涂層表面腐蝕區均形成了以Al2O3為主的連續且致密的氧化層,抑制熱腐蝕的進行,具有較好的抗熱腐蝕性能;與Al-Si涂層和Co-Al涂層有所不同,Al涂層表面腐蝕區形成了混合型氧化層,熱腐蝕反應會持續進行,抗熱腐蝕性能相對較差。此外,劉德林等[28]對DZ22B合金以及表面帶有NiCoCrAlYTa涂層的DZ22B合金在950℃熱腐蝕試驗研究也證實了NiCoCrAlYTa涂層的抗氧化和腐蝕作用,是基于在涂層的表面形成致密的Al2O3或Cr2O3氧化膜,這些氧化膜作為氧的障礙層(屏蔽層)阻止基體進一步氧化或腐蝕。圖2 含Al-Si、Al和Co-Al涂層的DSM11合金熱腐蝕動力學和腐蝕產物[27]Fig.2 Hot corrosion kinetics and corrosion products of DSM11 alloy with Al-Si,Al and Co-Al coatings[27]與金屬涂層相似,熱障涂層的抗熱腐蝕性能很大程度上取決于表面形成的連續Al2O3或Cr2O3氧化物薄膜。如李發國等[29]在近期發表的關于航空發動機高溫涂層耐海洋大氣腐蝕研究進展中指出,YSZ的抗熱腐蝕效應主要來自致密的Al2O3,其中Cr、Ta、Y能穩定Al2O3的生成提高涂層的抗熱腐蝕性。而外來的Na、V和S則會引起Y元素生成YVO4,使得YSZ涂層退化。當Na2SO4熔鹽單獨存在時,其不與YSZ發生化學反應,腐蝕機理主要是Na2SO4熔鹽附著在YSZ孔隙和裂紋中,在反復的冷熱循環中由于膨脹系數差異導致的熱應力使YSZ涂層失效[20,21,22,23,24,25,26,27,28,30],從而使Na2SO4熔鹽通過TGO-YSZ滲透進入粘結層,與粘結層發生反應,在TGO層下生成疏松的硫化物層,TGO層與硫化物層之間存在裂紋[29],最終導致涂層剝落。當存在V2O5熔鹽時,其與穩定劑Y2O3發生反應生成YVO4,如方程(1)所示,YVO4樹枝晶生長產生裂紋擴展應力[28,30,31];此外,YSZ發生四方晶系到單斜晶系晶體結構的轉變,伴隨有3%~5%的體積膨脹,相變應力和生長應力耦合作用導致涂層開裂甚至剝落。圖3 YSZ、Gd2Zr2O7和YSZ/Gd2Zr2O7熱障涂層在1 000℃熔融硫酸鹽和釩酸鹽(55%V2O5+45%Na2SO4)的熱腐蝕行為[31]Fig.3 Hot corrosion behavior of YSZ,Gd2Zr2O7and YSZ/Gd2Zr2O7thermal barrier coatings in molten sulfate and vanadate(55%V2O5+45%Na2SO4) at 1 000℃[31]當Na2SO4與V2O5共存形成NaVO3時,如方程(2)所示,根據Lewis acid-base理論,相較于V2O5的酸性,NaVO3還具有堿性。因此,相較于純V2O5的腐蝕過程,當共存Na2SO4和V2O5,即NaVO3熔鹽時,腐蝕速率更快,YVO4樹枝晶尺寸更大,YSZ熱障涂層失效更快。為了進一步提高熱障涂層的性能,國內外學者對雙層結構熱障涂層進行了研究和設計,并對其抗熱腐蝕性能進行了評價。雙層結構熱障涂層主要應用于力學性能較差的新陶瓷材料,通過在粘結層與新材料陶瓷層之間制備一層YSZ涂層,以減少層間熱膨脹系數差異,緩解涂層內部應力。Ozgurluk等[31]研究了YSZ、Gd2Zr2O7和YSZ/Gd2Zr2O7熱障涂層在1 000℃熔融的硫酸鹽和釩酸鹽(55%V2O5+45%Na2SO4)中的熱腐蝕行為,如圖3所示。研究發現高含量的V2O5導致涂層損傷加速,YSZ/Gd2Zr2O7雙層結構熱障涂層的抗熱腐蝕性能更好。在YSZ涂層中腐蝕產物為單斜ZrO2和YVO4,而在Gd2Zr2O7和YSZ/Gd2Zr2O7熱障涂層中腐蝕產物為單斜ZrO2和GdVO4,ZrO2從四方晶系到單斜晶系晶體結構的轉變對涂層造成損傷,熔融鹽對涂層的柱狀形貌造成破壞,降低涂層隔熱效果。當渦輪葉片涂層因受熱腐蝕和機械載荷作用剝落后,暴露出來的高溫合金基體在燃氣和海洋環境中將進一步發生熱腐蝕[32]。目前,航空發動機渦輪葉片主要有DD6、CMSX-4、CMSX-10、PWA1484單晶高溫合金葉片,燃氣輪機渦輪葉片包括單晶、定向凝固以及鑄造高溫合金葉片,如IN-738、DZ125、K444、GTD-111、MD2等[33]。在高溫熱腐蝕環境下,單晶高溫合金表現出更強的抗熱腐蝕性能,具有較低的平均腐蝕速率。如DD15[34]單晶高溫合金在燃油與海水氣霧混合的高溫(900℃)腐蝕環境下,合金平均熱腐蝕速率為0.071 g/(m2·h),且腐蝕層無脫落。結合DD10與DSM11等單晶材料的研究表明[35],單晶高溫合金在經歷高溫熱腐蝕后,其腐蝕產物內部會出現連續層狀分布的Cr2O3、TiO2和Al2O3保護性氧化膜,這些材料表層的腐蝕產物會對基體起到了很好的保護作用,從而阻礙了熱腐蝕的進一步進行,提高了單晶材料的抗熱腐蝕性能。在低溫熱腐蝕環境下,Luthra[36]研究發現涂敷在鈷基高溫合金表面的Na2SO4為固態,大氣中足夠的SO3分壓可以使得NiO硫化生成NiSO4,這種化合物將與過量的Na2SO4反應形成液態共晶鹽,熔融的混合硫酸鹽通過溶解保護性氧化層,將反應物質通過腐蝕坑中的液體來快速傳輸,增大腐蝕速率。而在鎳基合金中,NiO的硫酸化相對較少。Lortrakul等[37]通過對CMSX-4表面涂敷Na2SO4,并在O2-SO2-SO3的氣氛下加熱至700℃發現,腐蝕5 h后XRD表明NiSO4已經消失,意味著低熔點共晶鹽已無法形成,然而在50 h后在外/內腐蝕層界面附近以及內腐蝕層/基體界面處觀察到明顯的硫化物富集區,表明低溫熱腐蝕的實質仍然是局部熔融區域的硫化氧化作用,與高溫熱腐蝕作用機理相似。相較于單晶高溫合金葉片,定向凝固高溫合金中存在少量的晶界,會引起合金抗熱腐蝕能力的下降。Kumawat等[38]對定向凝固CM247LC合金在950℃、不同鹽沉積量的情況下的熱腐蝕行為進行評估。與空氣中純氧化相比發現,合金在熔融鹽環境中經歷了加速的腐蝕降解,在最初暴露的0.5 h內,合金通過與熔融鹽中的氧元素反應生成Al和Cr的氧化物,表現為較低的腐蝕速率。此后,隨著氧通量的增加而進入腐蝕加速階段,腐蝕機制也由堿性腐蝕機制向酸性腐蝕機制轉變,由于硫的滲入,使得熱腐蝕行為能夠持續不斷進行。Yang等[39]針對定向凝固DZ125合金開展了850℃高溫熱腐蝕研究,合金的腐蝕層分為內外兩層,外層表現為氧化物NiO/Cr2O3/Al2O3的多孔層,而內層則是均勻的主要由Cr2O3組成的氧化物,如圖4所示。高溫熱腐蝕除了加劇定向凝固合金表面氧化物的形成外,還導致在亞表面形成了強度較低的γ'貧乏區,如圖4(b)所示,這也是高溫熱腐蝕導致合金機械性能退化的主要原因之一。相較于單晶和定向凝固高溫合金,鑄造高溫合金存在較多的晶界,氧化物、硫化物形成元素可沿著晶界快速擴散,加速熱腐蝕和氧化[40]。鑄造高溫合金在面對長時間的腐蝕過程時,硫元素沿著晶界擴散,由此引起的晶間脆性對其服役性能影響較大。如圖4(d,e)所示,IN-792鑄造高溫合金葉片[32]在服役了大約21 000 h后呈現出機械和化學損傷。其中,高溫熱腐蝕致使晶界存在Ti硫化物以及游離形式的硫元素,導致晶間脆化和裂紋擴展抗力降低。調查發現IN-792渦輪葉片上幾乎所有的裂紋都以沿晶方式擴展。鑄造高溫合金K35[41]在含NaCl混合鹽的高溫熱腐蝕下,原本致密的Cr2O3氧化層變得疏松,為氧與硫的擴散提供了快速通道。Fig.4 Hot corrosion characteristics of superalloys with different processing routes航空發動機渦輪盤采用的高溫合金為變形高溫合金(如Inconel 718、GH4169等)和粉末高溫合金(如RR1000、ME3、FGH96等)。變形高溫合金渦輪盤其服役溫度通常不高于650℃,而粉末高溫合金渦輪盤其服役溫度通常不高于750℃,在海洋環境-工況耦合下發生的熱腐蝕主要為低溫熱腐蝕。目前,國內外學者主要是通過將渦輪盤合金在一定質量分數配比的Na2SO4+NaCl或Na2SO4+NaCl+V2O5中進行熱腐蝕,結合對熱腐蝕層微結構和成分表征,來研究渦輪盤合金熱腐蝕機理。Mahobia等[42,43,44]對Inconel 718和GH4169合金的研究表明,在Inconel 718和GH4169合金熱腐蝕過程中,NaCl中的氯離子會破壞氧化物層并滲透到基體中,從而形成金屬氯化物MCl,隨后從表面蒸發形成凹坑,為腐蝕性介質的流動提供通道,隨后氯離子會誘導內部腐蝕,造成金屬元素的自維持氯化和氧化,而硫元素的侵入還會造成合金內部硫化,造成熱腐蝕加劇。如圖5(a)所示,隨著S元素的侵入,會造成GH4169中針狀δ相(Ni3Nb)的硫化并在腐蝕層內部富集。此外,反應生成的低熔點硫化物Ni3S2(熔點787℃)可與金屬Ni形成更低熔點的共晶體(熔點645℃),液態的硫化物共晶體可沿晶界向金屬內部浸透;此外,液態硫化物及其與Ni的共晶體比氧化物的晶體缺陷數高得多,為金屬的擴散提供了快速的通道,從而導致基體合金的迅速破壞。在Na2SO4+NaCl+V2O5中,IN718高溫合金的熱腐蝕主要是氧化過程和V2O5所造成的釩蝕,其熱腐蝕機理模型如圖5(b)所示。隆小慶[45]的研究中討論了液態V2O5在燃氣渦輪發動機的工作環境中具有強烈的熱腐蝕作用,其中V2O5主要來自合金材料本身或燃油,其所產生的釩蝕會破壞Cr2O3(或Al2O3)氧化膜的連續性、完整性,使氧化膜失去防護作用[46]。經過在Na2SO4+NaCl+V2O5介質中熱腐蝕后,合金表面經過Na2SO4的滲硫、酸堿熔融后原氧化層下的基體合金形成了貧鋁區或貧鉻區,不再形成保護性的氧化膜來修補已破壞的保護層,失去保護性的外層氧化膜由于Na2SO4的浸透而變得更加疏松多孔且易剝落,從而造成加速氧化。Pradhan[47]、Mahobia等[42]的研究表明,Inconel 718合金在Na2SO4+NaCl+V2O5腐蝕介質中的熱腐蝕比在Na2SO4+NaCl中更加嚴重。不同的釩酸鹽化合物的形成與Na2Cr2O7的形成一起發生,硫離子與鉻、鐵和鎳或其氧化物反應,形成硫化物。對于粉末高溫合金,其低溫熱腐蝕過程與變形高溫合金類似。除了對粉末高溫合金熱腐蝕層中氧化、硫化產物進行表征外,國內外學者還從氧化深度、表面腐蝕形貌、腐蝕坑深度/直徑來表征熱腐蝕過程的損傷演變。如圖6(a)所示,Encinas-Oropesa等[48]通過熱重分析儀、聚焦離子束(FIB)和掃描電鏡測量RR1000合金的氧化物厚度和確定氧化損傷特征,結果表明RR1000合金表面氧化形成的鉻/鈦氧化物厚度隨時間呈拋物線增長,熱腐蝕損傷程度隨鹽沉積速率的增加而增加,但隨著鹽沉積速率中Cl含量的增加而降低。Birbilis等[49]通過光學輪廓測量法量化分析Rene 104合金表面腐蝕坑的深度、等效直徑等特征尺寸演變,提出可以進一步建立插值經驗模型來研究腐蝕損傷的生長動力學。如圖6(b)所示,基于腐蝕坑深度的量化分析結果可以看出低溫熱腐蝕在大規模損傷積累之前會有一個潛伏期(約5.5 h),而腐蝕損傷的演變在現象上表現為選擇性碳化物氧化引起的點蝕,隨著熱腐蝕持續進行,合金表面由于缺乏氧化鉻,損傷由硫相關的腐蝕決定。在這種氧化、硫化的熱腐蝕過程中,NASA格倫研究中心的Gabb等[50]還發現腐蝕坑內的晶界往往會被優先侵蝕。圖5 變形高溫合金不同腐蝕介質下的熱腐蝕機理[42,47]Fig.5 Hot corrosion mechanism of wrought superalloys under different corrosive environments[42,47]圖6 粉末高溫合金熱腐蝕后的損傷程度演變[49-50]Fig.6 Evolution of the hot corrosion damage in powder metallurgy Ni-based superalloys[49-50]針對不同條件下熱腐蝕對渦輪葉片高溫合金疲勞性能的影響,諸多學者進行了探索與研究,其主要方法是通過對高溫合金預先進行熱腐蝕處理,然后再開展疲勞試驗。在大多數情況下,腐蝕坑擴展和裂紋萌生占據了熱腐蝕-疲勞壽命的大部分[51]。未熱腐蝕試樣的疲勞裂紋往往萌生于靠近合金表面/亞表面的缺陷并向內擴展,亞表面缺陷引發的裂紋是最主要的損傷機制;而熱腐蝕試樣的裂紋形核始于腐蝕產物剝落的多個表面位置,這些裂紋通常是由腐蝕期間形成的微裂紋合并而成。預先熱腐蝕試樣中的疏松腐蝕層和γ'貧乏層,降低了合金表面力學性能,從而影響疲勞裂紋的萌生過程[52]。通常,熱腐蝕可使低周疲勞壽命降低60%~98%,疲勞裂紋萌生與腐蝕坑的大小和間距密切相關[53]。此外,載荷條件對熱腐蝕-疲勞行為也有影響。如Brooking等[54]的研究表明,當單晶CMSX-4合金處于低溫熱腐蝕環境時,在疲勞載荷峰值處引入60 s的保載會降低其疲勞壽命,如圖7(a)所示。這是由于疲勞與低溫型熱腐蝕結合時,長時間保載過程可使裂紋張開,使腐蝕性介質擴散到裂紋尖端,導致裂紋尖端周圍的氧化程度增加,加速了疲勞裂紋擴展,從而導致疲勞壽命降低。Chapman等[55]對單晶CMSX-4合金腐蝕-疲勞的研究中,也發現了類似的結果。Yang等[39,56]對DZ125合金高溫熱腐蝕后低周疲勞行為的研究發現,長時間預腐蝕和疲勞過程中的長時間保載加速DZ125合金腐蝕-疲勞失效,表面腐蝕層開裂導致裂紋萌生是腐蝕-疲勞失效的主要原因之一,如圖7(b~d)所示。此外,DZ125合金的低周疲勞失效還與熱腐蝕引起的再結晶、試樣有效面積的減少有關。如圖7(e)所示,高溫熱腐蝕后低周疲勞載荷會引起合金表面保護性氧化層的破壞,促使再結晶發生,形成許多小晶粒。在低周疲勞載荷作用下,裂紋往往在這些再結晶晶界處萌生。綜上所述,熱腐蝕后渦輪葉片高溫合金的低周疲勞壽命下降與腐蝕坑、缺陷、氧化/硫化物的形成以及熱腐蝕侵蝕引起的再結晶等因素密切相關。國內外雖然針對渦輪葉片高溫合金熱腐蝕-疲勞性能開展了一定的實驗研究,一定程度上揭示了熱腐蝕對疲勞失效的影響。然而,這些實驗研究主要是基于對高溫合金進行預先熱腐蝕然后開展疲勞試驗[57,58],實驗條件與渦輪材料服役環境(即燃氣-海洋環境耦合的服役環境)有所不同,不能實時反映熱腐蝕與機械載荷的交互作用。通常,機械載荷的作用往往會加速熱腐蝕的發生,而熱腐蝕又將反過來促進渦輪材料在機械載荷作用下疲勞裂紋的萌生和擴展[8,59,60]。因此,開展熱腐蝕-疲勞載荷耦合作用下渦輪材料的疲勞失效機理和規律仍有待于進一步研究,且燃氣-海洋環境耦合作用下的測試裝備仍有待于發展[61,62,63]。此外,目前所開展的渦輪葉片高溫合金熱腐蝕-疲勞性能主要是其低周疲勞性能研究,對熱腐蝕-高周疲勞性能研究較少。熱腐蝕對渦輪葉片高溫合金高周疲勞失效的影響也很顯著[47]。對于渦輪葉片而言,由于其服役溫度高,熱腐蝕損傷嚴重,且其受到氣動載荷的作用而往往發生高周振動疲勞失效。開展渦輪葉片材料在燃氣-海洋環境耦合作用下的振動疲勞失效機理和規律研究對渦輪葉片的疲勞強度/壽命設計意義重大,也仍需進一步的研究。圖7 高溫合金熱腐蝕-低周疲勞失效機理[39,54-56]Fig.7 Hot corrosion-low cycle fatigue failure mechanism of turbine blade superalloys[39,54-56]與渦輪葉片高溫合金相似,熱腐蝕也顯著降低渦輪盤合金的疲勞壽命[64]。如圖8(a)所示,Inconel718合金在75%Na2SO4+25%NaCl和90%Na2SO4+5%NaCl+5%V2O5中預先熱腐蝕后,應變控制的低周疲勞壽命大幅降低,尤其是在較低的塑性應變幅度下疲勞壽命降低更為明顯,且在90%Na2SO4+5%NaCl+5%V2O5中預先熱腐蝕對疲勞壽命影響更大[43]。對Inconel 718合金和GH4169合金預先熱處理后,開展應力控制的高周疲勞實驗,發現預熱腐蝕樣品的疲勞壽命急劇降低[49],如圖8(b)所示。對于未進行熱腐蝕的GH4169合金,疲勞裂紋主要在表面的滑移帶中萌生,然后沿{111}滑移面擴展。與其他鎳基高溫合金的情況類似,在裂紋萌生位置周圍可以觀察到大量的解理面[65,66]。對于熱腐蝕后的GH4169合金,疲勞裂紋主要從表面的熱腐蝕層萌生,裂紋萌生區周圍形貌較為光滑,未觀察到晶體學解理面。此外,從斷口上可以看出,熱腐蝕層的結構比較松散,由于熱腐蝕層的剝落,在裂紋萌生區的試樣表面形成了凹坑,如圖8(c)中第5幅圖所示。當裂紋穿過熱腐蝕層時,疲勞裂紋擴展特征與原始GH4169合金一致,呈現穿晶擴展,在疲勞裂紋擴展區可以觀察到明顯的疲勞條帶。斷口分析表明,熱腐蝕主要影響GH4169合金的疲勞裂紋萌生過程,但對疲勞裂紋擴展沒有影響,因此熱腐蝕導致GH4169合金疲勞壽命的降低主要與疲勞裂紋萌生過程有關。圖8(d)示意性地說明了熱腐蝕影響GH4169合金疲勞裂紋萌生過程,熱腐蝕影響疲勞裂紋萌生的因素包括以下幾個方面:(1)表面熱腐蝕層/氧化層剝落,降低了試樣的有效承載面積,增加了實際應力。(2)氯化物的揮發導致腐蝕坑的形成,表面熱腐蝕層的剝落形成凸起和起伏,引起應力集中,從而加速疲勞裂紋萌生。(3)氧化層中形成的裂紋或氧化層中已存在的微裂紋在疲勞載荷作用下通過硫化物層擴展進入基體,最終引起疲勞斷裂。在這種情況下,由于疲勞裂紋萌生階段較短或沒有,疲勞壽命會大大降低。(4)硫化層的硬度較低,表明該區域的變形可能發展得更明顯,導致應變局部化并加速裂紋萌生。圖8 Inconel 718和GH4169合金熱腐蝕-疲勞性能研究[43-44,47]Fig.8 Hot corrosion-fatigue behavior of Inconel 718 alloy and GH4169 alloy[43-44,47]對于粉末高溫合金,Li等[67]分析了低溫熱腐蝕對FGH96合金在700℃時低周疲勞行為的影響。研究發現低溫熱腐蝕導致FGH96合金疲勞裂紋萌生位置由亞表面缺陷向表面腐蝕坑過渡,疲勞壽命的降低與腐蝕坑加速裂紋萌生和晶界性能的退化密切相關。Child等[68]研究了粗、細晶RR1000合金在不同腐蝕介質濃度時的熱腐蝕-疲勞行為。如圖9(a)所示,在富含SO2的環境中,標準濃度腐蝕介質及單次預先熱腐蝕情況下導致粗、細晶RR1000合金疲勞壽命均有所降低。對粗晶RR1000合金開展了在兩倍標準濃度腐蝕介質中的預先熱腐蝕,發現隨著應力降低,熱腐蝕導致疲勞壽命降低的幅度有所降低。此外,在部分粗晶RR1000合金試樣熱腐蝕過程中,在間隔分別為15和30 h后,補充添加腐蝕介質,結果表明在規定的時間間隔補充腐蝕介質似乎不會影響最低應力水平下的疲勞性能。Dowd等[69]還研究了帶缺口的RR1000合金熱腐蝕-低周疲勞行為。圖9(b)顯示了光滑試樣、缺口試樣和缺口+預先熱腐蝕試樣的疲勞壽命數據。由于缺口的應力集中效應,與光滑試樣相比,缺口試樣在所有試驗載荷條件下疲勞壽命均有所降低。缺口+預先熱腐蝕試樣疲勞試驗結果表明,在相同應力水平下,熱腐蝕顯著降低缺口試樣的疲勞壽命,且應力水平越高,疲勞壽命降低程度越大,降低幅度在1~2個數量級。圖9(c,d)表明,在疲勞循環過程中,保護性表面氧化層的破裂使含硫化物的基體材料暴露并進一步氧化。隨著硫化物氧化,表面的濃度梯度導致固溶體中釋放的硫沿晶界向下擴散,與Cr和Ti元素進一步反應,導致新硫化物沿晶界形成。當應力水平足夠高時,晶界硫化/氧化物開裂,導致晶粒脫落,加速裂紋的萌生和擴展。
Gabb等[70,71]對表面噴丸強化的ME3合金進行了熱腐蝕后的疲勞性能研究。研究結果表明,對于未噴丸強化的ME3合金,熱腐蝕使低周疲勞壽命降低了60%~98%,疲勞裂紋萌生與腐蝕坑的大小和間距密切相關。此外,溫度對于熱腐蝕下的疲勞裂紋萌生也有影響。高溫(704℃)時裂紋沿腐蝕坑周圍晶界萌生,低溫(204℃)時裂紋由腐蝕坑底部晶界萌生。噴丸處理減輕了204℃輕度熱腐蝕對疲勞壽命的影響,但在重度熱腐蝕ME3合金中,噴丸強化抑制疲勞破壞的效果不明顯。分析認為噴丸處理可在試樣表面形成殘余壓應力,能夠減輕腐蝕坑對疲勞壽命的影響。但由于腐蝕坑處的疲勞開裂,較長的腐蝕時間和高溫下的疲勞仍會導致噴丸試樣的疲勞壽命大幅降低。此外,Smialek等[72]研究了熱腐蝕對帶有Cr2AlC涂層的LSHR合金疲勞壽命的影響,研究結果表明,對合金進行熱腐蝕后,無涂層合金相較于未熱腐蝕時的壽命降低約93%,而有涂層合金壽命降低僅為約15%,表明Cr2AlC涂層有益于抵抗熱腐蝕-疲勞破壞。
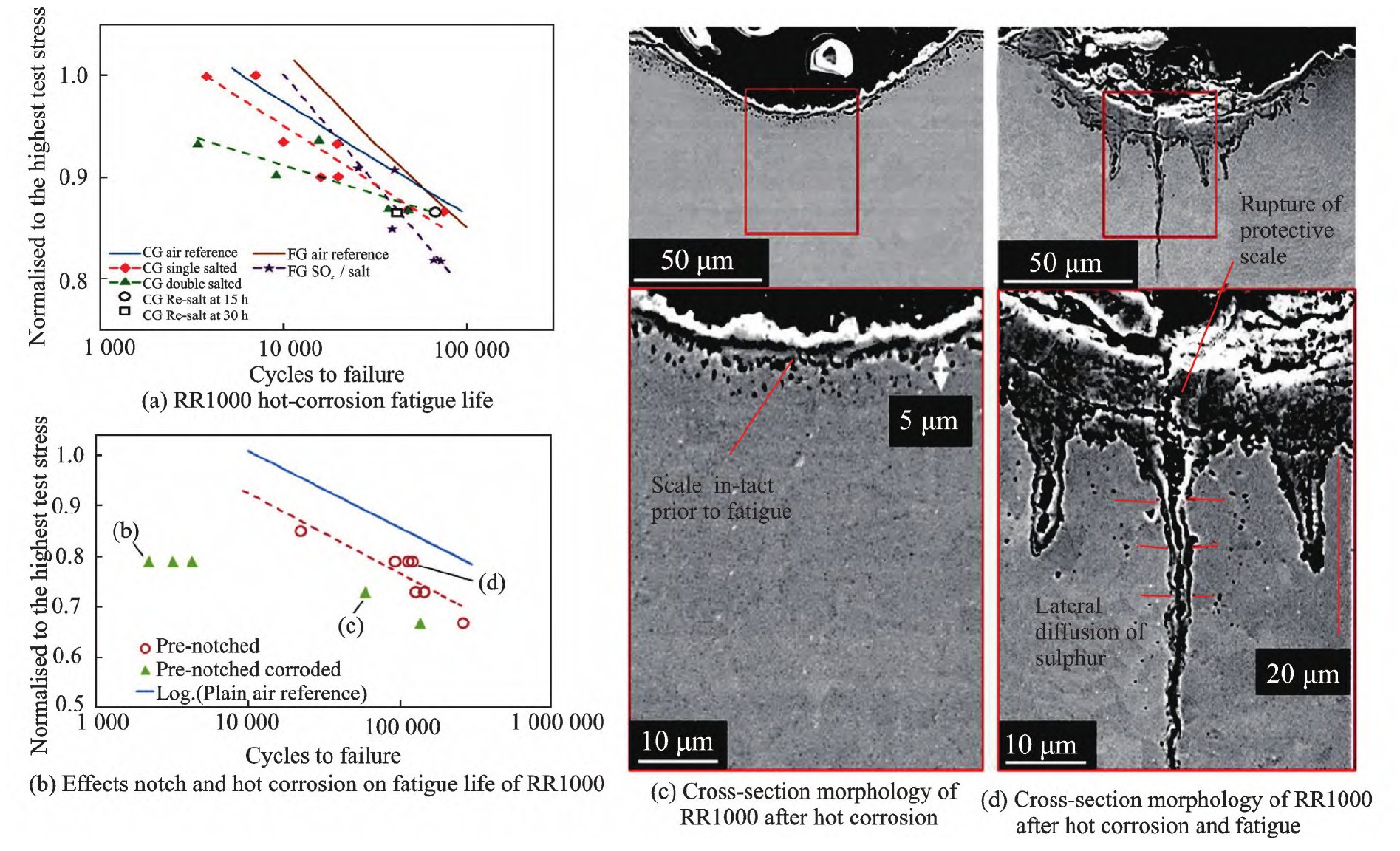
圖9 RR1000合金熱腐蝕-疲勞性能[68-69]Fig.9 Hot corrosion-fatigue failure mechanisms of RR1000 alloy[68-69]目前,關于熱腐蝕對渦輪盤合金疲勞性能的影響規律與機理有了較為清楚的認識,但與渦輪葉片高溫合金類似,現有的研究結果主要是基于對渦輪盤合金進行預先熱腐蝕然后開展疲勞試驗而獲得的,不能實時反映熱腐蝕與機械載荷的交互作用,因此,開展熱腐蝕-疲勞載荷耦合作用下渦輪盤合金的疲勞失效機理和規律仍值得進一步研究。此外,對于渦輪盤而言,為了提高渦輪盤損傷容限設計水平,以滿足高推重比航空發動機在海洋服役環境下耐久性、可靠性、安全性設計要求,需對渦輪盤用高溫合金在海洋環境-工況耦合下的疲勞裂紋擴展測試方法及微觀機理展開深入研究,為航空發動機渦輪盤材料的疲勞裂紋擴展壽命預測方法及損傷容限設計提供數據和技術支撐。高溫熱腐蝕環境下的疲勞過程同時受到載荷、溫度和腐蝕介質3方面的影響,其作用更加復雜,損傷過程分為熱腐蝕坑的萌生和生長、熱腐蝕坑向疲勞裂紋轉變、疲勞裂紋萌生、小裂紋擴展、長裂紋擴展和斷裂[73,74]。在這些損傷過程中,熱腐蝕坑的萌生和生長以及裂紋萌生和小裂紋擴展占據了疲勞壽命的絕大部分(70%~80%)。在熱腐蝕-疲勞模型研究方面,高溫熱腐蝕-疲勞壽命預測模型需要考慮溫度、載荷水平、介質濃度等許多方面的因素。目前常用的疲勞壽命預測模型主要包括唯象模型、損傷力學模型和斷裂力學模型[75,76]。唯象模型主要是基于對熱腐蝕損傷特征的表征,對應力或應變-壽命方程進行一定程度的修正;損傷力學模型主要是通過對熱腐蝕損傷的表征,建立耦合熱腐蝕損傷和機械載荷損傷的損傷變量,建立損傷變量演化和疲勞壽命之間的關系;斷裂力學模型是將熱腐蝕損傷視為初始裂紋,采用斷裂力學理論對剩余壽命進行預測和評定。然而,熱腐蝕-疲勞壽命預測的唯象模型、損傷力學模型和斷裂力學模型各有優缺點。唯象模型簡單且能較準確預測熱腐蝕-疲勞壽命,但其不能體現熱腐蝕-疲勞機理且其預測精度依賴于大量的實驗數據;損傷力學模型同樣可以獲得較為精準的預測結果,但其往往局限于一些簡單的結構;斷裂力學模型可用于復雜結構,但其未考慮裂紋萌生階段的疲勞壽命,因此預測結果往往偏于保守。近期,趙高樂等[75]在綜述中對熱腐蝕-疲勞壽命模型做了系統的總結和歸納,因此,下文著重針對近10年關于渦輪葉片和渦輪盤合金熱腐蝕-疲勞壽命預測方法進行總結。鑒于目前文獻中關于渦輪盤、渦輪葉片高溫合金熱腐蝕-疲勞壽命預測和分析均未考慮高溫合金的微結構特征,并且用于描述高溫合金變形的本構方程皆為宏觀唯象本構。因此,本節對熱腐蝕-疲勞壽命預測方法的總結和介紹不再區分渦輪盤合金和渦輪葉片合金。近年來,在NASA的資助下,美國Elder研究院(ERI)和西南研究院(SwRI)Chan等[77]開發了一套基于物理的建模工具HOTPITS,用于預測鎳基高溫合金的熱腐蝕[78]和低溫熱腐蝕壽命預測,并將其與概率損傷容限分析軟件DARWIN結合使用,用于預測發動機輪盤中因腐蝕坑引起的疲勞失效,其示意圖如圖10所示,主要步驟包括:(1)硫酸鹽沉積模型,用于根據燃料和空氣中污染物濃度的輸入以及相關發動機條件預測熱端部件上硫酸鹽層的形成;(2)用于預測熱腐蝕坑密度的熱腐蝕坑萌生模型;(3)用于預測熱腐蝕坑大小隨時間變化的熱腐蝕坑生長模型。同時針對熱腐蝕往往伴隨有多個熱腐蝕坑形成的情況,還進一步發展了考慮熱腐蝕坑合并的模型,以處理多個腐蝕坑的生長與合并。為了在熱腐蝕-疲勞壽命預測中考慮腐蝕坑的影響,建立了腐蝕坑到裂紋的轉化模型、疲勞裂紋形核模型、生長模型以及裂紋合并模型。通過將HOTPITS與DARWIN[79]軟件結合使用,Chan等以粉末高溫合金ME3為研究對象,發現了熱腐蝕坑生長和疲勞裂紋生長之間存在競爭,且低溫熱腐蝕疲勞壽命由熱腐蝕坑生長、循環相關的裂紋擴展以及時間相關的裂紋擴展共同控制,提出了一種預測粉末高溫合金渦輪盤腐蝕疲勞裂紋擴展壽命的概率預測方法,可用于評估渦輪盤中熱腐蝕引起的故障風險,避免發動機輪盤及其他金屬結構部件因長期暴露于高溫極端環境而發生腐蝕疲勞故障。Li等[80]提出了一種將FGH96合金中的腐蝕坑視為微缺口的腐蝕疲勞壽命預測方法,該方法考慮了熱腐蝕和非均勻應力場的影響。首先,對由粉末高溫合金FGH96制成的未涂鹽試樣和涂鹽試樣進行LCF測試,使用法拉第定律估計熱腐蝕坑形成時間。法拉第定律的表達式為
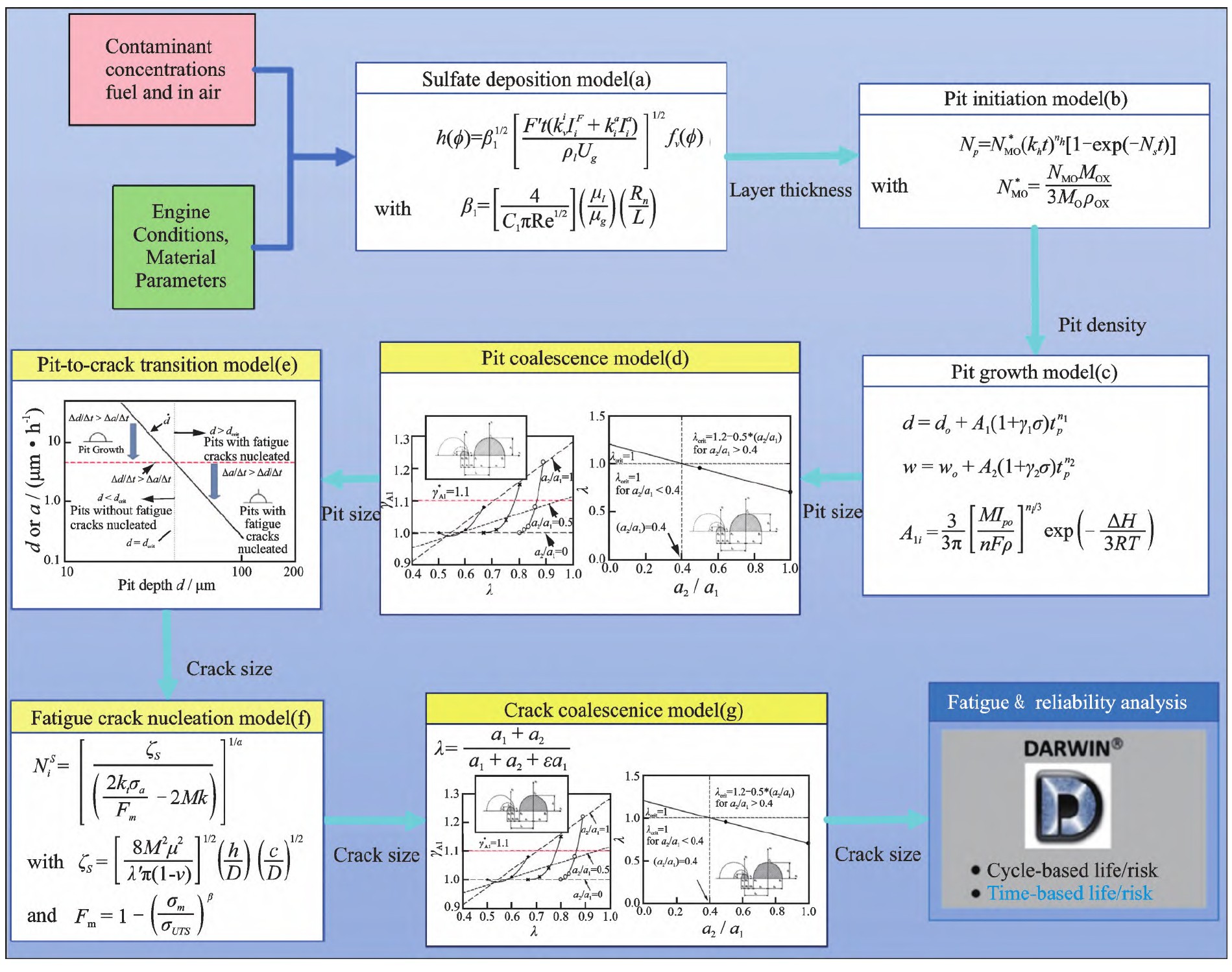
Fig.10 Schematic diagram of hot corrosion-fatigue prediction method

其次,使用傳統的經典方法預測熱腐蝕坑-疲勞斷裂壽命,包括熱點法、應變能模型、連續損傷力學(Continuum damage mechanics,CDM)法。對于熱點法,將最大應力點處的應變幅度引入基于總應變的模型;對于應變能模型,分別計算損傷參數并將其引入應變能模型;對于CDM方法,在CDM方法中使用了最大應力幅度。此外,定義了熱腐蝕-疲勞情況下的有效應變幅,有效應變幅可以通過將歸一化應力梯度和權函數的乘積積分來計算,表達式為

式中εa-eff和εa-max分別為缺口試樣的有效應變幅和最大應變幅。通過將定義的有效應變幅引入Manson-CoffinBasquin、Morrow、SWT和Walker模型,估算了從腐蝕坑形成到最終斷裂的疲勞壽命,并將實驗壽命與基于修改模型的預測結果進行了比較。結果表明,引入有效應變來考慮熱腐蝕坑引起的非均勻應力場的影響,有助于提高熱腐蝕-疲勞壽命預測精度,當臨界距離分別為0.1、0.2和0.3 mm時,大多數疲勞壽命預測結構在2倍誤差帶內,相同載荷下的預測壽命彼此接近,與實驗結果吻合良好。文獻[81]基于連續損傷力學和斷裂力學,針對表面熱腐蝕損傷引起的DZ125合金低周疲勞壽命退化,提出了一種新的壽命預測方法,如圖11(a)所示。通過Nf EA表面損傷區域的裂紋萌生和擴展的總壽命表征DZ125合金在不同熱腐蝕環境下的強度退化,Nf表達式為

式中Nf EA為表面損傷區域內裂紋萌生壽命(Ni)與擴展壽命(Np EA)之和,等同于此區域裂紋萌生壽命與裂紋擴展壽命之和,Nf EA通過用基體中的裂紋剩余擴展壽命Nf DS計算,有

式中:D表示損傷,M0、β和b為材料常數,α為載荷相關指數,Δσ為應力幅,σm為平均應力。通過Paris定律與Chaboche的疲勞損傷模型獲得NfEA,并通過實驗獲得的基體裂紋剩余擴展壽命Nf DS預測總的裂紋壽命模型。模型中熱腐蝕只在試樣表面進行,而不影響基體的開裂行為,在不同腐蝕環境下的裂紋萌生試驗修正模型系數,即可忽略環境和裂紋擴展的綜合影響進行壽命預測。通過一系列實驗數據,該模型在包括熱腐蝕、靜態空氣和濕H2S環境中都有較高的準確性,預測結果如圖11(b,c)所示。
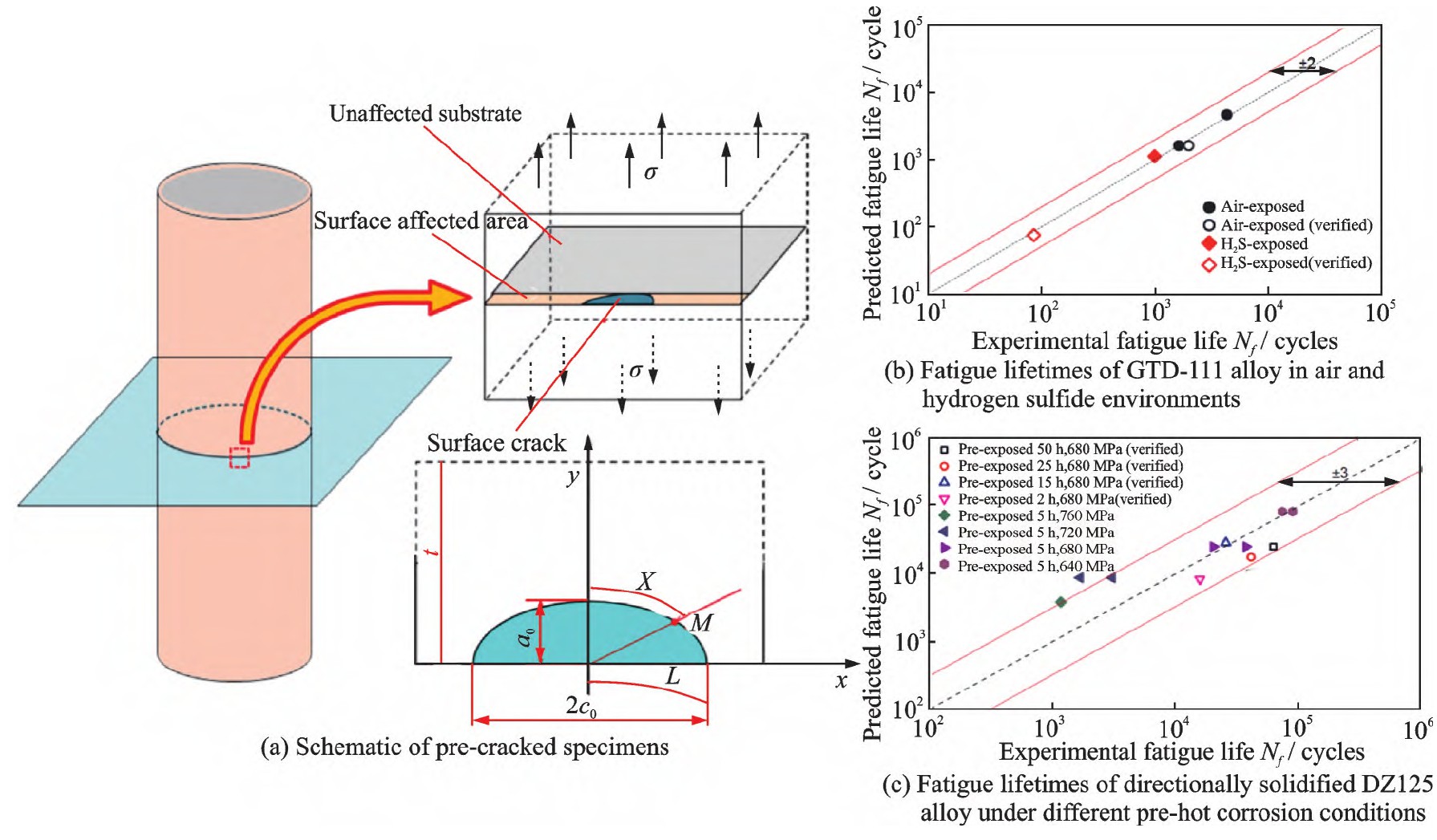
圖1 1 基于斷裂力學的熱腐蝕-疲勞壽命預測方法[81]Fig.11 Fracture mechanics based hot-corrosion fatigue life prediction[81]總的來說,目前基于唯象模型、損傷力學模型、斷裂力學模型的熱腐蝕-疲勞壽命預測精度在3倍分散帶之內。這些模型預測精度的提高一方面取決于對熱腐蝕損傷(如熱腐蝕坑形貌、尺寸等)的精確表征,以期更好地考慮熱腐蝕損傷所帶來的應力/應變梯度,另一方面取決于先進的材料本構模型,尤其是對于力學性能各向異性的單晶高溫合金,以更好地刻畫渦輪材料的應力應變響應,建立起更為準確的疲勞參量與疲勞壽命之前的量化關系。對于渦輪材料,由于其服役條件嚴苛,現階段仍較缺乏熱腐蝕-疲勞實驗數據。基于統計理論的機器學習可以在小樣本的條件下獲得較好的預測結果,且泛化能力強,對具有相同分布特征的樣本具有較好的預測能力。因此,近年來基于數據驅動的機器學習疲勞壽命預測模型/方法引起了人們的廣泛關注[82],比如Yang等[83]開發了結合臨界平面法和神經網絡的混合壽命預測模型,利用領域知識和機器學習在壽命預測中的作用,研究聚合物材料聚酰胺-6(PA6)的速率相關多軸疲勞壽命預測,預測結果基本在試驗結果的1.5倍誤差帶內。因此,建立基于人工智能(Artificial intelligence,AI)和大數據的熱腐蝕-疲勞損傷演化模型以及數據驅動和物理混合模型對于實現燃氣-海洋大氣耦合環境下航空發動機渦輪部件疲勞壽命精準預測具有重要意義,也是未來重要的發展方向。此外,為了滿足渦輪部件在燃氣-海洋環境耦合作用下的損傷容限設計需求,一方面要有大量的在燃氣-海洋環境耦合作用下的疲勞裂紋擴展數據,另一方面需要高精度的疲勞裂紋擴展模型和壽命預測方法。在腐蝕疲勞裂紋擴展模型方面,Larrosa等[76]對腐蝕-疲勞裂紋擴展宏觀唯象模型進行了較為全面的綜述,但這些模型對于熱腐蝕-疲勞的適用性仍需實驗數據的檢驗,同時,基于實驗數據的高精度宏觀唯象熱腐蝕-疲勞裂紋擴展模型仍亟待發展。此外,熱腐蝕-疲勞裂紋擴展過程復雜,為提高裂紋擴展速率預測精度,需考慮裂尖復雜的力學、化學的耦合作用。比如,Kashinga等[84,85]嘗試通過模擬裂尖變形和氧元素擴散,建立耦合裂尖非彈性塑性應變和氧濃度的裂紋擴展準則,結合擴展有限元模擬疲勞-氧化裂紋擴展。Pañeda等[86,87,88,89]嘗試將相場法和多物理場建模方法相結合,開展氫致裂紋擴展的數值模擬。通過對裂尖力學、化學耦合過程的準確模擬,以考慮環境/熱腐蝕對裂紋擴展的促進作用,以期實現高精度的疲勞裂紋擴展速率預測。目前,這些基于裂尖變形和熱腐蝕/氧化/環境損傷機理的高精度疲勞裂紋擴展速率預測方法仍需進一步發展,解決好精度與計算效率的匹配,從而推動其在工程中的應用。本文針對航空發動機和燃氣輪機熱端部件材料熱腐蝕機理、熱腐蝕-疲勞失效機理以及熱腐蝕-疲勞壽命預測進行了總結和綜述,并對航空發動機和燃氣輪機熱端部件熱腐蝕-疲勞試驗研究和壽命評估方法的發展趨勢進行了展望,主要有以下結論:(1)渦輪葉片常發生高溫熱腐蝕,形成均勻厚度的熱腐蝕層,單晶高溫合金相對于鑄造與定向凝固高溫合金具有較低的腐蝕速率。在葉片表面涂敷熱障涂層能夠形成氧、硫元素向基體擴散的屏障,起到對熱腐蝕的防護作用。渦輪盤服役溫度較葉片低,常常發生低溫熱腐蝕而形成局部點蝕坑,同時腐蝕也易于在點蝕坑內的晶界處繼續滲透腐蝕。點蝕坑不僅造成高溫合金表面力學性能退化,而且進一步影響部件的整體力學性能,具有相比普通氧化行為更為嚴重的影響。(2)熱腐蝕可使渦輪盤、渦輪葉片高溫合金疲勞壽命顯著降低(60%~98%),疲勞壽命降低程度與載荷條件有關,載荷水平越低,熱腐蝕對疲勞壽命的影響更為明顯。熱腐蝕加速渦輪盤、渦輪葉片高溫合金疲勞裂紋萌生過程,使疲勞裂紋萌生位置由亞表面缺陷向表面熱腐蝕坑過渡,疲勞壽命的降低與腐蝕坑的大小和間距以及晶界性能的退化密切相關。噴丸強化對抑制熱腐蝕-疲勞破壞的效果不明顯,但涂層能較好地提高高溫合金熱腐蝕-疲勞性能。(3)渦輪盤、渦輪葉片高溫合金熱腐蝕-疲勞壽命預測模型需要考慮溫度、載荷水平、介質濃度等許多方面的因素,常用的疲勞壽命預測模型主要包括唯象模型、損傷力學模型和斷裂力學模型,模型預測精度在3倍分散帶之內。然而,所采用的熱腐蝕-疲勞壽命預測和分析方法均未考慮高溫合金的微結構特征和熱腐蝕-疲勞失效機理。(4)為更準確表征渦輪盤、渦輪葉片高溫合金熱腐蝕-疲勞性能,亟需發展燃氣-海洋環境耦合作用下的疲勞測試裝備,開展機械載荷和海洋環境耦合的低周疲勞、高周振動疲勞以及疲勞裂紋擴展行為和機理研究,為渦輪盤、渦輪葉片疲勞壽命/強度設計以及損傷容限設計提供試驗數據支撐。在熱腐蝕-疲勞壽命預測方面,需發展基于高溫合金微結構和熱腐蝕-疲勞失效機理的預測方法、基于數據驅動和物理混合模型的預測方法以及考慮裂尖力、化耦合作用的熱腐蝕-疲勞裂紋擴展模型,提高熱腐蝕-疲勞壽命預測精度,建立燃氣-海洋環境耦合作用下的熱端部件結構完整性評定方法。