設備制造質量的優劣及設備制造工藝是否優化,都涉及到設備的使用壽命問題。本文就石化核電等靜設備中空冷器、換熱器和壓力容器在制造和使用中突出的非正常腐蝕失效的案例進行了簡要概述。
文| 束潤濤 武漢市潤之達石化設備有限公司
據中國青年網財經報道,某企業PX 項目爆炸起火,起因源于管理不善等諸多人禍因素。目前,部分石化企業為節約成本,采取最低價格中標的方式給石化裝置的正常運行帶來了很大的安全隱患。由偷工減料所涉及到的質量問題五花八門, 如新疆某石化企業采購的DN2000 不銹鋼固定管板式換熱器,使用周期僅3 個多月,經拆卸后發現管束殼程的8 塊不銹鋼支撐板全部沒裝;四川某企業采購的08Cr2AlMo 石油液化氣空冷器使用僅2 個多月就發生嚴重泄漏,給安全生產帶來巨大隱患。石化、核電等行業對于設備使用前的檢驗驗收都有嚴格的規范和要求,但由于部分石化企業管理不善,或簡單強調節約采購成本,而忽略了對產品質量的嚴格要求,特別是一些財團或地方企業跨界投資的新上化工項目,這種情況尤為突出。同時,我國石化裝備制造業近幾年發展迅猛,許多石化設備企業或故意以劣充優, 或技術水平低下,造成了很多設備非正常失效的案例,給石化企業的正常生產帶來極大困擾和巨大的安全隱患。以下是幾起與制造質量和制造工藝相關的非正常腐蝕失效的典型案例,以及一些與制造和材料相關的其它問題整理出來與大家一起學習和探討。
空冷器管束非正常腐蝕失效的典型案例
空冷器粗制濫造的典型案例
本案例為表面蒸發式空冷器上段的翅片管管束,管內為液化石油氣,介質中含硫化氫和氫氣,在氣體冷卻過程中經過露點溫度,設備處于濕硫化氫腐蝕環境,選用的翅片管基材為耐硫化氫腐蝕的08Cr2AlMo,管箱為Q245R,接管、法蘭為20#。該設備使用僅2 個月就陸續發現6 支翅片管的端部泄漏,由于介質易燃易爆,被迫停止使用(見圖1), 并重新采購。

圖1 空冷器管箱內部偷工減料焊接結構圖例
圖1 為空冷器管箱內部結構,圖示標注1 為插管與管箱側板的內部焊接接口, 未焊接;標注2 為翅片管管頭與管板焊接接口,未焊接;標注3 為管箱底板與管板連接處,未見封底焊縫;標注4 為底板與絲堵板連接處,未見封底焊縫。
該空冷器管箱焊縫外表比較美觀,但管箱內部所有焊縫都未按要求封底,目的是節省工時、節省焊接材料,并降低焊接能耗。
在該產品制造企業提供的竣工資料中, 未見任何焊接工藝和熱處理資料,其加工制造成本不及合格產品的一半,屬于典型的粗制濫造產品。
不合理的制造工藝給高壓空冷器帶來非正常腐蝕失效的案例
中石化某石化分公司加氫裝置4 臺高壓碳鋼空冷器使用僅幾天就有3 臺泄漏, 由于使用部位存在易燃易爆的安全隱患, 該部位的4 臺高壓空冷器被迫廢棄后重新采購,其停工損失高達2000 多萬元。
經追蹤分析,制造廠在高壓空冷器組裝工藝的前后順序方面存在有很大偏差。目前國內外許多高壓空冷器的圖紙要求大多都是先做管箱,后進行管頭焊的焊接, 其目的是保證高壓空冷器管箱的絕對安全。先焊管箱后焊管頭焊的工藝順序忽略了采用管箱深孔焊焊接的管頭焊縫拉脫力很差的事實,而且不能對管頭焊進行PT 檢查和煤油滲漏檢查,只能在水壓試驗或氣壓試驗時尋找泄漏點。發現缺陷后也不能進行挖補(挖除缺陷再補焊),解決方法也只能在有缺陷的部位進行重新堆焊。在缺陷沒有被徹底挖除的情況下,在焊縫表面加蓋焊縫是存在巨大安全隱患的。
相同的案例在國內已發生多起,國家某行業管理機構明確要求制造企業在空冷器的制造上按先管箱后管頭的工藝順序進行制造,目前大多數空冷器制造企業都遵守這一規定予以執行,這是導致問題頻發的原因之一。須知國內企業在深孔焊方面的焊接技術和檢驗方法都沒有成熟可靠的技術,制造及檢驗過程也沒有嚴格的控制措施。管頭焊接質量的絕對可靠是保證石化企業獲得生產穩定的保障,管箱的焊接質量是保證石化企業設備安全運行的前提, 二者不可孰輕孰重。其實,先焊接管板管頭, 后焊接管箱的制造方案早已獲得非常穩定的運行效果,對于管箱的焊接檢驗和焊后熱處理目前都有可靠的手段來予以保證, 管箱的各種焊縫質量都可以采用UT 檢驗的方式來進行檢驗,焊后熱處理可以采用爐外局部熱處理的方法完成。
以下是空冷器管頭焊縫的圖例說明:
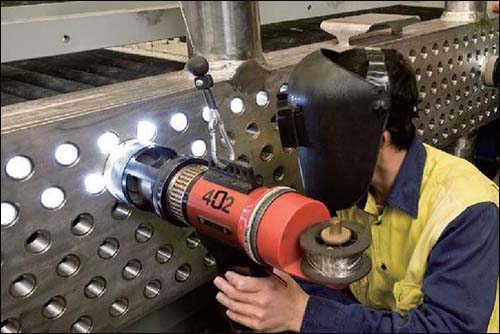
圖2 空冷器管頭深孔焊焊接圖例
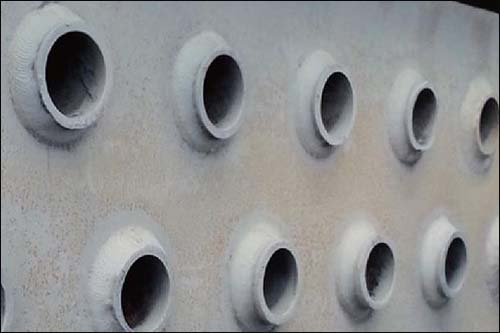
圖3 空冷器管子-管板焊接接頭PT檢驗圖例
圖2 是將管箱預制好以后再進行深孔焊接的制造工藝,圖3 是先焊接管板管頭, 進行PT 檢驗的圖示。圖2 的焊接方式等同于盲焊,焊后無法進行直接檢驗,焊接缺陷也無法挖補,而圖3 的焊接及焊后檢驗就不存在圖2 那樣的所有問題。
換熱器管束非正常腐蝕失效案例
不銹鋼U型管的腐蝕案例
本案例中U 型管不銹鋼換熱器管束的腐蝕問題來源于海川化工論壇,殼程介質中不含Cl-,含有溶劑乙酸乙酯和溶質有機物,管內通蒸汽加熱,使用周期大約一年。
從圖4 判斷,該換熱管的R 段有拼接痕跡(見圖4 中的藍色標記),GB151 僅允許在U 型管的直管段進行拼接,在R 段拼接屬于違規制造。小口經管對接焊縫的可靠性不高,應直接采購整支換熱管進行彎制。
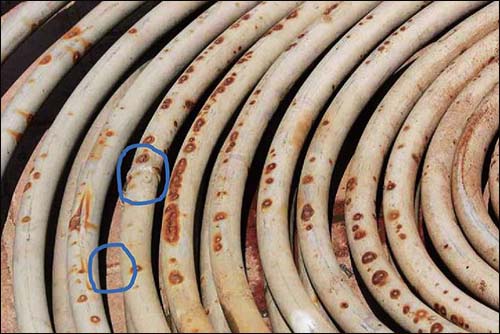
圖4 換熱器U型管R部位拼接圖例
U 型管在拼接后會產生焊接殘余應力,而彎制過程又將焊接殘余應力與彎曲形變應力疊加。材料在彎制時會延纖維方向拉伸,使管子靠R 外側的壁厚形成拉伸減薄,在管材進行彎制時就可能已經在焊縫處產生了微缺陷,這是使用壽命很短的主要原因。
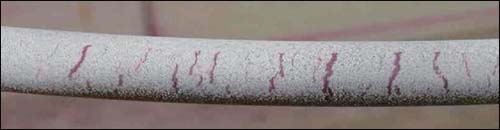
圖5 換熱器U型管腐蝕失效后的PT檢驗圖例
圖5 是另一臺U 型管加氫換熱器管束腐蝕失效后的PT 檢驗照片,從照片上可以看到很多橫向裂紋,是典型的應力腐蝕特征。
普通奧氏體不銹鋼材料中都含有少量鐵素體,部分條形鐵素體會在纖維拉伸的作用下斷裂,形成微小空洞。本人在其它科研項目中對304L 的焊接彎曲試樣進行微觀分析時發現,條形鐵素體斷裂的最大空洞尺寸約30μm。所以,對于U 型管應進行固溶熱處理以恢復材料的組織性能。很多制造企業由于條件有限而不做固溶熱處理,導致很多U 型管R 段在應力腐蝕介質的作用下腐蝕失效。U 型管冷彎后進行整體固溶熱處理處理或在R 段做局部固溶熱處理,按國內現有技術能力都是可以實現的,這樣既可以完全消除彎曲應力,又能將鐵素體重新固溶,起到修復微缺陷的作用。
管束管頭焊接質量問題
本案例為某地方煉油企業原料油- 減一線換熱器,換熱管材質08Cr2AlMo,管板16Mn 鍛,使用4 個月以后開始泄漏,后經過3 次堵管,使用11 個月后報廢(見圖6)。08Cr2AlMo 換熱器管束在該部位的正常使用壽命應該超過3 年。
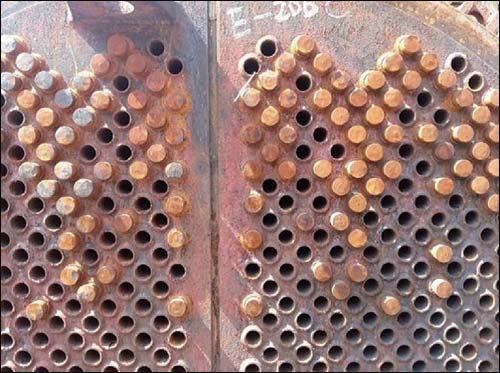
圖6 08Cr2AlMo換熱器管束非正常腐蝕圖例
該設備殼程介質原料油,溫度65~ 85 ℃,管程介質為減壓塔頂油氣,溫度130~100℃,管程為濕硫化氫腐蝕環境。殼程管外基本無腐蝕痕跡,管程換熱管、管板和焊縫金屬僅見輕微腐蝕痕跡,泄漏點均出現在管口焊縫的熔合區。經分析, 腐蝕原因如下:
(1) 材質不匹配:08Cr2AlMo, 管板16Mn 鍛,焊材H08CrMoA;
(2) 焊接質量很差:焊縫高度明顯不夠,不滿足圖紙和GB151 要求。
很多制造企業的焊接工程師不知道08Cr2AlMo 其實就是有淬硬傾向的Cr-Mo 鋼,這種淬硬傾向在北方的冬天尤為明顯, 必須按焊前預熱、焊后消氫和最終回火熱處理工藝來進行嚴格制造和過程控制。對于預熱、后熱和熱處理,很多企業把關不嚴,或不知道該怎么做,就干脆不做,這是該材質換熱器管束使用壽命很短的直接原因。
壓力容器非正常失效的案例
奧氏體不銹鋼容器非正常失效案例
奧氏體不銹鋼與碳鋼和低合金鋼相比,具有熱膨脹系數大,熱導率低的特點。由于冷卻速度慢,奧氏體不銹鋼設備在焊接時會導致焊縫收縮量大和焊接應力大, 在焊接過程中應嚴格控制線能量,并對設備本體進行有效防護。設備在焊接時若不對母材進行保護,而任由飛濺和焊瘤與母材熔為一體,這將使局部產生冷卻收縮應力,極易造成點腐蝕,以及由點腐蝕源所造成的應力腐蝕破壞。如某化工企業一臺316L 材質的環己烷污水分離器,使用1 年后就發生腐蝕泄漏,而原污水分離器在使用304L 的情況下正常運行時間都超過2 年。檢修時在罐內發現了大量焊瘤和飛濺痕跡, 在焊瘤和飛濺部位,均可用肉眼看到腐蝕坑點(見圖7)。在該設備物料介質中, 僅有極少量乙酸和氯離子,在入口處的氯離子含量僅2~5ppm,由于隨意起弧的焊瘤和飛濺給氯離子的聚集創造了條件,在污泥沉積后便形成由點腐蝕源構成的應力腐蝕破壞。
該設備僅在焊縫粗制濫造部位出現腐蝕泄漏,其余部位均未發現任何腐蝕痕跡, 如果能嚴格按工藝要求控制焊接過程,該設備在氯離子含量很低的情況下,其使用壽命將大大延長。圖7 是該設備隨意起弧以及焊瘤腐蝕后的凹坑痕跡。
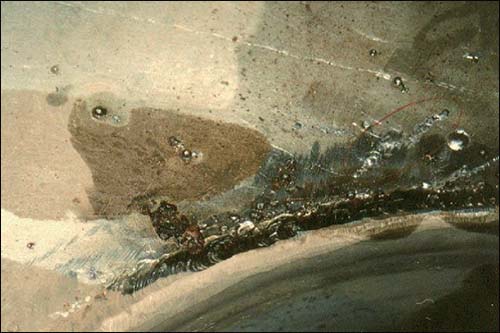
圖7 環己烷污水分離器脫水包與筒體焊縫野蠻焊接痕跡
低合金碳鋼容器內壁的非正常裂紋
本案例為某核電廠還沒有投入使用的除氧器,按ASME Ⅷ-1 卷進行制造,材質為SA516-G70,化學成分和機械性能相當于Q345R,厚度38mm。設備到現場后經檢驗發現容器內壁有一處裂紋,見圖8。
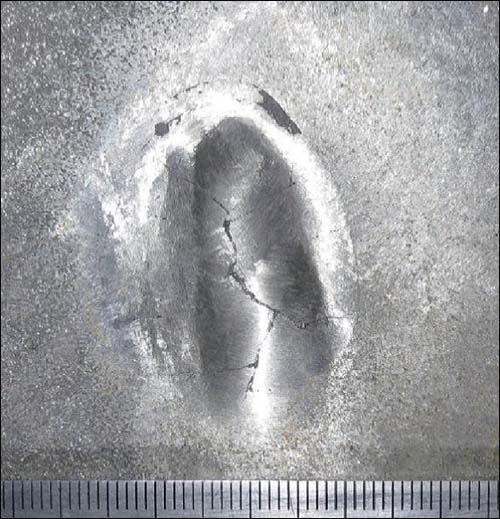
圖8 核電站除氧器筒體內部缺陷
經UT 檢測, 發現缺陷深度最大約11mm。該缺陷發現后現場檢驗人員認為是母材質量問題,但裂紋周邊橢圓形痕跡與母材明顯不同,橢圓長寬尺寸大約35×20mm,經判斷裂紋周邊橢圓形痕跡內的金屬為焊縫。該問題產生的原因無資料可追蹤,分析為鉚工在裝配時損傷了母材, 害怕被追責,而沒有按質保程序進行處理, 在沒有焊接工藝指導的情況下進行了私自補焊。缺陷挖補的焊接難度遠遠大于一般普通正常焊縫的焊接技能,沒有壓力容器焊接證書的鉚工是不可能完美完成焊接修補的。從宏觀可以判斷,該缺陷是由夾渣引起的裂紋。說到底,是鉚工想蒙混過關。對于核電設備的制造,比一般石化壓力容器的過程控制應更為嚴格,說明該設備制造企業的質保培訓被走了過場,鉚工質量意識薄弱。
本文之所以把這個案例拿出來與大家分享,是因為核電設備在使用前的檢驗非常嚴格,從而可以避免在使用過程中發生非正常失效。石化企業的設備驗收一般以水壓試驗和質量證明文件為依據,基本沒有對罐體內壁進行檢驗。該案例中出現的質量問題在石化企業大量存在,只有加強使用前的嚴格檢驗才有可能將非正常失效的安全危害降到最低。
其它與腐蝕相關的制造問題探討
關于換熱器管束的脹接問題
換熱器管束的腐蝕泄漏不僅僅發生在管頭焊縫,許多脹接過的換熱管也有腐蝕泄漏的情況。普通奧氏體不銹鋼、雙相不銹鋼, 以及15CrMo、12CrMo 的換熱管都有許多在脹接部位存在非正常腐蝕泄漏的案例,如大連石化在2000 年投入幾臺SAF2205 的雙相不銹鋼管束使用不到3 個月就發生多支換熱管穿孔,其穿孔部位均位于離管口15~20mm 處。還有許多企業也都有過奧氏體不銹鋼換熱管在脹接部位發生腐蝕泄漏的事故(見圖9)。由于泄漏點發生在離管頭焊縫較近的管子母材上, 責任的劃定往往由制造企業和管材生產企業擔責,很多制造企業都被當成了冤大頭。
德國巴斯夫公司在WN75-100 的企業標準中規定,當管子內外有腐蝕及應力腐蝕介質時,不推薦采用機械或其它方式脹管。北京鋼鐵研究總院的陸世英教授曾經做過試驗,發現321 不銹鋼材料的換熱管貼脹以后脹接變形臺階處的殘余應力超過100MPa。奧氏體不銹鋼在冷作變形過程中屈服強度會迅速上升,冷作硬化極其明顯, 是構成應力腐蝕的直接原因。雙相不銹鋼中的奧氏體只有50% 左右,在冷變形中不穩定的奧氏體會轉變為馬氏體,是造成脹接部位腐蝕穿孔的主要原因。鉻鉬鋼塑性較低,淬硬傾向明顯,脹接后在臺階處的附加應力很大,將會使脹接部位變脆。
奧氏體不銹鋼在脹接部位的腐蝕特征為微裂紋,雙相不銹鋼在脹接部位的腐蝕特征則主要為腐蝕穿孔,裂紋較少,而鉻鉬鋼在脹接部位的腐蝕特征主要為穿孔。因此,本人建議在所有存在氯離子及其它鹵素介質的應力腐蝕環境中,奧氏體不銹鋼、雙相不銹鋼和鉻鉬鋼換熱管都不進行任何形式的脹接,應以強度焊為主。
以下圖例中,圖9 是304 不銹鋼管束試壓時管內噴霧的圖片,圖10 是15CrMo 合金鋼管束試壓時管內噴水的圖片。
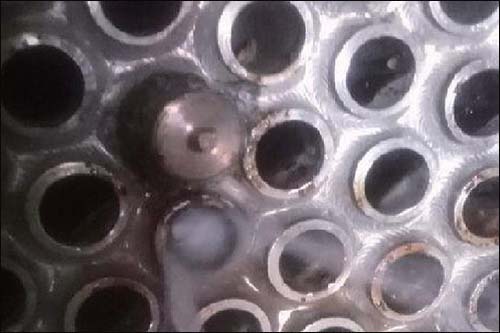
圖9 304不銹鋼管束脹接部位泄漏圖例
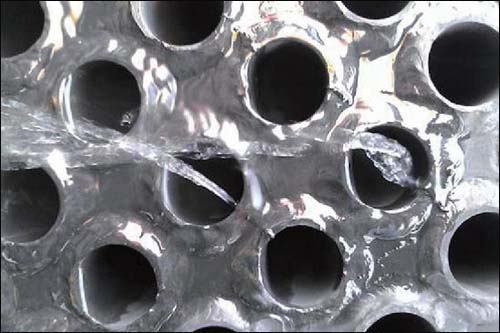
圖10 15CrMo管束脹接部位泄漏圖例
從圖9 和圖10 的試壓照片可以看出, 304 不銹鋼的水霧和15CrMo 的水柱都是從離管端很近的管內噴出來的,都是材料脹接以后的不適應性影響。脹接的目的是防止殼程管板管孔與管子外壁發生縫隙腐蝕, 但忽略了不同材質的換熱管在形變應力條件下的不適應性,這種不適應性將使管束使用壽命大大縮短。當縫隙腐蝕與脹接的不適應性發生沖突時,應以兩權相害取其輕來考慮。
奧氏體不銹鋼管件、膨脹節和封頭的非正常腐蝕失效
奧氏體不銹鋼管件和膨脹節在實際使用過程中出現大量腐蝕失效的案例。與前述U 型管冷作變形的原理一樣,管件和膨脹節在制造過程中的變形量都很大,只有固溶處理才能徹底消除形變應力和微觀缺陷,但大多數管件制造企業以高溫拔制或高溫推制代替了固溶熱處理。在國家相關標準中, 奧氏體不銹鋼膨脹節和封頭都沒有固溶熱處理的強制要求,所有制造企業在部件制造完成后都不做固溶熱處理,這是造成應力腐蝕的主要癥結所在。如果使用單位的工況介質中有硫化氫和氯離子等腐蝕介質, 建議在采購技術條件中對不銹鋼管件、膨脹節和封頭提出固溶熱處理的強制要求。
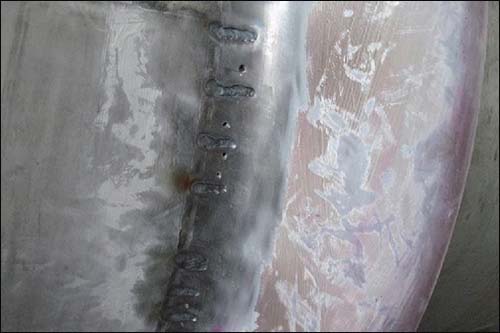
圖11 大型筒體膨脹節翻邊邊緣出現應力裂紋以后的補焊圖片
圖11 是膨脹節出現應力裂紋后補焊的圖片,裂紋出現在膨脹節翻遍的焊縫附近, 為形變應力與焊接應力疊加后出現的應力腐蝕失效。圖中圓孔是維修焊接前為阻止裂紋延伸的人工孔。
以上案例和探討的內容是國內空冷器、換熱器、壓力容器等靜設備在制造和使用管理上的一些共性問題,希望引起制造企業、使用單位以及行業管理部門的高度重視。國內壓力容器制造企業幾千家,絕大多數是中小企業,在此也衷心希望國內中小型壓力容器制造企業能夠真正從技術管理水平和質量檔次上強大起來。
免責聲明:本網站所轉載的文字、圖片與視頻資料版權歸原創作者所有,如果涉及侵權,請第一時間聯系本網刪除。
-
標簽: 石化核
相關文章
無相關信息
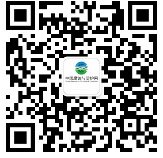
官方微信
《腐蝕與防護網電子期刊》征訂啟事
- 投稿聯系:編輯部
- 電話:010-62316606-806
- 郵箱:fsfhzy666@163.com
- 腐蝕與防護網官方QQ群:140808414
點擊排行
PPT新聞
“海洋金屬”——鈦合金在艦船的
點擊數:8135
腐蝕與“海上絲綢之路”
點擊數:6475