鎂合金是目前已知最輕的金屬結構材料,具有比強度和比剛度高、切削性優良等特點 。近年來,鎂合金引起了世界各國的廣泛關注,都將其作為最有潛力的輕質材料進行重點研究,并開發了一系列技術推動鎂合金在交通工具、航空航天和國防軍工等領域的應用 。隨著我國鎂合金研究的不斷深入,在鎂合金合金化設計、塑性變形等技術研究方面取得了長足的進步,開發了一系列高強、導熱、耐熱等鎂合金,在航空航天、國防軍工領域高強鎂合金已部分替代了中強鋁合金 。雖然鎂合金有著廣闊的應用前景,但鎂在金屬結構材料中具有最低的標準電極電位,而且其氧化膜疏松多孔,氧化膜的 PBR 比為 0.81, 不能形成有效的穩定保護膜,在大多數腐蝕性環境下容易出現電偶腐蝕、環境腐蝕等腐蝕問題,不能持續使用,限制了鎂合金的廣泛應用。因此,如何提高鎂合金的耐蝕性已成為鎂合金廣泛應用必須解決的瓶頸問題。
1、鎂合金主要腐蝕類型
全面腐蝕
鎂合金的全面腐蝕反應,通常與水發生電化學反應而導致鎂的溶解,同時形成了六方結構的氫氧化物膜,并產生氫氣,鎂離子和氫氧根離子在晶體結構中呈交替排列,造成膜的基底層易開裂,因此,膜層對基體沒有保護作用。鎂合金全面腐蝕產物隨著腐蝕環境與鎂合金化學成分的不同而發生變化。
局部腐蝕
局部腐蝕的形式主要有絲狀腐蝕、縫隙腐蝕和點蝕。氧濃度差電池驅動是絲狀腐蝕的主要因素,其頭部和尾部的電勢差在 0.1 ~ 0.2V 之間。對 AZ91 鎂合金的研究表明,點蝕和絲狀腐蝕是其早期腐蝕的主要特征,而且最初的點蝕會導致絲狀腐蝕。鎂合金的點蝕主要在表面的活性點上發生,而且電蝕一旦發生,會有向合金內部發展的趨勢。鎂合金的點蝕在含氯離子的溶液中表現最明顯,主要是因為氯離子的半徑較小,滲透性較強,可以透過表面的鈍化膜,且吸附到鈍化膜上的氯離子與鎂離子結合生成可溶性的氯化鎂,破壞了鈍化膜的結構,鈍化膜破壞處的地方與未破壞的地方形成鈍化鄄活化電池,因而加速了鎂合金的電偶腐蝕。
電偶腐蝕
鎂具有較低的電極電位,當與陰極接觸時極易發生電偶腐蝕,通常情況下,陰極是與鎂合金接觸的其他金屬材料,或者鎂合金內部的第二相和雜質元素,分別稱為外部電偶腐蝕和內部電偶腐蝕(圖 1)。Fe、Ni、Cu 等元素具有低氫過電位,通常充當高效陰極,在鎂合金中會導致嚴重的電偶腐蝕,而 Al、Zn、Cd 等金屬具有較高的氫過電位,對鎂合金的耐腐蝕性沒有多大的損害作用。高導電的電解液、高的點位差、陰極與陽極低的極化率、大的陰陽極面積比都會增加電偶腐蝕速率。
應力腐蝕
在含鉻酸鹽、硫酸鹽等腐蝕環境中,鎂合金同時受到內部與外部的應力作用時,鑄造鎂合金,特別是 Mg-Al 系鑄造鎂合金,在低于屈服強度的應力作用下表現出極強的應力腐蝕敏感性,而且應力腐蝕的存在又會大幅降低構件的服役性能。采用合理的零件形狀,利用熱處理減輕殘余應力,創建具有壓應力作用的表面層等都是防止應力腐蝕的有效途徑。
圖1 電偶腐蝕示意圖
2、影響鎂合金耐蝕性的因素
影響鎂合金耐蝕性的主要因素有合金成分、顯微組織、腐蝕介質。通過測試不同含量 Fe、Ni、Cu 等雜質元素的鎂合金的腐蝕速率表明,隨著雜質元素含量的增加,鎂合金的腐蝕速率急劇下降,如圖 2 所示。這些雜質元素在鎂中具有低的固溶度,常常形成金屬間化合物,并與鎂合金基體構成原電池,加速鎂合金的腐蝕。元素 Mn 在鎂中的固溶度較低,但其可以去除 Fe 或其他重金屬元素,從而避免生成有害的金屬間化合物,對于提高腐蝕性能具有積極作用。隨著 Ag、Ca 含量的增加,鎂合金的耐蝕性能逐漸降低,但其他合金元素對鎂耐蝕性的影響不明顯。
圖2 電偶腐蝕示意圖
顯微組織對鎂合金腐蝕行為有很大影響,如快速凝固的鎂合金,由于凝固速度較快,在基體中的合金元素分布相對均勻,提高了耐蝕性能。不同熱處理工藝下的晶粒尺寸差異也會對腐蝕速率產生影響,對不同晶粒尺寸 AZ91 合金的研究表明,合金的腐蝕速率隨晶粒尺寸的減小而減小。
鎂合金在不同的腐蝕介質中表現出不同的腐蝕特征,在干燥的環境中,表面易生成灰色的保護膜而不易腐蝕;而鹽,尤其是氯化物,可污染并破壞表面膜,造成嚴重的局部侵蝕;在農村及工業大氣中發生中等侵蝕,而在大多有機介質中則不受腐蝕。不同介質中的具體腐蝕情況見表 1 所示。
基于上述對影響鎂合金腐蝕行為三大因素的分析,可以從以下兩個方面對提高鎂合金防腐性能進行研究:一是改善鎂合金的本征耐蝕性,即通過優化合金成分、改善鎂合金的微觀組織等方式提高基體材料的耐蝕性;二是采用表面防護處理技術,通過表面防護層對基體進行保護,隔離腐蝕介質與基體的接觸,從而提高鎂合金的耐蝕性能,這是目前鎂合金耐蝕防護最常用的技術。
3、鎂合金防護技術研究現狀
提高鎂合金本征耐蝕性研究現狀
對于干燥無鹽分的服役環境,采用提高鎂合金的本征耐蝕性的方法就可滿足使用要求,而這方面的研究主要包括兩個方面,一是凈化合金成分或開發新型耐蝕鎂合金,二是改善鎂合金的表層微觀組織。
凈化合金成分或開發耐蝕新合金
目前,開發高純度鎂合金已成為歐美汽車工業增加鎂用量的主要途徑,主要采用純凈化處理工藝,降低有害雜質元素含量,使之控制在允許極限以下,例如據此開發的高純度 AZ91HP 鎂合金。
針對傳統鎂合金耐蝕性差的問題,開發新型耐蝕鎂合金也是另一重要途徑,如向鎂合金中添加稀土元素,可大幅提高鎂合金在含氯離子溶液中的耐蝕性能。
改善鎂合金的微觀組織
鎂合金微觀組織與耐蝕性關系的研究表明,單相、化學成分均一的鎂合金具有較好耐蝕性能,非晶態合金是其典型的代表。但常用的鎂合金都為晶態,存在組織和化學上的不均勻,這種不均勻會在不同相之間、晶界與基體之間發生電偶腐蝕,這是靜態鎂合金耐蝕性較差的主要原因。當鎂合金選定時,顯微組織主要受加工方式的影響,進而表現出不同的耐蝕性能,例如對于 AZ91D鎂合金來說,壓鑄工藝制備的合金晶粒比傳統鑄造合金的要細,茁相分布也更均勻,壓鑄合金的耐蝕性要優于傳統鑄造合金。相比于壓鑄合金,半固態工藝制備的琢鎂基體與茁相的面積比壓鑄合金中的要小,因而半固態工藝制備的合金的耐蝕性要優于壓鑄合金的。快速凝固合金的成分和組織均勻、大的固溶度,使局部腐蝕和電偶腐蝕被抑制,可以獲得較為優異的耐蝕性能。
4、鎂合金表面處理技術研究現狀
表面改性技術
1)化學轉化。鎂合金與轉化液發生化學反應生成一層保護性鈍化膜的處理技術稱為化學轉化法,其主要特點是設備簡單、成本低,適應于結構復雜件及大件的處理。化學轉化膜層與基體結合良好,擁有特定的孔隙,可以與有機層形成良好的結合,適用于環境溫度和表面質量精度要求不高的構件,如筆記本、手機外殼等。化學轉化膜層薄,對鎂基體保護有限,現多用于零件制備過程中的防護,特別是對大型復雜鎂合金構件機加工表面的短期防護。六價鉻轉化膜對鎂合金有較好的腐蝕保護作用,且工藝成熟,但六價鉻高度致癌,國際上已開始禁止使用。無鉻轉化膜技術受到廣泛關注,如磷酸鹽、高錳酸鹽、釩基鹽、稀土金屬鹽以及錫酸鹽處理等。非鉻酸鹽轉化方式及其優缺點如表 2 所示。
2)陽極氧化。利用電解作用在金屬表面成膜的過程稱為陽極氧化 , 陽極氧化膜為多孔雙層結構,較厚的多孔層為外層,較薄的致密層為內層,膜層的成分由合金元素的氧化物和沉積的氧化物共同組成。陽極氧化膜空隙大、無規則、分布不均勻,如果不進行封閉,耐蝕性非常差,因此,需進行后續的封孔處理,使其既美觀又耐蝕。早期的陽極氧化工藝主要有 DOW17、Cr22 及 HAE工藝等 , 如表 3 所示,處理液中含有鉻化合物,污染嚴重,因此逐漸開發了磷酸鹽等環保型陽極氧化工藝。
3)微弧氧化。微弧氧化是在金屬表面原位生長陶瓷層的技術,最早是由Gnterschulze 和 Betz 在 20 世 紀 30 年 代初提出,后經過各國科學家不斷完善。與化學轉化、陽極氧化技術相比,微弧氧化制備的膜層厚度可控,耐蝕性和耐磨性也更優異,在航天、航空、機械及電子等領域有廣泛的應用前景。微弧氧化膜層的生長是一個“成膜—擊穿—熔化—燒結—再成膜冶的多次循環過程,最終形成的膜層主要分為過渡層、致密層、疏松層。疏松層是由很硬的、孔隙較大的物質組成,表面疏松且粗糙,易打磨掉。致密層是微弧氧化層的主體,約占氧化層總厚度的 60% ~ 70%, 該層致密、孔隙小,每個孔隙的直徑約為幾微米,孔隙率在 5% 以下,主要是金屬氧化物,硬度高且耐磨。過渡層為界面層,是微弧氧化膜層與基體的交界處。過渡層凹凸不平,與基體相互滲透,使微弧氧化膜層與基體結合牢固,屬典型的冶金結合。當微弧氧化基體材料選定時,微弧氧化膜層的厚度與形貌主要受到電解液體系、電源類型、工作模式、電參數等的影響。鎂合金的微弧氧化已被證明是提高鎂合金的耐蝕和耐磨性能的有效途徑 。但微弧氧化膜層表面的微孔隙是限制耐蝕性提高的主要因素,需采用有效的封孔技術才能大幅度提高鎂合金的耐蝕性能。
4)離子注入及表面合金化。離子注入是將表面暴露在一束離子化的顆粒中,離子被嵌入并在基體的間隙位置被中和形成固溶體,從而改變基體的表面性能。離子注入也是提高鎂合金耐蝕表面改性的有效技術 , 采用一定劑量的離子可以抑制鎂合金的腐蝕,注入的元素主要有 N、O、Ti、Al 和 Zn 等。
但離子注入改性層的厚度一般較薄,耐蝕性能有可能不如厚陶瓷涂層。此外,表面合金化也是鎂合金改善鎂合金耐蝕性能的一種表面改性技術。通過激光等高能束流使基體表面預先涂覆的膜層和部分基體熔化,或者在表面熔化的同時注入某些粉末,膜層或表面在熔池中液態混合后發生快速凝固,從而在表面形成耐蝕性較好的合金薄層。近些年來,鋁合金表面激光合金化研究比較活躍,而對于鎂及鎂合金的激光表面合金化的研究并不多。
表面涂層處理
表面涂覆耐蝕涂層將鎂合金與腐蝕介質隔絕是提高鎂合金耐蝕性能的另一類有效途徑。目前耐蝕涂層主要有有機涂層、耐蝕金屬涂層以及化合物涂層等。有機涂層采用的主要工藝有涂漆、靜電噴涂、電泳等 , 金屬和化合物涂層采用的主要技術為電 / 化學鍍、冷噴涂、物理 / 化學氣象沉積、高能束流表面熔覆等技術 。
1)有機 / 聚合物涂層。涂覆有機 / 聚合物涂層可直接用于鎂合金表面耐蝕防護,還可用于鎂合金最外層防護涂層及封孔層,進一步提高耐蝕性。環氧樹脂、乙烯樹脂、聚氨酯等為常用的有機 / 聚合物涂層材料,其中環氧樹脂具有粘附力高、強度高、不浸潤水等特點,使用較廣。此外,粉末涂層因加熱固化成膜的溫度較高,會影響基體性能。
2)金屬 / 化合物涂層。金屬涂層主要是采用化學鍍和電鍍的方法在鎂合金基體表面涂覆一層金屬涂層。因鎂合金具有高的反應活性,屬于難電鍍基材,目前還未開發出耐蝕性較好的鎂合金電鍍方法。化學鍍鎳是通過自催化還原反應沉積 Ni-P(或 Ni-B)合金鍍層的工藝,鍍層為規則、均勻、致密的球形結點結構,且胞體具有明顯的界限,鍍層厚度均勻,具有較高的硬度和耐磨性,耐蝕性能優良。對 AZ91 的研究表明,經 Ni-P 與 Ni-P-SiC 化學鍍后,自腐蝕電位與 AZ91 基體相比明顯正移(表 4),腐蝕電流明顯降低,說明化學鍍層可以提高AZ91D鎂合金的耐蝕性,而添加SiC顆粒對耐蝕性的影響不大。與電鍍類似,有時也常常在鍍液中添加納米顆粒以提高耐磨等性能,或者通過化學鍍與電鍍的復合鍍層來提高鎂合金的耐蝕性。
化合物涂層在中性或者酸性腐蝕介質中呈現出比鎂合金基體高得多的化學惰性。在鎂及鎂合金基體表面制備出一層致密的化合物涂層將大大提高基體的腐蝕電位,提高耐蝕性。目前已通過 PVD 等技術在鎂合金表面制備出 TiN、AlN、CrN 以及 Al 2 O 3 等化合物膜。化合物層與基體附著力和耐磨性好,但因現有工藝制備的化合物涂層中存在孔隙,因此化合物涂層的耐蝕性并未充分體現出來。
冷噴涂是相對較新的一種噴涂技術,它是利用高速壓縮氣體將金屬或者陶瓷粉末加速后噴涂到基材表面,通過金屬粉末塑性變形形成致密的涂層。與傳統的熱噴涂相比,冷噴涂工藝過程溫度低,非常適合鎂合金等易氧化或對熱較敏感的基材,冷噴涂鋁合金等在鎂合金耐蝕防護領域展現出良好的應用前景。
5、結論
當前,鎂合金耐蝕性方面的研究已取得了可喜的成果。但隨著鎂合金應用深度及廣度的不斷擴大,將會遇到更為復雜的服役工況,鎂合金表面涂層在滿足防腐的同時,還要滿足耐磨等多種條件下的使用環境,對鎂合金表面處理技術提出了更高的要求。此外,還必須考慮鎂合金耐蝕技術的先進性、有效性,工藝的可操作性,涂層的性價比,以及環保問題等因素。這些因素直接決定了鎂合金的服役能力。因此,在未來相當長的一段時間里,提高鎂合金耐蝕性仍需做大量的研究才能滿足汽車、3C、國防軍工、航空航天等行業對輕質鎂合金材料的需求。
免責聲明:本網站所轉載的文字、圖片與視頻資料版權歸原創作者所有,如果涉及侵權,請第一時間聯系本網刪除。
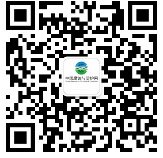
官方微信
《腐蝕與防護網電子期刊》征訂啟事
- 投稿聯系:編輯部
- 電話:010-62316606-806
- 郵箱:fsfhzy666@163.com
- 腐蝕與防護網官方QQ群:140808414