為了提高先進核反應堆的發(fā)電效率,在第四代超臨界水冷堆(SCWR)中,冷卻劑出口溫度被提高到550℃,壓力提高到25Mpa,其熱效率由目前第二代輕水反應堆(LWRs)的33%提高到44%左右。SCWR運行在水的臨界點(374℃,22.1Mpa)以上,此時冷卻劑對金屬材料的腐蝕性極強,現(xiàn)有的LWR堆芯構件和包殼材料已不再適用,結構材料的腐蝕已成為開發(fā)SCWR的一個關鍵問題[1] 。
對應用于超臨界火電站和壓水堆燃料組件等高溫環(huán)境中的材料進行了初步篩選與評估,提出了一系列SCWR候選材料,其中包括鐵素體-馬氏體(F/M)鋼、奧氏體不銹鋼、鎳基合金及氧化物彌散強化(ODS)鋼[2] 。其中,奧氏體不銹鋼因具有優(yōu)良的耐蝕性、加工性能、可焊性和高溫力學性能,在核電站結構件中被大量應用[3,4] 。
304NG奧氏體不銹鋼(簡稱304NG鋼)是使用最廣且價格相對低廉的一種奧氏體不銹鋼,常用于反應堆的堆內構件中,鉻含量約為20%(質量分數(shù),下同),鎳含量約為9%。與普通的低鉻奧氏不銹鋼相比,鉻含量超過18%的304NG鋼具有更加優(yōu)良的耐均勻腐蝕性能。為了研究304NG鋼在SCW中的均勻腐蝕性能以及溫度對其腐蝕性能的影響,本工作分別在550℃和650℃的低容氧(<10μg/L)SCW中對304NG鋼進行腐蝕增重試驗。
1 試驗
1.1 試樣
試驗選用304NG,其化學成分(質量分數(shù))為:wCr19.41%, wNi9.35%, wMn1.21%, wSi0.58%, wN0.089%, wCu0.062%,wCo0.028%, wP0.018%,wC0.018%, wS0.0072%,wB0.0015%,余量為鐵。試樣尺寸見圖1,并且通過在試樣表面打鋼號對其進行編號,避免發(fā)生混淆。采用180~2000號SiC水砂紙逐級打磨試樣表面,以消除加工硬化層對材料腐蝕性能的影響,之后在機械磨拋機上用氧化鋁拋光劑對試樣表面進行拋光處理,拋光期間用金相顯微鏡觀察拋光的效果。試樣拋光后用乙醇超聲清洗并烘干,之后用游標卡尺測量試樣的原始尺寸,并且采用高精度天平(精度為0.01mg)對試樣進行稱量。本工作采用腐蝕增重的方法研究材料在SCW中的腐蝕速率隨腐蝕時間的變化關系,取樣周期設定為100,300,600,1000,1500h,每個試驗周期結束后對所有試樣進行稱量。
圖1 均勻腐蝕試樣尺寸(mm)
Fig.1 Dimension of specimen in general corrosion test(mm)
1.2 試樣方法
均勻腐蝕試驗在高溫高壓循環(huán)水回路腐蝕系統(tǒng)中進行。如圖2所示,該設備主要包括一臺容積為1.5L的高壓釜,高壓釜的最高設計使用溫度為700℃,壓力為35Mpa,并且為了降低試驗過程中其他物質由于氧化釋放出雜質離子對試驗產(chǎn)生干擾,所用高壓釜釜體、釜蓋、熱電偶套管以及釜內配件等均采用625鎳基合金作為原材料,設備的低溫管路部分則采用316L不銹鋼,設備中的溫度測量單元和壓力測量單元分別為K型熱電偶和4~20mA輸出的高精度的壓力傳感器。本工作中的所有均勻腐蝕試驗均在控制水化學環(huán)境的循環(huán)水條件下進行,其中高壓泵給水流量大約為0.9L/h。
試驗條件如下:試驗介質采用超純水,采用H2除氧,溶液中溶解氧≤5μg/L,試驗溫度(550/650±0.5)℃,試驗壓力為(25.0±0.1)MPa,回水電導率≤0.1μS/cm。試驗結束后對材料在不同溫度下的腐蝕增重數(shù)據(jù)進行擬合,以得到材料的腐蝕增重規(guī)律,并且對其進行氧化動力學分析。同時采用SEM和EDS對試樣表面氧化膜的形貌、結構和成分進行研究,以得到材料在SCW中的腐蝕機理。
圖2 動態(tài)SCW腐蝕系統(tǒng)示意圖
Fig.2Schematic diagram of SCW experimental apparatus
2 結果與討論
2.1 氧化動力學
由圖3可見,腐蝕初期材料增重明顯,隨后腐蝕增重隨著腐蝕時間的延長而減小。由圖3還可見,相同腐蝕時間條件下,試樣在550℃時的腐蝕增重低于在650℃時的。304NG鋼在550℃和650℃的低溶氧SCW中的腐蝕增重曲線可以用式(1)擬合。
式中:k是氧化速率常數(shù),mg/(dm2·h);t是腐蝕的時間,h;n是時間指數(shù); ΔW代表增重,mg·dm-2。擬合結果見圖3,其中R2為擬合精度。
圖3 304NG鋼在550℃和650℃低溶氧SCW中的腐蝕增重曲線
Fig.3 Weigh gain curves of 304NG steel exposed to deaerated SCW at 550℃and 650℃
由擬合結果可知,304NG鋼在550℃和650℃的SCW中的氧化速率常數(shù)分別為0.35和4.66,表明304NG鋼具有良好的耐蝕性,尤其是在550℃條件下,材料的腐蝕速率極低。當溫度升高至650℃時,試樣的腐蝕速率明顯加快,1500h后腐蝕增重由550℃的18.50mg/dm2升高到143.05mg/dm2,腐蝕速率大約升高了8倍,這表明溫度對304NG鋼在SCW中的均勻腐蝕性能影響顯著。試樣在550℃和650℃時腐蝕增重所對應的時間指數(shù)分別為0.55和0.47。時間指數(shù)主要反映材料的腐蝕增重速率同腐蝕時間的關系,數(shù)值越小表明腐蝕增重的速率隨腐蝕時間的變化越快。試樣在SCW中的腐蝕速率隨著腐蝕時間的延長而下降,這是因為一旦表面形成氧化膜,會降低離子的擴散速率,因此時間指數(shù)越大表明腐蝕增重速率在腐蝕后期越快。304NG鋼在兩種溫度下的腐蝕增重雖然存在著巨大的差別,但是其時間指數(shù)類似,表明腐蝕過程中腐蝕速率的變化趨勢是類似的,而試樣的腐蝕增重變化規(guī)律反應其表面氧化膜的變化規(guī)律。總體來說,304NG鋼在550℃SCW中具有較好的耐蝕性,但是當溫度升高到650℃時,其腐蝕增重急劇升高。
2.2 氧化膜表面形貌
304NG鋼在550℃的低溶氧SCW中腐蝕1000h內,其表面氧化膜形貌沒有明顯變化,試樣表面仍然呈現(xiàn)出金屬光澤,表明試樣表面氧化膜的厚度很低。腐蝕1500h后,在試樣表面的局部區(qū)域觀察到了少量的癤狀腐蝕,見圖4。腐蝕1500h后材料表面的氧化膜依然很薄,并且能清楚地看到材料表面的劃痕,見圖4(a),同時在試樣表面還零星分布著少量癤狀腐蝕島,這些腐蝕島的尺寸較小,直徑約為20μm。為了更清楚地觀察材料表面癤狀腐蝕以及非癤狀腐蝕區(qū)的微觀形貌,分別對A、B區(qū)進行了局部形貌分析,見圖4(b)和圖4(c)。觀察發(fā)現(xiàn),試樣表面非癤狀腐蝕區(qū)的表面氧化膜極其致密,并且零星分布著尺寸很小的Fe3O4晶粒,因此該區(qū)域的氧化膜具有很好的保護性能;而癤狀腐蝕區(qū)域表面氧化膜形貌同F(xiàn)/M鋼表面氧化膜形貌類似,由大量的氧化物顆粒堆積而成,并且在這些顆粒物中還觀察到了少量的孔洞缺陷。在304NG鋼表面還觀察到了白色物質,分別對表面氧化膜的不同特征區(qū)進行EDS分析,結果見表1。由表1中不同區(qū)域的元素含量分析結果可知,區(qū)域1為癤狀腐蝕島,其主要成分為氧和鐵。癤狀腐蝕島是由基體材料內部的鐵擴散到材料表面被氧化后所形成的,由此可以推斷同其他金屬元素相比,鐵元素能夠以更快的速率通過癤狀腐蝕的形核區(qū),擴散到表面被氧化后形成了腐蝕島。區(qū)域2為非癤狀腐蝕區(qū),對比可知區(qū)域2中的鉻含量明顯高于區(qū)域1中的,表明該區(qū)域氧化膜的成分為鐵、鉻氧化物的固溶體,該結構比單純的鐵的氧化物更加致密,因此對基體材料具有更好的保護性。區(qū)域3的白色物質中含有大量鐵以及少量的鉻和氧,因此該白色物質為鐵單質和鐵、鉻氧化物的混合體,這是由于降溫過程中原本溶解在SCW中的氧化物和鐵單質由于溶解度下降而析出在氧化膜表面。為了更加直觀地觀察材料表面的癤狀腐蝕形貌,對試樣表面的一個獨立的癤狀腐蝕島進行三維形貌分析,見圖5。試樣表面癤狀腐蝕島為半球狀,是由基體材料內部的鐵元素向外擴散然后被氧化所形成的,腐蝕過程中,腐蝕島的體積會逐漸增大,然后孤立的腐蝕島之間相互連接,逐漸發(fā)展成為形狀各異尺寸更大的腐蝕島。
當溫度由550℃升高到650℃時,304NG鋼在SCW中的腐蝕過程同550℃時的情況類似,即腐蝕前期材料表面形成薄而致密的富鉻氧化膜,該氧化膜能夠有效抑制金屬離子以及氧的擴散,隨著腐蝕時間的延長,材料表面開始出現(xiàn)癤狀腐蝕,并且腐蝕島的尺寸隨著腐蝕時間的延長逐漸增大,然后不同的腐蝕島之間相互連接從而發(fā)展成為一個尺寸更大的腐蝕島。但是試樣在650℃的超臨界水中,其表面的癤狀腐蝕形核以及生長的速率更快,腐蝕100h就能在其表面觀察到大量的癤狀腐蝕島,癤狀腐蝕島的平均尺寸也遠大于550℃時腐蝕1000h后其表面的癤狀腐蝕島。可見,溫度對304NG鋼在SCW中的腐蝕性能有著重大的影響。溫度≤550℃,304NG鋼的耐蝕性良好,當溫度升高到650℃后材料表面出現(xiàn)了嚴重的癤狀腐蝕,導致材料的耐蝕性急劇下降。由圖6(a)可見,材料表面大部分區(qū)域已經(jīng)被癤狀腐蝕所覆蓋,在非癤狀腐蝕區(qū)繼續(xù)有新的癤狀腐蝕形核。650℃時試樣表面癤狀腐蝕島的形貌與550℃時的也不同,不僅尺寸更大,并且癤狀腐蝕島表面的氧化物晶粒的形貌也存在著差異。EDS分析表明,650℃時在SCW中腐蝕1500h后,腐蝕產(chǎn)物主要成分為鐵的氧化物,與550℃時的情況相同,但是650℃時幾乎所有的氧化膜晶粒都發(fā)生破裂,見圖6(c),從而使氧化膜的保護性能大大降低,并且加速了癤狀腐蝕的生長速率。而導致氧化膜晶粒發(fā)生開裂的原因可能是因為在腐蝕過程中,癤狀腐蝕區(qū)域所形成的氧化膜并不具有很好的保護性能,使得基體材料中的鉻、鎳發(fā)生流失,從而導致氧化膜內部的鉻和鎳的含量極低,見表2,最終在生長應力的作用下發(fā)生破裂[4,5] 。對于650℃時的非癤狀腐蝕區(qū),其元素含量同550℃時的類似。對650℃時的腐蝕試樣進行了三維形貌分析可知,此時癤狀腐蝕的密度更大,且腐蝕島的平均尺寸也更大,這表明溫度能夠加速304NG表面的癤狀腐蝕,見圖7。
圖4 304NG鋼在550℃的低溶氧SCW中腐蝕1 500h后的表面氧化膜形貌
Fig.4 SEM morphology of the 304NG exposed to SCW(1 500h)at 550℃for 1000h:(a)oxidation film;(b)enlarged view of A;(c)enlarged view of B
表1 304NG鋼(550℃)表面元素成分
Tab.1 Chemical composition of 304NG steel exposed at 550℃
圖5 304NG鋼在550℃的低溶氧SCW中腐蝕1500h后表面腐蝕島3D形貌
Fig.5 3D morphology of nodular island on 304NG steel after exposed to deaerated SCW at 550℃for 1500h
2.3 氧化膜截面形貌
由圖8可見,癤狀腐蝕氧化膜為典型的兩層結構,即外層腐蝕島以及內層氧化膜,并且通常內層氧化膜的厚度要大于外層氧化膜的。當溫度升高到650℃時,材料表面癤狀腐蝕的密度急劇升高,并且不同的癤狀腐蝕島之間相互連接,構成一個體積更大的癤狀腐蝕島。在650℃的低溶氧SCW中,當癤狀腐蝕島相互連接到一起之后,不同的氧化膜之間分層不明顯,并且氧化膜內部存在大量的孔洞以及裂紋等缺陷,這也導致氧化膜不具有很好的保護性能。對比兩種溫度下材料表面氧化膜的截面形貌可知,550℃的低溶氧SCW中形成的癤狀腐蝕氧化膜結構致密,其厚度在癤狀腐蝕的中心處達到最大值,然后依次向兩側遞減;650℃時材料的癤狀腐蝕嚴重,并且腐蝕島之間相互融合,表明當癤狀腐蝕向基體材料內部發(fā)展到一定深度后,由于氧在深度上的擴散阻力增大,從而選擇向兩側擴散,因此在癤狀腐蝕的發(fā)展后期癤狀腐蝕的深度基本不變,轉而在平面內繼續(xù)擴展,最終導致不同的癤狀腐蝕區(qū)域相互融合。
圖6 304NG鋼在650℃的低溶氧SCW中腐蝕1500h后表面氧化膜形貌
Fig.6 SEM morphology of 304NG exposed to SCW(1500h)at 650℃:(a)oxidation film;(b)enlarged view of A;(c)enlarged view of B
表2 304NG鋼(650℃)表面元素成分
Tab.2 Chemical composition of 304NG steel exposed at 650℃
圖7 304NG鋼在650℃的低溶氧SCW中腐蝕1500h后表面氧化膜3D形貌
Fig.7 3D morphology of 304NG steel exposed to deaerated SCW at 650℃for 1500h
圖8 304NG鋼在550℃和650℃的低溶氧SCW中腐蝕1500h后截面氧化膜形貌
Fig.8 Cross-sectional morphology of oxide scales of304NG steel exposed to SCW at 650℃(a),and550℃(b)for 1500h
由圖9可見,304NG鋼在550℃的低溶氧SCW中所形成的癤狀腐蝕內層氧化膜中的鉻含量同基體材料類似,沒有明顯的升高,鎳含量略高于基體材料;而外層氧化膜中的成分類似,幾乎全部由鐵的氧化物構成,鉻、鎳的含量極低。研究表明,材料表面氧化膜的保護性能主要由內層氧化膜的結構決定,內層氧化膜中的鉻含量越高則氧化膜的結構越致密,其保護性能也就越好[5,6,7]。在腐蝕過程中,材料內層氧化膜中的鉻會向外擴散,同時基體材料中的鉻也會對其進行補充,因此內層氧化膜中的鉻含量由這兩個過程的速率決定[8]。當鉻元素向外擴散的速率大于由基體材料向氧化膜內補充的速率時,氧化膜中的鉻含量會逐漸降低,反之則會逐漸升高;如果內層氧化膜中的鉻含量同基體材料中的相同時,表明兩個過程的反應速率相當,此時氧化膜的結構不夠致密,鉻會繼續(xù)向外擴散,并且外界的氧也會繼續(xù)向基體材料內部擴散,氧化膜的厚度也會進一步增加。當溫度升高到650℃時,氧化膜內部的元素分布呈現(xiàn)出典型的雙層結構,即外層富鐵貧鉻,而內層富鉻貧鐵,并且內層氧化膜中的鎳含量也明顯高于基體材料中的。可知此時的內層氧化膜結構致密,能夠有效抑制金屬離子以及氧的擴散,此時氧化膜的厚度基本不變,癤狀腐蝕轉而向四周擴展,最終導致不同癤狀腐蝕區(qū)域相互融合。
圖9 304NG鋼在550℃和650℃的低溶氧SCW中腐蝕1500h后的截面氧化膜元素分布
Fig.9 Cross-sectional composition distribution of 304NGsteel exposed to deaerated SCW for 1500h at 550℃ and 650℃
2.4 腐蝕機理研究
通過對氧化膜的表面以及截面形貌分析,可知304NG鋼浸泡在SCW中一定時間后,其表面會產(chǎn)生癤狀腐蝕,并且腐蝕溫度越高,癤狀腐蝕出現(xiàn)得越早,同時發(fā)展也越快。在550℃的超臨界水中,由于癤狀腐蝕的發(fā)展比較慢,因此304NG鋼在1500h內的腐蝕增重較低,但是癤狀腐蝕是一種局部腐蝕,會在后續(xù)過程中繼續(xù)擴展,并且造成非癤狀腐蝕區(qū)的氧化膜失去保護性能。同時,當溫度由550℃升至650℃時,材料表面的癤狀腐蝕嚴重,因此極大地限制了304NG鋼在SCW中的應用,因此有必要探討癤狀腐蝕形成的機理。
當前,學界對癤狀腐蝕形成機理的研究主要集中在鋯合金領域[9,10] ,而對于其他材料的癤狀腐蝕卻鮮見報道。在癤狀腐蝕的形成機理方面,目前主要有Kuwae[10] 所提出的氫聚集模型以及周邦新等人[11] 所提出的形核長大模型。本工作的研究結果表明,癤狀腐蝕的成因可能同所處的SCW環(huán)境有關。相關研究表明,Fe-Cr合金在含氧的蒸汽環(huán)境中呈現(xiàn)出同不含蒸汽的純氧環(huán)境中完全不同的氧化性能[12,13] 。Asteman[13] 的研究表明,304L奧氏體不銹鋼在873K純氧環(huán)境中發(fā)生氧化反應后會生成剛玉型結構(M2O3)的氧化物,然而在含氧的水蒸氣環(huán)境中,表面會形成一層相對較薄的(Cr,Fe)2O3氧化物,同時還能在試樣表面觀察到少量的磁鐵礦結構的癤狀腐蝕。Halvarsson[14] 的研究結果表明,在高溫水蒸氣環(huán)境中,304L鋼表面氧化膜內的鉻能夠同水發(fā)生反應,由于金屬離子以及氧在固態(tài)氧化物和金屬基體中的擴散速率主要由溫度控制,因此可用該理論來解釋304NG鋼在SCW中形成的癤狀腐蝕現(xiàn)象,見圖10。304NG鋼中鉻的質量分數(shù)約為19.4%,表明該材料的基體內有足夠的鉻可以用來補償氧化膜中由于揮發(fā)而損失的鉻。然而,鉻沿著晶界和在晶粒內部擴散的速率不同,通常鉻在晶界上的擴散較快,因此能夠及時補償晶界附近的氧化膜中因揮發(fā)而損失的鉻,而遠離晶界的氧化膜中的鉻由于得不到及時的補充,導致該區(qū)域的氧化膜中貧鉻。貧鉻的氧化膜通常不具備很好的保護性,外界的氧能夠很容易穿過氧化膜同基體材料發(fā)生反應,從而在氧化膜表面形成局部腐蝕區(qū)。隨著腐蝕時間的延長,基體材料內擴散速率更快的鐵穿過這個局部缺陷在表面同外界的氧發(fā)生氧化反應生成富鐵的腐蝕島,即外層氧化膜,同時外界的氧也穿過這個缺陷進入機體材料內部,形成內層氧化膜,最終導致癤狀腐蝕的形成。
304NG鋼在SCW中發(fā)生癤狀腐蝕的過程見圖11。在高溫高壓的SCW環(huán)境中,水會發(fā)生分解產(chǎn)生氧氣,由于304NG鋼內較高的鉻含量,其表面會迅速生成一層保護性氧化膜。在高溫高壓的SCW環(huán)境中,氧化膜中的鉻容易與水發(fā)生反應,并且生成易揮發(fā)的CrO2(OH)2,從而導致氧化膜中鉻含量降低;同時,基體材料中的鉻會向氧化膜中擴散,以補充鉻來維持氧化膜的保護性。但是由于鉻在沿著晶界與通過晶粒內擴散的速率不同,使得晶界附近的氧化膜富鉻,而遠離晶界的氧化膜貧鉻。隨著腐蝕過程的進一步發(fā)展,遠離晶界區(qū)域的氧化膜中的鉻含量將會進一步下降,最終使得該區(qū)域的氧化膜失去保護作用。然后,基體材料中的鐵、鉻、鎳等離子就會沿著這個缺陷處向外擴散,同時外界的氧離子則會沿著缺陷處向內擴散。由于鐵的擴散速率要遠大于鉻和鎳的[10] ,使得外層氧化膜主要為鐵的氧化物;另一方面,外界的氧進入基體材料后,會在基體材料內部形成鐵、鉻、鎳尖晶石結構,而鉻和鎳在這種物質中的擴散速率極慢,使得這兩種元素在該層堆積,被氧化之后使得該層氧化膜變得更加的致密,直到基體內的金屬離子以及外界的氧不再能穿過它為止,使得氧化膜在厚度方向上停止生長。此后,由于在深度方向上擴散的阻力逐漸增大,進入到氧化膜內的氧會向兩側擴散,使得癤狀腐蝕向四周擴展,最終同附近的癤狀腐蝕島融合到一起成為一個體積更大的癤狀腐蝕島。
圖10 304不銹鋼在高溫水環(huán)境中癤狀腐蝕形成機制示意圖[4]
Fig.10 Schematic diagram showing the formation of nodular corrosion on 304stain less steel in high temperature water environment[4]
3 結論
(1)304NG鋼在550~650℃、25MPa SCW中的腐蝕增重遵循冪指數(shù)規(guī)律,在550℃的SCW中具有較好的抗腐蝕性能,但是當溫度升高到650℃時,其腐蝕增重速率急劇升高。
(2)304NG鋼在SCW中出現(xiàn)癤狀腐蝕,并且溫度能夠極大地加劇癤狀腐蝕。
(3)304NG鋼在SCW中的癤狀腐蝕氧化膜為典型的兩層結構,外層富鐵貧鉻,而內層富鉻貧鐵,并且內層氧化膜的厚度要大于外層氧化膜的。隨著腐蝕時間的延長,腐蝕向周圍發(fā)展,最終導致不同的癤狀腐蝕區(qū)域相互融合。
(4)304NG鋼中鉻沿著晶界和在晶粒內部擴散速率的不同,導致癤狀腐蝕在遠離晶界處形核,并且最終發(fā)展為癤狀腐蝕。
圖11 SCW中304NG不銹鋼癤狀腐蝕機理模型
Fig.11 Model of nodular corrosion mechanism of 304NG stainless steel exposed to SCW
免責聲明:本網(wǎng)站所轉載的文字、圖片與視頻資料版權歸原創(chuàng)作者所有,如果涉及侵權,請第一時間聯(lián)系本網(wǎng)刪除。
-
標簽: 超臨界水, 304NG奧氏體不銹鋼, 癤狀腐蝕
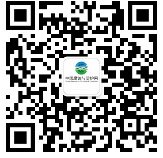
官方微信
《腐蝕與防護網(wǎng)電子期刊》征訂啟事
- 投稿聯(lián)系:編輯部
- 電話:010-62316606-806
- 郵箱:fsfhzy666@163.com
- 腐蝕與防護網(wǎng)官方QQ群:140808414