2 銅鎳合金耐蝕性的影響因素
圖 4 影響銅鎳合金耐蝕性的合金元素種類及作用
Fig.4 Types and effects of alloying elements that affect the corrosion resistance of copper-nickel alloys
2.2 溫度對銅鎳合金耐蝕性的影響
溫度對 Cu-Ni 合金耐蝕性能的影響包括對腐蝕反應的動力學參數、氧的擴散系數等方面,溫度的升高 可以使腐蝕反應的動力學參數和氧的擴散系數增加,但是氧的溶解量會降低[28]。溫度也影響了合金表面鈍 化膜的變化[29]。關于溫度對 Cu-Ni 合金耐腐蝕性能的影響還沒有形成統一的認識,結論各有差異[30-31]。ASTM 腐蝕研究數據顯示[32]:當 90Cu-10Ni 在 18 ℃和 28 ℃之間的浸泡時,比在該溫度范圍以下和以上浸泡時表現出更好的耐腐蝕性。Wan 等[33]研究了銅在高溫下的腐蝕,結果表明初期腐蝕速率與暴露時間呈線性關系, 隨后呈指數關系,而且溫度升高會成倍地加速銅的腐蝕。腐蝕產物分析表明,銅在高溫下的腐蝕產物為 Cu2O 和 CuO,其中內層是 Cu2O,外層由 CuO 和 Cu2O 組成。Cai 等[34]的研究表明前期溫度的升高會導致 擴散速率的加快,銅鎳合金腐蝕速率會升高;但是后期合金的腐蝕速率會隨著海中溶解氧的溢 出而降低。
2.3 pH 值對銅鎳合金耐蝕性的影響
pH 值也是銅鎳合金耐蝕性的重要影響因素之一。Al-Thubaiti 等[35]為了研究 pH 值對銅鎳合金腐蝕的影 響,在室溫大氣條件下加鹽酸進行了腐蝕試驗。實驗是在對大氣開放的容器中進行的,氧的含量較高。結果 表明在溫度相同的條件下,pH 值越小,極化電阻越小,其對應的腐蝕電流越大,合金越容易受到腐蝕。羅 宗強等[36]研究了 Cu-17Ni-3Al-X(X=Cr、Si、Ti、Mn、Zr;總含量≤4%)合金在 pH 值變化的 3.5% NaCl 溶 液中的腐蝕行為,結果表明隨著 pH 值的增加,合金的平均腐蝕速率迅速降低,當 pH 值=3 時,合金的平 均腐蝕速率為 0.147 mm/a;當 pH 值=6 時,合金平均腐蝕速率下降到 0.039 mm/a;當溶液的 pH 值=12 時, 合金的平均腐蝕速率約為 0.005 mm/a,說明合金在酸性溶液中相對于中性和堿性溶液更易受到腐蝕。原因 是當溶液為強酸性時,銅合金表面不容易形成致密的保護膜;且溶液 pH 不同時,電化學反應過程中陰極的 還原反應也有所差異。Chen 等[37]研究了 Cu-Cr-Zr 合金在 0.6 mol/L NaCl 溶液和不同 pH 的純水溶液條件下 的耐蝕性,結果顯示氯離子的加入降低了合金的耐蝕性;Cu-Cr-Zr 合金在堿性溶液中的耐蝕性優于在酸性 溶液中,在強酸溶液中發生均勻腐蝕,而在堿性溶液中發生局部腐蝕。Bai 等[38]研究了氯化物存在下產酸雜 色曲霉對銅的腐蝕的影響。結果表明:在 0.01% NaCl 溶液中,真菌會分泌多種有機酸,如乙酸和乳酸,會 使得溶液的 pH 從 7.01 降到 5.26,這些有機酸擴大了銅的腐蝕面積,促進了大氣腐蝕。在腐蝕產物中發現 有羧酸銅的存在,隨著腐蝕產物的積累,空氣中的 CO2 和 O2 在銅表面擴散,Cl-的擴散受到了抑制。綜上, pH 值的差異引起的合金耐蝕性的不同主要是由于不同的 pH 值條件下,電化學反應中吸氧腐蝕的陰極還原 反應不同[39],其次 pH 值的不同也會導致合金表面腐蝕產物的不同,這也是影響合金腐蝕速率的重要因素。
2.4 硫離子對銅鎳合金耐蝕性的影響
硫酸鹽細菌還原、工業廢棄物的排放、腐爛的動植物等最終都會以硫化物的形式進入到海水中。現有研 究證實天然海水或人造海水中硫化物的存在會加速銅鎳合金的腐蝕[40-41]。如鄭強等[42]研究了硫酸鹽還原菌 (SRB)生物膜下 BFe30-1-1 合金的腐蝕行為。結果表明 SRB 的存在使電極自腐蝕電位負移,合金腐蝕速 率顯著增加;極化電阻在細菌生長后期顯著降低,在 SRB 的作用下合金發生了嚴重的點蝕。Rahmouni 等[43] 研究了 3% NaCl 中添加硫化物對銅合金腐蝕的影響。EIS 測量結果顯示,隨著硫化物濃度增加,電化學阻抗 譜半徑逐漸減小,合金腐蝕傾向增加。有學者認為銅的鈍化膜結構和性能很大程度取決于硫化物的濃度。
Kong 等[44]研究了硫化物濃度對銅在含厭氧氯化物溶液中腐蝕的影響。結果顯示:在含硫化物溶液中生成的 腐蝕產物包含 Cu2S、CuS。銅的耐蝕性隨硫化物濃度增加而降低,保護膜的生長和溶解速率更高。Gao 等[45] 研究了 C71500 合金在高濃度硫化物污染的海水中的腐蝕行為。結果表明合金浸泡初期腐蝕速率較高,表現 出均勻腐蝕,腐蝕產物主要由 Cu2S、CuS、Cu2O 等組成,隨著浸泡時間的延長,Cu2S 的含量逐漸增加,S 2- 的加入導致了 Fe 和 Ni 的溶解,Cu2O 膜的形成受到了阻礙,促進了腐蝕過程。Chen 等[46]發現銅在含硫化 物環境中腐蝕很快,當硫化物濃度足夠大時,被硫化物沉積的表面區域和多孔沉積物的區域之間可以形成 微電偶腐蝕,這樣會導致多孔膜的局部腐蝕。
3 提高銅鎳合金耐蝕性的方法
研究表明銅鎳合金在海水中有良好的耐蝕性與銅鎳合金表面形成的腐蝕產物有關,在相同的腐蝕介質 條件下,合金抵御沖刷腐蝕的能力主要取決于自身的力學性能和表面的鈍化膜結構。為了提高銅鎳合金耐 腐蝕的能力,現有途徑主要包括合金化法、犧牲陽極的陰極保護法、緩蝕劑的應用、防腐涂料、超疏水膜技 術、自組裝單分子膜技術等。
3.1 合金化法
合金化法是提高銅鎳合金耐蝕性的最基礎、簡單有效的方法之一。Yang 等[47]研究了 Cu-7Ni-3Al-1Fe1Mn 合金在 3.5% NaCl 溶液中的腐蝕行為。微觀分析結果表明浸泡在 3.5%NaCl 溶液中形成的主要腐蝕產物 是Cu2(OH)3Cl和Cu2O。其中Cu2(OH)3Cl存在于合金表面,Cu2O主要集中在合金基體表面內側附近。Zubeir[48] 研究發現,當 Fe 的含量大于 2%時,90Cu-10Ni 換熱器在海水中的腐蝕速率會變大。過控制 Fe/Mn 比例找 到提高 B10 耐腐蝕性能的最佳合金配比,發現當 Fe/Mn=3:2 時,合金的耐腐蝕性能最好。Zhu 等[49]研究了 不同鐵含量對 70/30 銅鎳合金腐蝕性能的影響。結果顯示,當 Fe 的含量為 1.0%時,合金的耐蝕性最好。他認為鐵元素能夠提高合金耐腐蝕能力是因為在合金的腐蝕過程中一部分鐵會取代 Cu2O 薄膜中的陽離子空穴,空穴數量減少,薄膜電阻增加,除此之外一部分鐵還會以 γ-FeOOH 的形式在腐蝕產物膜中積累和富集, 該物質具有較高的電阻率。Shao 等[50]研究了 Fe/Mn 含量對 90/10 銅鎳合金腐蝕性能的影響。他認為當 Fe/Mn 含量為 1.69/0.69 時,此時 90/10 銅鎳合金具有良好的耐蝕性。Zhu 等[51]研究了不同 Mn 含量對 90/10 銅鎳合 金耐腐蝕性的影響。結果表明在銅鎳合金中添加適量的 Mn 元素可以提高合金的耐蝕性。他認為 Mn 的加入 促進了 Ni 對陽離子空位的填充,生成了更多的 NiO,進一步增強了腐蝕產物膜的穩定性。童慶坤等[5]研究 了微量 Zr、Ti、B 對 B30 合金鑄態組織和性能的影響,結果表明:三種元素均有晶粒細化和強化作用,其 中微量 B 對合金晶粒細化的效果強于微量 Zr 元素;而 Ti 的添加主要是提高了合金的硬度。微量元素的加 入使得合金的鑄錠組織枝晶偏析逐漸減弱,力學性能提高間接提高合金的耐蝕性。Taher 等[52]認為,從相圖 考慮,Cu-Ni 合金中加入的 Fe 的最大含量為 1.5%,若 Fe 的含量過多時會在晶界處形成第二相,腐蝕速率 加快;經人工鹽溶液浸泡的 Cu-Ni-Fe 合金,其表面形成的鈍化膜包括內層和外層,內層鈍化膜為多孔結構 且膜層較厚,與基體結合力較好,加入 Fe 會使外層孔隙消失,鈍化膜中生成的 Fe2O3 提高了鈍化膜的耐蝕 性,也增加了鈍化膜外層的密度。Rosalbino 等[53]研究了 Cu91.6-Nd8.4 和 Cu90.5-Er9.5 合金在堿性溶液中的 腐蝕性能,結果發現:與純銅相比,Cu-RE(RE=Nd、Er)合金的耐蝕性更好。Li 等[54]采用活化反應燒結技 術制備多孔 Ni-Cr-Mo-Cu 合金,通過 SEM、XPS 等技術表征結果表明,隨著 Cr 元素的增加,合金的防腐能 力也逐漸增強。稀土元素因其獨特的物理化學特性,可以吸收雜質氣體,凈化基體,近年來受到廣泛關注。Burleigh 等[55]發現銅鎳鑄件中加入鐵元素可以提高合金的耐蝕性,但是在海水中鐵的析出物會通過電偶腐 蝕導致晶界腐蝕,而通過沖擊試驗表明,2%的銦可以提高合金的耐蝕性也不會發生晶界腐蝕。Lin 等[56]發 現在鋁黃銅中加入稀土 Ce 和 La 可以使合金表面的腐蝕產物膜層更加致密,合金的點蝕程度 顯著降低。謝蔚等[57]發現純銅在 NaCl 溶液中浸泡后生成了 Cu2O 和 Cu2(OH)3Cl 等腐蝕產物,純銅中加 入稀土 La 以后會生成網格狀的 CuLa 中間相,其具有較大的體積分數,在合金表面形成阻擋層,提高純銅 的耐腐蝕性能。宋春梅等[4]研究了稀土釔對 B10 合金耐蝕性的影響。結果表明:添加稀土 Y 的 B10 合金能 夠細化二次枝晶的間距,優化了合金晶界結構,抑制了沿晶腐蝕的現象,從而提高了 B10 合金的耐蝕性。冷翔等[58]研究了稀土 La 對 B10 合金耐蝕性的影響,結果表明 La 能夠提高 B10 合金表面腐蝕產物膜與基體 的穩定性,減少腐蝕產物中的裂紋。郝齊齊[59]利用熱-力模擬技術對 BFe10-1.5-1 合金的熱變形行為進行研 究,結果表明當 Ce 含量為 0.014 wt.%時,可以有效細化合金的樹枝晶,合金中的稀土 Ce 以團狀顆粒、橢 球相形式存在。陳少華等[60]研究了稀土元素 Ce 對 Cu-10Ni-7Si-5Mn 合金組織和耐蝕性的影響。結果表明:CuCe 相與基體呈現半共格界面,起到細化合金組織作用。稀土 Ce 以其氧化物 Ce2O3 和 CeO2 的形式存在于 腐蝕產物中,通過提高腐蝕產物膜層的阻抗值,促使開路電位向正移動來提高合金的耐腐蝕性能。Zhang 等 [61]研究了稀土元素 Nd 對 Cu-13.0Al-4.0Ni 高溫形狀記憶合金組織、力學性能的影響。結果表明 Cu-13.0Al4.0Ni 合金中添加 Nd 可以細化晶粒,晶粒尺寸從毫米級減小到幾百微米級,晶粒細化改善了合金的力學性 能。Dalvand 等[62]研究了合金元素 Ti 和混合稀土 Ce、La 對 Cu-Ni-Al 系合金的組織的影響,結果表明稀土 作為二次細化劑的加入能促進晶粒尺寸縮小,使晶粒尺寸分布更加均勻。Leng 等[63]研究了稀土 La 對 Cu-Ni 合金在 0.1 mol/L NaOH 溶液中鈍化膜性能的影響。結果表明 Cu-Ni 合金表面都會形成高缺陷 p 型半導體(即 Cu2O),同時 La 的加入可以提高合金的耐蝕性。主要原因是在 Cu2O 中增加高價態陽離子,將增加鈍化膜層 的電阻,導致銅合金的耐蝕性增加。Zhang 等[64]認為在 Cu-Ni 合金中加入適量的 Y 可以細化鑄態組織的二 次枝晶間距,通過浸泡實驗可知合金的耐蝕性隨著 Y 含量的增加先升高后降低,當 Y 含量為 0.021%時,合 金的耐蝕性最好。
3.2 犧牲陽極的陰極保護法
犧牲陽極的陰極保護法是防止管路材料腐蝕的傳統方法。朱偉明等[65]參考了國外設計的鐵合金犧牲陽 極的方法,根據國標進行了材料的溶解形貌、自腐蝕電位、電流效率和陽極溶解性能的評價,開發了適用于 國內 B10 管材的鐵合金犧牲陽極材料。材料的選擇原則是(1)電位足夠負,但要避免陰極區產生析氫反應;(2)陽極的極化率要小。因此常選擇鋅-鉛-鎘合金和鐵合金作為犧牲陽極[66]。馬啟國等[67]采用了恒電流法 測試了純鐵犧牲陽極性能,并通過電偶腐蝕試驗進一步分析了純鐵進行陰極保護的可行性。結果表明:純鐵 的自腐蝕電位低于 B10 和 B30 銅鎳合金,作為陽極材料很好地抑制了銅合金的腐蝕,有良好的保護作用, 該方法利用了原電池的原理。選擇還原性強的金屬充當保護劑,其作為負極發生氧化反應而被消耗,B10 合 金作為正極免于腐蝕。
3.3 緩蝕劑
緩蝕劑有著生產簡單、見效快等特點,使用緩蝕劑是減緩銅合金腐蝕的另外一種措施,它主要抑制了陽 極或者陰極的腐蝕速率[68]。近年來學者對緩蝕劑在銅鎳合金方面的應用做了大量的研究[69-76]。如圖 3 所示, 緩蝕劑根據化學組成可以分為有機緩蝕劑和無機緩蝕劑;根據控制電化學腐蝕部位可分為陽極型、陰極型 和混合型緩蝕劑;根據形成的保護膜類型分為氧化膜型、沉淀膜型、吸附膜型緩蝕劑。在不同的腐蝕介質中 應用不同類型的腐蝕劑,在淡水或海水中,因其 pH 呈中性或者弱堿性常使用有機類緩蝕劑。在中性腐蝕介 質中應用最多的為苯并三氮唑(BTA)和它的衍生物類,緩蝕效率達到了 90%以上,但使用成本高、毒性重。王琳等[77]為了研究苯并三唑對碳鋼/銅合金電偶腐蝕行為的影響,通過觀察電極分布、電流密度分布和電化 學阻抗譜得出了在銅合金和碳鋼的電偶腐蝕過程中,BTA 的加入僅僅對銅合金的腐蝕起到了良好的抑制作 用,對碳鋼的耐蝕抑制效果不明顯;在銅合金表面形成的 Cu-BTA 分子膜更加穩定且緩蝕效果良好。關于緩 蝕劑的耐蝕機理學者提出了不同的理論,其中吸附膜機理最成熟[78]。有機類緩蝕劑含有的極性基團或者含 有不飽和有機物上的 Π 鍵與 Cu 原子上的空軌道形成配位鍵,在銅合金表面形成具有疏水性的吸附膜,可以 阻止腐蝕介質與合金的進一步接觸,提高了銅合金的耐蝕性。
圖 5 緩蝕劑分類
Fig.5 Classification of corrosion inhibitors
3.4 防腐涂料
使用防腐涂料是減緩銅合金腐蝕簡單有效的保護方式之一。但是,涂料附著力不夠,在海水的浸泡下涂 層容易出現大面積的脫落,因此需要提高涂層與基體的附著力改善涂料的防腐能力。白雪等[79]通過基體樹 脂、固化劑等配方試驗,篩選出對銅合金表面具有良好耐腐蝕效果的配方,經過各種性能測試,該涂料可以 作為銅合金管路防腐涂料。潘鑫宇等[80]利用聚多巴胺(PDA)輔助共沉積法制備了高性能防腐涂層,并借助 緩蝕劑進一步強化涂層的耐蝕性。Jena 等[81]提出了一種新型的三元復合涂層,由氧化石墨烯-殼聚糖-銀組成,該復合涂層具有很強的防腐性和抗菌性能,成本廉價也可工業規模化生產,在海洋環境中具有廣闊的應用前景。Gao 等[82]采用激光選區熔化法在 90/10 銅鎳合金表面制備了不同 Ti 含量的 Al-Ti-Ni 復合涂層,電化學實驗結果顯示帶有涂層的銅鎳合金比裸銅鎳合金在 3.5% NaCl 溶液中有更強的耐腐蝕性,當 Ti 含量為 30%時,合金表面形成的鈍化膜最致密,穩定性最強。石墨烯具有顯著的惰性和不滲透性,石墨烯涂層對鎳 和銅具有良好的耐腐蝕性。對含石墨烯涂層的耐腐蝕性的早期研究通常是在氯化物的環境中進行的。Raman 等[83]研究了石墨烯涂層在酸和堿等侵蝕性更大的環境中的耐腐蝕性,結果表明多層石墨烯的穩定性基本不 受腐蝕環境的影響。Vinodhini 等[84]合成反應制得反應性 SiC 納米顆粒,并通過 FE-SEM(場發射掃描電子 顯微鏡)、AFM(原子力顯微鏡)、FTIR(傅里葉紅外變換)和 TGA(光譜和熱重分析)等技術,對天然 海水中的 Cu-Ni 合金上形成的新型納米復合涂層進行了研究,結果表明反應性 SiC 納米顆粒均勻地分散在 材料導報, 2024, 38(18): 23020095 DOI: 10.11896/cldb.23020095 http://www.mater-rep.com 11 / 18 合金表面和涂層界面,阻礙了侵蝕離子的傳遞從而提高了合金的耐蝕性。現在對于防腐涂料的要求需要環 保無毒,逐漸向高固體分(指固體含量的體積分數在 65%-80%之間)、無溶劑和使用壽命長的方向發展。除此之外,如何提高涂層的附著力和致密性也是現在研究者們關注的焦點[85]。
3.5 超疏水膜技術
超疏水膜技術是指利用水熱法、刻蝕法、電化學沉積法等在低表面能的材料表面構建納米粗糙結構[86- 87]。該薄膜可以在微納米凹凸中產生一層空氣膜,避免腐蝕介質與金屬基體直接接觸,達到了防腐的目的。熊靜文等[88]采用高速電火花切割技術構造出表面粗糙結構,進一步降低材料表面能,在銅基體表面制備超 疏水膜,在 3.5% NaCl 溶液中對試樣表面進行極化測試時,帶有超疏水膜的試樣表現出良好的耐蝕性。Mohamed 等[89]發現通過 Ni 和 Ni-石墨烯復合材料恒電位沉積,用硬脂酸處理后制備的超疏水膜具有微納米 結構,有較高的化學穩定性和機械耐磨性,帶有超疏水膜的銅基材在 0.5 mol/L NaCl 中具有強的耐蝕性。表 1 列舉了多種制備超疏水表面的方法并介紹了其優缺點。
表 1 制備超疏水膜表面的方法及特點[86]
免責聲明:本網站所轉載的文字、圖片與視頻資料版權歸原創作者所有,如果涉及侵權,請第一時間聯系本網刪除。
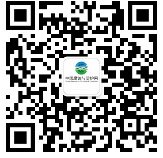
官方微信
《腐蝕與防護網電子期刊》征訂啟事
- 投稿聯系:編輯部
- 電話:010-62316606
- 郵箱:fsfhzy666@163.com
- 腐蝕與防護網官方QQ群:140808414