前言
不論是架空管線還是埋地管線,高質量的內外防腐對于延長管線使用壽命,實現安全運行都是至關重要的。隨著 3PE 技術的普遍應用,在外防腐方面我國有了較為完整的體系,包括采用 3PE、環氧粉末涂料、液體涂料(環氧涂料、聚氨酯涂料)及包覆類材料等技術。這些原材料的生產技術、防腐工藝、執行的標準都與國外先進技術相差無幾。
而在內防腐方面存在問題就比較復雜,一是介質的復雜性,管線輸送介質包括原油、水、含油污水、采出液等,有些介質的腐蝕性遠遠超出土壤和大氣的腐蝕性,二是焊接熱影響區的影響,由于內補口技術的滯后,焊接熱影響區的存在限制了有機涂層的使用,即使管體防腐層性能再好,補口解決不好也不能從根本上解決問題。三是成本的影響,由于成本控制使得一些耐蝕管材、雙金屬管的使用受到了限制,四是維護方便性的要求,非金屬管材在耐蝕方面有著較大的優勢,但在耐壓及使用維護方面又存在一些問題。
因此可以認為,不論是埋地管線還是地上管線(尤其是小口徑管線),內防腐的質量直接影響了管線的使用壽命及安全運行。以西北某油田一個采油廠為例,該采油廠有各類管道 5576 條,總長 6877.8km,2015 年對 3340 條管線進行摸排,共查出隱患 859 條,其中腐蝕穿孔 724 條,占總隱患數的 84.5%。輸送介質的強腐蝕性和內防腐措施薄弱是引起管道腐蝕的主要原因。
而在解決內防腐方面內補口又成為了制約因素,其中小口徑管線(DN200 以下)的內補口尤其是難點。本文主要討論用于埋地小口徑管線的內外防腐技術。
內補口技術的探索
防腐業界對管線內補口尤其是小口徑管線內補口近年來做了不懈的努力和探索,也包括引進消化了一些國外技術。國內曾經應用的技術如UB滑套、 補口車、焊接不銹鋼短節、在線擠涂等,這些技術都有一定的防護效果,但還是存在著成本高、受管徑限制、質量不易控制等不足,在一定程度上限制了推廣使用。
為了解決這一難題,在大量調研的基礎上,我們提出了小口徑管線內外一體化工廠預制防腐蝕的理念并進行了深入研究。 經過幾年的努力, 研究出了 “堆焊固溶端頭處理 + 內外有機防腐層”的小口徑管線內外一體化(簡稱 DGR)防腐蝕技術。利用 DGR 技術生產的防腐管可以現場直接焊接安裝,免除了內補口工序且能實現管內防腐層連續完好,能夠較好地解決小口徑管線的防腐難題。
圖1 內補口車
2道O型密封圈內襯套(左) 4道O型密封圈內襯套(右)
圖2 O型密封圈內襯套
DGR 內外一體化防腐技術
1、組成、特點及流程
⑴組成
DGR 內外防腐包括三部分:①管端內表面的耐蝕合金堆焊固溶層;②管體內表面的耐蝕環氧粉末防腐層;③管體外表面的環氧粉末或 3PE 防腐層。
⑵特點
DGR 內外防腐技術具有以下特點:
①單根鋼管內外涂(覆)層和端頭內堆焊均在工廠預制完成,質量可檢、可控,②管端堆焊層與管體內表面實現平滑過渡,③鋼管內壁除熱影響區外,管體及管體與堆焊層的過渡區環氧粉末一次成型(焊接熱影響區由耐蝕合金起到防腐作用),④可以根據輸送介質選擇不銹鋼焊材,⑤現場焊接完成后只需要做外補口,不需要內補口。
⑶流程
DGR 內外防腐技術的流程為:端頭內表面預處理→端頭堆焊固溶處理→內壁噴砂處理→內壁噴涂環氧粉末→外壁拋丸處理→外壁涂敷環氧粉末 ( 或3PE) →端頭外處理→質檢。
2、端頭處理
按照端頭熱影響區的尺寸,首先對端頭內表面進行預處理,之后進行堆焊固溶處理,其流程為:(1) 對管端內表面進行輕噴砂處理,(2) 預熱,(3) 選用適當的耐蝕合金做堆焊層,(4) 對堆焊層兩端進行固溶處理,(5) 對預補口內孔機械加工。
耐蝕合金可根據輸送介質的成分和腐蝕性,選擇鎳基合金、雙相不銹鋼和奧氏體不銹鋼等耐蝕合金材料。
由于采用了變電流堆焊工藝,并采用 TIG 焊接專用機,保證了堆焊層的平整度。堆焊層厚度 1.5 ~ 2.0mm,堆焊層長度可按經驗或實際測量確定,一般不小于 50mm。
通過對預補口內孔的車削加工,可實現不同鋼管管端內徑的一致,保證了管道內組對精度,從而保證了內焊道質量。
圖 3 小口徑鋼管DGR內外防腐示意圖
1-環氧粉末涂層;2-搭接覆蓋區;3-堆焊預補口區;4-鋼管母材
圖4 小口徑鋼管內壁“堆焊+涂層”防腐示意圖
3、內防腐粉末涂敷
內防腐粉末的性能首先要滿足 SY/T0442-2010《鋼質管道熔結環氧粉末內防腐層技術標準》的要求,在此基礎上,如果介質有特殊性就應該增加相應性能指標。如對于單井管線和污水管線,如果H 2 S、CO 2 含量較高或溫度較高,在選擇粉末涂料時就要相應增加耐 H 2 S、CO 2 或者耐溫試驗,以確保滿足使用要求。標準中關于涂層厚度分為了普通級和加強級,普通級≥ 300μm,加強級≥ 500μm。除消防管線外,只要是腐蝕較嚴重的介質建議采用加強級,適當增加涂層厚度對于提高防腐質量是很有好處的,內防腐環氧粉末涂料及涂層性能指標要求詳見表 1。
為了確保環氧粉末固化完全,本工藝采用固化爐進行后固化,固化時間為30min,固化溫度為 200℃~ 230℃。
內環氧粉末涂敷流程為:
噴砂處理 (Sa2.5級) →吹掃除塵 (2級)→中頻加熱→粉末噴涂→后固化→質檢
噴砂處理:除銹等級 Sa2.5 級,粗糙度 50 ~ 100μm
中 頻 加 熱: 鋼 管 加 熱 溫 度200 ~ 260℃
粉末噴涂:正壓噴粉
固化溫度:200 ~ 230℃
質檢:外觀、厚度、漏點等
4、外防腐技術
外防腐材料可選擇的余地較大,3PE、環氧粉末涂料、液體涂料(環氧涂料、聚氨酯涂料)及纏帶包覆類材料都可用于外防腐,選擇時可考慮以下因素:(1)土壤的腐蝕性(2)安裝過程機械損傷的可能性,(3)外補口的可靠性,(4)經濟性。
比較干燥且土壤條件較好,安裝回填不會造成機械損傷的建議采用環氧粉末涂料,土壤條件較差不能保證細土回填的建議采用 3PE 等。DGR 內外防腐技術由于是工廠預制,且針對的是小口徑管線, 僅采用環氧粉末或3PE兩種方式,液體涂料及纏帶包覆類材料不在本文討論范圍之內。
采用環氧粉末時,其流程為:
拋丸處理→中頻預熱→靜電噴涂→固化→水冷→檢驗。
拋丸處理:Sa2.5 級
錨紋深度:40 ~ 100μm
中頻加熱:180 ~ 230C
質量控制依據:SY/T0315-2013 《鋼質管道熔結環氧粉末外涂層技術規范》 ,詳見表 2。
表2 外防腐環氧粉末涂料及涂層性能指標
采用 3PE 時,其流程為:
拋丸處理→中頻預熱→靜電噴涂→固化→涂膠→包覆 PE →水冷→防腐層端頭處理→檢測。
質量控制依據 GB/T 23257-2009《埋地鋼質管道聚乙烯防腐層》,詳見表 3。
表3 3PE外防腐層的性能指標
焊接工藝評定
由于 DGR 管道端頭的特殊結構,為保證焊接質量,需要采取特殊的焊接方式,即:采用免充氬藥皮耐蝕合金焊絲TIG打底焊接, 然后采用手工電弧焊工藝填充蓋面。由于采用了耐蝕合金,使焊縫區域與堆焊層、內防腐層形成連續的防腐層,因此無需進行內補口防腐作業,施工簡單快速。
1-不銹鋼焊口;2-不銹鋼預補口區;3-固溶區;4-內熔結環氧防腐涂層;5-外熔結環氧防腐層;6-鋼管。
圖5 DGR一體化防腐鋼管示意圖
為驗證焊縫的焊接質量,委托中油一建焊接培訓中心和中國石油集團工程技術研究院焊接實驗室對 DGR 焊縫進行了焊評測試,測試標準采用石油行標 SY/T0452-2012《石油天然氣金屬管道焊接工藝評定》。具體的焊接工藝參數如下:
鋼管管徑:φ60
鋼管厚度:5.5mm
鋼管材質:20# 鋼
打底焊焊材:ER2209 2.4mm
填充及蓋面焊材:E309L-16 2.0mm
焊接方法:SMAW
焊接電流:70~90A
評定主要技術指標及測試結果見表 4。
從上表可以看出, 采用上述方式焊接的DGR管道端口焊接質量完全滿足標準要求。
圖6 焊評試驗照片
室內耐蝕性能評價
為測試 DGR 管道內防腐層的實際防腐性能,開展了室內耐蝕性性能評價,包括管道端口的堆焊層和管體的環氧粉末防腐層。
1、堆焊層耐蝕性評價
試 驗 采 用 SY/T0029-2012《 埋 地鋼質檢查片應用技術規范》中的失重法測試堆焊層的平均腐蝕速率,即把帶堆焊層的試片用環氧涂層封底封邊后,分別放置在常溫常壓下的兩種化學介質溶液(3% NaCl 溶液和 10% NaOH溶液)中,浸泡時間為 32d。試驗堆焊 材 質 為 不 銹 鋼 2209, 試 件 尺 寸 為50mm×80mm×25mm,具體尺寸如圖 7所示。
圖7 堆焊試件實物圖及試驗暴露面積示意圖
試驗結束后觀察發現,堆焊層表面光滑平整,沒有發現蝕坑,在兩種介質溶液中浸泡后的失重重量及腐蝕速率計算結果見表 5。
表5 堆焊層在不同介質中腐蝕速率測試結果
從表 5 中可以分析得出,耐蝕合金堆焊層耐 10%NaOH 溶液介質、3%NaCl 溶液腐蝕性能較好,浸泡 32d 后,腐蝕速率< 0.01mm/a。
2、環氧粉末內防腐層耐蝕性評價
作為保護管道內壁的主要防腐體系,環氧粉末內防腐層的耐蝕性能也是非常重要的,除按照標準 SY/T0442-2010《鋼質管道熔結環氧粉末內防腐層技術標準》要求的規定進行常規檢測外,還特別進行了防腐層在碳鋼及耐蝕合金基材的拉拔附著力和高溫高壓加速耐蝕性試驗,拉拔附著力的測試方法為 GB/T 5210,具體測試結果見表 6。
表6 環氧粉末內防腐層耐蝕性測試結果
從表 6 中可以看出,環氧粉末內防腐層與碳鋼及耐蝕合金基材均有良好的粘結性,在鹽霧試驗后附著力也沒有明顯下降,在加速耐蝕性試驗后,防腐層在耐蝕合金基材和碳鋼基材上均具有良好的防腐性能。
從上述試驗結果可以得知,內防腐體系中的耐蝕合金堆焊層和環氧粉末內防腐層均具有良好的防腐性能,且兩者之間的配套性良好。
現場試驗
DGR 防腐管于 2016 年 7 月和 2016 年 11 月,分別在長慶油田采油三廠五里灣第一采油作業區的柳 101-252 井組、柳 91-39 井組進行了現場試驗,輸送壓力0.3 ~ 0.5MPa,輸送溫度為 20~35℃。
1、柳 101-252 井組試驗管段
DGR 試驗管道尺寸為 φ60×4mm,共 3 根,試驗管段長度分別為 1.5m、4m、1.5m。將上述三根 DGR 防腐試驗管段對接焊連成一整根試驗管,對接焊后試驗管段總長度為 7m,其中試驗管包含 2 道焊口(焊口距離管端各 1.5m 處),將長度為7m 的 DGR 防腐試驗管接入柳 101-252 井組原油管線。
內防腐層:熔結環氧粉末防腐層,厚度 500 ~ 600μm。
外防腐層:熔結環氧粉末防腐層,厚度 300 ~ 400μm。
內補口:耐蝕合金堆焊層,厚度1.5mm,長度 65mm。
外補口 : 礦脂油防腐帶+外護帶結構。
圖8 現場試驗照片
2、柳91-39井組試驗管段
試驗管道尺寸為 φ60×4mm,每根試驗管段長度為 1m,一共 20 根。
污水管線:20 根總長度為 20m,分別接入和原油管線各 10m,即每種管線各有焊口 11 處。
內防腐層:熔結環氧粉末防腐層,厚度 500 ~ 600μm。
外防腐層:熔結環氧粉末防腐層,厚度 300 ~ 400μm。
內補口:耐蝕合金堆焊層,厚度1.5mm,長度 65mm。
外補口:礦脂油防腐帶 + 外護帶結構。
圖9 現場試驗照片
柳 91-39 井組水樣主要化學成分:
總礦化度:29269mg/L
pH 值:7.62
HCO3- 含量:396mg/L
Cl- 含量:12053mg/L
SO42- 含量:6243mg/L
目前試驗正在進行中,試驗管段運行正常,未出現腐蝕穿孔滲漏現象。
結論
利用 DGR 技術生產防腐管可以實現工廠化預制,質量可檢可控,現場直接焊接安裝,免除了內補口工序且能實現管內防腐層連續完好,也可以根據介質變化選取不同的耐蝕合金和防腐涂料,能夠較好地解決小口徑管線的防腐難題。
(本項目的研究與現場試驗得到了李廣華、魏國兩位同志的指導與幫助,也得到了山東勝利長龍管道科技有限公司的支持,在此一并致謝)
參考文獻
1、SY/T0029-2012《埋地鋼質檢查片應用技術規范》
2、SY/T0452-2012《石油天然氣金屬管道焊接工藝評定》
3、SY/T0442-2010《鋼質管道熔結環氧粉末內防腐層技術標準》
4、SY/ T0315-2013《鋼質管道熔結環氧粉末外涂層技術規范》
作者簡介
韓文禮,生于 1961 年。1982 年畢業于北京鋼鐵學院,現任中國石油集團工程技術研究院院長助理,防腐保溫研究所所長,教授級高工,中國石油集團高級技術專家。主要從事石油行業儲罐、管線防腐蝕技術研究開發與應用。
工作三十多年來,先后主持和組織完成了國家、中石油集團公司 20 余項重點課題的研究工作,多項技術成果填補國內和集團公司空白。近年來獲得省部級科技進步三等獎以上 5 項、中國腐蝕與防護學會科技進步一等獎 1 項、二等獎 2 項、局級科技進步創新獎 5 項。獲得授權發明專利 6 項。主編 SY/T 0320-2010鋼質儲罐外防腐層技術標準等行業標準 3 項,中石油集團企標 1 項。發表論文多篇。
2015 年被中國工程院環境與輕紡工程學部聘為“我國腐蝕狀況及控制戰略研究”項目組專家。中國腐蝕與防護學會第九屆理事會理事、 中國腐蝕與防護學會防腐蝕施工與技術專業委員會第五屆副主任委員、 《石油石化管線與技術》雜志編委、天津市防腐應用技術協會理事、 《石油工程建設》雜志編委、 《管線與技術》雜志編委副主任。
免責聲明:本網站所轉載的文字、圖片與視頻資料版權歸原創作者所有,如果涉及侵權,請第一時間聯系本網刪除。
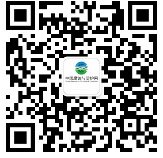
官方微信
《腐蝕與防護網電子期刊》征訂啟事
- 投稿聯系:編輯部
- 電話:010-62316606-806
- 郵箱:fsfhzy666@163.com
- 腐蝕與防護網官方QQ群:140808414