0前 言
隨著航天技術的發展,對航天器的輕量化需求非常迫切,特別是對于密度低、比剛度和比強度高、導熱性和減震性能好以及鑄造性能優良的鎂合金材料有著強烈的需求。但是,鎂合金具有極高的電化學活性,用于航天器結構材料使用時面臨著嚴重的腐蝕問題,特別是新建設的海南文昌發射場所處的環境是典型的熱帶海洋大氣環境,具有高溫高濕、大氣鹽霧濃度高腐蝕性強的特點。其年平均溫度24.1 ℃;相對濕度大于86%,遠高于大氣腐蝕性分類中規定的最高濕度τ5等級;Cl-質量濃度為0.01~0.05 mg/m3,平均值0.03 mg/m3,Cl-沉降速率0.06~1.37 mg/(100 cm2?d),平均值0.54 mg/(100 cm2?d),氯化物等級為S1~S2級,大氣腐蝕等級為C4級,屬高腐蝕性大氣。與現有的酒泉、西昌和太原3個內陸發射場相比,在海南文昌發射場發射的空間站等航天器中使用的鎂合金材料面臨更嚴酷的腐蝕環境及潛在的腐蝕問題,對航天器鎂合金材料提出了更高的防腐蝕要求。
同時,鎂合金作為航天器內各類電子設備機箱結構材料時,其內部各類元器件工作時產生大量的熱,由于航天器處在真空環境無法進行通風散熱,各類設備工作時產生并傳導至鎂合金的熱量只能通過輻射的方式散失出去,因此要求鎂合金材料表面具有高發射率的熱控特性。但鎂合金材料自身的發射率較低(εH≤0.30),必須在其表面制備高發射率層,以滿足輻射換熱的熱控需求。與微弧氧化等電化學制備高發射率熱控膜層的工藝相比,通過在鎂合金材料表面噴涂涂料制備防腐-熱控一體化涂層的工藝具有對產品尺寸、形狀適應性強、可實施性強等優點,在航天器鎂合金材料表面防腐-熱控處理方面具有廣闊的應用前景。本文研制了一種噴涂型防腐-熱控一體化涂層,研究了涂層組分配比、涂層厚度對涂層性能的影響,并對涂層防腐和熱控性能進行了測試和實驗研究。
1 實驗部分
1.1 涂層制備
1.1.1 原材料及設備
主要原材料包括羥基樹脂、脂肪族聚異氰酸酯、高發射率顏料、消光粉、功能助劑、混合溶劑[m(甲基異丁基酮)∶m(碳酸二甲酯)∶m(丙二醇甲醚乙酸酯)=60∶30∶10]等。
1.1.2 涂層制備
涂料制備時,首先將混合溶劑、功能助劑用電動攪拌器混合均勻后加入高發射率顏料及消光粉等采用砂磨法進行均質化處理制備漿料,然后在漿料中加入羥基樹脂,分散均勻后用150~200目銅網過濾,按n(—NCO)∶n(—OH)=1.05∶1加入脂肪族聚異氰酸酯,并將涂料的黏度調整為13~17 s(涂-4#杯),采用空氣噴涂法在基材表面制備涂層。涂層室溫條件下固化24 h。
1.2 涂層性能測試及實驗
為驗證鎂合金防腐-熱控一體化涂層的性能優劣,從以下7個方面對涂層性能進行測試及實驗:
(1)太陽吸收比(αS):用分光光度計(帶積分球)按《航天器熱控涂層試驗方法 第2部分:太陽吸收比測試》(GJB 2502.2—2006)規定的方法測試。
(2)半球發射率(εH):用AE輻射計按《航天器熱控涂層試驗方法 第3部分:發射率測試》(GJB 2502.3—2006)規定的方法測試。
(3)附著力按《色漆和清漆 拉開法附著力試驗》(GB 5210—2006)進行測試。
(4)真空揮發性測試按《真空條件下材料揮發性能測試方法》(QJ 1558A—2012)規定進行,在真空度優于7×10-3 Pa環境下,將試樣加熱至125 ℃并保持24 h,使試樣出氣,測試涂層的總質量損失(TML)和可凝揮發物(CVCM)。
(5)鹽霧試驗按《涂層檢驗方法 涂層耐鹽霧檢驗方法》(QJ 990.12—86)中規定的方法進行。采用3.5%氯化鈉水溶液間歇噴霧,即在溫度(40±2) ℃下連續噴霧8 h,然后停止噴霧及加熱,在靜止和密封狀態下保持16 h,24 h為1個周期,共進行42個周期(1 008 h)試驗。
(6)濕熱試驗按《漆膜耐濕熱測定法》(GB/T 1740—2007)中規定的方法進行。試驗溫度為(47±1) ℃,相對濕度為(96%±2%),試驗周期為504 h。
(7)冷熱交變性能按《航天器熱控涂層試驗方法第8部分:熱循環試驗》(GJB2502.8—2006)進行。即在-196 ℃下保持5 min,而后在-100 ℃下保持5 min,循環100次。
2 實驗結果與討論
2.1 涂層組分配比研究
鎂合金防腐-熱控一體化涂層采用底漆+面漆的復合涂層體系。底漆選用已在航天器上得到成熟應用的鋅黃丙烯酸聚氨酯底漆;面漆為以羥基樹脂與脂肪族聚異氰酸酯交聯制得的聚氨酯為黏結劑,以高發射率顏料、消光粉、功能助劑等組分采用均質化工藝配制而成。在面漆涂層組分配比優化研究中,依次以高發射率顏料、消光粉和功能助劑用量為考察因素,采用砂磨工藝進行涂料配制,并以空氣噴涂將涂料噴涂于鎂合金試片表面,涂層厚度控制在50 μm左右。從涂層太陽吸收比、半球發射率、涂層光澤、涂料細度等方面對各組分用量進行優化。
2.1.1 高發射率顏料用量對涂層性能影響
圖1所示為高發射率顏料用量對涂層熱物理性能影響。
從圖1可以看出,高發射率顏料用量對涂層熱物理性能有較大影響。隨著高發射率顏料用量的增加,涂層太陽吸收比和半球發射率均升高,當高發射率顏料用量高于8%時,涂層αS穩定在0.96左右,εH穩定在0.89左右;當其用量在10%以上時,涂料貯存穩定性變差。綜合高發射率顏料用量對涂層太陽吸收比、半球發射率及貯存穩定性的影響,高發射率顏料用量確定為8%。
2.1.2 消光粉用量對涂層性能影響
圖2所示為消光粉用量對涂層光澤影響。
從圖2可以看出,消光粉用量對涂層光澤有較大影響。隨著消光粉用量的增加,涂層光澤度先下降后穩定在62%左右;當消光粉用量高于8%時,涂層光澤度變化較小。因此,消光粉用量確定為8%。
2.1.3 功能助劑用量對涂料性能影響
圖3為功能助劑用量對涂料細度影響。
從圖3可以看出,功能助劑用量對涂料細度有較大影響。隨著功能助劑用量的增加,涂料細度先下降后穩定在30 μm左右;當功能助劑用量高于6%時,涂層細度趨于一穩定值。
表1所示為功能助劑用量不同時,涂層真空揮發性能測試數據。
從表1中可以看出,功能助劑用量對涂層真空揮發性有較大影響,功能助劑用量越高,制備涂層的TML和CVCM值也越高,可能是由于各類助劑中含有小分子物質,在真空條件下揮發導致的。當其含量高于6%時,涂層TML值超過了航天器要求TML≤1%的要求。因此,綜合功能助劑用量對涂料細度和真空揮發性能的影響,確定功能助劑用量為6%。
綜合實驗結果和分析,在鎂合金防腐-熱控一體化涂層面漆中,高發射率顏料用量優選8%,消光粉用量優選8%,功能助劑用量優選6%。表2給出了鎂合金防腐-熱控一體化涂層面漆的組分最佳配比。
2.2 涂層厚度對涂層性能影響研究
面漆涂層組分配比和均質化工藝確定后,涂層厚度是影響涂層防腐、熱控性能非常重要的一個參數。
在已噴涂20 μm底漆的MB2鎂合金試片表面制備不同厚度的面漆,測試涂層太陽吸收比、半球發射率、附著力、耐沖擊性并進行溫水72 h浸泡、NaCl溶液24 h浸泡試驗。
圖4所示為面漆厚度對涂層熱物理性能影響。
從圖4可以看出,面漆涂層厚度對涂層熱物理性能有較大影響。隨著厚度的增加,涂層太陽吸收比和半球發射率均升高,當涂層厚度>35 μm時,涂層αS穩定在0.96左右;厚度>50 μm時,εH穩定在0.90左右。
表3為不同面漆厚度的試片性能測試結果。
從表3的測試結果可知,隨著面漆厚度的增加,涂層的附著力、耐溶劑性能、耐溫水浸泡性能以及耐NaCl溶液浸泡性能都逐漸提高,當面漆厚度達到40μm后,上述性能基本穩定。綜合上述實驗結果,當面漆厚度>50 μm后,涂層性能可滿足預期指標要求;但為了保證涂層的最佳性能,避免涂層施工過程的不確定性,將面漆厚度控制在50~80 μm,涂層總厚度控制在70~100 μm。
2.3 涂層性能檢測及實驗
本文對鎂合金防腐-熱控一體化涂層熱物理性能、防腐性能、附著力、真空放氣性、耐冷熱交變等性能進行了檢測和實驗,以確認涂層的各項性能是否滿足航天器鎂合金材料表面的防腐、熱控需求和使用需求。
表4為鎂合金防腐-熱控一體化涂層性能檢測結果。
圖5為42個周期(1 008 h)的鹽霧試驗、504 h的濕熱試驗后MB2及ZM5支架表面涂層狀態。
從圖5可以看出,MB2及ZM5的鎂合金支架表面涂層經鹽霧和濕熱試驗后,支架鎂合金基材無腐蝕,表面熱控涂層無起泡、無脫落、無開裂。
從表4及圖5可以看出,研制的鎂合金防腐-熱控一體化涂層的各項性能指標均達到了預期指標要求,可滿足航天器鎂合金材料表面的防腐、熱控需求和使用需求。
3 結 語
(1)通過涂層組分配比研究,確定涂層組分配比中高發射率顏料用量為8%,消光粉用量為8%,功能助劑用量為6%。
(2)通過面漆厚度對涂層性能影響研究,確定面漆厚度50~80 μm,涂層總厚度70~100 μm。
(3)制備的涂層不僅具有高發射率(εH≥0.88)的熱控特性,同時具有耐濕熱≥504 h、耐中性鹽霧腐蝕≥1 000 h的防腐性能,另外,涂層真空放氣性、耐冷熱交變性能滿足空間環境下使用要求。
更多關于材料方面、材料腐蝕控制、材料科普等方面的國內外最新動態,我們網站會不斷更新。希望大家一直關注中國腐蝕與防護網http://www.ecorr.org
責任編輯:龐雪潔
投稿聯系:編輯部
電話:010-62313558-806
中國腐蝕與防護網官方 QQ群:140808414
免責聲明:本網站所轉載的文字、圖片與視頻資料版權歸原創作者所有,如果涉及侵權,請第一時間聯系本網刪除。
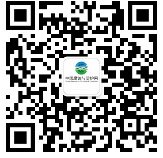
官方微信
《中國腐蝕與防護網電子期刊》征訂啟事
- 投稿聯系:編輯部
- 電話:010-62316606-806
- 郵箱:fsfhzy666@163.com
- 中國腐蝕與防護網官方QQ群:140808414