以中國北方某再生水廠的出水為研究對象,重點圍繞特征有機物腐殖酸對鑄鐵腐蝕的影響開展實驗研究,應用X射線衍射、掃描電鏡等手段,探討了再生水中腐殖酸對鑄鐵腐蝕形貌、腐蝕生長過程及腐蝕形成機制的影響。結果表明,在反應初期,再生水中的腐殖酸與鑄鐵表面反應形成穩定的吸附膜抑制鑄鐵表面的腐蝕,隨著反應時間的推移,逐漸生長的污垢將吸附膜破壞形成腐蝕,再生水中腐殖酸濃度為6 mg/L時腐蝕速率最小,因此,再生水中腐殖酸濃度過高和過低都不利于腐蝕控制。
再生水回用具有水質水量相對穩定,不受季節影響的特點,是解決水資源短缺現實可行的措施。但是,城市再生水由于原水水質復雜、各處理工藝出水水質差距較大等原因,經膜工藝處理后仍然具有較高的溶解性有機物 (DOM) 含量。其中最主要的組分是腐殖質,約占水中總有機物的60%~90%,其組成較復雜,通常沒有固定的結構,一般認為是由一些烷基芳香烴單元、羧基、酚羥基和醌基等官能團組成,可將其分為腐殖酸、富里酸及親水酸三類。目前,人們研究較多的是腐殖酸和富里酸,常把它們統稱為腐殖酸。腐殖酸在水體中通過酚羥基、羧基、醇羥基、羰基、醌基等多種基團可以與有機物進行結合,同時也對許多金屬離子具有很強的絡合作用,進而影響有機污染物和金屬離子在水體中的遷移轉化行為,威脅城市的供水安全。Rahman等對溶解性有機物在鑄鐵管上的吸附進行了研究,研究發現DOM會吸附在鑄鐵管的腐蝕產物Fe3O4和FeO(OH) 上,同時符合Langmuir吸附等溫線,表現為單層吸附,這種吸附能力在pH較低的情況下表現更加明顯。崔崇威等在腐殖酸對水源供水安全方面進行了研究,結果表明,腐殖酸易引起水廠出水色度超標,降低生物穩定性,影響給水衛生,是某些地方性疾病的主要環境因素之一。然而,在再生水輸配過程中腐殖酸對管道腐蝕影響的研究尚缺乏。為了減緩和防護再生水水質對管道產生的腐蝕作用,保證再生水在輸配環節的安全,提高再生水系統的運行可靠性和經濟性,開展再生水中腐殖酸對常用金屬管材的腐蝕特性研究具有很強的現實意義。
1 實驗方法
試驗采用鑄鐵腐蝕掛片 (5 cm×2.5 cm×0.2 cm),材料化學成分 (質量分數,%) 為:C 3.17,Si 1.56,Mn 0.34,P 0.12,S 0.12,Fe余量。再生水取自北方某再生水廠,該再生水廠采用超濾膜處理工藝。
根據再生水水質,利用純水與NaCl、Na2SO4、Na3PO4配制原水,并加入一定量腐殖酸,用于試驗分析。配水水質參數 (mg/L) 為:SiO2 0.3,Cl- 16.7,Ca2+ 30,SO42- 5.5,Na+ 10.1,HCO3- 40,PO43- 0.19,調節其pH值至5.9。本試驗所用腐殖酸為商用腐殖酸,將腐殖酸粉末在堿性條件下溶解,將溶液經0.45 μm濾膜過濾,濾后樣品作為腐殖酸原溶液,試驗過程中所需不同濃度的腐殖酸由高濃度原溶液用蒸餾水稀釋而成。
腐蝕掛片試驗在旋轉反應器中進行,如圖1所示。將15片掛片放置在旋轉反應器的雙層塑料支架上,原水加入反應器,在運行不同時段取出三片掛片,冷凍干燥后一片用于掃描電鏡分析,一片用于腐蝕失重分析,一片留存備用。試驗分別在2,4,6和8 mg/L 4組不同濃度的腐殖酸下進行,同時進行一組空白試驗 (即腐殖酸為0 mg/L)。試驗過程中保持間歇進水,每次進水210 mL,進水時間間隔為2 h,水力停留時間為48 h。旋轉攪拌器轉速穩定在122 r/min,水溫控制在20 ℃,pH值控制在6.0左右。
采用Quanta 200 FEG環境掃描顯微鏡 (SEM) 分析腐蝕掛片形貌。由于腐蝕掛片表面腐蝕產物疏松,在測試之前需進行預處理,用棉簽刮去掛片背面的腐蝕產物并用洗耳球進行吹掃,以免在測試時由于掉渣損傷儀器。采用Genesis能譜儀 (EDS) 進行微區元素定量分析。采用X'PERT-PRO MPD X射線衍射儀 (XRD) 分析鑄鐵掛片表面污垢晶體結構組成,測試條件:CuK輻射、管壓40 kV、管流40 mA,采用步進掃描方式,速度為10°/min,步長0.02°。
采用失重法對金屬腐蝕情況進行分析,腐蝕速率計算見下式:
式中,ν為年腐蝕深度,mm/a;m0為腐蝕前掛片的質量,g;m1為經過一段時間的腐蝕并去除表面腐蝕產物后掛片的質量,g;ρ為試驗金屬材料密度,g/cm3;S為掛片暴露在腐蝕環境中的表面積,m2;t為掛片腐蝕的時間,h。
2 結果與分析
2.1 鑄鐵腐蝕形貌特征
設置不同腐殖酸濃度,對鑄鐵掛片分別進行定期取樣,用10%HCl+0.5%六次甲基四胺配制的混合液對鑄鐵掛片進行清洗,洗去鑄鐵掛片表面污垢及雜質,在自然通風處風干后觀察鑄鐵掛片表面形貌。鑄鐵掛片表面腐蝕以點蝕開始,隨著反應時間的增加,由點蝕不斷擴大,形成條狀腐蝕區。反應末期,鑄鐵掛片表面出現粗糙的黑點物質,說明不同反應時間的腐蝕產物也有所不同。通過電鏡觀察,鑄鐵表面沒有明顯的腐蝕區與非腐蝕區,以全面腐蝕為主,如圖2a所示。鑄鐵表面出現兩種結構:一種是六棱片結構,如圖2b所示;另一種為空心球狀結構,如圖2c所示。六棱片狀腐蝕產物直徑約為20~30 μm,結構密實;空心球狀腐蝕產物直徑約為5~10 μm,空心,殼較厚,結構密實,且球體表面有羽毛狀纖維鐵氧化物。
張超等采用4個CDC生物膜反應器串聯模擬回用水管網,通過控制水力停留時間和攪拌轉速來描述不同長度管道在不同流速下的流態,針對鑄鐵回用水輸送管道腐蝕產物的沿程變化特征進行研究。通過對腐蝕產物的微觀形態進行分析,模擬回用水鑄鐵管道沿程腐蝕產物的微觀結構由表面存在著微小的顆粒物的疏松多孔結構向表面附著少量絲狀物的致密硬殼結構轉變。此結果與本研究結果相符合,這種結構致密的腐蝕產物在腐蝕層中的含量較多,有文獻報道過類似的鐵氧化物,認為是綠銹 (Green rusts) 和纖維鐵氧化物。
2.2 鑄鐵腐蝕產物分析
2.2.1 污垢層結構及其變化
利用SEM對不同濃度的腐殖酸影響下鑄鐵掛片表面進行觀察,同時對污垢微面積進行EDS分析,明確不同形貌污垢的元素組成,了解不同階段不同腐殖酸濃度影響下鑄鐵掛片表面污垢的內部結構。根據SEM觀察和EDS分析可知,掛片表面污垢層可分為凸起區和非凸起區。隨著反應時間的增加,鑄鐵掛片表面污垢由均勻分布發展成明顯的水紋狀凸起,掛片表面污垢層厚度不斷增大,同時污垢表面結構的剝落和內層結構的生長,表明污垢具有由內向外不斷生長的規律。污垢主要以Fe、O和C原子為主。
水中無腐殖酸存在時,掛片污垢層凸起區與非凸起區的組成類似,均以鐵化合物為主,污垢結構以多孔結構為主。腐殖酸濃度為4和8 mg/L時污垢表面形貌分別如圖3a和d所示,標記點1、標記點2、標記點3處污垢的能譜分析分別見圖3b,c和e。當腐殖酸濃度為4 mg/L時,隨著反應進行,污垢中原子C和原子O的原子分數明顯增加,分析可知是由于有機物被吸附在鑄鐵表面所致。另外,凸起區C原子分數比非凸起區低,說明凸起區的有機物含量比非凸起區低,可能是因為有機物吸附形成的吸附層遭到破壞,污垢層從內部向外擴展,產生凸起。反應后期,凸起區與非凸起區裂縫間出現片狀結構污垢,由能譜分析可知,此時O原子分數明顯下降,說明此時腐蝕產物可能由γ-FeOOH轉化為α-FeOOH[15]。污垢結構以菜花狀結構為主。當腐殖酸濃度為8 mg/L時,隨著反應進行,C原子分數明顯增加,但O原子分數有所下降,掛片表面污垢層凸起區和非凸起區組成結構類似,均以有機物吸附為主,污垢結構以密實排列的球狀結構為主。
2.2.2 污垢層相組成及其變化
腐殖酸濃度不同時鑄鐵掛片表面污垢晶體結構分析如圖4所示。圖4表明,不同濃度腐殖酸對鑄鐵掛片產生的影響趨勢基本一致。以腐殖酸濃度為4 mg/L為例,反應初期,污垢不穩定且組成成分較為復雜,主要以Fe、γ-FeO(OH) 為主。隨著反應的進行,腐蝕產物也逐漸發生變化,反應后期主要以α-FeO(OH) 為主。結合掃描電鏡分析結果,可以看出在腐蝕反應的進程中,腐蝕產物由Fe2+向γ-FeO(OH) 轉化,最終形成了以α-FeO(OH) 為主的污垢主體層。這是由于羥基氧化鐵在α-FeO(OH) 晶型時較穩定,其他晶型處于亞穩定狀態易于轉化成α-FeO(OH)[16]。Sarin等[17]研究鐵質供水管道的腐蝕垢層理化結構時發現,腐蝕垢層分為三層:最外層是疏松層,中間是較致密的殼狀層,最內層是多孔層。最外層中含有較多的α-FeO(OH),此結果與本試驗結果相吻合,這類鐵氧化物是由其他穩定性較差的鐵氧化物緩慢轉變而來的,其對金屬的進一步腐蝕有抑制作用,可以減緩腐蝕速率。
2.3 鑄鐵腐蝕速率分析
反應器內腐殖酸濃度分別為0,2,4,6和8 mg/L,通過腐蝕失重法對各反應器內的鑄鐵掛片在反應過程中的腐蝕速率進行分析,結果如圖5所示。
反應器內腐殖酸濃度分別為0,2,4,6和8 mg/L,通過腐蝕失重法對各反應器內的鑄鐵掛片在反應過程中的腐蝕速率進行分析,結果如圖5所示。由圖5可知,不同濃度腐殖酸對鑄鐵掛片的腐蝕速率影響基本遵循先下降后上升的趨勢。在無腐殖酸條件下,反應進行1 d時腐蝕速率達到13.3 mm/a,遠高于腐殖酸存在的情況,說明在腐蝕反應初期腐殖酸的存在會抑制腐蝕的發生。反應進行到4 d時,腐蝕速率降低,由圖4可知,此時鑄鐵表面逐漸形成較穩定的α-FeO(OH),保護了鑄鐵內部不受腐蝕,且有腐殖酸存在時,腐蝕速率更低,由圖3b,c和e可知,此階段C、O含量增加,證明鑄鐵表面被腐殖酸吸附,形成穩定的保護膜,使抑制腐蝕效果更加明顯,如腐殖酸濃度為4~8 mg/L時,腐蝕速率為2.9 mm/a,腐殖酸濃度2 mg/L時,腐蝕速率降到3.9 mm/a,說明更高濃度腐殖酸的存在使金屬表面形成的保護膜更加致密,抑制效果更強。在反應后期如反應進行到12和16 d,不同腐殖酸濃度所致的鑄鐵腐蝕速率均有所上升,并逐漸保持穩定,其中,腐殖酸濃度為2 mg/L時腐蝕速率增加最快,16 d時升高至8.7 mm/a,超過腐蝕初期的腐蝕速率 (反應1 d時為7.9 mm/a),說明腐殖酸濃度為2 mg/L時鑄鐵表面污垢結構很不穩定。反應進行至16 d時,腐殖酸濃度為6 mg/L時腐蝕速率明顯較低,說明腐殖酸濃度為6 mg/L時鑄鐵腐蝕最為穩定且腐蝕速率最小。
綜上所述,在反應初期,沒有腐殖酸加入的情況下,鑄鐵表面直接受到來自水體的沖擊,發生快速腐蝕。而大量的研究結果[18-21]表明,腐殖酸會通過配位交換、陰離子交換、陽離子架橋、靜電力和范德華力等作用吸附在金屬氧化物上。腐殖酸中含有的羧基和酚羥基 (—COOH、—OH) 官能團取代鑄鐵表面的羥基 (—OH)、陰離子和水分子等吸附在鑄鐵表面,與鐵氧化物發生絡合反應,在鑄鐵表面形成穩定的吸附膜,抑制腐蝕的進行。隨著反應進行,腐殖酸吸附在鑄鐵表面的保護膜被破壞,表面污垢結構平衡也失去穩定,腐蝕速率上升。一定濃度的腐殖酸通過吸附-脫附、微生物降解、光解以及生物富集等過程導致管壁中形成異常生物膜,降低管網系統的生物穩定性,進而加速管網腐蝕。在腐殖酸濃度小于6 mg/L時,鑄鐵腐蝕速率隨著濃度的增加而減小,在腐殖酸濃度大于6 mg/L時,鑄鐵腐蝕速率不降反升,加速鑄鐵的腐蝕,為控制鑄鐵腐蝕,腐殖酸濃度宜控制在6 mg/L。
責任編輯:王元
免責聲明:本網站所轉載的文字、圖片與視頻資料版權歸原創作者所有,如果涉及侵權,請第一時間聯系本網刪除。
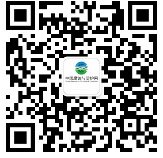
官方微信
《中國腐蝕與防護網電子期刊》征訂啟事
- 投稿聯系:編輯部
- 電話:010-62316606-806
- 郵箱:fsfhzy666@163.com
- 中國腐蝕與防護網官方QQ群:140808414