作為飛行器的“心臟”,航空發動機是技術高度集成和高附加值的科技產品,集中體現了一個國家的工業技術水平,被譽為現代工業皇冠上的明珠。經過幾代航空人艱苦卓越的奮斗,我國航空發動機工業取得了一系列令人矚目的成就,為我國國防事業發展和國民經濟建設做出了重要的貢獻。
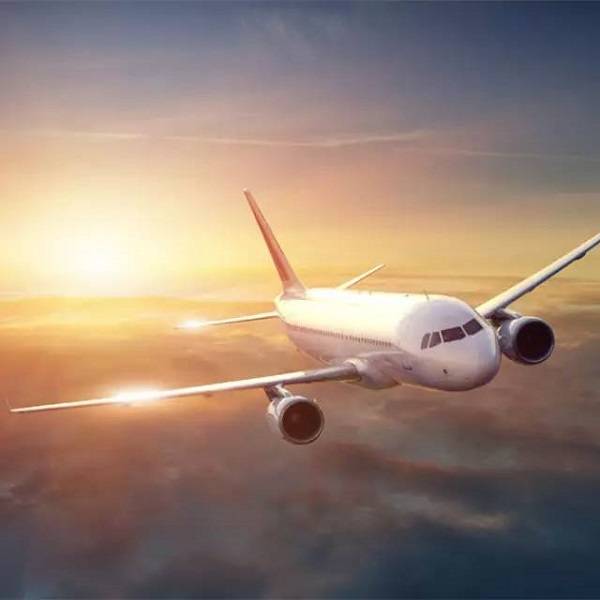
目前,復合材料已成為與金屬材料、高分子材料、無機非金屬材料并列的四大材料體系之一。一個國家的復合材料工業水平已經成為衡量其科技與經濟實力的主要標志之一。先進復合材料是國家安全和國民經濟具有競爭優勢的源泉。
復合材料具有比強度高、比模量大、耐高溫、抗疲勞性能好、可設計性強等獨有的優越性能,不僅在機械、化工、能源、交通、建筑等行業中得以廣泛應用,而且也成為航空航天、船舶等高技術領域的備受青睞的明星材料之一。
復合材料在渦輪發動機上的應用
由于具有密度小、比強度高和耐高溫等固有特性,復合材料在航空渦輪發動機上應用的范圍越來越廣且比例越來越大,使航空渦輪發動機向“非金屬發動機”或“全復合材料發動機”方向發展。
美國針對航空發動機實施的IHPTET 和VAATE 計劃,以及歐洲實施的ACME 和AMET 計劃,均將復合材料在航空發動機上的應用列為重點內容予以驗證和突破,包括:風扇寬弦復合材料葉片、纖維增強樹脂基復合材料機匣、350℃ 熱塑性復合材料中介機匣、SiC長纖鈦基復合材料的葉環、葉鼓和低壓渦輪軸、陶瓷基復合材料全環燃燒室、CMC 碳化硅復合材料浮壁燃燒室、CMC 碳化硅復合材料渦輪導向器、CMC 和C/C 復合材料渦輪轉子等相關結構,由此可見,復合材料在航空發動機上的大量使用己成為必然。
在NASA N+3 先進發動機項目中, GE 公司對將于2030~2035 年投入運營的高效安靜小型商用飛機所需的發動機進行了預研。
在NASA N+3 先進發動機項目中,除整體碳纖維風扇導向器/前機匣、復合材料風扇葉片和復合材料風扇機匣外,復合材料的應用還包含:復合材料附件機匣、新一代陶瓷基復合材料燃燒室、新一代陶瓷基復合材料高壓渦輪導向器葉片、新一代陶瓷基復合材料高壓渦輪葉片、新一代陶瓷基復合材料有圍低壓渦輪葉片、陶瓷基復合材料高壓渦輪支撐罩環和整流罩等,以及全復合材料整體發動機短艙。圖1顯示了NASA N+3 先進發動機項目中先進新材料應用情況。

圖1 NASA N+3 先進發動機項目中復合材料應用情況
1) 樹脂基復合材料
憑借比強度高、比模量高、耐疲勞與耐腐蝕性好、阻噪能力強的優點,樹脂基復合材料采用耐高溫樹脂(聚酰亞胺)制造,工作溫度可達250~350℃ ,用作發動機冷端部件,主要是在發動機的外涵道機匣、風扇機匣、進氣機匣、風扇靜子和轉子葉片、壓氣機葉片、包容機匣以及發動機短艙、反推力裝置等部件上得到廣泛應用。如在美國F404 、F101 、RB211 等發動機的復合材料外涵道整流罩或外涵道機匣及我國某發動機的復合材料外涵機匣等上都已廣泛應用
F119 發動機的碳纖維增強的聚酰亞胺基復合材料外涵機匣采用Dow-UT 公司研發的先進樹脂傳遞模塑(RTM) 成型法制造,外環、內轂、葉型支板模塑成一整體,通道表面光滑且滿足尺寸要求,工作溫度為316℃ ,質量減輕15% ~20% ,成本降低30%~35% 。該技術可以制造形狀復雜的進氣機匣,其所有外部氣流通道的表面粗糙度、最終尺寸精度可與經機械加工的鈦合金進氣機匣相媲美,并可使進氣機匣減少零件總數和取消許多勞動密集的裝配工序,因而可以大幅度減輕結構質量和降低成本。
惠普公司在經濟可承受的樹脂基復合材料研究計劃(后轉至JSF 研究計劃)下的推進系統可承受的復合材料研究項目(ACP) ,與Dow-UT 公司合作采用先進RTM 工藝制造風扇進口結構和風扇出口機匣。現在,為F119 發動機研制的復合材料風扇進口機匣已完成相關驗證。經驗證,與鈦合金的機匣相比較,費用降低了32% ,質量減輕了44% 。
通用電氣公司吸取了GE36UDF 發動機風扇葉片的研制經驗,采用樹脂基復合材料制造的單級大直徑(3 .43m) 寬弦實心復合材料風扇葉片。GE90 發動機風扇葉片(圖2) 的葉身和葉根均采用赫克塞爾(Hexcel) 公司的8551-7 高強度抗損傷結構用增韌改性環氧樹脂作為基體材料,用IM7 高強度、大伸長、中模量碳纖維作為增強體,制造成被稱為“大力神”的IM7/8551-7 碳纖維增強環氧樹脂復合材料預浸料。再由400 層預浸料帶從葉根到葉尖采用鋪層逐漸減薄的鋪層方式制成風扇葉片。為了提高葉片抗大鳥撞擊的能力,將鈦合金薄片用3MRAF191 膠黏在葉片前緣上,在葉尖與后緣處用凱芙拉細線進行縫合,這種結構不僅可以分散外物撞擊能量,還可以防止復合材料在葉片轉動時發生脫層。
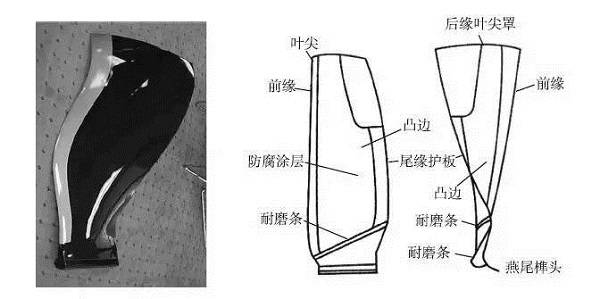
圖2 GE90 復合材料風扇葉片
復合材料的使用,大大減輕了風扇組件的質量。該風扇采用低葉尖速度、彈性變形吸收沖擊能量并重新分布、葉根在榫槽中偏擺減緩沖擊和局部包裹鈦合金的辦法成功地保證了風扇葉片的抗外物打擊性能;采用涂覆聚氨酯抗腐蝕涂層和使用特殊絲線縫合復材脫層部位等方式提高了風扇葉片的抗腐蝕性能。
波音787 用的GEnx 發動機風扇機匣采用7.62mm厚的三維織物以±60℃方式編織,并在邊角及彎曲處與工維織物混編在一起。編織采用自動化工藝,織物繞一風扇機匣工具編織成平面狀回在中部編織厚層作為風扇葉片的包容層,從而取消了鋁合金機匣上用的凱芙拉墊。織物一經鋪成,便從機匣外引入樹脂。
GEnx 風扇葉片設計方法與GE90-115B 相同,但葉片數量降到18 片(GE90-115B 為22片),直徑為2.82m 的風扇又進一步降低了噪聲。由于尖銳邊緣的復合材料有磨損的趨向,在葉片的前緣、葉尖及后緣增加了可以更換的鈦金屬包覆層。這種葉片邊緣也可以將外物打傷能量分散到風扇復合材料中去。復合材料風扇的使用除減重外,葉片數量的減少還可減少空氣阻力、降低噪聲(比CF6 降低30%)。由于復合材料本身具有耐腐蝕、耐疲勞的特性, GE公司認為復合材料風扇葉片在使用中可以免維護。由于復合材料葉片受到外物撞擊后,易于破碎成幾塊,在吸收撞擊能量的同時,還降低了對風扇機匣和包容環的撞擊程度,這使得復合材料葉片在減輕自身質量的同時,還減輕了風扇包容系統、風扇盤以及整個轉子系統的質量。另外,復合材料葉片還在抗顫振等方面優于金屬葉片,更利于實現大涵道比,進而達到降低泊耗和提高效率的目的。
法國斯奈克瑪(Snecma) 發動機公司采用編織復合材料和樹脂傳遞模塑(RTM) 技術最新研制的LEAP-X 發動機同樣采用碳纖維復合材料制造的18 片風扇葉片,其數量比CFM56-5C 減少一半,是CFM56-7B 的3/4。1.8m 直徑的葉片采用三維編織、樹脂傳遞模塑技術制造,可以給每架飛機減輕超過450kg的質量。
國內為設計高推重比發動機,也正積極開展先進復合材料的理論與研究,并取得了一定的成績。1972 年北京航空制造工程研究所以中等強度碳纖維為增強體,以648 環氧樹脂為基體研制出某型發動機風扇葉片,質量是鈦的56% ,榫頭拉斷強度為設計值的5 倍;由于振動阻尼系數為鈦葉片的5 倍,因而可以省去阻尼凸臺。某渦扇系列發動機中,已經廣泛采用先進樹脂基復合材料T300/KH304 和T300/BMP316 等制造復合材料外涵機匣,整體葉盤(外緣)纏繞結構等。在下一代高推重比發動機中,先進樹脂基復合材料將進一步用于制造風扇機匣、葉片,乃至低壓壓氣機機匣部件。
2) 金屬基復合材料
憑借密度小(有的僅為鎳基合金的1/2) 、比剛度和比強度高、耐溫性好等優點,碳化硅纖維增強的鈦基復合材料在壓氣機葉片、整體葉環、盤、軸、機匣、傳動桿等部件上已經得到了廣泛應用。美國的F100 發動機用硼纖維/鋁復合材料制作壓氣機葉片,不但可省掉鈦葉片需要的防顫振罩,增加空氣動力效率,且可減少葉片數量,提高葉尖速度和降低成本。
3) 陶瓷基復合材料
目前主要的陶瓷基復合材料產品是以SiC 或C 纖維增強的SiC 和SiN 基復合材料。憑借密度較小(僅為高溫合金的1/4~1/3) 、力學性能較高、耐磨性及耐腐蝕性好等優點,陶瓷基復合材料,尤其是纖維增強陶瓷基復合材料,已經開始應用于發動機高溫靜止部件(如噴嘴、火焰穩定器、燃燒室火焰筒、燃燒室和內外襯等) ,并正在嘗試應用于渦輪轉子葉片、渦輪導流葉片等部件上。其中, SiC/C 復合材料整體渦輪葉盤和CMC-SiC 渦輪導向葉片(圖3) ,不冷卻或簡單冷卻,可提高渦輪前使用溫度,降低結構質量并提高壽命。
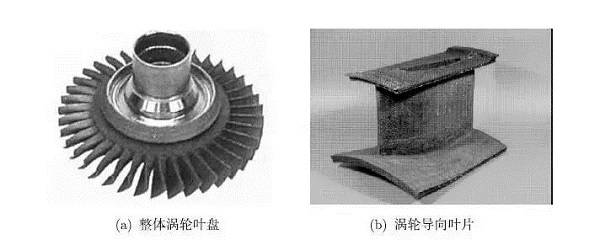
圖3 SiC/C 復合材料整體渦輪葉盤和CMC-SiC 渦輪導向葉片
復合材料在導彈和火箭發動機上的應用
以碳纖維復合材料為代表的先進復合材料的發展推動了航天整體技術的發展。碳纖維復合材料主要應用于導彈彈頭、彈體箭體和發動機殼體的結構部件和衛星主體結構承力件上,碳/碳和碳/酚醛是彈頭端頭和發動機噴管喉襯及耐燒蝕部件等重要防熱材料, C/C 最早用作其噴管喉襯,并由二維、三向發展到四向及更多向編織。碳纖維復合材料在美國侏儒、民兵、三叉戟等戰略導彈上均己成熟應用,美國、日本、法國的固體發動機殼體主要采用碳纖維復合材料,如美國三叉戟-2 導彈、戰斧式巡航導彈、大力神-4 火箭、法國的阿里安-2火箭改型、日本的M-5 火箭等發動機殼體,其中使用量最大的是美國赫克里斯公司生產的抗拉強度為5.3GPa 的IM-7 碳纖維,性能最高的是東麗T-800 纖維,抗拉強度5.65GPa、楊氏模量300GPa。
俄羅斯海上導彈系統中的佼佼者是“圓錘”(布拉瓦)型潛艇發射導彈,該導彈發射機動性好,同時擁有海基和陸基兩種打擊版本,可以攜帶6~10 枚分導式核彈頭,配備在海軍“臺風”級,以及未來新型“北風之神”級核潛艇上,可以突破敵方導彈防御系統,有效摧毀全球任何地方的敵方目標。這些新型導彈的發動機噴管及大面積防熱層均使用黏膠基碳纖維增強的酚醛復合材料。
目前為解決固體火箭發動機結構承載問題,美國和法國正在進行陶瓷纖維混合碳纖維而編織的多向(6 向)基質、以熱穩定氧化物為基體填充的陶瓷復合材料。SiC 陶瓷制成的喉襯、內襯已進行多次點火試驗。今天作為火箭錐體候選材料的有A12 03 、Zr02 、Th02 等陶瓷,而火箭尾噴管和燃燒室采用的高溫結構材料有SiC 、石墨、高溫陶瓷涂層等。
我國各類戰略和戰術導彈上也大量采用碳纖維復合材料作為發動機噴管、整流罩防熱材料。我國20 世紀90 年代后期開展了纖維增強復合材料材料殼體的研究,進行了T300CFRP 固體火箭發動機殼體的基礎試驗、殼體結構強度試驗、點火試車等全程考核中完成了12K-T700-CFRP 殼體結構強度試驗,開展了T800 碳纖維CFRP 多種殼體的預研試驗。
更多關于材料方面、材料腐蝕控制、材料科普等方面的國內外最新動態,我們網站會不斷更新。希望大家一直關注中國腐蝕與防護網http://www.ecorr.org
責任編輯:殷鵬飛
投稿聯系:編輯部
電話:010-62313558-806
中國腐蝕與防護網官方 QQ群:140808414
免責聲明:本網站所轉載的文字、圖片與視頻資料版權歸原創作者所有,如果涉及侵權,請第一時間聯系本網刪除。
相關文章
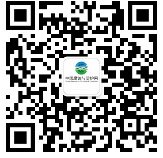
官方微信
《中國腐蝕與防護網電子期刊》征訂啟事
- 投稿聯系:編輯部
- 電話:010-62316606-806
- 郵箱:fsfhzy666@163.com
- 中國腐蝕與防護網官方QQ群:140808414
點擊排行
PPT新聞
“海洋金屬”——鈦合金在艦船的
點擊數:8125
腐蝕與“海上絲綢之路”
點擊數:6461