摘要:超高強韌鋼同時擁有超高強度和優良韌性,因而在國防和民用工程機械領域中廣泛應用。本文首先綜述了各類型傳統超高強韌合金鋼的典型鋼種、成分、性能及應用和發展歷程,并重點闡述了各典型鋼種的組織和強韌化機理;然后介紹了近年所研發的具有代表性的新型超高強韌鋼的成分、組織、強韌化機理及力學性能;接著梳理了我國近年來由于快速發展的經濟需求和地理、資源等特點,出現了對現役超高強韌鋼進行升級換代的迫切需求,包括新型輕質裝甲防護鋼、大型球磨機用鋼、高山隧道挖掘的盾構機刃具用鋼以及石油工程機械中的高壓壓裂泵用鋼等;最后介紹了作者團隊近期在超高強韌鋼的一些最新研究成果,并據此提出超高強韌鋼未來發展的思路。
關鍵詞: 超高強鋼 ; 韌性 ; 析出強化 ; 馬氏體 ; 殘余奧氏體
超高強韌鋼一般是指屈服強度大于1300 MPa,抗拉強度大于1500 MPa的合金鋼[1]。從20世紀40年代初期起,美國海軍為了節省造船費用而最先開始研發以能夠代替普通鋼,滿足強度和韌性要求,同時焊接性能良好的超高強度低合金鋼[2,3]。多年以來,超高強韌鋼已被廣泛應用于冶金、礦山、工程機械、電力、造船、國防等各工業領域的關鍵承力和受壓構件中。超高強韌鋼除了對高強度的要求外,還要有足夠的韌性、疲勞抗力以及根據服役工況條件所要求的抗腐蝕性和抗蠕變等其它要求。但是,超高強韌鋼的性能顯著受化學成分、加工過程、內在顯微結構特征、溫度、載荷性質、甚至材料在使用過程中所處的實驗環境等因素的影響。在一些代表高新技術和新型材料應用的關鍵領域,例如飛機起落架用鋼、高端軸承鋼、高壓柱塞泵用鋼和火箭發動機用高強度不銹鋼等均屬于超高強韌鋼[4],而這些鋼種目前國內生產技術和質量控制不穩定,會出現非金屬夾雜、內部裂紋、使用壽命低等問題,嚴重限制了其使用。從改善環境、節約能源和提高國產超高強韌鋼的整體質量方面考慮,降低合金含量,盡可能地降低生產成本,是鋼鐵材料領域的一個重要研究方向。本文從超高強韌鋼的分類及主要工程應用、超高強韌合金鋼的最新發展等幾方面進行論述,并且對超高強韌鋼目前存在的問題進行討論和展望。
1傳統超高強度高韌性合金鋼分類及應用
按照化學成分及組織性能的不同,傳統超高強度合金鋼可以劃分為:低合金中低碳馬氏體超高強度鋼,中、高合金二次硬化超高強度鋼,超低碳馬氏體時效超高強度鋼以及沉淀硬化超高強度不銹鋼[5,6,7,8,9,10]。
表1[7,10,11,12,13,14,15,16,17,18,19,20,21,22,23,24,25,26,27,28]為典型的傳統超高強度合金鋼的化學成分,下面按類別分別討論。
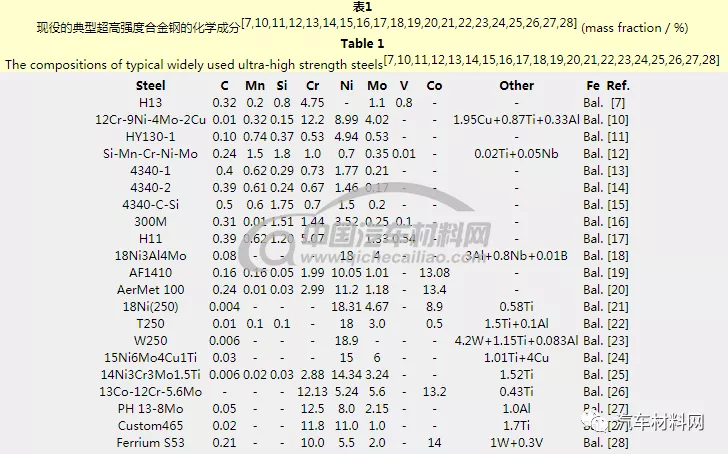
1.1 低合金超高強韌鋼
低合金超高強韌鋼是在調質鋼的基礎上發展起來的合金鋼,合金元素含量較低(不超過5%,質量分數,下同),其作用是保證鋼擁有高的淬透性,提高馬氏體的抗回火穩定性和抑制奧氏體晶粒長大,通常鋼中加入的合金元素有Cr、Ni、Mo、Si、Mn和V等。C含量一般在0.25%~0.60%之間,C含量低于0.25%時,鋼的塑性較好,但是強度達不到超高強度的要求;C含量高于0.60%后,鋼的強度很高,但是韌性很差而不能廣泛應用,同時C含量過高也嚴重惡化了鋼的焊接性能。低合金超高強韌鋼的熱處理制度為淬火加低溫回火或等溫淬火工藝,熱處理后得到如圖1[12,29]所示典型的回火馬氏體與細小彌散碳化物組織,因而具有超高的強度和適當的韌性。由于低合金超高強韌鋼的合金元素含量低、成本低、生產工藝簡單,因而廣泛應用于制造飛機起落架、發動機軸、高強度螺栓、固體火箭發動機殼體和化工高壓容器等領域。
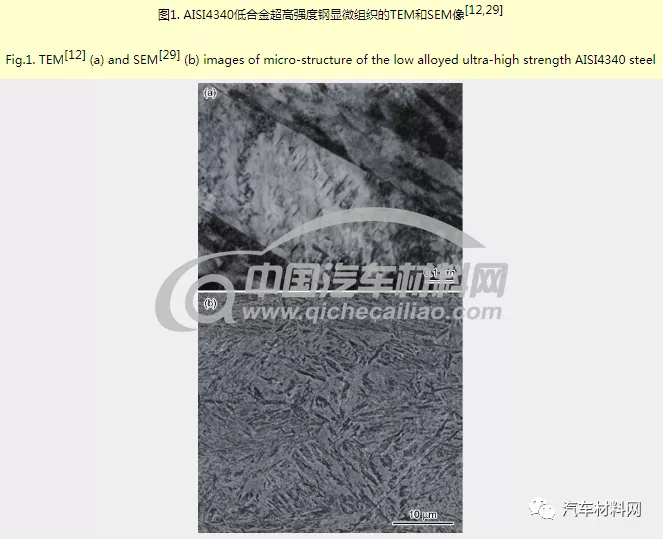
美國的AISI4130、AISI4140和AISI4340系列合金鋼是早期低合金超高強韌鋼的典型代表[29,30,31,32]。其中AISI4130是最早研發的超高強度合金鋼,為了獲得最好的強韌匹配,常將該鋼進行調質處理,但由于其屈服強度和抗拉強度分別為880和980 MPa,強度不能滿足超高強度合金鋼的要求,所以在4130鋼的基礎上繼續提高C含量至0.4%,同時加入少量的Ni和Mo元素,形成了4340鋼。之后開發的大多數低合金超高強韌鋼都是在AISI4130和AISI4340系列合金鋼的基礎上不斷改進的。因為低合金碳鋼C含量較高,導致其淬火后強度很高,但是塑韌性很差。因此,Krauss[33]對馬氏體碳鋼和低合金碳鋼進行了低溫回火處理(150~200 ℃)。結果表明,由含C量決定的低溫回火馬氏體的強度與馬氏體晶體中位錯和過渡碳化物的動態加工硬化有關。在含0.5%C的鋼中,當回火馬氏體基體中第二相粒子分散時,韌窩在其上形成并導致塑性斷裂。含0.5%C以上的低溫回火馬氏體鋼中,容易在原始奧氏體晶界發生脆性沿晶斷裂。所以,低合金超高強度鋼中的C含量一般不要超過0.5%,并且為了提高其韌性,一般要進行適當的低溫回火處理。為了進一步提高低合金超高強度鋼的韌性,Chang和Smith[34]研究了Si元素對馬氏體回火硬度及顯微組織的影響,發現了Si元素對低合金超高強度鋼的有利作用,為300M鋼的研發奠定了基礎。1952年,美國國際鎳公司開發設計了300M鋼[6],它是在AISI4340鋼的基礎上添加1.5%~2.0%的Si元素,并略微調整V含量而發展起來的。300M鋼可以在較高的溫度區間進行回火而不降低強度,擴大了回火溫度范圍,抑制了馬氏體的回火脆性。因為300M鋼擁有超高的強度、適當的塑性和一定程度的耐腐蝕等性能而被廣泛用作飛機起落架和壓力容器用鋼,但服役時常面臨含Cl-的環境,會導致應力腐蝕開裂。因此腐蝕行為的研究是300M鋼今后的研究重點[35]。
我國從20世紀50年代起開始了低合金超高強韌鋼的研發。目前國內外主要低合金超高強韌鋼的力學性能如表2[11,14,30,32,36,37,38,39,40]所示。從最初20世紀70年代仿制美國AISI4340鋼、300M鋼[36],到根據我國實際的資源情況自主研發的30CrMnSiNi2A鋼,之后的45CrNiMo1VA鋼[37,38]等,到無Ni、Cr的35Si2Mn2MoVA鋼,無Ni的406鋼和40CrMnSiMoVA鋼[39,40,41]等,我國低合金超高強韌鋼的發展經歷了從無到有,從仿制到研發,從低端到高端的歷程。
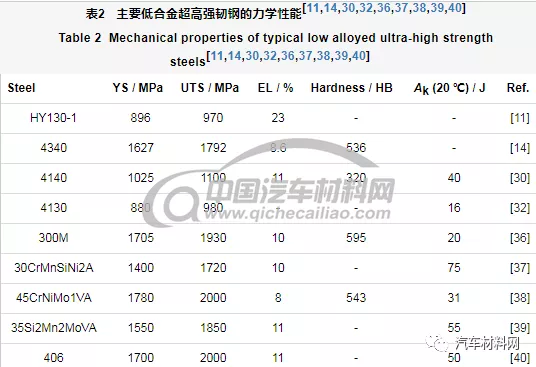
1.2 中、高合金二次硬化超高強韌鋼
二次硬化鋼是指含有Cr、Mo、V、Ti和Nb等碳化物的合金鋼,通過淬火后的馬氏體在500~600 ℃之間回火時,硬度不僅不降低反而升高的二次硬化機理進行強化。用這一機理研發了多種性能優良的超高強度合金鋼,如中溫超高強度合金鋼38Cr2Mo2VA(GC-19)[42],可用作飛機主承力框架等構件。但是,中合金超高強韌鋼與低合金超高強韌鋼有類似的缺點,即斷裂韌性(KIC)不高和抗應力腐蝕能力差,不能完全滿足現代航空航天材料和高壓容器的要求。高合金超高強韌鋼中含有較多的Ni和Co元素,可以在顯著提高硬度的同時提高韌性,如高合金超高強韌鋼AF1410和AerMet 100鋼通過分別加入10%以上的Ni和Co合金元素[20,43]獲得了高強度、優良的疲勞抗力和應力腐蝕開裂抗力,可以替代現有用在制造航空受力件、輪船主軸等大型承力構件上的超高強度合金鋼,可減輕質量并延長使用壽命。用AerMet 100鋼替代300M鋼做飛機起落架,可以克服300M鋼的低斷裂韌性和對應力腐蝕開裂敏感等缺點。目前常見的二次硬化超高強韌鋼的力學性能如表3[20,42,43,44,45,46]所示。

二次硬化超高強度合金鋼的高強度是由合金馬氏體在高溫回火時合金碳化物的脫溶與殘留奧氏體的二次淬火共同提供的,鋼中典型合金碳化物的顯微形貌如圖2[47]所示。Morikawa等[48]研究表明,回火時合金碳化物在析出過程中的組成是不確定的,其點陣常數隨合金化學成分而改變并影響碳化物與基體的共格關系。當二次硬化達到最大時,鋼的韌性最差;而過時效可以顯著提高鋼的韌性但導致鋼的強度明顯降低。但通過合理的化學成分配比和仔細調整熱處理工藝,可以使二次硬化鋼的強度和韌性同步增加,如Speich等[49]發現,往Fe-Ni-Mo-C鋼中添加Co可以提高M2C的形核率,細化M2C,同時抑制了回火過程中形成逆轉變奧氏體,既增強了固溶強化也提高了韌性。當二次硬化鋼10Ni-Cr-Mo-Co中粗大的滲碳體完全被細小的(Mo, Cr)2C取代后,可以獲得最高的韌性。對之后開發的AF1410和AerMet 100鋼深入研究[8,50]表明,二次硬化反應與析出高共格的細小針狀六方結構合金碳化物M2C密切相關,用Cr取代M2C中的Mo使M2C晶格常數變小,并與基體接近,進而獲得了更好的共格程度,提高了強韌性。
但AF1410鋼中含有大量的Ni和Co元素,合金成本昂貴,且在鑄造和鍛造時易發生偏析和組織不均勻,造成材料浪費。因此近幾年來迅速發展的激光增材制造(LAM)[51]是該類型鋼加工技術的未來趨勢,能夠實現構件的近凈成形,節約材料的同時還可以縮短生產周期,從而降低生產成本。目前,LAM技術已經成功用于多種金屬材料構件的制備。例如,采用LAM技術成功制備了AF1410鋼厚板試樣,激光增材制造沉積態組織具有定向凝固組織特征,表現為沉積方向生長的胞狀柱晶,且此時硬度相對較低,只有350 HV左右。經過后續熱處理后,組織得到細化,獲得了細小的回火馬氏體組織,強度和塑性與相同熱處理條件下的鍛件性能相當。
1.3 馬氏體時效超高強韌鋼
馬氏體時效超高強度合金鋼是以無碳(或微碳)馬氏體作為基體,時效時能產生金屬間化合物析出強化的超高強度合金鋼。具有工業應用價值的馬氏體時效鋼,是20世紀60年代初由國際鎳公司首次研發的。該公司在Fe-Ni馬氏體合金中加入不同含量的Co、Mo和Ti,通過時效硬化得到屈服強度分別達到1400、1700、1900 MPa的18Ni(200)、18Ni(250)和18Ni(300)鋼,并首先將18Ni(200)和18Ni(250)應用于火箭發動機殼體[52],典型馬氏體時效超高強韌鋼的力學性能如表4[18,21,22,23,24,25]所示。在含Co馬氏體時效鋼中,Co雖然固溶于馬氏體基體但并不形成金屬間化合物,它主要促進含Mo金屬間化合物的析出[53]。通過影響位錯亞結構,為析出相提供均勻的形核位置,進而促進析出相粒子細小彌散分布,達到明顯的析出強化效果。例如,Duan等[54]研發的CM400馬氏體時效鋼中含有15%Co,可以獲得高達2.4 GPa的抗拉強度,但是只有3%的延伸率,限制了CM400鋼的廣泛使用。為了改善其塑性,可以對鋼板表面進行噴丸處理,使其斷裂形核位置由表面集中點向亞表面與試樣內部分散轉移,噴丸處理之后,鋼板的屈服強度略有提高,抗拉強度不變,延伸率提高到4%以上。
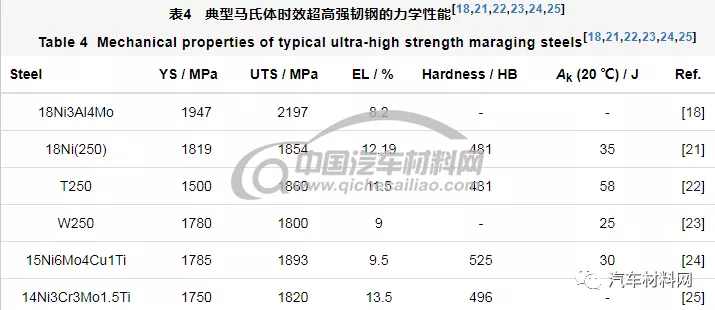
馬氏體時效超高強度合金鋼在相同的強度級別下擁有比低合金超高強韌鋼更高的韌性,加工硬化指數低,沒有脫碳和焊接困難等難題,熱處理工藝簡單,冷加工成型性好。但是,常用的18Ni馬氏體時效超高強度合金鋼中含9%的貴重Co元素,由于全球Co資源嚴重短缺,導致Co價格急劇飆升,使含Co馬氏體時效鋼的成本大幅上升,限制其進一步發展和應用。我國Co資源缺乏,因此國內大型固體火箭發動機殼體一般不選用這種材料。20世紀90年代,國內在18Ni馬氏體時效鋼的基礎上,采用取消Co元素,提高Ni和Ti含量的方法,成功仿制出了T250馬氏體時效鋼[22]。T250抗拉強度為1760 MPa,屈服強度大于1655 MPa,斷裂韌性大于80 MPa·m1/2,是制造我國固體發動機殼體的新一代材料。除了已經用于工程材料上的T250鋼,我國還在積極研究強韌性更高的無Co馬氏體時效鋼,何毅等[55]研發的T350無Co馬氏體時效鋼經過適當的熱處理后,其屈服強度達2050 MPa,抗拉強度達2150 MPa,同時擁有近10%延伸率和70 MPa·m1/2的斷裂韌性,該性能達到了18Ni(300)型含Co馬氏體時效鋼的同等水平。
低、中合金超高強韌鋼的缺點是KIC不高和抗應力腐蝕能力差,馬氏體時效超高強度合金鋼則打破了以C作為主要強化元素的傳統做法,而以Ni為主要合金元素形成韌性的Fe-Ni基馬氏體,通過Co、Mo和Ti等強化合金元素,時效時從過飽和固溶體中析出合金化合物作為第二相質點來實現強韌化。雖然馬氏體時效超高強度合金鋼有很多的優點,但是也有彈性模量低、剛性不足、抗疲勞性能低于300M鋼等缺點。而且,馬氏體時效超高強度合金鋼化學成分的微小變化都會顯著影響析出相的析出行為。例如,當減少馬氏體時效鋼中Co的使用量時會惡化二次相析出的動力學,進而降低韌性[56],引起力學性能的很大波動,所以限制了它的廣泛應用。為了克服這一缺點,可以在鐵素體/馬氏體鋼中析出納米共格的NiAl析出相,這種具有較小晶格錯配度的二次相可以獲得優良的機械性能[18]。
1.4 沉淀硬化超高強度不銹鋼
為了提高超高強韌鋼的耐腐蝕性能,在馬氏體時效超高強韌鋼的基礎上開發出了含Cr大于12%的沉淀硬化(PH)超高強度不銹鋼。它們是含有較多的Cr和Ni以及一定量的Mo、Co、Ti、Ni和Al等合金元素的超低碳合金鋼,通過馬氏體相變和時效強化獲得優異的綜合性能,典型沉淀硬化超高強度不銹鋼的力學性能如表5[27,28,57,58]所示。該系列鋼具有強度高、斷裂韌性高、焊接性好、易加工、高耐蝕性等優點,在空軍、航空航天等許多工程領域得到廣泛應用。沉淀硬化超高強度不銹鋼的高強度和良好的韌性來自于馬氏體基體上均勻、細小分散的金屬間化合物(NiAl、Ni3Ti、Laves相)的析出作用。這些細小的析出相在高溫淬火之后中溫(400~600 ℃)時效時析出。依據合金成分的不同,細小析出相的類型也不同。例如,PH 13-8 Mo沉淀硬化不銹鋼[59]在400 ℃以上時效時會析出B2型超點陣結構的β‘-NiAl相,這種析出相的晶格常數是0.2887 nm,與鐵素體的晶格常數(0.28664 nm)非常接近,所以NiAl析出相與基體即使在長時間時效后依然保持共格關系。Custom465鋼[60]在510 ℃時效后,馬氏體基體上彌散析出與基體半共格hcp結構的Ni3Ti相,同時少量逆轉變奧氏體起到提高塑韌性的作用,最終獲得抗拉強度高于1800 MPa的優良性能。
第一代沉淀硬化不銹鋼(PH 17-4、PH 15-5[57,58])的強度一般為1300 MPa左右,并不能很好地滿足某些領域對超高強度的要求。所以主要用于制造耐腐蝕的高強度部件,如噴氣發動機壓氣機機匣及大型汽輪機末級葉片。在此基礎上,提高Ni和Al含量開發了第二代中高強度沉淀硬化不銹鋼(Custom465),盡管第二代沉淀硬化超高強度不銹鋼的耐腐蝕性能優于一般的超高強度高韌鋼,但是其合金元素Cr、Ni含量較高,導致材料成本較高。為了解決這一矛盾,Kuehmann等[28]通過計算機輔助成分設計研發了新一代的沉淀硬化超高強度不銹鋼Ferrium S53,新的超高強度不銹鋼中Cr和Ni含量分別下降至10%和5.5%,適當提高了C和Co的加入量。通過析出硬質M2C型納米共格析出相強化馬氏體基體,達到了與300M鋼相同的強度級別,同時又具備優于300M鋼的耐腐蝕性能。
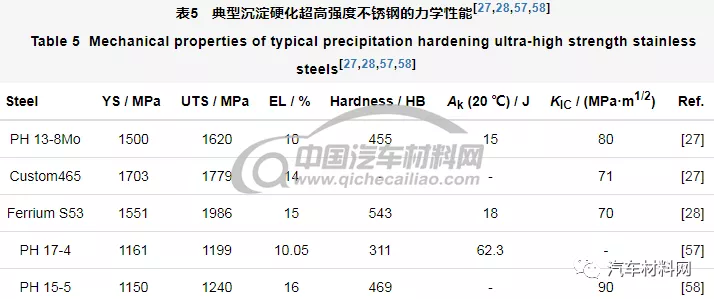
近年來,國內在超高強和高斷裂韌性馬氏體時效不銹鋼方面也進行了大量研究并取得了突出的成果。例如,Li等[61]研發的13Cr-12Co-3.5Mo-4Ni-0.5Ti馬氏體時效不銹鋼,通過時效過程析出的Ni3(Ti, Al)、富Mo的R’相和富Cr的α‘相,共同起到析出強化的作用,最終獲得1649 MPa屈服強度、1928 MPa抗拉強度、10%延伸率和83.6 MPa·m1/2斷裂韌性的力學性能。Tian等[62]研發的13Cr-8Ni-7Co-3Mo-2Ti馬氏體時效不銹鋼,在480 ℃時效不同時間后,析出納米尺寸的Ni3Ti和富Mo相,其達到了1920 MPa抗拉強度和80 MPa·m1/2的斷裂韌性,同時,耐腐蝕性能優于PH 15-5鋼。
1.5 傳統超高強高韌鋼存在的問題
低合金超高強韌鋼的優勢在于其經濟實用、制備工藝簡單。但是室溫下工作的大受力構件方面的要求逐漸增高,此類鋼的一些不足之處就逐漸顯露出來,一方面是韌性不足,另一方面是耐蝕性不夠。隨著強度的升高,塑性、韌性不斷下降,應用過程中鋼鐵材料常發生脆性失效。所以目前傳統的低合金超高強度合金鋼已經無法滿足關鍵工程領域的高要求。如何在提高強度的同時,改善塑韌性和耐應力腐蝕性,同時還要成本經濟性,這是研發新型低合金超高強韌鋼的熱點和難點。另外,低合金超高強韌鋼是中碳鋼,熱處理過程中存在嚴重的脫碳傾向,并且C含量過高嚴重惡化鋼板的焊接性能。因此,如何選擇合適的熱處理工藝尤為重要。
與傳統低合金超高強韌鋼相比,馬氏體時效鋼,中、高合金二次硬化鋼及沉淀硬化超高強度不銹鋼擁有很高的強度、韌塑性、疲勞抗力和良好的耐蝕性。但是,由于鋼中添加了大量的Cr、Co、Ni和Mo等貴重合金元素,使鋼的生產成本大幅度提高。同時由于鋼中加入的大量合金元素降低了鋼液的流動性,很容易在澆注過程中發生合金元素的偏析,造成成分不均勻,使鋼板在工程應用中發生開裂。為了避免鋼中合金元素的大量偏析,通常需要增加鋼水冶煉次數或者延長熱處理時間使成分均勻,這就顯著增加了能耗,降低了生產效率。開發新的冶煉工藝和改進熱處理方法是中、高合金超高強韌鋼今后的研究熱點和難點。
2新型超高強度高韌性合金鋼的發展
2.1 新型馬氏體時效超高強韌鋼
傳統馬氏體時效鋼中的析出相主要為六方晶系的η-Ni3Ti和正交晶系的δ-Ni3Mo,這2種析出相和周圍馬氏體基體是半共格或者非共格的,由于在半共格或非共格臨界形核形成過程中所需要的界面能較高,所以η-Ni3Ti和δ-Ni3Mo趨向于在顯微組織中的特殊位置非均勻形核,例如晶界、位錯、層錯或其它晶體缺陷處。析出相和基體之間較大的差異雖然能提供較高的強度,但是也促使材料在加載過程中容易過早萌生裂紋或者造成局部應力集中,這將嚴重惡化材料的整體塑性,而析出相和基體結構上過大的差異必然導致析出過程存在高的形核勢壘,最終致使可以起到強化作用析出相的密度降低。因此,傳統方法通過添加大量貴重合金元素,在高位錯密度的板條馬氏體基體內部析出大量納米半共格析出相的方法已經達到了馬氏體時效超高強度合金鋼的性能上限,成為馬氏體時效超高強韌鋼進一步發展的限制。
Jiang等[18]通過創新合金設計理念,實現高密度和最小晶格錯配度Ni(Al, Fe)共格納米粒子的析出強化,使新一代馬氏體時效超高強韌鋼的研究取得了突破,該鋼的抗拉強度達到2.2 GPa,延伸率達到8%。該鋼最大限度地減小了析出相與基體的點陣錯配度(0.03%±0.04%),并引入“有序效應”作為主要的強化機制,顯著降低了析出相的形核勢壘,促進高密度和良好熱穩定性的析出相均勻彌散分布。同時,這種共格度極高的界面可以有效緩解析出相粒子周圍的微觀彈性畸變,改善材料宏觀均勻塑性變形能力。另一方面,析出相可以有效阻礙位錯切過,從而獲得綜合性能優異的新型馬氏體時效超高強韌鋼。在該鋼中,采用Al元素代替合金元素Co和Ti等,不僅降低了材料成本,而且Ti的去除允許合金中添加一定量的C元素并以碳化物的方式起到協同強化作用,這也將有效簡化新型馬氏體時效超高強韌鋼的制備和精煉過程,擴大馬氏體時效鋼的工程應用范圍[63]。
2.2 超高強高韌納米貝氏體鋼
貝氏體鋼是一種具有較高強度和良好韌性的鋼種,納米貝氏體鋼的出現吻合了鋼鐵材料不斷提高強度和韌塑性的趨勢。英國劍橋大學Bhadeshia和Edmonds[64]利用Si對碳化物析出的抑制作用,發現了超級納米貝氏體的優異強韌性,這種貝氏體鐵素體板條中間不是析出碳化物而是殘余奧氏體薄膜,這樣的組織結構決定了其具有超高強度和良好的韌性匹配。納米貝氏體鋼的抗拉強度為1.77~2.20 GPa,甚至可高達2.5 GPa,屈服強度高達1.5 GPa,延伸率為5%~30%,斷裂韌性可達40 MPa·m1/2 [65]。但是當納米貝氏體鋼的強度在2000 MPa時,塑性超10%,韌性達10 J左右,保持高強度的同時提高其韌性是納米貝氏體鋼需要繼續改進的方向。超級貝氏體鋼的合金元素設計,首先是顯著推遲珠光體和鐵素體轉變,同時降低貝氏體和馬氏體開始轉變溫度,而且使2個轉變溫度之間的溫度差擴大,保證進行貝氏體轉變而不發生珠光體與馬氏體轉變,得到以貝氏體為主的組織。在超級貝氏體鋼的典型合金成分中,C含量較高(0.78%~0.98%),目的是降低貝氏體轉變溫度,得到納米級貝氏體鐵素體板條組織;含較多的Si (1.5%)以阻礙滲碳體析出;另外添加適量的Mn、Mo、Co或Al元素,起到提高組織淬透性、消除回火脆性、增加奧氏體向貝氏體轉變的驅動力和加速貝氏體相變的作用。
如圖3[66]典型納米貝氏體顯微結構所示,超級貝氏體鋼在125~300 ℃的低溫貝氏體區間長時間等溫(1~60 d)后,獲得20~100 nm的貝氏體鐵素體板條和板條間富C的薄膜狀殘余奧氏體,殘余奧氏體分數一般不小于20%。由于超級貝氏體組織中的貝氏體鐵素體為納米級,且處于C過飽和狀態,故起著強烈的細晶強化和固溶強化作用;同時,貝氏體鐵素體中存在較高的位錯密度,故有一定的位錯強化作用。超級貝氏體組織具有良好的塑性和韌性,一方面與貝氏體鐵素體板條的位錯亞結構有關,但最主要的原因是貝氏體鐵素體板條間的薄膜狀殘余奧氏體,在高的應力作用下會發生馬氏體轉變,可以有效提高材料的塑韌性,其薄膜狀的形態分布又增強了對裂紋的吸收效應。
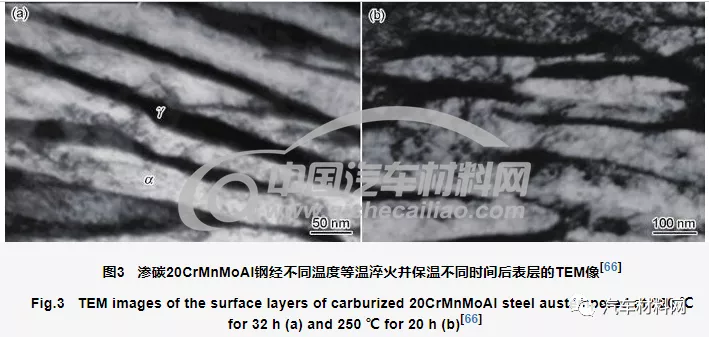
2.3 高位錯密度誘導大塑性變形-配分鋼
一般而言,鋼鐵材料隨著強度的不斷升高塑性逐漸下降,當強度達到2 GPa以上時,延伸率通常不超過10%,這幾乎是傳統鋼鐵材料強塑性平衡的極限。以前通過晶界和共格孿晶界的細化解決這一矛盾,但是當晶粒尺寸細化到一定尺度時,不僅僅強度將達到極限同時也由于塑性失穩導致塑性嚴重惡化。位錯可能是解決這一問題的另一個途徑,但是根據經典Taylor強化公式[71]可知,金屬材料的強度隨位錯密度單調增加,但是塑性隨著位錯增加而降低。但是如果存在高密度的可動位錯時,情況將有所不同。He等[72]開發了一種廉價的中錳超級鋼,鋼的化學成分為10Mn-0.47C-2Al-0.7V,不含任何Cr、Ni和Mo等貴重合金元素。將中錳鋼經熱軋、溫軋、兩相區退火、冷軋加低溫回火的工藝處理后,形成亞穩奧氏體板條嵌在高位錯密度馬氏體基體中的顯微組織,馬氏體中的總位錯密度高達1.27×1016 m-2,這種獨特工藝下獲得的馬氏體要比傳統淬火馬氏體中的位錯密度高出約2個數量級。因此,在變形時,高密度的位錯不僅僅通過位錯增殖和交割提供顯著的加工硬化從而獲得超高強度2.2 GPa;同時由于大量可動位錯的滑移并結合殘余奧氏體的相變誘導塑性(TRIP)和孿晶誘導塑性(TWIP)效應的共同作用獲得了可觀的塑性,延伸率達到16%。該鋼的工程應力-應變曲線如圖4[72]所示,這成功突破了強度和塑性的相互制約關系。這種通過將成分與加工工藝進行創新設計,獲得高密度可動位錯并結合殘余奧氏體的組織,有望用于設計新一代的超高強高韌合金鋼。
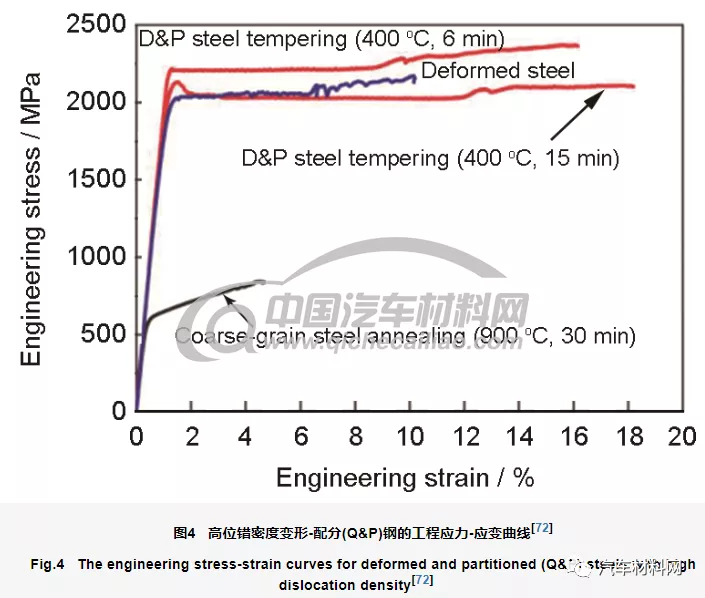
2.4 復合析出納米相超高強韌鋼
鋼中析出相與位錯的相互作用會產生很強的析出強化作用,析出相粒子對位錯的釘扎作用如圖5所示,主要有2種機制(切過機制和繞過機制)。當析出相尺寸小,與基體保持共格時,位錯切過析出相;當析出相不斷長大,與基體脫離共格關系時,位錯繞過析出相。超高強韌鋼經固溶時效后產生的金屬間化合物一般與基體保有良好的共格度,屬于切過粒子,而鋼中的碳化物、氮化物及粗大的析出相一般都是繞過粒子。傳統超高強韌鋼中的析出相多為合金碳化物、單相半共格或非共格的金屬間化合物,這樣的析出相雖然能夠提供很高的析出強化效果,但是由于弱的共格性一般都會導致鋼的韌性較差。所以可以通過析出金屬間化合物取代合金碳化物或者改變金屬間化合物的種類與配比來減小其與基體的錯配度,從而達到提高材料強度的同時增加塑韌性的目的[73]。但是,想要獲得共格度非常高的析出相,尤其是當要獲得極高的強度和韌性匹配時,往往需要對化學成分和加工工藝提出嚴苛的要求[18]。此時采用2種及以上析出相的復合強化,就成為一個可行的選擇。近年來典型超高強韌鋼中復合析出納米粒子種類如表6[61,74,75,76,77,78,79,80]所示,相對于單一類型納米析出相,采用復合析出的方法,可以將具有不同成分、晶體結構和微觀力學特性的多種析出相協同結合,產生超過納米析出相單獨加入鋼中產生的強韌性作用。
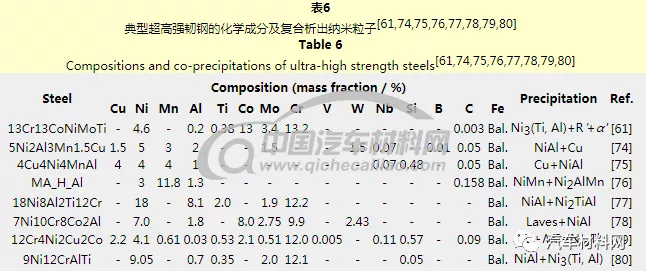
復合析出納米粒子強韌鋼要求精確控制各種納米析出相的尺寸、數量和空間分布。有2組納米析出相粒子的晶體結構與bcc-Fe基體有很高的共格性[81]:一組是bcc結構或者bcc結構的派生結構,例如bcc-Cu、B2-NiAl、L21-Ni2AlTi和Ni2AlMn;另一組是hcp結構,例如Ni3Ti和Mo2C。第一組的共格性是通過納米析出相與bcc-Fe基體在立方體平面上的近似重合實現的,而第二組的共格性是通過納米析出相的密排方向和bcc-Fe基體的立方體方向近似重合實現的。相反,非共格析出相,例如Fe3C、FeCr、Fe2Mo和Fe7W6通常析出尺寸很大,沒有有效的強化效應甚至因為在晶界析出引起材料脆斷,所以超高強度高韌合金鋼中應該盡可能避免出現此類非共格析出相[28,82]。近年來通過計算機輔助合金設計、納米結構表征方法的進步,人們研發出多種復合析出納米共格粒子的超高強度高韌性合金鋼。例如,Jiao等[74]研發的Fe-Cu-Ni-Al基超高強度合金鋼,通過納米尺寸的NiAl和Cu粒子的復合析出起到強化作用,展現出了1.9 GPa抗拉強度,10%延伸率的優良力學性能。Kapoor等[75]研發的Cu-Ni-Mn-Al基超高強低碳合金鋼中,通過Cu和NiAl的復合析出強化,獲得了最高1600 MPa的屈服強度。盡管Cu/NiAl復合析出相在很寬的成分范圍內都可以形成,但是依據Cu/Ni和Cu/Al比的不同,復合析出物的析出機制非常不同,有2個主要的析出路徑。如圖6a所示,當鋼中含有較多的Cu和相對較少的Ni和Al時,含少量Ni和Al的富Cu粒子首先在過飽和固溶體內形核,核內主要是Cu,隨析出相的不斷長大,Ni和Al不斷偏聚在Cu和基體之間的界面上,降低Cu析出相的界面能,因此促進NiAl析出相在Cu周圍不均勻析出,導致Cu-NiAl型復合析出相[83]形成。在低的Cu/Ni和Cu/Al配比鋼中,富含大量Ni、Al和Cu的粒子首先在過飽和固溶體中形核,由于Cu在bcc-Fe中幾乎沒有固溶度,很容易溶入NiAl的析出過程。隨著時效過程的進行,先形成的NiAl粒子開始向表面排出Cu,導致不均勻形核的Cu粒子在NiAl表面產生,因此形成NiAl-Cu型復合析出相。
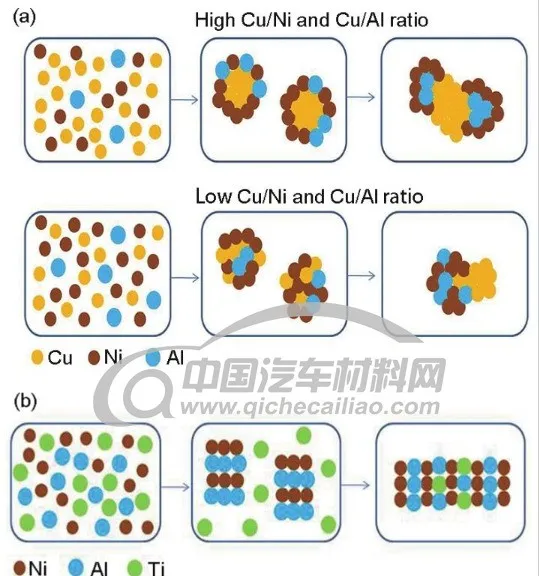
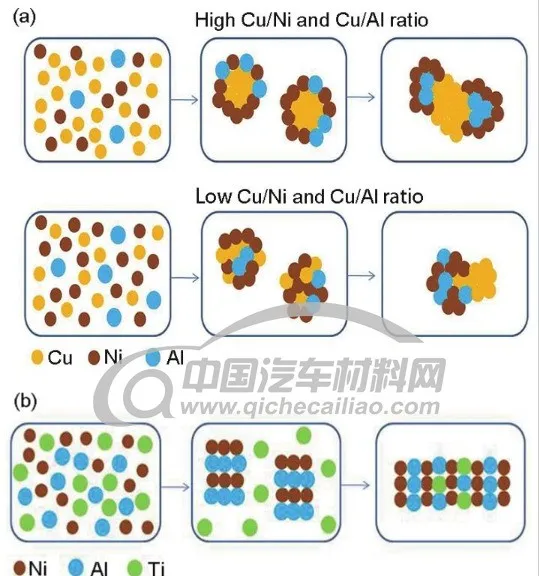

Millán等[76]研發的Fe-Mn-Ni-Al型超高強度合金鋼,通過向鋼中加入適量的Mn和Al后可以將鋼中的Ni含量降至5%以下,產生新一代的低成本超高強韌鋼。加入Al后可以生成B2-NiMn和Ni2MnAl復合納米析出相,這2種析出相的含Ni量都要低于Ni3Ti,基體中含有較低的Ni即可形成NiMn和Ni2MnAl納米析出相。同時,2種析出相都是與基體一樣bcc結構的有序相,而且Ni2MnAl析出相和基體的錯配度更低,所以形核半徑更小,導致析出相尺寸更小,數量更多地分散在馬氏體基體上,起到很強的析出強化作用。Liebscher等[77]研發的Fe-Al-Cr-Ni-Ti鐵素體基合金鋼,因為較低的成本、小的熱膨脹、良好的抗氧化性和高的熱傳導性作為高溫結構用鋼。鋼中主要通過析出B2-NiAl和L21-Ni2AlTi復合分層析出相起到強化作用。在時效的早期階段主要析出B2-NiAl析出相,隨著時效時間的增加,在B2-NiAl析出相的內部逐漸形成L21-Ni2AlTi析出相,最終析出分層分布的復合納米析出相,復合納米析出相的析出過程如圖6b所示。
Sun等[78]最近研發了一種擁有超高強度和耐500 ℃蠕變性能的Al-Co-Cr-Ni-Mo基超高強度馬氏體時效鋼,作為噴氣發動機中的低壓渦輪軸的材料。通過復合析出納米尺寸的金屬間化合物Laves相和β-NiAl析出相強化,得到室溫屈服強度大于1800 MPa,抗拉強度大于2000 MPa,延伸率達8%和700 MPa下蠕變斷裂壽命大于2000 h的優良綜合性能。與傳統馬氏體時效鋼利用Ni3Al析出相提高強度不同,新的超高強韌鋼含較少的Ni,通過2種納米尺寸金屬間化合物共同起到強化作用,B2型超點陣結構的NiAl和密排拓撲結構的Laves相提供了高強度和良好的抗蠕變特性。在該鋼中,奧氏體化溫度和時效溫度是決定其顯微結構演變和力學性能的關鍵因素,大量初生Laves相在較低的奧氏體化溫度下(825 ℃)沿原始奧氏體晶界和奧氏體晶內的孿晶界析出,并在時效過程中始終長大,隨著時效時間的增加,二次Laves相的強化增量也在增加[78]。β-NiAl析出相在時效初期開始發生粗化,強化機制逐漸由切過向Orowan繞過轉變;時效溫度的微小差別(20 ℃)雖然對β-NiAl化學成分的影響很小,但會對其空間分布特點產生顯著的影響。所以為了獲得良好的綜合力學性能,仍然需要對熱處理工藝進行仔細設計[78]。
除了在超高強韌鋼中復合析出2種納米析出相共同強化基體外,Xu等[79]還研究了在Cr-Ni-Cu-Ti-Nb超高強韌鋼中通過復合析出MC碳化物、Cu粒子和Ni3Ti 3種納米析出相共同起到強化作用。超高強韌鋼經過奧氏體化和淬火后得到完全馬氏體基體,在500 ℃時效24 h后基體內部析出了復雜的析出相:尺寸在100~300 nm之間均勻分布的(Ti, Nb)C碳化物,非常細小分散的10 nm球形Ni3Ti和一些小于10 nm且具有孿晶結構的Cu粒子。正是由于多種析出相的復合強化能力和相對較慢的析出動力學,超高強韌鋼在500 ℃時效24 h后才能獲得1.6 GPa的抗拉強度和9%延伸率的良好性能組合。
以上這些復合析出共格納米粒子強化鋼明顯優于前面提到的典型超高強韌鋼,擁有高強度和韌性的良好匹配。但是目前大部分研究中,共格析出的復合納米粒子多為同一種強化類型(剪切機制),因為可以較容易地在馬氏體回火中實現;但是結合了繞過機制粒子(如碳化物)和剪切機制粒子(如bcc-Cu)的共同析出對提高強韌性有更大的潛力,比如Saha等[84]在設計與開發的新型潛艇用鋼時,通過多級回火實現Cu與Mo2C共同析出強化,在屈服強度達到1100 MPa的同時常溫韌性(Akv)為176 J,這甚至超過了設計目標的韌性值約50%;另外Li等[85]在中錳鋼中實現了細小NiAl相(切過機制)和粗大富Cu相(繞過機制)的共同析出,其耦合析出強化貢獻高達500 MPa左右,要明顯高于單一NiAl相的析出貢獻(390 MPa)。所以同時結合切過機制和繞過機制的復合共格納米粒子強化鋼,預期在工程結構上有更大的應用潛能。
2.5 多相復合顯微組織超高強韌鋼
傳統超高強韌鋼是通過單相馬氏體組織為基體和時效形成納米析出相獲得超高強度,但塑韌性一般都難以繼續提高,這意味著通過單相馬氏體基體組織獲得超高強度和優良韌性的匹配存在瓶頸。當在馬氏體基體組織上引入足量的其它輔助相,形成復合組織時,即馬氏體基體保證了超高強度,而設計引入的其它輔助相則可抑制裂紋萌生和擴展,提高鋼的韌塑性,這是開發超高強韌鋼的另一思路。前文提到的超級貝氏體鋼就是這一思路的成功案例,而近年來經過持續的研發,已經出現了具有雙相甚至三相顯微組織的高強合金鋼。
Raabe等[86]研發了一種低碳中錳(9%~12%)鋼,鋼中含有1%~2%的Ni、Ti和Mo合金元素。鋼板經淬火加時效處理后的顯微組織由馬氏體基體和15%的殘余奧氏體組成,在馬氏體基體上彌散析出大量10 nm大小的Ni3(Ti, Al)析出相。變形后獲得1.5 GPa的抗拉強度和12%的良好塑性,強度和塑性的顯著增加歸因于馬氏體中納米析出相的析出強化和殘余奧氏體TRIP效應的協同作用。Li等[87]研發的40SiMnNiCr鋼經過適當的一步淬火加配分(Q&P)過程處理后獲得2400 MPa的抗拉強度和超過10%的塑性。研究結果表明,經過Q&P處理后合金鋼的強度首先增加,之后隨配分時間的不斷增加開始下降。強度開始下降的原因歸因于奧氏體含量的增加,C過飽和馬氏體的降低,馬氏體中位錯密度的減少以及過度碳化物的大量形成。Wang等[88]研發的Fe-0.5C-1.2Mn-1.2Si-1Ni-0.2Nb鋼,基于Q&P工藝采用了新的淬火-配分-回火(Q-P-T)工藝,經Q-P-T工藝處理后,鋼的拉伸強度超過2000 MPa,延伸率超過10%。Q-P-T鋼的超高強度來自于硬相(馬氏體)與軟相(奧氏體)復合存在的雙峰結構,并伴有細小分散的含Nb碳化物。室溫下穩定存在的殘余奧氏體和馬氏體的軟化共同提高了Q-P-T鋼的延伸率。Qin等[89]基于在Mn鋼中加入Si提高殘余奧氏體穩定性的想法研發了Fe-0.6C-1.5Mn-1.5Si-0.6Cr-0.04Nb鋼。熱軋鋼板正火后經過Q-P-T過程處理獲得抗拉強度達1800 MPa,延伸率超過28%的良好力學性能。
通過調整熱處理工藝,不僅可以得到板條馬氏體與殘余奧氏體組成的雙相顯微組織,還可以得到貝氏體、馬氏體、殘余奧氏體組成的三相顯微組織。例如,Gao等[90]將Q&P或Q-P-T過程與貝氏體轉變相結合,開發出了貝氏體淬火加配分(BQ&P)工藝,并應用于中碳Mn-Si-Cr合金鋼中。在Q&P或Q-P-T過程的最初淬火階段形成無碳化物貝氏體和馬氏體,這些無碳化物貝氏體和馬氏體分離奧氏體晶粒并減小未轉化塊狀奧氏體的尺寸。隨后的配分過程中,馬氏體中C向其周圍未轉化的奧氏體擴散,最終在配分后形成板條貝氏體鐵素體、馬氏體和薄膜奧氏體組成的三相復合組織。BQ&P處理后合金鋼獲得抗拉強度1688 MPa,總延伸率25.2%,-40 ℃沖擊韌性48 J/cm2的良好力學性能。
2.6 新型超高強韌鋼的缺點
與傳統超高強韌鋼相比,新型超高強韌鋼雖然具有前文提到的很多優點,但在制備和研發新型超高強高韌鋼時仍然有各種未解決的問題。例如,納米貝氏體鋼的制備需要在低溫進行長達數天的貝氏體轉變,在實際生產中效率較低。如果想要加快貝氏體轉變,就需要在鋼中加入Cr、Co、Ni等貴重合金元素,這必然會引起生產成本的增加;另外,貝氏體相變所要求的溫度工藝窗口通常較窄,大尺寸工件較難適用。如何在不添加貴重合金元素的前提下通過優化熱處理工藝,縮短貝氏體轉變需要的時間、增大熱處理工藝窗口是今后發展超級貝氏體鋼需要解決的難題。高密度可移動位錯變形-配分鋼中,正確控制每一步變形參數和熱處理工藝是得到高密度可移動位錯的關鍵因素,因此需要難度高的大載荷下軋制和對形變過程進行嚴格設計。對于多相組織鋼和復合析出納米粒子鋼,其化學成分的微小變化都會引起合金鋼的顯微組織構成和復合粒子成分與析出順序的不同。并且與單相顯微組織或析出相相比,多相顯微組織與復合納米析出相之間的相互作用更加復雜,對超高強韌鋼的作用機理還不是十分清楚,這些都是發展新型超高強韌鋼面臨的問題和需要解決的難點。
3中國國民經濟發展對新型超高強度高韌鋼的需求
我國經濟近年來發展非常迅速,尤其是制造業規模已經躋身全球最大,基于中國獨有的地理、資源的國情特色,發展了一批獨具中國特色的軍工和工程機械裝備,它們也對超高強度、高韌性的特種鋼有迫切需求,舉例說明如下。
3.1 輕質超高強裝甲鋼
傳統的超高強裝甲鋼包括瑞典的Armox系列裝甲鋼[91]、美國的MIL系列裝甲鋼[92]及澳大利亞的BISALLOY系列裝甲鋼[93]等。裝甲鋼的化學成分及主要性能如表7[91,92,93]所示。其多為Cr-Ni-Mo系低合金中碳鋼,通過淬火加低溫回火工藝獲得超高強度的馬氏體組織,起到很好的抵御作用。但是傳統裝甲鋼中含較多Cr、Ni等貴重合金元素,生產成本較高,同時淬火馬氏體鋼的韌塑性一般較差,很難在獲得超高強度的同時擁有高的韌塑性,裝甲鋼板經高速子彈沖擊時會發生沖塞破壞,對裝甲和防護人員產生直接的傷害。我國地域遼闊、地形復雜,軍事作戰需要長途跨區域作戰和高的載彈量,都對戰車的輕量化和移動性提出迫切需求,這就要求新一代裝甲防護材料,在提高強度和韌性的同時還需要降低密度,以實現裝甲鋼板輕量化、提高車輛機動性和載彈量,因此需要研發密度更低的、新型輕質超高強韌裝甲鋼。
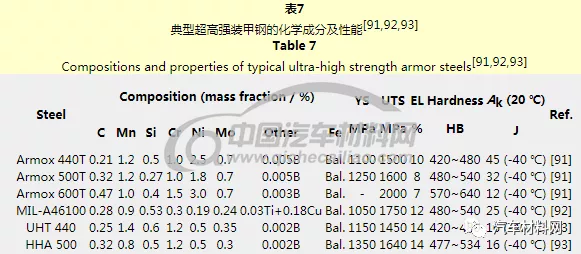
3.2 大型半自磨機用超高強韌耐磨鋼
半自磨工藝由于流程簡單(省去破碎機及篩分設備)、配置方便、投資小而作為現在主要的磨礦工藝在國內外被越來越多的礦山采用。襯板和提升條鋼作為其中主要的受力構件,在半自磨機運作中,提升起的鋼球下落時對筒體內部的襯板產生撞擊,這就要求自磨機襯板和提升條鋼擁有超高的強度、耐磨性和良好的韌性,能夠承受鋼球盡可能多次撞擊不開裂。目前國內外使用的耐磨鋼主要有3大類:奧氏體耐磨錳鋼、低合金高強度耐磨鋼及高鉻系耐磨白口鑄鐵,如表8[94,95,96,97]所示。其中,低合金高強度耐磨鋼具有生產工藝簡單、硬度高(不低于360 HB)、耐磨性好、焊接性能好和易加工等優點,在半自磨機組上廣泛使用。由于常用的半自磨機筒體較小,常在中、低沖擊工況下運轉,所以中碳Cr-Mo系低合金高強度耐磨鋼可以滿足普通半自磨機的工況使用。但是,我國富礦儲量的枯竭,以及對金屬需求的增加,導致需處理的礦石量日益增加,且隨著現代礦山規模的發展,磨機及相應配套設備制造水平的提高,為半自磨設備大型化提供了應用基礎及制造基礎,且為了提高生產效率,自磨機大型化漸成趨勢。目前全球最大的自磨機幾乎多半是在中國生產,如江西耐普生產并在蒙古額爾登特安裝的銅礦半自磨機組,設計規模在1.8×104 t/d。半自磨機直徑高達10 m,在這樣的高度下,由于鋼球的沖擊能量顯著增加,導致現在使用的珠光體低合金高強耐磨鋼服役壽命大幅度降低。曾經嘗試將上述的超級納米貝氏體鋼用于此大型半自磨機組上的半自磨機襯板和提升條,經過實際運行一個月后,提升條均出現明顯開裂,說明該鋼依然不能滿足該服役工況要求,需要研發具備更高韌性的新型超高強度鋼,才能在如此苛刻的工況條件下長時間服役。
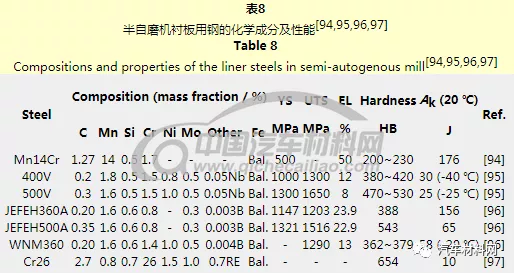
3.3 盾構機刃具用超高強韌鋼
盾構機在地鐵、能源輸送及鐵路交通等重大工程建設中應用廣泛,具有開挖速度快、施工質量高、經濟和環保等優點。作為盾構機關鍵部件之一的盾構刀具,是實現盾構機高效掘進功能的主要部件。因為盾構刀具在掘進破巖時不僅要承受很大的破巖作用力,同時又受到巖石硬礦物相的劇烈磨損,所以盾構刀具用鋼需要具有高硬度、高強度及良好的沖擊韌性,這樣在掘進時盾構刀具既耐磨,又能在遭受巨大沖擊時避免發生崩裂或塑性變形[98]。國內外常見的盾構機刀具用鋼如表9[99]所示,此類鋼多為中、高碳Cr-Ni-Mo系硬質合金鋼,通過二次硬化作用析出大量合金碳化物提高鋼的硬度和耐磨性。
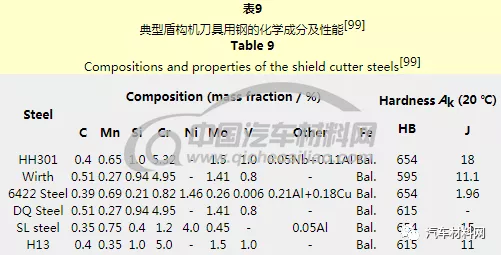
我國幅員遼闊,從沿海地區到高山再到沙漠,各個地區的地質狀況都不一樣,即使同一地區的不同區域,地質狀況也會存在較大差異。在盾構施工過程中,常會遇到各種不同地層,從淤泥、黏土、砂礫層到軟巖及硬巖等,各種地層巖土的物理力學性能相差較大,對刀具的磨損機理不同,相應刀具的性能要求也不同。比如我國西部多山區,含有花崗石類型極硬巖石,刀盤在挖掘隧道推進過程中,由軟地層進入較硬地層的瞬間,會有很高的瞬間載荷,容易使刀具產生崩落、脫落等情況。中鐵工程總公司在實際施工和進行理論計算后均發現盾構機掘進不超過2 km,其盾構刀具既會出現嚴重損壞,須全部更換,即使采用國外進口刃具也于事無補,導致材料費用高昂且工程進度受阻[100]。所以研發超高硬度、耐磨性和優良韌塑性的盾構刀具用鋼尤為迫切。
3.4 壓裂技術采油工藝中壓裂泵液力端用超高強韌鋼
在石油開采中,壓裂技術是目前充分采掘石油儲藏的主要手段。它通過高壓流體壓裂地下深層的巖石,并產生足夠大小的填砂裂縫增加油氣的流動性,是提高油氣采收利用率的一種有效方法[101]。傳統的壓裂泵液力端用鋼主要有4330V[102,103]、4340鋼[13,14]及其衍生鋼42CrMo和43CrNi2MoV[104,105]。如表10[102,103,104,105]所示,常用于油氣壓裂泵液力端鋼屬于高強度鋼,基本滿足30 MPa以下工作壓力的要求。但是近年來,為了緩解我國油氣資源日漸枯竭的現狀,國內石油工業隨之向西部和沿海地區轉移,同時國內汽車使用量逐年增加也加快內陸油氣資源的開采,導致現有的油田淺層油藏已經基本開采殆盡,迫使石油開采向地層深處轉移,這就要求將采油壓裂泵的工作壓力由30 MPa提高到100 MPa以上,這時壓力泵液力端處于高溫高壓、沙粒沖刷和鹽酸腐蝕的惡劣環境下,在超高強低合金鋼表面更易產生裂紋,使得服役壽命從之前低壓工況條件下的1000 h大幅度降低,不足300 h液力端就發生開裂和破壞,導致石油生產成本增高、效率下降[101]。因此,我國石油工程機械設備行業對用于高壓壓裂泵液力端的超高強、高韌和耐腐蝕用鋼有迫切需求。
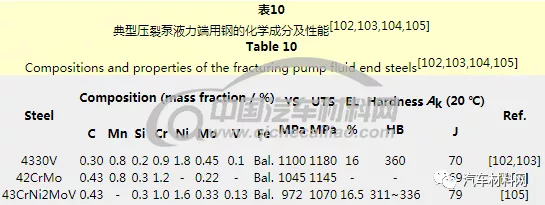
3.5 潛在的解決方案
上述這些鋼種,尤其是大型球磨機、山體隧道挖掘盾構機刀具和高壓壓裂泵液力端所用鋼,一方面要求顯著提升現有鋼鐵材料的強度和韌性水平,形成對材料科學的挑戰;另一方面,這些需求均與我國地理和資源特色相關,是我國國情特色在超高強高韌鋼方面的具體體現,意味著研發這類服務國民經濟的新型鋼鐵材料時,將無國際類似產品甚至類似研究作為參考,必須獨立自主地對成分、組織和制備工藝進行創新。
作者在近年來關于中錳鋼的研究中,發現該類型鋼強度和韌性匹配均很出色,且制備工藝相對簡單,成本經濟。中錳鋼是近年才出現的新鋼種,因為其優越的強度和塑性成為國際鋼鐵材料界的熱門研究對象。當鋼中加入適量的C和Mn元素后,冷卻至室溫然后在馬氏體形成溫度(Ms)點以上溫度配分后,可以獲得馬氏體加適量亞穩奧氏體的雙相組織。馬氏體基體可以保證材料基本的高強度,在變形過程中,亞穩的殘余奧氏體發生TRIP或TWIP作用轉變成馬氏體,應力不斷向未轉變的奧氏體轉移并生成新的馬氏體,所以應力不容易集中,延緩了裂紋的產生和傳播,導致抗拉強度升高的同時提高了延伸率、韌性。中錳鋼中加入適量的鐵素體形成元素Si和Al后,經過化學成分的合理配比,甚至可以在室溫得到由馬氏體基體、δ-鐵素體和殘余奧氏體組成的三相復合組織。多相復合組織與單相馬氏體組織相比,在保證超高強度的同時可以有效分配應力以提高塑性和韌性。
作者團隊基于上述思路,通過對中錳鋼化學成分、加工及熱處理工藝的合理設計,開發出了適合多種應用領域的高強韌和超高強韌中錳鋼。例如,Zhu等[106]發現當在9Mn鋼中加入0.3%V后,在奧氏體鐵素體兩相都析出納米碳化物,導致300~400 MPa的強化增量(圖7a[106])。Hu等[107]利用溫軋工藝取代傳統的熱軋-冷軋工藝,通過部分再結晶獲得不同形狀和尺寸的殘余奧氏體,因此殘余奧氏體晶粒有很寬的機械穩定性范圍;從而能在變形中逐步轉變為馬氏體。最終10Mn-V鋼獲得了超高強度(>1.5 GPa)與足夠延伸率(>15%)的結合(圖7b[107])。
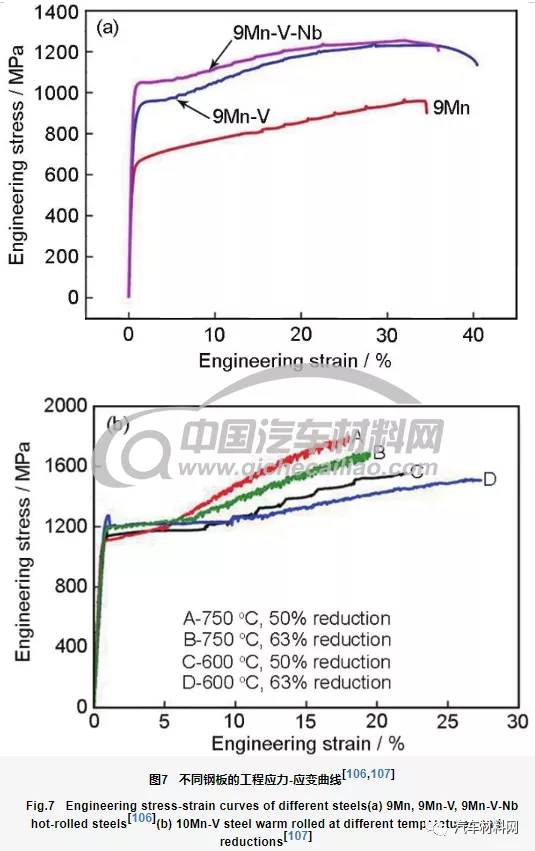
另外,作者團隊近期還研發出新型超高強韌中錳熱軋輕質鋼板。通過合理的成分設計、熱軋和熱處理工藝的仔細制定,得到了由高位錯密度的板條馬氏體、少量高溫δ-鐵素體和殘余奧氏體組成的三相復合層狀顯微組織。鋼中通過復合添加適量的Si和Al元素,成功使熱軋板的密度由7.85 g/cm3降低到7.39 g/cm3,實現鋼板減重近6%,節省燃料的同時也提高了裝甲車輛的機動性。鋼板經熱軋加低溫回火處理后的抗拉強度高達2.1 GPa,延伸率達到13% (圖8a),-40 ℃的沖擊功達到50 J。對鋼板進行冷彎實驗,彎曲壓頭半徑取鋼板6倍厚度,經90°彎曲后表面完好,沒有產生裂紋(圖8b),這表明該鋼板在常溫下冷加工成型性良好。對該鋼板進行防彈實驗,采用53式普通鋼芯彈進行射擊,射擊距離80 m,測試結果如圖8c所示。子彈射擊后鋼板正面產生凹陷,沒有產生可見裂紋。表明新研發的中錳熱軋鋼板能夠有效抵御子彈,用于軍用裝甲和民用防護的相關領域,對裝甲和人員起到很好的防護作用。這一新型超高強韌鋼的基本力學性能明顯超過了目前現有的超高強韌鋼,且具有密度低、成本經濟的優點,這也證明了中錳鋼作為超高強韌鋼未來鋼種的巨大潛力。
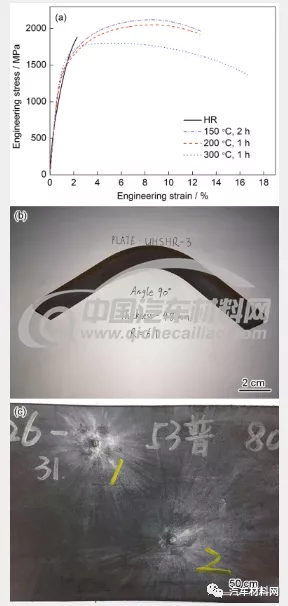

圖9為各類型超高強高韌鋼鋼種的典型強度與韌性[20,21,22,23,24,27,28,36,37,38,39,40,42,43,44,45,46,89,90,108]。由此可見,二次硬化類型鋼通常韌性較好而強度略遜,納米貝氏體鋼則是強度較高而韌性略遜,而低合金鋼的強韌性匹配相對更好,作者團隊所研發的7Mn中錳鋼則將上述強韌性極限又提高到一個新的水平。在設計這一新類型鋼時,需要考慮如下因素:(1) 將低合金鋼通過單相淬火馬氏體強化的思路轉變為以馬氏體為基體,同時引入次基體相如殘余奧氏體、貝氏體鐵素體、少量高溫δ鐵素體等形成多相復合顯微組織,在發揮馬氏體強化的同時,利用奧氏體的TRIP及TWIP作用和軟相鐵素體的變形作用提高韌塑性;(2) 高密度納米共格析出相或復合析出多類型納米粒子強化的設計,尤其是需要考慮當引入較多殘余奧氏體或鐵素體時,也必須讓這些次基體相發生析出強化,提高屈服門檻;(3) 根據以馬氏體為主基體加多種復合基體,并結合多類型析出相實現強韌化的的思路,在前期所積累的實驗數據基礎上,結合材料熱力學和動力學計算設計化學成分和關鍵工藝,從而最終開發出符合嚴苛服役工況條件的新型超高強韌鋼。綜上所述,中錳鋼在滿足上述我國對超高強高韌鋼特有需求方面有很大的潛力。
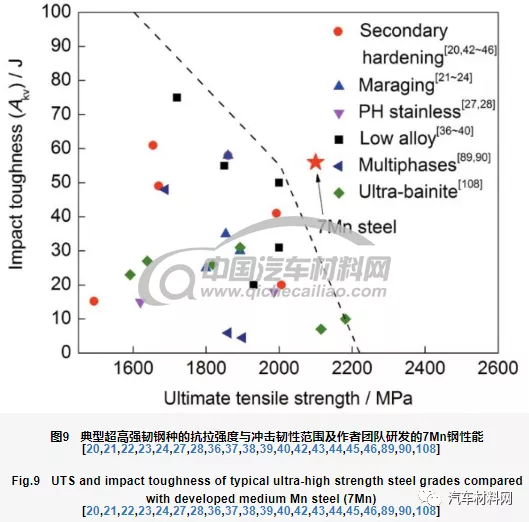
4總結與展望
經過幾十年的發展,超高強韌性鋼的研究取得了長足的進步。由最初的傳統單相馬氏體組織與半共格或非共格碳化物組成的超高強鋼正在逐漸向板條馬氏體、貝氏體鐵素體、殘余奧氏體與各種納米共格析出相強化的、多相復合組織的超高強韌鋼轉變。近期研究結果表明,多類型析出強化和在馬氏體基體上引入塑/韌性相阻礙裂紋擴展這一思路,將有助于進一步提高鋼鐵材料的強韌性極限,獲得超高強度和優良韌塑性的更佳匹配。同時,由于我國國民經濟的迅速發展以及國內獨特的資源、地理特點,在輕質裝甲鋼、大型半自磨機、盾構機刀具及油田裝備高壓壓裂泵等裝備機械領域,都迫切要求開發出比現有鋼材強度和韌性均大幅度提高的新型超高強韌鋼,以滿足更為苛刻的服役工況要求。因此,對不同類型析出相的耦合強化機制、馬氏體基體與塑性相組成的復合組織強韌化機理等科學規律進行研究是必要的,積累相關數據和經驗,并通過材料計算和實驗研究,最終可望開發出滿足我國經濟建設所需的超高強韌合金鋼。
免責聲明:本網站所轉載的文字、圖片與視頻資料版權歸原創作者所有,如果涉及侵權,請第一時間聯系本網刪除。
相關文章
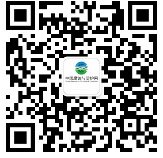
官方微信
《中國腐蝕與防護網電子期刊》征訂啟事
- 投稿聯系:編輯部
- 電話:010-62316606-806
- 郵箱:fsfhzy666@163.com
- 中國腐蝕與防護網官方QQ群:140808414
點擊排行
PPT新聞
“海洋金屬”——鈦合金在艦船的
點擊數:7130
腐蝕與“海上絲綢之路”
點擊數:5741