優化鎳磷鍍工藝的有效途徑
前處理是保證鍍層質量的前提。電鍍產品質量問題的80%以上都出在前處理工序。鎳磷鍍前處理則顯得更加重要,特別是石油機械產品的鍍,一般選用鈣鋼,經調質處理27~31HRC,滲碳0.05~0.1mm。工件形狀復雜、多孔和內、外有螺紋及盲孔等;多數零件采用20~40CrMo的合金鋼,均經過不同工藝的熱處理,為保證鍍層與基材的結合,各道工序之間必須徹底清洗,鍍件在沖洗槽中停留時間不少于2min己成為獲取質量良好鍍層的重要條件。
按前面敘述的典型前處理工藝外,要注意有些鍍件上有殘磁,要用消磁機消除材料上的磁性。除油后,要在大于80℃熱水中清洗,把粘附的氧化鈉(堿液遇到鹽酸生成物)除凈;在保護非鍍面和中心孔時,嚴禁用裸手操作,以防手脂油的污染;清理好的工件,要妥善存放好、防止第二次污染,待生產用;生產前仍要再次加強清洗,并用80℃以上熱純水,把粘附臟物、油污再次徹底清洗干凈;要在配制1:1活化液中,浸蝕1~3min,再經冷水洗→熱純水浸后,方可入專用的鍍槽,并攪拌、循環鍍液,要始終保持鍍液的流動性和穩定性。
另外,做好中心孔保護是需第二次磨削的關鍵。在高壓管匯元件中,旋塞的非鍍面保護,特別是中心孔的保護是夫系到鍍件施鍍尺寸達到要求,保證質量的難點。在實踐中我們采用了多種辦法,涂阻鍍液、用環氧樹脂材料堵塞、金屬夾具等等,仍然未完全解決中心孔的保護,使廠家在第二次磨削中尺寸偏位造成鍍件返修、甚至報廢。
在前處理過程中,增加了一道專有的清洗、保護工序,先要將中心孔除油,徹底清洗干諍。在工件經熱水清洗后,將“三和”牌密封膠滴入,經數小時干燥、固化后再使用;這種密封膠鍍前、鍍中耐堿、耐酸、耐溫,鍍后完整無損,而且也很易取下。工件經熱處理后的第二次磨削加工,中心孔的位置和尺寸都保證了加工質量。
鎳磷鍍層的磨削加工,要正確對待。要選用綠色碳化硅或白剛玉砂輪,粒度60~80#,硬度中軟,組織狀態中等,其尺寸和形狀視零件而定;同時要計算好磨削用量,確定砂輪和工件的轉速及切削深度和走刀量。同時,要注意鎳磷合金鍍層磨削時無火花,加工時,鍍層表面應涂上紅丹油,以便對刀。否則,容易將鍍層磨損。
鎳磷鍍層在85℃左右的溫度,厚的鍍層施鍍時間在6~7h條件下進行,石油機械零件,內外有管螺紋、連接頭的端面、內孔尺寸精度要求高,而且,都要保護。選用的保護材料,要耐高溫、耐酸、粘結力強、鍍后易撕下,工件表面無殘留膠;我們在生產中選用鴻富達特種膠粘帶(蘇州)公司生產的T×75電鍍膠帶及定制生產的專用尺寸膠片。使用非常方便,耐高溫、耐溶劑、粘性佳,又便于撕下,確保了用戶對鍍件非鍍面的尺寸要求。
鍍液質量是保證鍍層質量的基礎。
化學鍍鎳的反應過程是一個自催化的氧化-還原過程。以次磷酸鈉作還原劑的酸性鍍液,次磷酸鈉被氧化生成亞磷酸鹽懸浮于鍍液中或沉淀在鍍件上。因此,生產過程中,要適時補充濃縮液,以維護鍍液的穩定性。
在生產過程中,對鍍層≥0.06mm的鍍層,由于施鍍時間一般要五個小時左右,無論采用何種循環、攪拌,甚至對工件移動或振動,若潤濕劑未達到一定的比例,在鍍件的上端面或者經第二次磨削加工后,鍍層上的針孔,顯而易見。
為防止針孔,要在鍍液中添加潤濕劑十二烷基硫酸鈉。一般資料上介紹,添加量在0.05~0.1g/L之間,超量將影響鍍層的質量。經多年的生產、實驗和驗證,配方量要達到0.75g/L,并在鍍液升溫到≥80°C時,在攪拌或循環條件下緩慢加入;因生產過程中消耗和帶出量較大,每次開缸時,仍要按0.025g/L的量再補充。
生產前,取一根Φ2mm的鐵絲,做成Φ90mm的圓環,垂直放入鍍液中,然后輕輕提起,如圓環內液膜當即破裂、說明溶液中潤濕劑含量少、可按0.02g/L十二烷基硫酸鈉再補充。按此辦法施鍍的工件表面,光潔如鏡,無針孔,保證了產品的質量。
在應用中,鍍液的維護和控制是非常重要的。
化學鍍鎳時鎳離子消耗,還原劑濃度減少等問題,隨時影響化學鍍鎳液的穩定性。可以說這是化學鍍鎳工藝難以掌握的主要原因。一般情況下,要按化驗室分析結果,按比例添加濃縮液和穩定劑、光亮劑。對鍍層厚度大于0.06mm,定時分析Ni2+離子濃度和調整pH值非常重要,生產過程中每鍍一小時或槽液有異向時,要分析硫酸鎳的濃度,根據化驗結果計算所需添加的補充液,維護鍍液的穩定。
鎳離子濃度的調整和控制是化學鍍鎳工藝最基本的管理項目,它決定了鍍層的沉積速度和鍍層質量。同時,要控制好溫度和pH值。溫度對沉積速度影響極大,一般控制在85~90℃,新配鍍液先取下限,以維持沉積速度的穩定。由于pH值的高低將會影響鍍液的穩定性,必須加強控制。
在實踐中逐步摸索做鍍層厚0.06~0.09mm,Ni2+含量取上限,溫度和pH值低一點的操作辦法。即:Ni2+含量≥25g,溫度83±1℃,pH值4.4±1,鍍速控制在10~12μm/h;鍍液在生產中要過濾,鍍液中的沉積物、鍍槽、加熱管和掛具表面的鎳層及雜物,應及時清除或用褪鍍液退除;當發現鍍液生成氣泡,顏色變淡,這就顯示了鍍液已發生自然分解,應盡快進行處理,一般補加2g/L蘋果酸、2m1/L乳酸等絡合劑。按以上維護和控制辦法,加工的鍍件光潔一致,產品質量穩定、深受用戶好評。鍍液一般可用6~8個周期。
擴寬化學鍍鎳的優勢
用鎳磷鍍層代替鍍硬鉻在工業中應用己非常成功,特別是形狀復雜的工件、如油田抽油泵筒、管套、泵體、液壓管件等,不僅可以消除六價鉻對環境的污染,而且可以省略鍍后的研磨、大大提高了生產效益。
化學鍍鎳與電鍍硬鉻的比較、存在的不足和差距,主要是鍍態的硬度;鎳磷合金硬度500~650HV,硬鉻硬度800~900HV;鎳磷鍍層需經過熱處理后,才能達到900~1100HV;而在施鍍的方法上,結合力、孔隙率和均勻度上優于硬鉻。從市場上反饋的信息來看,選擇熱處理的鎳磷鍍層的潛力很大。
提高鎳磷鍍層硬度的熱處理工藝;熱處理溫度400℃,處理時間1h;為防止工件表面產生有色的氧化物,熱處理工序要在惰性和還原性氣氛或真空環境下進行。
一般電鍍企業,受生產條件和技術限制,不能滿足用戶的要求,均放棄了加工厚的鎳磷鍍層和需要熱處理的加工業務,使化學鍍鎳技術的推廣和發展受到一定的影響和制約。
提高硬度和耐磨性的熱處理采用鑄鐵粉末,放入專用鐵盒里,將鍍件完全保護好的辦法,可替代需用保護氣體或使用真空爐的要求。按以上熱處理工藝升溫到400℃,處理1h后,再緩慢隨爐溫自然冷卻到室溫,取出工件、清理,鍍層外觀光澤一致、無變色。多年來,熱處理的產品,經石油機械廠的檢測中心和機械工業表面覆蓋層產品質量監督檢測中心,采用M型顯微硬度計和MVD一1000JMT2型微氏硬度計,檢測的結果,鍍層硬度未經熱處理時為(500~600)HV0.918,經熱處理后達到(921~1017)HV0.918。
結論
對石油機械產品中鎳磷鍍層的特殊要求,在生產實踐中,探索新的途徑,確定最佳工藝條件,全面滿足用戶需求。
在鎳磷鍍層0.07~0.09mm施鍍中,優化鍍液配制,加強前處理,做好中心孔和非鍍面的保護,提高硬度的熱處理辦法和第二次磨削需正確操作等工藝控制要素。
化學鍍鎳磷合金的溶液十分敏感,因其濃度、溫度、pH值控制范圍較窄,使用和生產中要特別關注每一個環節的變化,操作中要加強控制、跟蹤分析、嚴格執行工藝。同時,隨著工藝的廣泛應用,在工業化實踐中要進步的創新、發展和提高。
免責聲明:本網站所轉載的文字、圖片與視頻資料版權歸原創作者所有,如果涉及侵權,請第一時間聯系本網刪除。
-
標簽: 化學鍍鎳石油機械
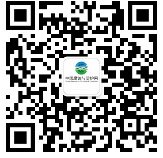
官方微信
《腐蝕與防護網電子期刊》征訂啟事
- 投稿聯系:編輯部
- 電話:010-62316606-806
- 郵箱:fsfhzy666@163.com
- 腐蝕與防護網官方QQ群:140808414