2018年4月17日,西南航空1380號航班(Southwest Airlines Flight 1380)的一架波音737型客機在巡航狀態時,突然發生發動機爆炸事故,事故導致1人遇難,148人生還。
初步的調查結果:這次事故是由于發動機發生了非包容性故障。
航空事故歷史中,發動機葉片損壞而引發的飛機事故還真不少見
2014年,我國南航CZ3739航班飛機引擎空中著火,事后調查顯示發生故障的發動機進口處,壓氣機風扇的葉片有斷裂。據推測,有可能是葉片斷掉后進入發動機內,損傷發動機進氣流場,導致后者發生“畸變”,進而形成“喘振”。所幸的是這次事故沒有造成人員傷亡。
2016年8月27日,一架西南航空的波音737-700型客機在執飛新奧爾良飛奧蘭多的航班時,同樣發生CFM56-7B型發動機的風扇葉片非包容性故障,所幸此次事故中客機安全降落,并無更為嚴重事故發生。
其實據不完全統計,我國空軍現役飛行的發動機事故中,80%都跟發動機葉片斷裂失效有關。而這么嬌貴的部分一旦發生斷裂失效,對發動機乃至整個飛機的損害往往是致命性的。
可見,發動機葉片斷裂不容小覷,那么今天小編就帶領大家全方位認識一下發動機葉片的斷裂,看看它為啥有這么驚人的破壞力。
從理論上看,渦輪葉片斷裂的故障機理有疲勞、超應力、蠕變、腐蝕、磨損等。
疲勞
發動機工作時,由于經常起動、加速、減速、停車以及其他條件的影響,會使渦輪各部件承受復雜的循環載荷作用,使得葉片經受大量彈性應力循環,最終引起高周疲勞、低周疲勞或熱疲勞,使得渦輪葉片斷裂。
渦輪發動機葉片根部疲勞裂紋擴展
超應力
渦輪葉片由于其形狀的不規則,葉片中存在應力集中部位。盡管在設計中往往會采取一系列措施加以避免,但實際上,超應力仍然是造成渦輪葉片斷裂的一個原因。
發動機葉片中應力分布建模
蠕變
高溫環境下,蠕變斷裂是渦輪葉片主要的失效形式之一。隨著渦輪后燃氣溫度從20世紀50年代的1150K增加到現在的2000K,蠕變將導致葉片的塑性變形過大甚至產生蠕變斷裂。
發動機葉片的蠕變斷裂
腐蝕
腐蝕來自于葉片所受的高溫燃氣。高溫燃氣對葉片的腐蝕既包括沖刷造成的腐蝕,也包括高溫燃氣對金屬葉片的氧化腐蝕。腐蝕會降低葉片的性能,當腐蝕達到一定程度,葉片材料性能不能滿足要求時,就會發生斷裂。
壓氣機葉片的嚴重腐蝕
葉片的斷裂除此還和材料和制造手段有一定的關系,下面小編介紹一下葉片的材料和主要制造技術。
1.變形高溫合金葉片
1.1 葉片材料
變形高溫合金發展有50多年的歷史,國內飛機發動機葉片常用變形高溫合金如表1所示。高溫合金中隨著鋁、鈦和鎢、鉬含量增加,材料性能持續提高,但熱加工性能下降;加入昂貴的合金元素鈷之后,可以改善材料的綜合性能和提高高溫組織的穩定性。
表1 國內飛機葉片用高溫合金牌號及其工作溫度
1.2 制造技術
變形高溫合金葉片的生產是將熱軋棒經過模鍛或輥壓成形的。模鍛葉片主要工藝如下:
1)鐓鍛榫頭部位;
2)換模具,模鍛葉身,通常分粗鍛、精鍛兩道工序。模鍛時,一般要在模腔內壁噴涂硫化鉬,減少模具與材料接觸面阻力,以利于金屬變形流動;
3)精鍛件,機加工成成品;
4)成品零件消應力退火處理;
5)表面拋光處理。分電解拋光、機械拋光兩種。
常見問題:
1)鋼錠頭部切頭余量不足,中心亮條缺陷貫穿整個葉片;
2)GH4049合金模鍛易出現鍛造裂紋;
3)葉片電解拋光中,發生電解損傷,形成晶界腐蝕;
4)GH4220合金生產的葉片,在試車中容易發生“掉晶”現象;這是在熱應力反復作用下,導致晶粒松動,直至剝落。
葉片是航空發動機關鍵零件它的制造量占整機制造量的三分之一左右。航空發動機葉片屬于薄壁易變形零件。如何控制其變形并高效、高質量地加工是目前葉片制造行業研究的重要課題之一。隨著數控機床的出現,葉片制造工藝發生重大變化,采用精密數控加工技術加工的葉片精度高,制造周期短,國內一般6~12個月(半精加工);國外一般3~6個月(無余量加工)。
精密數控加工技術加工葉片
2.鑄造高溫合金葉片
2.1 葉片材料
半個多世紀來,鑄造渦輪葉片的承溫能力從1940s年代的750℃左右提高到1990s年代的1700℃左右,應該說,這一巨大成就是葉片合金、鑄造工藝、葉片設計和加工以及表面涂層各方面共同發展所作出的共同貢獻。葉片用鑄造高溫合金如表2所示,圖11為鑄造高溫合金葉片。北京航空材料研究所、鋼鐵研究總院、沈陽金屬所是鑄造高溫合金的研制單位。
表2 國內葉片用鑄造高溫合金牌號及使用溫度
2.2 制造技術
研制新型航空發動機是鑄造高溫合金發展的強大動力,而熔鑄工藝的不斷進步則是鑄造高溫臺金發展的堅強后盾。回顧過去的半個世紀,對于高溫合金發展起著重要作用的熔鑄工藝的革新有許多,而其中三個事件最為重要:真空熔煉技術的發明、熔模鑄造工藝的發展和定向凝固技術的崛起。
葉片熔鑄加工
真空熔煉技術。真空熔煉可顯著降低高溫合盒中有害于力學性能的雜質和氣體含量,而且可以精確控制合金成分。使合金性能穩定。
熔模鑄造工藝。國內外熔模鑄造技術的發展使鑄造葉片不斷進步,從最初的實心葉片到空心葉片,從有加工余量葉片到無余量葉片,再到定向(單晶)空心無余量葉片,葉片的外形和內腔也越來越復雜;空心氣冷葉片的出現既減輕了葉片重量,又提高了葉片的承溫能力。
美國Howmet公司等用于細晶鑄造制造葉片等轉動件,常用合金為:In792、Mar-M247和In713C合金;導向葉片等靜止件則多用IN718C、PWA1472、Rene220、及R55合金。1990s年代之后,為滿足新型發動機之需要,計算機數值模擬在合金成分設計和鑄造工藝過程中的應用日趨增多。
3.超塑性成形鈦合金葉片
3.1 葉片材料
目前,Ti6Al4V和Ti6Al2Sn4Zr2Mo及其他鈦合金,是超塑性成形葉片等最為常用的鈦合金。
表3 葉片等旋轉件用鈦合金及其特點
我國耐熱鈦合金開發和應用方面也落后于其他發達國家,英國的600℃高溫鈦合金IMI834已正式應用于多種航空發動機,美國的Ti-1100也開始用于T55-712 改型發動機,而我國用于制造壓氣機盤、葉片的高溫鈦合金尚正在研制當中。其它像纖維增強鈦基復合材料、抗燃燒鈦合金、Ti-Al金屬間化合物等雖都立項開展研究,但離實際應用還有一個過程。
3.2 制造技術
早在1970s,鈦合金超塑性成形技術就在美國軍用飛機和歐洲協和飛機中得到了應用。在隨后的十年中,又開發了軍用飛機骨架和發動機用新型超塑性鈦合金和鋁合金。在軍用飛機及先進的民用渦扇發動機葉片等,均用超塑性成形技術制造,并采用擴散連接組裝。
4.新型材料葉片
4.1 碳纖維/鈦合金復合材料葉片
美國通用公司生產的GE90-115B發動機,葉身是碳纖維聚合物材料,葉片邊緣是鈦合金材料,共有渦扇葉片22片,單重30~50磅,總重2000磅。能夠提供最好的推重比,是目前最大的飛機噴氣發動機葉片,用于波音777飛機,2010年9月在美國紐約現代藝術館展出。
4.2 金屬間化合物葉片
盡管高溫合金用于飛機發動機葉片已經50多年了,這些材料有優異的機械性能,材料研究人員,仍然在改進其性能,使設計工程師能夠發展研制可在更高溫度下工作的、效率更高的噴氣發動機。不過,一種新型的金屬間化合物材料正在浮現,它有可能徹底替代高溫合金。
這是因為高溫合金在高溫工作下時會生成一種γ相,研究表明,這種相是使材料具有高溫強度、抗蠕變性能和耐高溫氧化的主要原因。因此,人們開始了金屬間化合物材料的研究。金屬間化合物,密度只有高溫合金一半,至少可以用于低壓分段,用于取代高溫合金。
NB-Si系化合物
英國羅爾斯-羅伊斯公司,在1999年,申請了一項γ相鈦鋁金屬間化合物專利,該材料是由伯明翰大學承擔研制的。這種材料可以滿足未來軍用和民用發動機性能目標的要求,可以用于制造從壓縮機至燃燒室的部件,包括葉片。這種合金的牌號,由羅爾斯-羅伊斯公司定為: Ti-45-2-2-XD。
2010年,美國通用公司、精密鑄件公司等申請了一項由NASA支持的航空工業技術項目(AITP),通過驗證和評定鈦鋁金屬間化合物(TiAl,Ti-47Al-2Nb-2Cr,原子分數)以及現在用于低壓渦輪葉片的高溫合金,使其投入工業生產中,如圖24所示為鋁化鈦金屬間化合物葉片(伽馬鈦合金)。與鎳基高溫合金相比,TiAl金屬間化合物的耐沖擊性能較差;將通過疲勞試驗等,將技術風險降至最低。
免責聲明:本網站所轉載的文字、圖片與視頻資料版權歸原創作者所有,如果涉及侵權,請第一時間聯系本網刪除。
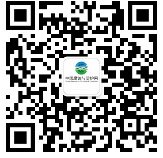
官方微信
《中國腐蝕與防護網電子期刊》征訂啟事
- 投稿聯系:編輯部
- 電話:010-62316606-806
- 郵箱:fsfhzy666@163.com
- 中國腐蝕與防護網官方QQ群:140808414