粉末涂料噴涂線的烘道上易形成沉積物,其中的灰分主要來源于聚酯樹脂中的揮發分,本文探討了影響聚酯樹脂揮發分含量的因素,在此基礎上制備了粉末涂料用低揮發分聚酯樹脂,用該樹脂配制成粉末涂料,具有固化時產生的灰分明顯降低的特點。
涂 料
1、前言
粉末涂料具有無溶劑揮發的特點,但相對于溶劑型及水性涂料來講,某固化溫度高,在噴涂線上普遍存在著烘道壁上出現大量沉積物的現象,造成安全風險,需要定期停產清理,影響生產效率。沉積的灰分不能回收利用,降低了粉末涂料的利用效率,增加了處理費用。這些問題在生產效率高且生產量大的鋁型材立式噴涂線上表現得更為明顯。
烘道壁上的沉積物分為兩部分:主要是黃灰色絮狀(灰分),另外還有部分焦油狀物質。本公司此前對其中的灰分進行了研究,發現其主要成分為含有聚酯結構的(來源于聚酯樹脂揮發分)組分R,其中還含有少量無機物及結構未經確認的褐色油狀物,并建立了其分離方法。
2、試驗
2.1主要原材料及儀器設備
對苯二甲酸(TPA),間苯二甲酸(IPA),乙二酸(AA),1.4—環己烷二甲酸(CHDA)、新戊二醇(NPG)、乙二醇(EG)、1.4—環己烷二甲醇(CHDM),2—乙基—2—丁基—1.3—丙二醇(BEPD)、酯化催化劑(Fc4100等)、亞磷酸三苯酯、主抗氧化劑B。
粘度劑(Brookfield)、NetsczhF200差示掃描量熱儀,300L不銹鋼反應釜。
2.2聚酯的合成
將配方量的醇投入反應釜中,升溫至120℃,待醇全部融化后開啟攪拌,將投入配方量的酸和催化劑,升溫至170℃,再以15℃/h的升溫速率升溫至250℃,維持溫度至反應物透明;
降溫至220℃,投入酸解劑及部分抗氧化劑,升溫至245℃,維持溫度至反應物透明;
降溫至220℃,投入剩余的部分抗氧化劑,攪拌均勻后開始抽真空,直至酸值、粘度合格,停止抽真空,投入配方量的固化促進劑,攪拌均勻后,出料。
2.3聚酯理化指標
采用前述方法,通過調節原材料種類及比例,制備了一系列樹脂。本研究制備的樹脂主要用于戶外鋁型材上,固化劑為TGIC,在綜合考慮與固化劑配比及儲存穩定性的條件下選擇以下五支樹脂進行應用性能研究,其參數如表1。
低揮發分粉末涂料用聚酯樹脂的制備研究
酸值根據GB/T6743-2008進行測試(mgKOH/g);熔融粘度根據GB/T9751.1-2008以BrookfieldCAP2000錐板粘度計測試(Cp/200℃);玻璃化溫度按GB/T19466.2-2004測試;軟化點根據GB/T12007.6-1989測試。
樹脂的酸度決定其固化劑的搭配比例,由合成樹脂時的酸醇比與抽真空時間決定。本文選擇制備配比為93:7、94:6、92:8的TGIC固化聚酯樹脂。
樹脂的玻璃化溫度是一個重要指標。當樹脂的玻璃化溫度高時,其抗結團性好,過低就會導致粉末涂料在儲存過程中結團,造成施工困難,尤其是TGIC會降低粉末涂料的玻璃化溫度,因此需要相對較高的玻璃化溫度。而在配方不變的情況下,提供玻璃化溫度會使樹脂的熔融粘度上升,流平性變差,因此必須綜合考慮。根據本研究的需求,所合成聚酯樹脂的Tg均在62℃以上。
2.4粉末涂料的制備及性能
將上述樹脂及某國外公司市售常規戶外鋁型材用聚酯樹脂(對比樣)按表2配制成粉末涂料,在雙螺桿擠出機上擠出、壓片、磨粉并靜電噴涂到鋁板上,200℃烘烤10min得到涂膜。由于粉末涂料的烘烤時的灰分沉積量在實驗室條件下難以檢出,因此本研究以粉末涂料揮發分來代替,同時將從樹脂中分離出的灰分主要組分R的含量作為參考。
流平通過目測評定;光澤按GB/T9754測試;耐沖擊性按GB/T1732-93測試;揮發分測試方法為:精確稱取2.0g左右的樣品于干燥(220℃)至恒重的坩堝中,200℃烘烤20min后取出,于干燥器中冷卻至室溫,測量烘烤前后樣品的質量并計算揮發分含量。耐候性根據ASTMG154CYCLE2測試240h,記錄保光率。
低揮發分粉末涂料用聚酯樹脂的制備研究
從上表中數據可以看出,本研究制備的低揮發分聚酯樹脂的揮發分含量明顯低于一般戶外鋁型材用聚酯樹脂,用其配制的粉末涂料揮發分含量也明顯較低,樹脂的基本應用性能達到要求。
值得指出的是,上述數據測試的時候受樣品儲存條件影響較大。當所用原材料儲存時間較長,尤其是未做好密封措施時,由于其會吸收空氣中的水分造成測量的揮發分偏高,因此必須使用同一批原材料進行同比試驗的結果才具有比較意義。
3、結果和討論
根據本公司之前的研究結果,聚酯樹脂中的灰分一部分為從工件飄落吸附的粉末涂料;另外一部分為聚酯樹脂中含有的低分子量揮發性物質,聚酯樹脂中的低分子量揮發性物質主要來源于合成過程中發生的副反應。如醚的生成、低聚物的生成、聚酯樹脂的熱氧化降解等。醚的生成主要發生在聚酯合成的酯化及縮聚起始階段,可能形成醚及含有醚鍵的聚酯,可通過使用酯化選擇性高的催化劑降低醚的含量。有文獻報道含磷聚合物可與聚酯中的金屬催化劑結合,對聚酯產生穩定作用,從而在縮聚階段抑制低聚物的產生。熱氧化降解在聚酯合成過程及烘烤固化過程中都有可能發生,但在真空縮聚階段,由于高溫及氧氣的作用,聚酯樹脂更易發生熱降解及熱氧化降解。本文對影響聚酯樹脂中低分子量揮發性物質含量的影響因素做了探討。
3.1催化劑的影響
酯化反應常使用有機錫如單丁基氧化錫等作為催化劑以加快反應速度,降低反應溫度。有機錫類催化劑活性高,在加快主反應的同時也加快了副反應的進行,導致低分子量揮發物的產生;使用活性低的催化劑將導致反應時間延長,熱降解及熱氧化降解增多,揮發物含量也會增加。
低揮發分粉末涂料用聚酯樹脂的制備研究
3.2抗氧化劑的影響
抗氧化劑分為主抗氧化劑及輔助抗氧劑。主抗氧劑一般為受阻酚類化合物,輔助抗氧劑以亞磷酸酯類化合物為代表。本研究分別考察了主輔抗氧劑添加方式對組分R含量的影響。由此可見,抗氧劑的加入方式對聚酯樹脂中R組分的含量有一定程度的影響。
低揮發分粉末涂料用聚酯樹脂的制備研究
3.3單體種類的影響
有文獻報道“無霜聚酯”中的“霜”為NPG與TPA形成的環狀低聚物,這也可能是R組分的組成之一,因此我們考察了BEPD、CHDM等對R組分含量的影響,結果見表5。由此可見,使用CHDM等新型單體可在一定程度上降低聚酯樹脂中的R組分含量。
低揮發分粉末涂料用聚酯樹脂的制備研究
3.4真空縮聚溫度的影響
粉末涂料用聚酯樹脂的合成一般是在較高溫度下采用本體聚合方式進行。反應溫度決定了反應的速度,過低的溫度將導致反應時間偏長,過高的溫度會增加副反應發生的幾率。本研究在真空縮聚階段分別采用210℃、220℃、230℃及240℃抽真空,考察了其對達到設定酸值/粘度所需時間及聚酯樹脂中灰分主要組分R含量的影響,結果見表3。從表中可以看出,隨真空縮聚溫度降低,R的含量也逐漸降低,真空縮聚的時間逐漸延長,因此本研究選用了220℃作為最合適的真空縮聚溫度。
低揮發分粉末涂料用聚酯樹脂的制備研究
4、結論
聚酯樹脂的揮發分含量取決于副反應發生的程度,選用催化劑K能有效地減少熱氧化及熱分解反應的發生,對降低揮發分有明顯作用;
抗氧劑的加入方式對聚酯樹脂的揮發分有一定的影響;
使用不易形成環狀低聚物的單體在一定程度上能降低聚酯樹脂的揮發分;
最佳的真空縮聚溫度為220℃。
采用上述合成條件,我們合成出了具有優良機械性能可用于戶外鋁型材的低揮發分粉末涂料用聚酯樹脂。
責任編輯:班英飛
《中國腐蝕與防護網電子期刊》征訂啟事
投稿聯系:編輯部
電話:010-62313558-801
郵箱:ecorr_org@163.com
中國腐蝕與防護網官方 QQ群:140808414
-
標簽: 粉末涂料
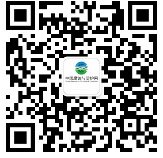
官方微信
《中國腐蝕與防護網電子期刊》征訂啟事
- 投稿聯系:編輯部
- 電話:010-62313558-806
- 郵箱:fsfhzy666@163.com
- 中國腐蝕與防護網官方QQ群:140808414