公用系統由燃料氣管網、氣柜、火炬、可燃氣體排放管網和水封罐等組成,擔負著為各生產裝置提供燃料氣、收集和排放各裝置的低壓燃料氣以及處理各裝置在開停工過程中和緊急情況下排放的無法利用的燃料氣的任務,是裝置異常狀態下緊急放空的安全保護系統,更是燃料氣回收利用、減少環境污染的節能環保系統 。某石化公司公用系統的二火炬至硫磺高壓燃料氣管線2008 年 12 月投用,2011 年開始出現腐蝕問題,2014 年頻繁發生腐蝕減薄和穿孔泄漏,共計發生嚴重腐蝕減薄或穿孔泄漏 14 次,更換管線 6 次,更換彎頭39 個、直管線2 078 m,局部管線腐蝕速率高達 6 mm/a,嚴重影響了公用系統的正常運行。
1 管線腐蝕情況介紹
1. 1 管線參數及運行記錄
該高壓燃料氣管線為二火炬至硫磺高壓燃料氣管線,于 2008 年 12 月投用,分為四段,全長3 458 m,其具體參數見表 1。
二火炬至硫磺高壓燃料氣管線 2008 年 12 月投用,2011 年停工檢修時發現某處 1 m 長直管段上有 4 處腐蝕穿孔泄漏;2012 年 3 月又發現某水平管段出現腐蝕穿孔泄漏,且有 3 個彎頭背彎處腐蝕減薄至 4. 4 mm 左右;2014 年,該管線的直管段及彎頭部位共計發生嚴重腐蝕減薄或腐蝕穿孔泄漏 14 次;2015 年,該管線發生腐蝕穿孔泄漏 2次,且都在彎頭部位。
1. 2 管線腐蝕調查
經統計,二火炬至硫磺高壓燃料氣管線在2011 年至 2015 年共計發生腐蝕減薄或泄漏 19次,腐蝕減薄或泄漏部位既有直管段又有彎頭。該管線全長 3 458 m,彎頭數量多達 200 個,其中頂部彎頭 58 個、底部彎頭 52 個、水平彎頭 90 個,管線彎頭迫使工藝物料流態發生變化,對彎頭部位形成沖刷腐蝕,特別是管道底部彎頭(低點向上爬升彎頭)腐蝕減薄較為嚴重。圖 1 是現場割下的底部彎頭內壁的腐蝕形貌。由圖 1 可見,底部彎頭沖刷腐蝕明顯,腐蝕減薄區域主要集中在彎頭背彎處,該區域腐蝕坑較為密集、且積垢較多,而彎頭內彎及兩側腐蝕減薄較輕微。
高壓燃料氣管線的腐蝕不只發生在彎頭部位,直管段的腐蝕也很嚴重,主要發生在管道低點易沉積燃料氣凝液的部位。將現場一段腐蝕減薄嚴重的管道沿軸向剖開,發現管線下半部分積液部位紅褐色腐蝕垢層較厚,清除垢層后管道表面腐蝕坑較為明顯,且腐蝕坑相互連接形成一條腐蝕溝槽,如圖 2 所示。管線上半部分腐蝕輕微,測厚無明顯腐蝕減薄。
圖 1 底部彎頭內壁腐蝕形貌
圖 2 直管段剖開后的腐蝕形貌
2 腐蝕原因分析
2. 1 腐蝕介質分析
二火炬至硫磺高壓燃料氣管線的工藝介質為高壓燃料氣,其主要成分是氫氣(體積分數為39%)、甲烷(體積分數為 12%)、氮氣(體積分數為 9%)、異丁烷(體積分數為 9%)、丙烷(體積分數為 6%)、異戊烷(體積分數為 6%)、乙烷(體積分數為 5%)、正丁烷(體積分數為 4%)、氧氣(體積分數為 1%)、硫化氫(3 000 mg/L)、水氣,還含有少量的二氧化碳、氯化氫等。
從高壓燃料氣的成分組成來看,其除了氫氣、氮氣及烷烴外,還含有硫化氫、氯化氫、二氧化碳等少量的腐蝕介質,由于高壓燃料氣中含有少量的水氣,其在管線底部彎頭及直管段低點部位容易積聚,給硫化氫、氯化氫、二氧化碳等腐蝕介質提供了水相環境,形成了 H 2 S-HCl-H 2 O 和 H 2 S-CO 2 -H 2 O 等濕硫化氫腐蝕體系,給管線底部彎頭及直管段低點部位造成嚴重的腐蝕減薄。
2. 2 濕硫化氫腐蝕
2.2.1 H 2 S-H 2 O 體系腐蝕
低溫環境中硫化氫對金屬管道不會造成腐蝕,但在有水存在的環境中會對金屬造成嚴重的腐蝕。硫化氫溶于水形成弱酸,并離解出 H+與金屬發生反應,硫化氫在水中的電離方程式為:
H 2 → S HS-+ H+HS → -S 2 - + H+
金屬管道在硫化氫水溶液中會發生電化學反應:
陽極反應:
Fe -2e → Fe 2 +
Fe 2 + + HS → -FeS + H+
陰極反應:
2H+ +2e → 2H
從上述反應過程來看,濕硫化氫(硫化氫水溶液)對金屬管道的可以形成以下兩種腐蝕,均勻腐蝕和應力腐蝕開裂。濕硫化氫的均勻腐蝕主要是管道金屬在硫化氫水溶液中的不斷溶解、腐蝕減薄,硫化物應力腐蝕開裂(SSCC)是一個硫化氫電離的電化學反應,水的存在是必須條件,除水以外,其他腐蝕介質如氯離子和 CO 2 的存在增加了硫化氫水溶液的腐蝕性,因而,也容易增加硫化物應力腐蝕開裂的傾向,但有時氯離子和 CO 2 的存在也會使腐蝕機理改變,而成為應力腐蝕開裂的主要影響因素 。
2. 2. 2 H 2 S-HCl-H 2 O 體系腐蝕
H 2 S-HCl-H 2 O 腐蝕是煉化裝置常見的電化學腐蝕形式,腐蝕溶液中的氯離子具有很強的穿透性,能破壞金屬表面的鈍化膜,因此它的存在會加重管線金屬的腐蝕。由于該腐蝕環境中同時具有 H 2 S 和 HCl 兩種腐蝕介質,在電化學腐蝕反應中,兩者相互促進,造成反應循環發生,最終導致管道腐蝕減薄、甚至穿孔,其化學反應式如下:
H 2 → S + Fe FeS + H 2→ FeS +2HCl FeCl 2 + H 2 S→ Fe + HCl FeCl 2 + H 2FeCl 2 + H 2 → S FeS +2HCl
2. 2. 3 H 2 S-CO 2 -H 2 O 體系腐蝕
燃料氣中含有的 H 2 S 和 CO 2 等腐蝕性介質在有水相環境中對設備造成電化學腐蝕,在這一腐蝕體系中,H 2 S 起到決定性的作用,CO 2 僅發生局部腐蝕,而 H 2 S 則發生應力腐蝕及氫腐蝕,并且兩者相互促進而加速腐蝕的進行,H 2 S 的腐蝕機理同 2. 2. 1,CO 2 的腐蝕機理為:
CO 2 溶于水形成碳酸,可直接與金屬發生反應,反應方程式如下:
Fe + H 2 CO → 3FeCO 3 + H 2
相同的 pH 值下,H 2 CO 3 比 HCl 對鋼鐵的腐蝕要嚴重得多,低碳鋼 CO 2 的腐蝕速率達7 mm/a,甚至更高,腐蝕產物為 FeCO 3 ,新鮮的 FeCO 3 為暗黑色,曝露在空氣中會被氧化為氧化鐵,顏色由黑變黃。
鋼鐵在 H 2 S-CO 2 -H 2 O 環境中不僅發生一般的電化學腐蝕,還會發生氫腐蝕和應力腐蝕開裂。
H 2 S 的腐蝕是氫去極化腐蝕,吸附在鋼表面的HS-促進陰極放氫加速,同時硫化氫又能阻止原子氫結合成分子氫,使氫原子聚集在鋼材表面,加速氫向鋼中的滲入和擴散,引起鋼的氫脆和氫鼓泡。當鋼材有殘余應力(或承受外拉應力)和鋼材內部的氫致裂紋同時存在時,則發生硫化物應力腐蝕開裂。
2. 3 垢下腐蝕
燃料氣管線的工藝介質成分復雜,不但含有氫氣、氮氣、烷烴、氧氣等,還含有硫化氫、氯化氫、二氧化碳等少量的腐蝕介質,而高壓燃料氣中含有的少量凝結水為各種腐蝕介質提供了腐蝕環境。從微觀上來看金屬表面是凹凸不平的,且存在凹坑或夾雜,這些缺陷部位往往先遭受腐蝕,由于高壓燃料氣管線腐蝕介質種類較多,形成了多種腐蝕體系,在這些缺陷部位生成多種腐蝕產物,并覆蓋在管道金屬表面形成垢層,導致垢下腐蝕。
高壓燃料氣管線的腐蝕為金屬在酸性溶液中的腐蝕,且其中含有大量的溶解氧,因此,其電化學腐蝕反應式為:
陽極反應:
2Fe -4e→ 2Fe 2 +
陰極反應:
4H++ O 2 +4e → 2H 2 O
垢下電化學腐蝕反應過程中,垢層下金屬成為電化學腐蝕反應的陽極區域,垢層外成為電化學腐蝕反應的陰極區域,陽極區域是鐵的溶解反應,而垢外陰極區域則是吸氧反應。垢下電化學腐蝕發生初期,由于垢下空間狹小造成酸性溶液在此滯留,腐蝕反應開始發生,垢下金屬生成Fe 2 + ,短時間內垢下氧消耗完畢,陰極反應停止。這時,由于垢下缺氧,垢外富氧,便形成氧濃差電池。氧的還原反應開始在垢外繼續進行,垢下只發生陽極反應,金屬不斷溶解生成 Fe 2 + ,出現過剩的正電荷,為了保持電中性,垢外氯離子遷移到垢下,與金屬離子形成 FeCl 2 ,并發生水解,生成腐蝕性較強的鹽酸,反應式如下:
FeCl 2 +2H 2 → O Fe(OH) 2 ↓ +2H++ Cl-
反應結果使垢下 pH 值下降、溶液酸性增加,垢下呈現深淺不一的蝕坑,隨著蝕坑的生長,在蝕坑周圍生成鐵銹及其他沉積物,使蝕坑內介質處于滯流狀態,這樣就構成了閉塞電池。閉塞區內處于鹽酸環境,加快了垢下金屬的溶解速度。對應地,垢外氧的還原速度也增加,使外部表面得到陰極保護,而加速了垢下金屬的溶解,垢下金屬離子進一步過剩又促使氯離子的遷入,形成 FeCl 2 ,水解后形成鹽酸,使垢下酸性溶液濃度增加,加速了金屬的不斷腐蝕,如此循環,便形成了垢下腐蝕發展的自催化過程,可見,造成垢下腐蝕加速進行的根本原因是閉塞電池的自催化作用。
在閉塞電池的自催化作用下,燃料氣管線金屬表面出現了大量的腐蝕坑,隨著腐蝕反應的加速進行腐蝕坑深度不斷增加,短時間內就會導致燃料氣管線穿孔泄漏。
3 結論及建議
3. 1 結 論
(1)高壓燃料氣中的硫化氫、氯化氫和二氧化碳等腐蝕介質形成了濕硫化氫腐蝕體系,對高壓燃料氣管線的底部彎頭(低點向上爬升彎頭)及直管段低點凝液部位造成嚴重結垢及坑蝕。
(2)燃料氣管線的腐蝕是濕硫化氫復雜腐蝕體系及垢下腐蝕共同作用的結果,其相互促進,共同發展,最終導致高壓燃料氣管線彎頭背彎處、直管段積液部位發生了嚴重的腐蝕減薄及泄漏。
(3)造成高壓燃料氣管線垢下腐蝕加速的根本原因是閉塞電池的自催化作用,而垢下腐蝕體系中的氧含量、氯離子則是加速陽極金屬鐵不斷溶解的主要影響因素,在閉塞電池的自催化作用下,金屬表面出現大量的腐蝕坑,且蝕坑深度不斷增加,導致燃料氣管線腐蝕穿孔。
3. 2 防護建議
(1)完善加工方案,建立脫硫裝置或堿洗設備,降低公用系統燃料氣管線中的硫化氫質量濃度至 200 mg/m 3 以下,減緩設備及管線腐蝕。
(2)加強公用系統燃料氣管線的低點排凝工作。選材應主要以碳鋼為主,評選耐蝕涂料進行防護。
(3)對燃料氣管線進行腐蝕監測,在管道的凝結水部位取樣,對 H 2 S,CO 2 -3和 HCl 等腐蝕介質每周進行一次分析;在管道彎頭、三通、管線低點等易腐蝕部位每季度進行一次管道測厚和每月進行一次管道腐蝕檢查。
更多關于材料方面、材料腐蝕控制、材料科普等方面的國內外最新動態,我們網站會不斷更新。希望大家一直關注中國腐蝕與防護網http://www.ecorr.org
責任編輯:殷鵬飛
投稿聯系:編輯部
電話:010-62313558-806
中國腐蝕與防護網官方 QQ群:140808414
免責聲明:本網站所轉載的文字、圖片與視頻資料版權歸原創作者所有,如果涉及侵權,請第一時間聯系本網刪除。
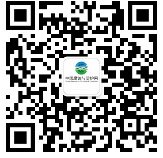
官方微信
《中國腐蝕與防護網電子期刊》征訂啟事
- 投稿聯系:編輯部
- 電話:010-62316606-806
- 郵箱:fsfhzy666@163.com
- 中國腐蝕與防護網官方QQ群:140808414