一文解析鋼的滲碳 將金屬或者合金工件放置在活性介質(zhì)中加熱或者保溫條件,讓一種或幾種元素滲入其表層改變其化學(xué)成分、組織和性能,稱(chēng)為金屬的化學(xué)熱處理。這種化學(xué)熱處理實(shí)際上是通過(guò)介質(zhì)高溫裂解物在金屬材料表面進(jìn)行分解、吸附、固溶、化合反應(yīng),使元素進(jìn)入金屬表面形成一種或多種合金元素的滲層,能夠提高工件“表硬內(nèi)韌”的性能要求。 今天我們主要解析滲碳,順便跟滲氮做一對(duì)對(duì)比,方便大家區(qū)別這兩種化學(xué)熱處理工藝。
化學(xué)熱處理技術(shù)在現(xiàn)代工業(yè)中被廣泛應(yīng)用,能夠提高金屬工件得表面強(qiáng)度、硬度、耐磨性等力學(xué)性能、抗咬合性能、抗疲勞性能以及特殊的耐蝕性、抗高溫氧化性能等物理化學(xué)性能,同時(shí)工件自身還應(yīng)保持原有的良好的塑韌型等基本性能,從而提高機(jī)器零件在各種復(fù)雜工況下的耐用度。
化學(xué)熱處理的主要特征:
固體擴(kuò)散滲入改變工件表面層的化學(xué)成分,又改變其組織,滲層與基體之間有擴(kuò)散層,獲得單一材料難以獲得的性能或進(jìn)一步提高工件的使用性能。絕大多數(shù)化學(xué)熱處理后對(duì)工件的變形小、精度高、尺寸穩(wěn)定性好的特點(diǎn)。該過(guò)程是一個(gè)復(fù)雜的物理化學(xué)過(guò)程,工藝處理周期較長(zhǎng),對(duì)設(shè)備的要求也比較高。
化學(xué)熱處理的驅(qū)動(dòng)力是濃度梯度。
化學(xué)熱處理形成滲層的結(jié)構(gòu)遵守相圖,其結(jié)構(gòu)是連續(xù)的,屬于冶金結(jié)合。
化學(xué)熱處理的分類(lèi)方法多樣,包括按照元素種類(lèi)、滲入先后順序及滲入時(shí)金屬狀態(tài)進(jìn)行分類(lèi):
定義:
將鋼件置于具有足夠碳勢(shì)的介質(zhì)中加熱到奧氏體狀態(tài)并保溫,使其表層形成一個(gè)富碳層的熱處理工藝。
碳勢(shì):
純鐵在一定溫度下于加熱爐氣中加熱時(shí)達(dá)到既不增碳也不脫碳并與爐氣保持平衡時(shí)的表面含碳量。
目的:
滲碳介質(zhì)在工件表面產(chǎn)生的活性碳原子,經(jīng)過(guò)表面吸收和擴(kuò)散將碳滲入低碳鋼或低碳合金鋼工件表層,使其達(dá)到共析或略高于共析成分時(shí)的含碳量,以便將工件淬火和低溫回火后,提高工件表面的硬度、耐磨性和疲勞強(qiáng)度,同時(shí)保持心部具有一定強(qiáng)度和良好的塑性與韌性。
應(yīng)用范圍:
在機(jī)器制造業(yè)中,有許多重要零件,如汽車(chē)變速箱齒輪、活塞銷(xiāo)、摩擦片等。可以滲碳的鋼一般是碳的質(zhì)量分?jǐn)?shù)為0.12%-0.25%的低碳鋼或低碳合金鋼如20、20Cr、20CrMnTi、20CrMnMo、18Cr2Ni4W等。
根據(jù)滲碳劑的不同,滲碳方法可分為固體滲碳、液體滲碳和氣體滲碳。
(1)固體滲碳---粒狀或膏狀滲碳劑中滲碳。
將工件置于填滿(mǎn)木炭(90%左右)和催滲劑(BaCO3、CaCO3或 Na2CO3等)(10%左右)的固體滲碳箱內(nèi)進(jìn)行的,如圖1所示。固體滲碳在滲碳法中歷史最老,不適于連續(xù)處理大量工件,作業(yè)環(huán)境不良,已有衰退傾向,不過(guò)爐及其他設(shè)備也較簡(jiǎn)單,多種少量的處理也較方便,不至完全絕跡。
圖1 固體滲碳箱
1-滲碳劑 2-工件 3-箱體4~6mm
鐵板 4-泥封 5-試棒?10mm
6-蓋:鐵板厚6~8mm
缺點(diǎn):滲速慢,勞動(dòng)條件差
(2)液體滲碳---鹽浴滲碳
液體滲碳就是在液體介質(zhì)中進(jìn)行的滲碳工藝。
可分為兩類(lèi):一類(lèi)是加有氰化物的鹽浴,另一類(lèi)是不加氰化物的鹽浴。因氰化物有劇毒現(xiàn)已基本不用。不加氰化物的鹽浴由NaCl或KCl、Na2CO3、和(NH2)2CO或木粉組成,如圖2所示。
圖2 井式氣體滲碳爐
1-風(fēng)扇電動(dòng)機(jī) 2-廢氣火焰 3-爐蓋 4-砂封 5-電阻絲 6-耐熱罐 7-工件 8-爐體
優(yōu)點(diǎn):液體滲碳技術(shù)滲層性能優(yōu)良,工藝簡(jiǎn)單,采用無(wú)毒低氰滲劑容易操作,且對(duì)人體危害小,可以廣泛的得到推廣與應(yīng)用
(3)氣體滲碳---有機(jī)含碳?xì)夥铡?/span>
氣體滲碳是指零件在氣體滲碳劑中進(jìn)行滲碳的工藝。氣體滲碳法的生產(chǎn)率高,滲碳過(guò)程容易控制,滲碳層質(zhì)量好,且易實(shí)現(xiàn)機(jī)械化與自動(dòng)化,應(yīng)用最廣。
優(yōu)點(diǎn): 質(zhì)量好, 效率高;
缺點(diǎn): 滲層成分與深度不易控制
原理
1)滲碳介質(zhì)的分解
由介質(zhì)中分解出活性碳原子。滲碳?xì)夥赵诟邷叵路纸獬龌钚蕴荚覽C],即:
注:在供應(yīng)的原料氣組分穩(wěn)定的情況下,只要控制氣氛中的微量組分CO2、H2O、CH4或O2中的任何一個(gè)含量,便可控制上述反應(yīng)達(dá)到某一平衡點(diǎn),從而實(shí)現(xiàn)控制氣氛碳勢(shì)的目的。通常,生產(chǎn)中用露點(diǎn)儀控制H2O含量;用紅外線(xiàn)儀控制CO2含量;用氧探頭法控制O2含量。
2)碳原子的吸收 工件表面吸收活性碳原子,也就是活性碳原子由鋼的表面進(jìn)入鐵的晶格而形成固溶體,或形成特殊化合物。
3)碳原子的擴(kuò)散 被工件吸收的碳原子,在一定溫度下,由表面向內(nèi)部擴(kuò)散,形成一定厚度的滲層。
工藝參數(shù)選擇
1)氣氛碳勢(shì)
一般滲碳件的表面含碳量可在0.6%-1.1%間變化。確定最佳表面碳含量的出發(fā)點(diǎn)首先是獲得最高的表面硬度;其次是使?jié)B層具有最高的耐磨性和抗磨損疲勞性能。研究表明,滲碳層的表面碳的質(zhì)量分?jǐn)?shù)最好在0.8%-1.0%范圍內(nèi)最佳表層碳含量確定后就可根據(jù)表面碳含量與碳勢(shì)的關(guān)系,確定碳勢(shì)。
2)滲碳溫度
滲碳溫度首先影響著分解反應(yīng)平衡,粗略地說(shuō),如果氣氛中的CO2含量不變,則溫度每降低10℃將使氣氛碳勢(shì)增加約0.08%;其次,溫度也影響碳的擴(kuò)散速度,如果氣氛碳勢(shì)不變,溫度每提高100 ℃可使?jié)B碳層深度增加1倍;第三,溫度還影響著鋼中的組織轉(zhuǎn)變,溫度過(guò)高會(huì)使鋼的晶粒粗大。生產(chǎn)上廣泛使用的溫度是900-930 ℃。對(duì)于薄層滲碳溫度可降到880-900 ℃,這主要是為了控制滲碳層深度;而對(duì)于深層滲碳(大于5mm),溫度可提高到980-1000 ℃,這主要是為了縮短滲碳時(shí)間。
3)滲碳時(shí)間
滲碳時(shí)間主要影響滲層深度,同時(shí)也在一定程度上影響濃度梯度。
d—滲層深度(mm);t—滲碳時(shí)間(h);T—滲碳溫度(K)
滲碳工藝參數(shù)的綜合選擇 圖3 氣體滲碳典型工藝曲線(xiàn) ①升溫階段 工件達(dá)到滲碳溫度前的一段時(shí)間,用較低的碳勢(shì); ②高速滲碳階段 正常溫度或更高溫度下,用高于所需表面碳含量的碳勢(shì),時(shí)間較長(zhǎng); ③擴(kuò)散階段 工件降到或維持在正常滲碳溫度下碳勢(shì)降到所需表面碳含量,時(shí)間較短; ④預(yù)冷階段 使溫度降低到淬火溫度,便于直接淬火。 低碳鋼滲碳后,表層含碳量可達(dá)過(guò)共析成分,由表往里碳濃度逐漸降低,直至滲碳鋼的原始成分。 滲碳件緩冷后,表層組織為珠光體加二次滲碳體;心部為鐵素體加少量珠光體組織;兩者之間為過(guò)渡層,越靠近表層鐵素體越少 。一般規(guī)定,從表面到過(guò)渡層一半處的厚度為滲碳層的厚度。 圖4 低碳鋼滲碳緩冷后的顯微組織 表1 典型零件滲碳層厚度確定方法 1.淬火 淬火是為了獲得馬氏體組織,以得到高硬度。通常有三種方法,即預(yù)冷直接淬火、一次加熱淬火和二次加熱淬火。滲碳零件淬火溫度的選擇要兼顧高碳的滲層和低碳的心部?jī)煞矫娴囊蟆T瓌t上,過(guò)共析層的淬火溫度低于Accm,而亞共析層的淬火溫度高于Ac3。如果Accm> Ac3,很容易選擇一個(gè)淬火溫度來(lái)同時(shí)滿(mǎn)足這兩者的要求;果Accm≤Ac3,則很難同時(shí)兼顧。在這種情況下,要根據(jù)對(duì)零件的主要技術(shù)要求、鋼件的心部能否淬透、滲碳后零件的表面含碳量和所采用的淬火方法等綜合考慮加以決定。 圖5 滲碳后的熱處理示意圖 滲碳件常用的淬火方法: ①預(yù)冷直接淬火 對(duì)于碳鋼,預(yù)冷溫度應(yīng)在Ar1~Ar3之間。對(duì)于多數(shù)合金鋼,通常預(yù)冷溫度在820~850℃之間。 ②一次加熱淬火 一般合金滲碳鋼,常采用稍高于Ac3的溫度(820~860℃)加熱淬火。 ③二次加熱淬火 第一次淬火的加熱溫度應(yīng)高于心部的Ac3溫度,第二次淬火主要是為細(xì)化表層組織,溫度選擇稍高于表層的Ac1。 常用方法是滲碳緩冷后,重新加熱到Ac1+30-50℃淬火+低溫回火。 此時(shí)組織為: 表層:M回+顆粒狀碳化物+A’(少量) 心部:M回+F(淬透時(shí)) 2.回火 滲碳件淬火后尚需進(jìn)行低溫回火,回火溫度通常為150~190℃。 3.冷處理 作用是減少或消除殘余奧氏體,從而適當(dāng)提高滲層硬度。由于冷處理生產(chǎn)成本高,又增加了工序,目前生產(chǎn)中除特殊滲碳零件外,一般很少采用。
1)外觀(guān)
工件表面無(wú)氧化、銹蝕、剝落、碰傷、裂紋等。
2)硬度
在淬火、回火后檢驗(yàn),表面硬度、心部硬度及非滲碳區(qū)硬度應(yīng)符合技術(shù)要求。對(duì)滲碳齒輪,JB/T7516-1994規(guī)定表面硬度以分度圓處齒面為準(zhǔn)[1],心部硬度的檢測(cè)部位為齒根圓與輪齒中心線(xiàn)相交處[2]。檢率按規(guī)定執(zhí)行。硬度不合格時(shí),應(yīng)加倍抽檢,仍不合格則視情況進(jìn)行返修或判報(bào)廢。
3)滲碳層深度
常用滲碳層深度檢測(cè)法有以下四種:
①宏觀(guān)斷口分析
將隨爐滲碳的試樣直接淬火,然后打斷,觀(guān)察其斷口。在斷口上滲碳層呈白色瓷狀斷口,未滲碳部分為灰色纖維狀斷口,根據(jù)兩種斷口交界至表面的距離就可以量出滲碳層深度,從而可以確定出爐時(shí)間。
②金相測(cè)量法
滲碳緩冷后的試樣經(jīng)磨制、腐蝕后,在顯微鏡下測(cè)定。碳鋼的滲碳層深度是從表面垂直量至1/2過(guò)渡區(qū)[3],其滲碳層包括過(guò)共析層+共析層+1/2過(guò)渡區(qū), 并要求過(guò)共析與共析區(qū)之和應(yīng)占總層深的75%以上;合金鋼滲層深度是從表面垂直量至出現(xiàn)心部原始組織為止,包括過(guò)共析層+共析層+過(guò)渡區(qū)全部,并要求過(guò)共析與共析區(qū)之和應(yīng)占總層深的50%以上。
③硬度測(cè)量法
根據(jù)GB/T9450-2005進(jìn)行測(cè)量。
④剝層化學(xué)分析法
此法精確可靠,但取樣和分析較麻煩,生產(chǎn)中很少采用。
4)金相組織檢驗(yàn)
一般在淬火、回火后,按有關(guān)行業(yè)標(biāo)準(zhǔn)進(jìn)行檢驗(yàn)。檢驗(yàn)項(xiàng)目包括碳化物(大小、數(shù)量和分布等),馬氏體針的大小及殘余奧氏體數(shù)量多少,心部游離鐵素體的大小和數(shù)量等。
5)裂紋
可靠性要求高的齒輪在熱處理和磨齒后,100%檢驗(yàn),一般齒輪進(jìn)行抽檢。檢驗(yàn)方法有磁粉探傷、超聲波探傷、金相法等。
6)畸變
按圖樣技術(shù)要求進(jìn)行檢驗(yàn)。
[1] 也可用齒頂硬度代替;對(duì)斜齒輪、圓錐齒輪,還可用齒端面硬度代替,但均應(yīng)考慮與齒面硬度的差異。對(duì)無(wú)法用硬度計(jì)檢驗(yàn)的齒輪,可用標(biāo)準(zhǔn)銼刀檢驗(yàn),或用隨爐試樣檢測(cè)。
[2] 心部硬度也可用隨爐試樣檢測(cè)。其他零件心部硬度在距表面三倍滲碳層深度以外處進(jìn)行檢測(cè)。
[3]所謂過(guò)渡區(qū),是指由共析區(qū)內(nèi)側(cè)至心部外側(cè)組織之間的區(qū)域。
(一)常見(jiàn)缺陷
1)表面硬度偏低
2)滲層深度不夠或不均勻
3)金相組織不合格
4)滲碳層內(nèi)出現(xiàn)氧化
5)零件變形超差
6)心部硬度過(guò)高
(二)產(chǎn)生原因
1.表面硬度偏低
可能是表面脫碳,或出現(xiàn)非馬氏體組織,或是表層馬氏體回火抗力低等
2.滲層深度不足或不均勻
深度不足:滲碳時(shí)間過(guò)短;
深度不均勻:爐氣循環(huán)不良或溫度不均勻,往往與爐子設(shè)計(jì)和零件裝爐情況不良有關(guān)。
3.金相組織不合格
不采用過(guò)高的氣氛碳勢(shì);采用細(xì)晶粒鋼;采用一次加熱淬火;采用冷處理;適當(dāng)提高淬火溫度
4.滲碳層內(nèi)氧化
滲碳?xì)夥罩泻蠴2,H2O,CO2等氧化性組分,而鋼中又含有與氧原子親和力比鐵強(qiáng)的合金元素。
5.變形超差
6.心部硬度過(guò)高
(1)硬度
獲得高硬度是滲碳的重要目的之一。滲碳并淬火后零件的表面層硬度可達(dá)58~62HRC。而硬度沿滲碳層的變化規(guī)律,大體上和碳濃度梯度的變化相一致,這是因?yàn)轳R氏體的硬度主要取決于馬氏體的含碳量。
(2)耐磨性
滲碳是提高耐磨性的重要手段之一,滲碳后鋼的耐磨性比普通淬火、回火的中碳鋼耐磨性高得多。
一般硬度升高,耐磨性亦隨之增加,但硬度并非是影響耐磨性的唯一因素。理論與實(shí)踐證明,細(xì)小或隱晶馬氏體和均勻分布的粒狀碳化物組織的表面層具有高的切斷抗力,也具有高的耐磨性。從提高耐磨性角度來(lái)看,碳量高一些好,但過(guò)高會(huì)引起起強(qiáng)度、塑性下降。通常滲碳件表面碳濃度以不超過(guò)1.05%為宜。
(3)強(qiáng)度
ⅰ滲碳層強(qiáng)度 圖6為滲碳層強(qiáng)度與合碳量的關(guān)系。
從圖可以看出,表層含碳且不應(yīng)超過(guò)1.1%C,而在0.8-1.05%C最為合適。滲碳層組織對(duì)強(qiáng)度有著決定性的影響,當(dāng)出現(xiàn)網(wǎng)狀碳化物或粗大馬氏體針和殘余奧氏體過(guò)多時(shí),均會(huì)顯著降低滲碳層的強(qiáng)度。
ⅱ 心部強(qiáng)度 隨著心部強(qiáng)度的增加,滲碳后整個(gè)工件強(qiáng)度亦增加。影響心部強(qiáng)度的主要因素是鋼的淬透性。淬透性愈好,愈易在心部得到低碳馬氏體。其次,心部含碳量愈高,強(qiáng)度也愈高。
圖6 滲碳層強(qiáng)度與含碳量的關(guān)系
(4)塑性
圖7為滲碳層的塑性(用壓痕直徑表示)與含碳量的關(guān)系。常用厚度為3毫米的薄片樣品作滲碳試驗(yàn),用它來(lái)了解滲碳層的塑性與表面層含碳量的關(guān)系。這是因?yàn)閴汉墼龃螅硎緷B碳層的塑性亦增加。實(shí)驗(yàn)發(fā)現(xiàn),含碳量增加會(huì)使?jié)B碳層的塑性下降,當(dāng)含碳量超過(guò)1.1%時(shí),塑性將顯著下降。
圖7 滲碳層的塑性與含碳量的關(guān)系
(5)沖擊韌性和斷裂韌性
鋼經(jīng)滲碳后沖擊韌性和斷裂韌性都會(huì)降低,而且表面碳含量越高、滲層越深,這兩種性能降低得也越多。
(6)疲勞強(qiáng)度
同高頻感應(yīng)加熱淬火一樣,滲碳也可顯著提高鋼的疲勞強(qiáng)度,這是因?yàn)樵诖慊饡r(shí),高碳的滲層發(fā)生馬氏體轉(zhuǎn)變比心部晚,而且其馬氏體的比容比心部大得多,使表層存在較大的殘余壓應(yīng)力。這種殘余壓應(yīng)力可以抵消相當(dāng)一部分由于外加負(fù)載在表層引起的拉應(yīng)力,從而提高疲勞強(qiáng)度。自然,滲層的高強(qiáng)度也有助于疲勞強(qiáng)度的提高。而工件表面壓應(yīng)力的大小則受滲碳層的深度及碳濃度高低的影響。當(dāng)滲碳層濃度以及組織完全相同的條件下,增加滲碳層深度會(huì)提高疲勞強(qiáng)度。但是,在通常的情況下,增加滲層厚度將會(huì)增加表面碳濃度并使組織惡化。所以,增加滲層深度并不一定使疲勞強(qiáng)度增加。
總結(jié):
滲碳可以大大改善鋼的力學(xué)性能,特別是使疲勞強(qiáng)度和耐磨性有明顯提高,因此滲碳是化學(xué)熱處理中最重要最常用的一種有效強(qiáng)化方法。隨著科學(xué)技術(shù)的發(fā)展,滲碳工藝也在不斷發(fā)展。例如,為了縮短滲碳時(shí)間,提高滲碳溫度的辦法已得到應(yīng)用,其溫度可達(dá)980~1080℃。由于真空爐的推廣,也大大促進(jìn)了真空滲碳工藝的發(fā)展。離子氮化成功地用于生產(chǎn)也帶動(dòng)了離子滲碳的研究。為了節(jié)約能源和石油消耗,直接在工作爐內(nèi)滴注有機(jī)液體以獲得滲碳?xì)夥眨蛞缘鶜鉃檩d體氣的氣體滲碳法目前也有了長(zhǎng)足的進(jìn)展。采用微機(jī)對(duì)滲碳過(guò)程進(jìn)行全自動(dòng)控制是一個(gè)重要的發(fā)展方向。
滲氮層硬度和耐磨性高于滲碳層,硬度可達(dá)69~72HRC,且在600~650℃高溫下仍能保持較高硬度;
滲氮層具有很高的抗疲勞性和耐蝕性;
滲氮后不需再進(jìn)行熱處理,可避免熱處理帶來(lái)的變形和其他缺陷; 滲氮溫度較低。
滲氮只適用于中碳合金鋼,需要較長(zhǎng)的工藝時(shí)間才能達(dá)到要求的滲氮層。
免責(zé)聲明:本網(wǎng)站所轉(zhuǎn)載的文字、圖片與視頻資料版權(quán)歸原創(chuàng)作者所有,如果涉及侵權(quán),請(qǐng)第一時(shí)間聯(lián)系本網(wǎng)刪除。
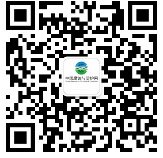
官方微信
《腐蝕與防護(hù)網(wǎng)電子期刊》征訂啟事
- 投稿聯(lián)系:編輯部
- 電話(huà):010-62316606
- 郵箱:fsfhzy666@163.com
- 腐蝕與防護(hù)網(wǎng)官方QQ群:140808414