1、普及下常規不銹鋼用于哪些氯離子環境
不銹鋼材質耐氯離子腐蝕標準可參照《火電廠循環水處理》一書明確約定:
⑴、T304不銹鋼使用環境:氯離子含量為0-200mg/L
⑵、T316不銹鋼使用環境:氯離子含量為<1000mg/L
⑶、T317不銹鋼使用環境:氯離子含量為<5000mg/L
按規范《GB 50235-2010 工業金屬管道工程施工規范》、《GB 50184-2011 工業金屬管道工程施工質量驗收規范》規定,水中氯離子含量不得超過25mg/L(25ppm)。
液壓試驗應符合下列規定:液壓試驗應使用潔凈水。當對不銹鋼、鎳及鎳合金管道,或對連有不銹鋼、鎳及鎳合金管道或設備的管道進行試驗時,水中氯離子含量不得超過25mg/L(25ppm)。
2、不銹鋼、超級不銹鋼和鈦材所用氯離子環境
下圖為不銹鋼、超級不銹鋼和鈦材所用氯離子環境。
紅色為低ppm和低溫環境,選用常規不銹鋼304,綠色高溫和高ppm環境,先用純鈦TA1。
從圖表可以看出,耐氯離子腐蝕有個簡易的排列:
304<316L<904L<254SMO<純鈦
3、雙相鋼耐氯離子腐蝕怎么樣?
有同學會問,雙相鋼耐氯離子腐蝕怎樣?性能如何?
下圖為PRE耐腐蝕當量值,耐點腐蝕指數 PRE (Pitting
Resistance Equivalent) 數值反映的是材料的耐氯離子點腐蝕傾向。
從下圖可以看出,雙相鋼2101、2304、2205、2507四個牌號耐腐蝕傾向均大于普通316L,有些材料和超級不銹鋼相當。
如2507耐點腐蝕就媲美254SMO,2205與904L的耐氯離子點腐蝕腐蝕性能相當。
代入上面第2部分,很清楚可以看到他們排在什么位置。
上面G150腐蝕試驗是奧托昆普發明的電化學臨界點蝕溫度的標準試驗方法,臨界點腐蝕溫度如上:可以看出,G150結果與PRE數值結果類同。
4、超級不銹鋼254SMO與316L耐氯離子腐蝕
上面黑白圖和藍色圖一樣,是來自奧托昆普不同年份和版本的圖示,可以看出:
316L耐氯離子點腐蝕性能遠低于254SMO,耐縫隙腐蝕結果同樣。
如60度溫度時候,316L僅耐200ppm不到,904L耐8500ppm,254SMO耐15000ppm氯離子。
數值大家可以按圖索驥。
5、FGD脫硫氯離子+氟離子腐蝕選材(55~70度)
以上兩圖年代不同,結果類似,上圖是奧托昆普結果,下圖為德國VDM公司。
圖示收集了從0~20萬ppm氯離子+氟離子腐蝕工況(大部分是氯離子)的選材區間,是不可多得的氯離子選材參考。
下圖更直觀,50~70度溫度下,按照酸堿性和氯離子濃度直接找到對應材料即可。
6、鈦系列金屬耐氯離子腐蝕如何?
上一張圖標,第一行是鈦材,可以看出,當C276鎳基合金在204度的溫度、3000ppm高壓釜下開始有點腐蝕時候,鈦材還依然在戰斗,沒有任何腐蝕。
鈦材在氯離子腐蝕上的應用。
眾所周知,鈦材對高氯離子的海水環境幾乎是免疫的,基本沒有腐蝕。
海水的鹽度通常小于5%,根據長期的實驗和實際使用,認為純鈦可以在120度以下的海水中安全使用,但溫度再升高就有可能發生縫隙腐蝕,繼續升高就有可能發生點蝕。
鈦在不同濃度,PH值(3-9),溫度的NaCl溶液中的使用范圍見下圖所述!
鈦鈀合金(Ti-0.2Pd,Grade7)和鈦鎳鉬合金(Ti-Grade-12),可以用到260度的高溫加壓海水中!
下面是純鈦,鈦鈀合金(Grade7),鈦鎳鉬合金(Grade12)在不同濃度的氯化鈉溶液,氯化鎂溶液中的耐腐蝕結果。
可以看出,在該工況中,鈦鈀合金和鈦鎳鉬合金耐氯離子的程度比純鈦高的多!
耐腐蝕度:Grade7>Grade12>純鈦(Grade2)
注意:圖中白色圓圈代表可以使用;黑色圓圈代表容易發生縫隙腐蝕或點蝕;白色三角形代表發生輕微的縫隙腐蝕,但是不影響使用。
對于重量百分比、體積百分比與ppm之間的換算,請另存下圖
對于摩爾濃度與重量百分比之間的換算,簡單如下:
1、應力腐蝕
不銹鋼在含有氧的氯離子的腐蝕介質環境產生應力腐蝕。應力腐蝕失效所占的比例高達45%左右。
常用的防護措施:合理選材,選用耐應力腐蝕材料主要有高純奧氏體鉻鎳鋼,高硅奧氏體鉻鎳鋼,高鉻鐵素體鋼和鐵素體—奧氏體雙相鋼。其中,以鐵素體—奧氏體雙相鋼的抗應力腐蝕能力最好。控制應力:裝配時,盡量減少應力集中,并使其與介質接觸部分具有最小的殘余應力, 防止磕碰劃傷,嚴格遵守焊接工藝規范。
嚴格遵守操作規程:嚴格控制原料成分、流速、介質溫度、壓力、pH 值等工藝指標。在工藝條件允許的范圍內添加緩蝕劑。鉻鎳不銹鋼在溶解有氧的氯化物中使用時,應把氧的質量分數降低到1. 0×10 - 6 以下。實踐證明,在含有氯離子質量分數為500. 0 ×10 - 6 的水中,只需加入質量分數為150. 0 ×10 - 6 的硝酸鹽和質量分數為0. 5 ×10 - 6亞硫酸鈉混合物,就可以得到良好的效果。
2、孔蝕失效及預防措施
小孔腐蝕一般在靜止的介質中容易發生。蝕孔通常沿著重力方向或橫向方向發展,孔蝕一旦形成,即向深處自動加速。,不銹鋼表面的氧化膜在含有氯離子的水溶液中便產生了溶解,結果在基底金屬上生成孔徑為20μm~30μm 小蝕坑,這些小蝕坑便是孔蝕核。只要介質中含有一定量的氯離子,便可能使蝕核發展成蝕孔。
常見預防措施:在不銹鋼中加入鉬、氮、硅等元素或加入這些元素的同時提高鉻含量。降低氯離子在介質中的含量。加入緩蝕劑,增加鈍化膜的穩定性或有利于受損鈍化膜得以再鈍化。采用外加陰極電流保護,抑制孔蝕。
3、點腐蝕
由于任何金屬材料都不同程度的存在非金屬夾雜物,這些非金屬化合物,在Cl 離子的腐蝕作用下將很快形成坑點腐蝕,在閉塞電池的作用,坑外的Cl 離子將向坑內遷移,而帶正電荷的坑內金屬離子將向坑外遷移。在不銹鋼材料中,加Mo的材料比不加Mo的材料在耐點腐蝕性能方面要好,Mo含量添加的越多,耐坑點腐蝕的性能越好。
4、縫隙腐蝕
縫隙腐蝕與坑點腐蝕機理一樣,是由于縫隙中存在閉塞電池的作用,導致Cl 離子富集而出現的腐蝕現象。這類腐蝕一般發生在法蘭墊片、搭接縫、螺栓螺帽的縫隙,以及換熱管與管板孔的縫隙部位,縫隙腐蝕與縫隙中靜止溶液的濃縮有很大關系,一旦有了縫隙腐蝕環境,其誘導應力腐蝕的幾率是很高的。
1 、304
這是最廉價、最廣泛使用的奧氏體不銹鋼(如食品、化工、原子能等工業設備)。適用于一般的有機和無機介質。例如,濃度<30%、溫度≤100℃或濃度≥30%、溫度<50℃的硝酸;溫度≤100℃的各種濃度的碳酸、氨水和醇類。在硫酸和鹽酸中的耐蝕性差;尤其對含氯介質(如冷卻水)引起的縫隙腐蝕最敏感。
2 、304L
耐蝕性和用途與304 型基本相同。由于含碳量更低(≤0.03%),故耐蝕性(尤其耐晶間腐蝕, 包括焊縫區)和可焊性更好,可用于半焊式或全焊式PHE。
3 、316
適用于一般的有機和無機介質。例如,天然冷卻水、冷卻塔水、軟化水;碳酸;濃度<50%的醋酸和苛性堿液;醇類和丙酮等溶劑;溫度≤100℃的稀硝酸(濃度<20%=、稀磷酸(濃度<30%=等。但是,不宜用于硫酸。由于約含2%的Mo,故在海水和其他含氯介質中的耐蝕性比304 型好,完全可以替代304 型。
4、316L
耐蝕性和用途與316 型基本相同。由于含碳量更低(≤0.03%),故可焊性和焊后的耐蝕性也更好,可用于半焊式或全焊式PHE。
5、317
適合要求比316 型使用壽命更長的工況。由于Cr、Mo、Ni元素的含量比316 型稍高,故耐縫隙腐蝕、點蝕和應力腐蝕的性能更好。
6、904L或890L
這是一種兼顧了價格與耐蝕性的高性價比的奧氏體不銹鋼,其耐蝕性比以上幾種材料好,特別適合一般的硫酸、磷酸等酸類和鹵化物(含Cl離子、F離子 )。由于Cr、Ni、Mo含量較高,故具有良好的耐應力腐蝕、點蝕和縫隙腐蝕性能。
7、254SMo
這是一種通過提高Mo含量對316 型進行了改進的超低碳高級不銹鋼,具有優良的耐氯化物點蝕和縫隙腐蝕性能,適用于不能用316 型的含鹽水、無機酸等介質。
8 、654SMo
這是一種Cr、Ni、Mo、N含量均高于254 SMO 的超低碳高級不銹鋼,耐氯化物腐蝕的性能比254 SMO更好,可用于冷的海水。
9、0Cr20Ni26Mo3Cu3Si2Nb
這是一種國產的Cr–Ni–Mo-Cu 不銹鋼。耐點蝕和縫隙腐蝕的性能相當于316型,而耐應力腐蝕的性能更好。可用于80 ℃以下的濃硫酸(濃度90~98%),年腐蝕率≤0.04mm/a。
10、Incoloy 825
這是一種Ni(40%)–Cr(22%)–Mo(3%)高級不銹鋼。Incoloy 是the nternational Nickel Co.公司的注冊商標。適用于低溫下各種濃度的硫酸;在濃度為50%~70%的苛性堿(如NaOH)溶液中,具有良好的耐蝕性,不產生應力腐蝕開裂。但是,對氯化物引起的縫隙腐蝕卻很敏感。此外,沖壓性能也不太好,故不是板片常用的材料。
11、31 合金
由904L改進后的(提高Mo、N含量)、標準的6%Mo高級不銹鋼(31%Ni-27%Cr-6.5%Mo-32%Fe)。在許多介質中的耐蝕性比904L更好;在濃度20%~80%、溫度60℃~100℃的硫酸中,耐蝕性能甚至超過 C-276。
12、33 合金
一種完全奧氏體化的鉻基高級不銹鋼,其耐蝕性可與Inconel 625等一些Ni-Cr-Mo合金媲美。在酸性和堿性介質(包括硝酸、硝酸與氫氟酸的混合物)中,具有良好的耐局部腐蝕和應力腐蝕開裂的性能;在濃硝酸中的耐蝕性比304L好得多。例如,適用于濃度大于96%~99%、溫度≤150℃、氧化硫含量小于200 mg/L的硫酸;熱的海水;濃度≤50%、沸騰的強腐蝕性溶液;濃度≤85%、溫度≤150℃的磷酸等。但是,不適用于還原性介質(如稀硫酸等)。價格與C-276相差不多。
13、C-2000 合金
一種二十世紀90 年代研發的鎳基合金,價格與C-276 相近,是以上材料中耐腐蝕性能最好者之一。在中等濃度以下的硫酸、稀鹽酸和沸騰溫度下,濃度≤50%的磷酸,以及熱的氯化物等介質中,其耐蝕性比C-276 和 C-22更好, 有取代C-22 合金的趨勢。但是,對于濃度≥70%的硫酸,耐蝕性不如C-276。
14、59 合金
化學成分與C-2000比較,除了Ni 含量稍高(59%),且低Fe,無Cu、W外,其余基本上相同。這是目前鎳基合金中耐蝕性、熱穩定性、可沖壓性和可焊性最好的一種材料,自1990年商業化以來,已廣泛用于硫酸、鹽酸、氫氟酸以及含氯、含氧、低pH值的許多介質。
免責聲明:本網站所轉載的文字、圖片與視頻資料版權歸原創作者所有,如果涉及侵權,請第一時間聯系本網刪除。
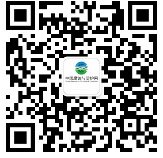
官方微信
《腐蝕與防護網電子期刊》征訂啟事
- 投稿聯系:編輯部
- 電話:010-62316606
- 郵箱:fsfhzy666@163.com
- 腐蝕與防護網官方QQ群:140808414