油氣管道腐蝕防護系統是確保管道長期安全運行的基本保障,隨著國家對油氣管道安全監督力度的加強,油氣管道腐蝕檢測成為管道安全防護的重要環節和技術手段。
腐蝕貫穿鋼質管道全生命周期,是導致油氣管道失效事故的主要誘因之一。定期對管道開展腐蝕檢測,及時、準確地發現腐蝕缺陷,并采取相應的控制、維修、更換措施,可有效降低腐蝕事故發生概率。
目前,中國在油氣管道腐蝕檢測方面已經形成以直接評價為核心的相對完善的檢測與評價技術體系,包括外腐蝕直接評價(ECDA)、內腐蝕直接評價(ICDA)、應力腐蝕開裂直接評價(SCCDA)。2000年左右,直接評價技術被引入中國,經過大量工程應用,已經形成自己的行業標準,相關內容也納入油氣管道定期檢驗項目。
近年來,針對油氣管道管體缺陷的非開挖檢測技術也得到較多工程應用,如瞬變電磁技術(TEM)、超聲導波檢測技術、磁應力檢測技術(MTM)等。工程實踐表明:直接評價雖然存在一定的局限性,但仍是目前用于評估油氣管道腐蝕控制狀況或腐蝕風險的有效手段,對于埋地長輸油氣管道而言,外腐蝕直接評價的工程應用最為廣泛,技術也更加成熟。
1 技術現狀
1.1 外腐蝕檢測與評價技術
1.1.1 發展概況
在2000年以前,埋地鋼質管道的外腐蝕檢測主要依靠開挖調查。當時主流的防腐層質量檢測技術是中國自主研發的變頻-選頻法,其以一定長度的管道為評估對象,通過測試單位面積防腐層與遠方大地之間的電阻,評估埋地鋼質管道外防腐層的狀況。該方法適用于評價一段管道防腐層的整體質量,無法定位找出防腐層破損位置,目前已很少應用。關于陰極保護有效性的評價,雖然提出了IR降的概念,但電位測量仍主要依賴于試片或極化探頭,檢測效率低。
在2000年以后,隨著一些檢測設備(如英國雷迪公司的RD-PCM測量設備、加拿大CATH-TECH公司的CIPS測量設備、中國自主研發的SL系列防腐層檢漏儀)的研發與應用,外檢測和評價技術得到快速發展,逐步形成以交流電流衰減法(ACAS)、交流電壓梯度法(ACVG)、皮爾遜法(PERSON)、密間隔電位測量法(CIPS)、直流電壓梯度法(DCVG)為核心的技術體系,建立了一套科學的外腐蝕直接評價技術流程(圖1),提高了外腐蝕檢測的效率和準確率,成為目前外腐蝕檢測和評價的主流方法。
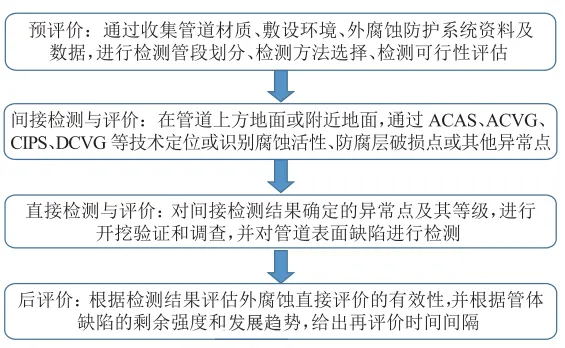
圖1 油氣管道外腐蝕直接評價( ECDA)技術流程圖
通過不同檢測方法的組合應用,可系統評估管道外防腐層質量、陰極保護有效性、雜散電流干擾的總體狀況,并結合防腐層破損處的開挖調查,對管體腐蝕缺陷及環境腐蝕性進行直接檢測和評價。但相關檢測設備的應用需要通過大地形成良好的回路,在一些特殊管段的應用存在困難,測量結果的準確性也因此受到影響,主要包括:
① 大型穿跨越、連續水網區等測試人員難以到達的管段;
② 鋪砌路面、凍土、鋼筋混凝土、含有大量巖石回填物等導電性較差的管段;
③ 防腐層剝離、套管、保溫層等易造成電屏蔽的管段;
④ 雜散電流干擾嚴重的管段。
1.1.2 技術標準
中國最早用于指導油氣管道內外腐蝕檢測的標準是SY/T 0087-1995《鋼質管道及儲罐腐蝕防護與調查方法標準》,其中開挖調查相關規定一直沿用至SY/T 5919-1994《埋地鋼質管道干線電法保護技術管理規程》,主要用于指導陰極保護和交直流雜散電流干擾的檢測與評價,其中的陰極保護度、陰極保護有效率概念也一直沿用至今。
2004年,中國石油規劃總院、中國石油大學(北京)、中國石油管道公司沈陽調度中心等單位,非等效采標美國防腐蝕工程師協會(NACE)標準NACE RP 0502-2002《管道外腐蝕直接評價方法》,編制了SY/T 0087.1- 2006《鋼制管道及儲罐腐蝕評價標準埋地鋼質管道外腐蝕直接評價》,形成了以間接檢測為核心的外腐蝕直接評價技術規程。目前,該標準已經完成第二次修訂,最新發布版本為SY/T 0087.1-2018,該標準較好地指導和推動了中國油氣管道外腐蝕檢測工作的開展,在工程實踐中積累了大量寶貴經驗,同時也發現一些不足,如流程過于復雜,檢測技術適用范圍受限,評價指標可操作性不強等。
自NACE RP 0502-2002之后,NACE又先后發布了一系列標準,對于提高ECDA的有效性起到了很好的支撐作用。NACE SP 0207-2010《埋地或地下水金屬管道上密間距和直流電壓梯度測量》提出了CIPS和DCVG檢測流程及技術要求,NACE TM0109-2009《地下管道防腐層狀況評價地面檢測技術》提出了間接檢測技術的操作流程和數據分析方法,NACE SP 0210-2010《管道外腐蝕確認直接評價》提出了綜合運用多個指標、多種因素評估和判斷外腐蝕風險的流程。
目前,中國除SY/T 0087.1之外,針對具體檢測方法的標準尚未形成完整的標準體系,SY/T 0087.1- 2018在原標準的基礎上重點修訂了評價準則以及間接檢測與評價部分,由原來的單-指標評價改為綜合指標評價,采用風險矩陣的思路將土壤腐蝕性、防腐層破損程度、陰極保護水平、雜散電流干擾程度等單一指標進行組合,以綜合評估外腐蝕風險,確定開挖調查的優先級,促進了評價思路的完善,但尚未完全解決檢測技術的規范性問題。
1.2 內腐蝕檢測與評價技術
1.2.1 發展概況
埋地鋼質管道內腐蝕檢測與評價技術的發展與外腐蝕檢測與評價技術基本相同,最初也是主要依賴介質腐蝕性分析和開挖調查。目前,針對內腐蝕的檢測與評價,除內檢測技術外,主要采用內腐蝕直接評價(ICDA)方法。
2006年,NACE發布了干氣管道內腐蝕直接評價標準NACE SP 0206-2006《干氣管道內腐蝕直接評價方法(DG-ICDA)》,國內也同步開始了輸氣管道內腐蝕直接評價的應用研究,隨后多相流管道內腐蝕直接評價方法(MF-ICDA)、濕氣管道內腐蝕直接評價方法(WG-ICDA)、液體管道內腐蝕直接評價方法(LP-ICDA)陸續進入研究應用階段。中國石油規劃總院通過持續開展ICDA研究與應用,積累了豐富經驗。
ICDA分為預評價、間接檢測、詳細檢查、后評價4步流程(圖2),其中間接檢測是核心,主要通過流體力學模型計算給出可能的內腐蝕風險點,再結合腐蝕預測模型分析其發展趨勢。常用的流體分析軟件包括Fluent、OLGA等,結合管道走向、流體狀態,預測水或腐蝕性介質易沉積的位置,并通過現場開挖進行驗證。
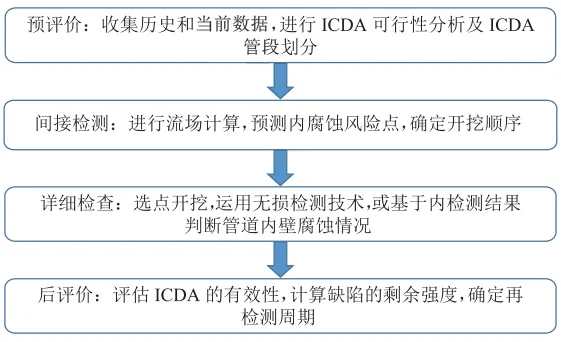
圖2 油氣管道外腐蝕直接評價(ICDA )技術流程圖
這些預測方法或模型并不是唯一的,通常不具有普遍適用性。北美地區的一些管道運營公司往往結合所轄管道的實際情況,開發有針對性的計算模型或軟件,可以重復使用和持續修正。
近年來,一些油氣長輸管道因游離水沉積或介質質量控制不到位等問題而發生內腐蝕,因而推進了ICDA技術的應用,但總體應用效果不如ECDA技術成熟。
在各種內腐蝕直接評價技術中,天然氣干線管道內腐蝕預測模型較為成熟,在國外已有較多的成功應用案例,而液體管道、多相流管道的腐蝕分析模型因介質情況復雜,成功應用案例較少,目前大都處于探索階段。
中國雖然在輸氣管道、液體管道、多相流管道均開展了ICDA應用,但整體處于試驗研究階段,目前面臨的問題主要包括:
① 在流場計算和腐蝕模型預測方面經驗不足,特別是液體管道、 多相流管道計算參數繁多,不同模型對不同管道的適用性各不相同;
② 現有計算軟件或模型在長距離管道流體計算分析方面精度不高,計算能力有限。
1.2.2 技術標準
自2006年起,NACE先后發布了針對不同輸送介質管道的ICDA技術標準,包括NACE SP 0206-2006、NACE SP 0208-2008《液體石油管道內腐蝕直接評價方法(LP-ICDA)》、NACE SP 0110-2018《濕氣管道內腐蝕直接評價方法(WG-ICDA)》、NACE SP 0116-2018《多相流管道內腐蝕直接評價方法》。每一部標準都針對具體的流體特性,給出流場計算和腐蝕預測的推薦模型,如Adams模型、Crolet模型、Dayalan模型等。這些模型與管道輸送介質的屬性、運行工況、敷設條件等參數的選取密切相關,直接決定計算精度和預測準確率。工程應用實踐表明:選擇合適的流場計算模型、腐蝕預測模型及工況參數是保證內腐蝕直接評價結果準確性的必要條件。
在2006年之前,中國用于指導內腐蝕檢測與評價的標準主要是SY/T 0087-1995。2010年,中國石油規劃總院牽頭編制了SY/T 0087.2-2012《鋼制管道及儲罐腐蝕評價標準第2部分:埋地鋼質管道內腐蝕直接評價》。
SY/T 0087.2-2012與NACE發布的標準雖然都建立了ICDA“四步”流程,但核心內容存在本質區別。SY/T 0087.2-2012推薦采用地面非開挖檢測技術(TEM、超聲導波、超聲測厚等)確定管道內腐蝕位置,這些非開挖檢測技術在實際應用中存在諸多局限性,對管道敷設條件和外界環境干擾較為敏感,也無法區分內、外腐蝕缺陷。
目前,在管道內腐蝕檢測與評價方面,中國一般參照NACE標準推薦的做法,而流場計算模型的運用則多種多樣。GB/T 34349-2017《輸氣管道內腐蝕外檢測方法》和GB/T 34350一2017《輸油管道內腐蝕外檢測方法》中關于內腐蝕檢測與評價的要求與NACE標準一致。
1.3 應力腐蝕開裂檢測與評價技術
1.3.1 發展概況
應力腐蝕開裂(SCC)是材料在應力和腐蝕環境共同作用下產生的以裂紋生長和脆性斷裂為特征的一種環境敏感斷裂形式,油氣長輸管道以外壁應力腐蝕開裂為主,裂紋常以群落的方式集中出現在某一區域,裂紋群內可能存在幾十到幾百個相互平行的微小裂紋。
1965年3月,美國路易斯安那州Natchitoches輸氣管道發生第一起SCC事故。20世紀90年代,高pH值SCC開裂機理得到業界的普遍認可,近中性pH-SCC開裂機理也得到不斷發展。中國從2001年開始對埋地鋼質管道的應力腐蝕開裂問題開展專項研究,對四川天然氣管網、陜京輸氣管道、澀寧蘭輸氣管道進行現場調查,并開展系統的實驗室研究工作。
SCC從萌生到引發事故是一個非常緩慢的過程,不易被發現或檢出,引發事故前,裂紋常潛伏于管體幾十年。應力腐蝕開裂直接評價方法(SCCDA)包括預評價、間接檢測、直接檢查、后評價4步流程,通過敏感性分析及開挖調查識別、確認管道的SCC風險,建立SCC敏感段開挖選點原則(圖3)。
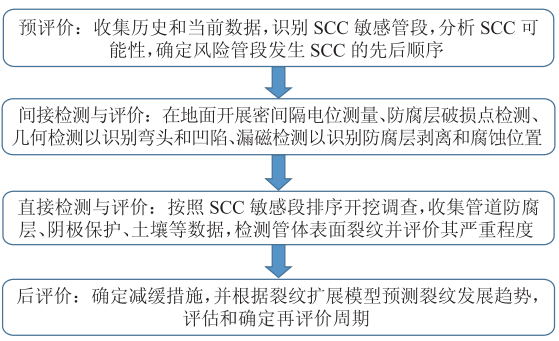
圖3 應力腐蝕開裂直接評價方法(SCCDA )技術流程圖
在SCCDA之外,北美地區的管道運營公司開展了數千公里基于內檢測的應力腐蝕裂紋檢測。漏磁檢測是目前比較成熟的管道內檢測方法,但管道表面裂紋形態各異,增加了裂紋檢測和量化難度,通過檢測信號難以精確識別出裂紋,只有當外加磁場方向最大限度地與被檢缺陷正交時,才能激勵出最大的漏磁場。美國TDW公司開發的螺旋漏磁檢測技術(SMFL),結合周向漏磁檢測技術的優點及傳統軸向漏磁檢測技術的精度特性,在未明顯增加測量節長度的情況下,能夠實現對各個方向狹長裂縫的精確測量。但針對軸向裂紋、尺寸較小裂紋和其他類裂紋缺陷的漏磁檢測技術有待開展深入研究。
超聲波檢測技術對裂紋等平面型缺陷較敏感,檢測精度高,但對耦合條件要求較高。GE-PII、ROSEN、NDT等管道檢測公司均擁有基于壓電超聲的腐蝕、裂紋檢測技術。ROSEN公司研發的電磁超聲裂紋檢測器不需要液體耦合劑,適用于輸氣管道的檢測,可以檢測裂紋、防腐層剝離,但檢測效果仍需通過工程應用加以驗證。Enbridge公司的檢測實踐表明,管道夾雜會影響超聲波信號的傳播,超聲檢測在裂紋尺寸和深度測量方面存在一定誤差,需要結合管道實際情況和開挖驗證情況,對檢測信號進行分析處理。
目前,中國裂紋內檢測設備尚處于實驗室研發和樣機試驗階段,實際應用效果不理想。
應力腐蝕裂紋檢測的另一個技術難點是定量化問題,超聲相控陣(PAUT)是目前唯一能夠檢測應力腐蝕裂紋并給出定量尺寸和深度的技術,但對管道表面的耦合條件要求較高,檢測效率低,只適用于開挖調查。
1.3.2 技術標準
國外針對埋地管道應力腐蝕開裂開展了大量的實際調查和科學研究,形成多個技術標準,包括NACE SP 0204-2008《應力腐蝕開裂直接評價方法》、ASME B31.8S-2014《輸氣管道系統完整性管理》、ASME STP-PT-011-2008《高后果區內天然氣管道應力腐蝕開裂的完整性管理》、API RP 1160-2013《危險液體管道的完整性管理》,以及加拿大能源管道協會編制發布的《應力腐蝕開裂評價推薦作法》。這些應力腐蝕風險識別和直接評價方面的標準,主要借鑒北美地區的相關經驗,受服役環境影響在中國的適用性有待驗證。
目前,中國的應力腐蝕開裂檢測與評價標準GB/T 36676-2018《埋地鋼制管道應力腐蝕開裂(SCC)外檢測方法》和SY/T 0087.4- 2016《鋼質管道及儲罐腐蝕評價標準 第4部分:埋地鋼質管道應力腐蝕開裂直接評價》在應力腐蝕開裂敏感性分析、敏感段識別和SCC裂紋評價方面主要參照NACE SP 0204-2008。
1.4 穿越段管道外腐蝕檢測與評價技術
1.4.1 河流穿越
河流定向鉆穿越段管道埋深大,無法實施地面檢測,主要依靠設計、建設期提高防腐等級保證其使用壽命。
GB/T 37369一2019《埋地鋼質管道穿跨越段檢驗與評價》對穿跨越段管道的檢測與評價提出了年度檢查和定期檢驗的要求,重點提出了檢測項目和要求,但具體的檢測方法和技術手段涉及較少。
NACE TM 0102-2002《地下管道涂層電導率測試標準》推薦采用防腐層電導率評價定向鉆穿越段管道防腐層質量,但該方法僅適合在施工完成后尚未與其他管段連接時應用。
中國石油天然氣集團有限公司企業標準QSY 1477-2012《定向鉆穿越管道外涂層技術規范》要求河流穿越段管道在水平定向鉆穿越后且未與主管道碰頭前,實施穿越段管道防腐層測試與評 價,該方法可實現對穿越段管道防腐層質量的整體評價,但無法準確定位防腐層缺陷位置。
羅旭研究了基于“電纜回路”和“管地回路”的電磁法水下管道埋深檢測及防腐層缺陷定位技術的可行性,繪制了沿管道方向的磁場強度曲線,可實現對管道防腐層缺陷區域的定位,該方法目前尚未在實際檢測中應用,而且應用于實際檢測的工程量將非常大。
中國石油管道科技研究中心研發了評價定向鉆穿越段管道陰極保護有效性的數值模擬計算模型,假設定向鉆穿越段管道防腐層破損點均勻分布,通過測量管道的極化曲線、不同層土壤電阻率,結合加拿大SES公司CDEGS軟件模擬結果,評估了爬坡段管道陰極保護電流需求量及電位分布情況。
天津嘉信技術工程公司自主研發的河流穿越段管道外腐蝕檢測系統River-ROV,結合潛水和聲吶設備,實現了對穿越段管道的定位、埋深測量、電位測量及防腐層破損點的定位功能,在多條河流穿越段實現了應用。
定向鉆穿越段管道投入運行后,防腐層質量評估的意義已經不大。現有檢測技術大都無法準確判斷防腐層破損位置和破損程度,即使定位后也無法采取修復措施。目前,對于普遍使用的3PE防腐層,局部破損也并不會顯著影響其絕緣電阻率。因此,應該重點關注陰極保護有效性評價,目前主要是基于數值模擬計算的方法來分析河流穿越段管道的陰極保護電流和電位分布狀況,但在模型邊界條件選取、土壤分層、防腐層破損點分布、絕緣電阻等方面仍需開展深入細致的研究。
1.4.2 金屬套管穿越
關于金屬套管穿越段管道的檢測與評價問題,目前相關標準并未給出具體的測試與評價方法,以至于管道運營公司無法及時掌握金屬套管穿越段管道的腐蝕狀況。近年來,金屬套管已逐漸被水泥套管取代,金屬套管穿越段管道檢測與評價的需求越來越小。美國交通運輸部管道與危險物質安全管理局(PHMSA)根據美國《2002年管道安全改進法令》提出了高后果區管段完整性管理的要求,并于2010年3月發布了《高后果區套管中天然氣管道的完整性評價導則(0版)》,強調了套管穿越段管道的完整性管理問題。
金屬套管與輸送管道的腐蝕問題與兩者之間的絕緣狀況密切相關。NACE RP 0200-2000《管道鋼質套管操作規程》推薦了通過測量金屬套管與管道電位差評估腐蝕風險的方法。Pikas提出了金屬套管穿越段管道的腐蝕風險評價指標及金屬套管穿越段管道腐蝕直接評價的4步流程。中國石油管道公司基于上述方法,曾連續開展金屬套管穿越段管道的檢測工作,實際驗證了該流程的可靠性,以及超聲導波技術在金屬套管穿越段管道檢測上的技術優勢。
1.5 其他地面非開挖檢測技術
1.5.1 瞬變電磁技術
1951年,加拿大物理學家Wait首先提出瞬變電磁(TEM)技術原理。1960年,蘇聯研制出第一臺檢測裝置,用于地下礦體探測、地質勘探及埋地管道檢測。中國從20世紀70年代開始研究,已成功研制出可用于埋地鋼質管道檢測的裝置。該技術原理是利用施加脈沖電流的發射線圈在埋地管道周圍激勵磁場,脈沖電流的瞬間變化會引起磁場的變化,變化的磁場在埋地管道上激勵出一種隨時間衰減的“渦流”,由衰變“渦流”激勵出隨時間衰減的磁場又會在接收線圈中感應出電動勢,感應電動勢的大小與電阻率和磁導率相關,當管道無缺陷時,電阻率和磁導率是均勻的,而缺陷截面則會引起電導率和磁導率的變化,感應電動勢的大小隨之變化。
TEM技術根據管道壁厚或物理特性變化識別缺陷,優缺點包括操作簡單,無需開挖和清管;可獲得埋地鋼質管道平均壁厚或金屬損失量,但與實際壁厚有一定偏差,無法識別出缺陷面積,不能檢測點蝕缺陷;檢測時受管輸介質、土壤、并行管道及外部電磁干擾影響較大;難以對埋深過大的管道進行檢測。總體而言,該技術在長輸管道應用較少,在埋深淺、干擾小的油田集輸管道應用較多。
1.5.2 超聲導波技術
1997年,英國導波公司(GUL)成功推出壓電式超聲導波檢測設備,并迅速在歐洲得到應用。美國西南研究院(SWRI)也于20世紀90年代研發出磁致伸縮式超聲導波檢測設備。這是目前超聲導波的兩大技術流派。其原理是利用陣列式超聲波探頭激發沿管道軸向傳播的超聲導波,當遇到管道橫截面積的任何改變時,都會反射一個回波信號,信號強度取決于橫截面積的改變量。通過信號的對稱與非對稱特征可識別出管道上的環焊縫、彎頭、法蘭、支管、缺陷等特征,最小可檢測到橫截面積變化的3%。
超聲導波可在不開挖或局部開挖條件下,在較長管段上實現“點”對“線”的快速掃查,定位出整個管段的內、外壁缺陷,識別出法蘭、焊縫、支管等特征,但無法精確測量缺陷深度、面積等參數,需要局部開挖,配合采用其他無損檢測技術實施缺陷定量測量。對于地上管段,可檢測上百米,但對于埋地管段,檢測距離較短,單側檢測長度一般只有5~25m。目前,超聲導波技術主要應用于站場工藝管道和套管穿越段管道的檢測。
1.5.3 磁應力檢測技術
1994年,俄羅斯Doubov教授首次提出金屬磁記憶概念,即鐵磁性金屬構件因受載荷和地磁場共同作用,在應力和變形集中區域發生具有磁致伸縮性質的磁疇組織定向和不可逆的重新取向,這種狀態的變化是不可逆的,在載荷消除后不僅會保留,而且與最大作用應力有關,“記憶”著金屬構件表面微觀缺陷或應力集中的位置,即所謂的磁記憶效應。
磁應力檢測(MTM)技術就是基于金屬磁記憶效應開發的一種弱磁檢測技術,檢測處于地磁場環境中的鐵磁性構件在缺陷或應力集中區域的漏磁場,從而實現缺陷定位。檢測人員只需要手持檢測儀器,在管道正上方行走即可開展缺陷掃描。
MTM技術可檢測管道金屬損失缺陷和應力集中區域,對應力集中缺陷較敏感,但受外界電磁干擾及管道內檢測后的剩磁影響較大。該技術產品自2002年商業化以來,目前已發展至第二代產品,在埋地鋼質管道實現了應用,主要應用于俄羅斯。中國近年來也開展了試應用,但檢測效果差異較大,仍需通過大量工程實踐驗證其檢測的準確性。
總體而言,上述檢測技術都是通過識別管道橫截面變化判斷管體缺陷,并不能區分外壁缺陷和內壁缺陷。其優點是無需開挖,操作簡單,檢測效率高,對管道檢測條件要求不高,適合局部管段的快速掃查,應用于長輸管道全面檢測效率不高。其缺點是精度低,易受外界電磁環境影響,檢出率不高,只能給出缺陷的相對嚴重程度,無法精確測量管壁或缺陷尺寸。2019年,中國石油管道公司嘗試采用MTM技術定位管道環焊縫,結果表明定位準確率只有50%。
2 應用現狀
長輸油氣管道外腐蝕檢測與評價技術相對成熟,內腐蝕和應力腐蝕開裂檢測與評價技術尚處于試點和摸索階段。油氣管道腐蝕檢測技術選型和檢測強度與企業生產需求和管理水平密切相關。TSG D7003-2010《壓力管道定期檢驗規則——長輸(油氣)管道》將外腐蝕、內腐蝕、應力腐蝕開裂的檢測與評價統稱為外檢測,并未明確要求在定期檢驗過程中對所有管道全部開展上述檢測,管道運營公司可根據需求靈活選擇。
2.1 外腐蝕檢測
外腐蝕檢測與評價是長輸管道定期檢驗的重要內容,通常按照新建管道3年內完成基線檢測,隨后每5年定期開展ECDA,最大時間間隔不超過8年。雖然當前外腐蝕控制水平有很大提升,但隨著管道運行年限的增加,防腐層老化、剝離、破損及雜散電流干擾問題將越來越突出。2019年,中石油管道有限責任公司組織開展了針對所轄管道ECDA效能評價工作,針對各地區公司所轄管道ECDA實施情況進行了調研,發現存在以下問題:
① ECDA的4步流程執行效果不好,尤其預評價和后評價不充分;
② 檢測服務商技術水平參差不齊,存在技術運用不當的問題;
③ 檢測服務商自行制定的評價準則差異較大,或評價指標運用不當;
④ 對檢測數據的分析和利用不夠,數據統計分析形式多種多樣,導致多次檢測結果無法對比分析。
主要原因可歸納為4個方面:
(1) 標準的指導作用有限。SY/T 0087.1是一部方法類的標準,重點規范的是ECDA的流程和評價準則,對檢測技術執行和數據分析的指導作用十分有限。總體而言,中國缺乏相應的技術規范來指導檢測技術執行、數據分析,現行標準中評價指標、準則以定性為主,檢測服務商運用評價準則的尺度把握各不相同,在實際應用過程中難以規范操作。而國外除ECDA方法標準外,還有配套的技術規范作為支撐。
(2) 檢測技術的局限性大。現有的間接檢測技術對檢測人員的經驗和水平依賴性較大,且本身存在局限性,在涂層剝離、高電阻率環境、深埋管段、雜散電流干擾段、管道埋深超過正常值的特殊管段,外腐蝕檢測與評價技術難以應用,部分方法抗干擾能力差,精度低。
(3) 過程管理不夠嚴格。在工程實踐中,相同條件下ECDA評價結果存在差異,這與管道運營公司的管理水平及檢測服務商的技術水平密切相關。管道運營公司雖然制定了管理流程,但一些公司的過程管理由分公司或基層站隊負責,因缺乏專業技術人員,故對檢測方案審查、檢測過程管理監督、報告驗收、質量控制的管理力度不夠。
(4) 數據分析和利用不充分。在ECDA工作完成后,部分檢測服務商只提供報告,不提供原始數據,報告中也只列出一些典型問題。管道運營公司無法驗證檢測數據的準確性,也無法對數據進行再分析和深度挖掘,多次檢測數據無法進行對比分析,無法與管道內檢測、風險評價、完整性評價數據深入融合。
2.2 內腐蝕檢測
在對1.1X10*km涵蓋天然氣、原油、成品油等輸送介質管道內檢測數據進行分析的過程中,將內部金屬損失確認為內腐蝕缺陷,得到不同輸送介質管道的內部金屬損失缺陷密度,如圖4所示。可見原油管道內腐蝕較為嚴重,其次為成品油管道,天然氣管道內腐蝕最輕。天然氣管道內腐蝕分布沒有明顯規律,管道底部相對較多,其他部位內腐蝕分布隨機性較大,沒有明顯的時鐘特征,與服役年限沒有明顯的對應關系,表明內腐蝕由投產前形成的可能性較大,局部位置的內腐蝕可能與清掃后干燥不徹底有關。液體管道內腐蝕存在明顯的時鐘分布規律,主要集中在管道下半部分,表現為顯著的積水腐蝕特征。服役年限較長的馬惠線、秦京線、鐵秦線、鐵撫線等原油管道及蘭鄭長線、港棗線、蘭成渝線等成品油管道,內腐蝕缺陷密度高,內腐蝕相對嚴重,表明內腐蝕隨著管道服役年限的增加趨于嚴重。
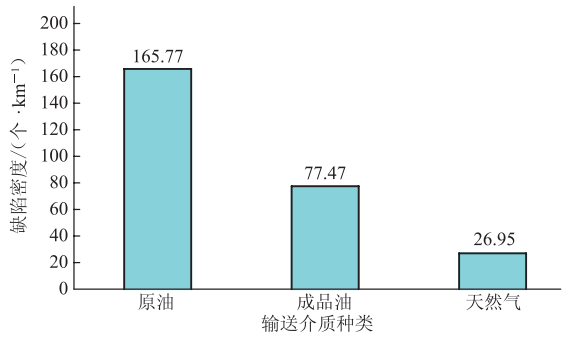
圖4 不同輸送介質管道內部金屬損失缺陷密度柱狀圖
目前在內腐蝕檢測方面,對于具備內檢測條件的長輸管道,管道運營公司優先選擇內檢測技術手段識別出內腐蝕高風險點,再結合定點監測和檢測持續關注內腐蝕高風險點的發展,如超聲定點測厚、安裝腐蝕監測探頭等,而ICDA在長輸管道上的應用目前整體處于嘗試階段。
2.3 應力腐蝕開裂檢測
在應力腐蝕開裂檢測方面,除2001年開展了系統研究和調查以外,一直未開展大規模研究與應用,主要原因是目前我國埋地鋼質管道尚未發生典型的高pH-SCC或近中性pH-SCC案例。對于影響應力腐蝕開裂敏感性的各項因素,我國管道具有以下特點:
(1) 管道服役時間短。國外統計資料表明,應力腐蝕開裂通常在管道運行20年后進入高發期,且主要發生在采用瀝青、纏帶和煤焦油瓷漆類等低性能防腐層或施工質量低的管道。我國輸氣管道僅陜京一線投產運行超過20年,澀寧蘭線投產運行接近20年,而且我國管道普遍采用工廠預制的3PE和FBE防腐層,防腐層使用壽命長。
(2) 管道運行壓力相對較低。國外案例分析表明,應力腐蝕通常發生在運行壓力大于管道屈服強度60%以上的管段。我國大部分管道設計壓力在屈服強度的60%~70%之間,但實際運行壓力低于設計壓力,只有陜京一線和西氣東輸線的實際服役壓力大于管道屈服強度的60%。同時,我國自行生產的管線鋼的屈服強度一般高于標準要求,如X80管線鋼屈服強度實測值通常在600MPa以上,高于標準要求的555MPa,因此管道實際運行壓力高于管道屈服強度60%以上的情況較少。
(3) 中國管道發生應力腐蝕開裂的主要風險點為補口、劃傷等易產生陰保屏蔽、陰保不足及存在雜散電流干擾的位置。近年來,中國長輸油氣管道外腐蝕控制水平持續提升,內、外檢測技術大規模應用后,通過及時開挖修復及雜散電流干擾專項治理,外腐蝕風險降低,應力腐蝕開裂風險也隨之降低。
3 總結與思考
近20年來,中國油氣管道腐蝕檢測技術水平整體提升較快,管理精細化程度不斷提高,但也存在一些技術和管理問題亟待解決。未來的管理和技術提升應重點關注以下內容:
3.1 管理提升
(1) 建立統一的技術規范。目前,油氣管道腐蝕檢測相關標準以直接評價標準為主,更注重方法流程,對技術應用條件和實施過程的規定不夠細化。管道運營公司應著手建立統一的規范,從檢測資質、檢測方案、技術運用、評價準則、數據格式、報告內容、驗收標準等方面提出統一要求。
(2) 建立數據管理平臺。目前,外檢測服務商提交的報告差異大,不便于后期的數據挖掘和綜合分析。北美地區的檢測服務公司會自行編制數據管理軟件,并提供給管道運營企業,從而為管道運營企業后期數據使用提供便利。對于同一條管道,通過重復利用原始數據,可有效提高ECDA工作效率。管道運營公司應該著手建立統一的數據管理平臺,對腐蝕檢測數據進行集中管理,并且加大內外檢測數據的對齊和對比分析。
(3) 建立專業化腐蝕檢測效能評價隊伍。外檢測實施效果與具體檢測人員的素質、責任心有很大關系。為了提升外檢測管理效果,管道運營公司應建立專業化腐蝕檢測效能評價隊伍,統一管理標準和尺度,加強腐蝕檢測的過程管理和最終檢測質量的評估。
3.2 技術提升
(1) 持續開展應力腐蝕開裂檢測與評價技術研究。我國長輸油氣管道雖然尚未發現應力腐蝕開裂的案例,但隨著運行年限的增加,應力腐蝕開裂風險會越來越大。3PE防腐層粘結力降低或發生剝離,都可能導致應力腐蝕開裂風險增大。北美地區針對應力腐蝕開裂的研究持續了50年,直至2012年仍有應力腐蝕開裂事故發生。目前,近中性pH-SCC的斷裂機理、硫酸鹽還原菌(SRB)在應力腐蝕開裂中發揮的作用都還有很多細節需要深入研究。未來仍需在高強鋼應力腐蝕開裂機理、敏感性分析、風險識別和現場檢測技術等方面持續開展深入研究。
(2) 啟動微生物腐蝕機理和檢測技術研究。我國關于微生物的腐蝕最早發生在成品油管道內壁,而最近在長輸管道外壁也發現了微生物腐蝕案例。微生物腐蝕機理復雜,腐蝕發展快,目前仍處于實驗室研究階段。對于長輸油氣管道,微生物與土壤成分、管道金屬材料、防腐層類型、運行溫度等因素的相互關系尚不確定,且缺乏有效的檢測手段和防護措施。
(3) 開展針孔腐蝕缺陷的檢測與驗證技術研究。內檢測可以檢出針孔缺陷,但要測量缺陷的真實深度卻很難。目前已有案例表明,在存在交流干擾腐蝕的管道上,漏磁內檢測報告結論是缺陷深度為壁厚的40%,但實際開挖檢測發現,缺陷深度已達壁厚的60%。漏磁內檢測技術對針孔缺陷的檢出率低于80%,缺陷深度檢測誤差均大于20%,報告給出的缺陷深度遠低于實際缺陷深度,嚴重影響評價結果的準確性。對于管道內腐蝕形成的直徑小于4mm的針孔缺陷,常規的超聲波檢測技術也很難準確檢出缺陷的實際深度。對于發展不規則的針孔缺陷,定點的超聲波測厚和壁厚監測均難以滿足工程實際需求。此時,不僅需要高精度的探頭,還需要精密控制探頭的掃描步進。
(4) 開展組合式內外檢測工具研發。為了保障長輸油氣管道安全平穩運行,需要定期開展外腐蝕檢測及內檢測。如果在內檢測設備上,搭載一些可以實施腐蝕檢測的裝置,如管中電流測試、積水測試、微生物濃度檢測,則可在實施內檢測的同時同步完成管道的內外腐蝕檢測。2008年,殼牌、貝克休斯公司開發了陰極保護電流在線檢測工具CPCM(Cathodic Protection Current Measurement),并已實現工程應用。
免責聲明:本網站所轉載的文字、圖片與視頻資料版權歸原創作者所有,如果涉及侵權,請第一時間聯系本網刪除。
相關文章
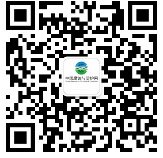
官方微信
《中國腐蝕與防護網電子期刊》征訂啟事
- 投稿聯系:編輯部
- 電話:010-62316606-806
- 郵箱:fsfhzy666@163.com
- 中國腐蝕與防護網官方QQ群:140808414
點擊排行
PPT新聞
“海洋金屬”——鈦合金在艦船的
點擊數:7130
腐蝕與“海上絲綢之路”
點擊數:5741