概述
從上世紀(jì)50年代至今,研究者在高溫防護(hù)涂層領(lǐng)域的研究已經(jīng)取得了很大的成果。其發(fā)展也從傳統(tǒng)意義上的鋁化物涂層發(fā)展到現(xiàn)在的熱障涂層、智能型涂層,數(shù)量也從單層發(fā)展為多層,成分從合金涂層發(fā)展到目前的陶瓷涂層以及復(fù)合型涂層,還可以通過添加活性元素進(jìn)一步提升其性能。
PART.1 高溫防護(hù)涂層的發(fā)展
高溫防護(hù)涂層的發(fā)展和耐熱材料的發(fā)展密不可分,尤其是與渦輪噴氣發(fā)動機(jī)涂層材料性能的改進(jìn)相關(guān)。
渦輪是飛機(jī)和航天飛機(jī)噴氣發(fā)動機(jī)的關(guān)鍵部件,工作運(yùn)轉(zhuǎn)條件非常嚴(yán)苛,易受到高溫氧化和熱腐蝕。在組成渦輪的零部件中,葉片的工作溫度最高,受力最復(fù)雜,也最容易損壞。為了保護(hù)這些熱端部件在高溫下免受氧化腐蝕和延長其使用壽命,研究者對高溫結(jié)構(gòu)材料和高溫涂層進(jìn)行了大量的研究,取得了較好的成果。
高溫防護(hù)涂層的發(fā)展歷程
PART.2 高溫防護(hù)涂層的作用
高溫合金一般要求必須同時具備兩方面的性能要求,即優(yōu)異的高溫力學(xué)性能和抗高溫腐蝕性能。但實(shí)際上對同一種合金,這兩方面的性能之間有時是相互矛盾的,不可能同時達(dá)到最優(yōu)化。要解決二者之間的矛盾,僅僅靠高溫合金基體材料本身的工藝改進(jìn)是不能滿足現(xiàn)代航空航天飛機(jī)發(fā)展的性能要求的,必須通過高溫防護(hù)涂層即在合金表面沉積合金涂層,即在合金涂層表面再施加氧化物陶瓷涂層來解決。通常涂層都較薄,主要起保護(hù)基體金屬不受高溫腐蝕的作用。而對高溫強(qiáng)度的要求則主要由基體合金本身來承擔(dān)。由于基體合金和防護(hù)涂層可以單獨(dú)地設(shè)計,所以施加防護(hù)涂層的合金部件就可以既保持合金足夠的高溫強(qiáng)度而表面又具有優(yōu)異的耐高溫腐蝕性能。
一般高溫涂層分為三種:
擴(kuò)散涂層
通過與基體接觸并與其內(nèi)的確定元素反應(yīng),從而改變了基體外層的涂層稱為擴(kuò)散涂層。這類涂層的典型代表是在鎳基、鉆基合金上熱擴(kuò)散滲鋁,分別獲得 NiAl,CoAl涂層。
覆蓋涂層
在基體表面沉積含保護(hù)性金屬元素的涂層為包覆涂層。利用各種物理的或化學(xué)的沉積手段在合金表面直接制備一層保護(hù)性薄膜,這層薄膜就是包覆涂層。
熱障涂層
熱障涂層是由陶瓷隔熱面層和金屬粘結(jié)底層組成的涂層系統(tǒng)。熱障涂層采用金屬結(jié)合底層的目的是為改善陶瓷面層和基體合金的物理相容性能以及抗氧化保護(hù)基體的作用。、
熱障涂層的作用主要在于:
①在導(dǎo)致冷卻器件蠕變性能下降的同時,降低金屬的溫度,延長其使用壽命;
②大大降低疲勞應(yīng)變,延長其使用壽命;
③降低發(fā)動機(jī)葉片冷卻所需要的空氣體積,從而提高其使用效果,延長其使用壽命。
PART.3 高溫防護(hù)涂層制備與性能要求
防護(hù)涂層主要起著保護(hù)基體合金免受高溫氧化的作 用,涂層材料本身必須具有優(yōu)良的抗高溫氧化性能。根據(jù)相關(guān)合金氧化機(jī)理的研究,涂層材料完全可參照那些具有良好抗氧化性的合金來設(shè)計。但還應(yīng)注意到,涂層作為薄膜材料,它是依附于合金表面起作用的。涂層與合金材料的最大不同是涂層會發(fā)生退化,即由于涂層與基體合金在界面處發(fā)生的互擴(kuò)散,容易使涂層內(nèi)的抗氧化性元素較快地消耗掉。其次,涂層與基體合金界面的結(jié)合要牢固,它必須能在合金表面穩(wěn)定地存在。此外,涂層制備的難易程度也是實(shí)際應(yīng)用時必須考慮的重要方面。將高溫防護(hù)涂層分成兩種:擴(kuò)散涂層 (Diffusioncoatings)和包覆涂層(Overlaycoatings)。
01 擴(kuò)散涂層
通過與基體接觸并與其內(nèi)確定元素反應(yīng)從而改變了基體外層形成的涂層為擴(kuò)散涂層。這類涂層的典型代表是在鎳基、鉆基合金上熱擴(kuò)散滲鋁,分別獲得NiAl,CoAl涂層。在鉬和鎢上熱擴(kuò)散滲硅,則分別得到MoSi2 和WSi2涂層。因NiAl,CoAl氧化形成Al2O3,而MoSi2和WSi2氧化形成SiO2,所以這類涂層具有良好的抗氧化性能。
以滲鋁涂層為例來說明擴(kuò)散涂層的形成原理。在鎳、鉆、鐵基合金經(jīng)擴(kuò)散滲鋁過程表面形成金屬間鋁化物,如 阝一NiAl,阝一CoAl或FeAI等。由于這些金屬間化合物氧化時形成 A1203,基體合金因?yàn)橛辛诉@層擴(kuò)散涂層,從而具有了好的抗氧化性能。
制備鋁化物涂層的擴(kuò)散滲鋁工藝成熟,方法多樣 化。主要的滲鋁方法有固體粉末滲鋁、熱浸鍍鋁、料漿滲鋁、氣體滲鋁、噴鍍滲 鋁、電泳滲鋁、電解滲鋁、快速電加熱滲鋁、化學(xué)氣相沉積(ChemicalVaporDeposition,CVD)滲鋁等多種。其中,固體粉末滲鋁工藝最為成熟。
制備工藝
1)固體粉末滲鋁
固體粉末滲鋁又稱為包裝滲鋁。滲鋁時,將滲鋁工件埋在粉末狀的滲鋁劑中,然后加熱到850℃ 一1050℃,保溫數(shù)小時即可。滲鋁劑一般由三部分組成:
鋁粉或鐵鋁合金粉,是提供鋁原子的原料;
氧化鋁,是一種稀釋填充劑,又兼有防止金 屬粉末粘結(jié)的作用;
氯化銨,是一種催滲劑(活化劑)。
鋼的滲鋁過程:
即在高溫下,NH4Cl分解釋放出HCl氣體。HCl和鋁粉或FeAI粉中的鋁反應(yīng)形成氣態(tài)AlCl3。AlCl3擴(kuò)散向滲件表面,并和基體元素鐵反應(yīng),鋁原子被置換出來。第三個反應(yīng)一般情況下不發(fā)生,但在金屬表面作催化劑的條件下是有可能發(fā)生的。在較低溫度下,滲劑中鋁的活度較高,涂層的生長主要以鋁元素向內(nèi)擴(kuò)散為主,因而稱為內(nèi)擴(kuò)散或高活度滲鋁。反之,溫度較高時,鋁的活度相對于鐵的活度較低,基體中的鐵向外擴(kuò)散,在表面和鋁形成化合物相。這種滲鋁被稱為外擴(kuò)散或低活度滲鋁。
固體粉末滲鋁的優(yōu)點(diǎn)是設(shè)備簡單,操作方便,特別適用于機(jī)械的零部件。其缺點(diǎn)是滲劑容易被氧化,工件尺寸受限制,對工件表面粗糙度有一定影響。
2) 熱浸鍍鋁
熱浸鍍鋁主要用于鋼鐵件表面,提高其耐蝕性和抗氧化性。它是把預(yù)處理過的工件浸入熔融的鋁液中,經(jīng)保溫一定時間取出,使其表面滲入一層鋁。
熱浸鍍鋁層形成過程如下圖所示:
熱浸鍍鋁工藝一般采用“改進(jìn)的森吉米爾法”,即讓經(jīng)過酸洗、洗滌和干燥后的鋼鐵件首先通過 900℃ 一1000℃的氫氣爐,然后再浸入 705℃ 一760℃的鋁浴中。保溫時間一般為 10min一20min。為改善滲鋁層的韌性和表面質(zhì)量,可以 往鋁液中加人一定量的鉬、錳、鋅、鈉及稀土元素等。
3)CVD滲鋁
利用CVD技術(shù)滲鋁具有極大優(yōu)越性。這是一種非接觸擴(kuò)散滲鋁技術(shù)。滲鋁時,一種確定成分的氣體可以預(yù)先在滲鋁爐外制取,然后被導(dǎo)入爐內(nèi)的腔體里,并與工件表面反應(yīng)形成涂層。
CVD法也常被用來沉積除鋁之外的其他元素,如鉻和硅。此外,鉑和鈀等貴金屬元素也可以用 CVD法沉積在基體合金的表面上,這是制備Pt一Al或 Pd一Al 涂層時的先前步驟。
02 覆蓋涂層
覆蓋涂層按材料屬性可分成金屬涂層、陶瓷涂層兩類.
金屬涂層
制備這類涂層可選擇的技術(shù)手段有多種,包括物理氣相沉積(PhysicalVapor Deposition,PVD)、熱噴涂、電鍍、化學(xué)鍍、激光熔覆等。
其中PVD和熱噴涂應(yīng)用最多。PVD是利用熱蒸發(fā) 或輝光放電、弧光放電等物理過程,在基材表面沉積所需涂層的技術(shù)。它包括真空蒸發(fā)鍍膜、離子鍍膜和濺射鍍膜。濺射和電子束一物理氣相沉積(EB一PVD)是制備MCrAIY涂層的主要手段 。
熱噴涂是利用熱源將噴涂材料加熱熔化或軟化,靠熱源自身的動力或外加的壓縮氣流,將熔滴霧化或推動熔粒成噴射的粒束 ,以一定速度噴射到基體表面形成涂層的工藝方法。熱噴涂可分成三種類型:氣體火焰噴涂、等離子噴涂 (PlasmaSpraying,PS)和電弧噴涂。其中,等離子噴涂技術(shù)在高溫氧化領(lǐng)域應(yīng)用較多,可用以制備 MCrAIY涂層和陶瓷涂層。
陶瓷涂層
在合金表面制備一層 SiO2或Al2O3膜,也可以起到隔離氣體介質(zhì)、降低合金氧化速度的作用。由于氧化物與基體合金的線膨脹系數(shù)相差較大,合金表面直接制備的氧化物涂層在溫度循環(huán)條件下容易破裂,如當(dāng)涂層較厚時,在制備過程就會發(fā)生這種情形,因此,Si02或Al203作為防護(hù)涂層使用時,往往用于短時間需要防護(hù)的場合。
實(shí)際使用中復(fù)合氧化物陶瓷涂層應(yīng)用更普遍。這類涂層的制備方法有 EB一PVD、反應(yīng)濺射、射頻濺射、等離子噴涂、化學(xué)氣相沉積、溶膠一凝膠法(Sol一Gel法)、自蔓延(Self-PropagationHigh-Temperature Synthesis,SHS)、微弧氧化法等。
03 性能要求
高溫防護(hù)涂層應(yīng)盡可能滿足以下要求:
優(yōu)良的抗氧化和抗熱腐蝕性能;
良好的組織穩(wěn)定性;
良好的結(jié)合力;
涂層內(nèi)缺陷少以及制備工藝簡單;
涂層具有低的韌脆轉(zhuǎn)變溫度;
但是實(shí)際制備的涂層不可能完全符合上述要求 ,因而在制備高溫防護(hù)涂層時,首先考慮要保證涂層的抗氧化和抗熱腐蝕性能,其次再考慮盡可能滿足其他方面的要求 。
免責(zé)聲明:本網(wǎng)站所轉(zhuǎn)載的文字、圖片與視頻資料版權(quán)歸原創(chuàng)作者所有,如果涉及侵權(quán),請第一時間聯(lián)系本網(wǎng)刪除。
-
標(biāo)簽: 高溫防護(hù)涂層, 高溫合金, 熱浸鍍
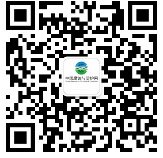
官方微信
《腐蝕與防護(hù)網(wǎng)電子期刊》征訂啟事
- 投稿聯(lián)系:編輯部
- 電話:010-62316606-806
- 郵箱:fsfhzy666@163.com
- 腐蝕與防護(hù)網(wǎng)官方QQ群:140808414