應力腐蝕開裂(SCC)是材料在拉應力和腐蝕環境共同作用下發生的低應力脆性開裂,自1965年美國首次記錄長輸埋地管道發生SCC以來,加拿大、歐洲、俄羅斯、伊朗、巴西、阿根廷和巴基斯坦等國也相繼發生了數百起由SCC導致的管道失效事故。SCC是近幾十年來導致管道失效事故的重要原因之一,它已經成為威脅埋地管道安全運行的重要因素,是管道特別是老舊管道完整性管理的重點關注問題。
大量SCC現場調查分析結果表明,SCC通常發生在防腐蝕涂層破損和陰極保護失效的管體位置,在管體上通常表現為垂直于主應力方向的多條平行裂紋。按照其發生的環境和開裂路徑,SCC可分為兩種類型:高pH SCC和近中性pH SCC。
2001-2002年間,中國石油集團公司組織開展的SCC調查結果表明,四川油氣管網、陜京管道和澀寧蘭管道暫未發現SCC,但管道服役環境存在發生SCC的風險。近十幾年來的大量室內試驗研究結果表明,國內埋地長輸管道具有發生SCC的可能性,然而國內埋地管道SCC事故鮮有報道。
SCC的孕育、萌生和前期擴展需要較長的時間,其風險隨著管道運行年限的增加而增加,一般認為服役超過10年的非環氧類防腐蝕層管道具有發生SCC的風險,管道運行20年左右進入SCC高發期。國內長輸管道經過近20年的快速建設和發展,在役管道里程接近14萬公里,與SCC相關的管道防腐蝕層類型、管線運行參數、管道防腐蝕和檢測管理方法都有了顯著的變化、提高或改進。
但目前尚缺乏與長輸埋地管道SCC風險狀況相關的調查數據或資料,本工作在分析SCC相關歷史調查和案例的基礎上,結合近年來開展的埋地長輸管道SCC現狀調查結果(補口位置現場開挖檢測,管道外腐蝕調查和環焊縫開挖檢測結果),分析目前國內埋地長輸管道發生SCC的原因,并探討其未來的SCC風險和防控方法,為國內埋地長輸管道的SCC防控管理提供參考和借鑒。
埋地管道SCC歷史調查及案例分析
在國外相繼發生多起由SCC導致的埋地管道開裂事故,加拿大能源管道協會(CEPA)于1996年首次頒布了SCC管理推薦做法的背景下,2001年中國石油集團公司組織了由中國石油大學、四川石油勘探設計研究院和石油管材所等多家單位參與的長輸埋地管道SCC調查和敏感性試驗評價。
該項目主要調查了19世紀60年代至90年代建設投產并采用石油瀝青防腐蝕層的2600多公里的四川油氣管網,分析了近40年來管道失效事故案例,結果沒有發現由SCC導致的事故。歷年來開展的169處現外腐蝕調查和21處SCC開挖檢測結果表明,部分管道存在瀝青防腐蝕層老化破損和腐蝕情況,但均未檢測到SCC裂紋。調查期間發現有一起裂紋開裂事故,管道開裂處存在機械損傷和腐蝕產物,開裂原因可能是機械損傷導致管道在服役早期形成的近中性pH SCC。然而,四川油氣管網、陜京一線、西氣東輸和澀寧蘭管道的室內SCC敏感性試驗研究結果表明,在國內中西部土壤環境中服役的管道具有發生SCC的可能性。
2011年運行9年的山東某天然氣管道發生爆裂事故,事故原因為:爆裂起源于管道外表面機械劃傷位置萌生的裂紋,機械劃傷使涂層破損,陰保失效導致劃傷底部發生腐蝕,劃傷造成的局部應力集中和腐蝕過程共同作用導致SCC裂紋的萌生,管道運行過程中裂紋不斷擴展最終導致了管道爆裂,裂紋的擴展路徑為沿晶開裂+穿晶開裂的混合型開裂方式,氫對裂紋的擴展也起到了一定的作用,該管道SCC的萌生主要是由于機械損傷引起,為管道服役初期發生SCC的情況。
2016年某儲氣庫管道經過11年服役后,在彎頭位置發生開裂失效,開裂源于管道外表面形成的裂紋。失效原因分析結果表明:該管道彎管材料的硬度和強度參數不合格,熱煨彎管工藝控制不當導致彎管表面組織變為硬度大且脆性敏感的馬氏體和魏氏體;在管道埋設位置,地下水豐富,土壤電阻率低,環境腐蝕性強,服役過程中,彎管外部的熱收縮帶涂層破損剝離,管體表面與外部腐蝕環境接觸;彎管位置的陰極保護電位在析氫電位以下,導致部分氫析出進入材料內部,在外部應力和氫的協同作用下,脆性相馬氏體組織發生氫致開裂,形成初期裂紋;服役過程中儲氣庫管道壓力波動和溫度變化產生低周疲勞導致裂紋不斷擴展,最終管體因疲勞而開裂失效。材料不合格導致氫致開裂是該管道產生裂紋的初始原因,因此該管道的SCC并不是典型的一般意義上的埋地管道近中性pH或者高pH SCC。
上述SCC歷史調查和僅有的兩個埋地管道SCC案例分析結果表明,國內埋地長輸管道發生SCC的案例很少,發生SCC的原因與管體機械損傷和材料質量有關,且都發生在管道服役初期,與典型的埋地管道SCC存在明顯差別。目前,未發現國內埋地管道發生由典型的SCC導致的開裂事故。
埋地管道SCC現狀調查
自2002年SCC調查以后,經過近20年的發展,國內長輸埋地管道里程數量、運行工況和日常管理維護方式都發生了巨大變化,長輸油氣管道總里程超過14萬公里,大口徑、高鋼級和高壓力的天然氣管道投運越來越多,在役管道外防腐蝕層90%以上為三層聚乙烯(3PE),定期開展的管道內外檢測成為管道完整性管理的重要依據。
部分管道的運行年限超過20年,進入了埋地管道SCC的高發時期。為明確在役管道SCC風險現狀,依據埋地管道SCC發生特點和直接評價標準,一方面選擇了不同服役時間的管道SCC高風險位置進行現場開挖,開展裂紋檢測和應力腐蝕相關參數的測試,明確所選擇管段的SCC風險,另一方面整理分析近年來的外腐蝕調查和環焊縫排查工作的調查結果,分析外腐蝕位置和管道補口位置的SCC風險。
01 埋地管道補口位置現場開挖檢測
本次開挖檢測包括位于榆林和泰安的天然氣管道和呼和浩特的原油管道,所開挖調查管道的服役時間分別為22年、8年和7年。共調查了8處位置。其中,6處管道的防腐蝕層為3PE防腐蝕層,補口采用熱收縮帶補口;1處管道的防腐蝕層為含聚氨酯泡沫的防腐蝕保溫層;1處站內管道的防腐蝕層為聚丙烯冷纏帶+環氧底漆。所開挖調查管道的基本信息如下:
A管道服役時間為22年,2018年內檢測結果表明,補口位置發生了腐蝕,而2012年內檢測結果表明補口位置沒有明顯腐蝕跡象。這說明隨著服役時間的延長,該管段補口位置的腐蝕風險升高。補口位置通常會出現陰保屏蔽,所以該位置發生SCC的概率增大,且該管道服役時間超過了20年,達到了SCC的高發年限。因此,選擇了5處典型的補口腐蝕位置進行開挖檢測。其中,距離上游壓氣站20km內4處、存在交流干擾位置1處。
在B管道上選擇了容易產生額外應力的石方區補口位置。
在C管道上選擇了距離壓縮機較近的管道出站焊縫位置,該處運行壓力較大、溫度高、壁厚變化容易導致應力集中。
在D管道上選擇了發生陰極保護屏蔽、導致管道發生微生物腐蝕的補口位置。
考慮到腐蝕檢測的需要、操作方便性和可視化效果,采用DPT-5型探傷滲透劑檢測裂紋位置,并采集了部分腐蝕樣品進行了物相分析。
A管道:補口位置的典型防腐蝕層和補口腐蝕形貌如圖1a所示,腐蝕以均勻腐蝕為主,腐蝕產物為棕褐色鐵銹,主要成分為Fe3O4和α-FeOOH,與大氣腐蝕產物類似,表明補口位置的腐蝕主要是由埋設位置沙土中的濕氣進入補口導致。打磨除銹后的裂紋滲透檢測結果如圖2a所示,僅在個別位置有很小的點蝕坑,點蝕深度在0.2mm左右,沒有發現裂紋類缺陷。
B管道:補口位置典型防腐蝕層和腐蝕形貌如圖1b所示,腐蝕產物為黃褐色浮銹,管道沒有發生明顯的點蝕。腐蝕產物的主要成分為α-FeOOH,部分為SiO2雜質,這表明該位置的腐蝕也主要是濕氣進入補口導致的。打磨除銹后的裂紋滲透檢測結果如圖2b所示,沒有發現點蝕或者裂紋類缺陷。
C管道:焊縫位置防腐蝕層形貌和腐蝕形貌如圖1c所示,在聚丙烯冷纏帶防腐蝕層底部存在翹邊和脆化的現象,但內部紅色底漆基本良好,沒有明顯的腐蝕跡象。打磨后的裂紋滲透檢測結果如圖2c所示,沒有發現點蝕或者裂紋類缺陷。
D管道:補口位置的腐蝕形貌如圖1d所示,腐蝕產物為灰黑色黏稠物質,管道存在明顯的點蝕,且點蝕坑深度較大,達管道壁厚的70%。腐蝕產物的主要成分為FeCO3和FeS,是典型的厭氧環境硫酸鹽還原菌腐蝕產物,同時腐蝕產物中還含有部分β-FeOOH,該物質主要在富含氯離子的環境中產生。這表明該環境中的氯離子加速了細菌腐蝕。打磨除銹后的裂紋滲透檢測結果如圖2d所示,除了較大的點蝕坑外,補口局部位置還存在深度1mm左右的點蝕坑,沒有發現明顯的裂紋類缺陷。
(a) A管道 (b) B管道
(c) C管道 (d) D管道
圖1 不同調查點管道的防腐蝕層和腐蝕形貌
(a) A管道 (b) B管道
(c) C管道 (d) D管道
圖2 不同調查點管道裂紋的滲透檢測結果
上述現場調查結果表明,所調查管線的補口位置均未發生SCC現象。
02 管道外腐蝕開挖調查結果
收集分析了2015-2020期間開展的總共98處管道外腐蝕調查結果。現場調查檢測均未發現管道表面有裂紋類缺陷,具體調查信息和結果如表1所示。其中管道防腐蝕層主要為3PE,防腐蝕層類型中的其他是指聚丙烯冷纏帶或瀝青。調查結果表明,在發生外腐蝕的管道中,陰保屏蔽或者保護不足的有62處,存在機械損傷的有33處,發生明顯點蝕的有43處。陰保不足或屏蔽導致管道發生腐蝕是管道發生SCC的必要條件,機械損傷導致的應力集中可明顯增大管道發生SCC的風險。而調查結果表明,在上述易發生SCC的管道位置均未發現SCC現象,這表明目前國內埋地長輸管道SCC的風險較低。
表1 2015-2020管道外腐蝕調查結果
03 環焊縫排查檢測結果
針對事故風險高的環焊縫補口位置,中石油自2018年起開展了環焊縫排查工作,將需要排查的環焊縫定位、開挖、去除補口防腐蝕層并打磨后,采用超聲相控陣、超聲衍射時差法、磁粉、滲透和X射線等無損檢測技術,對焊縫位置的缺陷進行詳細的檢測,并對檢測出的缺陷定性、定量、分級和評價。
目前,總共已完成3萬多處環焊縫開挖檢測工作,截至2019年底共發現了180多處裂紋類缺陷,但通過滲透或者磁粉檢測發現的表面開口裂紋僅3處,且都是單一裂紋。其中,兩處焊縫表面裂紋沿管道軸向擴展,焊縫位置沒有腐蝕跡象:裂紋1位于管道的1點鐘位置,長度7mm,裂紋2位于11點半位置,長度8 mm,裂紋形貌如圖3所示。
(a) 裂紋1
(b) 裂紋2
圖3 焊縫表面裂紋
由于焊縫表面沒有腐蝕跡象,所以這兩處裂紋主要由焊接和應力集中導致。另一處存在表面裂紋的補口位置有浮銹,射線檢測時發現了3mm左右的裂紋,去除浮銹后再次進行滲透檢測時,裂紋消失,這表明該處裂紋很淺。該處補口位置土壤較為干燥,補口熱收縮套黏結力合格(大于80N/cm),腐蝕產物僅為一層浮銹,不存在明顯的點蝕,發生腐蝕的風險低。且該位置管線運行壓力為6.7MPa,壁厚17.5mm,管徑1016mm,管道環向受力僅為194MPa,為管道屈服強度(485MPa)的40%,受力較低,因此該位置出現SCC的風險較低,該裂紋由焊接導致的可能性較大。
以上分析表明,環焊縫排查發現的裂紋多數為內部裂紋而非表面開口裂紋,僅有3處表面開口裂紋,其中兩處裂紋位置不存在腐蝕,1處裂紋位置發生腐蝕和SCC的可能性很小,因此可判定這3處裂紋不是SCC導致的裂紋。環焊縫排查結果表明,現階段國內管道補口位置發生SCC的風險較低。
原因分析
上述國內管道SCC相關調查結果表明,目前國內尚未發現典型的管道高pH或者近中性pH的SCC,SCC風險較低。國內外大量的現場調查和試驗研究數據表明,管道SCC只有在應力、環境和材質3個因素的協同作用下才會發生,風險隨著管道運行年限延長而增加,且SCC只可能在因涂層破損而發生腐蝕的位置發生。目前,國內管SCC風險較低的原因主要有以下幾點:
01 國內在役管道外腐蝕風險低
通常采用防腐蝕涂層加陰極保護的方式抑制土壤對埋地長輸管道的腐蝕,目前在使用的管道外防腐蝕層有瀝青、煤焦油瓷漆、聚乙烯纏帶、三層聚乙烯(3PE)和熔結環氧粉末(FBE)等。其中,3PE防腐蝕層由于其優良的絕緣性、耐腐蝕、抗滲透和耐破壞性能,自20世紀90年代引入國內后,在陜京管道、西氣東輸和中俄東線等重大管道工程中得到了廣泛應用,成為國內長輸埋地管道應用最多的外防腐蝕層,3PE防腐蝕層管道占長輸埋地管道總里程的90%以上。同時,還有少部分管道采用了FBE防腐蝕層,其他類型防腐蝕層管道基本停用。FBE防腐蝕層與陰極保護兼容性很好,不會發生SCC,而3PE防腐蝕層管道存在由陰保屏蔽導致近中性pH SCC的風險。然而近年來的腐蝕調查結果表明,即便3PE防腐蝕層出現剝離,管體上暫未出現由大面積剝離失效導致的陰極保護屏蔽的情況。國內3PE防腐蝕層管道發生SCC的主要為補口、劃傷、硌傷等容易產生陰保屏蔽、陰保不足或雜散電流干擾的位置。目前我國針對外腐蝕開展的外檢測和針對管體缺陷開展的內檢測頻率較高,一般3~5年開展一次外檢測和內檢測,且每次檢測后都制定了針對防腐蝕層和外腐蝕的開挖修復計劃,并開展了專項的陰極保護問題或雜散電流干擾的治理工作,使得管道發生外腐蝕的風險明顯降低,從而降低了SCC發生的風險。
02 管道服役時間較短
SCC的發生需要較長的裂紋萌生和孕育時間,國外統計資料表明,對于瀝青、纏帶和煤焦油瓷漆類等現場涂覆施工的管道,通常在管道運行20年左右進入SCC高發期。一方面,相對于其他防腐蝕層,3PE防腐蝕層的抗老化能力強,SCC裂紋的萌生和擴展需要的時間更長。另一方面,目前國內管道服役時間大多不滿20年,大部分管道未進入SCC高發期。
03 管道運行壓力相對較低
國外SCC案例分析表明,應力腐蝕通常發生在運行壓力大于管線鋼屈服強度60%的管段。國內大部分管道的設計壓力管線鋼屈服強度的60%~70%,但實際運行壓力一般低于設計壓力,主要輸氣管道運行壓力如表2所示。可見,只有陜京一線和西一線的實際服役壓力大于管線鋼屈服強度的60%,此外國產管線鋼的屈服強度一般高于標準要求,如X80管線鋼屈服強度的實測值通常偏高,高于標準要求的555MPa,因此管道實際運行壓力高于管材屈服強度60%以上的情況較少,管線鋼不具有發生SCC所需的應力條件。
表2 國內主要輸氣管道運行壓力
雖然目前國內3PE防腐蝕層管道發生SCC的風險較低,然而防腐蝕層的涂覆質量差別較大及施工過程中可能遭受的外力破壞等都可能使3PE防腐蝕層存在局部破損和較為嚴重的涂層剝離情況,另外其絕緣電阻高,容易屏蔽陰極保護電流,導致剝離涂層下管道發生腐蝕。此外,3PE防腐蝕層管道補口位置大多采用液態環氧加熱收縮帶的結構,投產后這種結構補口發生失效的比例較大,補口位置容易發生陰極保護屏蔽導致管道腐蝕。
調查結果表明,大量補口存在腐蝕跡象。室內試驗結果表明,在陰保屏蔽的自腐蝕條件下,管線鋼存在發生近中性pH SCC的可能性。隨著服役年限的增加,3PE防腐蝕層管道存在較高的SCC風險。
結合國內管道服役現狀,建議現階段采取以下措施降低3PE防腐蝕層管道發生SCC的風險:
(1)繼續加強外腐蝕控制,通過定期開展外檢測和內檢測,修復破損涂層,防止出現3PE防腐蝕層發生大面積剝離腐蝕的情況;
(2)根據埋設土壤環境,對在役的X70和X80鋼級管道設定合適的陰極保護電位范圍,避免發生析氫;
(3)在日常外腐蝕開挖檢測工作中,重點關注防腐蝕補口、劃傷、硌傷、凹陷、環境干濕交替和石方區等SCC高風險位置,并開展裂紋檢測工作;
(4)對運行20年以上的管線開展SCC直接評價,建立SCC位置識別模型,積累SCC高風險位置識別經驗;
(5)管道運行和啟停輸過程中,盡量減少壓力波動范圍、升降壓速度和次數。
結束語
國內現有SCC案例分析和管道補口、環焊縫和外腐蝕開挖調查結果分析表明,國內尚未發現典型的埋地管道SCC案例,已發生的管道SCC主要與材料制造缺陷、焊接缺陷和機械損傷有關。目前,國內3PE防腐蝕層埋地管道外腐蝕控制較好,服役時間較短和服役壓力較低,因此管道發生SCC的風險較低。但國內3PE防腐蝕層管道存在較多的剝離和補口失效問題,易產生陰極保護屏蔽導致管道腐蝕,隨著服役時間的延長,管道存在發生近中性pH SCC的風險。建議通過加強外腐蝕控制,防止高強鋼陰極析氫導致的氫脆,減少運行壓力波動,開展針對性SCC調查和直接評價工作,降低SCC風險,保障管道的安全運行。
免責聲明:本網站所轉載的文字、圖片與視頻資料版權歸原創作者所有,如果涉及侵權,請第一時間聯系本網刪除。
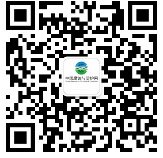
官方微信
《腐蝕與防護網電子期刊》征訂啟事
- 投稿聯系:編輯部
- 電話:010-62316606-806
- 郵箱:fsfhzy666@163.com
- 腐蝕與防護網官方QQ群:140808414