摘要:
鎂合金的比熱容和相變潛熱均比鋁合金低,在壓鑄時冷卻快、流動性差,容易產生欠鑄、缺肉等缺陷。通過提高鎂合金加熱溫度和模具溫度,增加壓射速度能大幅降低廢品率。
近年來, 人們對產品輕量化的要求越來越高,尤其對汽車提出了進一步減輕重量,降低燃耗和排放,以及提高駕駛安全性和舒適性要求,而鎂合金材料的使用正好迎合了這一發展趨勢。鎂合金性能的不斷改善及壓鑄技術的顯著進步,使得壓鑄鎂合金的用量顯著增長。
1.產品概況
汽車轉向支架產品3D模型見圖1,輪廓尺寸為92mm×94mm×61mm,產品平均壁厚
圖1
4.5mm,材料為AZ91D,凈質量為114g,是典型鎂合金壓鑄件。該產品結構較為復雜,模具有上、下、左、右4個側滑塊。由于產品功能需要,零件許多部位原先圓角過小,不利于零件成形。
2.廢品分析
根據統計數據,該產品廢品率為23%。對259373件廢品進一步分析發現,欠鑄250378件,占96.53%;缺肉8995件,占3.47%。如圖2所示,再現了在充型遠端部位的欠鑄問題。
圖2
3.欠鑄分析
壓鑄過程中出現欠鑄主要有合金液流動性不良、澆注系統不合理、排氣不暢三種情況。產品開發初期對模具澆注系統及排氣系統利用CAE作過模擬并在調試階段進行過優化,澆注系統及排氣應該沒有大的問題。零件材料為鎂合金AZ91D,其比熱容和相變潛熱均比鋁合金低,冷卻快。分析認為合金液流動性不良是產品產生欠鑄缺陷的主要原因。
下面對合金液流動性不良進一步詳細分析。
(1)合金液氧化嚴重,流動性下降 由于澆注系統及溢流系統的存在,再加上不合格的產品,在連續的壓鑄生產過程中一般會產生50%以上的回爐料。由于鎂合金材料熔煉時的防護性要求非常高,工廠無滿足要求的熔化爐,不具備精煉條件,實際生產過程中回爐料被直接加入保溫爐,操作者僅對合金液表面的浮渣進行簡單清理。相比于精煉的成品合金錠,回爐料氧化嚴重,流動性差,是產品欠鑄的主要原因之一。
(2)合金澆注溫度及模具溫度過低 溫度是壓鑄過程中的重要工藝參數,為了滿足良好的充型條件,保證壓鑄件的成形質量,必須選用恰當的合金澆注溫度和模具溫度。本產品采用冷室壓鑄機生產,要求合金溫度在660~680℃,為了方便控制和測量,一般控制和保證爐內合金液的溫度。為了保證澆注溫度的穩定性,鎂合金壓鑄專用保溫爐為長方形,爐膛分為澆注腔和熔化腔,中間連通,合金錠從熔化腔加入后一般不會降低澆注腔內合金溫度。保溫爐設定溫度為670℃,用便攜式測溫儀測量加料前后澆注腔內合金溫度,數值如下:加料前663℃;加料0.5min后662℃;加料3min后648℃,加料后溫度明顯降低。
在鎂合金壓鑄中,理想的加熱方式是用模溫機通過熱油對模具進行加熱,熱油不間斷地通過模具內的管道,從內部對模具進行加熱,使模具達到需要的平衡溫度。導熱油的功能像熱交換器,使模具溫度保持在一定范圍內。這種加熱方式,模具的溫度穩定而均勻,能有效地提高產品質量,延長模具壽命,而且使生產節拍穩定。鎂合金壓鑄過程中模具的溫度一般在1 8 0 ~ 2 8 0 ℃。轉向支架的模溫機設定在240℃,用紅外測溫儀測量連續生產時的模具溫度,動模在190~200℃,靜模在170~180℃,靜模溫度明顯偏低。以上數據顯示,合金液溫度及模具溫度偏低,壓鑄過程中容易產生欠鑄、冷隔等缺陷。
(3)內澆道流速過低 因生產轉向支架的壓鑄機系統本身未帶有顯示壓射曲線功能,壓鑄機快壓射速度通過流量閥控制,流量閥開啟大小在壓鑄機上按比例顯示,無法對應出相應的快壓射速度,先用壓射曲線測試儀測試出快壓射流量與快壓射速度對應關系,見表1。從表1可以看出,快壓射流量由60%逐步提高到80%的過程中,快壓射速度逐步提高,最高速度能達到6m/s。過去生產中,轉向支架的快壓射流量設定在60%,即壓射速度在3m/s左右,此時內澆道合金液流速為72m/s,該速度能滿足鋁合金零件的壓鑄要求,但未能達到鎂合金零件需要的高速度,這也是產品欠鑄的主要原因之一。
4.對策及驗證
(1)回爐料與成品合金錠分別作原料生產比較 因為鎂元素化學特性較活潑,很容易被氧化,在無特殊除渣和精煉工藝的條件下,壓鑄中使用回爐料作原材料時鎂合金液流動性比成品鎂合金錠差。為了驗證原材料流動性對鎂合金轉向支架欠鑄缺陷的影響,在不同批次分別用回爐料(50%)與成品合金錠生產,其余工藝參數保持不變,統計欠鑄廢品率分別為:回爐料23.3%,成品合金錠19.1%。可以發現,采用成品合金錠作原料時,合金流動性比回爐料要好,欠鑄比例明顯下降。
(2)提高合金液溫度 為驗證合金液溫度對鎂合金支架廢品率的影響,穩定合金液溫度為690℃,其余工藝參數保持不變進行生產,原材料分別采用回爐料及合金錠各生產一批。統計欠鑄廢品率分別為:回爐料生產造成的廢品率為16.3%;成品合金錠13.5%。對比先前合金液溫度為660℃時統計的欠鑄廢品率不難發現,合金液溫度升高,不管是采用回爐料還是成品合金錠,欠鑄廢品率都明顯下降。其中采用成品合金錠生產批次的工件質量最好,廢品率最低。
(3)提高模具溫度 由于模具溫度受合金液溫度的影響很大,模溫機分別設定為240℃、280℃,合金液溫度分別設定為660℃、690℃,分四批次分別對模具實際溫度進行現場監控,其結果見表2。
由表2可看出,合金液溫度提高30℃后,模具溫度也相應地提高了20℃左右,但是把模溫機溫度提高40℃后模具溫度只提高了5℃左右。分析認為模具加熱流道設計存在一定問題,提高模溫機設定溫度未能達到提高模具溫度的目標。
(4)提高快壓射速度為進
進一步驗證快壓射速度對廢品率的影響,將快壓射流量由原生產時的68%提高到78%,即快壓射速度由3.6m/s提高到5.3m/s左右,采用不同的原材料,分別用不同的合金液溫度進行生產,其余工藝參數保持不變,分8批次進行欠鑄廢品率統計,結果見表3。
表3顯示,隨著合金液溫度提高,欠鑄廢品率降低,同時適當提高快壓射速度也能大幅降低欠鑄廢品率。在提高合金液溫度和快壓射速度的條件下,可以克服回爐料流動性差的問題,采用成品合金錠生產對降低廢品率有一定好處,但降低幅度不大。提高快壓射速度后,由于內壓增大,零件飛邊較大,增加了后續清理難度,這可以適當降低增壓壓力及增壓速度來解決。
5.結語
合金液溫度和模具溫度提高后,合金液流動性增加,充型能力大大提高,欠鑄廢品率明顯降低。同時,適當提高快壓射速度也能大幅降低欠鑄廢品率。采用成品合金錠生產能降低一定廢品率,但降低幅度不大。改善壓鑄工藝條件后,解決了回爐料流動性差、廢品率高的問題,廢品率由過去的23.30%下降到現在的3.70%,給企業帶來了可觀的經濟效益。
更多關于材料方面、材料腐蝕控制、材料科普等方面的國內外最新動態,我們網站會不斷更新。希望大家一直關注中國腐蝕與防護網http://www.ecorr.org
責任編輯:龐雪潔
投稿聯系:編輯部
電話:010-62313558-806
中國腐蝕與防護網官方 QQ群:140808414
免責聲明:本網站所轉載的文字、圖片與視頻資料版權歸原創作者所有,如果涉及侵權,請第一時間聯系本網刪除。
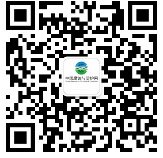
官方微信
《中國腐蝕與防護網電子期刊》征訂啟事
- 投稿聯系:編輯部
- 電話:010-62316606-806
- 郵箱:fsfhzy666@163.com
- 中國腐蝕與防護網官方QQ群:140808414