航空鋁合金常規成形方法包含鑄造,鍛造,焊接,擠壓,軋制等方法。然而,隨著航空鋁合金應用范圍的不斷擴大,航空結構件日漸復雜,各種特種成形方法不斷出現。今天,材料+小編帶你來盤點航空鋁合金特種成形方法的各種方法。
爆炸成形
炸藥可以釋放巨大的能量,雖然大多數炸藥的爆炸都帶有毀滅性,但如果合理的利用炸藥的能量就可以制造我們需要的產品零件。
常用爆炸成形法方法是模具和工件都浸沒在水中,金屬板材由一環形夾固定在模具內,將模具形腔內的空氣抽去使其成為真空狀態,炸藥放置在工件和形腔之間。同時炸藥與工件保持一定的距離,炸藥放置在深水里面,爆炸時產生的沖擊波通過水傳到工件,并使工件在模具形腔內成形,這種高能率成形方法還能用于厚度比較大的板材。
如北美航空公司用爆炸加工法生產了“土星”宇宙火箭助推器用的直徑10m(33ft)的2014鋁合金球形封頭瓜瓣零件,航空通用動力公司也用此法生產了厚度為3.175mm(0.125in)直徑1371mm(54in)的AMS6434高強度鋼封頭。中國研制了最大厚度40~50mm、直徑3m的大形封頭。
金屬爆炸加工引人注目之處在于:能源不受限制,設備投資少,應用非常廣泛。
譬如,可以把炸藥做成各種形狀,以適應待成形零件輪廓所需要的爆炸壓力分布。可以方便地改變炸藥的放置位置或選用不同品種的炸藥將壓強從幾千兆帕降低到一般壓力加工的數值。如果要求增大能量,只須增加炸藥量即可。爆炸成形示意圖如下所示:
爆炸成形周期長,適合尺寸較大且不盡相同的小批量零部件的生產。爆炸成形的模具可以選用便宜或易成形材料,但也可以制成可長久使用的模具,模具材料包括:鋁、木材、混泥土、塑料鐵和鋼。如果用彈性模量低的材料(如塑料)制作的模具,在成形過程中將大大降低金屬板的回彈量,從而保證成形工件更高的精度。
炸藥的用量取決于系統類型和成形部件所需的壓力大小,爆炸時所產生的沖擊波向各方向傳播,而大部分沖擊波的能量沒有被工件吸收。
另外有一種罐裝彈藥或桶裝彈藥的密閉系統,這種系統通常用于制造比噴射系統更小的零件,所有的能量都作用在模腔的內壁上,罐裝彈藥所釋放的能量迫使金屬板材按照模腔內壁形狀成形。
使用爆炸成形時,安全很重要,特別是在密閉系統中,所以模具失效是一個需高度關注的問題。
電液成形
電液成形也稱放電成形,是航空鋁合金鈑金成形中一種比較獨特的高能成形工藝,該成形過程的能量由細金屬線的燃燒來提供,該成形工藝適用于相對較小的成形零件。
制造過程中用環形夾將金屬板材毛坯固定在模具頂部,將板材下部的模腔抽成真空狀態,金屬絲熔化后,存儲在電容內的電能就通過電極和導線放電,通過水產生的沖擊波將工件壓至模腔內成形。
電液成形產生的沖擊波能量相對較小,產生的沖擊力也較小,所以適合用于薄板的成形,每放電一次,連接兩電極的電線就需更換一次,這種成形方法的生產效率都比較低。
電磁成形
電磁成形是通過磁力激增來成形板材,是一種常用的高能成形工藝,電磁成形也被稱作磁脈沖成形。
其成形原理是:將通電線圈放置在靠近板材的地方,連接兩電極的通電線圈中電流發生驟變,于是在線圈周圍就會產生磁場,當導體處于變化的磁場中時,該導體內部將會產生電流。
由于導電工件與通電線圈距離很近,而通電線圈所產生的磁場發生變化,于是工件內部就產生了渦電流,工件內部的渦電流又產生與線圈磁場相排斥的磁場(可參考楞次定律),該排斥力作用在工件上并使其成形。
通電線圈可以根據所期望的效果放置在工件內表面,也可放置在工件上表面。許多電磁成形用來擴大管道管徑或擴大管道某個部位的管徑,該成形方法一般用于成形較薄的鈑金零件,如航空結構中常用的管形件。
液壓成形
液壓成形也被稱為“內高壓成形”,它的基本原理是以管材作為坯料,在管材內部施加超高壓液體同時,對管坯的兩端施加軸向推力,進行補料。在兩種外力的共同作用下,管坯材料發生塑性變形,并最終與模具型腔內壁貼合,得到形狀與精度均符合技術要求的中空零件。
板材液壓成形是采用液體作為傳力介質,代替剛性凸模或者凹模,使金屬板材在壓力作用下貼模,加工所需形狀曲面零件的成形工藝。由于液體的運用,使得成形壓力均勻,零件回彈小,表面質量和尺寸精度高,模具成本低。因此,液壓成形得到廣泛的適用。
1、管材液壓成形技術
管材液壓成形技術,也叫內高壓成形技術,它是將管材置于模具中,利用管材內部充入的混合液體產生的壓力,使材料膨脹最后流入模具內。
2、橡皮囊液壓成形
橡皮囊液壓成形原理是橡皮隔膜將高壓液體和板料分隔開,省略了另外一個半模,充入的高壓液體將橡皮隔膜脹形,其脹形壓力使板坯貼模成形。瑞典 Avure 公司根據此技術研制了 Quintus 橡皮囊液壓機,它采用鋼帶纏繞增強技術,減輕了成形機框架的重量,增強了液室的強度,其成形壓力為 80~140MPa。
3、液壓拉深成形
液壓拉深成形是采用高壓液體介質代替剛性模具,使板材在液體介質壓力作用下貼模成形為所需零件。歐美、日本等國家開展此技術較早,并應用于航空發動機、運載火箭整流罩等復雜零件成形中。如日本的 AMINO 公司采用此技術生產了飛機唇口和鋁合金車身零件。
與傳統的沖壓工藝相比,液壓成型工藝在減輕重量、減少零件數量和模具數量、提高剛度與強度、降低生產成本等方面具有明顯的技術和經濟優勢,在航空、航天等領域,減輕結構質量以節約能量是人們長期追求的目標。液壓成形是實現結構輕量化的一種先進制造技術。
對于空心變截面結構件,傳統的制造工藝是先沖壓成形兩個半片,然后再焊接成整體,而液壓成形則可以一次整體成形沿構件截面有變化的空心結構件。
與沖壓焊接工藝相比,液壓成形技術和工藝有以下主要優點:
減輕質量,節約材料。對于汽車發動機托架、散熱器支架等典型零件,液壓成形件比沖壓件減輕20%~40%;對于空心階梯軸類零件,可以減輕40%~50%的重量。
減少零件和模具數量,降低模具費用。液壓成形件通常只需要1套模具,而沖壓件大多需要多套模具。液壓成形的發動機托架零件由6個減少到1個,散熱器支架零件由17個減少到10個。
可減少后續機械加工和組裝的焊接量。以散熱器支架為例,散熱面積增加43%,焊點由174個減少到20個,工序由13道減少到6道,生產率提高66%。
提高強度與剛度,尤其是疲勞強度,如液壓成形的散熱器支架,其剛度在垂直方向可提高39%,水平方向可提高50%。
降低生產成本。根據對已應用液壓成形零件的統計分析,液壓成形件的生產成本比沖壓件平均降低15%~20%,模具費用降低20%~30%。
溫熱成形
溫熱成形是利用材料加熱后塑性和延伸率提高,屈服強度下降的特性進行板材成形的技術,并且成形溫度低于材料的再結晶溫度,減少了能源消耗。例如,5000 和 6000 系列的鋁合金從20℃升到 320℃,其材料伸長率從20% 增加到 80%。溫熱成形技術可以提高板材的成形性,并得到均勻厚度的零件,適合小批量零件的生產。
溫熱成形有以下三種成形工藝:
(1)等溫溫熱成形,需要預先加熱模具和板材,使其達到板材成形所需溫度,然后進入壓力機中進行成形。
(2)預成形-熱處理-精加工成形。板材在室溫下預成形,然后將預成形零件采用感應線圈局部加熱進行退火處理以去除應力,最終室溫成形。
(3)非等溫溫熱成形。溫熱的板材(200~300℃鋁合金)在常溫模具下即可成形全尺寸零件,不需要預加熱模具。國外對熱成形工藝技術研究較早,歐洲已有設備生產企業提供沖壓生產線,如德國Schuler公司和瑞典AP&T能夠提供全套熱沖壓設備,如下圖所示。
噴丸成形
噴丸成形技術是利用高速彈丸撞擊金屬板材表面,使受撞擊表面及其下層金屬發生塑性變形而延伸,促使板材彎曲變形從而達到所需外形的一種成形方法,是飛機壁板類零件的主要成形方法之一。
目前,噴丸成形技術在波音公司和空客公司已經發展成為一種相當成熟的壁板成形手段,德國 KSA公司采用噴丸成形技術成形Ariane5動力模塊框架的錐形板,為空客 A380 提供了機身整體壁板制造的數控噴丸強化和噴丸成形設備,美國 MIC 公司(Metal ImprovementCompany)采用預應力噴丸成 A380 超臨界機翼下壁板。我國于2006年成功實現了ARJ21超臨界機翼整體壁板噴丸成形。
隨著噴丸技術的發展,涌現了一些新的噴丸技術:激光噴丸、超聲噴丸和高壓水噴丸技術。
激光噴丸代替傳統的金屬、陶瓷或者玻璃噴丸,其激光能量脈沖直接作用于零件特定部位,產生的沖擊波能夠壓縮金屬表面,提高其表面裂紋和腐蝕的抵抗性能,增加材料疲勞強度。激光噴丸還可以用于成形較大的復雜輪廓部件的成形,如美國的MIC公司采用此成形技術成形波音747-8飛機機翼蒙皮面板。
多點模具成形技術
多點模具成形技術是把模具曲面離散成有限個高度可調的基本單元,用這些單元代替傳統模具進行三維曲面成形,柔性多點模具,用于飛機蒙皮拉伸成形。它根據零件的外形,通過數字化程序控制成形工具按照一定軌跡逐步成形零件。
英國劍橋大學、美國西北大學和坎布爾印度理工學院等均對漸進成形進行了研究。國內的研究機構,如西北工業大學、哈爾濱工業大學和南京航空航天大學等也均對此技術進行了研究。
蠕變時效成形
“蠕變”一般是指材料在高溫和低于材料宏觀屈服應力條件下發生的緩慢塑性變形行為。蠕變時效成形技術(時效應力松弛成形技術),是將人工時效和成形制造相結合,利用了鋁合金材料在彈性應力作用下在一定溫度發生蠕變變形,從而得到一定形狀的結構件。由于時效成形鋁合金結構件殘余應力水平低、回彈量小、產品精度高、適用大型蒙皮類鈑金成形的特點,而被廣泛應用于航空領域。
一般來說,蠕變時效成形過程包括3個階段:
1) 加載。在室溫下,對整體壁板施加載荷,使其發生合適的彈性變形,與此同時使壁板固定在具有設定目標型面的模具或工裝上;
2) 人工時效。將整體壁板和工裝/模具一起放入熱壓罐,然后將溫度升高至人工時效溫度,并保溫一定的時間。在保溫的過程中,由于材料受到人工時效、蠕變和應力松弛的耦合作用,材料內部微觀組織發生顯著變化,部分彈性變形逐漸轉化為了塑性變形。同時,在人工時效的過程中,材料完成了時效強化的過程,材料的性能得到改善;
3) 卸載。在人工時效結束后,去掉預先的工裝約束。由于加載過程中的彈性變形不可能全部轉化為塑性變形,因此,材料將發生一定程度的回彈,從而得到預定形狀的結構件。
與傳統噴丸成形相比,蠕變時效成形工藝具有以下優點:
1) 蠕變時效成形時,外加應力一般低于材料的屈服應力,蠕變時效成形過程減小了構件引發損傷甚至破裂的可能性。同時,可以顯著地降低構件發生加工裂紋、空洞等宏微觀損傷的概率;
2) 利用材料的蠕變特性和時效強化,在成形的同時,完成了對構件材料的人工時效強化過程,材料的微觀組織得到改善,力學性能得到提升;
3) 蠕變時效成形的成形精度高,而且具有可重復性和成形效率高的特點。在成形具有復雜結構的構件時,僅需一次熱循環就可以達到構件外形所需的精度,外形精度誤差小于1mm;
4) 蠕變時效過程中,構件內部殘余應力基本上可完全被釋放。因此,成形構件的尺寸相對穩定。此外,蠕變時效還可以有效地降低焊縫處殘余應力,增強材料抗腐蝕的能力,延長構件的服役壽命。
由于蠕變時效成形技術具有上述優點,美歐等西方發達國家很早就開始研究蠕變時效成形技術。
其研究成果已被廣泛應用于飛機整體壁板的制造中。例如,美國B-1B超音速戰略轟炸機機翼的上下壁板、“彎流”Ⅴ 和“彎流”Ⅳ公務機的馬鞍形上機翼蒙皮和“大力神”Ⅳ火箭整體結構壁板等。
其中, B-1B機翼整體壁板曾被認為是飛機工業發展史上制造的結構最復雜、尺寸最大的機翼壁板。該壁板長度15.24m,外端寬0.9m,根部寬2.74m,厚度從2.54mm逐漸增加至63.5mm, 而且展向有整體加強桁條等復雜細微結構。采用蠕變時效成形制造的壁板表面光滑,形狀精度較高,其裝配貼合度可有效控制在0.25mm以內。
在民用飛機方面的也得到了應用,麥道、空客和波音等早期機型已經部分應用了蠕變時效成形技術。例如:MD82、A380和A330/340等大型民機的整體壁板,已部分采用蠕變時效成形工藝。
結束語
隨著先進制造技術的發展和新型材料的開發應用,航空鋁合金零件精度更高、質量更輕、強度更高,形狀更復雜,成形效率更快,并且減少了原材料和能源的消耗,縮短了開發周期、極大地減少了制造成本。航空鋁合金成形設備朝著大型化、精密化、智能化、集成化、成套化和柔性化發展。
更多關于材料方面、材料腐蝕控制、材料科普等方面的國內外最新動態,我們網站會不斷更新。希望大家一直關注中國腐蝕與防護網http://www.ecorr.org
責任編輯:王元
投稿聯系:編輯部
電話:010-62313558-806
中國腐蝕與防護網官方 QQ群:140808414
免責聲明:本網站所轉載的文字、圖片與視頻資料版權歸原創作者所有,如果涉及侵權,請第一時間聯系本網刪除。
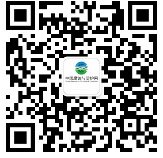
官方微信
《中國腐蝕與防護網電子期刊》征訂啟事
- 投稿聯系:編輯部
- 電話:010-62316606-806
- 郵箱:fsfhzy666@163.com
- 中國腐蝕與防護網官方QQ群:140808414