對于海洋或沿海地區工作的航空發動機來說,其高溫結構表面易沉積硫酸鹽(主要為NaCl、Na2SO4或V2O5等的混合物)。在高溫作用下,硫酸鹽容易引起一種被稱為“熱腐蝕”的加速損傷模式,從而使得高溫合金表面容易萌生裂紋,最終導致高溫結構強度下降和壽命降低。最近幾年,連續出現多起因高溫結構熱腐蝕導致的葉片斷裂故障。
在結構設計階段,可通過考慮熱腐蝕因素的安全壽命設計或損傷容限設計來保障高溫結構的安全性;在運行維護階段,為了減少發動機的維護成本并提高其可用性,需要提供經濟和安全的外場維護方案。本文主要關注后者。目前,外場維護正處在由定時維護逐漸向視情維護轉變的階段。因此,亟待采用主動積極的方式對含熱腐蝕缺陷的高溫結構進行運行維護。視情維護是通過在線監測或離線檢測手段獲取航空發動機結構的損傷程度,以此為發動機提供最經濟的維護方案。在線監測的精度較低,難以監測到熱腐蝕缺陷。因此,不得不通過離線檢測方法獲得熱腐蝕損傷信息,即在不損傷被檢對象的情況下,借助聲、電、磁、電磁波、中子、激光等手段檢出缺陷的形態、大小和數量,最終建立熱腐蝕損傷程度或其與失效因子(或剩余壽命)的映射關系。這種方法可以彌補狀態監測的不足,從而為航空發動機視情維護的進行提供更好的支撐。
國家標準GB/T 10123-2001中對腐蝕的定義是金屬與環境間的物理-化學相互作用,其結果使金屬的性能發生變化,并??蓪е陆饘?、環境或由它們作為組成部分的技術體系的功能受到損傷。
可從不同角度對腐蝕進行分類,若按腐蝕機理分類,可分為化學腐蝕、電化學腐蝕、物理腐蝕和生物腐蝕;按是否受力分類,可分為無應力作用下的腐蝕和應力作用下的腐蝕;按腐蝕形態分類,可分為均勻腐蝕和局部腐蝕。
如圖1所示,均勻腐蝕是指整個金屬表面均發生腐蝕;而局部腐蝕即金屬表面局部位置發生腐蝕,主要包含點蝕、晶間腐蝕、剝蝕、電偶腐蝕、縫隙腐蝕等。
圖1 腐蝕形貌示意圖
航空發動機中的熱腐蝕通??煞譃棰裥蜔岣g(高溫熱腐蝕)和Ⅱ型熱腐蝕(低溫熱腐蝕)。一般認為Ⅰ型熱腐蝕發生在800~950 ℃的溫度范圍內,此時沉積鹽為熔融態,因此,Ⅰ型熱腐蝕的損傷特征是在合金表面產生均勻的腐蝕層,屬于均勻腐蝕;而Ⅱ型熱腐蝕通常發生在650~800 ℃的溫度范圍內,此時沉積鹽為固態和熔融態共存,其顯著特征是形成點蝕坑,屬于局部腐蝕中的點蝕。航空發動機高溫結構的熱腐蝕與常溫下有所不同,無論是腐蝕產物、還是腐蝕機理均存在差異。如常溫下金屬腐蝕產物可以是金屬氧化物、氫氧化物、硫化物、鹵化物等,而熱腐蝕最終產物主要為金屬氧化物和硫化物。相比于一般腐蝕,熱腐蝕反應復雜,目前典型的Ⅰ型熱腐蝕機理模型主要有硫化模型、酸堿熔融模型。其中,硫化模型認為Ⅰ型熱腐蝕發生時,金屬中還原性組分與熔融鹽反應還原成硫化物(MS),然后硫化物進一步與金屬反應生成低熔點的金屬-金屬硫化物共晶(即M·MS),隨后金屬-金屬硫化物共晶又進一步的氧化,生成氧化物(MO)和硫化物,硫化物再次與金屬基體組分形成共晶,形成自催化過程。酸堿熔融模型則認為金屬發生熱腐蝕時,表面形成的具有保護作用的氧化膜在沉積的熔融鹽中發生酸性(O2-濃度低,熔融鹽呈酸性)或堿性(O2-濃度高,熔融鹽呈堿性)溶解,導致金屬的加速腐蝕。相比于Ⅰ型熱腐蝕,Ⅱ型熱腐蝕發生的溫度范圍“較低”,沉積鹽為固態或固液共存態,其腐蝕機理與Ⅰ型熱腐蝕存在差異。Luthra描述了幾種鈷基合金在不同溫度和SO3分壓(PSO3)下發生Ⅱ型熱腐蝕時腐蝕形貌和腐蝕產物的傳輸過程與分布,提出了鈷基合金熱腐蝕機理,這一機理還被推廣到預測鎳基合金的Ⅱ型熱腐蝕行為。Ⅱ型熱腐蝕條件下涂敷在合金表面的Na2SO4為固態,大氣中如果有足夠的PSO3便可以使得NiO或者CoO硫化以生成NiSO4或CoSO4。兩種化合物將進一步與表面上過量的Na2SO4反應,形成液態共晶鹽Na2SO4-MSO4(M代表Ni和Co)。低熔點共晶鹽的存在使得合金表面出現熔融鹽,熔融的混合硫酸鹽通過溶解保護性的氧化層,并通過點蝕坑中的液體來傳輸反應產物,加快了腐蝕速率。這一混合熔融硫酸鹽液相侵蝕的Ⅱ型熱腐蝕機理目前被廣泛接受。另外,有研究者用電化學機理對熱腐蝕反應過程(包括硫化物生成、疏松金屬氧化物在熔融鹽中的沉積等)進行了解釋。他們認為引起熱腐蝕的沉積熔融鹽是離子導體,亦即是電解質,熱腐蝕在幾何上與薄水溶液電解質膜下的金屬和合金的腐蝕形式極為類似,實際上是金屬和合金在薄熔鹽電解質膜下發生的腐蝕破壞。無損檢測技術種類繁多,常見的無損檢測技術主要包括超聲檢測、渦流檢測、磁粉檢測、滲透檢測、射線檢測、光學檢測、聲發射檢測等。從文獻調研看,這些技術的大部分都已應用于航空發動機結構的檢測維護之中。超聲檢測技術主要利用超聲波在界面(聲阻抗不同的兩種介質的結合面)處的反射和折射以及超聲波在介質中傳播時的衰減等性質來檢測缺陷,是應用最廣泛的無損檢測技術。超聲檢測技術可對發動機金屬或非金屬結構進行檢測,對于內部缺陷的定位定量檢測較其他檢測方法有綜合優勢,同時對裂紋、未焊透等缺陷也有較高的檢測能力。超聲檢測技術在發動機壓氣機葉片、渦輪葉片、整體葉盤等結構的檢測中均有應用。渦流檢測技術基于電磁感應現象對被檢對象的性質或缺陷進行評價。渦流檢測只適用于導電材料的檢測,并且由于趨膚效應的存在,更適用于表面及近表面缺陷的檢測,不太適用于較厚工件的內部缺陷檢測。它對結構表面的缺陷比較敏感,且檢測時不需要清理涂層。渦流檢測技術對發動機渦輪葉片、榫槽、篦齒盤等結構表面裂紋的檢測均有文獻報道。磁粉檢測技術只適用于鐵磁性材料缺陷的檢測,它是利用被磁化工件表面或近表面缺陷形成的漏磁場吸附磁粉來顯示缺陷。磁粉檢測技術在發動機壓氣機葉片等結構表面裂紋的檢測上有應用。滲透檢測技術是基于毛細作用和顯影劑在一定條件下的發光現象對表面開口缺陷進行檢測的一種技術。它不受被檢對象材料的影響,但由于其檢測原理,無法對多孔結構進行檢測。有文獻報道了滲透檢測技術在發動機復雜機匣表面缺陷檢測的應用。射線檢測技術是利用X射線、γ射線和中子射線易于穿透物體,但在穿透物體過程中受到吸收和散射而衰減的性質來檢測缺陷的技術。射線檢測技術對較薄結構內部體積型缺陷的檢測更有優勢,對于發動機渦輪葉片、機匣、火焰筒等結構缺陷的檢測均有應用。光學檢測即利用光在傳播時的反射、折射、干涉和衍射等特性進行直接觀察被檢對象形貌或間接測量其在加載時的表面變形來評價對象缺陷或性質的檢測技術。在發動機結構的檢測維護中,孔探儀是最常用的光學檢測手段之一。通過發動機機匣上的探視孔,不用拆解發動機便可有效發現發動機壓氣機、渦輪、燃燒室的腐蝕、裂紋等損傷缺陷情況。
聲發射檢測技術是通過接收聲發射現象產生的信號并進行一定的處理分析來對材料或結構的性質和存在的缺陷進行評價的技術。聲發射檢測的缺陷是動態的,且發射源為缺陷本身,對于缺陷發展過程中伴隨著聲發射現象的檢測對象,它都是潛在的檢測方法。目前聲發射檢測技術在飛機結構狀態監測上已有應用,同時研究人員也在研究和探索其在發動機結構監測上的應用。
金屬點蝕發生時,常會伴隨聲發射現象。早在1984年,Arora便對鋁合金點蝕過程產生的聲發射特征進行了研究,結果表明數字化記錄的聲發射頻率和波形分析有助于識別主動腐蝕過程。Idrissi等以聲發射作為評估方法,研究了2024T351鋁合金點蝕不同階段的聲發射活動特征,并與氯離子濃度進行了相關性分析,得到了如下重要結論:在點蝕萌生的初始階段無法被聲發射檢測到;但是,金屬表面微氣泡或大氣泡氣體釋放時釋放的能量是聲發射探測的發射源,即當H3O+還原形成第一個氫微泡時,通過聲發射可以立即檢測到鋁合金的點蝕現象。Fregonese等對316L不銹鋼點蝕過程的研究同樣表明聲發射源來自點蝕生長過程,而在點蝕萌生過程無明顯聲發射現象。這些研究揭示了點蝕過程中聲發射現象的特點,體現了聲發射技術用于金屬材料點蝕檢測的潛力。聲發射信號可分為突發型和連續型兩種基本類型,一般以信號持續時間的長短進行區分。點蝕的聲發射檢測過程中受到各種隨機因素的影響,既有連續型信號,也有突發型信號,屬于非平穩的隨機信號。典型的點蝕聲發射信號如圖2所示。對于不同類型的聲發射信號,常采用不同的信號特征參數進行描述。突發型信號特征參數主要有撞擊計數、振鈴計數、上升時間、持續時間等,連續型信號特征參數有振鈴計數、平均信號電平和有效電壓。
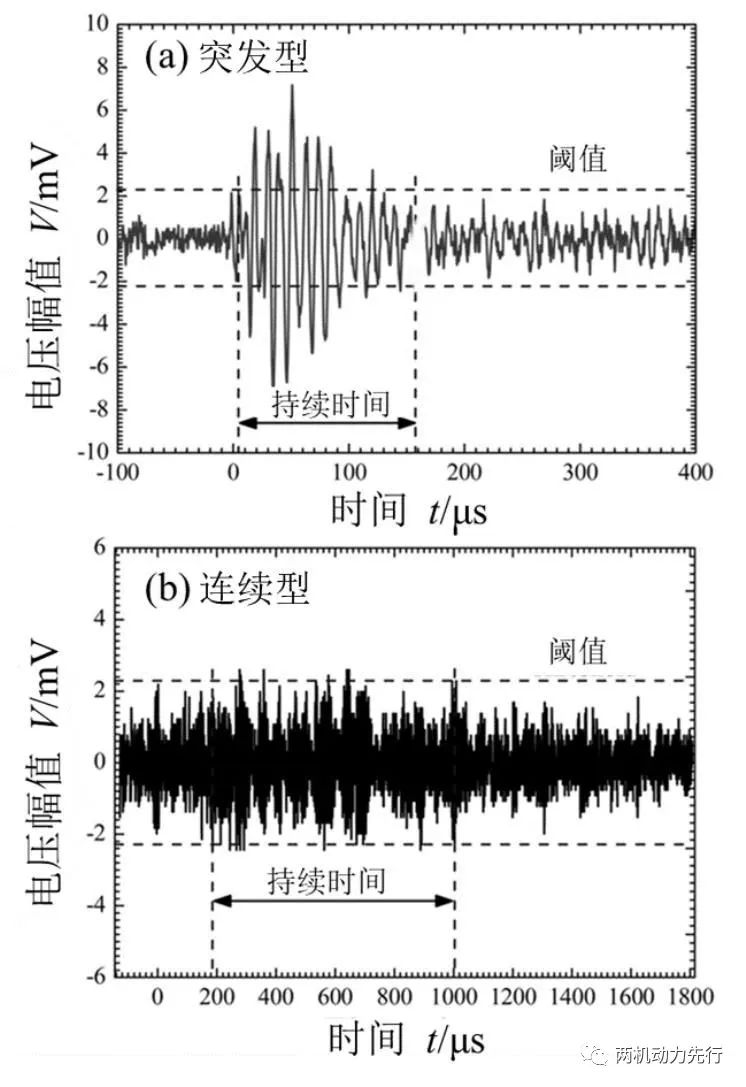
圖2 典型聲發射信號
在點蝕發生過程中,兩種聲發射信號占比受到材料類型、溶液濃度等因素的影響。且在點蝕的三個階段(點蝕萌生、生長、穩定)中,點蝕萌生階段幾乎沒有信號(撞擊計數、振鈴計數)發出,聲發射信號是在點蝕萌生后一段時間才出現。相對于點蝕萌生階段,生長階段聲發射信號較多且增長較快,而穩定階段增長變緩。點蝕聲發射信號的這些特征是對金屬點蝕進行檢測的基礎。
由于點蝕過程會伴隨聲發射現象,聲發射技術在點蝕的監測上有較多研究與應用。王光卿等研究了儲罐底板鋼點蝕過程中聲發射信號特征,對評估金屬儲罐罐底腐蝕程度,鑒別腐蝕類型具有一定的指導意義。Tang等在碳鋼的聲發射監測過程中采用開路電位測量并通過光學顯微鏡原位觀察腐蝕形貌,開發了聲發射信號處理和腐蝕類型識別方法。該方法能有效區分點蝕與均勻腐蝕,表明聲發射技術可用于不同行業碳鋼或不銹鋼容器腐蝕的現場監測中。Wu等分析了單個點蝕坑在萌生和生長過程的聲發射信號,認為腐蝕產物的開裂或流出可能是除氫氣泡以外的另一聲發射源。
聲發射技術的點蝕檢測效果顯著,為人們進一步了解金屬點蝕機理提供了手段。目前的研究主要集中在聲發射機理探索和溶液環境中點蝕的檢測,對于非溶液以及高溫環境中點蝕的檢測,聲發射技術難以實現。
通有交變電流的渦流檢測線圈產生的磁場使試樣表面產生渦流,試樣表面的點蝕缺陷會導致渦流分布發生變化。渦流分布變化會影響線圈磁場分布從而使檢測線圈阻抗發生變化,最終反映在輸出信號發生變化。將帶點蝕試樣信號與對比試樣輸出信號進行對比,從而對點蝕損傷進行評估。
樊明亮等用不同半徑不同深度的人工圓孔缺陷模擬奧氏體不銹鋼點蝕損傷,通過建立的脈沖渦流實驗系統提取缺陷出現的峰值來分析其響應特性用于點蝕缺陷的評估。李鵬改變帶圓孔型腐蝕缺陷管道的包覆層厚度,發現渦流檢測差分電壓信號峰值隨厚度的增大而增大,當包覆層厚度小于20 mm,信號峰值呈線性增加趨勢,當超過這個厚度信號幅值增加變緩并在30 mm時趨于穩定。Yin等通過對傳感器參數的優化設計,提出了一種基于解析優化的電渦流傳感器的點蝕坑檢測方法,結合數字電感測量系統和數據處理方法,檢測系統具有較高的靈敏度,能夠檢測百微米級別的點蝕坑。
目前,研究者們在提升渦流檢測技術對點蝕缺陷檢測能力的研究上取得了不錯的進展,主要體現在對隱藏點蝕缺陷和微小尺寸點蝕缺陷的檢測上。
超聲導波和非線性超聲表面波由于特殊的傳播性質常應用于檢測點蝕。超聲導波檢測點蝕和通用的超聲檢測原理類似,主要是利用超聲導波在試樣中傳播時遇到點蝕缺陷時的反射、散射等線性特征,并通過聲速、衰減系數等進行表征,以判斷點蝕的位置和大小。其本質是利用缺陷和材料聲阻抗的差別來實現檢測。非線性超聲表面波對點蝕的檢測則是利用點蝕缺陷與大幅度超聲表面波相互作用產生的非線性效應(表現為產生高次諧波)來對點蝕缺陷進行評價。
超聲導波檢測信號按照檢測方式的不同可分為A型顯示和超聲成像顯示。A型顯示是沿聲傳播方向的一維波形顯示,表示的是超聲信號的幅值和傳播時間的關系,一般橫坐標代表傳播時間,縱坐標代表信號幅值。圖3為無缺陷(圖a)和有缺陷(圖b)超聲導波的A型顯示信號。超聲成像顯示信號是綜合了沿著試樣截面某一方向(B顯示)或沿著整個截面掃描(C型顯示)得到的A型信號,能夠顯示缺陷的深度或形狀等信息。圖4為典型的超聲成像C型顯示,坐標對應的為掃查位置,坐標系中信號幅值以灰度顯示。
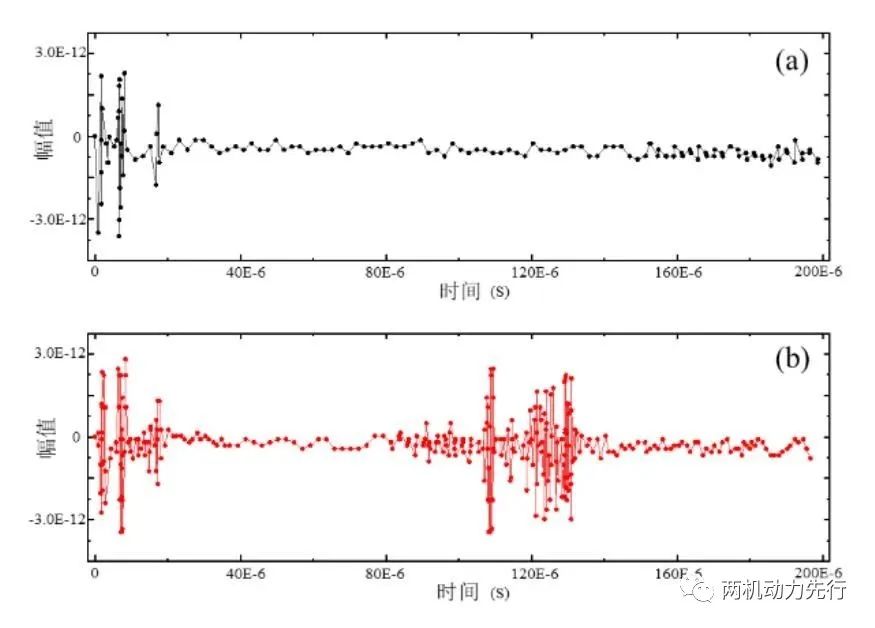
圖3 超聲導波A型顯示信號:(a)無缺陷;(b)有缺陷
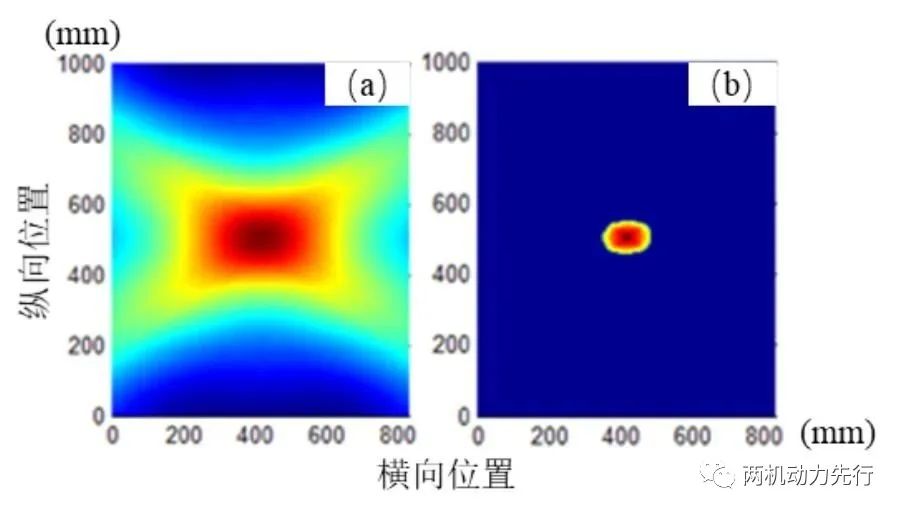
圖4 超聲導波C型顯示信號:(a)濾波前;(b)濾波后非線性超聲表面波表征點蝕損傷的參數為超聲非線性系數,其定義公式如下:
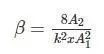
其中,k為波數;x為超聲波傳播距離;A1與A2分別為頻域信號基波與二次諧波幅值。圖5為帶有不同點蝕坑尺寸試樣的超聲非線性系數曲線圖,當凹坑尺寸增加時,非線性系數也增加。
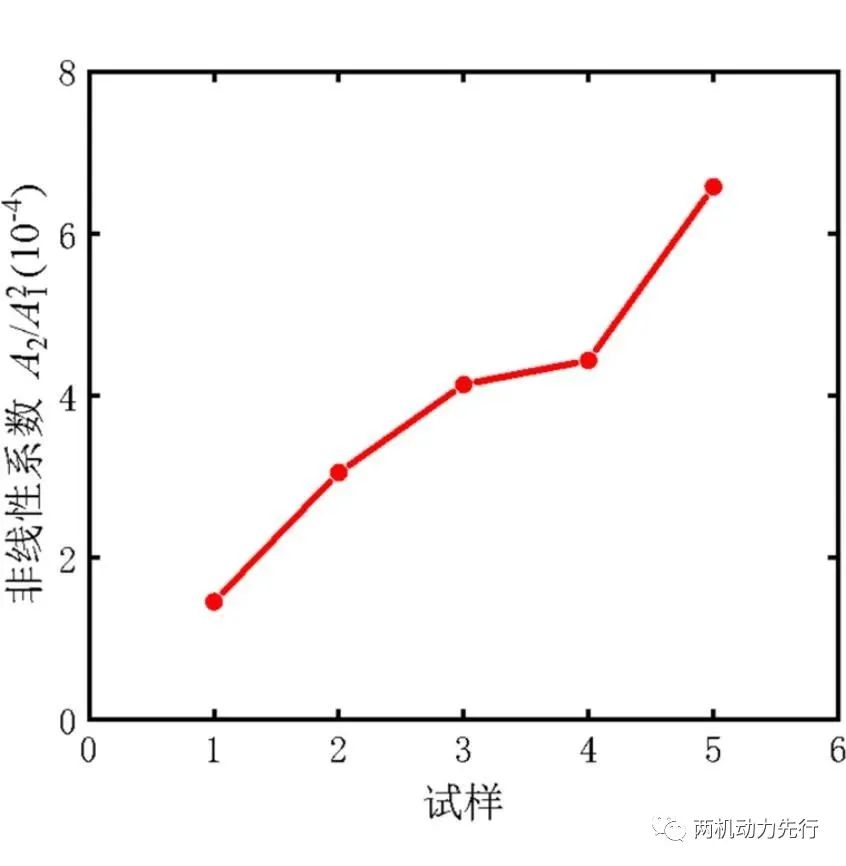
圖5 超聲非線性系數
點蝕在萌生和發展時具有較大隨機性,其數量、位置分布、形貌等難以預測。數值模擬能夠建立任意數量,任意分布、任意形貌點蝕坑模型,是研究點蝕缺陷對超聲波影響的有效方法,可為點蝕的超聲檢測技術研究提供參考。對超聲波傳播過程的數值模擬,合理設置模型網格尺寸、邊界條件和積分時間步長等參數是關鍵。為了保證模擬精度,網格尺寸需根據超聲波波長來確定,最大網格尺寸必須滿足:
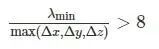
其中,λmin為最小超聲波長,Δx、Δy、Δz為節點間距。超聲波在遇到邊界會發生反射,為了消除反射信號的干擾,常采用吸收邊界或適當擴大模型尺寸的方法。積分時間步長是數值模擬的另外一個重要參數,決定模擬結果的準確性及精確度。超聲檢測模擬積分時間步長的選擇需遵循Nyquist定律和Moser定律。Shivaraj等采用高階圓柱超聲導波對管道隱蔽位置點蝕進行檢測,并建立帶針孔型缺陷的圓環二維有限元模型,觀察了波在圓環中的傳播方式,得到了含缺陷圓管的反射波紋圖和反射能量值,并與實驗結果進行了比較,兩者吻合較好。王曉娟等針對管道常見的點蝕缺陷超聲導波檢測問題,通過有限元仿真對其反射回波信號進行分析,提出了確定仿真參數最優設置的優化策略,保證建模仿真的準確和高效。王騰騰構建了非線性表面波檢測模型,模擬研究了蝕坑形貌參數對表面波傳播行為的影響。
數值模擬是研究超聲波在介質中傳播行為的有效手段,為點蝕的超聲檢測研究提供了新思路。但是,由于超聲波模擬需滿足最大網格尺寸小于八分之一波長的要求,常導致過大網格數量的和過高的計算成本,這尤其限制了其在三維有限元分析中的應用。
均勻腐蝕是工業生產中常見的腐蝕形貌之一,往往導致構件大面積減薄。各種工程結構(如管道、儲罐等)內部發生均勻腐蝕時常常難以及時察覺,為能減少這種隱蔽性損傷引起的結構破壞,研究者們對均勻腐蝕的無損檢測進行了研究。Jirarungsatian等將均勻腐蝕過程聲發射源分為三類:腐蝕開始時金屬表面損傷源;腐蝕在金屬表面的形核和發展;腐蝕過程中氣泡破裂,并選取信號持續時間和共振頻率作為聲發射參數對均勻腐蝕與點蝕進行分類。李偉等分析了低碳鋼均勻腐蝕過程的聲發射信號特性,并對比實驗條件下低碳鋼腐蝕聲發射信號與實際條件下儲罐罐底腐蝕聲發射信號的參數特征,為低碳鋼均勻腐蝕過程聲發射特征研究和儲罐在線聲發射檢測提供參考。張春輝建立了一套提取均勻腐蝕聲發射信號的實驗系統,對均勻腐蝕各個過程進行聲發射監測,分析了Q235均勻腐蝕氣泡產生和金屬溶解過程的聲發射特征,運用小波分析相關理論對聲發射信號進行處理,實現了對兩種腐蝕模式的識別。Yang等通過數值模擬、實驗和現場實測,研究了均勻腐蝕對導波傳播規律的影響。結果表明均勻腐蝕會產生相干噪聲,使導波能量衰減,腐蝕層越厚,相干噪聲越大,導波衰減速率越大。而使用較高的導波頻率能降低相干噪聲,但也會降低導波傳播的能量。實測結果與數值模擬結果吻合較好,研究獲得的結果有助于檢查人員區分管道均勻腐蝕區域內的局部腐蝕,管道均勻腐蝕的有限元模型如圖6所示。Shim等發現690合金蒸汽發生管均勻腐蝕行為與渦流檢測旋轉探頭測量的管道噪聲密切相關,因此,可將管道噪聲用于預測其均勻腐蝕行為。與點蝕相比,均勻腐蝕的無損檢測研究較少。這些研究通過實驗或仿真探索了均勻腐蝕對各種檢測技術信號的影響,找到合適的信號特征是將這些技術應用于均勻腐蝕檢測的關鍵。
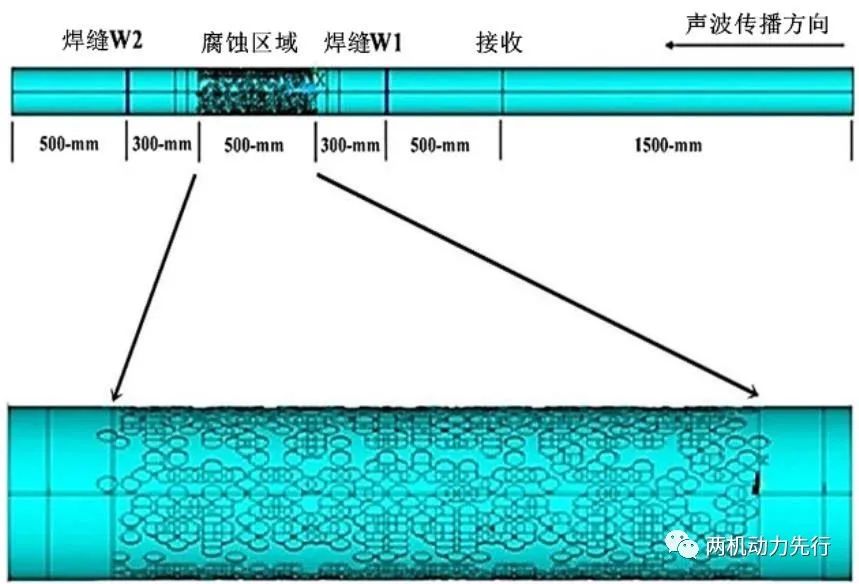
圖 6 管道均勻腐蝕有限元模型
在檢測到缺陷后,有必要進一步的對缺陷類型進行識別并大致對缺陷進行定位。對于腐蝕缺陷的識別,根據聲發射信號特征,可分辨處于不同階段的點蝕,或對腐蝕嚴重程度進行判斷。另外,通過結合各種算法及信號處理方法建立的基于特征識別的腐蝕類型分類方法已能夠實現對多種腐蝕類型的分類,如Tang等通過聲發射信號的二維模式識別方法有效區分了低碳鋼的均勻腐蝕與點蝕,Van等則利用小波分析及機器學習實現了無腐蝕、均勻腐蝕、點蝕、應力腐蝕開裂四種腐蝕模式的分類,分類準確度可達75.7%。雖然腐蝕缺陷的危害性不同于一般的表面缺陷,但是目前基于聲發射檢測的缺陷類型識別的研究還較少,如在對于分辨腐蝕缺陷與其他類型缺陷(如外物打傷等)的研究幾乎沒有。常規的超聲檢測對缺陷的識別主要通過人工判別試塊和被檢工件超聲信號波形的差異來進行的,隨著各種模式識別與分類方法的發展,超聲檢測對缺陷識別的研究與應用已趨于自動化,有效提高了缺陷識別的效率及準確性。在腐蝕缺陷識別的研究上,Ghodsi等通過離散小波變換和離散傅里葉變換從超聲Lamb波信號中提取基頻頻帶作為信號特征對裂紋、局部減薄(厚度減薄程度與腐蝕試樣近似,由電火花加工而成)、均勻腐蝕三種缺陷進行了識別與分類,分類準確度達到95%。圖7所示為傅里葉變換后的三種缺陷信號。

圖7 三種缺陷信號的FFT輸出
Deng等利用分段主成分分析(S-PCA)法對實驗和有限元法獲得的鐵軌超聲導波信號特征進行提取后,利用支持向量機算法實現了裂紋缺陷和腐蝕缺陷的高準確率分類。
研究者們在研究超聲檢測的缺陷識別時,常使用機械加工的缺陷來代替真實的腐蝕缺陷,如禹化民用多種人工缺陷來模擬點蝕和腐蝕穿孔等缺陷。這種方法雖然簡便,但只是真實缺陷的幾何近似,圖7中真實均勻腐蝕缺陷試樣和人工減薄試樣信號的差異在一定程度上說明了這種近似處理方法的局限性。
目前,已經有一些對于腐蝕缺陷厚度測量和重構的研究,Liu等發現合金基體與腐蝕層界面會產生一個微弱的回波信號,將時域信號轉換成時頻域信號后提高了信號對比度,通過測量信號飛行時間實現了對100 μm以下腐蝕層厚度的測定。這些研究表面了超聲檢測應用于更精確的腐蝕缺陷識別的潛力。
實際應用中,渦流檢測對缺陷的識別同樣需要通過比較被檢工件與對比試樣的信號差異。對渦流檢測缺陷識別技術的研究中,大部分都是通過提取渦流信號的時域或頻域特征,然后選擇適當的數據處理方法及識別分類算法來識別缺陷。
目前,對腐蝕識別的渦流檢測研究中同樣使用了人工缺陷模擬腐蝕層或點蝕缺陷,如有文獻用不同深度盲孔近似點蝕,也有文獻用激光加工的不同厚度人工缺陷模擬多層結構中腐蝕導致的金屬損失。這些研究很好地識別了缺陷的幾何特征,但忽視了除幾何特征外的腐蝕特征(如腐蝕層)的識別。
無損檢測技術對包括腐蝕缺陷在內的各種缺陷識別的研究上大都是基于信號特征的識別,更優的信號處理技術、特征相關性算法和分類方法實現了對缺陷高準確度的識別。但是,對于多類型缺陷的識別上研究較少,且研究過程中預制的人工缺陷不能很好的反映真實缺陷的特征。
缺陷定位是無損檢測技術的另外一個重要能力。聲發射檢測技術缺陷的定位即聲發射源定位,主要是通過分析檢測過程中傳感器陣列接收到的信號來確定缺陷的位置。對于突發型信號可采用時差定位或區域定位等方法,對于連續型信號則可采用互相關式定位或衰減測量式定位法。
渦流檢測對缺陷的定位主要依靠探頭在工件表面移動時阻抗變化來確定。另外,由于渦流的趨膚效應,不同深度不同大小的缺陷信號幅值可能相同,此時需要利用相位分析來確定缺陷深度。
超聲檢測技術對缺陷的定位是通過超聲波飛行時間來實現的。當超聲波發射后,通過接收到缺陷回波的時間來計算缺陷位置,這種可以根據信號飛行時間來計算缺陷位置的方法被稱為脈沖反射法。另外相控陣超聲檢測技術可以實現對缺陷的成像,從而直接顯示出缺陷的位置。
目前,各種無損檢測技術對缺陷識別的研究具有一定的局限性。大量研究未能考慮到腐蝕缺陷的特殊性,僅考慮了其幾何特征。超聲檢測技術在進一步的腐蝕特征識別上表現了不錯的效果,具有打破缺陷識別技術困境的潛力。各種無損檢測技術對于缺陷的定位方法有一點差異。
總的來說,聲學手段的檢測技術主要通過計算信號飛行時間對缺陷定位,光學手段的檢測技術主要通過成像顯示缺陷位置,電磁手段的檢測技術則依靠了傳感器相對缺陷位置變化時檢測信號的變化來實現對缺陷的定位。各種無損檢測技術中,光學檢測、超聲檢測和渦流檢測常應用于金屬結構的腐蝕損傷無損評估,而對于管道、壓力容器等運輸和儲存液體的結構,聲發射檢測技術也有廣泛應用和研究。對于腐蝕的檢測,每種無損檢測技術都有一定的優勢和局限性,表1對其優勢與局限性做了總結。不同技術不同的方法在不同類型的缺陷檢測上將有不同的表現,應當根據檢測需求結合技術或方法的特點選擇合適的檢測手段。
表 1 幾種技術腐蝕檢測的優勢與局限性
無損檢測技術在獲得結構的損傷信息后,為了進一步評價結構劣化程度,一些研究者通過無損檢測獲得的損傷信息對結構的剩余壽命進行了評估。這些壽命評估方法大致可分成三類。第一類方法通過無損信號特征直接與壽命聯系來評估壽命。早在1956年,Truell等已經發現疲勞實驗時鋁試樣中超聲波信號的衰減與循環數存在聯系。Joshi等基于這一現象測量了疲勞實驗過程中鋁和鋼試樣的超聲波信號衰減,結果表明超聲信號衰減對疲勞損傷非常敏感,可用于預測實際應用中的早期疲勞損傷和疲勞壽命。Birt等使用超聲C掃描和渦流檢測技術對試樣的點蝕與縫隙腐蝕進行檢測,發現無損檢測信號與試樣疲勞壽命有很好的相關性。閻紅娟研究了超聲非線性系數隨金屬構件彎曲疲勞壽命的變化趨勢,提出了基于超聲非線性綜合參數與疲勞壽命的曲線,形成基于超聲非線性和概率分析預測金屬構件疲勞壽命的P-α-F方法。第一類方法是最容易實現的方法,其壽命評價的精度取決于選擇的信號特征是否合適。第二類方法通過智能算法建立信號特征與壽命之間的聯系。Shell等使用超聲波測試、白光干涉顯微鏡和顯微放射照相對試樣進行檢查來量化試樣腐蝕損傷水平,為壽命預測模型提供輸入,使用多元線性回歸(MLR)和人工神經網絡(ANNs)探究了無損信號和剩余疲勞壽命之間的相關性。Carson在自適應學習網絡(ALN)中使用從超聲信號特征(幅值、時間、頻譜)中選擇的特征來檢測早期疲勞損傷并對剩余壽命進行預測。Ibekwe使用24組低周疲勞實驗的聲發射幅值數據來訓練和測試用于預測壽命的反向傳播神經網絡(BPNN),最終得到一個能夠預測失效壽命的網絡。Spivey通過Kohonen自組織映射網絡和反向傳播神經網絡,對收集的7075-T6鋁合金試件的聲發射數據進行了失效機理分類和疲勞循環次數預測。Okur拓展了Ibekwe和Spivey等的工作,利用聲發射數據對鋁合金缺口試樣的裂紋擴展進行識別并預測其失效。第二類方法通過相關算法找到信號特征中與壽命相關性最好的特征,是基于第一類方法的改進。盡管這兩種方法所用的具體的分析模型不同,但都是引入能夠反映熱腐蝕缺陷尺寸的檢測信號。因此,對于應力和載荷歷程相對簡單的機械結構來說是有效的。然而,對于渦輪葉片等來說,其幾何結構復雜、應力分布不均勻,且應力分布和載荷歷程的影響則顯得尤為重要,采用第一、二類方法無法有效地進行評估。第三類方法結合了無損檢測技術和損傷力學的剩余壽命評估方法。朱旭程等提出一種基于力殘差向量的損傷檢測和結構壽命評估方法,即采用力殘差向量進行槳葉的損傷定位和損傷大小估計,利用腐蝕疲勞裂紋擴展規律建立槳葉剩余壽命預測模型。程興根據埋地燃氣管道腐蝕深度發展規律建立了腐蝕發展趨勢預測模型。
這種方法突破了前兩種方法無法考慮腐蝕缺陷損傷過程的物理機制或規律的局限性。但是,無損檢測得到的通常是局部損傷,因此,通過檢測信息的反演與結構損傷演化過程的正演相結合才有可能進行準確評估。
當無損檢測技術應用于缺陷檢測時,需了解該技術在檢測中的靈敏度或檢測能力??蓹z測到的最小缺陷尺寸越小,則檢測靈敏度越高,檢測能力越強。圖8顯示了在合適的應用場景下光學檢測、超聲檢測、聲發射檢測和渦流檢測在檢測點蝕缺陷的能力。其中,當點蝕坑尺寸生長到某一尺寸時將發展為裂紋。
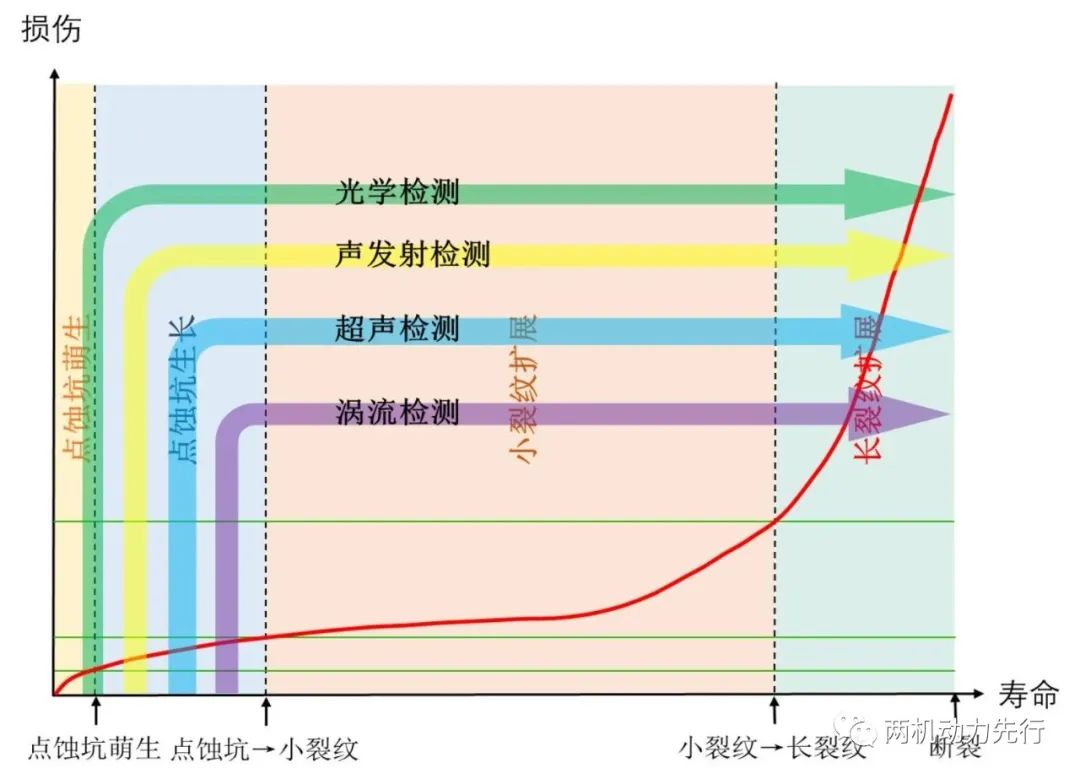
圖 8 幾種技術檢測能力對比
光學檢測能在點蝕萌生時便檢測到點蝕坑;對于聲發射檢測,聲發射信號通常出現在點蝕萌生后一段時間,對相關文獻中點蝕坑萌生后的尺寸進行測量,尺寸約為60 μm。對于渦流檢測,有文獻使用渦流檢測技術對單個點蝕坑進行了檢測,所能檢測到的點蝕坑直徑最小約為592 μm,最小坑深約為148 μm。還有文獻利用非線性超聲表面波對單個點蝕坑進行檢測,點蝕坑直徑最小約為280 μm,最小坑深約為60 μm。發動機高溫結構服役環境惡劣,容易產生熱腐蝕損傷。雖然各種無損技術已大量應用于金屬結構腐蝕的檢測,但對于發動機高溫結構腐蝕的檢測仍存在一些難點,主要體現在以下幾個方面。首先,結構幾何形狀復雜導致技術難以應用。雖然實際結構大都幾何形狀簡單或可由簡單結構組成,在各種無損檢測技術的研究上,對簡單結構進行研究已能夠滿足大部分工程應用的需求,但發動機高溫結構(典型的如渦輪葉片)大都具有復雜幾何形狀和結構。對于這類復雜構件,一些無損檢測技術難以較理想的應用。如用反射法對不規則的變厚度工件進行超聲檢測時,各掃描點的界面波和底波位置隨工件形狀變化而變化,難以確定缺陷位置;超聲波在進入復雜幾何構件后,存在波束變形、方向偏移、靈敏度損失等問題,導致檢測性能下降;另外,復雜幾何形狀導致的換能器接觸不良、換能器移動時的定向障礙都會使檢測靈敏度下降,導致無法正確表征缺陷。其次,對于高溫結構使用的各向異性材料(如定向凝固高溫合金、單晶高溫合金),材料的各向異性還會導致超聲檢測信號產生散射、模式耦合、能量聚焦和衰減,對缺陷檢測帶來不利影響。不少研究者為改善這種狀況已經做了一些努力。Putkis等選擇具有更優分辨率與靈敏度的檢測信號頻率和傳感器位置來減弱碳纖維復合材料各向異性對導波檢測的影響。Wang等則使用帶雙矩陣陣列探頭的自動相控陣系統實現了各向異性焊縫中缺陷更高準確度的識別。最后,檢測能力不足將導致小缺陷無法被有效檢測。圖9所示為CF6發動機斷裂渦輪葉片上的點蝕坑截面形貌,該點蝕坑尺寸約83 μm。對于非承力或承力較小結構,腐蝕在較嚴重時才會影響其功能,此時無損檢測技術檢測能力綽綽有余,在腐蝕威脅結構安全前缺陷已被檢出。而對于承受巨大疲勞載荷的發動機高溫結構(如發動機渦輪葉片),類似圖9所示的小尺寸腐蝕缺陷難以在維修維護時被有效檢出,此時該缺陷已經足夠威脅到結構的安全運行。有文獻報道了CF6發動機渦輪葉片斷裂的事故便是維修時未檢測到低溫熱腐蝕產生的小尺寸腐蝕坑導致的。
圖9 渦輪葉片點蝕坑形貌
對于均勻熱腐蝕和點蝕兩種典型腐蝕的檢測,光學檢測、聲發射檢測、渦流檢測和超聲檢測最為常用。對比了這幾種檢測技術對腐蝕的檢測能力、技術的優點及局限,其中光學檢測具有最高的檢測能力,但是難以檢測隱藏的腐蝕;聲發射技術具有較高靈敏度,能實時監測腐蝕,但是只適合在溶液環境中應用;渦流檢測和超聲檢測技術都可實現百微米級別點蝕坑的檢測,對于隱蔽腐蝕有不錯的檢測能力。
在實現對缺陷檢測的同時,研究者們更進一步的探索了無損檢測信號特征與結構疲勞壽命的聯系,或結合無損檢測技術與損傷力學方法建立了剩余壽命模型,對結構剩余壽命進行了評價。無損檢測技術的應用為結構疲勞壽命預測提供了新思路。
然而,由于發動機高溫結構的復雜性、材料的各向異性等,當前的無損檢測技術雖然能夠檢測管道、壓力容器等結構的腐蝕,但是對發動機高溫結構腐蝕的檢測仍存在難點。
在腐蝕的無損檢測技術研究與應用上仍然有巨大的進步空間,基于本文的綜述,以后的研究重點應該在以下幾個方面:即對復雜結構的檢測;實現更強的檢測能力;同時采用多種檢測技術的結合對復雜結構進行全面精確的檢測。
此外,一方面應重點關注無損檢測與其他技術(如信號處理、人工智能等)的結合;另一方面,無損檢測獲得了結構的損傷信息后,如何利用固體力學知識對結構的剩余壽命進行評價,這是無損檢測技術走向無損評估研究的一個重要方向。