鎮海煉化公司在加工高硫(含硫)原油的同時 ,劣質高酸值原油的加工量也呈逐年快速遞增的態勢。高酸值原油具有密度大、酸值高、粘度大和殘炭高等特點 ,給煉油生產帶來了產品質量、系統平衡以及設備腐蝕等一系列不利因素 ,但因其市場資源豐富、價格相對較低 ,利用得好的話 ,也可成為企業創造效益的有效途徑。
1 高酸值原油加工情況
1. 1 原油中石油酸及其分布規律原油酸值的大小反映了原油中環烷酸、脂肪酸以及酚類等酸性氧化物(總稱石油酸) 的多少。在原油的酸性物質中 ,以環烷酸最為重要 ,含量也高 ,它約占原油酸性物質的 90 %。當原油酸值大 于0. 5mgKOH/ g即能引起設備腐蝕 ,故通常將酸值大于 0. 5mgKOH/ g的原油稱之為高酸值原油。
環烷酸是一種帶有五員或六員環的十分復雜的羧酸混合物 ,相對分子質量變化范圍很大 ,但以300~400 居多。低分子量的環烷酸在水中有一定溶解度 ,而高分子量環烷酸幾乎不溶于水。環烷酸在原油中的分布規律十分特殊 ,中間餾分 (250~350 ℃)環烷酸含量最高 ,而在低沸餾分和高沸餾分中環烷酸含量都比較低。也就是說環烷酸含量一般從煤油餾分開始逐漸增加 ,至柴油餾分其含量幾乎達到最高峰 ,然后有所下降[1 ]。
1. 2 近年來高酸值原油加工情況鎮海煉化公司共有三套常減壓裝置(常減壓) ,其中 I套常減壓按伊朗和沙輕原油對半加工設計 ,處理量 5. 0Mt/ a ; III套常減壓按只加工沙輕原油設計 ,處理量 10. 0Mt/ a ,均為含硫低酸值原油 ,設計酸值小于 0. 5mgKOH/ g ;僅有 II 套常減壓按卡賓達和渤海原油對半加工設計 ,處理量 3. 0Mt/ a ,設計酸值0. 58mgKOH/ g。但由于受加工量等因素制約 ,目前 II套常減壓停工 ,高酸值原油主要安排在 I套常減壓加工 ,如果高酸值原油集中到廠 ,也臨時安排在 III套常減壓加工。
近年來 ,常減壓裝置加工過的高酸值原油品種已達十余種 ,其中酸值最高的羅凱利亞原油 ,酸值達到3. 40mgKOH/ g。高酸值原油的酸值、加工量及所占比例均逐年快速遞增 ,見表 1。2 加工高酸值原油存在的問題2. 1 高酸值原油對系統平衡的影響(1)柴油精制問題加工高酸值原油時 ,常減壓柴油餾程正好處在環烷酸集中分布的范圍內 ,產品中環烷酸含量大 ,因而酸度高 ,見表 2。因此 ,欲生產合格柴油必須進行精制。
目前鎮海煉化公司柴油精制手段主要是堿洗電精制和加氫精制。如果集中加工高酸值原油 ,或者 Ⅰ, Ⅱ, Ⅲ套常減壓連續加工高酸值原油的話 ,會導致柴油產品酸度不合格。主要原因是:
① Ⅲ加氫的能力有限 ,只能基本滿足 Ⅲ常三線和催化裂化柴油的加氫要求 ,若 Ⅲ常二線酸度高時則無法加氫。
② 柴油的堿洗能力低 ,二線電離器堿洗能力為 33t/ h ,三線、催化柴油電離器堿洗能力為 65t/ h ,不能滿足 Ⅰ常三線和減一線的精制要求。
③ 酸度高的柴油安排堿洗電精制時 ,會導致堿液嚴重乳化 ,影響精制效果。同時大量柴油被堿渣帶走 ,造成全廠加工損失增加 ,大量廢堿渣的處理也帶來了環保問題。
表 3 所列為 2001 年 8 月 15 日 Ⅰ, Ⅲ常減壓同時加工高酸值原油時 ,柴油各組分及柴油罐的酸度數據。
由表 3 可見 , Ⅰ, Ⅲ常減壓同時加工高酸值原油時 ,受加氫能力的影響 , Ⅰ常三線和 Ⅲ常二線酸度較大 ,但也只能直接調合柴油 ,導致柴油罐酸度出現了高達 108. 4mgKOH/ L 的現象。
(2) 蠟油平衡問題鎮海煉化公司常減壓蠟油的去向有兩個 ,一是作催化裂化原料 ,二是作加氫裂化原料。高酸值劣質蠟油的特點是密度大、氮含量高(見表 4) ,環烷基及部分中間基高酸值原油的蠟油氮含量較石蠟基類蠟油氮含量高 3~8 倍 ,最高的羅凱利亞蠟油氮含量高達 0. 34 % ,其中堿性氮會被催化劑的酸性中心吸附成為焦炭的一部分 ,而使焦炭量增加 ,加速催化劑的中毒 (失活) ,影響催化裂化的轉化率。同時氮的存在還會影響產品的質量。作加氫裂化原料同樣存在氮含量高的問題 ,含氮化合物尤其是堿性氮化合物會強烈地吸附在催化劑表面 ,使酸性中心因中和而失活。因此加氫裂化裝置要求控制原料中的 氮 含 量 不 大 于 0. 18 %。同時加氫裂化原料對鐵離子濃度也有要求 ,在常減壓裝置現有加工條件下 ,高酸值原油的蠟油鐵離子濃度容易超標 ,鐵鹽沉積在催化劑上 ,將造成床層壓力降增大。#p#分頁標題#e#
(3) 劣質渣油平衡問題鎮海煉化公司渣油最主要的消化途徑是作焦化、化肥、瀝青以及減粘裂化的原料。高酸值劣質渣油的一個顯著特點是殘炭高 ,其中最高的葵土油高達 20. 97 %(見表 5) ,當作為焦化原料時 ,將使焦化液體收率明顯降低 ,焦炭收率大幅度上升 ,焦化產品質量變差。所產的 蠟 油 ,其 氮 含 量 都 在0. 47 %以上 ,比石蠟基類渣油的氮含量還要高 ,作催化裂化原料不合適 ,經加氫精制后作催化裂化原料成本又太高。高酸值劣質渣油部分可作道路瀝青、建筑瀝青原料 ,而公司加工高硫原油數量大 ,瀝青原料充足。高酸值劣質渣油作化肥原料時 ,由于粘度和殘炭超標 ,對生產影響較大。用減粘裂化裝置減粘后作燃料油同樣存在著粘度高的問題。如果在加工過程中注堿 ,鈉離子又會對催化裂化和加氫裂化原料造成二次污染 ,同時作焦化原料生產的石油焦因鈉含量高 ,對 CFB 鍋爐也會帶來不利的影響。
2. 2 加工高酸值原油對裝置設備的影響加工高酸值原油對裝置設備的影響主要是環烷酸腐蝕。當原油酸值大于 0. 5mgKOH/ g 時即能引起設備腐蝕。環烷酸在 220 ℃以下腐蝕很輕 ,在沸程為 270~280 ℃時腐蝕最嚴重 ,主要機理是環烷酸與鐵反應生成油溶性的環烷酸鐵 ,此后溫度再升高腐蝕反而減小。但當溫度達到 350 ℃時在硫化氫的作用下腐蝕又重新加劇 ,這時環烷酸不但與鐵反應生成環烷酸鐵 ,而且與硫化氫腐蝕產物硫化鐵反應生成環烷酸鐵 ,破壞硫化物形成的金屬保護膜 ,因此高酸值原油比高硫原油的腐蝕范圍更廣。
環烷酸腐蝕反應如下[2 ]:
2RCOOH + Fe →Fe (RCOO)2 + H2
2RCOOH + FeS →Fe (RCOO)2 + H2S
目前由于 II 套常減壓停工 ,高酸值原油主要安排在 I套常減壓加工 ,形成了高酸、高硫(含硫)原油交替加工的格局 ,這種交替加工將阻礙保護膜的形成 ,加劇裝置設備的腐蝕。從 I ,II套常減壓加工高酸值原油的設備腐蝕部位看 ,從低溫段至高溫段均有 ,特別是減壓塔的下部 ,如減二、三線及洗滌油段腐蝕最為嚴重。
從 I 套常減壓前期加工葵土原油和羅凱利亞原油減三線鐵離子分析數據看(見表 6) ,加工高酸值原油的設備腐蝕在加劇。
2. 3 加工高酸值原油對生產操作的影響⑴高酸值劣質原油幾乎都是重質原油 ,輕組分少 ,重組分多 ,熱量后移 ,導致生產時因低溫部位熱量少 ,造成電脫鹽溫度低。同時由于高酸劣質原油在脫鹽過程中乳化嚴重 ,電脫鹽罐油水界位控制困難 ,容易出現電壓回零 ,切水發黃的現象 ,從而降低了電脫鹽裝置的脫鹽效果。
⑵蠟油量大 ,裝置冷卻設備超負荷 ,蠟油冷后溫度超標。
⑶渣油量大、粘度高 ,造成外放困難。如果要求渣油進低溫罐時 ,由于渣油粘度大 ,傳熱效果差 ,不僅冷卻難度大 ,而且加大了泵出難度。
⑷高酸值劣質原油“頭輕腳重”,產品分布不均 ,常壓拔出量少 ,減壓蠟油、渣油量大 ,加大了加熱爐負荷 ,產品質量控制困難 ,難以提高裝置處理能力。
3 對策
3. 1 加強系統配套改造加強系統配套改造 ,以適應大量加工高酸值原油需要。目前 ,大量加工高酸值原油后續裝置處理能力不配套 ,柴油堿洗能力低、加氫能力有限 ,在 Ⅰ套、Ⅲ套常減壓同時加工高酸值原油時 ,柴油的高酸度問題已無法完全解決 ,若三套常減壓裝置同時加工高酸油 ,則柴油酸度高的問題更是無法解決。
同時蠟油氮含量高、渣油殘炭高也導致平衡困難。
因此 ,擴大柴油加氫處理能力 ,新建蠟油、柴油加氫裝置等配套設施十分必要。鎮海煉化公司正在建造的 3. 0Mt/ a 柴油加氫裝置和 1. 8Mt/ a 蠟油加氫裝置投產后將解決加氫能力不足的矛盾 ,提高酸值原油加工能力。
3. 2 全面提高裝置設備材質等級在沒有理想的工藝防腐蝕手段的情況下 ,提高設備材質的耐蝕等級是減輕環烷酸腐蝕最有效的方法。提高材質耐蝕等級的實質就是采用加入一定量的合金元素如 Cr ,Ni , Ti 的合金鋼 ,以便形成有一定效果的氧化物保護膜 ,該氧化物保護膜對金屬離子擴散有著強烈的阻滯作用 ,從而保護金屬不受進一步腐蝕。目前 ,常減壓裝置加工油種多 ,油性雜 ,特別是 Ⅰ套常減壓高硫高酸、低硫高酸、高硫低酸原油交替加工 ,設備腐蝕嚴重。就加工高酸值原油而言 ,目前 Ⅰ套常減壓一些主要部位的材質還不符合規范要求 ,如常壓爐、減壓爐的出口管線轉油線材質為 1Cr18Ni9Ti ,常二中蘇爾壽分配器材質為 1Cr13 ;一些高溫部位仍有部分碳鋼材質 ,如高溫設備的壓力表引出管線 (共 20 個) 和溫度計套管(共 15 個) ,與高溫管線相連的重污油線和吹掃蒸汽線 ,以及常二中 ,常二、三、四線 ,常底 ,減四線等機泵的泵缸。此外常二中和減壓塔的蘇爾壽填料雖然材質為 316L ,但厚度只有 0. 2mm ,長期加工高酸值原油很難保證填料不被腐蝕。Ⅲ套常減壓材質在耐環烷酸腐蝕方面較 Ⅰ套常減壓更差。因此要大量加工高酸值原油 ,有必要逐步提高常減壓裝置設備材質的耐蝕等級。#p#分頁標題#e#
3. 3 采取混煉加工技術在未對 Ⅰ, Ⅲ套常減壓材質耐蝕等級進行提升前 ,為保證裝置的長周期運行 ,加工高酸值劣質原油時應以帶煉和摻煉為主 ,并控制好混合原油的酸值低于 0. 5mgKOH/ g。計劃調度部門要避免高酸值原油集中到廠 ,盡可能不要安排 Ⅰ, Ⅲ套常減壓同時加工高酸值原油。在 Ⅰ套常減壓加工高酸值原油時 , Ⅲ套常減壓盡可能加工低酸值的含硫原油 ,這樣 Ⅰ常的二線、三線和減一線可堿洗后生產柴油 ,而 Ⅲ常二線不經加氫直接產柴油也不會對柴油罐造成嚴重影響 ,而當 Ⅲ常二線酸度高時若要直接生產柴油 ,必須間斷生產柴油 ,間斷改產加氫原料 ,以便于調合。高酸值原油的蠟油可以采用控制干點的辦法來控制其氮含量 ,同時可以與低氮含量的蠟油調合后給加氫裂化和催化裂化作原料。高酸值原油的劣質渣油也可以通過與低粘度渣油調合的方法供化肥作原料或作燃料油。
3. 4 重視脫鹽和注堿操作原油脫鹽不僅是原油蒸餾裝置塔頂系統工藝防腐蝕的關鍵環節 ,而且是對重油催化裂化和加氫等后續加工有重要作用的原油預處理工藝。提高脫鹽脫水效果 ,一方面可以減輕裝置腐蝕和結垢 ,另一方面通過電脫鹽裝置脫水脫鹽后 ,有效地減少原油中的金屬離子、氯離子 ,去除雜質成分 ,優化常減壓蒸餾裝置產品質量。開發篩選普遍適用于高酸值劣質原油的高效破乳劑 ,優化高酸值劣質原油脫鹽條件(如脫鹽溫度、注水量、混合強度等) ,采用合理的電場梯度等是提高電脫鹽效果的有力手段。
注堿可以中和原油中所含的酸性物質 ,從而降低原油酸值。同時注堿是一種比較容易實現的防腐蝕措施 ,也是目前大部分蒸餾裝置解決高酸值原油腐蝕的主要手段。在渣油不作催化裂化原料時 ,可以考慮注堿 ,但必須控制好注入量和注入時機 ,嚴防注堿過量和隨意注堿 ,以免給后續裝置生產帶來不必要的困難。
3. 5 采用新型有機胺和高溫緩蝕劑鑒于傳統的注堿方式 ,鈉離子對二次加工裝置影響較大 ,可以考慮用有機胺代替苛性鈉作為高酸原油的中和劑 ,如單乙醇胺 ,二乙醇胺等 ,不過成本相對較高。
針對環烷酸腐蝕特點 ,試用新型高溫緩蝕劑可以達到不注堿的情況下減緩蒸餾裝置高溫部位環烷酸腐蝕的目的。國內目前使用較好的是 GX -195 高溫緩蝕劑 ,該劑以高分子量、高沸點有機聚合物為原料 ,在金屬材質表面形成吸附性保護膜 ,同時部分高溫緩蝕劑直接與環烷酸作用 ,生成環烷酸脂 ,大分子量環烷酸脂可在金屬表面建立吸附平衡 ,將環烷酸等有機酸與金屬表面隔離 ,達到保護材質的目的 ,國內已有多家煉油企業采用 ,效果較好 ,缺點是成本稍高。考慮到鎮海煉化公司原油品種較雜 ,往往高硫、高酸原油交替加工 ,不利于保護膜的形成 ,高溫緩蝕劑可以考慮在長期加工高酸值原油的某一套常減壓裝置中使用。
3. 6 研究流速流態的控制在煉油工藝過程中 ,流速流態的控制十分重要。不同的流速流態對設備的腐蝕截然不同 ,流體流動方向的突然改變 ,流體高速沖刷 ,一些部位如轉油線腐蝕特別嚴重。高溫高速條件下 ,酸值很低的油品就可能有很高的腐蝕速率 ,即使是高合金鋼材料(如 316 ,317 ,含 6 %Mo 的合金) 也會被腐蝕。
因此研究控制好流體流速、流態有利于防止環烷酸腐蝕。
4 結束語高酸值原油的加工直接關系到產品質量、設備腐蝕、操作費用及環境保護等一系列問題 ,在原油采購過程中 ,應綜合考慮其經濟效益 ,不能單純追求原油的價格低廉。此外 ,考慮到三套常減壓裝置之間加工能力的優勢互補 , Ⅱ套常減壓裝置在改造時應按照高酸值原油設計選材 ,設計酸值應大于1. 0 mgKOH/ g為好。
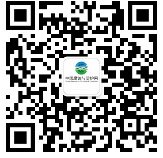
官方微信
《中國腐蝕與防護網電子期刊》征訂啟事
- 投稿聯系:編輯部
- 電話:010-62313558-806
- 郵箱:fsfhzy666@163.com
- 中國腐蝕與防護網官方QQ群:140808414