文/ 馬娜,王理·反應(yīng)堆燃料及材料國家級重點(diǎn)實(shí)驗(yàn)室
秦金光·江蘇核電有限公司
作者簡介
馬娜,助理研究員,碩士,2011年畢業(yè)于中國核動力研究設(shè)計(jì)院反應(yīng)堆燃料及材料專業(yè),目前從事反應(yīng)堆材料結(jié)構(gòu)與性能研究,及核電站技術(shù)服務(wù)領(lǐng)域工作。
本文以某核電站大修時發(fā)現(xiàn)壁厚減薄超標(biāo)而更換下來的管道件為研究對象,通過成分分析、微觀形貌分析和氧化膜分析等手段,結(jié)合管道的運(yùn)行工況環(huán)境分析,最終明確了這些管道的壁厚減薄模式分別為沖刷腐蝕、流動加速腐蝕和汽蝕,并提出針對性改進(jìn)措施建議。
核電站二回路的主蒸氣管道、主給水管線、凝結(jié)水管線、疏水管線、部分抽氣管線等用材主要是碳鋼。近年來,許多核電站出現(xiàn)了二回路碳鋼管道壁厚減薄現(xiàn)象,并由此引發(fā)了不少安全事故。1986年發(fā)生在美國Surry核電站中的冷凝水管道彎頭破裂事故,以及2004年發(fā)生在日本Mihama核電站中的給水管道破裂事故,均造成了人員傷亡。研究表明,這些管道發(fā)生破裂都是管道出現(xiàn)嚴(yán)重的壁厚減薄導(dǎo)致的。
某核電站在大修的超聲檢查中發(fā)現(xiàn),二回路中部分小規(guī)格(管徑小于50mm)的彎管、彎頭和孔板出現(xiàn)了破口或壁厚減薄現(xiàn)象。針對此情況,在被更換下的壁厚減薄管道中選取了一些典型管段進(jìn)行分析,并根據(jù)分析結(jié)果給出應(yīng)對措施建議。由于管道樣品較多,本文僅給出具有代表性的兩個彎管和一個孔板管道樣晶的分析過程。
樣品選取
本文選取了三個樣晶進(jìn)行分析:I號為疏水系統(tǒng)中的彎管,2號為給水系統(tǒng)中的彎管,3號為疏水系統(tǒng)中的孔板。比較I號、2號彎管,研究流速對于壁厚減薄的影響;比較1號彎管、3號孔板,研究管內(nèi)流體狀態(tài)對壁厚減薄的影響。三個管道樣品材料均為20G優(yōu)質(zhì)碳鋼,其樣品尺寸信息和服役工況如表1所示。
1號彎管位于該核電站2號機(jī)組主蒸汽系統(tǒng)的高壓疏水管線系統(tǒng)中,高壓疏水器前,控制閥后。主蒸汽系統(tǒng)壓力遠(yuǎn)高于疏水系統(tǒng)的壓力,故高壓管線疏水系統(tǒng)中流速較高。從該核電站系統(tǒng)流程圖冊中可以發(fā)現(xiàn),在1號機(jī)組的相同位置設(shè)置有節(jié)流孔板,相應(yīng)彎管并未發(fā)生壁厚減薄現(xiàn)象。而1號彎管所在的2號機(jī)組相應(yīng)位置并未設(shè)置節(jié)流孔板,彎管發(fā)生明顯壁厚減薄。
2號彎管位于給水系統(tǒng)的低壓加熱器和高壓加熱器之間,除氧器之后,屬于給水泵出口逆止閥的旁路管道,彎管下游為一個旁路閥。一般情況下,旁路閥是閉合的,當(dāng)給水泵單向閥出現(xiàn)故障或進(jìn)行檢修時才打開旁路閥,給水通過旁路閥進(jìn)入高壓加熱器。特殊情況下,流體可以經(jīng)該旁路進(jìn)入除氧器,對除氧器進(jìn)行清洗。由上述分析可知:2號彎管內(nèi)為經(jīng)過除氧的給水,水質(zhì)較好,且水溫較高;彎管內(nèi)長期有給水存在,可以傳質(zhì),但是由于旁路閥不常打開,故傳質(zhì)速度較慢。
3號節(jié)流孔板位于I號機(jī)組的高壓管線疏水線上,控制閥后,疏水器前,與1號彎管位置類似。孔板前后焊縫間長度為75mm,孔徑為10mm,孔長22mm,兩側(cè)為120度梯形過渡,核電站二回路蒸汽管道中的凝結(jié)水經(jīng)疏水管線匯入高壓疏水器內(nèi),由于主蒸汽系統(tǒng)壓力遠(yuǎn)高于疏水系統(tǒng)的壓力,故管中流速較高。
將上述管道樣品沿軸向和周向鋸開并實(shí)測發(fā)現(xiàn):1號彎管嚴(yán)重減薄(約1.5mm),內(nèi)壁黑色發(fā)亮,有尖銳的沖刷痕跡;2號彎管壁厚輕微減薄(約0.3mm),內(nèi)壁呈暗紅色;3號節(jié)流孔板在距離焊縫10mm處出現(xiàn)腐蝕穿孔,穿孔附近壁厚減薄明顯且表面粗糙,呈漩渦狀沖刷痕跡。三個樣品的局部形貌如圖1所示。
為了研究上述管道壁厚減薄的原因,進(jìn)行了相關(guān)分析工作。
試驗(yàn)結(jié)果
化學(xué)成分分析
采用電感耦合等離子體一原子發(fā)射光譜(ICP一AES)儀和碳、硫?qū)S梅治鰞x對上述管道樣品進(jìn)行了化學(xué)成分分析,并與GB5310一2008(高壓鍋爐用無縫鋼管)進(jìn)行比較,結(jié)果如表2所示。可以看出:管道中的Mn、Si、P等元素含量均符合標(biāo)準(zhǔn)的要求,但1號彎管中C元素含量偏低,s元素含量是國標(biāo)中限值的兩倍多。2號彎管中s元素含量也是國標(biāo)中限值的兩倍多。
金相分析
取上述管道樣品進(jìn)行鑲樣、研磨、拋光,用2%硝酸-酒精刻蝕,置于金相顯微鏡下觀察其金相組織,結(jié)果如圖2所示:樣品的金相組織正常,由鐵素體晶粒和呈網(wǎng)狀分布的珠光體構(gòu)成,夾雜物較少,表層無脫碳現(xiàn)象。
微觀形貌分析
利用掃描電子顯微鏡(SEM)觀察發(fā)生壁厚減薄部位基體的形貌特征。管道表面附著一層黑色或暗紅色的氧化膜,采用克拉克溶液100g濃HCL+2gSb203+5gSnCL)進(jìn)行了管道樣品的脫氧化膜處理,以便觀察基體。SEM下基體的微觀形貌如圖3所示。
1號彎管肘部內(nèi)壁在低倍下可見波紋狀形貌,高倍下可見表面較明顯的韌窩,局部有材料損失,說明管道內(nèi)壁在外力作用下發(fā)生塑性形變,并且有材料剝落現(xiàn)象。2號彎管在低倍下觀察到表面呈魚鱗狀分布的凹坑,尺寸約為200~300μm.高倍放大情況下,可見鐵素體晶粒及晶粒中不同取向的晶面,無明顯的機(jī)械形變特征。3號節(jié)流孔板表面可見大量細(xì)微的韌窩,尺寸為幾微米到十幾微米不等,明顯小于碳鋼晶粒,說明材料表面的各細(xì)微局部均分別受到了外力作用。
表面膜分析
對管道樣品原始內(nèi)壁的氧化膜進(jìn)行了Ⅹ射線衍射分析,結(jié)果如圖4所示。1號彎管內(nèi)壁盡管呈黑色,但是氧化膜衍射峰中Fe304特征峰很低,說明表面氧化膜非常薄,證明其生成時間很短。2號彎管內(nèi)壁檢測到了中等強(qiáng)度的Fe304特征峰,說明該彎管表面氧化膜相對較厚,存在時間較長。3號節(jié)流孔板內(nèi)壁檢測出了較弱的Fe304特征峰,說明表面有氧化膜,但較薄。
分析討論
1號彎管
C元素作為一種強(qiáng)化元素,可以提高碳鋼的強(qiáng)度和硬度,從而提高耐磨損、耐沖刷腐蝕的能力。1號彎管中C元素含量偏低,使得其硬度降低,耐磨性下降,耐沖刷腐蝕的能力下降。1號彎管處于高壓疏水管線,內(nèi)部流速較高,與流體接觸的表面在高速流體的作用下,表面材料不斷被沖蝕掉,導(dǎo)致管道減薄。由于表面材料不斷損失,故氧化膜不易留存,因而也起不到保護(hù)基體的作用。
另外,鋼中的S是有害元素,會與Mn元素形成MnS塑性非金屬夾雜物,影響鋼的抗氫致裂紋(HIC)和抗硫致應(yīng)力開裂(SSC)性能。但無論是金相分析還是微觀形貌分析,都未觀察到其對壁厚減薄的直接影響。
通過上述分析認(rèn)為,1號彎管內(nèi)的高速流體導(dǎo)致管道受到?jīng)_刷作用,發(fā)生壁厚減薄,屬于沖刷腐蝕。若在其上游設(shè)置節(jié)流孔板,將增加管道中的流動阻力,降低流體的壓力,起到保護(hù)管道的作用,避免管道發(fā)生因沖刷腐蝕導(dǎo)致的減薄。
2號彎管
2號彎管表面氧化膜是三類樣品中最厚的,且基體無可見的形變特征和機(jī)械作用導(dǎo)致的材料損失,說明氧化膜隔離了流體對基體的直接作用。從工況條件分析,2號彎管位于給水系統(tǒng)的旁路,內(nèi)部流速緩慢,不足以對管道材料產(chǎn)生沖刷作用。但流動的介質(zhì)加速了氧化膜的溶解和氧通過氧化膜向基體的擴(kuò)散,導(dǎo)致氧化膜在溶解的同時也不斷生長,最終使管壁減薄,符合流動加速腐蝕的過程。另外,2號彎管微觀形貌呈魚鱗狀,也屬于典型的流動加速腐蝕形貌。
盡管2號彎管中的S元素含量也偏高,但分析中同樣未觀察到其對壁厚減薄的直接影響。
通過上述分析認(rèn)為,2號彎管發(fā)生壁厚減薄的特征表現(xiàn)為氧化膜的加速溶解和生長,屬于流動加速腐蝕。根據(jù)目前對流動加速腐蝕的認(rèn)識,更換碳鋼材料,使用Cr含量高于1%的低合金鋼是較有效的途徑。對于正在使用的碳鋼管道,應(yīng)加強(qiáng)管道壁厚的監(jiān)測。
1、2號彎管雖然同屬于彎管,但內(nèi)部流速差異很大,因此發(fā)生壁厚減薄的機(jī)理完全不同,處理方式也截然不同,在工程實(shí)際中應(yīng)注意區(qū)別。
3號孔板
與1號彎管相比,3號節(jié)流孔板下游的彎管并未發(fā)生明顯的壁厚減薄現(xiàn)象,說明節(jié)流孔板的存在確實(shí)可以降低流速、降低流體壓力,從而避免管道發(fā)生因高速流體導(dǎo)致的沖蝕減薄。但是3號孔板自身出現(xiàn)了減薄穿孔,在損傷表面觀察到的大量細(xì)微韌窩,說明材料表面的各細(xì)微局部均分別受到了外力的作用。
分析其工況認(rèn)為,外力的來源與流體經(jīng)過孔板時產(chǎn)生的氣泡有關(guān):流體經(jīng)過孔板時壓力下降,低于流體的飽和蒸汽壓力,于是產(chǎn)生氣泡,即閃蒸;當(dāng)下游流體的壓力回升,氣泡發(fā)生潰滅,對材料局部造成巨大沖擊,即汽蝕。從材料已發(fā)生的微區(qū)塑性變形來看,其原因主要為汽蝕。
綜上,盡管3號孔板有效抑制了下游彎管的沖刷腐蝕,但該節(jié)流孔板的結(jié)構(gòu)形式導(dǎo)致流體通過時對孔板材料產(chǎn)生了汽蝕作用,導(dǎo)致孔板壁厚減薄并穿孔。因此應(yīng)優(yōu)化節(jié)流孔板的設(shè)計(jì)或者使用多級節(jié)流孔板。
結(jié)束語
經(jīng)過上述分析,得出以下結(jié)論。
(1)1號彎管內(nèi)的高速流體導(dǎo)致了沖刷腐蝕,造成管壁減薄。解決措施為:①在管道適當(dāng)位置安裝一定的分流系統(tǒng)來分擔(dān)流量,或增大管徑,降低管道中的流速。②提高管道中Cr元素含量,使用更加耐沖刷腐蝕的低合金鋼或不銹鋼。③減少彎管的使用或增大彎管的曲率半徑,緩解由于流體方向改變而造成的擾流程度。
(2)2號彎管內(nèi)發(fā)生的是以氧化膜加速溶解和生長為特征的流動加速腐蝕。解決措施為:①提高鋼管中的Cr元素含量或更換耐流動加速腐蝕的材料(如不銹鋼)。②控制氧濃度在合理的范圍內(nèi)(主要通過控制加入聯(lián)氨的量),控制腐蝕發(fā)生的環(huán)境。③加強(qiáng)對流動加速腐蝕敏感區(qū)域的壁厚測量力度。
(3)流體經(jīng)過節(jié)流孔板時產(chǎn)生氣泡潰滅導(dǎo)致對材料的汽蝕是3號孔板壁厚減薄、穿孔的原因。解決措施為:①根據(jù)具體的使用工況(如系統(tǒng)的流量、流速等)重新設(shè)計(jì)孔板,如孔徑、孔板厚度等。②設(shè)計(jì)多級孔板,通過多次降壓,避免汽蝕的發(fā)生。
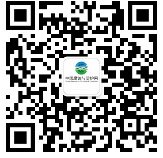
官方微信
《中國腐蝕與防護(hù)網(wǎng)電子期刊》征訂啟事
- 投稿聯(lián)系:編輯部
- 電話:010-62313558-806
- 郵箱:fsfhzy666@163.com
- 中國腐蝕與防護(hù)網(wǎng)官方QQ群:140808414