摘要
本文總結了第一代~第三代先進高強鋼的各自典型代表鋼種——相變誘發塑性鋼(TRIP鋼)、孿晶誘發塑性鋼(TWIP鋼)、淬火配分鋼(QP鋼)和中錳鋼的氫脆研究現狀和重要結果。主要結論為,TRIP鋼的氫脆敏感性主要體現在塑性降低,而強度損失不大。TWIP鋼的氫脆敏感性嚴重依賴于應變速率,即隨應變速率降低而顯著增加;形變孿晶界和ε/γ相界面易發生氫致開裂,而Σ3退火孿晶界不易開裂;深入研究表明,當ε/γ相界面滿足西山取向關系時,則與Σ3孿晶界類似,能夠阻礙氫致裂紋擴展,這一結論將不同學者的結果統一起來。QP鋼的氫脆敏感性與TRIP鋼相似。中錳鋼因含有較多的奧氏體相,變形時伴隨著強烈的TRIP效應,氫脆敏感性較大,既有明顯的塑性損失也有較大的強度損失。對含有奧氏體組織的TRIP鋼、QP鋼和中錳鋼等,調控奧氏體組織的形態和分布是改善其氫脆的主要對策;而對TWIP鋼則可通過控制預應變速率和Al合金化等措施來改善氫脆。
關鍵詞: 先進高強鋼 ; TRIP鋼 ; TWIP鋼 ; 氫脆
1875年,Johnson[1]發現鐵絲在酸中浸泡短暫的幾分鐘后韌性和斷裂應變劇烈降低,進一步觀察發現這種變化不是永久性的,因為“隨著時間的推移,金屬慢慢恢復原始的韌性和強度”;強度高的鋼浸入酸中的韌性損失大于強度低的鋼;同時通過對多種酸溶液的研究發現,只有與鋼發生反應并產生H的酸才會導致鋼的性能降低;此外,H必須是原子態的,而不是分子態,因為在H2 (氣態)中鋼的性質沒有任何變化。為了區分酸和H的影響,作者設計了一種僅用曼徹斯特城鎮用水進行電化學充氫的實驗,證明了只有釋放H的鐵電極發生脆化而沒有釋放H的位置不發生脆化。這篇140多年前的論文以精妙的簡單實驗抓住了脆化現象的本質,被認為是“氫脆”領域的起源和開篇之作。
在這之后,隨著鋼鐵行業的進步,鋼的強度不斷提高,人們針對鋼中氫脆問題開展了大量研究,形成了比較一致的認識:對具有單相組織的鋼來說,通常認為具有馬氏體組織的鋼氫脆敏感性高,奧氏體組織的鋼氫脆敏感性低。同時,普遍認為鋼的強度越高,氫脆敏感性越高,這顯然與目前超高強度鋼通常具有馬氏體組織,而具有鐵素體、奧氏體組織的鋼的強度一般較低有關。隨著鋼鐵材料的進一步發展以及汽車行業對鋼材的巨量消耗,人們對燃料消耗和溫室氣體排放日益關注,對行車安全性日益重視,從而發展了先進高強度鋼(advanced high-strength steel,AHSS)。自20世紀90年代初至今,大約每10年發展出新一代鋼[2],其中,第一代AHSS以鐵素體多相組織鋼為主,包括相變誘發塑性(transformation induced plasticity,TRIP )鋼、雙相(double phase,DP)鋼、復相組織(complex phase,CP)鋼,合金元素含量一般小于3% (質量分數,下同),因而材料的成本低,但是強度和延伸率也都比較低;第二代AHSS以具有奧氏體組織的孿晶誘發塑性(twinning-induced plasticity,TWIP)鋼為代表,因合金元素含量高(一般在15%~40%)而具有很高的強度和塑性,但是成本高、加工難;第三代AHSS則以具有復雜多相組織的淬火配分(quenching & partitioning,QP)鋼、中錳鋼和輕質鋼等為主要代表,合金元素含量一般為5%~12%,因而成本遠低于第二代AHSS,但性能又大大好于第一代AHSS,在成本與性能之間實現了良好的匹配。
與一般以馬氏體組織為主的超高強鋼相比,汽車用AHSS的微觀組織更復雜,且在變形過程中會產生相變(TRIP效應)或形成孿晶(TWIP效應),因而其氫脆行為和性能與以馬氏體組織為主的高強鋼有所不同。正是基于此,本文總結了幾種典型的AHSS的氫脆特征,主要包括第一代AHSS中的TRIP鋼,第二代AHSS中的TWIP鋼以及第三代AHSS中的QP鋼和中錳鋼。
1 TRIP鋼
1.1 TRIP鋼的微觀結構特點
在應力作用下,鋼中奧氏體相逐步發生馬氏體相變導致強度和塑性升高的超高強度鋼又稱TRIP鋼。TRIP鋼的典型顯微組織主要由鐵素體、貝氏體、殘余奧氏體和少量馬氏體組成。TRIP鋼的突出性能來自于鋼中多相組織的合理配比以及相變誘發塑性現象。馬氏體、貝氏體與合金元素固溶強化的共同作用獲得了高的強度,殘余奧氏體、貝氏體和鐵素體三相組織的優勢互補則產生了高的塑性。TRIP效應能提高加工硬化率和延緩頸縮,能有效地提高材料的強度和塑性,TRIP效應通常產生于變形過程中亞穩殘余奧氏體向馬氏體的轉變,與殘余奧氏體含量和穩定性有關[3,4]。有研究[5]表明,在平面應變拉伸中,奧氏體轉變為馬氏體比在雙軸拉伸和單軸拉伸條件下更為明顯。直接的γ→α′ (奧氏體→α′馬氏體)轉變使得從奧氏體到鐵素體的應變局部化,導致大量的位錯在鐵素體堆積,產生較高的背應力;多級轉變γ→ε→α′ (奧氏體→ε馬氏體→α′馬氏體)有助于強度和延性的良好結合;γ→ε轉變會導致奧氏體和鐵素體中產生少量的位錯增殖,而隨后的α′馬氏體相變提供了與位錯堆積有關的額外加工硬化能力[6]。模擬結果[7]發現,fcc→bcc轉變是自發的,而bcc→fcc轉變則需要較高的應力。這種不對稱性分別與fcc結構的Peierls應力(點陣阻力)和bcc結構的螺位錯相關。另外還發現,正向的fcc-bcc轉變對板條馬氏體的表觀塑性有顯著貢獻,納米尺度的奧氏體薄膜能顯著提高板條馬氏體的延展性和韌性[8]。
1.2 TRIP鋼中的H擴散行為
由于TRIP鋼含有奧氏體,變形時發生馬氏體相變,界面增多,而且H在奧氏體與馬氏體中的溶解度和擴散系數存在很大差異,因而H在其中的擴散富集勢必會受到影響。這方面學者們已做了大量研究。例如,Allen和Nelson[9]對TRIP鋼(TBF-980)和雙相鋼(DP-980)在充氫后不同時間進行了H濃度測試,發現2種鋼中的擴散氫濃度呈指數衰減,但TRIP鋼的衰減速率更快;同時在充氫后的短時間內2種鋼的擴散速率都呈現出各向異性,H通過<001>和<101>取向離開表面的速率快于<111>取向。Zhou等[10]研究發現,鋼的微觀組織對H的捕獲和擴散行為有很大的影響;相界面和殘余奧氏體都可以作為H的捕獲點,從而降低H在鋼中的擴散系數。此外,還發現殘余奧氏體在H捕獲行為中的作用取決于其形貌,薄膜狀的殘余奧氏體可作為可逆氫陷阱,而塊狀殘余奧氏體為不可逆性氫陷阱。Lu等[11]的研究發現,在H環境下,應變誘發的γ-α′馬氏體相變受到一定程度的抑制。Kim等[12]利用新的電化學滲透技術,成功地對TRIP鋼在加載條件下的H滲透電流變化進行了原位研究,發現發生馬氏體相變后,原始奧氏體基體中的H原子變成了可移動的H原子,這些H原子在塑性區附加載荷作用下,很容易擴散到新形成的馬氏體中,使得H原子的擴散速率加快,滲透通量增大。Ryu等[13]通過數學模型,定量預測TRIP效應導致的H脫附,發現相變導致陷阱結合能降低,從而提高H的表觀遷移率,使得含有奧氏體的TRIP鋼在變形過程中容易發生馬氏體相變,導致更嚴重的氫致塑性損失。而Hojo等[14]研究發現,變形引起的H脫附不僅是γ-α′馬氏體相變的結果,還是γ-ε馬氏體相變的結果,而且變形后α′馬氏體的H脫附量大于變形后的ε馬氏體。這表明H在ε相中的溶解度高于α′馬氏體,但低于奧氏體。
1.3 TRIP鋼的氫脆
TRIP鋼具有高的強度,因此它的應用不可避免地受到氫脆的限制。Zhu等[15]對市售TRIP 780鋼的研究發現,充氫5 min使鋼的延伸率由充氫前的34%降低到15.7%,即塑性損失達54%,而強度基本不受影響。TRIP 780鋼采用液氮低溫回火(CT)處理后,塑性損失減小至39%,氫脆敏感性得到改善,如圖1[15]所示。Yang等[16]發現,抗拉強度為1002 MPa的TRIP鋼,延伸率約為28.9%,充氫慢應變速率拉伸后延伸率降至約3.9%,即氫致塑性損失高達86.5%。Sun等[17]發現,充氫使臨界退火(IA)處理的TRIP鋼產生了較大的塑性損失和強度損失,其中IA800 (在800 ℃退火處理的TRIP鋼)充氫前抗拉強度高達1327 MPa,延伸率51.0%,充氫后強度下降為991 MPa,延伸率降至12.9%。Sojka等[18]研究發現,TRIP800鋼在含毒化劑的充氫溶液中塑性損失可達到88%。Laureys等[19]發現,抗拉強度約為700 MPa的TRIP鋼充氫后試樣的塑性損失高達75%,而同樣條件下純Fe的塑性損失僅為50%。
圖1 TRIP (相變誘發塑性) 780鋼在不同充氫條件下的工程拉伸應力-應變曲線[15]
Depover等[20]研究了包括TRIP鋼、DP鋼等4種高強鋼的氫脆。結果表明,TRIP鋼對H最敏感,塑性損失達到60%。與DP鋼相比,TRIP鋼的H擴散系數較低,對變形速率的依賴性較小。同時發現,充氫使缺口附近的斷裂特征由韌性斷裂轉變為穿晶解理斷裂。Zhang等[21]同樣發現,與未充氫試樣的韌性斷裂不同,充氫試樣在裂紋萌生區呈現脆性晶間斷裂和韌性晶內斷裂混合形貌,脆性斷裂面積隨臨界退火溫度的升高而增加。
Papula等[22]對氫致裂紋做了進一步研究,發現裂紋沿鐵素體和α'-馬氏體擴展。bcc晶體結構使H快速擴散到裂紋尖端區域,而在具有較高奧氏體穩定性的不銹鋼中沒有觀察到延遲開裂現象。由此可見,α'馬氏體的存在提高了氫致裂紋敏感性。Laureys等[23]研究了一種含有鐵素體、貝氏體、殘余奧氏體和一些馬氏體的多相組織的TRIP鋼,發現在樣品表面有典型的應力誘發氫致微裂紋。有限元模擬結果表明,觀測到的裂紋形態與缺口引起的應力增加區域相吻合。通過對氫致裂紋更深入的研究[24],發現TRIP鋼缺口試樣的氫致微裂紋呈S形,以穿晶方式擴展,如圖2[24]所示,通過逐步合并形成主裂紋并導致最終的斷裂。這些結果表明,氫致裂紋的產生與馬氏體有關,裂紋起源主要是由馬氏體引起的。氫致裂紋尖端周圍的高應變區表明,H促進的局部塑性變形可導致裂紋的進一步擴展。
圖2 Fe-1.6Mn-0.4Si-0.17C-(0.5~2)Al TRIP鋼裂紋沿馬氏體/鐵素體或馬氏體/貝氏體界面擴展[24]
奧氏體是γ-Fe中固溶少量C的固溶體,與鐵素體和馬氏體相比,能夠容納更多的H原子,成為更強的氫陷阱阻止H的擴散。因此奧氏體相對TRIP鋼的氫脆作用不容忽視。Zhang等[25]發現,與常規馬氏體鋼相比,TRIP馬氏體時效鋼由于具有殘余奧氏體/馬氏體層狀組織表現出優異的塑性和抗疲勞性能。軟的奧氏體區是裂紋擴展的優先路徑,但裂紋張開過程中的塑性變形導致馬氏體相變,相變引起的局部硬化會抑制隨后的裂紋擴展。裂紋沿著殘余奧氏體/馬氏體界面和穿過塊體邊界擴展形成一條鋸齒形的裂紋路徑。
Zhu等[15]的研究還發現,對TRIP 780鋼進行CT處理,可在基體中形成較多的薄膜狀奧氏體,因此降低了鋼的氫脆敏感性,同時發現裂紋起源于奧氏體相變產生的新鮮馬氏體。而Cameron等[26]的研究表明,由于微裂紋的成核和生長,馬氏體鋼中的長條狀奧氏體對氫脆性能的改善是有限的,因為先析出的大的α′馬氏體區使裂紋無約束的解理擴展,導致試樣斷裂失效,減弱了長條狀奧氏體對氫脆性能的改善。消除先析出的α′馬氏體區域能在保持強度提升的同時,使塑性進一步增加,進而提出了可以通過提高軋制壓下量實現組織均勻化,同時提高奧氏體穩定性以減少裂紋形核和擴展的方法。Laureys等[27]發現,環境中的H比內部的H更容易使TRIP鋼變脆。斷口分析和二次裂紋分析表明,在加載過程中連續供氫和H與位錯的相互作用在材料失效過程中至關重要。
總之,TRIP鋼氫脆敏感性主要表現為塑性損失,強度損失不大。氫致裂紋主要在馬氏體中或沿相界面形核。多數學者認同這樣的理由:變形過程中殘余奧氏體轉變為馬氏體,因奧氏體具有較高的H溶解度、而馬氏體的H溶解度低的多,當奧氏體將H遺傳給新形成的馬氏體時,可能會由于H的過飽和而富集進而導致氫致開裂。控制奧氏體形態保持長條狀甚至薄膜狀,或通過低溫回火處理,可以改善TRIP鋼的氫脆敏感性。雖然關于TRIP鋼的氫脆研究已經很多,但受檢測手段的限制,H與TRIP效應的相互作用機理、H與TRIP鋼中各組成相的相互作用機制以及奧氏體在發生TRIP效應后釋放H的方式等仍然不清楚,有待于深入研究。
2 高錳TWIP鋼
TWIP鋼是國內外目前正在積極研發中的第二代先進高強鋼,具有高強度(600~1100 MPa)、高塑性(延伸率可達到95%)和高應變硬化能力(加工硬化指數n>0.3,瞬時加工硬化指數可達0.7以上)[28]。高錳TWIP鋼在室溫無載荷狀態下是穩定的奧氏體組織,通過形變孿晶產生無縮頸延伸,具有優異的力學性能。然而,杯突實驗發現高錳TWIP鋼杯突邊緣易發生延遲開裂[29,30,31],延遲開裂的確切機制尚未確定,一般認為它與殘余應力存在下的馬氏體相變有關,還可能與H有關[32]。目前,對于高錳TWIP鋼氫脆研究主要集中在以下幾個方面:微結構演化特征對TWIP鋼氫致開裂性能的影響;合金元素的影響;H含量和應變速率的影響。
2.1 TWIP鋼的微結構演化與氫致開裂
氫致開裂具有組織敏感性,特別是微結構特征的演變對氫致裂紋的萌生與擴展起著至關重要的作用。對高錳鋼的氫脆,H的擴散與富集依賴于變形誘導的微結構演變(形變孿生、相變和位錯滑移等)過程中逐漸形成的微應力集中。高錳鋼在熱處理和加工過程中,孿晶(退火孿晶和形變孿晶)的出現是不可避免的,特別是在變形過程中產生的形變孿晶是其優異力學性能的根本保證,因此,了解孿晶對氫致開裂的影響至關重要。
孿晶分為2種:形變孿晶與退火孿晶。前者是在變形過程中形成的,通常處于奧氏體晶粒內部,與基體之間的界面上由位錯協調其共格關系[33];后者是在合金再結晶退火過程中形成的,與基體之間的界面通常呈現完整共格關系[34]。
研究[35,36,37]發現,在Mn含量較高的奧氏體鋼中,會出現沿形變孿晶界的氫致裂紋,這些裂紋以鋸齒形的方式沿一次形變孿晶和二次形變孿晶擴展。Koyama等[36,37,38]研究了Fe-18Mn-1.2C (質量分數,%,下同)高錳TWIP鋼形變孿晶對氫致開裂行為的影響,對經過預應變的試樣進行動態充氫慢拉伸,發現氫致裂紋優先于晶界及形變孿晶界起裂[38]。有研究[39]認為TWIP鋼中晶界本身就是H的可逆陷阱,有利于H的富集。在塑性變形過程中,當一次形變孿晶的生長受到晶界的阻礙后,在孿晶尖端裂紋就會沿晶界起裂和擴展;而二次形變孿晶的生長受到一次孿晶的阻礙時會導致裂紋沿孿晶界開裂。本課題組前期工作[40]對Fe-18Mn-0.6C的研究表明,在較快的應變速率(如1×10-5 s-1)下,TWIP鋼中更易形成形變孿晶。形變孿晶與晶界交互作用會產生應力或應變集中,從而導致H在晶界處富集,進而促進氫致裂紋萌生,如圖3[40]所示。而在較慢的應變速率(1×10-6 s-1)下,位錯面滑移會攜帶H原子向晶界位置運動,使得晶界處富集更多H,最后導致沿晶開裂[40]。總體來看,高錳TWIP鋼的氫致裂紋易沿形變孿晶開裂。
圖3 應變速率為1×10-5 s-1時Fe-18Mn-0.6C TWIP (孿晶誘發塑性)鋼的氫致裂紋萌生[40]
Kwon等[41,42]通過不同熱處理工藝獲得不同體積分數Σ3晶界的TWIP鋼,發現提高Σ3晶界的體積分數可降低氫脆敏感性。本課題組前期工作[43]通過晶界設計,制備出了Σ3晶界體積分數為13.4%~40.7%的8種試樣,發現提高Σ3晶界體積分數可以提高TWIP鋼的抗晶界腐蝕性能。因此,Σ3晶界對改善氫致開裂和晶間腐蝕是有益的。
前文提到,高錳TWIP鋼在室溫下為穩定的奧氏體組織。當高錳鋼成分發生變化時,層錯能就會發生變化,當層錯能小于15 mJ/mm2時會發生α'和ε馬氏體相變[44]。有H存在時,奧氏體穩定性降低,α'馬氏體相變幾率增加。研究[45]發現,在α'馬氏體相位置容易發生氫致開裂。因此在高錳TWIP鋼中,α'馬氏體對抗氫脆性能起負面作用。
關于ε馬氏體對高錳鋼氫致開裂的影響可以分為ε馬氏體自身和ε/γ相界面2方面。Chun等[46]研究了含有不同ε馬氏體體積分數的高錳TWIP鋼的抗氫脆性能,發現ε/γ相界容易開裂,引發嚴重的氫脆現象。而Lee等[47]認為,H更易處在奧氏體或ε馬氏體板條中,而不是聚集在ε/γ相界上,與Chun等[46]的結論相反。本課題組前期工作[40]對此現象進行了深入研究,認為ε/γ相界面不能一概而論。分析發現,滿足[110]γ //[21?1?0]ε關系即西山取向關系的ε/γ相界面,能夠阻礙氫致裂紋的擴展,抑制氫脆,如圖4[40]所示。而不滿足這一關系的ε/γ相界面則容易發生氫致開裂。這是因為滿足[110]γ //[21?1?0]ε關系的ε/γ界面原子排布與Σ3晶界相似[40]。這樣就可以理解Chun等[46]和Lee等[47]得出相互矛盾的結果的原因了。
圖4 應變速率1×10-6 s-1時Fe-18Mn-0.6C TWIP鋼的氫致裂紋萌生[40]
高錳TWIP鋼的屈服強度較低,有研究[44,48]通過沉淀硬化相(κ-carbide)來提高Fe-C-Mn-Al系高錳鋼的屈服強度。由于高錳鋼中的C和Al含量較高,熱處理后會形成鈣鈦礦結構的沉淀相[49,50],可顯著提高其屈服強度,但存在沉淀相的高錳TWIP鋼容易發生氫致沿晶開裂[51]。沉淀相附近的局部滑移導致晶界處形成微孔洞,H促進微孔洞長大與聚合[52],從而導致微觀上韌性而宏觀上脆性的斷裂。
2.2 合金元素對TWIP鋼氫致開裂的影響
合金元素是TWIP鋼合金化設計的重要環節,同時也是改善抗氫脆性能的重要途徑。Al、Si、Cu和P等元素均對TWIP鋼氫脆性能有影響。
添加Al元素可以改善TWIP鋼的延遲開裂早已得到公認,Al對杯突實驗后杯口開裂的抑制作用就是最直接的證據[29,53]。為了進一步明確Al對TWIP鋼氫致延遲開裂也就是氫脆的影響,Ryu等[39]對比研究了無Al和添加1.5%Al的高錳鋼Fe-0.6C-18Mn-0/1.5Al,發現添加1.5%Al可使充氫后的塑性損失由62%降低到48%,并且斷口上的脆性區明顯減小。Dieudonné等[54]也獲得了添加Al有益于改善抗氫脆性能的結論。另外還有研究[55]表明,添加2%Al,長時間陰極充氫后在鋼的次表面會形成一層α-Al2O3薄膜,這層膜能阻礙H原子進入,從而改善沿晶開裂性能。
馬氏體相變、形變孿晶和應變時效都有助于氫致裂紋的萌生,而Al能增加TWIP鋼的層錯能進而抑制ε馬氏體相變和形變孿晶[56,57,58]。另一方面,層錯能增加容易發生交叉滑移,抑制位錯堆積和H的局部富集[59]。因此,Al的添加降低了TWIP鋼的氫脆敏感性。
現有文獻資料中,關于合金元素Si對TWIP鋼抗氫脆性能影響的工作很少。Lee等[47]研究表明,不含Si的TWIP鋼在充氫后只有fcc結構的(Fe, Mn)O氧化層,而含有Si試樣在充氫后除了(Fe, Mn)O外,還會產生斜方結構的(Fe, Mn)2SiO4 氧化層,這種斜方結構的氧化層可以有效抑制H進入材料內部,從而起到改善氫脆的作用。但是Si是降低層錯能的元素,當含量達到0.3%時,會發生ε馬氏體相變,而ε馬氏體容易引發氫致開裂。此外,Dieudonné等[60]研究了Cu的影響,結果表明,在TWIP鋼中添加Cu能夠提高材料的抗延遲開裂性能。P元素的作用依賴于Al的存在:對于含Al的TWIP鋼,P元素會嚴重增加其氫脆敏感性;不含Al的TWIP鋼的延伸率基本不會因P的存在而降低[60]。因此,P的存在會抵消Al對抗氫脆性能的積極作用,導致Fe-Mn-Al-C系TWIP鋼的脆化敏感性更高。
2.3 應變速率對TWIP鋼氫致延遲開裂性能的影響
本課題組前期工作[40]表明,當應變速率由1×10-5 s-1降低到1×10-6 s-1時,全奧氏體組織Fe-18Mn-0.6C TWIP鋼動態充氫拉伸的塑性損失由64%增加到94%,即隨應變速率降低,氫脆敏感性顯著增加,如圖5[40]所示。與Bal等[61]發現的結果相同。Koyama等[31]發現,用很小的電流密度(如1 A/m2)對Fe-18Mn-0.6C鋼進行原位電化學充氫慢應變速率拉伸(5.1×10-5 s-1)時,材料的力學性能與不充氫變化不大,因為充氫僅導致H富集在試樣表面很淺(幾個微米)的區域,不足以顯著惡化試樣整體的力學性能。但是當降低應變速率時,H能借助位錯的遷移作用而擴大在材料中的影響區域,導致充氫前后延伸率發生顯著變化。這些研究表明,在H作用下的位錯運動是應變速率依賴的關鍵因素。由于位錯和可擴散氫運動存在競爭關系[62,63,64],當降低應變速率時,H能夠跟隨位錯一起運動。同時,應變速率的降低導致H有充裕的時間向晶界等位置聚集。因此,隨著應變速率的降低,TWIP鋼的氫脆敏感性顯著提高。
圖5 Fe-18Mn-0.6C鋼在2種應變速率下的動態充氫拉伸曲線[40]
此外,Koyama等[65]研究了“預應變速率”對高錳鋼氫致延遲開裂的影響。在無H條件下,以不同的預應變速率拉伸到應變為69%時停止,保持該位移狀態,充氫。如果在10 h內試樣未發生延遲斷裂,則將試樣再次以最初的應變速率拉伸直至斷裂。結果顯示,在較慢預應變速率(1.7×10-5和1.7×10-4 s-1)下能夠發生氫致延遲斷裂,而在較快預應變速率(1.7×10-3和1.7×10-2 s-1)下不發生氫致延遲斷裂。因此,通過增加預應變速率可以抑制氫致延遲斷裂。作者認為這與C的應變時效有關。
總之,盡管H在TWIP鋼中的擴散系數很小,但由于變形過程中會產生形變孿晶或ε-馬氏體,有H存在時容易造成TWIP鋼的延遲開裂,塑性和強度均顯著降低。一般認為,TWIP鋼中的Σ3晶界對改善氫致開裂有益處,ε/γ相界面則易發生開裂。本課題組的研究[40]表明,滿足[110]γ//[21?1?0]ε即西山取向關系的ε/γ相界面與Σ3晶界相似,能夠阻礙氫致裂紋的擴展,有益于TWIP鋼的抗氫脆性能。添加合金元素Al、增加應變速率可降低TWIP鋼的氫脆敏感性。
3 QP鋼
3.1 QP鋼的微觀結構特點
正如前文所述,第一代AHSS強度高但塑性相對較低,限制了其在復雜形狀汽車零件上的應用;第二代AHSS雖然同時具有高的強度和大的塑性,但由于合金元素含量高,不僅造成了高成本,也給批量生產和焊接方面帶來困難,因此阻礙了其在汽車上的推廣應用。因此,以QP鋼和中錳鋼為典型代表的第三代AHSS引起了廣泛關注,因為它們的材料成本大大低于第二代AHSS,而機械性能又比第一代AHSS好得多,在成本與性能之間有很好的折衷。
QP鋼由Speer等[66]在2003年提出,也稱淬火延性鋼。典型成分范圍為Fe-(0.2~0.3)C-(1~1.5)Si-(1~3)Mn[69,70,71]。QP指的是一種淬火配分的生產工藝,與傳統的淬火回火(quenching & tempering,QT)工藝獲得碳化物從而提高韌性不同,QP工藝是通過配分處理得到富C奧氏體而不形成碳化物。具體工藝為:先將試樣加熱到兩相區(鐵素體+奧氏體)或完全奧氏體區保溫一段時間,然后淬火到介于馬氏體轉變起始溫度(Ms)和馬氏體轉變終止溫度(Mf)之間的某一溫度。隨后,樣品在這個溫度或更高溫度下保存,促進C從馬氏體向奧氏體的擴散,提高奧氏體的穩定性,使其在室溫下得以保留。最后得到貧C的馬氏體基體和富C殘余奧氏體多相組織相互配合的微觀結構。QP工藝的關鍵在于控制配分過程,使得C配分和富集達到預期的奧氏體穩定水平。馬氏體保證鋼的強度,殘余奧氏體在形變過程中發生相變,提高了鋼的塑性。與傳統的高強鋼相比,QP鋼成本低廉,且具有較高的強塑積,強度最高可以達到1500 MPa,而延伸率仍能超過15%。
3.2 QP鋼的氫脆及微觀組織的影響
QP工藝帶來高強度的同時,不可避免地易受到H的影響。Liu等[72]發現,H固溶軟化導致QP鋼屈服強度降低13%,頸縮后的塑性區面積從65%降至9%。Zhu等[73]對Fe-0.22C-1.40Si-1.80Mn鋼進行淬火配分處理,引入1.5×10-6 H后,總延伸率由19.5%急劇下降到2.5%,但強度幾乎不受影響,如圖6[73]所示。通過對斷裂方式的進一步研究,他們發現H使斷口特征從韌性微孔聚集的韌窩斷裂向“準解理”區和沿晶開裂混合形態轉變。氫致裂紋在馬氏體/奧氏體界面處萌生,然后通過殘余奧氏體和馬氏體擴展,而在鐵素體相中沒有觀察到裂紋,如圖7[73]所示。Liu等[74]同樣發現H改變了QP鋼的斷裂模式,有H后,斷裂主要發生在馬氏體/馬氏體(M/M)界面或馬氏體/奧氏體(M/γ)界面。Wang等[71]研究了QP980和QP1180鋼的氫致延遲斷裂,發現氫致裂紋在殘余奧氏體或應變誘發的新鮮馬氏體等敏感區域形核,并傾向于沿原奧氏體晶界和馬氏體晶界擴展,鋼中的鐵素體可以用來鈍化氫致裂紋,并中斷原奧氏體晶界和馬氏體界面的連續性。QP980鋼具有較高的鐵素體體積分數、不連續的原奧氏體晶界和馬氏體界面,是其具有較好的抗氫致延遲斷裂性能的主要原因。
圖6 Fe-0.22C-1.40Si-1.80Mn QP (淬火配分) 980鋼在不同H含量下的工程應力-應變曲線[73]
圖7 Fe-0.22C-1.40Si-1.80Mn QP鋼中氫致裂紋的形核和擴展[73]
此外,有學者試圖對QP鋼微觀組織與H的相互作用進行研究,如Yang等[75]通過對比研究QP鋼和QT鋼,發現QP鋼的氫脆比QT緩和,因為QP鋼中的殘余奧氏體可以阻止H擴散,增加H的溶解度,提高了QP鋼的抗氫脆性能。同時細化顯微組織后單位面積H含量較低,可進一步提高塑性。Zhu等[70]研究發現,低溫回火使ε碳化物在QP鋼馬氏體基體中析出,作為氫陷阱可捕獲晶格中的H原子,降低擴散氫含量,從而提高QP鋼的抗氫脆性能。Liu等[76,77]研究了H在QP鋼中的滲透行為和可逆氫陷阱密度,發現充氫電位越負,氫陷阱效應越不明顯。由以上介紹可知,對QP鋼中H與微觀組織的相互作用,目前尚停留在實驗現象的描述上,并未真正從微觀上解釋清楚各種組織與H是如何相互作用的。因此弄清H在各種微觀組織中擴散、富集的情況,以及在應力狀態下的重新分布與富集,有助于理解氫致裂紋的形核與微觀組織的關系,進而推進對QP鋼的氫脆機制的研究。
3.3 改善QP鋼抗氫脆性能的方法
為了改善QP鋼的氫脆現象,學者們采用了不同的處理方法。Yang等[78]提出了一種淬火-配分-回火(QPT)工藝,通過引入鐵素體相以降低低碳鋼氫脆敏感性的方法。結果表明,鐵素體可以降低馬氏體相變引起的應力集中,延緩變形過程中的裂紋擴展。細化的組織可以在界面處捕獲更多的H,降低H在晶格中的濃度,進一步提高抗氫脆能力。同樣,Zhu等[70]研究發現,在QPT鋼中出現了ε-碳化物,在回火處理后,充氫后總延伸率損失由42.7%降至0.6%。通過熱脫附光譜分析和三維原子探針檢測表明,碳化物對H有較高的捕獲能力。另外Zhu等[79]通過對比高強度鋼在臨界退火淬火配分(IAQP)、QP和QT 3種不同熱處理條件下的氫脆敏感性,發現QP工藝形成的薄膜狀的奧氏體比塊狀奧氏體具有更低的氫脆敏感性。Zhou等[80]用電沉積法在QP鋼基體上制備了純Ni、Ni-MoS2和Ni-石墨烯涂層,并與鍍鋅層進行了比較。結果表明,鍍鋅層和鎳基及鎳基鍍層均能降低H滲透電流,Ni-石墨烯涂層在QP鋼中具有最慢的析氫動力、最小的穩態滲透電流密度和最小的H擴散系數,因而表現出最好的抗氫脆性能。
綜上,QP鋼作為第三代先進高強鋼的代表鋼種之一,成本低廉的同時擁有較高的強塑性配合。QP工藝的研究重點主要集中在配分過程,包括配分前的組織形態,配分時的工藝參數,以及配分后的各相組分和形態的變化。與TRIP鋼相似,QP鋼的氫脆主要表現為塑性損失,強度損失較小。目前的研究主要集中于氫致裂紋起源和擴展與微觀組織及形態的關系,氫致裂紋主要沿應變誘發的新鮮馬氏體或M/γ界面形核。在合金成分被基本框定的條件下,改善QP鋼抗氫脆性能的方法主要是通過控制淬火配分工藝參數(溫度和時間)獲得一定含量、且具有相當穩定性的奧氏體相,特別是控制奧氏體的微觀組織形態,使其盡可能保持為在馬氏體板條間的長條狀甚至是薄膜狀,以作為H的儲存“容器”并阻礙H的擴散,這一點與改善TRIP鋼氫脆的措施一樣。此外,到目前為止,H與QP鋼中各種微觀組織的相互作用、H對馬氏體相變的影響、QP鋼的氫脆機制等還不十分清楚,有待進一步研究。
4 中錳鋼
除了上文的QP鋼,中錳鋼是第三代先進高強鋼的另一主要代表。關于中錳鋼的研究進展,本課題組曾專門對其研究現狀、成分設計、微觀組織、熱處理工藝、力學性能等進行了綜述[81],本文在簡要介紹其微觀組織后,重點介紹中錳鋼的氫脆研究狀況。
4.1 中錳鋼的微觀結構特點
“中”錳鋼是相對于TWIP鋼的高Mn含量來說的。中錳鋼的主要成分特點是低碳中合金鋼,與傳統TRIP鋼的不同點在于,傳統TRIP鋼Mn含量約1.5%,利用C、Si和Al提高奧氏體穩定性,這種元素組合獲得的奧氏體含量較少,一般在20%以下[82],因而TRIP效應相對較弱。中錳鋼通過添加5%~12%的Mn,使得室溫下鋼中奧氏體的含量可達40%以上[83],成為基體組織,從而在變形過程中獲得持續的TRIP效應,因而抗拉強度可達700~2000 MPa、延伸率可處于20%~85%的寬泛范圍[84,85,86,87,88,89,90,91],強塑積可達30~70 GPa·%。另外,添加合金元素Al、Si,會使微觀組織中出現尺寸較大的δ-鐵素體,影響中錳鋼的力學性能。
中錳鋼的軋制工藝主要為熱軋[92]、溫軋[93]和冷軋[94],后期熱處理大多采用兩相區臨界退火處理[95]或淬火配分處理等[96,97]。經過熱軋-退火或溫軋-退火之后,材料的組織主要呈現細小的、條狀的逆變奧氏體和鐵素體[92,93];由于臨界退火的溫度已經進入兩相區,比一般的回火溫度高,所以經過冷軋-臨界退火之后,晶粒發生部分回復再結晶,導致材料的組織主要呈現細小的、等軸的逆變奧氏體和鐵素體晶粒[94]。
統計發現,中錳鋼的強塑積更多地依賴于鋼的延伸率而不是強度[81,84],而延伸率則主要依賴鋼中奧氏體體積分數,這為今后的研究指明了方向:若欲提高鋼的強塑積,需要把更多的注意力放在提高延伸率上。
4.2 中錳鋼的氫脆
目前對中錳鋼的研究主要集中在微觀組織演化和力學性能方面,對其氫脆性能的研究報道比較少,僅有的幾篇文獻顯示中錳鋼有明顯的氫脆現象。如Han等[98]對比研究了熱軋和冷軋2種組織狀態的中錳鋼,發現2種軋制狀態均表現出很大的氫致塑性損失和強度損失,如圖8[98]所示,但是冷軋態的損失比熱軋態要小一些。對此Han等[98]從裂紋擴展角度給出如下解釋:熱軋態為條狀組織,裂紋沿原奧氏體晶界擴展,路徑平直;而冷軋態晶粒細小,裂紋沿晶界擴展時經常改變方向,或者進入晶粒內部,路徑曲折,因而抗氫脆性能更好。Kim等[12]發現,在變形過程中,被逆變奧氏體捕獲的H原子會被新生成的馬氏體所繼承,而馬氏體的H溶解度遠低于奧氏體,導致H在某處(如界面)富集形成氫致裂紋,造成試樣斷裂。Wang等[99,100]對Fe-9Mn-3Ni-1.4Al中錳鋼開展了一系列研究,發現退火后的試樣在馬氏體板條界面處含有納米級薄膜狀奧氏體;未經退火的試樣為全馬氏體組織,不含奧氏體。預充氫拉伸結果顯示,不含奧氏體的試樣在彈性階段就發生斷裂,而含薄膜狀奧氏體的試樣在發生一定的塑性變形后才斷裂,抗氫脆性能明顯優于不含奧氏體的試樣。同時發現,在新生馬氏體與鐵素體界面處,氫致裂紋形核、長大并相互合并。
圖8 Fe-7Mn-0.1C-0.5Si 冷軋和熱軋中錳鋼充氫前后應力-應變曲線和EBSD像[98]
Shao等[101]研究了臨界退火時間對溫軋中錳鋼氫脆敏感性的影響,發現在相同充氫條件下,隨退火時間延長,試樣中的H含量降低,但塑性損失卻增加;進一步分析發現,隨退火時間延長,在拉伸后鋼中奧氏體發生馬氏體相變的比例增加,因此認為奧氏體穩定性越低,氫脆敏感性越高。Zhang等[102]發現,隨奧氏體體積分數的增加,鋼中的擴散氫濃度近似呈線性增加。同時由于奧氏體的體積分數增加,拉伸變形過程中奧氏體轉變形成的馬氏體增多,使得臨界退火試樣的氫脆敏感性增加。因此認為TRIP效應對TRIP鋼的抗氫脆性能是有害的,奧氏體的含量和穩定性都對TRIP鋼的氫脆性能有很大的影響。進一步,Zhang等[103]通過施加89%的溫軋壓下量,使材料的抗拉強度增加約200 MPa,在同樣充氫條件下,鋼中H含量增多,但氫脆敏感性卻降低。分析發現,溫軋后試樣斷口發生層狀分裂,作者認為,一方面分層釋放了拉伸變形過程中的三軸應力,從而延遲了斷裂的發生;另一方面,溫軋增大了奧氏體的穩定性,并細化了晶粒,進而分散了H濃度。2方面的共同作用使大壓下量試樣的氫脆敏感性得到改善。Jeong等[104]研究了中錳鋼中奧氏體形態對氫脆的影響,發現長條狀或薄膜狀奧氏體比等軸狀奧氏體具有更好的抗氫脆性能,并且認為這是由于長條狀或薄膜狀奧氏體在晶粒間的分布面積較大,阻礙了H的遷移和富集。
本課題組最新研究結果[105]表明,添加合金元素Si對中錳鋼Fe-0.2C-6Mn-3Al的抗氫脆性能有明顯影響,即:與不加Si的試樣相比,添加0.6%Si后(微觀組織中出現δ-鐵素體)退火3 min,鋼的氫脆敏感性升高;而退火30 min后,鋼的氫脆敏感性降低。這意味著在工業生產時,不加Si的試樣適合短時間退火(比如連續退火),而添加Si后適合采用較長時間退火(例如罩式退火)。
本課題組對含10%Mn的中錳鋼分別進行了400 ℃回火和600 ℃兩相區退火處理,獲得奧氏體體積分數分別為47%和79%的2種試樣,抗拉強度分別為1728和1690 MPa,延伸率分別為27.3%和28.7%,如圖9所示。但是預充氫后拉伸,回火和退火態的延伸率分別剩余3.5%和16%,對應的塑性損失分別為87%和45%,相差近一倍。這表明中錳鋼的氫脆敏感性與微觀組織中的奧氏體含量和穩定性有密切關系,更多信息有待進一步深入分析。
圖9 回火和退火中錳鋼充氫前后的拉伸曲線
4.3 中錳鋼層錯能與奧氏體穩定性
如4.2描述可知,奧氏體組織對中錳鋼氫脆敏感性影響巨大,奧氏體組織在變形中的穩定性起到了決定性的作用。隨著奧氏體穩定性的降低中錳鋼氫脆敏感性增加,這主要是因為在變形過程中,原先被奧氏體陷阱捕獲的H原子,會被新生馬氏體繼承,導致氫致裂紋在新生馬氏體和鐵素體界面處形核。因此為了進一步理解中錳鋼的氫脆,有必要對中錳鋼中奧氏體的穩定性做進一步研究。與QP鋼和TRIP鋼相比,中錳鋼所含的奧氏體相顯著增多,因此形變過程中最重要的就是奧氏體的變形機制,而變形機制由層錯能(SFE)決定,一般認為,當SFE≤20 mJ/m2時,主要發生TRIP效應;當SFE處于20~50 mJ/m2時,主要為TWIP效應;當SFE≥50 mJ/m2 時,主要發生位錯滑移[106]。層錯能與化學成分、晶粒尺寸、溫度等有關,對高錳鋼的研究發現,Al會提高奧氏體的層錯能,Si會降低層錯能[107]。計算結果[108]表明,Mn對Fe-Mn二元合金SFE的影響在Mn質量分數約為13%處有極小值。前面說過,中錳鋼中Mn質量分數一般為5%~12%[81],因此,中錳鋼中奧氏體相的層錯能隨Mn含量增加而降低。層錯能降低引起剪切帶(可以ε馬氏體、形變孿晶或密集的層錯束形式存在)形成速率升高,剪切帶交叉可作為馬氏體的形核點[109],會促使TRIP效應活躍。已發表的文獻中,SFE的計算主要針對純奧氏體結構的TWIP鋼,到目前為止還沒有雙相或多相結構的SFE計算模型。關于中錳鋼中層錯能計算的文獻非常少[110,111],僅有的一些研究結果尚不具備普遍的指導意義。因此,未來若要借助層錯能這一概念預測中錳鋼的變形機制,需要在考慮非奧氏體組織對奧氏體相變形的約束或影響的前提下,建立計算多相結構層錯能的物理模型。未來,也許有可能借鑒“TWIP鋼中用SFE判斷形變模式”這一判據,預測中錳鋼的相變或形變機制。
總之,與TRIP鋼和QP鋼相比,中錳鋼因具有相對高的Mn含量,微觀組織中的奧氏體體積分數可以達30%甚至50%以上,因而可以實現高強度和高塑性的良好配合,強塑積可達30~60 GPa·%。統計分析表明,中錳鋼的強塑積更多地依賴于延伸率而不是強度。實現中錳鋼高強塑積的主要措施為:通過調整Mn、Al等合金元素含量,設計合適的熱處理工藝路線,得到足夠多的奧氏體相,并使其保持一定程度的穩定性。現有結果表明,雖然中錳鋼的晶粒較小,但氫脆敏感性仍然較大。不過,經過冷軋的中錳鋼的氫脆敏感性比熱軋態低;含有納米級薄膜狀奧氏體的中錳鋼抗氫脆性能可以得到很大改善。因此,未來改善中錳鋼抗氫脆性能可以在這2方面采取更多的措施。
5 總結和展望
本文總結了第一代到第三代先進高強鋼各自典型代表鋼種——TRIP鋼、TWIP鋼、QP鋼和中錳鋼的氫脆研究現狀和主要結果,并指出了各鋼種改善抗氫脆性能的可能的措施。對于具有復雜多相組織、變形伴隨著TRIP效應或TWIP效應的AHSS,合金元素、退火/臨界退火條件(溫度、時間、加熱速率等)、應變速率等通過影響奧氏體體積分數而嚴重影響著鋼的微觀組織和力學性能,進而影響著鋼的抗氫脆性能。
(1) H對TRIP鋼的影響主要體現在塑性降低而強度變化不大。
(2) 對TWIP鋼,氫脆敏感性嚴重依賴于應變速率,隨應變速率降低而顯著增加。形變孿晶界和ε/γ相界面一般易于發生氫致開裂,而Σ3退火孿晶不易開裂;但是當ε/γ相界面滿足西山取向關系時,則與Σ3孿晶類似,能夠阻礙氫致裂紋擴展。
(3) 與TRIP鋼相似,QP鋼的氫脆主要表現為塑性損失,強度損失較小,氫致裂紋主要沿應變誘發的新鮮馬氏體或M/γ界面形核。
(4) 中錳鋼含有較多的奧氏體相,變形時伴隨著強烈的TRIP效應,氫脆敏感性較大,既有明顯的塑性損失也有較明顯的強度損失。氫致裂紋主要沿應變誘發的新鮮馬氏體或M/γ界面形核。
對微觀組織中含有奧氏體的復相組織鋼如TRIP鋼、QP鋼、中錳鋼等,由于奧氏體組織具有大的H溶解度和慢的H擴散系數,如果能夠在控制其穩定性的前提下,通過工藝調控奧氏體均勻分布且以長條或薄膜形態存在于其它組織的界面處,如馬氏體板條界面間,則這些薄膜狀的奧氏體就可以成為H擴散的一道道屏障,阻礙H在基體中的“長途”擴散和富集,從而提高鋼的抗氫脆性能。調控奧氏體形態和分布是這類鋼未來的主要發展方向。
對具有全奧氏體組織的TWIP鋼,現有結果表明,Al合金化是改善其抗氫脆性能的有效措施;此外,通過增加預應變速率而影響鋼中C的應變時效,也可以改善TWIP鋼的抗氫脆性能;本課題組的最新結果表明,滿足西山取向關系的γ/ε相界面具有與Σ3晶界類似的作用,可以阻礙氫致裂紋的擴展,從而改善鋼的氫脆。這為通過晶界工程設計改善鋼的抗氫脆性能指明了又一方向。
免責聲明:本網站所轉載的文字、圖片與視頻資料版權歸原創作者所有,如果涉及侵權,請第一時間聯系本網刪除。
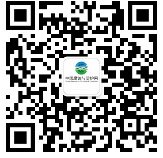
官方微信
《腐蝕與防護網電子期刊》征訂啟事
- 投稿聯系:編輯部
- 電話:010-62316606
- 郵箱:fsfhzy666@163.com
- 腐蝕與防護網官方QQ群:140808414