摘要:涂層的耐陰極剝離能力是環氧涂層性能中的一項非常重要的技術指標,該指標的好壞直接影響著管道的運行成本。那么涂層耐陰極剝離性能的測試方法及規范是一個非常重要的環節。對陰極剝離的測試,一些標準進行了規范,重點歸納總結了這些國內外標準對陰極剝離測試的規定。
關鍵詞:環氧涂層 涂層耐陰極剝離性能
0 引言
金屬的腐蝕按照腐蝕過程可以分為化學腐蝕和電化學腐蝕。化學腐蝕是金屬直接與環境介質發生化學反應而造成金屬的損傷,比如和酸、鹽(硝酸鹽、硫酸鹽等)、氧化劑等。電化學腐蝕是指不純的金屬與電解質溶液接觸時發生原電
池反應而使活潑金屬失去電子造成金屬的損傷。在自然界中,金屬的腐蝕主要是電化學腐蝕。
金屬防腐的主要手段就是采取金屬表面涂覆防腐涂層外加陰極保護的方式。金屬表面的防腐層能夠起到屏蔽外界環境對金屬的侵蝕作用,但是在管道的運輸、鋪設以及回填的過程中難免會出現防腐層的損傷而造成漏點。在漏點處與電解質接觸就會發生金屬的電化學腐蝕。為了延長管道的使用壽命,在管道鋪設過程中要對管道采取陰極保護的處理。所謂陰極保護系統則是提供了一個可以失去電子的遠陽極,通過外加電流或犧牲陽極的腐蝕電流將電子源源不斷地供給被保護金屬,使之陰極極化達到其腐蝕平衡電位以下。結果,在電解質中得到外援電子的金屬不被腐蝕。不過陰極保護會對陰極區域的涂層起到一定的破壞作用,因為在陰極電流作用下,氧被還原產生OH-,或H2O離解產生的H+,H+在陰極得到電子,形成初生態氫,這兩個陰極反應都使陰極區域形成過剩的OH-,造成堿性環境。陰極區pH值升高,大量的OH-遷移至金屬/防腐層交界面,使與防腐層粘結的基體金屬氧化物層溶解,或侵蝕界面的聚合物,或降低聚合物與金屬的粘結力,從而使防腐層產生剝離,這就是所謂的陰極剝離。
涂層的耐陰極剝離能力是環氧涂層性能中的一項非常重要的技術指標,該指標的好壞直接影響著管道的運行成本。因為陰極剝離的面積越大需要供給的電子就會越多。無論是犧牲陽極的方式還是外加電流的方式,都會提高其運行成本。評價涂層的耐陰極剝離能力可以通過陰極剝離試驗的測試方法進行,那么陰極剝離的測試規范就尤為重要了。下面我們就行業內常用的幾個標準對涂層耐陰極剝離性能的測定規范進行探討。
1 陰極剝離試驗
實驗室模仿陰極保護過程,人為制作電解質溶液、漏點以及陰極保護電流觀察陰極部位剝離的半徑,就是陰極剝離試驗。陰極剝離試驗的結果與溫度、電解質種類和濃度、施加電位、涂膜厚度、前處理等因素有關。試驗能夠在短期
內顯示出涂層的耐陰極剝離能力。陰極剝離試驗的測試方法直接影響著試驗結果。陰極剝離的具體測試過程中包括試驗孔的孔徑、電極距離試驗孔的位置、長期陰極剝離性能時電解質液體的更換頻率等。對于陰極剝離試驗的這些具
體要求,各個標準具體要求有所不同。對于管道防腐常用的標準包括我國國家標準GB/T 23257—2017《埋地鋼質管道聚乙烯防腐層》、GB/T 39636—2020《鋼質管道熔結環氧粉末外涂層技術規范》、GB/T 18593—2010《熔融結合環氧粉末涂料的防腐蝕涂裝》,以及行業標準SY/T 0442—2018《鋼質管道熔結環氧粉末涂料內防腐層技術標準》、SY/T 0315—2013《鋼制管道熔結環氧粉末外涂層技術規范》等,另外還有ISO 21809-2、CSA Z245.20-18等國際標準。本文重點介紹GB/T 23257—2017、GB/T 39636—2020、SY/T 0315—2013、ISO 21809-2和CSA Z245.20-18,之所以列出SY/T 0315的檢測方法是因為SY/T 0442—2018以及GB/T 18593—2010等標準中測試陰極剝離的方法引用的是SY/T 0315的檢測方法。
1.1 陰極剝離實驗裝置
1.1.1 實驗裝置示意圖
測試陰極剝離試驗的實驗裝置包括:直流電源、烘箱或者加熱板、參比電極、鉑電極、塑料圓柱筒、3%氯化鈉溶液、多功能刀、直尺或游標卡尺。測試陰極剝離性能的裝置示意圖如圖1所示,該裝置相當于一個外加電流的方式,在被測涂層上面打一個試驗孔模擬漏點,通過一個直流電源給被保護的金屬提供源源不斷的電子,用3%的氯化鈉溶液模擬電解質溶液。
1.1.2 不同標準對實驗裝置的規范要求
(1) 試驗孔直徑規定
標準對試驗孔徑的要求見表1。
1.1.2 不同標準對實驗裝置的規范要求
(1) 試驗孔直徑規定
標準對試驗孔徑的要求見表1。
對于試驗孔孔徑的規定,除了SY/T 0315—2013和CSA Z245.20-18標準規定了單一的孔徑外,其他標準都根據涂層厚度規定了孔徑的大小,基本是涂層厚度增加,要相應增大試驗孔的孔徑。
(2) 電極與試驗孔的距離
不同標準中電極與試驗孔的距離見表2。
表2中列舉的5個環氧防腐涂層相關標準中對陰極剝離測試的方法中除了GB/T 39636—2020和ISO 21809-2:2014中規定了電極與試驗孔的距離外,其他標準都沒有明確規定電極距離試驗孔的高度。那么電極距離試驗孔的高度對陰極剝離的結果有沒有影響呢?本文進行了一組實驗對比。選用相同的粉末,相同的基材處理方式,電極距離試驗孔的高度分別為10 mm、40 mm和70 mm的位置進行陰極剝離實驗。在65 ℃,-1.5 V,條件下測試30 d的陰極剝離,結果如表3所示。
從表3中的數據來看,電極距離試驗孔的位置為10 mm的時候測試的結果為6.47 mm,距離40 mm的時候測試的結果為6.12 mm,距離為70 mm的時候測試的結果偏差較大為21.50 mm,因此在測試過程中還要注意電極距離試驗孔的位置。
(3) 電解質溶液的要求
不同標準對電解質溶液要求見表4。
表4中列出的幾個標準對電解質溶液的規定來看,都規定的是3%的氯化鈉溶液作為電解質溶液,除了GB/T 23257—2017以外,其他標準都明確規定了溶液的體積不得少于300 mL。另外,GB/T 23257—2017和GB/T 39636—2020中規定,在測試過程中要保持溶液的pH值為6~9,而加標CSA Z245.20-18中明確規定,在測試長期陰極剝離時,要在第7 d、14 d、21 d之后更換新的溶液。在測試陰極剝離試驗過程中實際上是一個原電池反應的過程,在陰極處水電離的H+離子得到電子釋放出H2,同時使得陰極區域OH-
離子濃度升高,堿性增強,在陽極區域電解質中的Cl-失去電子生成Cl2,Cl2溶于水生成次氯酸和HCl,消耗一定的Cl-離子,同時也會影響溶液的pH值,使溶液的pH值降低,因此,在測試長期陰極剝離實驗的過程中,最好是定期更換電解質溶液來確保電解質溶液的濃度。
1.2 不同標準對涂層耐陰極剝離性能的規定
涂層的陰極剝離測試的是試驗孔邊緣到被剝離掉的涂層的邊緣之間的距離,即剝離半徑R,如圖2所示。涂層的陰極剝離試驗測試分為長期陰極剝離試驗和短期陰極剝離試驗,長期陰極剝離試驗一般測試時間為28 d或者30 d,短期陰極剝離試驗一般為48 h或者24 h,不同標準對陰極剝離性能的具體規定列于表5中。
從表5中的數據來看,不同標準對涂層的耐陰極剝離性能的規定基本是一致的,都規定了短期陰極剝離和長期陰極剝離的技術指標,陰極剝離的技術指標相差也不大,不過隨著工程質量要求的越來越嚴格,對涂層的耐陰極剝離能
力的要求也越來越高,特別是長期陰極剝離的技術指標,有的技術項目規格書中就明確規定,涂層的長期陰極剝離不得大于10 mm。
2 結語
環氧涂層的耐陰極剝離性能是涂層的重要性能之一,涂層的耐陰極剝離性能與電解質溶液的溫度和濃度、電解質溶液的含氧濃度,施加的電壓,涂層的厚度,涂層涂裝前金屬基材預處理的方法以及金屬基材的類型等因素有關。按照一定的規范進行陰極剝離試驗的測試是非常必要的。綜合考慮不同標準對陰極剝離測試的規定,在測定陰極剝離過程中要注意以下幾點。
(1) 電解槽塑料桶的直徑為75 mm,電解質溶液的體積不少于300 mL,電解質溶液液面與盲孔的距離不少于70 mm;同時GB/T 23257—2017中規定了溶液的高度為電解槽的4/5,所以電解槽的高度要在87.5 mm以上。
(2) 鉑電極距離試驗孔的距離為10 mm和40 mm所測的陰極剝離結果基本一致,但是距離70 mm時的測試的剝離結果明顯不同于其他兩個,也就是鉑電極距離試驗孔的距離不能太大,最好是按照已經規定了距離的標準執行,鉑
電極距離實驗孔的距離定為10 mm;
(3) 在測定長期陰極剝離試驗時一周更換一次電解質溶液,來確保電解質溶液的濃度;
(4) 涂層的厚度對陰極剝離的測試結果有直接影響,涂層越厚,陰極剝離半徑越小,上述的5個標準中,除了ISO 21809-2:2014中規定的涂層的厚度為350~500 μm之外,其他標準對涂層厚度的規定都是(350±50) μm,在測試過程中一定要注意要按照標準規定的厚度制備樣件。
免責聲明:本網站所轉載的文字、圖片與視頻資料版權歸原創作者所有,如果涉及侵權,請第一時間聯系本網刪除。
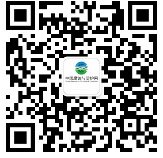
官方微信
《腐蝕與防護網電子期刊》征訂啟事
- 投稿聯系:編輯部
- 電話:010-62316606
- 郵箱:fsfhzy666@163.com
- 腐蝕與防護網官方QQ群:140808414