隨著油氣資源需求量不斷增加及高溫高含硫酸油氣田的勘探開發,油氣田面臨的服役環境日益苛刻。高溫、高H2S/CO2分壓、Cl-及S元素等多因素綜合作用對油氣工業用管材方案設計和現場生產安全提出挑戰。
鎳基耐蝕合金因具有良好的力學、加工及耐蝕性,被廣泛應用于酸性油氣田開發中。鎳基合金中Cr、Ni元素含量較高,可以在材料表面形成鈍化膜,有效保護金屬基體。服役溫度及H2S/CO2分壓升高、S元素沉積及高鹽環境Cl-侵蝕等因素均可能影響鎳基合金表面鈍化膜的完整性。鈍化膜一旦遭到破壞且不能有效自修復,可能會形成點蝕,從而引發腐蝕失效問題。
鎳基耐蝕合金在高溫高酸性環境中存在的主要失效風險為點蝕和陽極溶解型應力腐蝕開裂。而陽極溶解型應力腐蝕開裂多萌生于鈍化膜局部破損形成的點蝕坑位置。因此,點蝕的萌生與發展對鎳基耐蝕合金在高含硫酸環境中的服役性能變化起著重要作用。
目前,對于鎳基耐蝕合金在高溫高含硫酸環境中的腐蝕行為研究多聚焦于其在服役環境中的腐蝕速率、點蝕敏感性和應力腐蝕開裂敏感性評估,針對其在高溫高酸性工況下點蝕萌生與發展機制的系統分析討論相對較少。為此,有必要開展試驗評價及分析工作,探究鎳基耐蝕合金在高溫高酸性腐蝕環境中的鈍化膜破鈍機制。
中海油研究總院有限責任公司和北京科技大學的研究人員利用高溫高壓反應釜模擬高溫高含H2S/CO2酸性腐蝕環境,開展不同周期下的腐蝕模擬評價試驗,研究了G3合金在高溫高酸性腐蝕環境中的點蝕敏感性,提出了G3合金的鈍化膜破鈍機制。
試驗材料及溶液
試驗材料為G3合金(UNS N06985),熱處理狀態為退火+固溶態。將材料加工成尺寸為20 mm×20 mm×3 mm的試樣,用水磨砂紙逐級打磨試樣表面后拋光,并依次進行丙酮除油、去離子水和無水乙醇清洗、冷風吹干后,放置在無氧器皿中備用。每組腐蝕模擬試驗取6個平行試樣。
試驗溶液為30000 mg/L NaCl溶液,使用去離子水和分析純級化學試劑配制而成。試驗開始前,向試驗溶液中通入99.999%高純氮氣進行除氧處理,每升溶液的通氣時間約為12 h。
高溫高壓腐蝕模擬試驗
在高溫高壓反應釜中模擬高溫高含H2S/CO2腐蝕環境:150 ℃,3 MPa H2S分壓,2 MPa CO2分壓,30000 mg/L NaCl溶液。
將腐蝕試樣安裝在高溫高壓反應釜內的夾具上,采用高純氮氣吹掃釜體除氧1 h,然后導入試驗溶液。釜體升溫至150 ℃后,通入試驗氣體至設定壓力,試驗周期分別為168,336,504,672 h。
腐蝕形態觀察
高溫高壓腐蝕模擬試驗結束后取出試樣,去離子水清洗,無水乙醇脫水后冷風吹干。利用SEM觀察試樣表面腐蝕形態,并結合EDS對試樣表面鈍化膜進行物相分析。
圖1 試樣經過不同時間腐蝕試驗后的表面微觀形貌
由圖1可見:腐蝕168 h后的試樣表面平整且具有肉眼可見的金屬光澤,微觀可見清晰完整的原始機械劃痕,幾乎沒有腐蝕痕跡;腐蝕336 h后,試樣表面出現少量顆粒狀腐蝕產物凸起,原始機械劃痕深度變淺,未見明顯腐蝕產物生成。隨著腐蝕時間的延長,試樣表面的顆粒狀腐蝕產物逐漸增多,腐蝕504 h后,基體表面依然完整,而腐蝕672 h后,試樣表面完整性受到破壞,部分區域鈍化膜出現破損并形成了大小不一的點蝕坑。其中,最大點蝕坑直徑約為42.0 μm。進一步觀察發現,點蝕坑呈閉合狀態,蝕坑口仍覆蓋有多孔鈍化膜。
進一步分析腐蝕672 h后試樣表面點蝕坑內外鈍化膜的元素組成,可見蝕坑內鈍化膜主要含有Fe、Ni、Cr、Mo、O和S元素,而點蝕坑外沒有檢測到S元素,說明經過腐蝕后點蝕坑內鈍化膜中含有一定量的硫化物,H2S參與了G3合金在高酸性環境中的點蝕發展進程。
鈍化膜性能測試
采用AXIS-UltraDLD型X射線光電子能譜在不同電位條件下進行測試,進一步分析鈍化膜的組成,光源選用單色Al Kα(入射光子能量為1486.6 eV),15 kV靶電壓,1.33×10-6 Pa真空度。對譜圖進行譜線能量校正后,利用XPS peak41曲線擬合程序對譜圖峰位進行擬合分析。
圖2 試樣經過不同時間腐蝕試驗后表面鈍化膜中Cr元素的高分辨XPS結果
圖3 試樣經過不同時間腐蝕試驗后表面鈍化膜中Ni元素的高分辨XPS結果
圖4 試樣經過不同時間腐蝕試驗后表面鈍化膜中Fe元素的高分辨XPS結果
由圖2~4可見:腐蝕336 h后,G3合金表面鈍化膜依舊保持完整,由Cr2O3、Cr(OH)3、NiO、Ni(OH)2和FeO、Fe3O4等組成;腐蝕504 h后,鈍化膜逐漸受到侵蝕,出現了少量NiS;腐蝕672 h后,Cr、Ni的氫氧化物和氧化物及Fe氧化物的信號均明顯減弱,鈍化膜中出現了Cr、Ni的硫化物Cr2S3、NiS2及鐵硫化物FeS,且信號均較強。材料表面鈍化膜穩定性被破壞,誘發點蝕。金屬硫化物的出現可能是導致G3合金表面鈍化膜發生不可逆損傷的原因。
破鈍機制分析
根據MACDONALD等提出的點缺陷模型(PDM模型),鈍化膜具有雙層結構且存在高含量的點缺陷。鈍化膜中電子及空穴傳輸處于動態平衡狀態。對于電子來說,在金屬/膜或膜/溶液界面進行的電化學反應是一個速度控制步驟,而金屬離子或氧離子缺陷在鈍化膜中的傳輸也是一個速度控制步驟。
在鈍化膜的生長過程中,施主缺陷(氧空位)主要存在于金屬/鈍化膜界面,并消耗于鈍化膜/溶液界面,而受主缺陷(金屬間隙離子)主要存在于鈍化膜/溶液界面,并消耗于金屬/鈍化膜界面。氧空位的遷移會導致鈍化膜的生長,而金屬間隙離子的遷移使得鈍化膜發生溶解。
圖5 G3合金在高溫高酸性環境中的鈍化膜破鈍機制
如圖5所示,腐蝕初期,G3合金鈍化膜表層主要由Cr、Ni的氫氧化物組成,鈍化膜內層主要由Cr、Ni、Fe的氧化物組成。鈍化膜結構具有雙極性n-p型半導體特性,能夠很好地阻礙陰離子向鈍化膜內層擴散及陽離子向鈍化膜外層擴散,有效保護基體表面。
根據PDM模型,隨著腐蝕的進行,鈍化膜中的氧空位不斷遷移至鈍化膜/溶液界面處,發生Schottky空位對反應,導致鈍化膜表面金屬陽離子溶解并與OH-形成金屬氧化物沉淀。由于溶液中S2-、HS-大量存在,且其極性高于Cl-和OH-,與Cl-及OH-發生競爭吸附,在鈍化膜表層形成金屬硫化物,這與上述試驗及XPS分析結果相符。同時,鈍化膜中的S2-可以借助氧空位向基體一側擴散遷移。
鈍化膜中空位遷移速率可能改變鈍化膜的保護性能。當S2-空位遷移速率小于金屬氧化物氧空位遷移速率時,遷移到鈍化膜中的S2-不足以破壞鈍化膜的完整性,鈍化膜內層的金屬氧化物仍然維持在動態平衡的穩定狀態。而當鈍化膜表層金屬硫化物中S2-空位遷移速率大于氧空位遷移速率時,S2-借助空位不斷向鈍化膜內部遷移擴散,最終使金屬氧化物完整性遭到破壞。
由于耐蝕元素Cr和Ni化學活性較高,在材料晶界處容易以碳化物形式析出,并在析出相中富積,造成晶界處貧Cr、貧Ni,因此容易在晶界處形成點蝕源。
點蝕源位置的金屬大量溶解將促進溶液中的陰離子向點蝕源遷移。一方面,S2-、HS-與Cl-競爭吸附,導致點蝕源位置富集高濃度的S2-和HS-,加速氧化物膜的分解;另一方面,由于歧化反應,鈍化膜局部大量H+電離,局部酸化也將加速鈍化膜中氧化物層溶解。
S2-、HS-與金屬基體發生反應生成的硫化物膜質地疏松,且易于吸附溶液中的Cl-。Cl-進入鈍化膜后能夠占據膜中的氧空位,并通過Mott-Schottky Pair反應產生氧空位/金屬離子空位對,新生成的氧空位再次被Cl-占據,氧空位數量減少,金屬離子空位增加。多余的金屬離子空位會在基體/膜界面局部堆積,并阻止鈍化膜繼續生長,破壞鈍化膜結構的動態平衡。最終,由于鈍化膜局部完全溶解或破裂,點蝕萌生并發展,進而形成穩定的點蝕坑。
結論
1 在高溫、高H2S/CO2分壓腐蝕環境中,腐蝕初期,G3合金表面鈍化膜主要由Cr、Ni的氫氧化物、氧化物 [Cr2O3、Cr(OH)3、NiO、Ni(OH)2] 及Fe的氧化物(Fe3O4和FeO)組成。隨著腐蝕時間的延長,鈍化膜中出現了Cr、Ni的硫化物Cr2S3、NiS2及鐵硫化物FeS。
2 G3合金在高溫高酸性環境中具有較高的點蝕敏感性。在模擬高溫、高H2S/CO2分壓腐蝕環境中腐蝕672 h后,G3合金表面鈍化膜破損并形成了大小不一的點蝕坑,其在高溫高酸性環境中的鈍化膜破鈍及點蝕萌生與S2-對鈍化膜的硫化作用有關。
免責聲明:本網站所轉載的文字、圖片與視頻資料版權歸原創作者所有,如果涉及侵權,請第一時間聯系本網刪除。
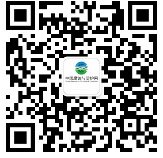
官方微信
《腐蝕與防護網電子期刊》征訂啟事
- 投稿聯系:編輯部
- 電話:010-62316606
- 郵箱:fsfhzy666@163.com
- 腐蝕與防護網官方QQ群:140808414